Module-Type Triboelectric Nanogenerators Capable of Harvesting Power from a Variety of Mechanical Energy Sources
Total Page:16
File Type:pdf, Size:1020Kb
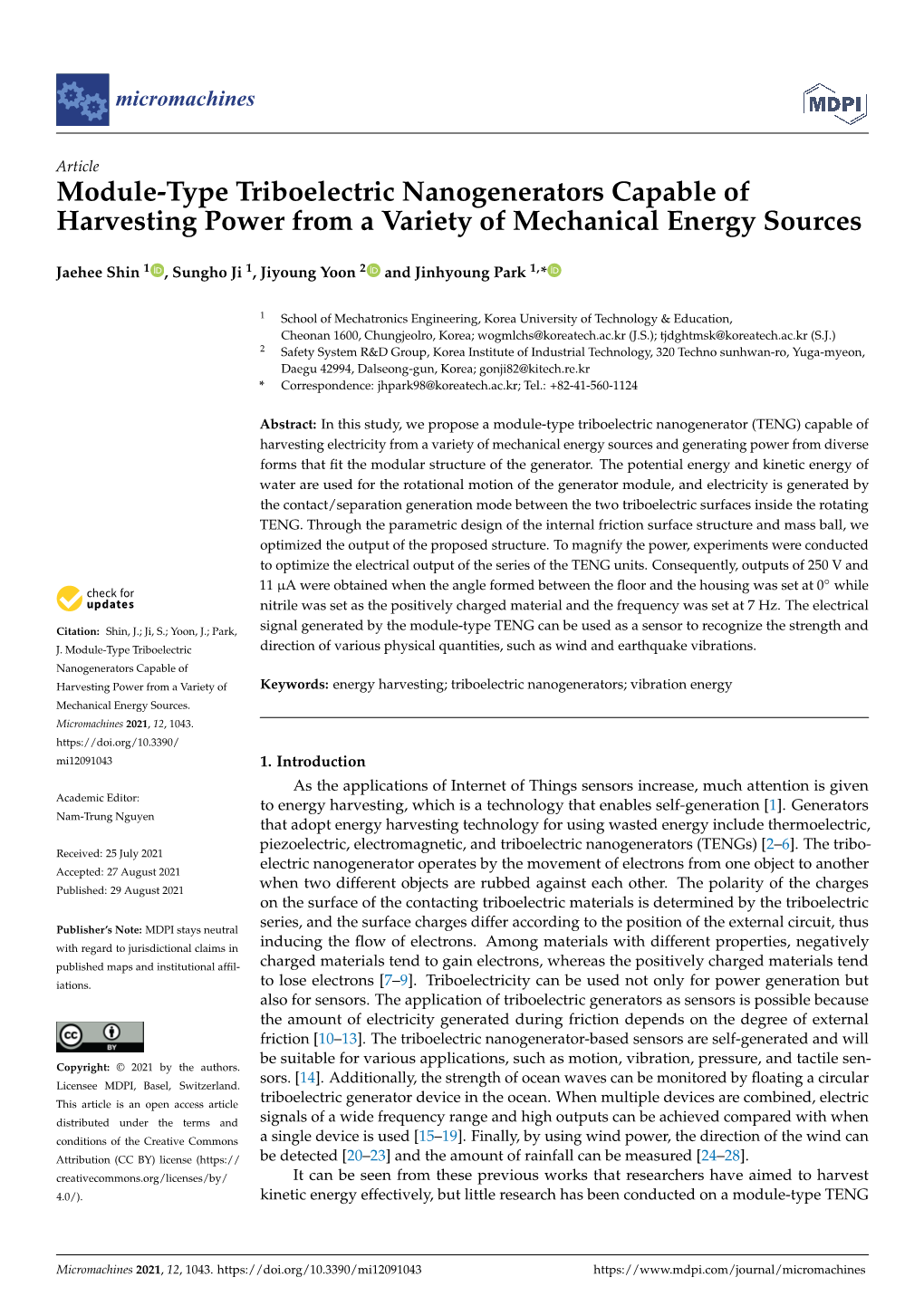
Load more
Recommended publications
-
Triboelectric Nanogenerator Networks Integrated with Power Management Module for Water Wave Energy Harvesting
FULL PAPER Blue Energy www.afm-journal.de Triboelectric Nanogenerator Networks Integrated with Power Management Module for Water Wave Energy Harvesting Xi Liang, Tao Jiang, Guoxu Liu, Tianxiao Xiao, Liang Xu, Wei Li, Fengben Xi, Chi Zhang,* and Zhong Lin Wang* by the consumption of fossil fuels have Ocean waves are one of the most promising renewable energy sources for attracted worldwide attention.[1,2] It is large-scope applications. Recently, triboelectric nanogenerator (TENG) network highly urgent to search for other renew- has been demonstrated to effectively harvest water wave energy possibly able and clean energy sources. Water toward large-scale blue energy. However, the absence of effective power wave energy, which has abundant reserves and little dependence on environmental management severely restricts the practicability of TENGs. In this work, a conditions, is a promising renewable energy hexagonal TENG network consisting of spherical TENG units based on spring- source with great potential for large-scale assisted multilayered structure, integrated with a power management module applications.[3–5] However, such energy has (PMM), is constructed for harvesting water wave energy. The output perfor- rarely been exploited due to lack of eco- mance of the TENG network is found to be determined by water wave frequen- nomical energy scavenging technologies in spite of the great efforts devoted.[6–8] cies and amplitudes, as well as the wave type. Moreover, with the implemented So far, most demonstrated converters for PMM, the TENG network could output a steady and continuous direct current water wave energy rely on the electromag- (DC) voltage on the load resistance, and the stored energy is dramatically netic generators, which are heavy, bulky, improved by up to 96 times for charging a capacitor. -
Power Sources for Wireless Sensor Networks
Power Sources for Wireless Sensor Networks Shad Roundy1, Dan Steingart2, Luc Frechette3, Paul Wright2, and Jan Rabaey2 1Australian National University, Department of Engineering, Canberra ACT 0200, Australia [email protected] 2University of California at Berkeley, Department of {Mechanical Engineering, Electrical Engineering and Computer Science}, Berkeley CA 94720, USA [email protected], [email protected], [email protected] 3Columbia University, Department of Mechanical Engineering , 228 S.W. Mudd Bldg, Mail Code 4703, 500 West 120th Street, New York, NY 10027-6699, USA [email protected] Abstract. Wireless sensor networks are poised to become a very significant enabling technology in many sectors. Already a few very low power wireless sensor platforms have entered the marketplace. Almost all of these platforms are designed to run on batteries that have a very limited lifetime. In order for wireless sensor networks to become a ubiquitous part of our environment, alternative power sources must be employed. This paper reviews many potential power sources for wireless sensor nodes. Well established power sources, such as batteries, are reviewed along with emerging technologies and currently untapped sources. Power sources are classified as energy reservoirs, power distribution methods, or power scavenging methods, which enable wireless nodes to be completely self-sustaining. Several sources capable of providing power on the order of 100 µW/cm3 for very long lifetimes are feasible. It is the authors’ opinion that no single power source will suffice for all applications, and that the choice of a power source needs to be considered on an application-by-application basis. 1 Introduction The vast reduction in size and power consumption of CMOS circuitry has led to a large research effort based around the vision of ubiquitous networks of wireless sensor and communication nodes [1-3]. -
