A Brief Analysis on Packaging Design for Consumer Electronics Products Lei ZHANG Zhengzhou Institute of Technology, Zhengzhou, China
Total Page:16
File Type:pdf, Size:1020Kb
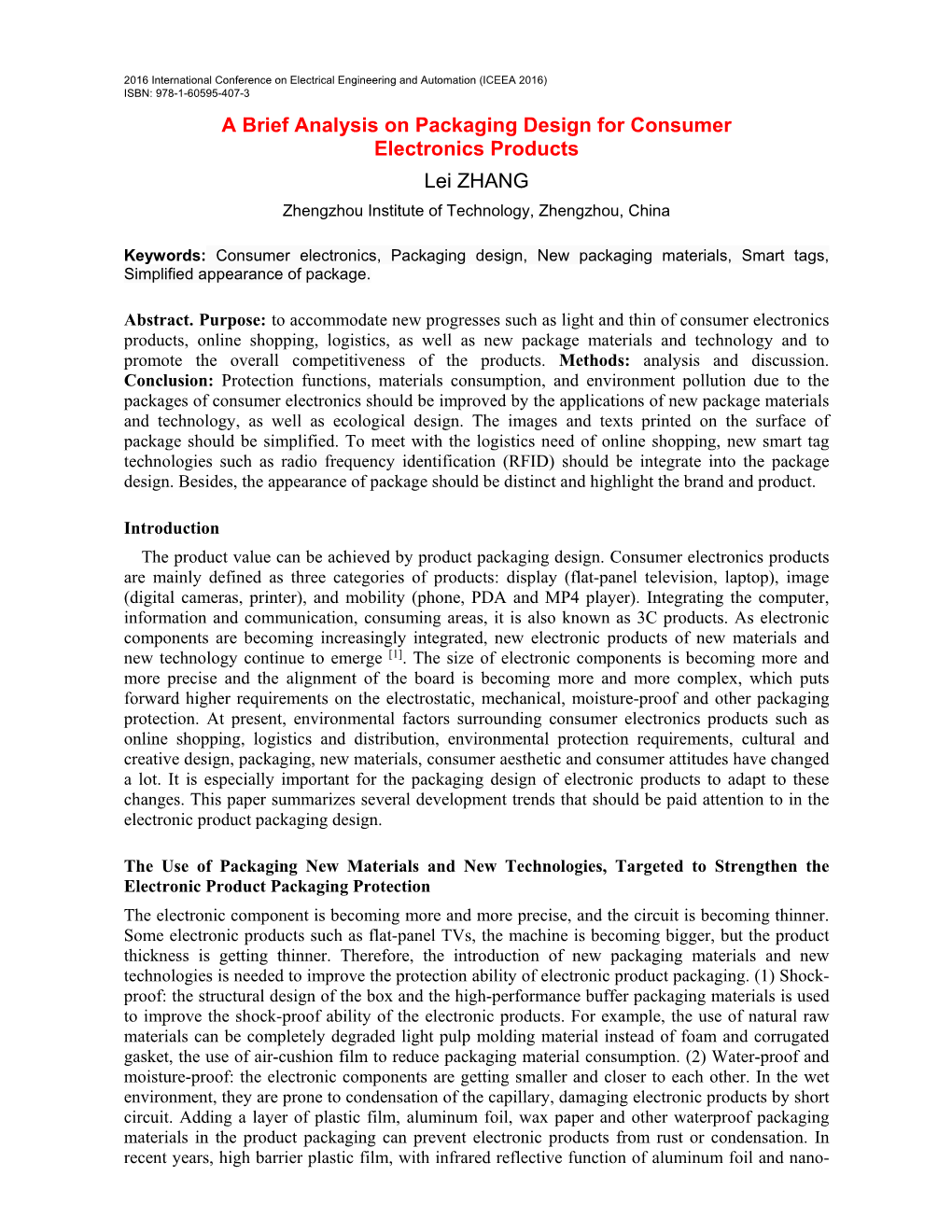
Load more
Recommended publications
-
Ecological Design and Material Election for Furniture Under the Philosophy of Green Manufacturing
·416· Proceedings of the 7th International Conference on Innovation & Management Ecological Design and Material Election for Furniture under the Philosophy of Green Manufacturing Zhang Qiumei1, Zhang Weimei2, Wang Gongming1 1 Central South University of Forestry and Technology, Changsha, P.R.China, 410002 2 Hunan City University, Yiyang, P.R.China, 413000 (E-mail: [email protected], [email protected], [email protected] ) Abstract Based on the principles of green manufacturing, the ecological system of furniture design consists of the ecological furniture design analysis, implementation, evaluation, as well as supporting and maintenance. Compared to the traditional furniture material election, the material election subject to the green manufacturing presents a new philosophy. The principle of furniture material election subject to the green manufacturing involves the combination of technical principle, economical principle and environmental principle. This paper also discusses the minimization of life-cycle cost of furniture material election subject to green manufacturing. Key words Green manufacturing; Ecological design of furniture; Furniture material election; Materials life cycle 1 Introduction Furniture manufacturing is one of the most important basic industries to maintain the constant development of the national economy. However, while the furniture making has contributed to the material progress of the society, it has also led to possible ecological crisis like exhaustion of resources and environmental deterioration. Therefore, the learning circle carries out the study on ecological and green design of furniture, green manufacture technology and green material for furniture, hence an efficient way of solving for the ecological crisis in the furniture manufacturing. Compared with the above study, ecological design and material election for furniture under the philosophy of green manufacturing is a kind of brand-new concept and pattern. -
Ecological Design 10Th Edition
ENVIRONMENTAL DESIGN Advance praise for VAN DER • RYN 10th ANNIVERSARY EDITION Ecological Design: Tenth Anniversary Edition: “The publication of Ecological Design was a seminal moment for the green building movement, and the book remains one of our most valuable and relevant texts today. ecological Sim Van der Ryn is one of the fathers of sustainable design, but his work transcends time; together with Stuart Cowan, he has written a work that will inspire and inform us for years to come.” —S. Richard Fedrizzi, President, CEO and Founding Chairman of the U.S. Green Building Council COWAN design “A benchmark pioneering work that remains vitally relevant today after a decade of influencing the ecodesign community, and now with new ideas and a critical assess- ment of the sustainability status quo in the introduction.” —Dr. Ken Yeang, Architect and Planner, Llewleyn Davies Yeang, UK. Praise for the original edition: ecological de SIM VAN DER RYN “[Ecological Design] is a ground-breaking book that will change the way we think STU ART COWA N about buildings, agriculture, industrial processes, and our management of resources and wastes.” —Environmental Building News “Visionary ...Van der Ryn and Cowan delight in showing us each detail of transform- ing both consciousness and substance from ‘dumb design’ (environmentally wasteful) to ecological design.” —San Francisco Chronicle SIM VAN DER RYN is the founder of the Eco-Design Collaborative, the non-profit Ecologic Design Institute, and the Center for Regenerative Design at the College of Marin. He has served as California State Architect, founded the University of California Berkeley’s ecological design program, and has been a professor of architecture there for thirty-five years. -
