Borax As Internal Stock Additive in Papermaking
Total Page:16
File Type:pdf, Size:1020Kb
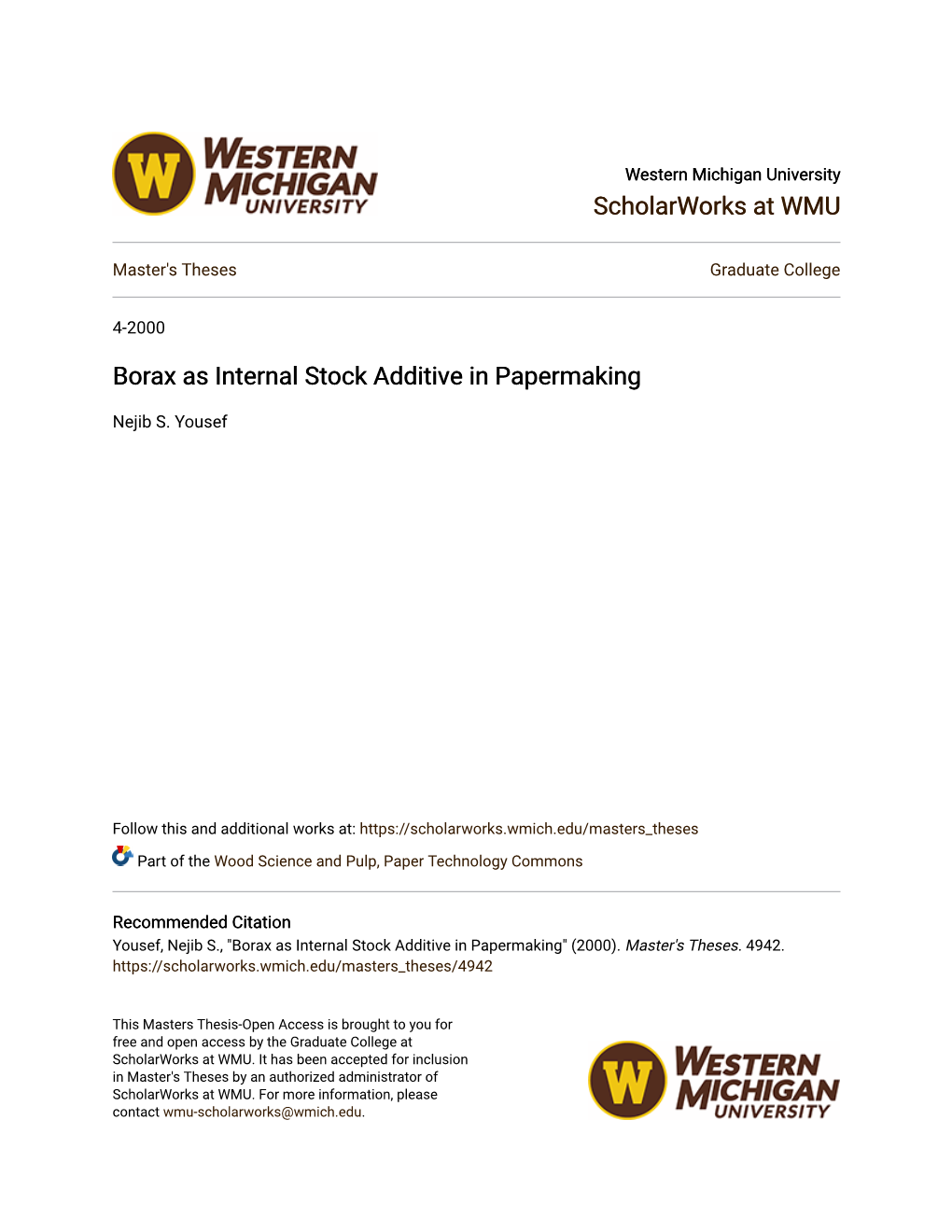
Load more
Recommended publications
-
Government Paper Specification Standards
Government March 2011 No. 12 Government March 2011 No. 12 Printed on recycled paper For sale by the Superintendent of Documents, U.S. Government Printing Office Internet: bookstore.gpo.gov Phone: toll free (866) 512-1800; DC area (202) 512-1800 F1ax: (202) 512-2104 Mail: Stop IDCC, Washington, DC 20402-000 ISBN 978-0-16-088382-8 U.S. GOVERNMENT PRINTING OFFICE WILLIAM J. BOARMAN Keeping America Informed I www.gpo.gov Public Printer of the United States March 16, 2011 The Honorable Joseph R. Biden The President of the Senate The Honorable John A. Boehner The Speaker of the House of Representatives Sirs: I have the honor to transmit herewith the Annual Report of the U.S. Government Printing Office (GPO) for the fiscal year ending September 30, 2010. The report contains the results of an audit of GPO’s financial statements conducted by an independent accounting firm. Respectfully submitted, WILLIAM J. BOARMAN Public Printer 732 North Capitol Street, NW, Washington, DC 20401-0001 I [email protected] TABLE OF CONTENTS Advisory Council on Paper Specifications ………………………………………… v Introduction …………………………………………………………………………. vii Recycled Fiber Content and Permanent Paper Standards ………...……….…………. ix Part 1. Specifications ………………...……………………………………………... 1 Runnability Requirements for Paper Used in a Federal Printing Plant ………………. 3 Printing Papers ………………………………………………………………………. 5 JCP A10: Newsprint JCP A25: Heat-Set Web Offset Machine-Finish Book JCP A50: Machine-Finish Book End JCP A55: Heat-Set Web Offset Book JCP A60: Offset Book JCP A61: No. 1 Offset -
Conservation of Coated and Specialty Papers
RELACT HISTORY, TECHNOLOGY, AND TREATMENT OF SPECIALTY PAPERS FOUND IN ARCHIVES, LIBRARIES AND MUSEUMS: TRACING AND PIGMENT-COATED PAPERS By Dianne van der Reyden (Revised from the following publications: Pigment-coated papers I & II: history and technology / van der Reyden, Dianne; Mosier, Erika; Baker, Mary , In: Triennial meeting (10th), Washington, DC, 22-27 August 1993: preprints / Paris: ICOM , 1993, and Effects of aging and solvent treatments on some properties of contemporary tracing papers / van der Reyden, Dianne; Hofmann, Christa; Baker, Mary, In: Journal of the American Institute for Conservation, 1993) ABSTRACT Museums, libraries, and archives contain large collections of pigment-coated and tracing papers. These papers are produced by specially formulated compositions and manufacturing procedures that make them particularly vulnerable to damage as well as reactive to solvents used in conservation treatments. In order to evaluate the effects of solvents on such papers, several research projects were designed to consider the variables of paper composition, properties, and aging, as well as type of solvent and technique of solvent application. This paper summarizes findings for materials characterization, degradative effects of aging, and some effects of solvents used for stain reduction, and humidification and flattening, of pigment-coated and modern tracing papers. Pigment-coated papers have been used, virtually since the beginning of papermaking history, for their special properties of gloss and brightness. These properties, however, may render coated papers more susceptible to certain types of damage (surface marring, embedded grime, and stains) and more reactive to certain conservation treatments. Several research projects have been undertaken to characterize paper coating compositions (by SEM/EDS and FTIR) and appearance properties (by SEM imaging of surface structure and quantitative measurements of color and gloss) in order to evaluate changes that might occur following application of solvents used in conservation treatments. -