Micropower Generation Using Combustion
Micro-Power Generation Using Combustion: Issues and Approaches A. Carlos Fernandez-Pello Department of Mechanical Engineering, University of California, Berkeley Berkeley, CA 94720-1740, USA FAX: (510)642-6163 e-mail: [email protected] Colloquium: 14. New Concepts in Combustion Technology. Micro-combustors Prepared for presentation as a Topical Review at the Twenty-Ninth International Symposium on Combustion, July 21-26, 2002, Sapporo, Japan ABSTRACT The push toward the miniaturization of electro-mechanical devices and the resulting need for micro-power generation (milli-watts to watts) with low-weight, long-life devices has led to the recent development of the field of micro-scale combustion. The concept behind this new field is that since batteries have low specific energy, and liquid hydrocarbon fuels have a very high specific energy, a miniaturized power generating device, even with a relatively inefficient conversion of hydrocarbon fuels to power would result in increased lifetime and/or reduced weight of an electronic or mechanical system that currently requires batteries for power. In addition to the interest in miniaturization, the field is also driven by the potential fabrication of the devices using Micro Electro Mechanical Systems (MEMS) or rapid prototyping techniques, with their favorable characteristics for mass production and low cost. The micro-power generation field is very young, and still is in most cases in the feasibility stage. However, considering that it is a new frontier of technological development, and that only a few projects have been funded, it can be said that significant progress has been made to date. Currently there is consensus, at least among those working in the field, that combustion in the micro-scale is possible with proper thermal and chemical management. -
IMPROVED MICROPOWER LOGIC CIRCUITS by John C
IMPROVED MICROPOWER LOGIC CIRCUITS by John C. Sturman Lewis Research Center Cleveland, Ohio NATIONAL AERONAUTICS AND SPACE ADMINISTRATION WASHINGTON, D. C. JULY 1967 TECH LIBRARY KAFB, NM I111111 lllll llll 118 II18 1111 Ill 111 0130769 NASA TN D-4052 IMPROVED MICROPOWER LOGIC CIRCUITS By John C. Sturman Lewis Research Center Cleveland, Ohio NATIONAL AERONAUTICS AND SPACE ADMINISTRATION For sale by the Clearinghouse for Federal Scientific and Technical Information Springfield, Virginia 22151 - CFSTl price $3.00 lMPROVED MICROPOWER LOGIC CIRCUITS by John C. Sturman Lewis Research Center SUMMARY Modifications to a previously reported micropower logic circuit improve its perform- ance and make possible its fabrication in monolithic form. A further improvement in power consumption was made by designing the circuit to operate from power supply volt- ages that vary with temperature. Logical gating circuits that use these techniques are discussed. These circuits were designed to operate at pulse rates of approximately 100 000 pulses per second at power levels of approximately 100 microwatts each. At reduced pulse rates, the same basic circuits can be designed to operate at power levels as low as a few microwatts per ele- ment. INTRODUCTION A steadily increasing effort is being expended to develop low-power logic circuits and semiconductor devices suitable for them. This trend has been in effect for at least 6 years, although the motivations for micropower development have changed considerably during this period. Originally, low-power circuits were necessary to provide any reason- able life for experiments on the relatively small, weight-limited satellites then available. Today, it is possible to launch much larger payloads, but the experiments they carry have become so much larger and more sophisticated that they require a vast increase in the amount of electronics. -
