Effects of Surface Coatings on the Joint Formation During Magnetic Pulse Welding in Tube-To- Cylinder Configuration
Total Page:16
File Type:pdf, Size:1020Kb
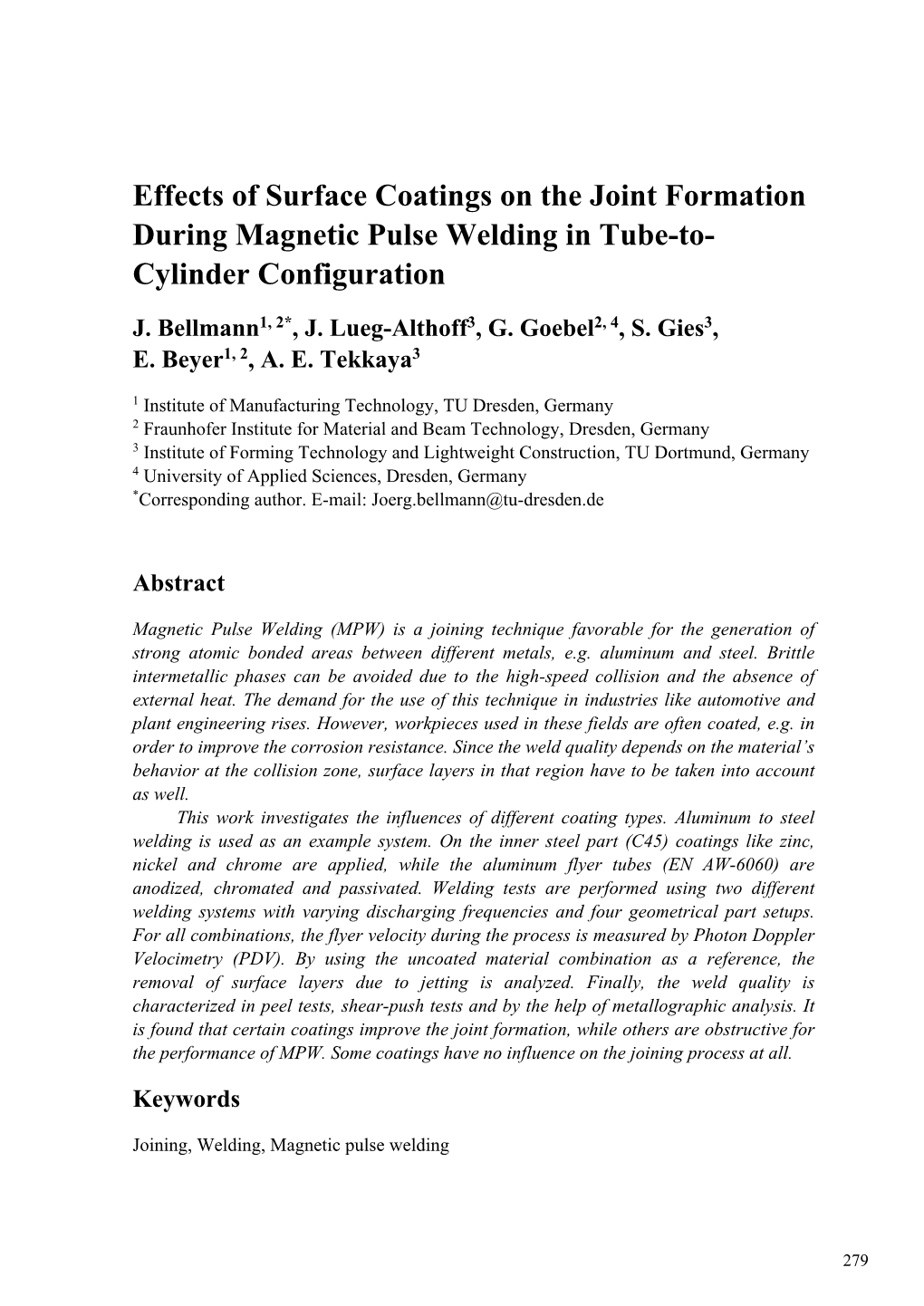
Load more
Recommended publications
-
Jet Composition in Magnetic Pulse Welding: Al-Al and Al-Mg Couples
Stern Supplement Aug2014112_Layout 1 7/14/15 2:31 PM Page 257 WELDING RESEARCH Jet Composition in Magnetic Pulse Welding: Al-Al and Al-Mg Couples MPW jet phenomena were investigated and jet material composition for similar Al alloys and two samples of dissimilar Al-Mg alloy couples were observed BY A. STERN, O. BECHER, M. NAHMANY, D. ASHKENAZI, AND V. SHRIBMAN the maximum magnetic pressure. The ABSTRACT acceleration of the outer tube through the standoff gap is higher near the open Magnetic pulse welding (MPW) produces a mechanically induced essentially solid end of the tube due to higher magnetic state but partially fusion-type weld, with an extremely small fusion zone and pressure and decreases down to zero at extremely high cooling rates. Composition of material jet emission in MPW was inves- the weld end where there is no move- tigated for similar and dissimilar metal lap joints. The jet residues emitted from Al/Al ment of the outer tube (Refs. 6–8). As a and Al/Mg lap joints were collected and characterized, and their composition was mi- croanalyzed by scanning electron microscopy with energy-dispersive spectometry result, the collision is oblique and the (SEM-EDS). The composition of the jet remains was governed by the degree of rela- initial part of the joint collides at a high tive density difference between the two metal components. The metal jet emitted collision angle and at very high collision during Al/Mg welding was mainly composed of Mg, the metal component with lower velocity; frequently, no bond is formed density. -
Solid State Welding
EAA Aluminium Automotive Manual – Joining 7. Solid state welding Content: 7. Solid state welding 7.0 Introduction 7.1 Friction welding 7.1.1 Friction welding of components 7.1.1.1 Rotational friction welding 7.1.1.2 Linear friction welding 7.1.1.3 Orbital and multi-orbital friction welding 7.1.2 Linear friction stir welding 7.1.2.1 The linear friction stir welding process 7.1.2.2 Application of linear friction stir welding 7.1.2.3 Variants of the linear friction stir welding technique 7.1.3 Friction stir spot welding 7.1.3.1 The friction stir spot welding technique 7.1.3.2 Further developments of the friction stir spot welding technique 7.1.4 Friction stud welding 7.1.5 Friction element welding 7.2 Pressure welding processes 7.2.1 Contact and cold pressure welding 7.2.2 Diffusion and hot pressure welding 7.2.3 Explosion welding 7.2.4 Electromagnetic pulse welding 7.2.5 Roll bonding 7.2.6 Co-extrusion welding 7.3 Ultrasonic welding Version 2015 ©European Aluminium Association ([email protected]) 1 7.0 Introduction Solid-state welding describes a group of joining techniques which produces coalescence at temperatures below the melting point of the parent materials without the addition of third material. External pressure and relative movement may or may not be used to enhance the joining process. This group of joining techniques includes e.g. friction (stir) welding, cold pressure welding, diffusion welding, explosion welding, electromagnetic pulse welding, , and ultrasonic welding. -
Magnetic Pulse Welding and Spot Welding with Improved Coil Efficiency—Application for Dissimilar Welding of Automotive Metal Alloys