Paper & Paperboard Testing Program
Collaborative Testing Services, Inc. Paper & Paperboard Testing Program Summary Report #2951 S - July 2018 Introducon to the Paper & Paperboard Interlaboratory Program Explana on of Tables and Definions of Terms Analysis Analysis Name 305 Bursng Strength - Prinng Papers 310 Bursng Strength - Packaging Papers 311 Tearing Strength - Newsprint 312 Tearing Strength - Prinng Papers 314 Tearing Strength - Packaging Papers 320 Tensile Breaking Strength - Newsprint 321 Tensile Energy Absorpon - Newsprint 322 Elongaon to Break - Newsprint 325 Tensile Breaking Strength - Prinng Papers 327 Tensile Energy Absorpon - Prinng Papers 328 Elongaon to Break - Prinng Papers 330 Tensile Breaking Strength - Packaging Papers 331 Tensile Energy Absorpon - Packaging Papers 332 Elongaon to Break - Packaging Papers 334 Folding Endurance (MIT) - Double Folds 336 Bending Resistance, Gurley Type 338 Bending Resistance, Taber Type - 0 to 10 Units 339 Bending Resistance, Taber Type - 10 to 100 Taber Units 340 Bending Resistance, Taber Type - 50 to 500 Taber Units - Recycled Paperboard 343 Z-Direcon Tensile 345 Z-Direcon Tensile, Recycled Paperboard 348 Internal Bond Strength - Modified Sco Mechanics 349 Internal Bond Strength - Sco Bond Models The CTS Paper & Paperboard Interlaboratory Program In 1969, the National Bureau of Standards (now designated the National Institute for Standards and Technology) and the Technical Association of the Pulp and Paper Industry (TAPPI) developed an interlaboratory program for paper and paperboard testing. Since 1971, Collaborative Testing Services has operated the Collaborative Reference Program for Paper and Paperboard. With hundreds of organizations from around the world participating in these tests, this program has become one of the largest of its kind. The program allows laboratories to compare the performance of their testing with that of other participating laboratories, and provides a realistic picture of the state of paper testing. -
Application of Ethylene Oxide Gas and Argon Gas Mixture System Method for Scale Deacidification of Cellulose-Based Cultural Heritage Collections
coatings Article Application of Ethylene Oxide Gas and Argon Gas Mixture System Method for Scale Deacidification of Cellulose-Based Cultural Heritage Collections Yunpeng Qi, Zhihui Jia *, Yajun Zhou, Yong Wang, Guangtao Zhao, Xiaolian Chao, Huiping Xing * and Yuhu Li * School of Materials Science and Engineering, Engineering Research Center of Historical Cultural Heritage Conservation, Ministry of Education, Shaanxi Normal University, Xi’an 710119, China; [email protected] (Y.Q.); [email protected] (Y.Z.); [email protected] (Y.W.); [email protected] (G.Z.); [email protected] (X.C.) * Correspondence: [email protected] (Z.J.); [email protected] (H.X.); [email protected] (Y.L.); Tel.: +86-029-8153-0715 (Z.J. & H.X. & Y.L.) Abstract: Deacidification plays an important role in the conservation of paper-based cultural heritage objects. Herein, a novel approach for the conservation of scale paper-based cultural heritage objects is proposed using a mixture of argon and ethylene oxide (EO-Ar) for the first time. The optimum process conditions for deacidification of ethylene oxide and argon mixture system are determined by orthogonal testing. To evaluate the stabilization effect of paper treated with EO-Ar, the degradation of the mechanical properties (tensile strength, folding endurance and tearing strength tests) of paper after artificial aging was evaluated. The results show that the treated paper had better durability with respect to tensile strength, folding endurance and tearing strength. Additionally, thermal Citation: Qi, Y.; Jia, Z.; Zhou, Y.; stability, crystallinity and fiber wall thickness increased after EO-Ar treated, which was determined Wang, Y.; Zhao, G.; Chao, X.; Xing, H.; by scanning electron microscope (SEM), diffraction of X-rays (XRD), and thermo gravimetric (TG) Li, Y. -
