Objective Tyre Development Band 57 Quantification of Their Conflicts of Tyre Characteristics and Analysis and Definition Objective Tyre Development Peckelsen Ulrico
Total Page:16
File Type:pdf, Size:1020Kb
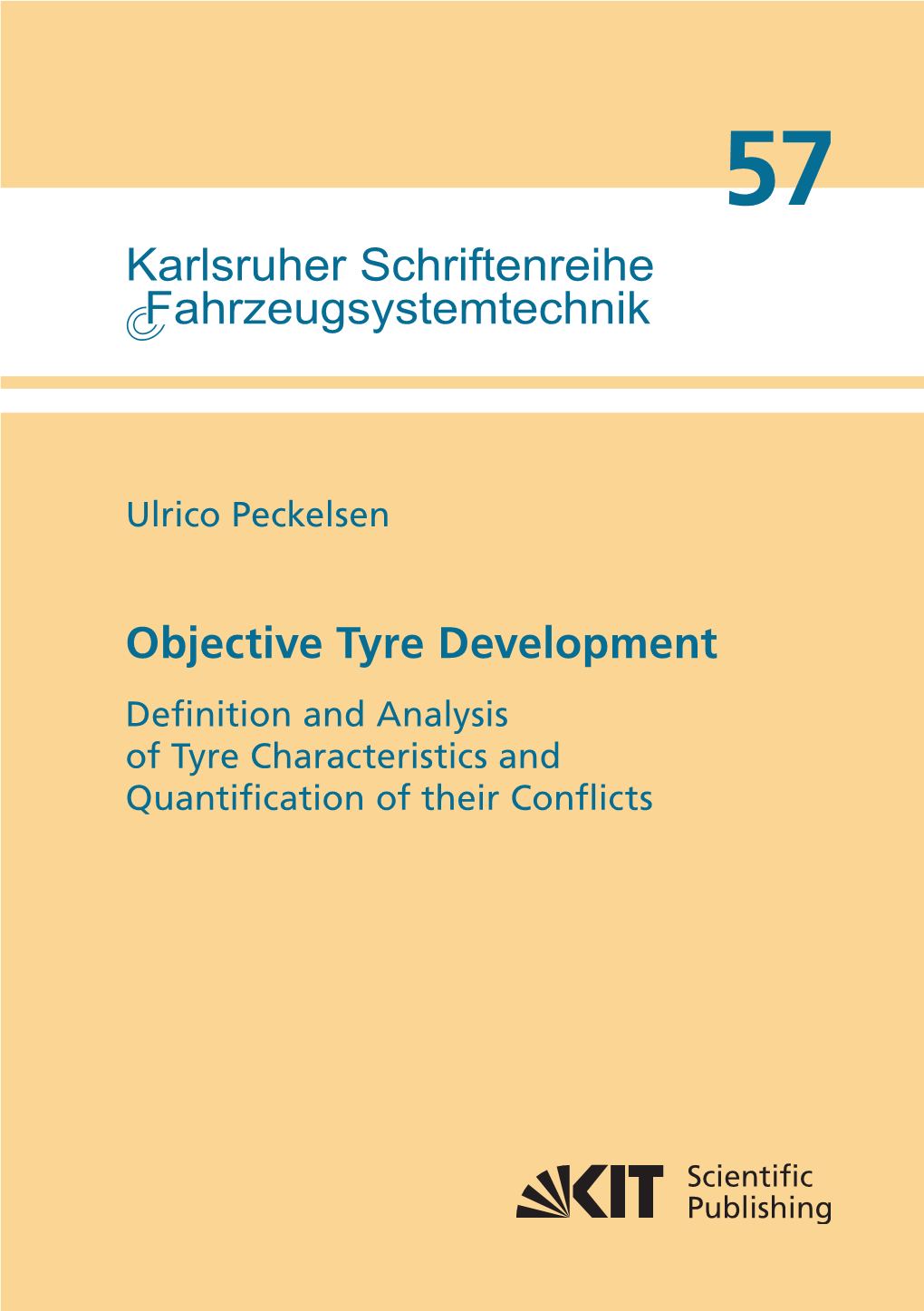
Load more
Recommended publications
-
Performance Analysis of Constant Speed Local Abstacle Avoidance Controller Using a MPC Algorithym on Granular Terrain Nicholas Haraus Marquette University
Marquette University e-Publications@Marquette Master's Theses (2009 -) Dissertations, Theses, and Professional Projects Performance Analysis of Constant Speed Local Abstacle Avoidance Controller Using a MPC Algorithym on Granular Terrain Nicholas Haraus Marquette University Recommended Citation Haraus, Nicholas, "Performance Analysis of Constant Speed Local Abstacle Avoidance Controller Using a MPC Algorithym on Granular Terrain" (2017). Master's Theses (2009 -). 443. http://epublications.marquette.edu/theses_open/443 PERFORMANCE ANALYSIS OF A CONSTANT SPEED LOCAL OBSTACLE AVOIDANCE CONTROLLER USING A MPC ALGORITHM ON GRANULAR TERRAIN by Nicholas Haraus, B.S.M.E. A Thesis submitted to the Faculty of the Graduate School, Marquette University, in Partial Fulfillment of the Requirements for the Degree of Master of Science Milwaukee, Wisconsin December 2017 ABSTRACT PERFORMANCE ANALYSIS OF A CONSTANT SPEED LOCAL OBSTACLE AVOIDANCE CONTROLLER USING A MPC ALGORITHM ON GRANULAR TERRAIN Nicholas Haraus, B.S.M.E. Marquette University, 2017 A Model Predictive Control (MPC) LIDAR-based constant speed local obstacle avoidance algorithm has been implemented on rigid terrain and granular terrain in Chrono to examine the robustness of this control method. Provided LIDAR data as well as a target location, a vehicle can route itself around obstacles as it encounters them and arrive at an end goal via an optimal route. This research is one important step towards eventual implementation of autonomous vehicles capable of navigating on all terrains. Using Chrono, a multibody physics API, this controller has been tested on a complex multibody physics HMMWV model representing the plant in this study. A penalty-based DEM approach is used to model contacts on both rigid ground and granular terrain. -
Mitas Tires – Designed to Perform in Your Fields
AGRICULTURAL RADIAL TIRES Mitas Tires – DESIGNED TO PERFORM IN YOUR FIELDS • Product Information • Warranty Policy • Service After the Sale www.mitasag.com A TECHNOLOGY FOR TECHNOLOGY Agricultural technology is evolving rapidly, and today’s high-horsepower tractors and combines demand tires that can keep up with the pace. That’s why Mitas is committed to providing advanced radial tires to ensure your farming operation is expertly outfitted from the ground up. If your tires aren’t up to speed with your machinery, you may experience: • Subpar machine performance • Decreased productivity • Increased operating costs • Suboptimal crop yields • Lost profits EXPERTISE MEANS EVERYTHING Given the high stakes and rewards of your operation, would you rather buy your tires from a manufacturer that dabbles in agriculture or one that focuses all its resources solely on agricultural and off-road tires? At Mitas, agriculture alone accounts for 70 percent of our global business. When you purchase Mitas premium-grade agricultural radial tires, you can be confident they are engineered and manufactured to exacting standards for superior quality, durability and performance. 1 Table of Contents Tire applications .............................................................................3 List of tire sizes ...............................................................................5 SuperFlexionTire (SFT) .................................................................7 Combine drive tires: AC 70 H / G / N and SuperFlexionTire (SFT) .................................................. -
Summer, All-Season and Winter Tyres 2018 Passenger Car and Van