Micropower Generation Using Combustion: Issues and Approaches
UC Berkeley UC Berkeley Previously Published Works Title Micropower generation using combustion: Issues and approaches Permalink https://escholarship.org/uc/item/1q2284dj Journal PROCEEDINGS OF THE COMBUSTION INSTITUTE, 29 ISSN 0082-0784 Author Fernandez-Pello, Carlos Publication Date 2002-07-21 Peer reviewed eScholarship.org Powered by the California Digital Library University of California Micro-Power Generation Using Combustion: Issues and Approaches A. Carlos Fernandez-Pello Department of Mechanical Engineering, University of California, Berkeley Berkeley, CA 94720-1740, USA FAX: (510)642-6163 e-mail: [email protected] Colloquium: 14. New Concepts in Combustion Technology. Micro-combustors Prepared for presentation as a Topical Review at the Twenty-Ninth International Symposium on Combustion, July 21-26, 2002, Sapporo, Japan ABSTRACT The push toward the miniaturization of electro-mechanical devices and the resulting need for micro-power generation (milli-watts to watts) with low-weight, long-life devices has led to the recent development of the field of micro-scale combustion. The concept behind this new field is that since batteries have low specific energy, and liquid hydrocarbon fuels have a very high specific energy, a miniaturized power generating device, even with a relatively inefficient conversion of hydrocarbon fuels to power would result in increased lifetime and/or reduced weight of an electronic or mechanical system that currently requires batteries for power. In addition to the interest in miniaturization, the field is also driven by the potential fabrication of the devices using Micro Electro Mechanical Systems (MEMS) or rapid prototyping techniques, with their favorable characteristics for mass production and low cost. -
Tritium:Tritium: AA Micropowermicropower Sourcesource Forfor Onon--Chipchip Applicationsapplications
Tritium:Tritium: AA MicroPowerMicroPower SourceSource forfor OnOn--ChipChip ApplicationsApplications Nazir P. Kherani1, Baojun Liu2, Stefan Zukotynski1, Kevin P. Chen2 1Department of Electrical & Computer Engineering 2Department of Electrical and Computer Engineering and Department of Materials Science & Engineering University of Pittsburgh, Pittsburgh, PA, 15261 University of Toronto, Toronto, Ontario, M5S 3G4 Invited Presentation at Materials Innovations in an Emerging Hydrogen Economy February 24-27, 2008, Cocoa Beach, Florida Organized by the American Ceramic Society and ASM International Endorsed by National Hydrogen Association and Society for Advancement of Material and Process Engineering 1 OutlineOutline z Tritium: Basics z Tritium: A MicroPower Source – Beta-Voltaics – Beta-Powered MEMS – Beta-Luminescence – Cold Electron Source z Tritium: A Characterization/Diagnostic Tool – Tritium Tracer Studies – Tritium Effusion Studies – Defect Dynamics – Particle Sensor Applications z Summary 2 TritiumTritium z Isotope of Hydrogen 3 3 + − z H Æ He + β + νe + 18.6 keV z Nuclear Half-life: t ½ = 12.32 years λ = 1.78 x 10-9 s-1 z Activities: 1 Ci = 3.7 x 1010 Bq 1 Ci = 0.39 std cc 1 Ci = 33.7 μW z Biological: Half-life: 10 days ALI*: 80 mCi *Annual Limit on Intake z Chemically: Identical to 1H Mass effect (~3amu) Beta catalysis z Range (max): 4.5 – 6 mm in air 5 – 7 micron in water 3 ProducersProducers && UsersUsers CANDU z Producers of Tritium – Ontario Power Generation (OPG) • ~1 kg/year – Korean Electric Power Company (KEPCO) – USA • -