STP60-B-EB/Jul. 1963
STP60-B-EB/Jul. 1963 INDEX A Blotting paper, 1, 11 Absorbency, 51, 52 Boards, 28 Acidity (see also pH Value) types, 29 determination of, 59 uses, 29 of bond papers, 20 Bogus bristol, 22 Adhesives in paper, 70 Bond inks, 47 Aging, accelerated test for, 82 Bond papers, 18, 41 Air permeability, 61 Bonding strength, surface, I10 Alkalinity (see also pH Value), 59 Book inks, 47 Alpha-cellulose, 62, 76 Book papers, 40, 121 Aniline sulfate stain for groundwood, 78 Boxboards, 34 Antique finish, 41 Bright fiber stain, 77 Apparent density, 121, 122 Brightness, 4, 73, 101 Asbestos paper, 39 Bristol board, 35 Ash content Bristols, 21, 42 determination of, 63 Brush surface analyzer, 113 examination of, 63 Buffer action, 60 of bond papers, 20 Building boards, 36 related to other properties, 64 Building papers, 23, 36 significance of, 63 Bursting strength, 68 Asphalt impregnated papers, 24, 90 determination of, 69 ASTM methods, vii of bond papers, 19 Automotive panel boards, 37 of envelope papers, 28 significance of, 69 B C Bag papers, 17 "C" stain for fibers, 77 Basis weight Calender cuts, 86 paper, 65 Caliper (see also Thickness) paperboard, 67 bond paper, 19 wedding bristols, 22 paperboard, 33 Beach puncture test, 103 Capacitor paper, thickness of, 121 Beating of fibers, 1, 76 Cardboard, 35 Bekk smoothness tester, 113 Cards, thickness of, 121 Bending board, 34 Casein, 71, 97 Bending chip, 80 Castor oil test, 88 Ben&sen smoothness tester, 113 Cellulose, 2, 62, 92, 100 Beta-cellulose, 62 Chapman smoothness tester, 113 Binders board, 36 Chipboard, 33 -
Docuisit Anon
DocuisiT anon 'RD 104 345 IR 001 734 AUTHOR Roberson, David D. TITLE Revised Specifications for Uncoated Permanent/Durable Book,Paper. INSTITUTION Barrow (N.J.) Research Lab., Richmond, Va. 3PONS AGENCY Council on Library Resources, Inc., Washington, D.C.; 'Library-of Congress, Washington, D.C. MAME 73 NOTE 126p. EDRS- PRICE BP-$0.76 HC -$6.97 PLUS POSTAGE DESCRIPTORS *Books; Library Materials; Measurement; *Paper (Material); *Preservation; Publishing Industry; Testing _IDENTIFIERS *Permanent Durable Book Paper ABSTRACT ' To aid in the evaluation of ther_physiCal guaiitiet.of_ _ books, specifications for permanent/durable book paper-were developed- and-authenticated. Permanent/durable book-paper was defined aspaper suitable=for use in the manufacture of books that meets or'exCeeds- tests which demonstrate that it has-an expectation of usefullife --under normal storage conditions of not less than-500 years. The literature was studied:for material on factors affecting the longevity Of-paper and methods of testing permanenceand-durability. -The resulting specifications include-ihe minimum cold-extractionpH,- folding endurance, tear resistance, and.retention of fading .endurancw_after_aging.'Tmenty commercially-available paper 'mere tested by the studrs_pethods. The test results are given in tabular . ibmcm.--1 211-item bibliography is appended. (Author/PF) REVISED SPECIFICATIONS FOR UNCOATED PERMANENT/DURABLE BOOK PAPER Final Report, on a Project Jointly Supported by The Library of Congress and The Council on Library Resources Principal Investigator, David D. Roberson U.S DEPARTMENT OF HEALTH. EDUCATION SONELfAltE NATIONAL INSTITUTE OF EDUCATION THIS DOCUMENT HAS BEEN REPRO OUCEO EXACTLY AS RECEIVED FROM THE PERSON OR ORGANIZATION ORIGIN ATING IT. POINTS OF VIEW OR OF UNIONS STATED DO NOT NECESSARILY REPRE SENT OFFICIAL NATIONAL INSTITUTE OF EDUCATION POSITION OR POLICY W. -
