Reactions of Nickel-Based Ohmic Contacts with N-Type 4H Silicon Carbide B
Total Page:16
File Type:pdf, Size:1020Kb
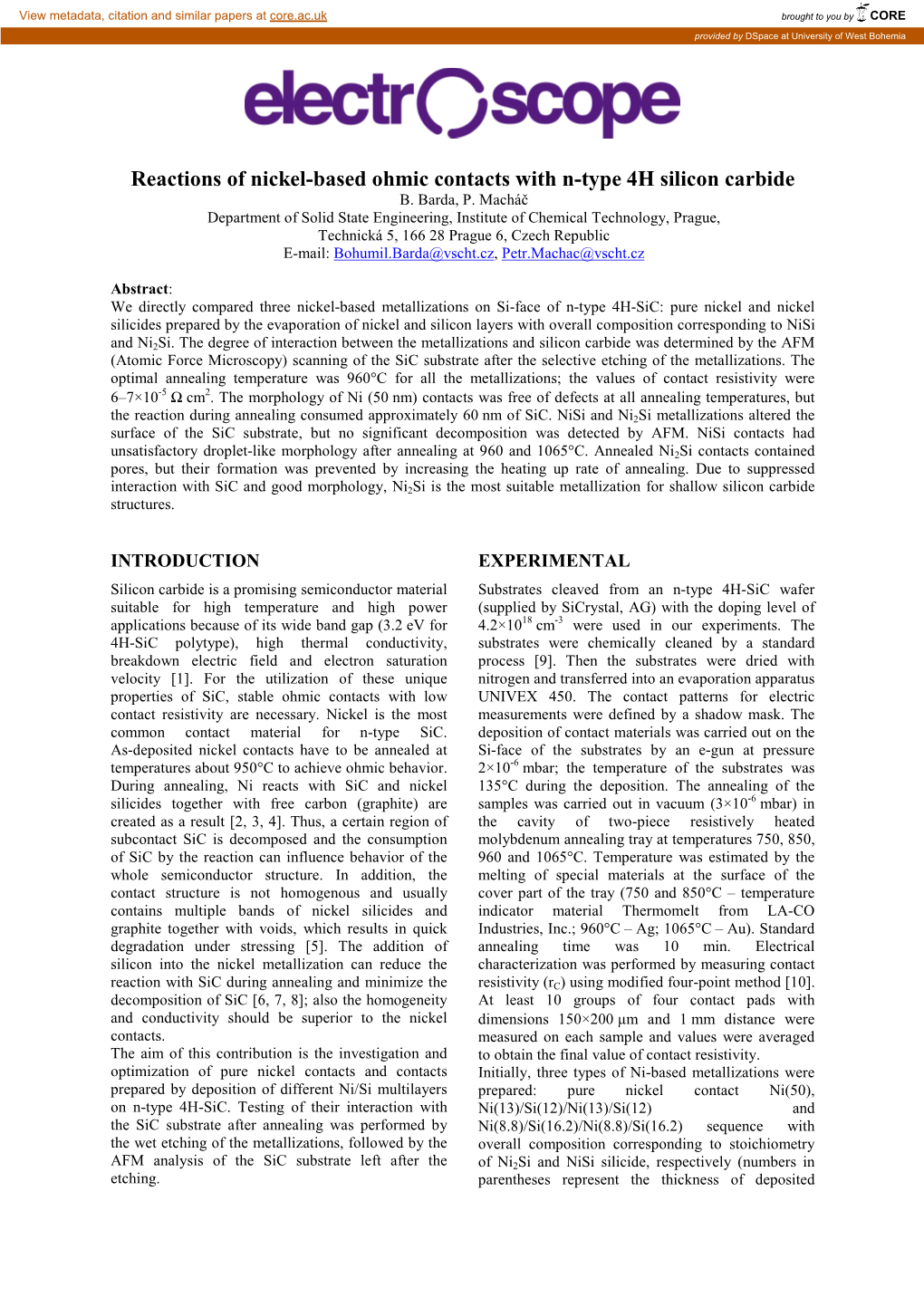
Load more
Recommended publications
-
High Purity Inorganics
High Purity Inorganics www.alfa.com INCLUDING: • Puratronic® High Purity Inorganics • Ultra Dry Anhydrous Materials • REacton® Rare Earth Products www.alfa.com Where Science Meets Service High Purity Inorganics from Alfa Aesar Known worldwide as a leading manufacturer of high purity inorganic compounds, Alfa Aesar produces thousands of distinct materials to exacting standards for research, development and production applications. Custom production and packaging services are part of our regular offering. Our brands are recognized for purity and quality and are backed up by technical and sales teams dedicated to providing the best service. This catalog contains only a selection of our wide range of high purity inorganic materials. Many more products from our full range of over 46,000 items are available in our main catalog or online at www.alfa.com. APPLICATION FOR INORGANICS High Purity Products for Crystal Growth Typically, materials are manufactured to 99.995+% purity levels (metals basis). All materials are manufactured to have suitably low chloride, nitrate, sulfate and water content. Products include: • Lutetium(III) oxide • Niobium(V) oxide • Potassium carbonate • Sodium fluoride • Thulium(III) oxide • Tungsten(VI) oxide About Us GLOBAL INVENTORY The majority of our high purity inorganic compounds and related products are available in research and development quantities from stock. We also supply most products from stock in semi-bulk or bulk quantities. Many are in regular production and are available in bulk for next day shipment. Our experience in manufacturing, sourcing and handling a wide range of products enables us to respond quickly and efficiently to your needs. CUSTOM SYNTHESIS We offer flexible custom manufacturing services with the assurance of quality and confidentiality. -
Morphological and Electrical Properties of Nickel Based Ohmic Contacts Formed by Laser Annealing Process on N-Type 4H-Sic
Preprint – Manuscript submitted to Materials Science in Semiconductor Processing (November 20, 2018) Morphological and electrical properties of Nickel based Ohmic contacts formed by laser annealing process on n-type 4H-SiC S. Rascunà 1*, P. Badalà 1, C. Tringali 1, C. Bongiorno 2, E. Smecca 2, A. Alberti 2, S. Di Franco 2, F. Giannazzo 2, G. Greco 2, F. Roccaforte 2, M. Saggio 1 1 STMicroelectronics SRL, Stradale Primosole 50, 95121 Catania, Italy 2 Consiglio Nazionale delle Ricerche – Istituto per la Microelettronica e Microsistemi (CNR-IMM), Strada VIII, n.5 Zona Industriale, I-95121 Catania, Italy (*) Corresponding author: [email protected], For the n-type SiC, annealed Ni-films are Abstract. This work reports on the commonly used to form nickel silicide (Ni 2Si) morphological and electrical properties of Ni- back-side Ohmic contacts. Typically, rapid based back-side Ohmic contacts formed by thermal annealing (RTA) exceeding 900°C laser annealing process for SiC power diodes. are used to achieve an Ohmic behavior [3]. Nickel films, 100 nm thick, have been However, today there is the need to replace sputtered on the back-side of heavily doped the conventional thermal annealing by laser 110 µm 4H-SiC thinned substrates after annealing processes carried out on the back- mechanical grinding. Then, to achieve Ohmic side of thinned wafers at the end of the behavior, the metal films have been irradiated fabrication flow [4]. with an UV excimer laser with a wavelength In Fig. 1, a schematic of a standard flow of 310 nm, an energy density of 4.7 J/cm 2 and chart (with and without grinding step) for the pulse duration of 160 ns. -
