Open Manoharan 999805608.Pdf
Total Page:16
File Type:pdf, Size:1020Kb
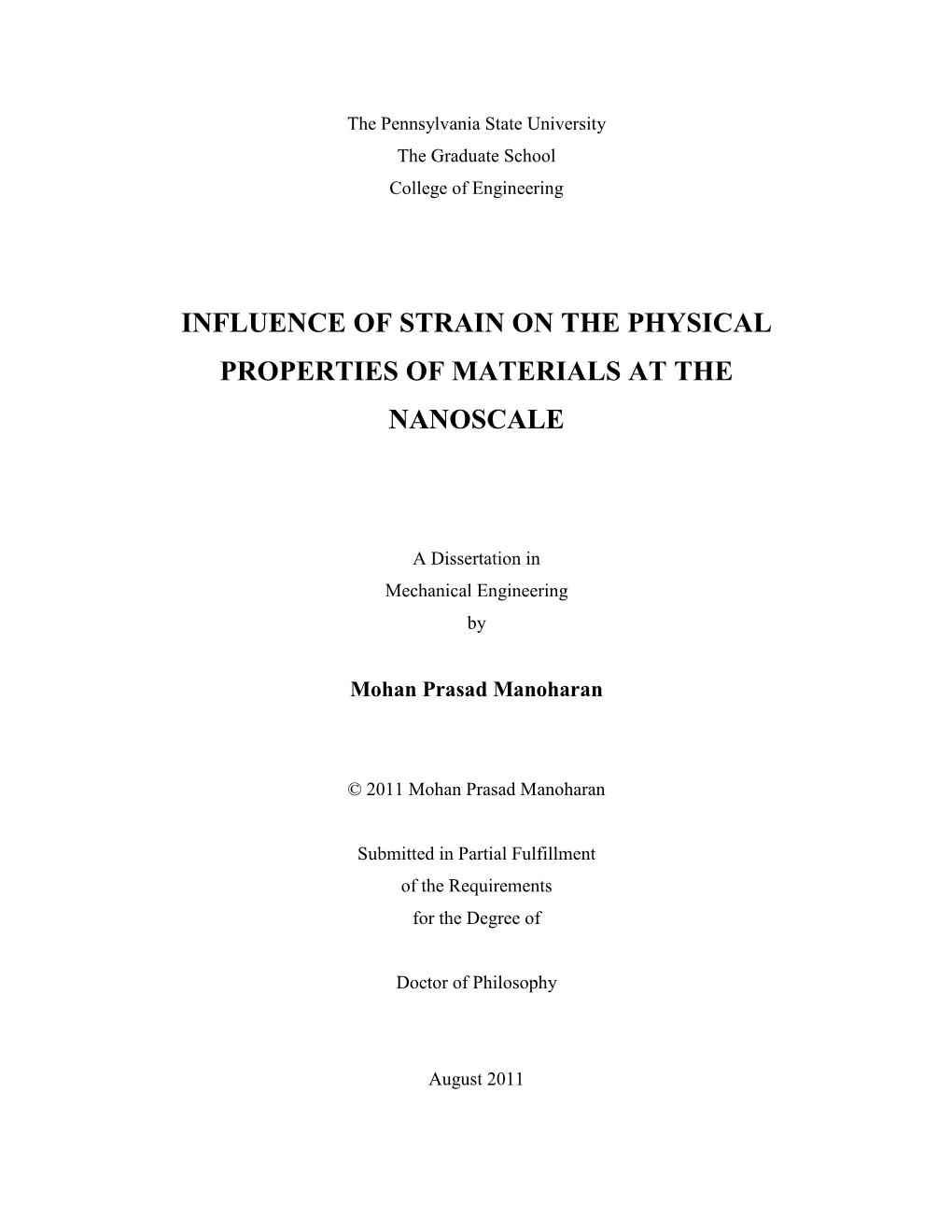
Load more
Recommended publications
-
The Laser Generation Threshold Characteristics of a Colloidal Solution of Gold and Platinum Nanoparticles with Rodamine 6G
View metadata, citation and similar papers at core.ac.uk brought to you by CORE provided by Tomsk State University Repository 370 17th INTERNATIONAL CONFERENCE ON MICRO/NANOTECHNOLOGIES AND ELECTRON DEVICES EDM 2016 The Laser Generation Threshold Characteristics of a Colloidal Solution of Gold and Platinum Nanoparticles with Rodamine 6G Valeriy A. Donchenko1,2, Mikhail M. Zinoviev1, Alexey A. Zemlyanov2, Vladimir A. Kharenkov1,2, Anna N. Panamaryova3 1National Research Tomsk State University, Tomsk, Russia 2Siberian Physical Technical Institute, Tomsk, Russia 3 National Research Tomsk Polytechnic University, Tomsk, Russia Abstract – In the work the spectral-energy characteristics of or more orders greater than the density of the incident wave stochastic (non-resonator) laser generation of a thin layer of power. organic dye Rhodamine 6G solution with the addition of gold This increases the number of excited molecules within and platinum nanoparticles in the form of a colloidal solution these regions. Due to the Purcell effect [6-8] it is also in ethanol have been experimentally investigated. It has been experimentally established that the generation thresholds possible to increase the speed of active medium molecules are reduced by two orders when adding nanoparticles to the conversions from the excited level into the primary. As active medium. It is shown that the use of nanoparticles having a result, during the agitation action, a large number of a plasmon absorption band in the region of the agitation stimulated emissions of photons appear. This should lead to radiation does not lead to a significant change of the active a decrease in the generation and intensity of emission of the medium generation thresholds. -
A Review of the Use of Nanoparticle Tracking Analysis (NTA)
WHITEPAPER Nanoscale Material Characterization: a Review of the use of Nanoparticle Tracking Analysis (NTA) PARTICLE SIZE Summary PARTICLE This white paper describes the central role of high resolution particle size CONCENTRATION and concentration measurement nanoparticle research. The technique of FLUORESCENCE Nanoparticle Tracking Analysis (NTA) is described and compared to other DETECTION - DELETED characterization methodologies, and comparative papers are cited. A wide range of application studies is then summarized with specific reference to the use and value of NTA. For those seeking a full listing of NTA experience to date by application type, the NanoSight publication “Nanoparticle Tracking Analysis - A review of applications and usage 2010 - 2012, (Carr B and Wright M (2013)) and its successors provides a detailed catalogue. This item is available from your local Malvern Instruments representative or email [email protected]. Malvern Instruments Worldwide Sales and service centres in over 65 countries www.malvern.com/contact ©2017 Malvern Instruments Limited WHITEPAPER Introduction Nanoscale materials, in the form of nanoparticles, are playing an important and growing role across a range of different applications and industries which seek to exploit the unique properties exhibited by these materials, such as their very high surface area to volume ratio and high number. The overall properties and stability of many manufactured products often depends upon the ability to produce particle populations within fine tolerances, without contaminants or aggregates. The concentration of particles within a suspension is another factor that may have an effect upon the desired outcome of the product. It is clear then that there is a real need to characterize a variety of different properties when analyzing nanoparticles, in order to understand the relationship between the formulation and the overall bulk characteristics of the materials (Fedotov, 2011). -
