Light-Emitting Diode Technology for Solid-State Lighting (Paper)
Total Page:16
File Type:pdf, Size:1020Kb
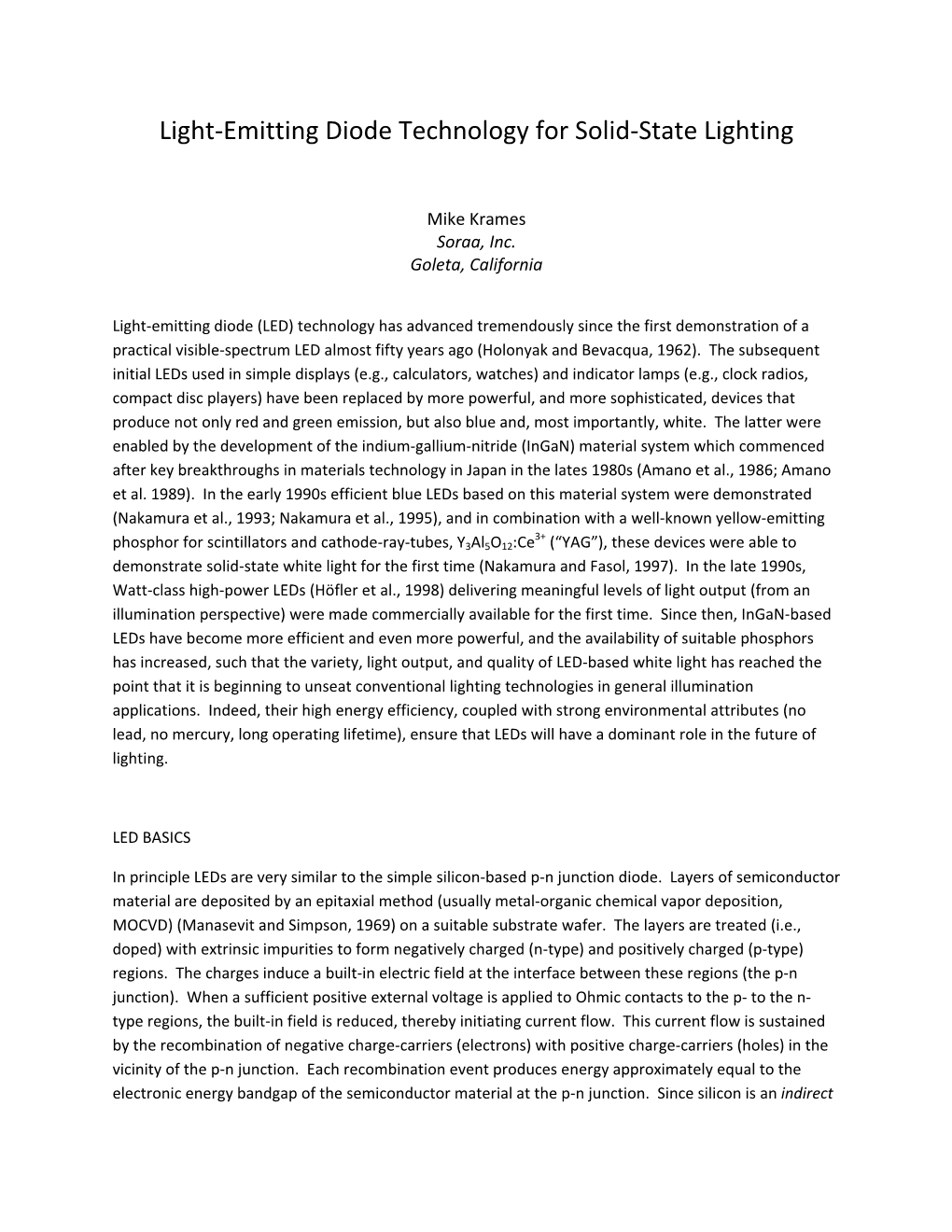
Load more
Recommended publications
-
Compact Fluorescent Light Bulbs
Compact Fluorescent Light Bulbs What is a compact fluorescent lamp (CFL) bulb? A CFL bulb is a type of fluorescent bulb that screws into a standard light socket, such as a lamp or ceiling light fixture. CFLs use much less energy and last up to 10 times longer than standard light bulbs. What is in a compact fluorescent lamp (CFL) bulb? A CFL bulb is made of glass, a ceramic and metal base, a luminous powder called phosphor, and a small amount of mercury. How much mercury is contained in a CFL bulb? Manufacturers report that the amount of mercury contained in a CFL bulb is five milligrams, which is less than two ten-thousandths of an ounce. The mercury could be in the form of an invisible vapor or in a bead the size of the period at the end of this sentence. A mercury fever thermometer contains about 100 times more mercury than a CFL bulb. Is it harmful is it to be in the room where a CFL bulb has broken? The amount of mercury vapor that is released from one broken bulb is not enough to make anyone sick. However, it is best to avoid any exposure to mercury. We recommend that you ventilate the room air to the outdoors by opening a window or a door and leave the room for a few hours before cleaning up the broken bulb. How should I clean up a broken CFL bulb? It is not necessary to hire a professional to clean up the bulb. By following the directions below, you can safely clean up a broken CFL bulb. -
Light Sources and Photodetectors for OBS® Sensors Application Note
APPLICATION NOTE APPLICATION App. Note Code: 2Q-R Written by John Downing Light Sources and Photo- detectors for OBS® Sensors ® CAMPBELL SCIENTIFIC, INC. WHENW H E N MEASUREMENTSM E A S U R E M E N T S MMATTERA T T E R Copyright (C) April 2008 Campbell Scientifi c, Inc. Light Sources and Photodetectors for OBS® Sensors Sensors that use the OBS® method have narrow- or intermediate-band illumination systems, depending on whether a laser diode (LD) or infrared-emitting diode (IRED) is used in their construction. This application note describes infrared-emitting diodes and laser diodes, as well as photodiodes, daylight fi lters, and operating spectra. Laser Diodes Laser diodes have narrow, multimode emission spectra resembling the one shown in Figure 1. The LD bandwidth is about 2 nm at half power (FWHM). They have built-in photodiodes to monitor the light output of the laser chip so that photocur- rent can be used to control the illumination of the sample. In this way, fluctuations in light power caused by sensor temperature and laser aging are virtually elimi- nated. The drift of our OBS-4 LD-based sensor, for example, is less than 2% per year of continuous operation. The two disadvantages of lasers are that they emit coherent light, which because of interferences can fluctuate in intensity in a sample volume by as much as 50%, and they are less efficient in converting electrical current to light than IREDs. Figure 1. Graph shows the relative power, transmission and responsivity of a laser diode. Laser diodes have narrow, multimode emission spectra. -
Article Soot Photometer Using Supervised Machine Learning
Atmos. Meas. Tech., 12, 3885–3906, 2019 https://doi.org/10.5194/amt-12-3885-2019 © Author(s) 2019. This work is distributed under the Creative Commons Attribution 4.0 License. Classification of iron oxide aerosols by a single particle soot photometer using supervised machine learning Kara D. Lamb1,2 1Cooperative Institute for Research in Environmental Sciences, University of Colorado Boulder, Boulder, CO, USA 2NOAA Earth System Research Laboratory Chemical Sciences Division, Boulder, CO, USA Correspondence: Kara D. Lamb ([email protected]) Received: 15 March 2019 – Discussion started: 22 March 2019 Revised: 20 June 2019 – Accepted: 21 June 2019 – Published: 15 July 2019 Abstract. Single particle soot photometers (SP2) use laser- each class are compared with the true class for those particles induced incandescence