Journal of Manufacturing and Materials Processing Article Magnetic Pulse Welding and Spot Welding with Improved Coil Efficiency—Application for Dissimilar Welding of Automotive Metal Alloys Chady Khalil, Surendar Marya and Guillaume Racineux * Research Institute in Civil and Mechanical Engineering (GeM, UMR 6183 CNRS), Ecole Centrale de Nantes, 1 rue de la Noë, F-44321 Nantes, France; [email protected] (C.K.); [email protected] (S.M.) * Correspondence: [email protected] Received: 4 June 2020; Accepted: 6 July 2020; Published: 8 July 2020 Abstract: Lightweight structures in the automotive and transportation industry are increasingly researched. Multiple materials with tailored properties are integrated into structures via a large spectrum of joining techniques. Welding is a viable solution in mass scale production in an automotive sector still dominated by steels, although hybrid structures involving other materials like aluminum are becoming increasingly important. The welding of dissimilar metals is difficult if not impossible, due to their differential thermo mechanical properties along with the formation of intermetallic compounds, particularly when fusion welding is envisioned. Solid-state welding, as with magnetic pulse welding, is of particular interest due to its short processing cycles. However, electromagnetic pulse welding is constrained by the selection of processing parameters, particularly the coil design and its life cycle. This paper investigates two inductor designs, a linear (I) and O shape, for the joining of sheet metals involving aluminum and steels. The O shape inductor is found to be more efficient both with magnetic pulse (MPW) and magnetic pulse spot welding (MPSW) and offers a better life cycle. -
Monthly Jurnal 2020 [January]
IIM METAL NEWS Vol. 23 No. 1 January 2020 C O Obituary 3 N T G D Birla Gold Medal Lecture 2019 Joining of Advanced Materials for E 4 Defence Systems N - G Madhusudhan Reddy T S IIM Chapter Activities 26 Seminars & Conferences 30 Members’ News 30 The IIM Metal News and The Indian Institute of Metals do not accept any responsibility for the statements made and the opinion expressed by the author(s) in the technical articles. Printed and Published by Shri Kushal Saha, Secretary General, on behalf of “The Indian Institute of Metals”, and printed at Print Max, 44, Biplabi Pulindas Street, Kolkata-700009 • Email : [email protected] and published at ‘Metal House’, Plot 13/4, Block AQ, Sector V, Salt Lake, Kolkata-700091, West Bengal, India E-mail: [email protected], [email protected] Phone: 033-2367 9768 / 2367 5004 Website: www.iim-india.net Fax: (033) 2367 5335 Editor : Dr. Santanu Ray Vol.23 No.1 JANUARY 2020 1 IIM METAL NEWS THE INDIAN INSTITUTE OF METALS PATRONS Mr R M Dastur Mr Sajjan Jindal Dr Baba Kalyani Mr Satish Pai ADVISORY COMMITTEE OF FORMER PRESIDENTS Mr R N Parbat Dr Dipankar Banerjee Prof K Chattopadhyay Mr L Pugazhenthy Mr M Narayana Rao Dr R N Patra Dr Sanak Mishra Mr H M Nerurkar Mr S S Mohanty Dr U Kamachi Mudali, Convenor COUNCIL FOR THE YEAR 2019-20 PRESIDENT Dr U Kamachi Mudali VICE PRESIDENT & CHAIRMAN VICE PRESIDENT & CHAIRMAN VICE PRESIDENT & CHAIRMAN Non-Ferrous Division Ferrous Division Metal Science Division Prof Amol A Gokhale Mr T V Narendran Dr Samir V Kamat IMMEDIATE FORMER PRESIDENT Mr Anand Sen SECRETARY GENERAL Mr Kushal Saha HON TREASURER CONTROLLER OF EXAMINATION CHIEF EDITOR, TRANSACTIONS MANAGING EDITOR, IIM METAL NEWS Mr Somnath Guha Prof P K Mitra Prof B S Murty Dr Santanu Ray Jt. -
VOCABULARI DE SOLDADURA Institut Tècnic Català De La Soldadura
