=-(Accoss7 U) Qo",B= )
Total Page:16
File Type:pdf, Size:1020Kb
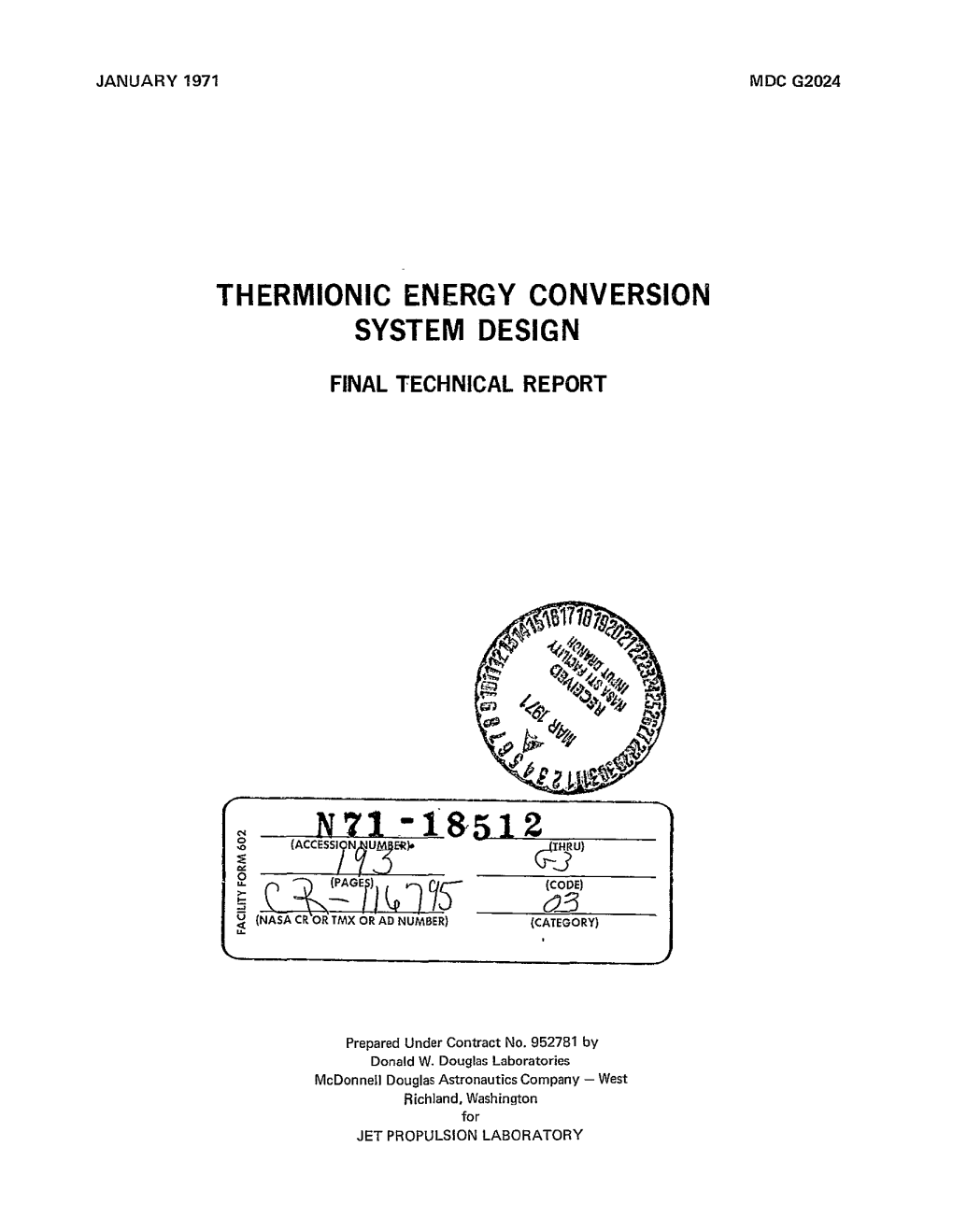
Load more
Recommended publications
-
Measurements of Plasma Parameters in a Simulated Thermionic Converter
JPL Quarterly Technical Review Volume 1, Number 3 October 1971 Measurements of Plasma Parameters in a Simulated Thermionic Converter K. Shimada Guidance and Control Division Cesium-filled thermionic energy converters are being considered as candidate electrical energy sources in future spacecraft requiring tens to hundreds of kilowatts of electric power. The high operating temperatures necessary for a large specific power and high efficiency inevitably impose stringent constraints on the.converter fabrication to achieve the desired reliability of the power system. The converter physics for reducing operating temperatures and cesium plasma losses are being studied to achieve high reliability without sacrificing the power performance of the converters. Various cesium parameters which affect the converter performance are: (1) electron temperatures, (2) plasma ion densities, and (3) electric potential profiles. These were investigated using a Langmuir probe in a simulated converter. The parameters were measured in different cesium discharge modes. Introduction Cesium-filled thermionic energy converters are being considered as candidate electrical energy sources in future spacecraft requiring tens to hundreds of kilowatts of electric power. The advantage of the thermionic- converter over other direct energy conversion devices is its high conversion efficiency, which in turn reduces the required fuel inventory. The conversion efficiency, which is typically larger than 15%, stems mainly from an operating temperature of nearly 2000 K at an emitter electrode where the primary heat is received. The high operating temperature also results in a reduced radiator area for heat rejection, which is an additional advantage. Conversely, the requirements for high temperatures add stringent con- straints to the materials and the fabrications of these converters which must have high reliability. -
The Design of a Combustion Heated Thermionic Energy Converter
The design of a combustion heated thermionic energy converter Citation for published version (APA): Kemenade, van, H. P. (1995). The design of a combustion heated thermionic energy converter. Technische Universiteit Eindhoven. https://doi.org/10.6100/IR438219 DOI: 10.6100/IR438219 Document status and date: Published: 01/01/1995 Document Version: Publisher’s PDF, also known as Version of Record (includes final page, issue and volume numbers) Please check the document version of this publication: • A submitted manuscript is the version of the article upon submission and before peer-review. There can be important differences between the submitted version and the official published version of record. People interested in the research are advised to contact the author for the final version of the publication, or visit the DOI to the publisher's website. • The final author version and the galley proof are versions of the publication after peer review. • The final published version features the final layout of the paper including the volume, issue and page numbers. Link to publication General rights Copyright and moral rights for the publications made accessible in the public portal are retained by the authors and/or other copyright owners and it is a condition of accessing publications that users recognise and abide by the legal requirements associated with these rights. • Users may download and print one copy of any publication from the public portal for the purpose of private study or research. • You may not further distribute the material or use it for any profit-making activity or commercial gain • You may freely distribute the URL identifying the publication in the public portal. -
