Effective Boronizing Process for Age Hardened Inconel 718
Total Page:16
File Type:pdf, Size:1020Kb
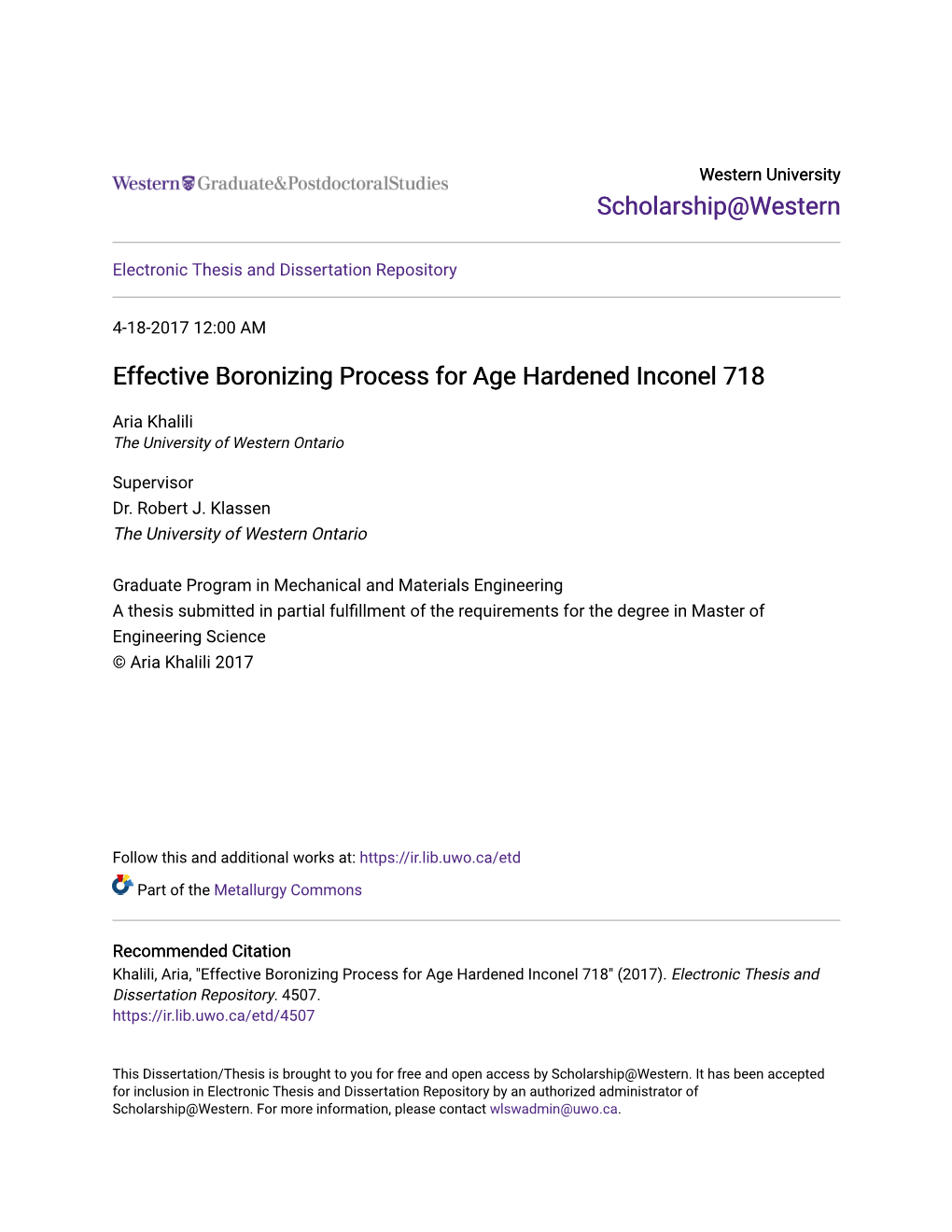
Load more
Recommended publications
-
Effect of Alloying Elements on Heat Treatment Behavior of Hypoeutectic
Materials Transactions, Vol. 47, No. 1 (2006) pp. 72 to 81 #2006 The Japan Institute of Metals Effect of Alloying Elements on Heat Treatment Behavior of Hypoeutectic High Chromium Cast Iron Sudsakorn Inthidech1;*, Prasonk Sricharoenchai1 and Yasuhiro Matsubara2 1Department of Metallurgical Engineering, Faculty of Engineering, Chulalongkorn University, Bangkok10330, Thailand 2Department of Metallurgical Engineering, Faculty of Engineering, Chulalongkorn University, Bangkok10330, Thailand The relationship between hardness and volume fraction of retained austenite (V ) was investigated in heat-treated 16 mass% and 26 mass%Cr hypoeutectic cast irons with and without addition of a third alloying element of Ni, Cu, Mo and V. In as-hardened state, hardness changed remarkably depending on the V . Overall, Ni and Cu decreased hardness but Mo increased it. Hardness increased in 16 mass%Cr cast iron but decreased in 26 mass%Cr cast iron by V addition. The V increased with Ni, Cu and Mo addition but diminished with V addition in 16 mass%Cr cast iron. In 26 mass%Cr cast iron, Ni and Mo increased the V but Cu and V reduced it. Higher austenitization caused more V . Curves of tempered hardness showed an evident secondary hardening due to precipitation of special carbides and transformation of destabilized austenite into martensite. High tempered hardness was obtained in the specimens with high V in as-hardened state. Maximum tempered hardness (HTmax) was obtained when V was less than 20% and it increased with an increase in Mo content. The HTmax slightly increased with V content in 16 mass%Cr cast iron and decreased in 26 mass%Cr cast iron. -
The Parallel Oxidation of Carbon and Chromium