Interactions of Newly Synthesized Platinum Nanoparticles with ICR-191 and Their Potential Application
www.nature.com/scientificreports OPEN Interactions of newly synthesized platinum nanoparticles with ICR- 191 and their potential application Received: 26 November 2018 Agnieszka Borowik1, Rafal Banasiuk2, Natalia Derewonko3, Michal Rychlowski3, Accepted: 4 March 2019 Marta Krychowiak-Masnicka 2, Dariusz Wyrzykowski4, Magdalena Ziabka5, Published: xx xx xxxx Anna Woziwodzka1, Aleksandra Krolicka 2 & Jacek Piosik 1 One of the greatest challenges of modern medicine is to fnd cheaper and easier ways to produce transporters for biologically active substances, which will provide selective and efcient drug delivery to the target cells, while causing low toxicity towards healthy cells. Currently, metal-based nanoparticles are considered a successful and viable solution to this problem. In this work, we propose the use of novel synthesis method of platinum nanoparticles (PtNPs) connected with their precise biophysical characterization and assessment of their potential toxicity. To work as an efcient nanodelivery platform, nanoparticles should interact with the desired active compounds spontaneously and non-covalently. We investigated possible direct interactions of PtNPs with ICR-191, a model acridine mutagen with well-established biophysical properties and mutagenic activity, by Dynamic Light Scattering, fuorescence spectroscopy, and Isothermal Titration Calorimetry. Moreover, to determine the biological activity of ICR-191-PtNPs aggregates, we employed Ames mutagenicity test, eukaryotic cell line analysis and toxicity test against the model -
Controllable ALD Synthesis of Platinum Nanoparticles by Tuning
Journal of Physics D: Applied Physics PAPER Related content - Nucleation and growth process of atomic Controllable ALD synthesis of platinum layer deposition platinum nanoparticles on strontium titanate nanocuboids Chuandao Wang, Linhua Hu, Kenneth nanoparticles by tuning different synthesis Poeppelmeier et al. parameters - Atomic layer deposition of Pd and Pt nanoparticles for catalysis: on the mechanisms of nanoparticle formation To cite this article: Chuandao Wang et al 2017 J. Phys. D: Appl. Phys. 50 415301 Adriaan J M Mackus, Matthieu J Weber, Nick F W Thissen et al. - Sub-nanometer dimensions control of core/shell nanoparticles prepared by atomic layer deposition View the article online for updates and enhancements. M J Weber, M A Verheijen, A A Bol et al. This content was downloaded from IP address 129.105.122.65 on 04/12/2017 at 17:10 IOP Journal of Physics D: Applied Physics Journal of Physics D: Applied Physics J. Phys. D: Appl. Phys. J. Phys. D: Appl. Phys. 50 (2017) 415301 (9pp) https://doi.org/10.1088/1361-6463/aa8709 50 Controllable ALD synthesis of platinum 2017 nanoparticles by tuning different synthesis © 2017 IOP Publishing Ltd parameters JPAPBE Chuandao Wang1,2,4, Linhua Hu2, Yuyuan Lin1,2, Kenneth Poeppelmeier2, Peter Stair2,3 and Laurence Marks1 415301 1 Department of Materials Science and Engineering, Northwestern University, 2220 North Campus Drive, Evanston, IL 602083108, United States of America C Wang et al 2 Department of Chemistry, Northwestern University, 2145 Sheridan Road, Evanston, IL 602083113, United States of America 3 Chemical Sciences and Engineering Division, Argonne National Laboratory, 9700 South Cass Avenue, Argonne, IL 60439, United States of America Printed in the UK Email: [email protected] Received 17 July 2017, revised 11 August 2017 JPD Accepted for publication 18 August 2017 Published 15 September 2017 10.1088/1361-6463/aa8709 Abstract Pt nanoparticles were successfully deposited using three different atomic layer deposition (ALD) methods, e.g. -