to detect aerosols on a single particle to estimate generalization performance. While the specific basis. SP2s that have been modified to provide greater spec- class approach performed well for rBC and Fe3O4 (≥ 99 % tral contrast between their narrow and broad-band incandes- of these aerosols are correctly identified), its classification of cent detectors have previously been used to characterize both other aerosol types is significantly worse (only 47 %–66 % refractory black carbon (rBC) and light-absorbing metallic of other particles are correctly identified). Using the broader aerosols, including iron oxides (FeOx). However, single par- class approach, we find a classification accuracy of 99 % for ticles cannot be unambiguously identified from their incan- FeOx samples measured in the laboratory. The method al- descent peak height (a function of particle mass) and color lows for classification of FeOx as anthropogenic or dust-like ratio (a measure of blackbody temperature) alone. -
Semiconductor Light Sources
Laser Systems and Applications Couse 2020-2021 Semiconductor light sources Prof. Cristina Masoller Universitat Politècnica de Catalunya [email protected] www.fisica.edu.uy/~cris SCHEDULE OF THE COURSE Small lasers, biomedical Semiconductor light sources lasers and applications . 1 (11/12/2020) Introduction. 7 (19/1/2021) Small lasers. Light-matter interactions. 8 (22/1/2021) Biomedical lasers. 2 (15/12/2020) LEDs and semiconductor optical amplifiers. Laser models . 3 (18/12/2020) Diode lasers. 9 (26/1/2021) Laser turn-on and modulation response. Laser Material Processing . 10 (29/1/2021) Optical injection, . 4 (22/12/2020) High power laser optical feedback, polarization. sources and performance improving novel trends . 11 (2/2/2021) Students’ . 5 (12/1/2021) Laser-based presentations. material macro processing. 12 (5/2/2021) Students’ . 6 (15/1/2020) Laser-based presentations. material micro processing. 9/2/2021: Exam Lecturers: C. Masoller, M. Botey 2 Learning objectives . Understand the physics of semiconductor materials and the electron-hole recombination mechanisms that lead to the emission of light. Learn about the operation principles of light emitting diodes (LEDs) and semiconductor optical amplifiers (SOAs). Become familiar with the operation principles and characteristics of laser diodes (LDs). 3 Outline: Semiconductor light sources . Introduction . Light-matter interactions in semiconductor materials . Light Emitting Diodes (LEDs) . Semiconductor optical amplifiers (SOAs) . Laser diodes (LDs) The start of the laser diode story: the invention of the transistor Nobel Prize in Physics 1956 “For their research on semiconductors and their discovery of the transistor effect”. The invention of the transistor in 1947 lead to the development of the semiconductor industry (microchips, computers and LEDs –initially only green, yellow and red). -
Introduction 1
1 1 Introduction . ex arte calcinati, et illuminato aeri [ . properly calcinated, and illuminated seu solis radiis, seu fl ammae either by sunlight or fl ames, they conceive fulgoribus expositi, lucem inde sine light from themselves without heat; . ] calore concipiunt in sese; . Licetus, 1640 (about the Bologna stone) 1.1 What Is Luminescence? The word luminescence, which comes from the Latin (lumen = light) was fi rst introduced as luminescenz by the physicist and science historian Eilhardt Wiede- mann in 1888, to describe “ all those phenomena of light which are not solely conditioned by the rise in temperature,” as opposed to incandescence. Lumines- cence is often considered as cold light whereas incandescence is hot light. Luminescence is more precisely defi ned as follows: spontaneous emission of radia- tion from an electronically excited species or from a vibrationally excited species not in thermal equilibrium with its environment. 1) The various types of lumines- cence are classifi ed according to the mode of excitation (see Table 1.1 ). Luminescent compounds can be of very different kinds: • Organic compounds : aromatic hydrocarbons (naphthalene, anthracene, phenan- threne, pyrene, perylene, porphyrins, phtalocyanins, etc.) and derivatives, dyes (fl uorescein, rhodamines, coumarins, oxazines), polyenes, diphenylpolyenes, some amino acids (tryptophan, tyrosine, phenylalanine), etc. + 3 + 3 + • Inorganic compounds : uranyl ion (UO 2 ), lanthanide ions (e.g., Eu , Tb ), doped glasses (e.g., with Nd, Mn, Ce, Sn, Cu, Ag), crystals (ZnS, CdS, ZnSe, CdSe, 3 + GaS, GaP, Al 2 O3 /Cr (ruby)), semiconductor nanocrystals (e.g., CdSe), metal clusters, carbon nanotubes and some fullerenes, etc. 1) Braslavsky , S. et al . ( 2007 ) Glossary of terms used in photochemistry , Pure Appl. -