Thermionic Energy Conversion in the Twenty-First Century: Advances and Opportunities for Space and Terrestrial Applications
https://ntrs.nasa.gov/search.jsp?R=20170011125 2019-08-31T13:52:57+00:00Z REVIEW published: 08 November 2017 doi: 10.3389/fmech.2017.00013 Thermionic Energy Conversion in the Twenty-first Century: Advances and Opportunities for Space and Terrestrial Applications David B. Go1,2*, John R. Haase1,2, Jeffrey George 3, Jochen Mannhart 4, Robin Wanke 4, Alireza Nojeh 5 and Robert Nemanich6 1 Department of Aerospace and Mechanical Engineering, University of Notre Dame, Notre Dame, IN, United States, 2 Department of Chemical and Biomolecular Engineering, University of Notre Dame, Notre Dame, IN, United States, 3 Johnson Space Center, National Aeronautics and Space Administration (NASA), Houston, TX, United States, 4 Max Planck Institute for Solid State Research, Stuttgart, Germany, 5 Department of Electrical and Computer Engineering, Quantum Matter Institute, University of British Columbia, Vancouver, BC, Canada, 6 Department of Physics, Arizona State University, Tempe, AZ, United States Thermionic energy conversion (TEC) is the direct conversion of heat into electricity by the mechanism of thermionic emission, the spontaneous ejection of hot electrons from a surface. Although the physical mechanism has been known for over a century, it has yet to be consistently realized in a manner practical for large-scale deployment. This Edited by: perspective article provides an assessment of the potential of TEC systems for space Guillermo Rein, Imperial College London, and terrestrial applications in the twenty-first century, overviewing recent advances in the United Kingdom field and identifying key research challenges. Recent developments as well as persisting Reviewed by: research needs in materials, device design, fundamental understanding, and testing and Dong Liu, University of Houston, validation are discussed. -
Thermophotovoltaic Energy in Space Applications: Review and Future Potential A
Thermophotovoltaic energy in space applications: Review and future potential A. Datas , A. Marti ABSTRACT This article reviews the state of the art and historical development of thermophotovoltaic (TPV) energy conversion along with that of the main competing technologies, i.e. Stirling, Brayton, thermoelectrics, and thermionics, in the field of space power generation. Main advantages of TPV are the high efficiency, the absence of moving parts, and the fact that it directly generates DC power. The main drawbacks are the unproven reliability and the low rejection temperature, which makes necessary the use of relatively large radiators. This limits the usefulness of TPV to small/medium power applications (100 We-class) that includes radioisotope (RTPV) and small solar thermal (STPV) generators. In this article, next generation TPV concepts are also revisited in order to explore their potential in future space power applications. Among them, multiband TPV cells are found to be the most promising in the short term because of their higher conversion efficiencies at lower emitter temperatures; thus significantly reducing the amount of rejected heat and the required radiator mass. 1. Introduction into electricity. A few of them enable a direct conversion process (e.g. PV and fuel cells), but the majority require the intermediate generation A number of technological options exist for power generation in of heat, which is subsequently converted into electricity by a heat space, which are selected depending on the mission duration and the engine. Thus, many kinds of heat engines have been developed within electric power requirements. For very short missions, chemical energy the frame of international space power R&D programs. -