Silver Based Nanoparticles Synthesis and Characterization of Silver
Silver-based nanoparticles Synthesis and characterization of bimetallic silver- platinum and silver-gold nanoparticles Dissertation Zur Erlangung des akademischen Grades eines Doktors der Naturwissenschaften Dr. rer. nat. vorgelegt von Viktoria Grasmik Fakultät für Chemie Institut für Anorganische Chemie Universität Duisburg-Essen 2018 II Die vorliegende Arbeit wurde im Zeitraum von April 2015 bis Mai 2018 im Arbeitskreis von Prof. Dr. Matthias Epple am Institut der Anorganischen Chemie der Universität Duisburg-Essen angefertigt. Gutachter: Prof. Dr. Matthias Epple Prof. Dr. Malte Behrens Vorsitzender: PD Dr. Holger Somnitz Tag der Disputation: 04.09.2018 III IV List of contents List of contents Index of abbreviations ................................................................................... VIII Abstract ............................................................................................................... X Deutscher Abstract ............................................................................................ XI 1. Introduction ..................................................................................................... 1 2. Theoretical background .................................................................................. 4 2.1 Colloids, nanoclusters, and nanoparticles – a definition .................................................. 4 2.2 Stabilization of nanoparticles ............................................................................................ 5 2.3 Synthesis routes and crystallization -
Size-Dependent Activity and Selectivity of Carbon Dioxide Photocatalytic Reduction Over Platinum Nanoparticles
ARTICLE DOI: 10.1038/s41467-018-03666-2 OPEN Size-dependent activity and selectivity of carbon dioxide photocatalytic reduction over platinum nanoparticles Chunyang Dong1, Cheng Lian1, Songchang Hu1, Zesheng Deng1, Jianqiu Gong1, Mingde Li2, Honglai Liu1, Mingyang Xing 1 & Jinlong Zhang 1 fi 1234567890():,; Platinum nanoparticles (Pt NPs) are one of the most ef cient cocatalysts in photocatalysis, and their size determines the activity and the selectivity of the catalytic reaction. Never- theless, an in-depth understanding of the platinum’s size effect in the carbon dioxide pho- tocatalytic reduction is still lacking. Through analyses of the geometric features and electronic properties with variable-sized Pt NPs, here we show a prominent size effect of Pt NPs in both the activity and selectivity of carbon dioxide photocatalytic reduction. Decreasing the size of Pt NPs promotes the charge transfer efficiency, and thus enhances both the carbon dioxide photocatalytic reduction and hydrogen evolution reaction (HER) activity, but leads to higher selectivity towards hydrogen over methane. Combining experimental results and theoretical calculations, in Pt NPs, the terrace sites are revealed as the active sites for methane generation; meanwhile, the low-coordinated sites are more favorable in the com- peting HER. 1 Key Laboratory for Advanced Materials and Institute of Fine Chemicals, School of Chemistry & Molecular Engineering, East China University of Science and Technology, 130 Meilong Road, Shanghai 200237, P. R. China. 2 Department of Chemistry and Key Laboratory for Preparation and Application of Ordered Structural Materials of Guangdong Province, Shantou University, Shantou 515063, P. R. China. These authors contributed equally: Chunyang Dong, Cheng Lian. -