Operating the Pulsed Laser Diode SPL LL90 3 Application Note
Operating the Pulsed Laser Diode SPL LL90_3 Application Note Introduction Optical peak power The SPL LL90_3 is a hybrid laser module. As shown in figure 2 the peak current and Additional to the laser chip the module therefore optical peak power is adjusted by contains two capacitors and a MOSFET the applied charge voltage. The SPL LL90_3 which act as a driver stage. The two typically delivers 70 W at 18.5 V (30 ns, 1 capacitors are connected in parallel to sum kHz). their individual capacitance of 47 nF. The The maximum rating of peak power is 80 W. emission wavelength is 905 nm. The By increasing of pulse repetition frequency specified optical peak power is 70 W. the peak optical power will be slightly decreased (as shown in fig 2). Principal of operation The capacitors are charged using a constant DC voltage. Each time the gate of the MOSFET is triggered, the capacitors are discharged via the laser chip leading to a short and high-amp current pulse. These high-amp current pulses are required to obtain the high peak power laser emission (at charge voltage of 18.5V a current pulse of up to 30A is possible) The pin configuration of the SPL LL90_3 laser diode is as follows: Pin 1: Trigger signal for the MOSFET gate Pin 2: Charge voltage Pin 3: Ground Figure 1: Hybrid pulsed laser diode SPL Variation of optical peak power LL90_3 with integrated driver stage. Figure 2: with charge voltage (pulse width 30 ns, PRF 1 kHz and 25kHz, gate voltage 15 V) for SPL LL90_3 using the MOSFET driver 3 Elantec EL7104C. -
VCSEL Pulse Driver Designs for Tof Applications
Vixar Application Note VCSEL Pulse Driver Designs for ToF Applications 1 Introduction ............................................................................................................................. 2 2 Design Theory ......................................................................................................................... 2 2.1 Schematic Components .................................................................................................... 2 2.2 Design Inductance ............................................................................................................ 3 2.3 Rise and Fall Time ........................................................................................................... 5 2.4 Timing Delay.................................................................................................................... 5 3 Low Power Driver Design ...................................................................................................... 5 4 High Power Driver Design...................................................................................................... 7 4.1 GaN FETs ......................................................................................................................... 7 4.2 Gate Drivers ..................................................................................................................... 7 5 VCSEL Performance .............................................................................................................. 8 6 Conclusions -
Fluorescent Lighting About the Guide