Electrolyte-Based On-Demand and Disposable Microbattery Ki Bang Lee and Liwei Lin, Member, IEEE, Member, ASME
840 JOURNAL OF MICROELECTROMECHANICAL SYSTEMS, VOL. 12, NO. 6, DECEMBER 2003 Electrolyte-Based On-Demand and Disposable Microbattery Ki Bang Lee and Liwei Lin, Member, IEEE, Member, ASME Abstract—A micromachined battery based on liquid electrolyte and metal electrodes for on-demand and disposable usages has been successfully demonstrated. The microbattery uses gold as the positive electrode and zinc as the negative electrode and is fabricated by using the standard surface micromachining technology. Two kinds of electrolytes have been tested, including the combination of sulfuric acid/hydrogen peroxide and potassium hydroxide. The operation of the battery can be on-demand by putting a droplet of electrolyte to activate the operation. Theo- retical voltage and capacity of the microbattery are formulated and compared with experimental results. The experimental study shows that a maximum voltage of 1.5 V and maximum capacity of 122.2 -min have been achieved by using a single droplet of about 0.5 l of sulfuric acid/hydrogen peroxide. [848] Index Terms—Battery, disposable micropower, MEMS, micro- machines, microsystems. Fig. 1. Schematic of a electrolyte on-demand and disposal microbattery: both I. INTRODUCTION positive electrode (gold) and supports for forming the electrolyte cavity are placed on the lower substrate while the negative electrode (zinc) is capped; the ICROPOWER generation aiming at generating power microbattery works after putting liquid electrolyte (see Fig. 2). M directly from microstructures may greatly impact the ap- plication and architecture of microsystems. Various approaches [7] and rechargeable microbatteries [8]–[11] have been investi- to supply power for microscale devices are now being investi- gated by using rather complicated micromachining processes. -
Molecular Surface Functionalization to Enhance the Power Output of Triboelectric Nanogenerators† Cite This: J
Journal of Materials Chemistry A View Article Online PAPER View Journal | View Issue Molecular surface functionalization to enhance the power output of triboelectric nanogenerators† Cite this: J. Mater. Chem. A,2016,4, 3728 Sihong Wang,‡a Yunlong Zi,‡a Yu Sheng Zhou,a Shengming Li,a Fengru Fan,b Long Lina and Zhong Lin Wang*ab Triboelectric nanogenerators (TENGs) have been invented as a new technology for harvesting mechanical energy, with enormous advantages. One of the major themes in their development is the improvement of the power output, which is fundamentally determined by the triboelectric charge density. Besides the demonstrated physical surface engineering methods to enhance this density, chemical surface functionalization to modify the surface potential could be a more effective and direct approach. In this paper, we introduced the method of using self-assembled monolayers (SAMs) to functionalize surfaces for the enhancement of TENGs' output. By using thiol molecules with different head groups to functionalize Au surfaces, the influence of head groups on both the surface potential and the triboelectric charge density was systematically studied, which reveals their direct correlation. With amine Received 14th December 2015 as the head group, the TENG's output power is enhanced by 4 times. By using silane-SAMs with an Accepted 28th January 2016 amine head group to modify the silica surface, this approach is also demonstrated for insulating DOI: 10.1039/c5ta10239a triboelectric layers in TENGs. This research provides an important route for the future research on www.rsc.org/MaterialsA improving TENGs' output through materials optimization. Introduction materials' aspect, it has been shown that the performance gure-of-merit of TENGs is proportional to the square of the As a huge energy reservoir in the environment that can be triboelectric charge density, which is the most important 31 potentially utilized by human beings, mechanical energy is parameter to determine the power output. -