Wide Gap Braze Repairs of Nickel Superalloy Gas Turbine Components
WIDE GAP BRAZE REPAIRS OF NICKEL SUPERALLOY GAS TURBINE COMPONENTS by Cheryl Hawk A thesis submitted to the Faculty and Board of Trustees of the Colorado School of Mines in partial fulfillment of the requirements for the degree of Master of Science (Metallurgical and Materials Engineering). Golden, Colorado Date: ______________________ Signed: ______________________________ Cheryl Hawk Signed: ______________________________ Dr. Stephen Liu Thesis Advisor Golden, Colorado Date: ______________________ Signed: ______________________________ Dr. Ivar Reimanis Professor and Head Department of Metallurgical and Materials Engineering ii ABSTRACT The effect of microstructure and processing parameters on the bend properties of wide gap braze repairs has been investigated for BNi-2 and BNi-5 filler metals. BNi-2 braze alloys developed a brittle eutectic constituent that was the source for crack initiation and propagation. BNi-5 braze alloys developed large pores and lack of fusion to the base metal René 108 that decreased the strength of the joint. Three types of crack behaviors were observed within the two braze alloys. (1) Crack initiation and propagation through the brittle eutectic constituent. (2) Crack initiation and propagation through the brittle eutectic constituent/ matrix interface. The crack would propagate through grain boundaries if the eutectic constituent was dispersed. (3) Crack propagation follows type 1 or type 2, but propagated due to a major defect and coalesced with the defect. Braze alloy chemistry was improved by changing the filler metal-additive powder ratio. For the BNi-2 braze alloys, a mixing ratio of 40 wt.% BNi-2 produced the lowest volume percent of the brittle eutectic constituent. These alloys produced the highest strengths. -
Investigation of a Self-Aligned Cobalt Silicide Process for Ohmic Contacts to Silicon Carbide
Journal of ELECTRONIC MATERIALS, Vol. 48, No. 4, 2019 https://doi.org/10.1007/s11664-019-07020-0 Ó 2019 The Author(s) Investigation of a Self-Aligned Cobalt Silicide Process for Ohmic Contacts to Silicon Carbide MATTIAS EKSTRO¨ M ,1,2 ANDREA FERRARIO ,1 and CARL-MIKAEL ZETTERLING 1 1.—Department of Electronics, School of Electrical Engineering and Computer Science, KTH Royal Institute of Technology, 164 40 Kista, Sweden. 2.—e-mail: [email protected] Previous studies showed that cobalt silicide can form ohmic contacts to p-type 6H-SiC by directly reacting cobalt with 6H-SiC. Similar results can be achieved on 4H-SiC, given the similarities between the different silicon car- bide polytypes. However, previous studies using multilayer deposition of sil- icon/cobalt on 4H-SiC gave ohmic contacts to n-type. In this study, we investigated the cobalt silicide/4H-SiC system to answer two research ques- tions. Can cobalt contacts be self-aligned to contact holes to 4H-SiC? Are the self-aligned contacts ohmic to n-type, p-type, both or neither? Using x-ray diffraction, it was found that a mixture of silicides (Co2Si and CoSi) was reliably formed at 800C using rapid thermal processing. The cobalt silicide mixture becomes ohmic to epitaxially grown n-type (1 Â 1019cmÀ3) if annealed at 1000C, while it shows rectifying properties to epitaxially grown p-type (1 Â 1019cmÀ3) for all tested anneal temperatures in the range 800–1000C. À4 2 The specific contact resistivity (qC)ton-type was 4:3 Â 10 X cm . This work opens the possibility to investigate other self-aligned contacts to silicon car- bide. -
