Bracing, Tie-Down and Other Issues
Total Page:16
File Type:pdf, Size:1020Kb
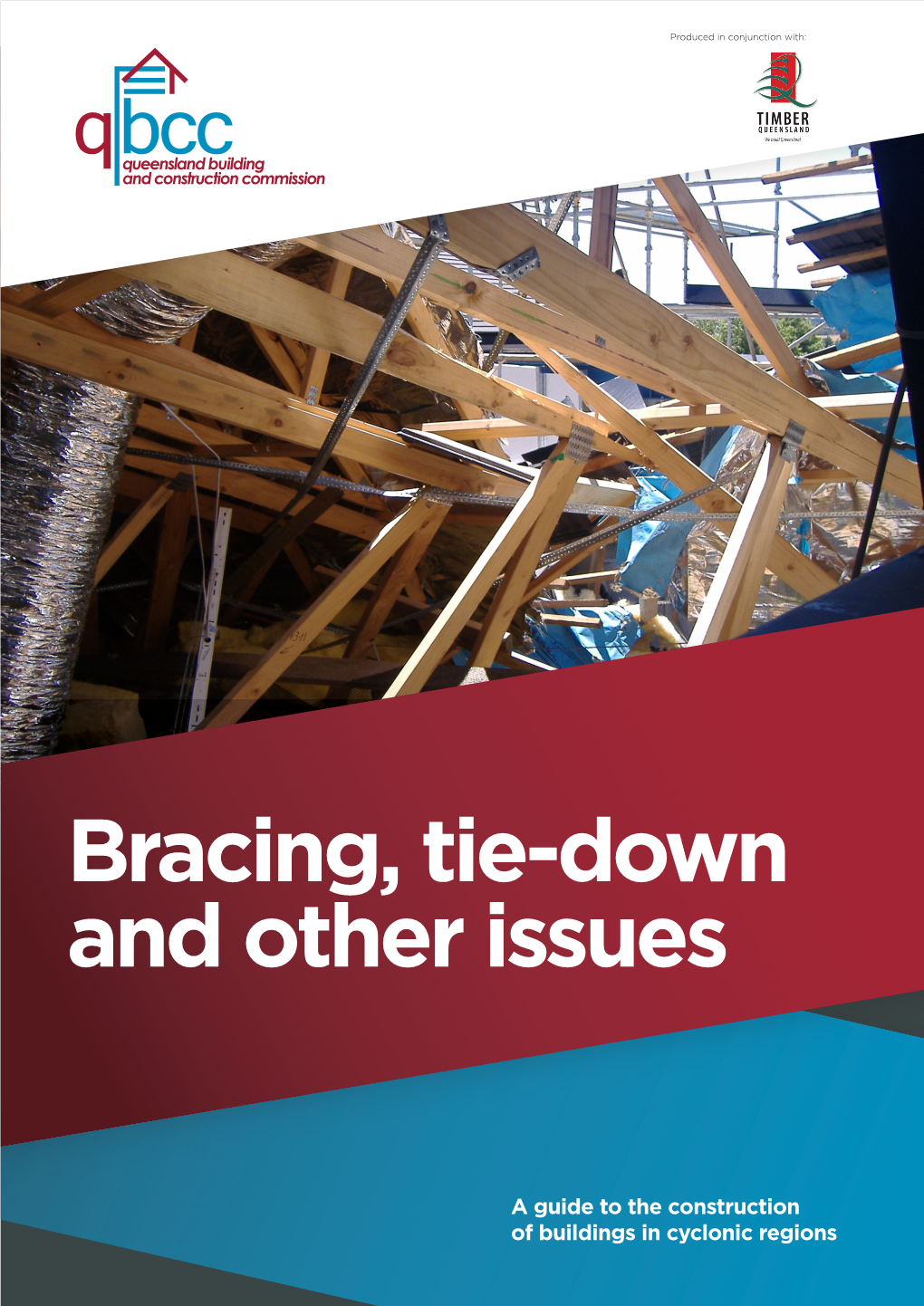
Load more
Recommended publications
-
Technical Notes
Strong-Rod™ Systems SEISMIC AND WIND RESTRAINT SYSTEMS GUIDE 800-999-5099 | www.strongtie.com Seismic and High-Wind Restraint Systems NEES-Soft test validates seismic retrofit solutions for soft-story buildings. Your Full-Solution Partner Simpson Strong-Tie introduces the Strong-Rod™ continuous rod tiedown system for light-frame, multi-story wood construction. Our Strong-Rod Anchor Tiedown System for shearwall overturning restraint and Strong-Rod Uplift Restraint System for roofs address many of the design challenges speciically associated with multi-story buildings that must withstand seismic activity or wind events. Multi-story structures require a variety of special design considerations, and having a reliable, highly knowledgeable design partner is critical to keeping projects on time and within budget. No company knows light- frame wood construction better than Simpson Strong-Tie, and we have everything you need to design your building. Code-listed components and systems that come with unmatched testing and design expertise are your formula for success. Let Simpson Strong-Tie be your partner in designing the safest building possible with materials suited speciically for the application, making installation easier and costs lower. To ind out how we can help you, visit us at www.strongtie.com/srscontact or call 800-999-5099. Company Proile For nearly 60 years, Simpson Strong-Tie has focused on creating structural products that help people build safer and stronger homes and buildings. A leader in structural systems research and technology, Simpson Strong-Tie is one of the largest suppliers of structural building products in the world. The Simpson Strong-Tie commitment to product development, engineering, testing and training is evident in the consistent quality and delivery of its products and services. -
Trussed Rafter Technical Guide
TRUSSED RAFTERS have proved to be an efficient, safe and economical method for supporting roofs since their introduction into the UK in 1964. They are manufactured by specialised timber engineering companies, who supply to all sections of the construction industry. Developments have been extensive, and today complex roofscapes are easily formed with computer designed trussed rafters. With the continuing trend toward individualism in domestic house styling, let alone the reflection of this in new inner city estates, the facility to introduce variations to the standard designs is vital. The provision of many character differences by designing and then constructing L returns, doglegs and hips for example, satisfies the inherent need for individuality at affordable prices. Economical roofing solutions for many commercial, industrial and agricultural buildings; hospitals, army barracks and supermarket complexes, are achieved by the expeditious installation of trussed rafters. Experienced roof designers and trussed rafter manu- facturers are therefore in an ideal position to assist the architect or specifier in achieving affordable solutions throughout the building industry. Simply provide a brief sketch or description of that being considered, including alternatives, and we will do the rest. The whole roof is designed and specified using state-of-the-art computer aided technology supplied by Wolf Systems. We can also arrange for one of our specialists to visit and advise you. This technical manual highlights some of the basic structural arrangements and assembly information you may require. In addition, we can offer technical expertise and experience in a comprehensive advisory service to clients, from initial sketch to completed trussed rafters. 1 Technical Data Design Trusses are designed in accordance with the current Code of Practice, which is BS 5268: Part 3, and the relevant Building Regulations. -
Builder's Guide to Trusses