Energy Options for Wireless Sensor Nodes
Sensors 2008, 8, 8037-8066; DOI: 10.3390/s8128037 OPEN ACCESS sensors ISSN 1424-8220 www.mdpi.com/journal/sensors Review Energy Options for Wireless Sensor Nodes Chris Knight 1,*, Joshua Davidson 2 and Sam Behrens 1 1 CSIRO Energy Technology, PO Box 330, Newcastle NSW 2300, Australia. E-Mail: [email protected] 2 School of Maths, Physics & Information Technology, James Cook University, Townsville QLD 4811, Australia. E-Mail: [email protected] * Author to whom correspondence should be addressed; E-Mail: [email protected]; Tel.: +61-2- 4960-6049; Fax: +61-2-4960-6111 Received: 24 September 2008; in revised form: 3 December 2008 / Accepted: 5 December 2008 / Published: 8 December 2008 Abstract: Reduction in size and power consumption of consumer electronics has opened up many opportunities for low power wireless sensor networks. One of the major challenges is in supporting battery operated devices as the number of nodes in a network grows. The two main alternatives are to utilize higher energy density sources of stored energy, or to generate power at the node from local forms of energy. This paper reviews the state-of-the art technology in the field of both energy storage and energy harvesting for sensor nodes. The options discussed for energy storage include batteries, capacitors, fuel cells, heat engines and betavoltaic systems. The field of energy harvesting is discussed with reference to photovoltaics, temperature gradients, fluid flow, pressure variations and vibration harvesting. Keywords: Energy Harvesting; Energy Storage; Wireless Sensor Networks, Sensor Nodes 1. Introduction Reduction in size and power consumption of consumer electronics has opened up many new opportunities for low power wireless sensor networks. -
Analysis of Electron Transport in the Plasma of Thermionic Converters
[••iw'-'^-Tr-' "'"^ •*"$J?,«*WS' •^••"w**" Analysis of Electron Transport in the Plasma of Thermionic Converters Maria L. Stoenescu and Peter H. Heinicke Plasma Physics Laboratory, Princeton University Princeton, New Jersey 085<f<* ABSTRACT Electron transport coefficients of a gaseous ensemble are expressed analy tically as function of density, and are expressed analytically as function of tempera- & ture urp to an unknown function 6 _ which has to be evaluated for each specific e,eo electron - neutral atom cross section. In order to complete the analytical tempera- ture dependence one may introduce a polynomial expansion of the function 6 _Qt or, one may derive the temperature dependence of a set of coefficients, numbering thirteen for a third approximation transport evaluation, which completely determine the transport coefficients. The latter approach is used for determining the electron transport coefficients of a cesium plasma for any ion neutral composition and any temperature between 500 K and 3500°K. The relation betweea the transport coefficients of a fully and partly ionized gas is readily available and shows that, in the classical formalism, electron-ion and electron-neutral resistivities are not additive. The present form of the transport coefficients makes possible an accurate numerical integration of transport equations eliminating ten0.hy computations which are frequently inaccessible. It thus provides a detailed knowledge of spatial distribution of particle and energy transport and makes possible the determination of one of the three internal voltage drops, surface barrier, siieath and plasma, which are linked together experimentally by current density versus voltage characteristics of thermionic converters. 2 I. INTRODUCTION The advantage of introducing cesium vapor in the thermionic converter which improves the thermionic emission by lowering the emitter work function is counter acted by the increase of plasma resistance due to the presence of neutral particles. -