Technical Program
Technical Program sheets growth, split and roll-up model for the formation of 1-D titanate thin films was proposed. 2008 Nanomaterials: Fabrication, Properties, and 9:30 AM Applications: Processing and Properties Wet Chemical Synthesis of Highly Aligned ZnO Nanowires with Optical Sponsored by: The Minerals, Metals and Materials Society, TMS Electronic, Magnetic, Properties: Jean-Claude Tedenac1; Mezy Aude1; Ravot Didier1; Tichit Didier1; and Photonic Materials Division, TMS: Nanomaterials Committee 1 1 Program Organizers: Wonbong Choi, Florida International University; Seong Jin Gerardin Corinne ; Institut Gerhardt Universite de Montpellier 2 Koh, University of Texas at Arlington; Donna Senft, US Air Force; Ganapathiraman ZnO nanowires have a great commercial stake, due to their physical and Ramanath, Rensselaer Polytechnic Institute; Seung Kang, Qualcomm Inc chemical properties. Many methods have been employed for the growth of ZnO nanomaterials (sputtering, chemical vapour deposition, molecular beam epitaxy, Wednesday AM Room: 273 metal-organic chemical vapour deposition) which greatly improve the crystalline March 12, 2008 Location: Ernest Morial Convention Center quality. However, low cost and simplicity of the synthesis processes are required for commercial applications. The wet chemical synthesis route seems to meet Session Chairs: Pawel Keblinski, Rensselaer Polytechnic Institute; Douglas these requirements, enabling the preparation of high crystal quality and proper Chrisey, Rensselaer Polytechnic Institute growth orientation of ZnO nanowires. Nethertheless, control of the ZnO size, morphology, dimensionality, and self-assembly remains a very important 8:30 AM Invited stake, due to their tight influence on ZnO properties. Efficient control of both Optical Assembly of Nanomaterials: Paul Braun1; 1University of Illinois at nanostructure dimensionality and assembly is obtained by using appropriate Urbana-Champaign synthesis parameters during the seeded growth process. -
Effective Boronizing Process for Age Hardened Inconel 718
Western University Scholarship@Western Electronic Thesis and Dissertation Repository 4-18-2017 12:00 AM Effective Boronizing Process for Age Hardened Inconel 718 Aria Khalili The University of Western Ontario Supervisor Dr. Robert J. Klassen The University of Western Ontario Graduate Program in Mechanical and Materials Engineering A thesis submitted in partial fulfillment of the equirr ements for the degree in Master of Engineering Science © Aria Khalili 2017 Follow this and additional works at: https://ir.lib.uwo.ca/etd Part of the Metallurgy Commons Recommended Citation Khalili, Aria, "Effective Boronizing Process for Age Hardened Inconel 718" (2017). Electronic Thesis and Dissertation Repository. 4507. https://ir.lib.uwo.ca/etd/4507 This Dissertation/Thesis is brought to you for free and open access by Scholarship@Western. It has been accepted for inclusion in Electronic Thesis and Dissertation Repository by an authorized administrator of Scholarship@Western. For more information, please contact [email protected]. Abstract Boronizing or boriding is a technique to mitigate wear damage in industrial valves made of age-hardenable Inconel® 718 which is a nickel-based superalloy. Boriding involves immersing the part in a patented boron-based compound and heating over 800 oC. Boriding combined with aging has a detrimental thermal effect and was the subject of this investigation. The effects on hardness, wear and grain size, of boriding and aging separately, subsequently, and simultaneously, were investigated to observe the microstructure and mechanical properties. The results show that boriding has negligible effect on the grain size and the hardness of the substrate. Besides, a boride coating can improve the surface hardness by a factor of five and reduce the wear damage by over 75%. -
