Optimization of Tungsten Inert Gas Welding on 6063 Aluminum Alloy on Taguchi Method
Total Page:16
File Type:pdf, Size:1020Kb
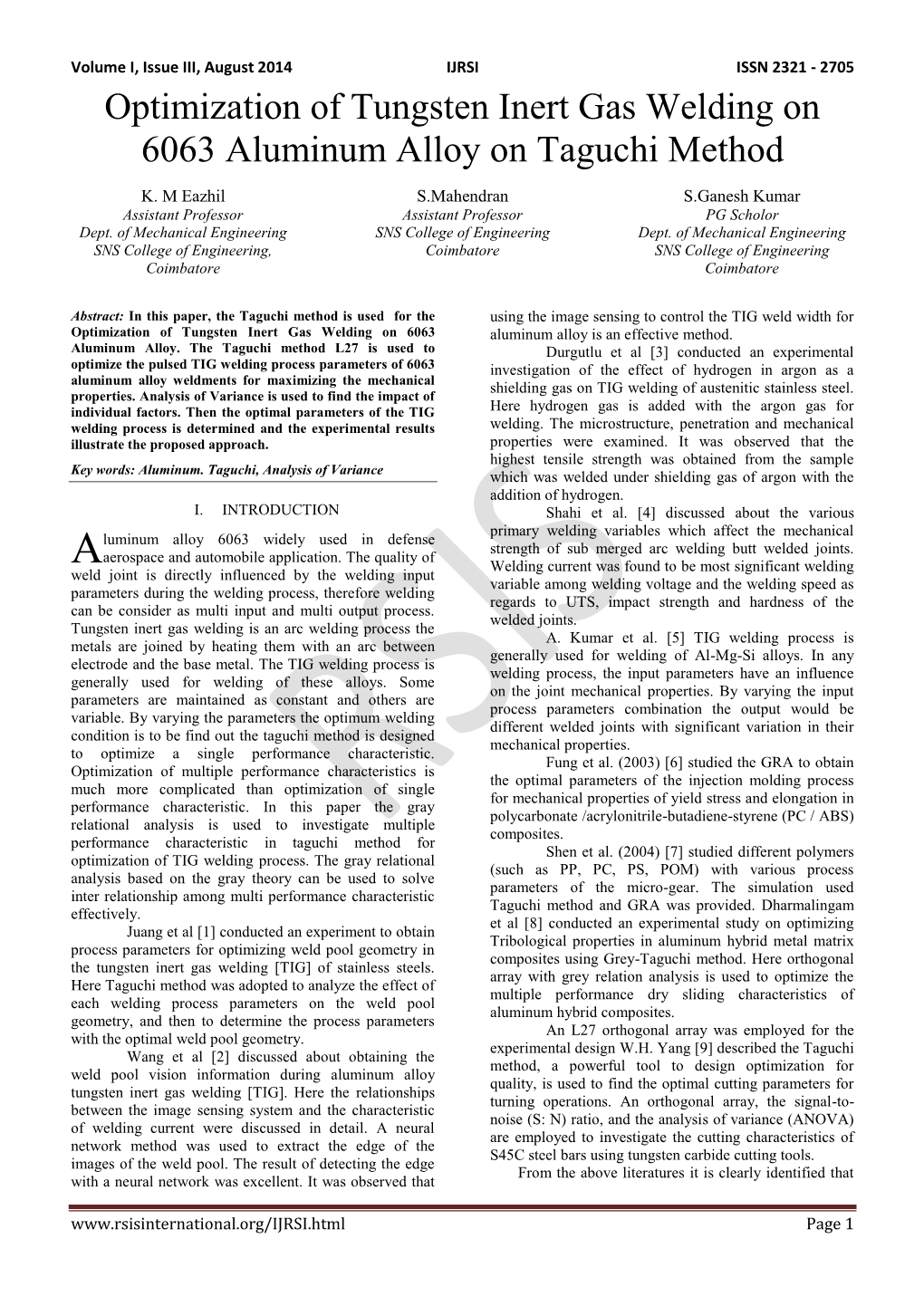
Load more
Recommended publications
-
Tensile Behavior of Aluminium Alloy 6063 - T6 in Sea Water
International Journal of Engineering Research and Development e-ISSN: 2278-067X, p-ISSN: 2278-800X, www.ijerd.com Volume 10, Issue 5 (May 2014), PP.68-74 Tensile Behavior of Aluminium Alloy 6063 - T6 In Sea Water P.John Maclins RVS Educational Trust’s Group of Institutions, Asst. Professor, Department of Aeronautical Engineering, Dindigul, Tamilnadu, India. Abstract:- Sea water, by virtue of its chloride content, is a most efficient electrolyte. The Omni-presence of oxygen in marine atmospheres, sea spray increases the aggressiveness of salt attack. The differential concentration of oxygen dissolved in a droplet of salt spray creates a cell in which attack is concentrated where the oxygen concentration is lowest. The sea environment is the most structurally hostile environment within which aircraft operate. The structural components are being exposed to salt spray continuously during its operation and it experiences heavy loading during landing. Corrosion also leads to crack propagation when subjected to loading. Corrosion along with damage leads to the failure of structural components prematurely and presents a serious problem in the aging aircraft. This requires a different approach to the maintenance of structural components subjected to corrosion and repetitive loads. This paper studies the effect of corrosion and low impact damage on aluminium alloy 6063- T6. The 6063 aluminium alloy that was used for the study was heat treated and soaked in seawater prepared per ASTM D1141 for different intervals of time between 0hours and 1000hours. Corroded specimens were subjected to low impact damage. The result shows a gradual degradation in mechanical properties of the alloy due to corrosion and damage. -
MATRIX Al-ALLOYS for SILICON CARBIDE REINFORCED METAL MATRIX COMPOSITES
IJRET: International Journal of Research in Engineering and Technology eISSN: 2319-1163 | pISSN: 2321-7308 INFLUENCE OF VOLUME FRACTION, SIZE, CRACKING, CLUSTERING OF PARTICULATES AND POROSITY ON THE STRENGTH AND STIFFNESS OF 6063/SICP METAL MATRIX COMPOSITES A. Chennakesava Reddy1 1Professor, Department of Mechanical Engineering, JNTUH College of Engineering, Kukatpally, Hyderabad – 500 085, Telangana, India Abstract The objective of this study is to examine the influence of volume fraction, size of particulates, formation of precipitates at the matrix/particle interface, particle cracking, voids/porosity, and clustering of particulates on the strength and stiffness of 6063/SiCp metal matrix composites. Tensile strength and stiffness increase with an increase in the volume fraction of SiC particulates. The tensile strength and stiffness decrease with increase in size of the particulates, presence of porosity, clustering, and particle cracking. Formation of particulate clusters is more prominent in the composites having very small-reinforced particulates. Mg2Si compound is likely to precipitate at the matrix/particle interfaces of 6063/SiC composite. Keywords: 6063, SiC, clustering, cracking, porosity, clustering --------------------------------------------------------------------***------------------------------------------------------------------ 1. INTRODUCTION matrix composite have become of principal importance for the manufacturer to make a quality product as per the Consolidation of a high strength ceramic particulate in a soft designer specifications. The objective of this work is to metal matrix is the technological renovation in the domain study the influence of the volume fraction and particle size of composites for the designer to assure high specific elastic of SiCp, clustering and cracking of particulates, modulus, strength-to-weight ratio, fatigue durability, and voids/porosity, and formation of precipitates at the wear resistance in the fields of aerospace and automotive particle/matrix interface on the tensile strength and stiffness applications. -
DEVELOPMENT and CHARACTERIZATION of Al-3.7%Cu-1.4%Mg ALLOY/PERIWINKLE ASH (Turritella Communis) PARTICULATE COMPOSITES
DEVELOPMENT AND CHARACTERIZATION OF Al-3.7%Cu-1.4%Mg ALLOY/PERIWINKLE ASH (Turritella communis) PARTICULATE COMPOSITES BY MICHEAL NEBOLISA NWABUFOH THE DEPARTMENT OF METALLURGICAL AND MATERIALS ENGINEERING AHMADU BELLO UNIVERSITY, ZARIA JUNE, 2015. DEVELOPMENT AND CHARACTERIZATION OF Al-3.7%Cu-1.4%Mg ALLOY/PERIWINKLE ASH (Turritella communis) PARTICULATE COMPOSITES BY Michael Nebolisa NWABUFOH, B. Eng (Met), E.S.U.T M.Sc/Eng/01731/2010-2011 A THESIS SUBMITTED TO THE SCHOOL OF POSTGRADUATE STUDIES, AHMADU BELLO UNIVERSITY, ZARIA. IN PARTIAL FULFILLMENT OF THE REQUIREMENTS FOR THE AWARD OF A MASTER DEGREE IN METALLURGICAL AND MATERIALS ENGINEERING. DEPARTMENT OF METALLURGICAL AND MATERIALS ENGINEERING, FACULTY OF ENGINEERING AHMADU BELLO UNIVERSITY, ZARIA. NIGERIA. JUNE, 2015 ii Declaration I hereby declare that, this research work titled "Development and Characterization of Al-3.7%Cu-1.4%Mg Alloy/Periwinkle Shell (Turritella communis) Ash Particulate Composites" was carried out by me, and the results of this research were obtained by tests carried out in the laboratory and all quotations are indicated by references. Name of Student Signature Date iii Certification This research work titled "Development and Characterization of Al-3.7%Cu- 1.4%Mg/Periwinkle (Turritella communis) Shell Ash Particulate Composites" by Nwabufoh M. Nebolisa with Registration Number M.Sc/Eng/01731/2010-2011 meets the regulations guiding the Award of Master degree in Metallurgical and Materials Engineering at Ahmadu Bello University, Zaria. ____________________ ________________ Prof. S.B. Hassan Date Chairman, Supervisor committee ____________________ _______________ Prof. G.B. Nyior Date Member, Supervisor committee ____________________ _______________ Prof. S.A. Yaro Date Head of Department _____________________ ________________ Prof. -
ISSN: 2320-5407 Int. J. Adv. Res. 7(9), 779-794