Colloidal Platinum (Nano) and Acetyl Tetrapeptide-17 Colloidal Platinum (Nano)
SCCS/1630/21 Final Opinion Scientific Committee on Consumer Safety SCCS OPINION ON Platinum (nano), Colloidal Platinum (nano) and Acetyl tetrapeptide-17 Colloidal Platinum (nano) The SCCS adopted this document at its plenary meeting on 24-25 June 2021 SCCS/1630/21 Final Opinion Opinion on Platinum (nano) ___________________________________________________________________________________________ ACKNOWLEDGMENTS Members of the Working Group are acknowledged for their valuable contribution to this Opinion. The members of the Working Group are: The SCCS members: Dr U. Bernauer (Chairperson) Dr L. Bodin Prof. Q. Chaudhry Prof. P.J. Coenraads Prof. M. Dusinska Dr E. Gaffet Prof. E. Panteri Dr C. Rousselle Dr M. Stepnik Dr S. Wijnhoven (Rapporteur) The SCHEER members Dr W.H. de Jong External experts Dr N. von Goetz All Declarations of Working Group members are available on the following webpage: Register of Commission expert groups and other similar entities This Opinion has been subject to a commenting period of eight weeks after its initial publication (from 16 April until 14 June 2021). There were no comments received. _________________________________________________________________________________ 2 SCCS/1630/21 Final Opinion Opinion on Platinum (nano) ___________________________________________________________________________________________ 1. ABSTRACT The SCCS concludes the following: (1) In view of the above, and taking into account the scientific data provided, does the SCCS consider the nanomaterials A (Platinum and Colloidal Platinum -
Platinum and Iron Oxide Working Together Get the Job Done 16 September 2015
Platinum and iron oxide working together get the job done 16 September 2015 dioxide (CO2), hydrogen gas (H2) is oxidized to water (H2O). These reactions are also possible without platinum, but they can occur at much lower temperatures in the presence of platinum particles. "We used to believe that these chemical reactions occur right on top of the platinum particles. But our pictures clearly show that the iron oxide really does the job", says Professor Gareth Parkinson. For Left: Tiny platinum nanoparticles on an iron oxide years he has been studying the behaviour of tiny surface. center: H2 gas leads to trenches in the surface. particles on metal-oxide surfaces together with right: O2 gas causes additional iron oxide islands to Professor Ulrike Diebold (both TU Vienna). Now the grow. team could show that the oxygen needed for the chemical reactions does not originate from the surrounding atmosphere but from the iron oxide below. Scientists at the Vienna University of Technology (TU Wien) have figured out how a platinum catalyst works. Its remarkable properties are not just due to the platinum, the iron-oxide substrate beneath also plays a role. Platinum is a great catalyst and can be used for many different applications. It's expensive stuff though, so tiny platinum nanoparticles sitting on cheap metal oxide materials are used to convert harmful carbon monoxide into carbon dioxide. Using scanning tunnelling microscopes, scientists at TU Vienna have now been able to image the catalytic behaviour of platinum sitting on iron-oxide, which allowed them to explain the process on an atomic scale. -
A Clean-Green Synthesis of Platinum Nanoparticles Utilizing a Pernicious Weed Lantana ( Lantana Camara )