Study of Sic-Nickel Alloy Bonding for High Temperature Applications
Study of SiC-nickel alloy bonding for high temperature applications Lamine Hattali, Stéphane Valette, Francois Ropital, Guy Stremsdoerfer, Nadir Mesrati, Daniel Tréheux To cite this version: Lamine Hattali, Stéphane Valette, Francois Ropital, Guy Stremsdoerfer, Nadir Mesrati, et al.. Study of SiC-nickel alloy bonding for high temperature applications. Journal of the European Ceramic Society, Elsevier, 2009, 29, pp.813-819. 10.1016/j.jeurceramsoc.2008.06.035. hal-00657486 HAL Id: hal-00657486 https://hal.archives-ouvertes.fr/hal-00657486 Submitted on 6 Jan 2012 HAL is a multi-disciplinary open access L’archive ouverte pluridisciplinaire HAL, est archive for the deposit and dissemination of sci- destinée au dépôt et à la diffusion de documents entific research documents, whether they are pub- scientifiques de niveau recherche, publiés ou non, lished or not. The documents may come from émanant des établissements d’enseignement et de teaching and research institutions in France or recherche français ou étrangers, des laboratoires abroad, or from public or private research centers. publics ou privés. Study of SiC–nickel alloy bonding for high temperature applications M.L. Hattali a,∗, S. Valette a, F. Ropital c, G. Stremsdoerfer a, N. Mesrati b, D. Tréheux a a Laboratoire de Tribologie et Dynamique des Systèmes, UMR CNRS ECL ENISE ENSMSE 5513, École Centrale de Lyon, 69134 Ecully cedex, France b Laboratoire de Sciences et Génie des Matériaux, École Nationale Polytechnique d’Alger, 10, avenue de Hassen Badi EL harrach Alger, Algeria c IFP, BP 3-69360 Solaize, France Abstract We have studied the formation of metal/ceramic joints by solid state bonding technique for applications at temperatures >600 ◦C. -
Calibration Standards and Specimens
3_Calibration_Standards_Specimens_0510:Layout 1 17/6/10 16:27 Page 39 3 - Calibration standards and specimens All microscopes include a scale or read-out of magnification which is Agar Scientific specialises in offering and producing a wide range of helpful for the purposes of routine calibration. However, it is not always specimens specifically for this purpose and always endeavours to possible for such a calibration to be as accurate as is required for maintain the highest possible preparation standards in their production. quantitative results. The rapid growth of automated measuring systems Where possible, we offer specimens that are certified. and the advances in EM technology, particularly with high resolution microscopy, within the last two decades has brought a new importance The reasons for calibration and the appropriate specimens for TEM, to the standardisation, verification and assessment of instrumentation. SEM and light microscopes are outlined in a review by A.W. Agar Due to pressures of traceability there is an increasing need for entitled “Calibration of Microscopes for Magnification and Resolution” specimens which can be utilised for checking instrument performance in Microscopy and Analysis July 1988. A reprint of this article is whether it be on the scale of an optical microscope or an ultra-high available on request. resolution TEM. Magnification standards for light microscopy Stage micrometers These are used on the stage of the microscope and provide a simple and reliable means of accurately calibrating eyepiece graticules. A finely divided scale is protected by a cover glass to correspond exactly with the specimen it replaces. The scale is prepared on a glass disc mounted in a metal slide (76 x 26 mm) for convenient handling. -