VVOOCCAABBUULLAARRII DDEE SSOOLLDDAADDUURRAA VVOOCCAABBUULLAARRIIOO DDEE SSOOLLDDEEOO WWEELLDDIINNGG VVOOCCAABBUULLAARRYY CCCaaatttaaalllààà CCCaaasssttteeellllllààà AAAnnnggglllèèèsss CCCaaatttaaalllááánnn CCCaaasssttteeellllllaaannnooo IIInnnggglllééésss CCCaaatttaaalllaaannn SSSpppaaannniiissshhh EEEnnngggllliiissshhh 2a Edició VOCABULARI DE SOLDADURA institut tècnic català de la soldadura Rubí, Desembre de 2010 2a Edició www.itcsoldadura.org PRESENTACIÓ L’ITCS, mitjançant aquest recull de més de 3.000 paraules i termes en llengua catalana, castellana* i anglesa* relacionades principalment amb la soldadura i les tecnologies connexes, pretén la difusió del català en el sector del metall i, especialment, entre els professionals de la indústria catalana propers als processos de soldadura. * Els termes recollits tant en llengua castellana com en llengua anglesa responen, majoritàriament, a les equivalències que s’empren a Europa, és a dir, el significat d’aquests termes castellans i anglesos pot ser diferent a Amèrica. 1a Edició: Recull de 2.200 paraules i termes 2a Edició: Recull de 3.500 paraules i termes PRESENTACIÓN El ITCS, a través de esta recopilación de más de 3.000 palabras y términos en lengua catalana, castellana* e inglesa* relacionadas principalmente con la soldadura y las tecnologías conexas, pretende la difusión del catalán en el sector del metal y, especialmente, entre los profesionales de la industria catalana próximos a los procesos de soldadura. * Los términos recogidos tanto en lengua castellana como en lengua inglesa -
Probing Magnetic Pulse Welding of Thin-Walled Tubes
Journal of Manufacturing and Materials Processing Article Probing Magnetic Pulse Welding of Thin-Walled Tubes Koen Faes 1,* , Rishabh Shotri 2 and Amitava De 2 1 Belgian Welding Institute, Technologiepark Zwijnaarde 935, B-9052 Ghent, Belgium 2 Indian Institute of Technology, Bombay, Mumbai 400076, India; [email protected] (R.S.); [email protected] (A.D.) * Correspondence: [email protected] Received: 29 October 2020; Accepted: 9 December 2020; Published: 11 December 2020 Abstract: Magnetic pulse welding is a solid-state joining technology, based on the use of electromagnetic forces to deform and to weld workpieces. Since no external heat sources are used during the magnetic pulse welding process, it offers important advantages for the joining of dissimilar material combinations. Although magnetic pulse welding has emerged as a novel technique to join metallic tubes, the dimensional consistency of the joint assembly due to the strong impact of the flyer tube onto the target tube and the resulting plastic deformation is a major concern. Often, an internal support inside the target tube is considered as a solution to improve the stiffness of the joint assembly. A detailed investigation of magnetic pulse welding of Cu-DHP flyer tubes and 11SMnPb30 steel target tubes is performed, with and without an internal support inside the target tubes, and using a range of experimental conditions. The influence of the key process conditions on the evolution of the joint between the tubes with progress in time has been determined using experimental investigations and numerical modelling. As the process is extremely fast, real-time monitoring of the process conditions and evolution of important responses such as impact velocity and angle, and collision velocity, which determine the formation of a metallic bond, is impossible. -
Development of Analytical and Experimental Tools for Magnetic Pulse Welding Ethan Hunter Thibaudeau University of New Hampshire, Durham