American Journal of Engineering and Applied Sciences Original Research Paper A Clean-Green Synthesis of Platinum Nanoparticles Utilizing a Pernicious Weed Lantana ( Lantana Camara ) 1,2 Musthafa O. Mavukkandy, 1Sudip Chakraborty, 2Tasneem Abbasi and 2Shahid A. Abbasi 1Centre for Pollution Control and Environmental Engineering, Pondicherry University, India 2iWater, Masdar Institute of Science and Technology, UAE Article history Abstract: A rapid, reproducible single step method is proposed for Received: 13-01-2016 synthesizing platinum nanoparticles using an invasive weed lantana Revised: 15-01-2016 (Lantana camara , L). The method involves mixing of platinum (VI) Accepted: 25-01-2016 solution, lantana leaf extract and ascorbic acid in appropriate Corresponding Author: concentrations and keeping the mixture at 95 °C for 8 min. The Musthafa O. Mavukkandy collective action of ascorbic acid and leaf extract reduced the Centre for Pollution Control and chloroplatinic acid to platinum nanoparticles and leaf extract then Environmental Engineering, served the additional purpose of stabilizing the nanoparticles. The Pondicherry University, India and resulting nanoparticles have an average size of 35 nm and crystallized iWater, Masdar Institute of in face centred cubic symmetry. The course of the synthesis was Science and Technology, UAE trekked by UV-visible spectrophotometry and the characterization of Email: [email protected] the nanoparticles was done with scanning electron microscopy and confocal laser Raman spectroscopy. Particle size distribution was estimated by dynamic light scattering and the crystal structure was determined by XRD. The purity of the product was checked by EDAX. Keywords: Biomimetic Synthesis, Green Synthesis, Platinum Nanoparticle, Weed Utilization Introduction development of novel green syntheses approaches which do not involve the use of hazardous chemicals Nanoparticles of noble metals, such as gold, silver (Ankamwar et al ., 2005; Roy and Barik, 2010). -
Gold, Silver and Platinum Nanoparticles: from New Synthetic
Adrián Fernández Lodeiro Gold, Silver and Platinum Nanoparticles: From New Synthetic Routes to Sensing, Catalysis and Bio-Applications Dissertação para a obtenção do Grau de Doutor em Química Sustentável Orientador Doutor José Luís Capelo Martínez Professor Associado com Agregação Faculdade de Ciências e Tecnologia (FCT) Universidade Nova de Lisboa (UNL), Portugal Co-Orientadores Doutora Julia Lorenzo Rivera Visiting Professor, Universitat Autònoma de Barcelona, UAB, Spain Doutor Hugo Miguel Baptista Carreira dos Santos Investigador Auxiliar, FCT Investigator Programme, FCT, UNL, Portugal Júri Presidente Prof. Doutor Manuel Luís De Magalhães Nunes Da Ponte Vogais Prof. Doutor Gilberto Paulo Peixoto Igrejas Prof. Doutor José Luís Capelo Martínez Prof. Doutor Jorge Pérez Juste Doutora Elisabete De Jesus Oliveira Marques March - 2019 Adrián Fernández Lodeiro Gold, Silver and Platinum Nanoparticles: From New Synthetic Routes to Sensing, Catalysis and Bio-Applications Dissertação para a obtenção do Grau de Doutor em Química Sustentável (Sustainable Chemistry) Orientador Doutor José Luís Capelo Martínez Professor Associado com Agregação Faculdade de Ciências e Tecnologia (FCT) Universidade Nova de Lisboa (UNL), Portugal Co-Orientadores Doutora Julia Lorenzo Rivera Visiting Professor, Universitat Autònoma de Barcelona, UAB, Spain Doutor Hugo Miguel Baptista Carreira dos Santos Investigador Auxiliar, FCT Investigator Programme, FCT, UNL, Portugal Júri Presidente Prof. Doutor Manuel Luís De Magalhães Nunes Da Ponte Vogais Prof. Doutor Gilberto -
South Carolina Researchers Study the Environmental Behaviors of Platinum Nanoparticles