SUMMER, ALL-SEASON AND WINTER TYRES 2018 PASSENGER CAR AND VAN SPORTY. STRONG. SAFE! Viking. A brand of Continental. SUMMER TYRES 2018 SPORTY. STRONG. SAFE! Viking is a brand of Continental, developed in Germany and manufactured in Europe. With more than 80 years of experience ProTech HP CityTech II TransTech II as a European tyre manufacturer and the continuous further development of For middle-class vehicles For compact- and For transporter our products in state-of-the-art develop- and executive cars. middle-class cars. and vans. ment centres, Viking stands for cutting- edge technology. Convincing ALL-SEASON & WINTER TYRES 2017/18 quality features Sporty: Outstanding performance, even for powerful vehicles Strong: Durable products which deliver even in demanding conditions FourTech FourTech Van WinTech WinTech Van Safe: For compact- and For transporter For compact- and For transporter Reliable protection due to state-of-the- middle-class cars. and vans. middle-class cars. and vans. art technology 2 3 ProTech HP The UHP tyre CityTech II The compact tyre The well balanced high performance tyre The CityTech II is an economical attractive tyre with sporting capabilities. with low rolling resistance and high mileage. For middle-class vehicles and executive cars. For compact-class and middle-class vehicles. Technical highlights Technical highlights Exemplary handling in dry conditions. Improved protection against aquaplaning. The closed outer shoulder of the tyre increases the The modern lateral groove system in the tread transverse rigidity and enlarges the area in contact grooves means that water is effectively channelled with the road. This results in exemplary handling in from the contact area in the middle to the large dry conditions and improves the transfer of forces, circumferential grooves. -
FOCUS on TYRES PASSENGER CAR TYRES Table of Contents
FOCUS ON TYRES PASSENGER CAR TYRES Table of contents Signs of wear Information about tyres and damage 1 and wheels 2 Wear on both shoulders 4 Tyre structure 20 Wear in the centre of the tread 5 Markings on the sidewall of the tyre 21 Foreign object puncture in tread 6 Tread depth 22 Sidewall wear or damage 7 Tyre life, rolling resistance and fuel consumption 23 Totally broken tyre 8 Maximum speed (speed limit symbol) 24 Bulge or deformation in sidewall 9 Maximum load capacity (load index 25 Saw-tooth wear (cupping) 10 or load capacity code) Uneven wear 11 Tyres and legal requirements (general) 26 Toe wear 12 Tyres and legal requirements (tyre label) 27 Camber wear 13 Run-flat tyres 28 Brake mark 14 TPMS (Tyre Pressure Monitoring System) 29 Age-related cracks 15 Summer, All-season and Winter tyres 30 Steering complaint: The car or steering wheel shakes 16 Steering complaint: car pulls to one side 17 DISCLAIMER: Although this brochure was produced with due care, those involved in its production accept no liability whatsoever for any incomplete- ness or inaccuracy in this publication. 2 Signs of wear and damage 1 Wear on both tread shoulders situation possible cause advice The wear on the shoulders is greater than in the 1. Driving with underinflated tyres due to: 1. Find the cause and: centre of the tread (round wear). Low-section tyres a. negligence a. inform the driver are more prone to this wear pattern. b. punctured tyre b. depending on the leak: repair or c. leaking valve replace the tyre d. -
European Tyre and Rim Technical Organisation RETREADED TYRES
European Tyre and Rim Technical Organisation RETREADED TYRES IMPACT OF CASING AND RETREADING PROCESS ON RETREADED TYRES LABELLED PERFORMANCES European Tyre and Rim Technical Organisation Content 1. Executive summary ........................................................................................................................... 4 2. Retreaded tyres: reminder of concept, definition and vocabulary ....................................................... 5 3. Impact of casing on retreaded tyre rolling resistance ......................................................................... 6 3.1. Results summary........................................................................................................................ 6 3.2. Design of Experiment description ............................................................................................... 