ISSN: 2320-5407 Int. J. Adv. Res. 7(9), 779-794 Journal Homepage: - www.journalijar.com Article DOI: 10.21474/IJAR01/9728 DOI URL: http://dx.doi.org/10.21474/IJAR01/9728 RESEARCH ARTICLE TAFEL POLARIZATION AND IMPEDANCE STUDIES OF AL-7075 ALLOY AND ITS COMPOSITES IN DIFFERENT MEDIUM. Sravanthi.M1, Dr.K.G.Manjunatha2, Dr.Saifulla Khan3 and Sunitha N4 1. Assistant professor, Department of Chemistry,AMC Engineeing College, Banneerghatta Main Road, Bangalore,Karnataka-560083, India. 2. Prof. and HOD R&D Centre, Department of Engineering Chemistry, Ghousia College of Engineering, Ramanagaram, Bangalore, Karnataka-56215, India. 3. Assistant professor, Department of Chemistry, Ghousia college of Engineering, B.M Road, Ramanagaram – Bangalore, Karnataka-562159, India. 4. Assistant Professor, Department of Chemistry, City Engineering College, Kanakapura Road, Bangalore, Karnataka-560083, India. …………………………………………………………………………………………………….... Manuscript Info Abstract ……………………. ……………………………………………………………… Manuscript History Aluminum metal matrix composites because of their high potential in Received: 09 July 2019 satisfying the recent demands have a wide variety of applications in Final Accepted: 12 August 2019 aviation, defense system, and automobile industries. It has been noticed Published: September 2019 in research that the properties of composites can be enhanced by the addition of ceramic particles like SiC and graphite to metal matrix Key words:- Al7075, OCP, Tafel polarization, EIS composites. This paper attempts on corrosion studies of Al 7075 base and SEM. alloy/SiC/graphite based composites in different inorganic acid mediums (0.1M HCl,0.1M H2SO4 medium) and neutral chloride medium (3.5% NaCl medium) by making use of Tafel Polarization Technique and Electrochemical Impedance Spectroscopy Technique. Test samples were casted by taking the various percent of SiC/graphite by stir casting method as per ASTM standards. -
Comparison of Aluminum Alloys from Aircraft of Four Nations Involved in the WWII Conflict Using Multiscale Analyses and Archival Study
heritage Article Comparison of Aluminum Alloys from Aircraft of Four Nations Involved in the WWII Conflict Using Multiscale Analyses and Archival Study Toufa Ouissi 1,2,*, Gilles Collaveri 3, Philippe Sciau 1, Jean-Marc Olivier 2 and Magali Brunet 1,* 1 CEMES, UPR 8011 CNRS, 31055 Toulouse, France; [email protected] 2 FRAMESPA, UMR 5136, University of Toulouse Jean-Jaurès, 31058 Toulouse, France; [email protected] 3 Aerocherche, 31700 Blagnac, France; [email protected] * Correspondence: [email protected] (T.O.); [email protected] (M.B.) Received: 30 September 2019; Accepted: 14 November 2019; Published: 22 November 2019 Abstract: Aluminum alloys are very interesting witnesses of industrial and technical development. The first ever developed was Duralumin, a light metal with good mechanical properties. In the 1930s, the rise of nationalism stimulated research and development, generating various aluminum alloys. This work reports the comparison of two versions of aluminum alloys, which were found in collected parts of WWII crashed aircraft from four nations: a Messerschmitt Bf 109 (DE), a Dewoitine D.520 (FR), and a P-51 Mustang (USA) and an Avro Lancaster (United Kingdom). The first version of alloy with magnesium content below or equal to 1 wt.% and the second version with higher magnesium content (1.5 wt.%), were identified as respectively AlCuMg1, AlCuMg2 in Germany; Duralumin, Duralumin F.R. in France; Hiduminium DU Brand, Hiduminium 72 in the UK and 17S, 24S in the USA. This study uses a multiscale approach based on historical research complimented by laboratory analyses of materials directly collected on the crashed aircraft. -
Constitutive Model of 6063 Aluminum Alloy Under the Ultrasonic Vibration Upsetting Based on Johnson-Cook Model