Direct Conversion of Energy. INSTITUTION Atomic Energy Commission, Washington,D
DOCUMENT RESUME ED 107 521 SE 019 210 AUTHOR Corliss, William R. TITLE Direct Conversion of Energy. INSTITUTION Atomic Energy Commission, Washington,D. C. Office of Information Services. PUB DATE 64 NOTE 41p. AVAILABLE FROM USAEC Technical Information Center,P.O. Box 62, Oak Ridge, TN 37830 (cost to the generalpublic for 1-4. copies, $0.25 ea., 5-99, $0.20ea., 100 or mare, $0.15 ea.) EDRS PRICE MF-$0.76 HC-$1.95 PLUS POSTAGE DESCRIPTORS Electricity; Electronics; *Energy; NuclearPhysics; Physics; *Scientific Research;*Thermodynamics IDENTIFIERS AEC; Atomic Energy Commission ABSTRACT This publication is one ofa series of information booklets for the general public publishedby the United States Atomic Energy Commission. Directenergy conversion Involves energy transformation Without moving parts.The concepts of direct and dynamic energy conversion plus thelaws governing energy conversion are investigated. Among the topics discussedare: Thermoelectricity; Thermionic Conversion; MagnetohydrodynamicConversion; Chemical Batteries; The Fuel Cell; Solar Cells;Nuclear Batteries; Ferroelectric Conversion and ThermomagneticConversion. Five problems related to the reading materialare included. Alist of suggested references concludes this report. Acomplete set of these booklets may be obtained by school and public librarieswithout charge. (BI). It®tr. A 1)+10+ u, OEPARTMENT OF HEALTH. EOUCATiON &WELFARE NATIONAL INSTiTUTL OF )1\ EOU CATION ontsocsE 00 OECXUANIC ET Zs.; AHSA et BC EE EIVNE DI PRROOM I) 1 ti L, E PERSON OR ORGANIZATION ORIGIN + APERSONC IT POINTS OF VIBEW OR OPINIONS STATE() 00 NOT NECESSARILYREPRE SENT OFFICIAL NATIONAL INSTITUTEOF EDUCATION POSITION OR POLICY ++ + + ++ I++. te t++ + t + tet+ + + +Jo+ ++®+ + -+tot++ +of+ IIet@tetzt\®tet ++ +t 1\®+ t@t®I\ +tot+Soto to+ ()tete+ f+tc)+0, @tiot@+ +®1\+ 1\ bY. -
Energy Options for Wireless Sensor Nodes
Sensors 2008, 8, 8037-8066; DOI: 10.3390/s8128037 OPEN ACCESS sensors ISSN 1424-8220 www.mdpi.com/journal/sensors Review Energy Options for Wireless Sensor Nodes Chris Knight 1,*, Joshua Davidson 2 and Sam Behrens 1 1 CSIRO Energy Technology, PO Box 330, Newcastle NSW 2300, Australia. E-Mail: [email protected] 2 School of Maths, Physics & Information Technology, James Cook University, Townsville QLD 4811, Australia. E-Mail: [email protected] * Author to whom correspondence should be addressed; E-Mail: [email protected]; Tel.: +61-2- 4960-6049; Fax: +61-2-4960-6111 Received: 24 September 2008; in revised form: 3 December 2008 / Accepted: 5 December 2008 / Published: 8 December 2008 Abstract: Reduction in size and power consumption of consumer electronics has opened up many opportunities for low power wireless sensor networks. One of the major challenges is in supporting battery operated devices as the number of nodes in a network grows. The two main alternatives are to utilize higher energy density sources of stored energy, or to generate power at the node from local forms of energy. This paper reviews the state-of-the art technology in the field of both energy storage and energy harvesting for sensor nodes. The options discussed for energy storage include batteries, capacitors, fuel cells, heat engines and betavoltaic systems. The field of energy harvesting is discussed with reference to photovoltaics, temperature gradients, fluid flow, pressure variations and vibration harvesting. Keywords: Energy Harvesting; Energy Storage; Wireless Sensor Networks, Sensor Nodes 1. Introduction Reduction in size and power consumption of consumer electronics has opened up many new opportunities for low power wireless sensor networks. -