Guidance for Responding to the Paragraph 71(1)(B) Notice Of
Guidance for responding to the Notice with respect to certain nanomaterials in Canadian Commerce Published in the Canada Gazette, Part I, on July 25, 2015 TABLE OF CONTENTS 1. OVERVIEW ........................................................................................................................ 3 1.1- PURPOSE OF THE NOTICE .............................................................................................................................. 3 1.2- REPORTABLE SUBSTANCES ........................................................................................................................... 4 1.3- DETERMINING IF A SUBSTANCE IS AT THE NANOSCALE ............................................................................... 12 2. WHO DOES THE NOTICE APPLY TO? ...........................................................................13 2.1- REPORTING CRITERIA ................................................................................................................................. 13 2.2- EXCLUSIONS ............................................................................................................................................... 14 2.3- FLOWCHART ............................................................................................................................................... 15 Figure 1: Reporting Diagram for Nanomaterials. ............................................................................................ 15 2.4- EXAMPLES OF HOW TO DETERMINE WHETHER THE REPORTING CRITERIA ARE MET -
DIRECT OBSERVATIONS of NICKEL SILICIDE FORMATION on (100) Si and Si0.75Ge0.25 SUBSTRATES USING IN-SITU TRANSMISSION ELECTRON MICROSCOPY
DIRECT OBSERVATIONS OF NICKEL SILICIDE FORMATION ON (100) Si AND Si0.75Ge0.25 SUBSTRATES USING IN-SITU TRANSMISSION ELECTRON MICROSCOPY RAMESH NATH S/O PREMNATH (B.Sc.(Hons.), NUS) A THESIS SUBMITTED FOR THE DEGREE OF MASTER OF SCIENCE DEPARTMENT OF MATERIALS SCIENCE NATIONAL UNIVERSITY OF SINGAPORE 2004 Acknowledgements I would like to express my utmost gratitude and thanks to my supervisor Professor Mark Yeadon for this project accomplishment. Without his patient guidance, this work will not have been possible. From my early days of ignorance, he had been there to provide knowledge, mentorship and assistance whenever difficulties are encountered. I am also grateful for Prof. Yeadon’s invaluable coaching in the handling of his precious transmission electron microscope and the knowledge of the operating techniques and little tricks here and there that he transferred to the me. It is a joy to work with him in the laboratory and get to know him as a friend. I am also deeply indebted to Dr. Christopher Boothroyd for his mentorship and guidance in helping me better understand the principles of the transmission electron microscope and the Gatan Image Filter. The long discussions we had over tea have definitely helped shaped me to be a better microscopist. I would also like to thank Dr. Lap Chan (CSM) for being an excellent teacher and facilitator who has helped to put this project together. I must particularly express my most sincere gratitude to my colleagues and also my friends, Dr. Foo Yong Lim and Soo Chi Wen, for their advice, understanding and help along the way. -
Graphene and Its Interaction with Different Substrates Studied by Angular-Resolved Photoemission Spectroscopy