Micropower Energy Harvesting
Solid-State Electronics 53 (2009) 684–693 Contents lists available at ScienceDirect Solid-State Electronics journal homepage: www.elsevier.com/locate/sse Micropower energy harvesting R.J.M. Vullers a,*, R. van Schaijk a, I. Doms b, C. Van Hoof a,b, R. Mertens b a IMEC/Holst Centre, High Tech Campus 31, 5656 AE Eindhoven, The Netherlands b IMEC, Kapeldreef 75, 3001 Leuven, Belgium article info abstract Article history: More than a decade of research in the field of thermal, motion, vibration and electromagnetic radiation Received 17 November 2008 energy harvesting has yielded increasing power output and smaller embodiments. Power management Accepted 22 December 2008 circuits for rectification and DC–DC conversion are becoming able to efficiently convert the power from Available online 25 April 2009 these energy harvesters. This paper summarizes recent energy harvesting results and their power man- agement circuits. The review of this paper was arranged by Prof. P. Ashburn Ó 2009 Elsevier Ltd. All rights reserved. Keywords: Energy harvesting Micromachining Power management Micropower 1. Introduction different ambient situation are considered. They correspond to var- ious level of available power, and hence of generated electrical The low power consumption of silicon-based electronics has en- power. We notice that outdoor-light outperforms all other energy abled a broad variety of battery-powered handheld, wearable and sources, but indoor-light is fairly comparable to thermal and vibra- even implantable devices. A range of wireless devices spanning tion energy. We also notice that while industrial environments six orders of magnitude power consumption are shown in Table seem to have energy to spare, around the body energy is far more 1, with their typical autonomy. -
Utilizing Waste Hydrogen for Energy Recovery Using Fuel Cells and Associated Technologies
UTILIZING WASTE HYDROGEN FOR ENERGY RECOVERY USING FUEL CELLS AND ASSOCIATED TECHNOLOGIES Copyright Material IEEE Paper No. PCIC-2004-14 Paul Buddingh, P.Eng. Vince Scaini, P.Eng. Leo Casey, PhD Member, IEEE Member, IEEE Member, IEEE Universal Dynamics SatCon Power Systems SatCon Technology 100-13700 International Place 835 Harrington Crt. 161 First Street Richmond, BC V6V 2X8 Burlington, ON L7N 3P3 Cambridge, MA 02142-1228 Canada Canada USA Abstract- Electrochemical and other process industries one could argue that we will eventually be using 100% frequently vent or flare hydrogen byproducts to the hydrogen fuel without the motivation of environmental atmosphere. This paper will discuss hydrogen power benefits. conversion methods including fuel cells and combustion Hydrogen has higher energy per unit of mass, but lower technologies. This paper presents an overview of some of the energy per unit volume than any other fuel. By weight, practical implementation methods available, and the hydrogen “carries” three times the energy of our most challenges that must be met. The pros and cons of distributing common fuels. For example, 1 kg of hydrogen has power to either the AC power system or DC process bus are approximately the same amount of energy as 1 US gallon of examined. This technology is expected to become cost- gasoline (approximately 3 kg). The major downside of competitive as energy prices continue to climb and fuel cell hydrogen is its poor volumetric energy density, making proficiency matures. storage and transportation a fundamental challenge. To help resolve this problem, the hydrogen industry is currently Index Terms – Hydrogen, Fuel Cells, DC/DC Converters, certifying 10,000 psi hydrogen cylinders. -