University of New Hampshire University of New Hampshire Scholars' Repository Master's Theses and Capstones Student Scholarship Fall 2013 Development of analytical and experimental tools for magnetic pulse welding Ethan Hunter Thibaudeau University of New Hampshire, Durham Follow this and additional works at: https://scholars.unh.edu/thesis Recommended Citation Thibaudeau, Ethan Hunter, "Development of analytical and experimental tools for magnetic pulse welding" (2013). Master's Theses and Capstones. 826. https://scholars.unh.edu/thesis/826 This Thesis is brought to you for free and open access by the Student Scholarship at University of New Hampshire Scholars' Repository. It has been accepted for inclusion in Master's Theses and Capstones by an authorized administrator of University of New Hampshire Scholars' Repository. For more information, please contact [email protected]. DEVELOPMENT OF ANALYTICAL AND EXPERIMENTAL TOOLS FOR MAGNETIC PULSE WELDING BY ETHAN HUNTER THIBAUDEAU B.S., University of New Hampshire, 2011 Submitted to the University of New Hampshire In Partial Fulfillment of The Requirements for the Degree of Master of Science in Mechanical Engineering September, 2013 UMI Number: 1524460 All rights reserved INFORMATION TO ALL USERS The quality of this reproduction is dependent upon the quality of the copy submitted. In the unlikely event that the author did not send a complete manuscript and there are missing pages, these will be noted. Also, if material had to be removed, a note will indicate the deletion. Di!ss0?t&iori Piiblist’Mlg UMI 1524460 Published by ProQuest LLC 2013. Copyright in the Dissertation held by the Author. Microform Edition © ProQuest LLC. -
1 Intro and Contents
Steel Buildings Publication No. 35/03 Steel Buildings Publication No. 35/03 Apart from any fair dealing for the purposes of research The British Constructional Steelwork Association or private study or criticism or review, as permitted Limited (BCSA) is the national organisation for the steel under the Copyright Design and Patents Act 1988, this construction industry: its Member companies publication may not be reproduced, stored or undertake the design, fabrication and erection of transmitted in any form by any means without the prior steelwork for all forms of construction in building and permission of the publishers or in the case of civil engineering. Associate Members are those reprographic reproduction only in accordance with the principal companies involved in the purchase, design terms of the licences issued by the UK Copyright or supply of components, materials, services related to Licensing Agency, or in accordance with the terms of the industry. Corporate Members are clients, licences issued by the appropriate Reproduction professional offices, educational establishments which Rights Organisation outside the UK. support the development of national specifications, quality, fabrication and erection techniques, overall Enquiries concerning reproduction outside the terms industry efficiency and good practice. stated here should be sent to the publishers, The British Constructional Steelwork Association Ltd at the The principal objectives of the Association are to address given below. promote the use of structural steelwork; to assist specifiers and clients; to ensure that the capabilities and Although care has been taken to ensure, to the best of activities of the industry are widely understood and to our knowledge, that all data and information contained provide members with professional services in herein are accurate to the extent that they relate to technical, commercial, contractual and quality either matters of fact or accepted practice or matters assurance matters. -