Organosolv Pulping of Wheat Straw by Glycerol
CELLULOSE CHEMISTRY AND TECHNOLOGY ORGANOSOLV PULPING OF WHEAT STRAW BY GLYCEROL E. SABERIKHAH, J. MOHAMMADI ROVSHANDEH* and P. REZAYATI-CHARANI** Department of Chemistry, Faculty of Science, Islamic Azad University of Rasht, Gilan, Iran *Caspian Faculty of Engineering, University College of Engineering, University of Tehran, Rezvanshahr, Gilan, Iran **Department of Pulp and Paper Technology, Faculty of Forestry and Wood Technology, Gorgan University of Agriculture and Natural Resources, Gorgan, Iran Received May 6, 2010 Pulping of wheat straw was studied with an organic solvent (glycerol) and 2% NaOH as a catalyst, and without catalyst, at various cooking times (180, 90, 45 and 30 min), and at reflux temperature (195-205 °C) as cooking temperature, to investigate the properties of the obtained pulp (cooking yield, kappa number, freeness (CSF), fiber length, α-cellulose, γ-cellulose, ash) and paper (breaking length, burst index, fold endurance, tear index). The best properties of the handsheets were obtained with 2% sodium hydroxide in the cooking solvent, at 30 min as cooking time. As a result of using the processing variables over the variation ranges considered, the following optimum values of the dependent variables were obtained: 64.1% (yield), 64 (kappa number), 300 mL CSF (freeness), 11.89 km (breaking length), 60.38 (folding endurance), 9.27 mNm2g-1 (tear index) and 4.60 kNg-1 (burst index) for pulps and handsheets. The results obtained showed that, under the cooking conditions applied, either including the use of a catalyst or not, delignification increased by increasing the cooking time, although the brightness of the handsheets was reduced. These results involved a secondary reaction between the organic solvent glycerol and the micro-fragments of fibers during cooking. -
Some Aspects on Strength Properties in Paper Composed of Different Pulps
Faculty of Technology and Science Chemical Engineering Hanna Karlsson Some aspects on strength properties in paper composed of different pulps Karlstad University Studies 2007:38 Hanna Karlsson Some aspects on strength properties in paper composed of different pulps Karlstad University Studies 2007:38 Hanna Karlsson. Some aspects on strength properties in paper composed of different pulps Licentiate thesis Karlstad University Studies 2007:38 ISSN 1403-8099 ISBN 978-91-7063-141-2 © The author Distribution: Karlstad University Faculty of Technology and Science Chemical Engineering SE-651 88 Karlstad SWEDEN Phone +46 54 700 10 00 www.kau.se Printed at: Universitetstryckeriet, Karlstad 2007 Abstract For paper producers, an understanding of the development of strength properties in the paper is of uttermost importance. Strong papers are important operators both in the traditional paper industry as well as in new fields of application, such as fibre-based packaging and light-weight building material. In this study, two approaches of enhancing paper strength, reinforcement and multilayering, were addressed. In specific, the effects of adding abaca ( Musa Textilis ) as a reinforcement fibre for softwood pulp were investigated. Moreover, a handsheet former for the production of stratified sheets, the LB Multilayer Handsheet Former, was evaluated. The LB Multilayer Handsheet Former was then used to study the effects of placing selected fibres in separate layers, rather than by making homogeneous sheets from a mixture of the pulps. Handsheets of a softwood sulphate pulp with the addition of abaca fibres were made in a conventional sheet former. It was seen that the addition of abaca fibres increased the tearing resistance, fracture toughness, folding endurance and air permeance. -