6 3.3. Detailed results .......................................................................................................................... 6 3.3.1. Global casing impact ........................................................................................................... 6 3.3.2. Impact of casing brand ........................................................................................................ 9 3.3.3. Impact of casing unit ........................................................................................................... 9 3.3.4. Impact of casing age ........................................................................................................ -
VTI Rapport 971A Published 2021 Vti.Se/Publications
The effect of water and snow on the road surface on rolling resistance Annelie Carlson Tiago Vieira VTI rapport 971A Published 2021 vti.se/publications VTI rapport 971 A The effect of water and snow on the road surface on rolling resistance Annelie Carlson Tiago Vieira Author: Annelie Carlson, VTI, http://orcid.org/0000-0002-8957-8727 Tiago Vieira, VTI, https://orcid.org/0000-0001-8057-6031 Reg.No.: 2016/0589-9.1 Publication: VTI rapport 971A Published by VTI, 2021 Publikationsuppgifter – Publication Information Titel/Title Effekten på rullmotstånd av vatten och snö på vägytan/The effect of water and snow on the road surface on rolling resistance Författare/Author Annelie Carlson, Linköpings Universitet, http://orcid.org/0000-0002-8957-8727 Tiago Vieira, VTI, https://orcid.org/0000-0001-8057-6031 Utgivare/Publisher VTI, Statens väg- och transportforskningsinstitut/ Swedish National Road and Transport Research Institute (VTI) www.vti.se/ Serie och nr/Publication No. VTI rapport 971A Utgivningsår/Published 2021 VTI:s diarienr/Reg. No., VTI 2016/0589-9.1 ISSN 0347–6030 Projektnamn/Project State-of-the-art om påverkan av vatten och snö på rullmotstånd/State-of-the-art om påverkan av vatten och snö på rullmotstånd Uppdragsgivare/Commissioned by Trafikverket/Swedish Transport Administration Språk/Language Engelska/English Antal sidor inkl. bilagor/No. of pages incl. appendices 43 VTI rapport 971A 3 Sammanfattning Effekten på rullmotstånd av vatten och snö på vägytan av Annelie Carlson (VTI) och Tiago Vieira (VTI) Rullmotstånd uppkommer vid interaktionen mellan vägyta och däck och utgör en del av det färdmotstånd som ett fordon behöver överkomma för att röra sig framåt. -
The Effect of the Tractor Tires Load on the Ground Loading Pressure
ACTA UNIVERSITATIS AGRICULTURAE ET SILVICULTURAE MENDELIANAE BRUNENSIS Volume 65 165 Number 5, 2017 https://doi.org/10.11118/actaun201765051607 THE EFFECT OF THE TRACTOR TIRES LOAD ON THE GROUND LOADING PRESSURE Lukáš Renčín1, Adam Polcar1, František Bauer1 1 Department of Technology and Automobile Transport, Faculty of AgriSciences, Mendel University in Brno, Zemědělská 1, 613 00 Brno, Czech Republic Abstract RENČÍN LUKÁŠ, POLCAR ADAM, BAUER FRANTIŠEK. 2017. The Effect of the Tractor Tires Load on the Ground Loading Pressure. Acta Universitatis Agriculturae et Silviculturae Mendelianae Brunensis, 65(5): 1607 – 1614. The contribution, based on the experimental measurement, analyses the issue of a specific pad loading pressure in relation to radial wheel load and tire inflation. Tile inflation in terms of allowed radial load, which we wish to be high as far as possible in terms of the power transmission from the wheels to the ground is important for the field tensile works, on the other hand, the pressure in the tire is closely related to the contact area and ground loading pressure. The obtained results show the following: Michelin Multibib 650/65 R38 tire, inflated to a pressure of 80 kPa has a sufficient reserve in radial load. As the measurement results show, ground loading pressure at the highest load of 36.55 kN, which was used during the measurement, is under the value of 100 kPa, which would mean on loamy soil at a humidity of 17 % that the limit of the ground pressure on the ground has not been exceeded. Keywords: stress transmission, tire inflation pressure, area of imprint, pressure in area of imprint layer. -