Table of Contents Roof Construction Techniques: Pro’s and Con’s . 2 Trusses: Special Benefits for Architects and Engineers . 4 Special Benefits for Contractors and Builders . 5 Special Benefits for the Owner. 5 How Does A Truss Work? . 6 Typical Framing Systems. 8 Gable Framing Variations . 11 Hip Set Framing Variations . 13 Additional Truss Framing Options Valley Sets . 15 Piggyback Trusses . 17 Typical Truss Configurations . 18 Typical Truss Shapes. 20 Typical Bearing / Heel Conditions Exterior Bearing Conditions. 21 Crushing at the Heel . 22 Trusses Sitting on Concrete Walls . 22 Top Chord Bearing. 23 Mid-Height Bearing . 23 Leg-Thru to the Bearing. 23 Tail Bearing Tray. 24 Interior Bearing Conditions . 24 Typical Heel Conditions. 25 Optional End Cosmetics Level Return. 25 Nailer . 25 Parapet. 26 Mansard . 26 Cantilever. 26 Stub . 26 Bracing Examples . 27 Erection of Trusses . 29 Temporary Bracing . 30 Checklist for Truss Bracing Design Estimates . 32 Floor Systems . 33 Typical Bearing / Heel Conditions for Floor Trusses Top Chord, Bottom Chord, and Mid-Height Bearing. 34 Interior Bearing Conditions . 35 Ribbon Boards, Strongbacks and Fire Cut Ends . 36 Steel Trusses . 37 Ask Charlie V. 38 Charlie’s Advice on Situations to Watch Out for in the Field. 41 Glossary of Terms. 42 Appendix - References. 48 1 Builders, Architects and Home Owners today have many choices about what to use in roof and floor systems Traditional Stick Framing – Carpenters take 2x6, Truss Systems – in two primary forms: 2x8, 2x10 and 2x12 sticks of lumber to the job • Metal Plate Connected Wood Trusses – site. They hand cut and fit this lumber together Engineered trusses are designed and into a roof or floor system. -
Deck Framing Connection Guide
Deck Framing Connection Guide RECOMMENDATIONS FOR THE CONSTRUCTION OF CODE-COMPLIANT DECKS 800-999-5099 | www.strongtie.com Contents Introduction – Improperly Built Decks Can Be Dangerous. 3 Critical Deck Connections. 4 Existing Decks: Retrofit or Replace. .5 Selecting Connectors and Fasteners: Corrosion Issues. .6 Stainless-Steel Connectors and Fasteners . 7 Ledger Attachment. .8 Lateral Load Connection. .9 Footings. .10 Post Bases. .12 Beam-to-Post Connections. 13 Joists Terminating into Beam/Ledger . .14 Joists Bearing on a Beam. .15 Railing Post-to-Deck Framing . .16 Stair Stringers & Treads. 17 Fastening Deck Boards. .18 A Word About Building Codes This guide recommends connectors and fasteners for deck for details. Check with your local building department to verify construction that may meet the requirements of the 2006 what building codes have been adopted in your area. International Building Code® and the 2006 International Selection of products based upon performance and/or Residential Code®. The information contained here is a suitability for a specific application should be made by a summary of the requirements of these codes as they pertain qualified professional. Simpson Strong-Tie recommends that to the connections highlighted in this guide. The building codes contain other requirements regarding aspects of deck deck designs are approved by the local building department construction that are not addressed here, check the codes before construction begins. International Building Code and International Residential Code are registered trademarks of their respective organizations. LIMITED WARRANTY Simpson Strong-Tie Company Inc. warrants catalog products to be free from defects in and the condition of the soils involved, damage may nonetheless result to a structure material or manufacturing. -
Engineered Wood Products and Mass Timber Use in Wood Buildings
Engineered Wood Products and Mass Timber Use in Wood Buildings Daniel Hindman, Ph.D., P.E., Virginia Tech Associate Professor in Department of Sustainable Biomaterials at Virginia Tech for 17 years Classes Include Design of Wood Structures, Timber Engineering, Green Introduction Building Systems, Wood Mechanics and BIM for Wood-Based Structures Research Areas Include Development of Cross-Laminated Timber from Alternative Species, Mechanical Properties of Engineered Wood Products, Connection Design of Engineered Wood Products Discussion or inclusion of products in this presentation does not constitute an endorsement Products discussed serve as illustrations only Disclaimer Most products mentioned have several companies that produce similar or equivalent materials You should have a basic understanding of wood material properties You