Ecology Design
ECOLOGY and DESIGN Ecological Literacy in Architecture Education 2006 Report and Proposal The AIA Committee on the Environment Cover photos (clockwise) Cornell University's entry in the 2005 Solar Decathlon included an edible garden. This team earned second place overall in the competition. Photo by Stefano Paltera/Solar Decathlon Students collaborating in John Quale's ecoMOD course (University of Virginia), which received special recognition in this report (see page 61). Photo by ecoMOD Students in Jim Wasley's Green Design Studio and Professional Practice Seminar (University of Wisconsin-Milwaukee) prepare to present to their client; this course was one of the three Ecological Literacy in Architecture Education grant recipients (see page 50). Photo by Jim Wasley ECOLOGY and DESIGN Ecological by Kira Gould, Assoc. AIA Literacy in Lance Hosey, AIA, LEED AP Architecture with contributions by Kathleen Bakewell, LEED AP Education Kate Bojsza, Assoc. AIA 2006 Report Peter Hind , Assoc. AIA Greg Mella, AIA, LEED AP and Proposal Matthew Wolf for the Tides Foundation Kendeda Sustainability Fund The contents of this report represent the views and opinions of the authors and do not necessarily represent the opinions of the American Institute of Architects (AIA). The AIA supports the research efforts of the AIA’s Committee on the Environment (COTE) and understands that the contents of this report may reflect the views of the leadership of AIA COTE, but the views are not necessarily those of the staff and/or managers of the Institute. The AIA Committee -
Ecological Landscape Design
Chapter 13 Ecological Landscape Design Filiz Çelik Additional information is available at the end of the chapter http://dx.doi.org/10.5772/55760 “Choose only one master-Nature” Rembrandt Harmenszoon van Rijn (1606-1669) 1. Introduction The most critical changes in the world over the last century have been derived from the variety of environmental problems. Growing environmental problems now affect entire the world. The majority of environmental problems originates in human greed and interference. It is well known that planet Earth is experiencing a so-called environmental crisis (ecological crisis). This crisis is characterized by three major themes: Rapid growth of the human population and its associated economic activity, The depletion of both non-renewable and renewable resources, and Extensive and intensive damage caused to ecosystems and biodiversity. The environmental crisis is a predicament of inappropriate design-it is a consequence of how cities have been developed, industrialization undertaken, and ecoscapes used. Fundamentally, the problem has been one of inadequate integration of ecological concerns into planning (Shu-Yang et al., 2004). In many ways, the environmental crisis is a design crisis. It is clear that design has not been given a rich enough context. Design is a hinge that inevitably connects culture and nature through exchanges of materials, flow of energy, and choices of land use. The every world of buildings, artifacts, and domesticated landscape is a design world, one shaped by human (Van Der Ryn and Cowan, 1996). Some environmental problems have arisen from design problems. Design can have a crucial impact upon the environment in many different ways. -
Sustainability by Design in Textile Products and Fashion