An Exploratory Study Into the Feasibility of Magnetic Pulse Welding
An exploratory study into the feasibility of magnetic pulse welding Kevin Loncke Promotor: prof. dr. ir. Wim De Waele Begeleiders: Koen Faes (BIL) Masterproef ingediend tot het behalen van de academische graad van Master in de ingenieurswetenschappen: bouwkunde Vakgroep Mechanische constructie en productie Voorzitter: prof. dr. ir. Patrick De Baets Faculteit Ingenieurswetenschappen Academiejaar 2008-2009 De auteur en promotor geven de toelating deze scriptie voor consultatie beschikbaar te stellen en delen ervan te kopi¨eren voor persoonlijk gebruik. Elk ander gebruik valt onder de beperkin- gen van het auteursrecht, in het bijzonder met betrekking tot de verplichting uitdrukkelijk de bron te vermelden bij het aanhalen van resultaten uit deze scriptie. The author and promoter give the permission to use this thesis for consultation and to copy parts of it for personal use. Every other use is subject to the copyright laws, more specifically the source must be extensively specified when using from this thesis. Gent, Juni 2009 De promotor De begeleider De auteur Prof. dr. ir. W. De Waele ir. K. Faes Kevin Loncke Acknowledgments With the finishing of this master thesis, my time at Ghent University has almost come to an end. I am truly grateful to a large number of people who have helped me throughout my study and the fulfilling of this master thesis. First and foremost, I would like to express my appreciation to my promotor Prof. Dr. Ir. Wim De Waele, and my mentor Ir. Koen Faes. They were always prepared to give advice and feedback during the experimental research. I very much appreciate the time they took to read and re-read the numerous drafts of this thesis. -
High-Velocity Impact Welding Process: a Review
metals Review High-Velocity Impact Welding Process: A Review Huimin Wang 1 and Yuliang Wang 2,3,* 1 National Center for Materials Service Safety, University of Science and Technology Beijing, Beijing 100083, China; [email protected] 2 School of Mechanical Engineering and Automation, Beihang University, Beijing 100191, China 3 Beijing Advanced Innovation Center for Biomedical Engineering, Beihang University, Beijing 100191, China * Correspondence: [email protected]; Tel.: +86-1861-252-5756 Received: 26 December 2018; Accepted: 27 January 2019; Published: 28 January 2019 Abstract: High-velocity impact welding is a kind of solid-state welding process that is one of the solutions for the joining of dissimilar materials that avoids intermetallics. Five main methods have been developed to date. These are gas gun welding (GGW), explosive welding (EXW), magnetic pulse welding (MPW), vaporizing foil actuator welding (VFAW), and laser impact welding (LIW). They all share a similar welding mechanism, but they also have different energy sources and different applications. This review mainly focuses on research related to the experimental setups of various welding methods, jet phenomenon, welding interface characteristics, and welding parameters. The introduction states the importance of high-velocity impact welding in the joining of dissimilar materials. The review of experimental setups provides the current situation and limitations of various welding processes. Jet phenomenon, welding interface characteristics, and welding parameters are all related to the welding mechanism. The conclusion and future work are summarized. Keywords: impact welding; impact velocity; impact angle; welding interface 1. Introduction Welding technique has wide applications in the areas of aerospace, automobiles, shipbuilding, pressure vessels, and bridges. -