Investigation of an Auxiliary Discharge Thermionic Converter Using Barium Oxide Electrodes Paiboon Limpaphayom Iowa State University
Iowa State University Capstones, Theses and Retrospective Theses and Dissertations Dissertations 1969 Investigation of an auxiliary discharge thermionic converter using barium oxide electrodes Paiboon Limpaphayom Iowa State University Follow this and additional works at: https://lib.dr.iastate.edu/rtd Part of the Electrical and Electronics Commons Recommended Citation Limpaphayom, Paiboon, "Investigation of an auxiliary discharge thermionic converter using barium oxide electrodes " (1969). Retrospective Theses and Dissertations. 4126. https://lib.dr.iastate.edu/rtd/4126 This Dissertation is brought to you for free and open access by the Iowa State University Capstones, Theses and Dissertations at Iowa State University Digital Repository. It has been accepted for inclusion in Retrospective Theses and Dissertations by an authorized administrator of Iowa State University Digital Repository. For more information, please contact [email protected]. 70-13,606 LIMPAPHAYOM, Paiboon, 1941- INVESTIGATION OF AN AUXILIARY DISCHARGE THERM IONIC CONVERTER USING BARIUM OXIDE ELECTRODES. Iowa State University, Ph.D., 1969 Engineering, electrical University Microfilms, Inc., Ann Arbor, Michigan © Copyright by PAIBOON LIMPAPHAYOM 1970 THIS DISSERTATION HAS BEEN MICROFILMED EXACTLY AS RECEIVED INVESTIGATION OP AN AUXILIARY DISCHARGE THERMIONIC CONVERTER USING BARIUM OXIDE ELECTRODES by Paiboon Llmpaphayom A Dissertation Submitted to the Graduate Faculty in Partial Fulfillment of The Requirements for the Degree of DOCTOR OP PHILOSOPHY Major Subject: Electrical -
Microfabricated Thermionic Electron Emitters
Microfabricated Thermionic Electron Emitters K. Blair Huffman Stanford University To fulfill the undergraduate Honor’s Program requirements for the Department of Electrical Engineering June 2014 I certify that I have read this Honor’s thesis and that, in my opinion, it is fully adequate in scope and quality to fulfill the requirements for the undergraduate Honor’s Program for the Department of Electrical Engineering _______________________________ Roger T. Howe, Principal Adviser I certify that I have read this Honor’s thesis and that, in my opinion, it is fully adequate in scope and quality to fulfill the requirements for the undergraduate Honor’s Program for the Department of Electrical Engineering _______________________________ R. Fabian Pease, Second Reader Acknowledgements I would like to first thank Professor Roger Howe for his constant advice and assistance on this project and on my academic aspirations. None of this would have been possible without his support throughout my undergraduate career, and I cannot thank him enough. Prof. Howe’s energy group has been a tremendous resource for me. I would especially like to thank Dr. Justin Snapp for helping me with the fabrication. Next, I would like to thank Professor Fabian Pease and Dr. J Provine for introducing me to nanofabrication during my freshman year. They both helped me find my passion and have helped me pursue it during my undergraduate career. I would also like to thank the Department of Electrical Engineering for providing me with support on my project over the summer in 2013. I would like to thank the STEM fellowship, the American Indian Science and Engineering Society, Google, and Intel for providing funding. -
A Comparative Study of Nuclear Technology and Direct Energy Conversion Methods for Space Power Systems