New Design Ideas Vol.1, No.1, 2017, pp.37-49 SUSTAINABILITY BY DESIGN IN TEXTILE PRODUCTS AND FASHION Nesrin Önlü1* 1Textile & Fashion Design Department, Fine Arts Faculty, Dokuz Eylul University, Izmir, Turkey Abstract. Sustainability is to deliver everything we need to live, without disturbing the natural equilibrium, to future generations and to produce and sustain them in ways that they can benefit. Sensitivity to the environment is essential in sustainability. Manifesto, take it from nature, give it back to nature, or reapply it. Natural return is the goal of sustainability to produce environmentally friendly products and to recreate less consuming society. We have to spend our consumption habits for a sustainable life, we must adopt slow fashion instead of fast fashion in order to reduce the most damage to the environment in the concept of fashion which is effective in every area of our life today. Fashion, on the other hand, is a concept that is connected to a much more design than any other period, and has become a phenomenon that shapes every stage of our life, every field. The ultimate in design is the design and production of much more product variety than we can consume. This kind of production damages the neighborhood too much and confronts future generations with a world that can not be experienced. For this reason, this article will talk about the importance of sustainability, its contribution to sustainability of design, and how sustainability can be achieved through design within textiles and fashion. Keywords: sustainability, design, textile, fashion. Corresponding Author: Nesrin Önlü, Professor, Textile & Fashion Design Department, Fine Arts Faculty, Dokuz Eylul University, Izmir, Turkey, e-mail:[email protected] Manuscript received: 8 November 2017 1. -
Importance of Humane Design for Sustainable Landscape
IACSIT International Journal of Engineering and Technology, Vol. 6, No. 6, December 2014 Importance of Humane Design for Sustainable Landscape S. Toofan energy consumption, transport and the urban footprint[3], [4]. Abstract—Realizing the environmental threats, real or Curiously, and with the recent exception of the compact city potential, to the quality of life, environmental movements have debates [5], this literature has largely neglected the challenge begun in virtually all sectors of industrialized countries, of designing cities as sustainable and live able places which including business, manufacturing, transportation, agriculture, and architecture. Sustainable landscape architecture is one of can adapt their unique cultural identities and specific historic the most incredible fields of design at contemporary topics. heritage to contemporary needs. Conservation and Important problem that will be resolved in this research is sustainability in relation to the patrimony and cultural finding standard spots and positions in urban landscape for heritage of the built environment are core themes. coming to sustainable landscape. The main purpose of this Scientific research continues to provide information about article is investigation of humane factors for better design in all the links between human health and environmental quality. scales of landscape architecture, into special consideration to sustainability. The research method of this paper is Essential components of life-air, water, and food-provide "Descriptive Study", with two strategies: definition of potential pathways for contaminants to affect our health. keywords and discussion about them to receiving useful World health organization said: “Health is a state of complete alternatives. Basic subjects had defined and then major objects physical, mental and social well-being and not merely the had analyzed. -
Metabolicity: How Can Design Nurture Amateur Cultures of Food Production in the City?