Opportunities for Micropower and Fuel Cell/Gas Turbine Hybrid Systems in Industrial Applications
Opportunities for Micropower and Fuel Cell/Gas Turbine Hybrid Systems in Industrial Applications Volume II: Appendices Subcontract No. 85X-TA009V Notice: Final Report to Lockheed Martin Energy Research Corporation and This report was prepared by Arthur D. Little for the account of the DOE Office of Industrial Lockheed Martin Energy Research Corporation and the DOE’s Technologies Office of Industrial Technologies. This report represents Arthur D. Little’s best judgment in light of information made available January 2000 to us. This report must be read in its entirety. The reader understands that no assurances can be made that all financial liabilities have been identified. This report does not constitute a legal opinion. No person has been authorized by Arthur D. Little to provide any information or make any representations not contained in this report. Any use the reader makes of this report, or any reliance upon or decisions to be made based upon this report are the responsibility of the reader. Arthur D. Little does not accept any responsibility for damages, if any, suffered by the reader based upon this report. Arthur D. Little, Inc. Acorn Park Cambridge, Massachusetts 02140-2390 U.S.A. Reference 38410 Table of Contents Appendix A: Approach ............................................................................................... 1 Appendix B: Calculation of Economic Fit ................................................................. 6 Appendix C: Calculation of Techno-Economic Fit ................................................ -
Bio-Mechanically Driven MEMS Power Generator for Implantable Medical Devices
University of Windsor Scholarship at UWindsor Electronic Theses and Dissertations Theses, Dissertations, and Major Papers 1-1-2007 Bio-mechanically driven MEMS power generator for implantable medical devices. Jose Martinez-Quijada University of Windsor Follow this and additional works at: https://scholar.uwindsor.ca/etd Recommended Citation Martinez-Quijada, Jose, "Bio-mechanically driven MEMS power generator for implantable medical devices." (2007). Electronic Theses and Dissertations. 7112. https://scholar.uwindsor.ca/etd/7112 This online database contains the full-text of PhD dissertations and Masters’ theses of University of Windsor students from 1954 forward. These documents are made available for personal study and research purposes only, in accordance with the Canadian Copyright Act and the Creative Commons license—CC BY-NC-ND (Attribution, Non-Commercial, No Derivative Works). Under this license, works must always be attributed to the copyright holder (original author), cannot be used for any commercial purposes, and may not be altered. Any other use would require the permission of the copyright holder. Students may inquire about withdrawing their dissertation and/or thesis from this database. For additional inquiries, please contact the repository administrator via email ([email protected]) or by telephone at 519-253-3000ext. 3208. BIO-MECHANICALLY DRIVEN MEMS POWER GENERATOR FOR IMPLANTABLE MEDICAL DEVICES by Jose Martinez-Quijada A Thesis Submitted to the Faculty of Graduate Studies through the Department of Electrical and Computer Engineering in Partial Fulfillment of the Requirements for the Degree of Master of Applied Science at the University of Windsor Windsor, Ontario, Canada 2007 © 2007 Jose Martinez-Quijada Reproduced with permission of the copyright owner.