RESPONSIBLE PURCHASING GUIDE fluorescent lighting About the Guide The Responsible Purchasing Guide for Lighting is published by the Responsible Purchasing Network in print, as a PDF file, and on the web. Print and PDF copies are available to the public for purchase. The online edi- tion includes additional resources available to members of the Responsible Purchasing Network, including: searchable product listings, multiple policy and specification samples, comparisons of standards, and related documents. Visit www.ResponsiblePurchasing.org to purchase a copy or to access the members-only web- based edition of the Guide. Responsible Purchasing Network © 2007 About the Responsible Purchasing Network The Responsible Purchasing Network (RPN) was founded in 2005 as the first national network of procurement-related professionals dedicated to socially and environmentally responsible purchasing. RPN is a program of the Center for a New American Dream (www.newdream.org) and guided by a volunteer Steering Committee of leading procurement stakeholders from government, industry, educational institutions, standards setting organizations, and non-profit advocacy organizations. Acknowledgements The Responsible Purchasing Network (RPN) would like to thank the following people for assisting with the development of this Guide. Their expertise helped to ensure quality and accuracy, though RPN alone accepts responsibility for any errors or omissions. Affiliations listed below were current when input was provided to RPN and are listed for identification purposes -
Speed of Light with Nanosecond Pulsed 650 Nm Diode Laser M
Speed of Light with Nanosecond Pulsed 650 nm Diode Laser M. Gallant May 23, 2008 The speed of light has been measured many different ways using many ingenious methods. The following note describes a method which is conceptually very easy to understand and fairly easy to implement. The technique is the simple time-of-flight optical pulse delay method using a fairly short (nanosecond) optical pulse and an oscilloscope with bandwidth between 50 - 100 MHz. THE LASER Common low power laser pointers, typically emit at a wavelength of 650 nm and operate from two to four 1.5 V button cells. Many of these lasers can be easily extracted from the pointer assembly and pulse-modulated to several hundred megahertz. The laser used here was removed from a low power (< 5mW) laser pointer assembly from a popular retail outlet. GENERATION OF SHORT OPTICAL PULSES The laser is prebiased below threshold, at 5 - 10 mA current (threshold current for the laser used here is 24 mA) using an inductor as a bias insertion element. A short (< 5 ns) electrical pulse modulates the laser. Since a very low duty cycle is used for pulsing the laser, fairly high current pulses are possible without degrading the laser. The actual forward current and voltage achieved during the drive pulse are dependent on the details of the I-V characteristic of the specific laser used, but are typically in the range of 50 - 100 mA and 6 - 10 V respectively. The short electrical pulse is generated using a simple avalanche transistor circuit. Due to the high frequency content of the short pulse, the actual shape of the current pulse driving the laser will depend on the circuit components (series resistors etc.) and parasitic electrical effects (series inductance of connection wires etc.) The circuit has been described by Jim Williams in a Linear Technology Measurement and Control Circuit Collection and has many other uses. -
Skylighter™ Brand Fluorescent Strobe Lighting
Skylighter™ Brand Fluorescent Strobe Lighting Operator’s Manual Skylighter CFF2 Skylighter CFF4 Skylighter CFF8 OPERATOR MANUAL FOR SKYLIGHTER Skylighter CFF2 Skylighter CFF4 Skylighter CFF8 Thank you for selecting the Photogenic Professional Skylighter CFF series. The CFF series incorporates the newest electronic components, lamps, reflectors, and diffusion panels providing improved lighting distribution and control. These products are built for the demanding operational needs of the professional photographer and it is our expectation that your Skylighter CFF will provide you with years of dependable service. INTRODUCTION The Skylighter CFF series are an extremely diffused light head and require an external power supply. They have one, two, or four professional, plug-in, linear flashtubes, and one, two, or four non-adjustable, linear, fluorescent modeling lamps. The Skylighter CFF series are stand mounted on