Graphene and its Interaction with Different Substrates Studied by Angular-Resolved Photoemission Spectroscopy Carsten Enderlein Fritz-Haber Institut der Max Planck Gesellschaft FU Berlin im Fachbereich Physik der Freien Universit¨at Berlin eingereichte Dissertation 2010 ii 1. Reviewer: Prof. Karsten Horn 2. Reviewer: Prof. William Brewer Day of the defense: 28/06/2010 iii iv To Charly Kr¨uger and little and big Atmos ii Contents List of Figures vii List of Tables xi 1 Introduction 1 1.1 Graphene ................................... 1 1.1.1 The band structure of graphene . 4 1.1.1.1 Derivation of the electronic structure of the graphene pz-states .......................... 5 1.1.1.2 Breaking the symmetry of the two carbon sublattices . 9 1.1.2 The extraordinary properties of graphene . 10 1.1.3 Possible future applications . 11 1.2 Grapheneondifferentsubstrates . 11 1.2.1 Graphene on SiC . 12 1.2.1.1 Gap or no gap . 12 1.2.1.2 Multilayer graphene that behaves like a single graphene sheet ............................ 14 1.2.2 Graphene on metals . 14 1.3 Aimsofthisthesis .............................. 15 2 Experimental 17 2.1 An introduction to photoemission spectroscopy . 17 2.1.1 Thephotoelectriceffect . 17 2.1.2 Photoemission spectroscopy . 18 2.1.2.1 The three-step model of photoemission . 18 2.1.2.2 Beyond the three-step model of photoemission . 23 iii CONTENTS 2.1.3 Fermimapping ............................ 24 2.1.4 Core level spectroscopy . 25 2.2 Apparatus . 26 2.2.1 The laboratory PES setup . 26 2.2.1.1 The UVS300 He-lamp as a photon source . -
Oriented Growth of Silicide and Carbon in Sic-Based Sandwich Structures with Nickel
doi:10.1016/j.matchemphys.2008.02.009; Materials Chemistry and Physics 110 (2008) 303-310 Oriented growth of silicide and carbon in SiC-based sandwich structures with nickel A. Hähnel, V. Ischenko, J. Woltersdorf Max-Planck-Institut für Mikrostrukturphysik, D-06120 Halle, Weinberg 2, Germany Abstract We report on the formation kinetics and the metal-mediated structuring in nanoregions of silicide and carbon containing interlayers in SiC-based materials. The silicide formation and the graphite texturisation are determined by complex reactive diffusion processes. High resolution and analytical electron microscopy evidenced a €-Ni2Si growth with a <506> fibre texture in parallel orientation to the <0001> direction of the SiC substrate. The oriented growth of graphitic regions in the silicide hints to a diffusion controlled carbon precipitation from the silicide supersaturated with carbon, explaining the observed orientation relationships between graphite and silicon carbide: perpendicular and parallel to the {0001} silicon carbide surfaces. Keywords Thin films, textured growth, nickel silicide, graphitic carbon, silicon carbide, high resolution and analytical electron microscopy. Introduction Carbon containing interlayers with specially structured nanoregions have essential micromechanical and electronic relevance for SiC and Si-O-C-based high-tech materials; particularly the improvement of the mechanical properties of such composites demands the tailoring of their interlayers [1-6]. For SiC fibre-reinforced ceramics and glasses a controlling of the mechanical properties is possible by graphitic interlayers with basal plane alignment parallel to the fibre/matrix interface [7], which can result from appropriate chemical reactions during the composite processing [8,9]. An enhancement of the oriented growth of graphitic interlayer regions can be achieved via the catalytic graphitisation by transition metals [10-13].