should be familiar with the National Design Specification for Assumptions Wood Construction (NDS) You should be familiar with ASD and LRFD factors (these will not of Audience be discussed but do apply according to the NDS) You should be familiar with the way that design stresses of wood materials are modified (base design values are found in the NDS Supplement, then modified for the particular design situation) Definition of EWPs Discussion of proprietary vs. nonproprietary materials and where to find design values Goals of Use of SCL and I-joists in taller wood construction along with Presentation detailing and connections An introduction to mass timber (Glulam & CLT) and how to design mass timber -
Glulam Handbook Volume 1
GLULAM HANDBOOK VOLUME 1 2013-10-17 GLULAM HANDBOOK Volume 1 CONTENTS INTRODUCTION GLULAM AS A STRUCTURAL MATERIAL Strength x Performance x Beauty = Wood3 = Glulam Glulam of course! THE HISTORY OF GLULAM The development of glued laminated timber New possibilities The breakthrough Nordic glulam The factory in Sweden The need for railway station halls The company AB Fribärande Träkonstruktioner Reliable material A growing market for Nordic glulam Highly advanced architecture FACTS ABOUT GLULAM GLULAM AND THE ENVIRONMENT Glulam in the life-cycle CERTIFICATION AND CONTROL CE-marking Factory production control PROPERTIES Timber species Adhesives Appearance quality 2 2 Size and form Strength properties Thermal qualities Moisture content Humidity movement Properties in a fire Durability GLULAM PRODUCTS Appearance and surface finishing Stock range Size tolerances Manufacturing standard Straight glulam members Curved glulam members Transport protection Erection PLANNING STRUCTURAL PREREQUISITES Constructional aspects of glulam structures Bracing of glulam structures Building envelope Moisture protection STRUCTURAL SYSTEMS Structural systems – an overview Beam – column system Glulam in multi-storey buildings Continuous beams Trusses Three-pin roof trusses Three-pin arches Three-pin portal frames Cantilevers Composite system CONCEPTUAL STRUCTURAL DESIGN Design load for roof structures Size tables Straight roof beams Double pitched beams Three-pin roof truss with steel ties Three-pin arches with steel ties Three-pin portal frames Roof purlins Floor -
Design Guide for Timber Roof Trusses
TFEC 4-2020 Design Guide for Timber Roof Trusses August 2020 This document is intended to be used by engineers to provide guidance in designing and evaluating timber roof truss structures. Do not attempt to design a timber roof truss structure without adult supervision from a qualified professional (preferably an experienced timber engineer). The Timber Frame Engineering Council (TFEC) and the Timber Framers Guild (TFG) assume no liability for the use or misuse of this document. TFEC-4 Committee: Jim DeStefano, P.E., AIA, F.SEI chairman Ben Brungraber, Ph.D., P.E. David Connolly, P.E. Jeff Hershberger, E.I. Jaret Lynch, P.E. Leonard Morse-Fortier, Ph.D., P.E. Robin Zirnhelt, P.Eng Illustrations by Ken Flemming and Josh Coleman Copyright © 2020 Timber Frame Engineering Council TFEC 4-2020 Page 2 Table of Contents Background 5 Truss Analysis 7 Ideal Trusses 7 Classical Methods 8 Graphical Methods 10 Squire Whipple 11 Computer Modeling 12 Truss Deflection and Camber 16 Development of Truss Forms 17 King Post Trusses 21 Queen Post Trusses 23 Howe Trusses 25 Pratt Trusses 26 Fink Trusses 27 Scissor Trusses 28 Hammer-Beam Trusses 31 Parallel Chord Trusses 34 Truss Joinery and Connections 36 Howe Truss Example 37 Scissor Truss Example 40 Scissor Truss with Clasping King 42 Block Shear 43 Friction and Joinery 45 Free Body Diagram 49 Steel Side Plates 50 Hardwood Pegs 53 Nuts and Bolts 55 Ogee Washers 57 TFEC 4-2020 Page 3 Split Rings and Shear Plates 58 Tension Joinery 59 Special Considerations 60 Truss Bracing 60 Raised and Dropped Bottom Chords 61 Curved Members 63 Grain Matched Glulams 68 Seasoning Shrinkage Considerations 69 Epilogue – Topped Out 71 TFEC 4-2020 Page 4 Background Man has been building with timber trusses for over 2,000 years. -
Forming Accessories Handbook Concrete Construction Products