Ultrasonics 96 (2019) 1–9 Contents lists available at ScienceDirect Ultrasonics journal homepage: www.elsevier.com/locate/ultras Constitutive model of 6063 aluminum alloy under the ultrasonic vibration upsetting based on Johnson-Cook model T ⁎ Zhendong Xie, Yanjin Guan , Jun Lin, Jiqiang Zhai, Lihua Zhu Key Laboratory for Liquid-Solid Structural Evolution and Processing of Materials (Ministry of Education), Shandong University, Jinan 250061, China ARTICLE INFO ABSTRACT Keywords: Establishing an accurate constitutive relation in ultrasonic vibration assisted metal forming, can provides a Ultrasonic vibration reliable theoretical basis for analyzing the mechanism of the ultrasonic vibration on materials. A constitutive Johnson-Cook model model of 6063 aluminum alloy under the ultrasonic vibration upsetting at room temperature was constructed Strain rate based on Johnson-Cook Model and experimental results. The influence of amplitude and frequency on the yield Acoustic softening strength, hardening coefficient and exponent were analyzed quantitatively. Results showed that the yield Hardening strength was reduced due to the softening effect induced by the ultrasonic vibration. The maximum decreasing amount was 68.8% when imposing the maximum ultrasonic energy in this study. The hardening coefficient and exponent increased by 10.9% and 16.6% in maximum, respectively. However, the ultrasonic vibration has little impact on the strain rate hardening. The modified Johnson-Cook constitutive model under the ultrasonic vi- bration upsetting was established and was in good agreement with the experimental results. 1. Introduction ultrasonic intensity. Based on elastic-viscoplastic constitutive relation, He et al. [11] studied the variation of the uniaxial tensile stress and Considerable efforts are being devoted to the investigation of the strain under the vibration condition. -
Evaluación De La Resistencia a La Fatiga De La Aleación De Aluminio Aa-6061 Tratada Térmicamente Mediante Un Proceso De Envej
UNIVERSIDAD DE CARABOBO FACULTAD DE INGENIERÍA ESCUELA DE INGENIERÍA MECÁNICA EVALUACIÓN DE LA RESISTENCIA A LA FATIGA DE LA ALEACIÓN DE ALUMINIO AA-6061 TRATADA TÉRMICAMENTE MEDIANTE UN PROCESO DE ENVEJECIMIENTO ARTIFICIAL CON PERÍODOS DE 8 Y 10 HORAS. AUTORES: Martínez Motamayor, Javier Enrique Pérez Ramos, Nestor Osue TUTOR: Díaz, Eleazar Valencia, Noviembre del 2008 DEDICATORIA El presente trabajo especial de grado está dedicado primero que nada, a Dios por darme la oportunidad de llegar a donde he llegado y por ser siempre mi fortaleza en momentos de debilidad. En segundo lugar, a toda mi gran familia, pero en especial a mis padres Rubén José Martínez Pisani y Clara Cecilia Motamayor de Martínez, quienes me han enseñado grandes cosas a lo largo de mi vida, haciendo énfasis en los valores y el trabajo duro para alcanzar todas las metas propuestas. También quisiera dedicarlo a mi hermana Valeria Valentina Martínez Motamayor, por su cariño y apoyo incondicional. Por último, pero no menos importante, se lo dedico a mi Alma Mater la Universidad de Carabobo y a mi querido país Venezuela, de los cuales me siento orgulloso de provenir y que por ellos pienso luchar y trabajar para ayudar a que se desarrollen y progresen cada día más. Javier Enrique Martínez Motamayor DEDICATORIA No quiero que culmine mi carrera sin antes dar gracias a dios por darme la fuerza y su eterna compañía en los momentos difíciles de mi carrera. A mis padres que han sido, son y seguirán siendo mi apoyo incondicional cuando necesité un consejo a lo largo de toda mi vida. -