a strong, rotating yoke, but may be ceiling hung, as required. Before using your new Skylighter CFF for the first time, please read this manual carefully and acquaint yourself with the controls and features. In this way, you can quickly get the greatest benefit from your new unit and maintain an efficient and safe operation. SAFETY PRECAUTIONS Despite the measures that have been taken to make electronic flash equipment safe, it must be recognized that high voltages and high temperatures do exist within the power supply / lighting unit. Certain precautions must be observed in handling the unit. Contact with internal high voltage may result in severe injury or death. 1. Before installing or removing the flashtubes and modeling lamps, be sure this appliance is turned off, cooled and unplugged from AC power source and external power supply. -
2. Making Fires Burn Or Go out 1: Introduction to the Fire Triangle
2. Making Fires Burn or Go Out 1: Introduction to the Fire Triangle Lesson Overview: In this activity, students describe and organize what they already know Subjects: Science, Mathematics, Writing, about fire so it fits into the conceptual model of Speaking and Listening, Health and the Fire Triangle. They examine the geometric Safety stability of a triangle and how that property Duration: one half-hour session applies to fire. Group size: Whole class. Students work in groups of 2-3. Lesson Goal: Increase students’ understanding of Setting: Indoors how fires burn and why they go out. Vocabulary: Fire Triangle, fuel, heat, ignition, oxygen, model Objectives: • Students can construct a triangle out of toothpicks and gumdrops, and can label its legs with the three components of the Fire Triangle. • Students can demonstrate that removing one side of the triangle makes it collapse. • Students can identify the component(s) of the Fire Triangle that are removed in various scenarios, and explain how this makes the fire go out. Standards: 1st 2nd 3rd 4th 5th CCSS Writing 2, 7, 8 2, 7, 8 2, 7, 10 2,7, 9, 10 2,7, 9, 10 Speaking/Listening 1, 2, 4, 6 1, 2, 4, 6 1, 2, 4, 6 1, 2, 4, 6 1, 2, 4, 6 1, 2, 3, 4, Language 1, 2, 4, 6 1, 2, 4, 6 6 1, 2, 3, 4, 6 1, 2, 3, 4, 6 MP.4, MP.4, MP.4, MP.4, Math MP.5 MP.5, MP.5 MP.5 MP.4, MP.5 Matter and Its PS1.A, NGSS Interactions PS1.B PS1.B From Molecules to Organisms: Structure/Processes LS1.C Engineering Design ETS1.B ETS1.B EEEGL Strand 1 A, B, C, E, F, G A, B, C, E, F, G Teacher Background: This activity explores the chemistry of combustion as described by a conceptual model called the Fire Triangle. -
Fluorescent Lamp
FLUORESCENT LAMP SELECTION GUIDE FEBRUARY 2015 Keystone presents the easiest solution for high performance, high efficiency lamps. With long life and exceptional reliability, Keystone energy efficient lamps provide the same high quality you have come to expect from Keystone. When installing Keystone lamps and ballasts together, you experience the industry’s best warranty program and a lighting system that is guaranteed to perform. FEATURES AND BENEFITS • High Color Rendering Index • Lumen Maintenance of Up to 94% • Eco-Friendly and TCLP Compliant • Energy Efficient • Long Life: Up to 36,000 Hours • Reduced Maintenance and Disposal Costs KEYSTONE FLUORESCENT SYSTEM WARRANTY Keystone Standard Lamp Warranty Period Keystone Fluorescent System Warranty Period 24 months 36 months (Lamp Portion) We proudly stand behind all of our products. By pairing a Keystone lamp with a Keystone ballast, customers are eligible for a 36-month Keystone Fluorescent System Warranty. The Keystone Fluorescent System Warranty extends the standard 24-month warranty included with our lamps by an additional 12 months. In the event that you need to utilize our warranty, we’ll work with you to make it easy and hassle-free. Visit www.keystonelamp.com for more details. LIGHTING COLOR GUIDE Warm Light Neutral Light Cool Light Warm White Color, Warm Tones Neutral to Bright White Color, Neutral or Cooler Tones Cool White Color, Cooler Daylight Tones 2600K 3500K 4100K 5000K 6500K ELECTRICAL SPECIFICATIONS T5 Linear Rated Average Life3 Nominal Base Nominal Case Color Temp. Initial