State-Of-The-Art Report Page 1 of 45
Low Emission Optimised tyres and road surfaces for electric and hybrid vehicles State -of -the -Art Report Piotr Mioduszewski Circulation: All Partners File Version Date WP Status LEO-TUG-WP1-D001- 20131231-(State-of- 0.1 2013-12-31 1 draft the-Art Report).doc State-of-the-Art Report Page 1 of 45 CORE 2013 Project Proposal No. 196195 NCBiR decision No 87/2013 Project Officer (NCBiR): Maciej Jędrzejek Since 2013-11-13: Konrad Kosecki Starszy Specjalista Dział Zarządzania Programami Narodowe Centrum Badań i Rozwoju tel. 22 39-07-460 [email protected] State-of-the-Art Report Page 2 of 45 List of Contents 1 OBJECTIVE........................................................................................................................................ 4 2 INTRODUCTION................................................................................................................................ 4 3 HISTORICAL REVIEW ........................................................................................................................ 5 4 ECONOMIC AND USER INCENTIVES FOR ELECTRIC VEHICLES.......................................................... 7 4.1 Incentives in Norway .................................................................................................................... 7 4.2 Incentives in Poland...................................................................................................................... 7 5 POWERTRAIN CONCEPTS OF ZERO AND LOW EMISSION VEHICLES............................................... -
Chapter 1. Tuning of Iveco Stralis Multibody Model in Adams/Car 14
POLITECNICO DI TORINO MECHANICAL AND AEROSPACE ENGINEERING DEPARTMENT Master’s Degree Course in Automotive Engineering Master’s Degree Thesis EXPERIMENTAL-NUMERICAL COMFORT ANALYSIS OF A HEAVY-DUTY VEHICLE Academic supervisors: Prof. Mauro VELARDOCCHIA Prof. Enrico GALVAGNO Company supervisor: Dott. Vladi Massimo NOSENZO Student: Michele GALFRE’ ACADEMIC YEAR 2018–2019 Index INDEX ............................................................................................................................................. 2 ABSTRACT .................................................................................................................................... 4 PICTURE INDEX .......................................................................................................................... 5 TABLE INDEX ............................................................................................................................. 10 INTRODUCTION ........................................................................................................................ 11 THE COMPANY ..................................................................................................................... 12 IVECO STRALIS ..................................................................................................................... 12 CHAPTER 1. TUNING OF IVECO STRALIS MULTIBODY MODEL IN ADAMS/CAR 14 1.1 POSITIONING ................................................................................................................... 15 1.2 -
How to Optimize Your Tyre Pressures and Temperatures on Your Caravan
How to Optimize your Tyre Pressures and Temperatures on your Caravan/Camperinsert image here: and your150 x 80mm vehicle www.kimberleygroup.com.au 20121126 2 Importance of Optimum Tyre Pressure and Temperature Table of Contents 1. Why is tyre pressure and temperature so crucial? 2. What is the link between Tyre Pressure and Temperature? 