Tensile Fractography of Artificially Aged Al6061-B4c Composites
Proceedings of 3rd International Conference on Mechanical and Aeronautical Engineering Held on 18th- 19th January 2017, in Bangkok, Thailand. ISBN: 9788193137390 TENSILE FRACTOGRAPHY OF ARTIFICIALLY AGED AL6061-B4C COMPOSITES Gowri Shankar Achutha Kini Department of Mechanical and Manufacturing Department of Mechanical and Manufacturing Engineering, Manipal UniversityManipal Engineering, Manipal UniversityManipal Institute of Technology,Manipal, Institute of Technology,Manipal Karnataka State, India Karnataka State, India S S Sharma Department of Mechanical and Manufacturing Engineering, Manipal UniversityManipal Institute of Technology,Manipal Karnataka State, India Abstract— Presence of B4C reinforced particles in I. INTRODUCTION Al6061 alloy and various weight percentages of (2, Aluminum- magnesium-silicon alloys (Al-Mg-Si; also 4 and 6) on the hardness and tensile behaviour is denoted as 6xxx series), are medium strength, heat studied in the present work. Under different aging treatable alloys with good formability and corrosion temperatures the influence of artificial aging on the resistance. The 6061Al alloy has been studied mechanical properties was also assessed. Brinell extensively because of their technological importance macro hardness and mechanism of tensile fracture and farther increase in strength obtained by behavior have been discussed. Failure mode of precipitation hardening [1]. Aluminium matrix fracture surface is studied to determine the composites reinforced with ceramic particles such as parameters which influence the crack growth SiC, B4C, Al2O3 and TiC are the most commonly used characteristics. Lower temperature aging and materials in automobile and marine industries, have addition of B4C particles shows improvement in been paid more consideration because of high strength, hardness by 170% and tensile strength by 90% due high modulus and low density. -
Experimental Studies on Grey Cast Iron Reinforced Aa6061 Composite
EXPERIMENTAL STUDIES ON GREY CAST IRON REINFORCED AA6061 COMPOSITE 1SHIVAPRAKASH Y M, 2GOWRISHANKAR M C, 3SS SHARMA, 4K V SREENIVASA PRASAD 1MIT,Manipal,Karnataka,India; 2MIT,Manipal,Karnataka,India; 3MIT,Manipal,Karnataka,India; 4SJCE,Mysore,Karnataka,India E-mail: [email protected], [email protected], [email protected], [email protected] Abstract- Aluminium alloy composites are widely used because of their higher strength, stiffness and good wear resistance. In producing these composites the reinforcing materials used in common have been silicon carbide, aluminum oxide, boron carbide and graphite in the form of particles or whiskers. The ceramic particles reinforced aluminum composites are new generation materials which can be tailored for particular properties for specific application requirements. The particulates reinforced composite have best plastic forming ability than that of whisker or fiber counterpart and hence have emerged as most demanding reinforcements