Publications on Paper and Paper Research by the Staff of The
Letter vii-3 Circular LC 447 DEPARTMENT OF COMMERCE NATIONAL BUREAU OF STANDARDS WASHINGTON (August 21, 1935) PUBLICATIONS ON PAPER AND PAPER RESEARCH BY THE STAFF OF THE NATIONAL BUREAU OF STANDARDS EEPAHTMEFT CE COMMERCE HATI017AL BUREAU OF STANDARDS FASEIHGTOH Letter VI 1-3 Circular (August 21, 1935) LC 447 PUBLICATIONS OiT PAPES AID FARES .RESEARCH SI THE STAFF OF THE 1. FAT I ORAL EUSEAU OF STANDARDS GEHEKAL IFFOSI AT I OF Character of Researches The paper research of the Fa.tional Bureau of Standards consists of studies re- lated to the standardization2. of paper and the materials and processes used in its manufacture. The work on the standardization of paper leads to formulation of standards of quality, and includes, necessarily, the development of means of measuring quality. Eor research related to the manufacture of paper, the paper section is equipped with complete lahoratory and semi- commercial papermaking facilities. This is used to o’: tain information which will assist the paper maker in obtaining the desired qualities in paper at a minimum of cost, in developing new or improved paper products, and in utilizing new fibrous raw materials, parti- cularly waste materials. General3. Scope of Bureau Work The Bureau of Standards is charged with the development, construction, custody, and maintenance of reference and working standards, and their intercomparison, im- provement, and application in science, engineering, industry, and commerce. The bureau is organized in three principal groups - research and testing; commercial standardization; administrative4. work, operation of plant, and construction of lab- oratory instruments and apparatus . The following divisions comprise the research and testing group; electricity, weights and measures, heat and power, optics, chemistry, mechanics ana sound, organic and fibrous materials, metallurgy, clay and silicate products. -
High-Yield Catalysed Organosolv Pulping of Non-Wood Fiber Sources
HIGH-YIELD CATALYSED ORGANOSOLV PULPING OF NON-WOOD FIBER SOURCES by DOMTNGGUS YAWALATA Ir., Pattimura University, 1987 A THESIS SUBMITTED IN PARTIAL FULFILLMENT OF THE REQUIREMENTS FOR THE DEGREE OF MASTER OF SCIENCE in THE FACULTY OF GRADUATE STUDIES (Faculty of Forestry) (Department of Wood Science) We accept this thesis as conforming to the required standard THE UNIVERSITY OF BRITISH COLUMBIA January 1996 © Dominggus Yawalata In presenting this thesis in partial fulfilment of the requirements for an advanced degree at the University of British Columbia, I agree that the Library shall make it freely available for reference and study. I further agree that permission for extensive copying of this thesis for scholarly purposes may be granted by the head of my department or by his or her representatives. It is understood that copying or publication of this thesis for financial gain shall not be allowed without my written permission. Department of The University of British Columbia Vancouver, Canada Date DE-6 (2/88) ABSTRACT Global demand of pulp, paper and paperboard increases by the year. In contrast, shortages in wood supply were reported in many countries. On the other hand, large quantities of available non-wood fibrous materials are under-utilized. Furthermore, reduction of the environmental impacts by the pulp industries is now enforced in many parts of the world. Diversification of the raw material to non-wood fiber sources and introduction of new pulping and bleaching technologies, which are environmentally friendly, are seen as alternatives to alleviate the problems mentioned above. Therefore, in this study neutral alkali earth metal (NAEM) salt catalysed organosolv pulping was used to pulp some non- wood fibrous materials (sugarcane rind, sisal and tebu-tebu), in addition to spruce (softwood) and mangrove (hardwood). -