BUILDING STRENGTH™ FORMING ACCESSORIES HANDBOOK CONCRETE CONSTRUCTION PRODUCTS Table of Contents General and Technical Information.............. 1 Medium/Heavy Forming ............................47 General Slabwork .......................................77 Definitions ....................................................................... 1 B1 Two Strut Coil Tie and B2 Four Strut Coil Tie ......... 47 C1B and C1C Wedge Hangers .....................................77 Safety Notes and Product Application ........................ 1 B1B3 and B2B3 Screw-On Coil Tie .......................... 48 C2 Coil Hanger Saddle Type ...................................... 78 Dayton Superior Technical Services ......................... 1 Coils ............................................................................... 49 C3 Coil Half Hanger .................................................... 79 Usage Affecting a Product’s Safe Working Load .............2 B6 Welding Coil Tie ..................................................... 49 C13 Plate Saddle Hanger ............................................ 79 Induced Tension Loads ................................................. 6 B7 and B22 Inserts (Crimp) ...................................... 49 C13A All-Wire Saddle Hanger ...................................80 Induced Shear Loads .................................................... 6 B11 Flat Washers ..........................................................50 C14 Channel Hanger.....................................................81 Combined Shear and -
Wind Tie-Down Connections – Getting It Right 32 Recommended Practice // June 2016
TECHNICAL DATA SHEET ISSUED BY TIMBER QUEENSLAND WIND TIE-DOWN CONNECTIONS – GETTING IT RIGHT 32 RECOMMENDED PRACTICE // JUNE 2016 Even at low wind speed classifications such as non-cyclonic N2, sheet roofed houses will have net wind uplift forces that need to be tied-down with specific tie-down connections. As site wind classifications increase all roof types require specific tie-down. Wind uplift forces increase in proportion to the square of the velocity of the wind so, for example, a site with a wind velocity of 61m/s (C2) will have 50% higher uplift forces than a 50m/s (C1) site. Getting every required tie-down connection right is critical as failure of one link in the tie- down chain can lead to loss of a whole roof in a wind event. This data sheet addresses common issues with tie-down and support that are regularly seen on building sites. Refer also to TDS 26 - Truss Installation and AS 1684 Part 2 and 3 for more detailed design information. MACHINE NAILING Care needs to be taken when using machine driven nails through joist hangers, framing anchors and tie-down straps etc. All connector manufacturers have specific recommendations on acceptable practices where machine nails are used. These cover minimum edge distances, types and sizes of nails as well as number of nails which usually have to be increased over the supplied standard nails to account for their smaller diameters. Following extensive consultation with industry, the Queensland Building and Construction Commission recently revised and released their requirements for use of gun nails in metal tie-down connections. -
Design of Wood Framing
CHAPTER 5 Design of Wood Framing 5.1 General This chapter addresses elements of above-grade structural systems in residential construction. As discussed in Chapter 1, the residential construction material most commonly used above grade in the United States is light-frame wood; therefore, this chapter focuses on structural design that specifies standard dimension lumber and structural wood panels (i.e., plywood and oriented strand board sheathing). Design of the lateral force resisting system (i.e., shearwalls and diaphragms) must be approached from a system design perspective and is addressed in Chapter 6. Connections are addressed in Chapter 7, and their importance relative to the overall performance of wood-framed construction cannot be overemphasized. The basic components and assemblies of a conventional wood frame home are shown in Figure 5.1; the reader is referred to Chapter 1 for more detailed references to house framing and related construction details. Many elements of a home work together as a system to resist lateral and