with great cost advantage. The particulate reinforced composites have been proved to be most suitable for heat and wear resistance applications. In the present study microstructure, hardness, tensile and impact properties of AA 6061based composite reinforced with Grey Cast Iron (GCI) is analyzed and presented. The presence of Grey Cast Iron resulted in improving the mechanical properties of their respective composites. The micrographs of the composites studied revealed the uniform distribution of the particles in the matrix system. Comparison of the characteristics study before and after heat treatment was done and it was found that there is an improvement in hardness, tensile strength and impact resistance of the composites as well as AA 6061 alloy after heat treatment. Index Terms- particulate, metal matrix composites, stir casting, heat treatment I. -
Review on Friction Stir Processed TIG and Friction Stir Welded Dissimilar Alloy Joints S
Preprints (www.preprints.org) | NOT PEER-REVIEWED | Posted: 25 October 2019 doi:10.20944/preprints201910.0226.v2 Peer-reviewed version available at Metals 2020, 10, 142; doi:10.3390/met10010142 “Review On Friction Stir Processed TIG And Friction Stir Welded Dissimilar Alloy Joints S. Mabuwa1*, V. Msomi1 1Cape Peninsula University of Technology, Faculty of Engineering and the Built Environment, P.O. Box 1906, Bellville, 7535, South Africa. *Corresponding author: [email protected];27219538778” Abstract “There is an increase towards reducing the weight of structures through the use of aluminium alloys in different industries like aerospace, automotive, etc. This growing interest would lead towards using dissimilar aluminium alloys which would require welding. TIG and friction stir welding are the well- known techniques that are currently suitable for joining dissimilar aluminium alloys. The welding of dissimilar alloys has its own dynamics which impact on the quality of the weld. This then suggests that there should be a process which can be used to improve the dissimilar alloys welds post their production. Friction stir processing is viewed as one of the techniques that could be used to improve the mechanical properties of the material. This paper reports on the status and the advancement of FSW, TIG and FSP technique. It further looks at the variation use of FSP on TIG and FSW welded joints with the purpose of identifying the knowledge gap.” KeyWords: Tensile analysis; Microhardness; Friction stir welding; TIG welding; Friction stir processing; Aluminium alloys; Microstructure. 1 Introduction “Aluminium alloys are known to be good candidates for different applications in various fields like aerospace, food packaging, automotive industries, etc. -
Elevated Temperature Effects on the Mechanical Properties of Age Hardened 6Xxx Series Aluminum Alloy Extrusions