Paper Glossary
PAPER GLOSSARY A Abrasion Resistance Alcohol/Alcohol Substitutes The level at which paper can withstand continuous scuffing or Liquids added to the fountain solution of a printing press to rubbing. reduce the surface tension of water. Absorption Aluminum Plate The properties within paper that cause it to absorb liquids A metal press plate used for moderate to long runs in offset (inks, water, etc.) which come in contact with it. lithography to carry the image. Announcement Cards Accordion Fold Cards of paper with matching envelopes generally used for A binding term describing a method of folding paper. When social stationery, announcements, weddings, greetings, etc. unfolded it looks like the folds of an accordion. Antique Finish Acetate Proof A paper finish, usually used in book and cover papers, that has A transparent, acetate printing proof used to reproduce a tactile surface. Usually used in natural white or creamwhite anticipated print colors on a transparent acetate sheet. Also colors. called color overleaf proof. Apron Acid Free Extra space at the binding edge of a foldout, usually on Paper made in a neutral pH system, usually buffered with a French fold, which allows folding and tipping without calcium carbonate. This increases the longevity of the paper. interfering with the copy Acidity Archival Degree of acid found in a given paper substance measured by Acid free or neutral paper that includes a minimum of 2% pH level. From 0 to 7 is classified acid as opposed to 7 to 14, calcium carbonate to increase the longevity of the paper. which is classified alkaline. Artificial Parchment Against the Grain Paper produced with poorly formed formation. -
D 643 – 97 (Reapproved 2002) an American National Standard
Designation: D 643 – 97 (Reapproved 2002) An American National Standard Standard Test Method for Folding Endurance of Paper by the Schopper Tester1 This standard is issued under the fixed designation D 643; the number immediately following the designation indicates the year of original adoption or, in the case of revision, the year of last revision. A number in parentheses indicates the year of last reapproval. A superscript epsilon (e) indicates an editorial change since the last revision or reapproval. 1. Scope 3. Terminology 1.1 This test method describes the use of the Schopper type 3.1 Definitions—Definitions shall be in accordance with of folding apparatus. It is suitable for papers having a thickness Terminology D 1968 and the Dictionary of Paper.5 of 0.25 mm (0.010 in.) or less. 1.2 The procedure for the M.I.T.-type apparatus is given in 4. Significance and Use Test Method D 2176. 4.1 Folding endurance is not a measure of the foldability of 1.3 This standard does not purport to address all of the paper, but a measure of the strength of paper. In many cases, it safety concerns, if any, associated with its use. It is the is a better measure of strength than the conventional tests for responsibility of the user of this standard to establish appro- tensile strength, bursting strength, and tearing resistance. The priate safety and health practices and determine the applica- uniqueness of the folding endurance tests leads to many special bility of regulatory limitations prior to use. uses for this test method.