axial forces imposed on the above-grade structure and transfer them to the foundation. The above-grade structure also helps resist lateral soil loads on foundation walls through connection of floor systems to foundations. Therefore, the issue of system performance is most pronounced in the above-grade assemblies of light-frame homes. Within the context of simple engineering approaches that are familiar to designers, system-based design principles are addressed in this Chapter. The design of the above-grade structure involves the following structural systems and assemblies: • floors; • walls; and • roofs. Residential Structural Design Guide 5-1 Chapter 5 - Design of Wood Framing Components and Assemblies of a Conventional Wood- FIGURE 5.1 Framed Home Each system can be complex to design as a whole; therefore, simple analysis usually focuses on the individual elements that constitute the system. -
Rough Framing
After the foundation is built and the batter boards are removed, the carpenter builds the framework. The framework consists of beams, trusses, walls and partitions, flooring, ceilings, sheathing and siding, stairways, roof framing and coverings (Chapter 7), and doors and windows (Chapter 8). This chapter familiarizes the carpenter with materials, tools, and techniques used to build the framework. TYPES OF FRAMING Framing consists of light, heavy, and expedient framing. LIGHT FRAMING There are three principal types of framing for light structures: western, balloon, and braced. Figure 6-1, page 6-2, illustrates these types of framing and specifies the nomenclature and location of the various members. Light framing is used in barracks, bathhouses, and administration buildings. Figure 6-2, page 6-3, shows some details of a 20-foot wide building (such as ground level, window openings, braces, and splices) and labels the framing parts. Much of light framing can be done in staging areas while staking out, squaring, and floor framing is being done. Subflooring can begin when a portion of the floor joists has been laid. The better-skilled men should construct the frame, and with good coordination, a large force of men can be kept busy during framing. Western Frame The western or platform frame (Figure 6-1, 1) is used extensively in military construction. It is similar to the braced frame, but has boxed-sill construction at each floor line. Also note that cross bridging is used between the joists and bridging is used between the studs. The platform frame is preferred for one-story structures since it permits both the bearing and nonbearing walls (which are supported by the joist) to settle uniformly. -
Steel-Ply Application Guide
PERFORM WITH PRECISIONPERFORM WITH PRECISION STEEL-PLY® STEEL-PLY ® CONCRETE FORMINGCONCRETE SYSTEMFORMING SYSTEM APPLICATION GUIDE APPLICATION GUIDE INNOVATION CENTER REAL-WORLD SOLUTIONS INNOVATION INSPIRED BY YOUR VISION CENTER REAL-WORLDYour vision is to take concrete construction SOLUTIONS to new heights. We turn that vision into real-world solutions through INSPIREDprecision research and BYdevelopment, YOUR testing andVISION technology. Your vision is to take concrete construction to new heights. Together we are redefining what is possible in the We turn that vision into real-world solutions through concrete construction industry. Our Innovation Center precision research and development, testing and technology. is comprised of: Together we are redefining what is possible in the concrete • A state construction of the art industry. chemical Our lab Innovation Center is • comprised A full-featured of: mechanical test facility • Product demonstration areas • AContemporary state of the arttraining chemical and labmeeting areas • A full-featured mechanical test facility Bring• Product us your demonstration ideas and we will areas deliver your solution. • Contemporary training and meeting areas Bring us your ideas and we will deliver your solution. Call today: 888-977-9600 Perform with Precision™ 800.876.4857 Call today: 888-977-9600 Perform with Precision™ STEEL-PLY® APPLICATION GUIDE Table of Contents Introduction ................................................................1 Adjustable Shear Wall Brackets .................................31