Elevated Temperature Effects on the Mechanical Properties of Age Hardened 6xxx Series Aluminum Alloy Extrusions A Senior Project Presented to The Faculty of the Materials Engineering Department California State University, San Luis Obispo In Partial Fulfillment of the Requirements for the Degree: Bachelors of Science in Materials Engineering by Rachael Donovan Rose Fortune Robert Trout June 2015 0 Abstract The purpose of this project is to determine if over-aging of aluminum causes the yield or tensile strength to fall below the minimum strength values set by the aluminum industry. Extruded aluminum alloys, 6061-T6, 6063-T6, and two proprietary alloys, HS6X-T6 and RX82-T6, were exposed to reheating treatments at extended times and temperatures. The three temperatures were 350°F, 390°F, and 425°F. The times of reheat increased logarithmically from 30 minutes to 64 hours. The samples were tensile tested to determine the tensile strength and yield strength. Statistical methods helped model the behavior of yield and tensile strength as a function of alloy, time, and interaction of alloy and time for each temperature. This showed which alloy experienced a change in strength and at what time and temperature the strength fell below minimum acceptable values. The strongest to weakest untreated alloys respectively were HS6X, RX82, 6061, and 6063. As time progressed at each temperature, the strongest to weakest alloys changed to HS6X, 6061, RX82, and 6063 respectively. For the 6061 and 6063 alloys, the yield strength did not go below the lower bound value at 350°F, at 390°F it took 16 hours, and for 425°F it took 4 hours. -
MATRIX Al-ALLOYS for SILICON CARBIDE REINFORCED METAL MATRIX COMPOSITES
IJRET: International Journal of Research in Engineering and Technology eISSN: 2319-1163 | pISSN: 2321-7308 INFLUENCE OF VOLUME FRACTION, SIZE, CRACKING, CLUSTERING OF PARTICULATES AND POROSITY ON THE STRENGTH AND STIFFNESS OF 6063/SICP METAL MATRIX COMPOSITES A. Chennakesava Reddy1 1Professor, Department of Mechanical Engineering, JNTUH College of Engineering, Kukatpally, Hyderabad – 500 085, Telangana, India Abstract The objective of this study is to examine the influence of volume fraction, size of particulates, formation of precipitates at the matrix/particle interface, particle cracking, voids/porosity, and clustering of particulates on the strength and stiffness of 6063/SiCp metal matrix composites. Tensile strength and stiffness increase with an increase in the volume fraction of SiC particulates. The tensile strength and stiffness decrease with increase in size of the particulates, presence of porosity, clustering, and particle cracking. Formation of particulate clusters is more prominent in the composites having very small-reinforced particulates. Mg2Si compound is likely to precipitate at the matrix/particle interfaces of 6063/SiC composite. Keywords: 6063, SiC, clustering, cracking, porosity, clustering --------------------------------------------------------------------***------------------------------------------------------------------ 1. INTRODUCTION matrix composite have become of principal importance for the manufacturer to make a quality product as per the Consolidation of a high strength ceramic particulate in a soft designer specifications. The objective of this work is to metal matrix is the technological renovation in the domain study the influence of the volume fraction and particle size of composites for the designer to assure high specific elastic of SiCp, clustering and cracking of particulates, modulus, strength-to-weight ratio, fatigue durability, and voids/porosity, and formation of precipitates at the wear resistance in the fields of aerospace and automotive particle/matrix interface on the tensile strength and stiffness applications.