Magnetic Field Measurements During Magnetic Pulse Welding Using CMR-B-Scalar Sensors
sensors Article Magnetic Field Measurements during Magnetic Pulse Welding Using CMR-B-Scalar Sensors Voitech Stankevic 1,2,* , Joern Lueg-Althoff 3 , Marlon Hahn 3 , A. Erman Tekkaya 3, Nerija Zurauskiene 1,2 , Justas Dilys 1, Jonas Klimantavicius 1, Skirmantas Kersulis 1 , Ceslovas Simkevicius 1 and Saulius Balevicius 1 1 Center for Physical Sciences and Technology, Department of Functional Materials and Electronics, Sauletekio ave. 3, LT-10257 Vilnius, Lithuania; [email protected] (N.Z.); [email protected] (J.D.); [email protected] (J.K.); [email protected] (S.K.); [email protected] (C.S.); [email protected] (S.B.) 2 Faculty of Electronics, Vilnius Gediminas Technical University, Naugarduko 41, LT-03227 Vilnius, Lithuania 3 Institute of Forming Technology and Lightweight Components, TU Dortmund University, Baroper Str. 303, D-44227 Dortmund, Germany; joern.lueg-althoff@iul.tu-dortmund.de (J.L.-A.); [email protected] (M.H.); [email protected] (A.E.T.) * Correspondence: [email protected]; Tel.: +370-610-47928 Received: 16 September 2020; Accepted: 16 October 2020; Published: 20 October 2020 Abstract: The possibility of applying CMR-B-scalar sensors made from thin manganite films exhibiting the colossal magnetoresistance effect as a fast-nondestructive method for the evaluation of the quality of the magnetic pulse welding (MPW) process is investigated in this paper. This method based on magnetic field magnitude measurements in the vicinity of the tools and joining parts was tested during the electromagnetic compression and MPW of an aluminum flyer tube with a steel parent. -
Diploma Engineering Mechanical (Packaging) Project - Djj5141 Session December 2019
DIPLOMA ENGINEERING MECHANICAL (PACKAGING) PROJECT - DJJ5141 SESSION DECEMBER 2019 TITTLE: AUTOMATIC ARC WELDING MACHINE PROJECT ADVISOR: MR ROSLAN BIN KAMARUDDINN CLASS: DMP5B PREPARED BY: MUHAMMAD HAZIQ HAKIMI BIN MOHAD SHAHRIZAL (08DMP18F1080) 1 ACKNOWLEDGEMENT Grateful for divine intentions, we are able to successfully complete the final project within a set time frame without facing any difficult issues. We would like to thank everyone involved directly and indirectly especially our supervisor ENCIK ROSLAN BIN KAMARUDDIN who has provided us with all the guidance, advice, encouragement and constructive criticism we have been able to complete in the final report on this project. Please do not forget our friends and family members and our academic advisor SIR BRYAN TZE KEON HEE who was very helpful in terms of vision and finances in completing this final project assignment. We are grateful to Allah SWT for this final project. We hope that this report will serve as an example and a guide to future parties. 2 ABSTRACT Safety in welding is a very important aspect. Welding is one of the most widely used metal fabrication methods in world wide. Welding is safe operation when carried out under normal and correct workshop conditions, but it must be pointed out that equipment free from defects and well arranged, properly ventilated , tidy workplace are important factors for safe working. Even though, welding is carried out widely across the world, when certain basic measures and precautions are not followed, it results in injuries, discomfort, loss of eye sight after a longer period, or sometimes even leading to death of the people work there.