Multiple Ways to do Design Research: Research Cases that Shape the Design Discipline Swiss Design Network Symposium, Lugano, Switzerland. 12th – 13th November 2009 Title MetaboliCity: How can Design Nurture Amateur Cultures of Food Production in the City? Abstract This paper introduces a current design research project that explores how designers can intervene sensitively within local urban food growing cultures by providing a design thinking and crafting that may help to sustain these initiatives and catalyse larger positive changes in the surrounding environment. MetaboliCity is the name for a vision of a city that metabolizes its resources and waste to supply its inhabitants with all the nourishment they need and more. This one-year (October 2008 – October 2009) participatory design research project on urban agriculture is based at Central Saint Martins, School of Art and Design and funded by the Audi Design Foundation. The aim of the project is to design an urban grow-kit accompanied by a set of guidelines to be tested and developed at a selection of sites in London, UK. This is a design-service system that integrates both traditional and hi-tech industrialized agricultural techniques into the fabric of the built environment whilst simultaneously being rooted in permaculture thinking. Permaculture is defined as an ‘ecological design system’ that empowers city-dwellers to create ‘sustainable human habitats by following nature’s pattern’. (Robert Hopkins, 2008, p203) The complex nature of the project calls for a Metadesign approach. Metadesign can be described as ‘a shared design endeavour aimed at sustaining emergence, evolution and adaptation’. It creates ‘open-ended and infinite interactivity capable of accommodating always-new variables’. -
A Social-Ecological Approach to Architecture and Planning
Journal of Architecture and Construction Volume 2, Issue 4, 2019, PP 33-44 ISSN 2637-5796 A Social-Ecological Approach to Architecture and Planning Richard Graves1*, Bonnie Keeler2, Maike Hamann2, Elizabeth Kutscke1 and Chris Nootenboom3 1Center for Sustainable Building Research, College of Design, University of Minnesota, Minneapolis, USA 2Institute on the Environment, Humphrey School of Public Affairs, University of Minnesota, Minneapolis, USA 3Institute on the Environment, University of Minnesota, Minneapolis, USA *Corresponding Author: Richard Graves, AIA, Director and Associate Professor, Center for Sustainable Building Research, College of Design, University of Minnesota, 1425 University Ave SE, Room 115, Minneapolis, Email: [email protected] ABSTRACT Sustainable design has failed to fundamentally transform the performance of the built environment in the most critical indicator: social-ecological impact. Design has focused on making systems more efficient, instead of redesigning the system to continually enhance natural processes and center the welfare of the people who live, work, and experience the built environment. Buildings, neighborhoods, and infrastructure must be reimagined using a social, ecological, and technological systems approach connecting the social needs of the community within the constraints of biophysical systems. We present an approach in the evolution of sustainable design, one that builds on green design and regenerative design, but advances a social-ecological design methodology - one that is sensitive to scale, -
The Design Charrette Ways to Envision Sustainable Futures the Design Charrette
Rob Roggema Editor The Design Charrette Ways to Envision Sustainable Futures The Design Charrette Rob Roggema Editor The Design Charrette Ways to Envision Sustainable Futures Editor Rob Roggema Department of Landscape Architecture Van Hall Larenstein, Wageningen University The Netherlands The Swinburne Institute for Social Research Swinburne University of Technology Hawthorn, Australia ISBN 978-94-007-7030-0 ISBN 978-94-007-7031-7 (eBook) DOI 10.1007/978-94-007-7031-7 Springer Dordrecht Heidelberg New York London Library of Congress Control Number: 2013947776 © Springer Science+Business Media Dordrecht 2014 This work is subject to copyright. All rights are reserved by the Publisher, whether the whole or part of the material is concerned, specifi cally the rights of translation, reprinting, reuse of illustrations, recitation, broadcasting, reproduction on microfi lms or in any other physical way, and transmission or information storage and retrieval, electronic adaptation, computer software, or by similar or dissimilar methodology now known or hereafter developed. Exempted from this legal reservation are brief excerpts in connection with reviews or scholarly analysis or material supplied specifi cally for the purpose of being entered and executed on a computer system, for exclusive use by the purchaser of the work. Duplication of this publication or parts thereof is permitted only under the provisions of the Copyright Law of the Publisher’s location, in its current version, and permission for use must always be obtained from Springer. Permissions for use may be obtained through RightsLink at the Copyright Clearance Center. Violations are liable to prosecution under the respective Copyright Law. The use of general descriptive names, registered names, trademarks, service marks, etc. -
Ecological Design of Urban Landscapes: Economic, Social