N PS ARCHIVE 1997 REASON, J. NAVAL POSTGRADUATE SCHOOL MONTEREY, CALIFORNIA THESIS A COMPARATIVE STUDY OF NUCLEAR TECHNOLOGY AND DIRECT ENERGY CONVERSION METHODS FOR SPACE POWER SYSTEMS by Joseph P. Reason, Jr. June, 1997 Thesis Co-Advisors: Sherif Michael Barry Leonard Thesis R25456 Approved for public release; distribution is unlimited. OXLIBRARY TGRAOUAT£SCHOO» REPORT DOCUMENTATION PAGE Form Approved OMB No. 0704-0 \i Public reporting burden for this collection of information is estimated to average 1 hour per response, including the time for reviewing instruction, searching existing data sources, gathering and maintaining the data needed, and completing and reviewing the collection of information. Send comments regarding this burden estimate or any other aspect of this collection of information, including suggestions for reducing this burden, to Washington Headquarters Services, Directorate for Information Operations and Reports, 1215 Jefferson Davis Highway, Suite 1204, Arlington, VA 22202-4302, and to the Office of Management and Budget, Paperwork Reduction Project (0704-0188) Washington DC 20503. 2. 1 . AGENCY USE ONLY (Leave blank) REPORT DATE 3. REPORT TYPE AND DATES COVERED June 1997 Master's Thesis TITLE AND SUBTITLE A COMPARATIVE STUDY OF NUCLEAR 5. FUNDING NUMBERS TECHNOLOGY AND DIRECT ENERGY CONVERSION METHODS FOR SPACE POWER SYSTEMS 6. AUTHOR(S) Reason, Joseph, P., Jr. 7. PERFORMING ORGANIZATION NAME(S) AND ADDRESS(ES) PERFORMING Naval Postgraduate School ORGANIZATION Monterey CA 93943-5000 REPORT NUMBER 9. SPONSORING/MONITORING AGENCY NAME(S) AND ADDRESS(ES) 10. SPONSORING/MONITORING AGENCY REPORT NUMBER 1 1 . SUPPLEMENTARY NOTES The views expressed in this thesis are those of the author and do not reflect the official policy or position of the Department of Defense or the U.S. -
Arxiv:2010.03556V2 [Physics.Plasm-Ph] 1 Feb 2021 Uigo Oe Osmn.Figure Pro- Power Consuming
Simulations of Argon Plasma Decay in a Thermionic Converter R. E. Groenewald,1 S. Clark,1 A. Kannan,1 and P. Scherpelz1 1Modern Electron Inc., Bothell, WA 98011, USA (Dated: February 2, 2021) The dynamics of an argon plasma in the gap of a thermionic diode is investigated using particle- in-cell (PIC) simulations. The time-averaged diode current, as a function of the relative electrical potential between the electrodes, is studied while the plasma density depletes due to recombination on the electrode surfaces. Simulations were performed in both 1D and 2D and significant differences were observed in the plasma decay between the two cases. Specifically, in 2D it was found that the electrostatic potential gradually changes as the plasma decays, while in 1D fluctuations in the plasma led to large potential fluctuations which changed the plasma decay characteristics relative to the 2D case. This creates significant differences in the time-averaged diode current. Furthermore, it was found that the maximum time-averaged current is collected when the diode voltage is set to the flat-band condition, where the cathode and anode vacuum biases are equal. This suggests a novel technique of measuring the difference in work functions between the cathode and anode in a thermionic converter. Introduction electron motive diagram of a thermionic diode. The elec- tron motive diagram plots the negative of the electrical potential (φ = eV , where e is the electronic charge and Thermionic energy converters (TECs) are devices that − directly convert heat into electrical energy [1, 2]. The lack V is electrostatic potential). The device produces power of moving parts and scalability (core conversion efficiency whenever the anode Fermi level is at a lower electrical is independent of system size) of the technology makes potential than the cathode’s i.e.