3. Getting the starting pressure right 4. Adjusting the pressure with the 4PSI rule 5. Adjusting the pressure to the optimum 6. TPMS 7. Suggested Pressure and Speed for conditions 8. Conversion Table 9. Is there an Optimum Tyre Size? 10. Acceleration, Braking and Load Transfer 11. Specifications of TPMS 12. TPMS Kit from Kimberley 13. Tyre Markings/ Tyre Size 14. Tyre Ageing kimberleygroup.com 3 Importance of Optimum Tyre Pressure and Temperature This eBook addresses the question: How much of Australia do you want to experience? kimberleygroup.com 4 Importance of Optimum Tyre Pressure and Temperature Why is Tyre Pressure so crucial? Your tyre’s inflation pressure is measured as pounds per square inch, (psi) or “Bar (metric). The maximum recommended psi for your tyres printed right on them. However, manufacturers may print a lower recommended psi than your tyre can truly handle because the lower inflation rate will give you a softer ride. If you over inflate your tyres, you might cause some safety hazards. You’ll definitely wear out the tyres more quickly. A tyre that is over inflated shows more wear along the center width of the tyre than along its edges. When your tyres develop uneven tread wear, it shortens the overall life expectancy of your tyre. -
Tire & Track Pressures
December 2014 THE LEADER IN NO-TILL SEEDING TECHNOLOGY Tire & Track Pressures: Goal-setting by Matt Hagny, consulting agronomist for no-till systems since ‘94. Thinking about upgrading tractors, combines, sprayers? The features and capacity are what everyone dreams of and drools over. The tires (or tracks) to carry that newer equipment are always an afterthought. Gee, the price to upgrade that piece of equipment is soooo much that we ran out of money in our budget and we’ll just get by with whatever tires are standard—which are always too small (just enough to roll the machine out the OEM’s door L). With upgrades, the machine weight always seems to creep up, up, up—and which now are truly of monstrous proportions. You really ought to be thinking about how the extra machine weight should be carried before you seriously contemplate an upgrade. And don’t think, “Well, it’s almost as good as my current setup,” because nearly everything I see in the field is causing major soil problems—especially in the low-OM and more highly weathered soils (more ancient geologically) that are found in the Winter wheat failed to make a stand and survive southern USA (let’s use the rough guideline of Interstate 80 again to define the winter in tractor & air cart tracks from ‘southern’), or any other soils that are degraded. seeding the previous soybean crop. The transport wheels on the wings of the drill are also visible. And the track angling across is a sprayer track. But first: How serious is this compaction anyway? You probably get a lot Sprayer had correct inflation of 22 psi (lowest of different views. -
Airframes and Systems
Airframes and Systems I. Fuselage II. Cockpit and Cabin Window III. Wing IV. Stabilizing surfaces V. Landing gear VI. Flight controls (construction and operation) VII. Hydraulics VIII. Air Driven System (Piston Engine) IX. Air Driven System (Turbo propeller And Jet Aircraft) X. Non-pneumatic operated de-ice and anti-ice systems XI. Fuel System Fuselage: 1.What are the most frequent used materials in a monocoque or semi-monocoque structure? A) Wood. B) Composite fibres. C) Aluminium or magnesium alloy. D) Steel. A framework of truss type fuselage is used in: A) Supersonic aircraft B) Medium range commuter type turbo-props C) Heavy wide bodied subsonic turbo-fan aircraft D) Light training aircraft mainly A semi-monocoque fuselage has... in the longitudinal direction. Together with the frames, they resist... moments and axial forces. The skin panels are loaded mainly in... A) Bars, buckling, bending. B) Stringers, bending, shear. C) Spars, torsion, shear. D) Stringers, bending, buckling. Aircraft structures consists mainly of: A) Magnesium alloy sheets with aluminium rivets and titanium or steel at points requiring high strength. B) Light alloy steel sheets with copper rivets and titanium or steel materials at points requiring high strength. C) Aluminium alloy sheets and rivets with titanium or steel materials at points requiring high strength. D) Aluminium sheets and rivets with titanium or steel materials at points requiring high strength. What is the purpose of the stringers? A) To absorb the torsional and compressive stresses. B) To support the primary control surfaces. C) To produce stress risers. D) To prevent buckling and bending by supporting and stiffening the skin.