South Carolina Researchers Study the Environmental Behaviors of Platinum Nanoparticles Researchers from the Arnold School of Public Health’s Environmental Health Sciences Department and the South Carolina SmartState Center for Environmental Nanoscience and Risk at the University of South Carolina have collaborated with a scientist from the National Center for Earth and Environmental Nanotechnology Infrastructure to study the synthesis, characterization, and environmental behaviors of platinum nanoparticles. The resulting paper was published in the Journal of Colloid and Interface Science. The release of platinum group elements, including platinum nanoparticles, has been increasing over recent decades. However, few studies have investigated the fate, behavior and effects of these nanoparticles in environmental media. With this study, the researchers report a protocol for the synthesis of five different sizes (8.5 ± 1.2, 10.3 ± 1.3, 20.0 ± 4.8, 40.5 ± 4.1, and 70.8 ± 4.2 nm) of monodispersed citrate- and polyvinylpyrrolidone (PVP)-coated PtNPs, together with a characterization of their behaviors in relevant biological and toxicological media. In general, platinum nanoparticle sizes measured using dynamic light scattering, field flow fractionation, single-particle inductively-coupled plasma-mass spectroscopy, transmission electron microscopy and atomic force microscopy, were all in good agreement when their sizes were larger than the size detection limits of each analytical technique. The authors found slight differences in sizes measured were attributable to differences in analytical techniques, measuring principles, nanoparticle shape and nanoparticle permeability. The thickness of the PVP layer increased (from 4.4 to 11.35 nm) with increases in NP size. Further, the critical coagulation concentration of cit-platinum nanoparticles was independent of nanoparticle size, possibly due to differences in surface charges as a function of nanoparticle size. -
From Cellulose to Cellulose Nanofibrils—A Comprehensive
materials Review From Cellulose to Cellulose Nanofibrils—A Comprehensive Review of the Preparation and Modification of Cellulose Nanofibrils 1, 1, 1 1 1,2, 1,2 1 Tan Yi y, Hanyu Zhao y, Qi Mo , Donglei Pan , Yang Liu *, Lijie Huang , Hao Xu , Bao Hu 1 and Hainong Song 3 1 College of Light Industry and Food Engineering, Guangxi University, Junwu Rd, Xixiangtang District, Nanning 530004, China; [email protected] (T.Y.); [email protected] (H.Z.); [email protected] (Q.M.); [email protected] (D.P.); [email protected] (L.H.); [email protected] (H.X.); [email protected] (B.H.) 2 Guangxi Key Laboratory of Clean Pulp & Papermaking and Pollution Control, Junwu Rd, Xixiangtang District, Nanning 530004, China 3 Guangxi Bossco Environmental Protection Technology Co., Ltd., 12 Kexing Road, High-tech Zone, Nanning 530012, China; [email protected] * Correspondence: [email protected]; Tel.: +86-155-7832-3385 Co-first author. y Received: 24 September 2020; Accepted: 30 October 2020; Published: 10 November 2020 Abstract: This review summarizes the preparation methods of cellulose nanofibrils (CNFs) and the progress in the research pertaining to their surface modification. Moreover, the preparation and surface modification of nanocellulose were comprehensively introduced based on the existing literature. The review focuses on the mechanical treatment of cellulose, the surface modification of fibrillated fibers during pretreatment, the surface modification of nanocellulose and the modification of CNFs and their functional application. In the past five years, research on cellulose nanofibrils has progressed with developments in nanomaterials research technology.