Ecological Design of Urban Landscapes: Economic, Social, and Ecological Benefits EM 9107 • March 2015 Signe Danler, © Oregon State University State © Oregon Danler, Signe Figure 1. The downtown Corvallis Riverfront accommodates multiple uses, and incorporates elements of ecological landscaping and green infrastructure. S. Danler and G. Langellotto-Rhodaback ities of the future, from small towns to huge design, and bringing ecology and design together to metropolises, may be much different from form a sustainable urban landscape. the typical city of today. Imagine a city C Introduction designed with tree-lined boulevards and peace- ful, green neighborhoods, with clean air and pure Nature operates in cycles. Water, air, and nutri- water. Thriving communities are veined with parks, ents are all continually circulated in closed, circular greenways, yards, and creeks, interconnecting and systems that waste nothing. Cities built with little providing life-giving habitat for native plants, ani- knowledge of, or regard for, these cycles are leaky, mals, insects, birds—and people. linear systems that interrupt natural ecosystem func- Cities like this, which support both functioning tions and create waste that must be dealt with by urban ecosystems and human society, need land- engineered infrastructure. scape designers, planners, architects, and developers In the natural water cycle, for example, rainwater who are knowledgeable about ecological landscap- percolates through vegetation and soil, recharging ing, in addition to their other skills. An ecological aquifers and eventually evaporating back to the air approach to landscape design incorporates natural to fall again as rain. The impermeable surfaces of a systems as an integral part of urban landscapes (Figure 1). -
Sustainable Design Principles
ENGS 44 SUSTAINABLE DESIGN Sustainable Design Principles Benoit Cushman-Roisin 28 March 2019 “Our current age sees everything as an object of manufacture, as something which can be got hold of and improved, or altered, to produce better or more effective outcomes. This is our present fate, especially in the West, to understand all things in this way.” Laurence Paul Hemming in Worship as Revelation burns & oates, 2008, page 10. So, we seek to improve and alter, even disrupt . We love to design and redesign. Buzz words today are innovation and disruption, both considered as positive. The question is: How can we design and redesign responsibly? What should be the guiding principles? 1 Underlying principle We don’t design for the sake of designing. We design for a purpose: - To meet a need in a new way, in a better way, - To achieve a goal, - To make a statement. This holds true regardless of the size of what is being designed, from a bicycle shed to an entire city, from a spoon to a cell phone. “If you cannot measure it, you can’t improve it.” Lord Kelvin “We cannot solve our problems with the same thinking we used when we created them.” Albert Einstein Conclusions: - We need to be quantitative → engineering sciences - We need to think creatively → some art involved The Science and Art of Sustainable Design! 2 Principles of Sustainable Design according to Jason F. McLennan, “The Philosophy of Sustainable Design”, 2004 1. Learning from natural systems (Biomimicry Principle) 2. Respect for energy & natural resources (Conservation Principle) 3. -
Sustainable Interiors: Green Design Methods and Its Influence on Ecopsychology Tillie M
Fordham University Masthead Logo DigitalResearch@Fordham Student Theses 2015-Present Environmental Studies May 2018 Sustainable Interiors: Green Design Methods and its Influence on Ecopsychology Tillie M. O'Reilly Fordham University, [email protected] Follow this and additional works at: https://fordham.bepress.com/environ_2015 Part of the Environmental Design Commons, Interior Architecture Commons, Natural Resources and Conservation Commons, and the Sustainability Commons Recommended Citation O'Reilly, Tillie M., "Sustainable Interiors: Green Design Methods and its Influence on Ecopsychology" (2018). Student Theses 2015-Present. 51. https://fordham.bepress.com/environ_2015/51 This is brought to you for free and open access by the Environmental Studies at DigitalResearch@Fordham. It has been accepted for inclusion in Student Theses 2015-Present by an authorized administrator of DigitalResearch@Fordham. For more information, please contact [email protected]. O’Reilly 1 Word Count: 14,068 Sustainable Interiors: Green Design Methods and its Influence on Ecopsychology Tillie O'Reilly O’Reilly 2 Abstract The profession of interior design proposes to enhance interior spaces through the use of furnishings, lighting, and color palettes while adhering to safety standards and building codes. Although designers follow strict codes to beautify a space, they may disregard the natural environment when choosing materials that are aesthetically pleasing. It is difficult for designers to design sustainably when they must balance many demands in design such as functionality, aesthetics, safety, and clients’ tastes. This paper addresses how sustainable design methods can be incorporated into the field of interior design to benefit the environment, while simultaneously improving the beauty of the space. Chapter one offers a problematic view of modern interior design, where most interior designers do not follow sustainable principles or consider the impacts of their actions on the environment.