THE PARALLEL OXIDATION OF CARBON AND CHROMIUM IN LIQUID IRON (16oo0 c) by LYALL FRANKLIN BARNHARDT B. Sc. Queen's University (1947) Submitted in partial fullfillment of the requirements for the degree of DOCTOR OF PHILOSOPHY at the Massachusetts Institute of Technology 1965 Signature of Author Department of Metallurgy Signature of Professor in Charge of Research jE Signature of Chairman of - A ii Departmental Committee on Graduate Students VI 38 ABSTRACT THE PARALLEL OXIDATION OF CARBON AND CHROMIUM IN LIQUID IRON (16000c) by LYALL FRANKLIN BARNHARDT Submitted to the Department of Metallurgy in April, 1965, in partial fulfillment of the requirements for the Degree of Doctor of Philosophy. The path followed by carbon and chromium concentrations in liquid iron during oxidation was investigated experimentally by blowing gaseous oxygen on to slag-free iron - chromium - carbon melts at 16004C in an induction furnace. The carbon oxidation reaction occurred at the surface of the melt, with an initial constant rate of decarburization which was dependent on the rate of oxygen input. The mechanism of this reaction is expressed in the chemical equation: C + 1/2 02 (g) = CO (g). During the initial stage, which was characterized by a constant rate of decarburization, carbon oxidized preferentially with no loss of chromium. Beyond this stage, the rate of carbon loss declined rapidly and the oxidation of iron and chromium occurred. The entry of argon into the furnace atmosphere, during the oxygen blow, lowered the partial pressure of carbon monoxide at the metal surface. This allowed the carbon concentration of the melt to drop far below the equilibrium iii carbon content for one atmosphere pressure of carbon monoxide. -
Effect of Tempering Conditions on Secondary Hardening of Carbides
materials Article Effect of Tempering Conditions on Secondary Hardening of Carbides and Retained Austenite in Spray-Formed M42 High-Speed Steel Bowen Liu 1,*, Tian Qin 2, Wei Xu 1, Chengchang Jia 1,*, Qiuchi Wu 2, Mingying Chen 2 and Zhe Liu 2 1 Institute for Advanced Materials and Technology, University of Science and Technology Beijing, Beijing 100083, China; [email protected] 2 School of Materials Science and Engineering, University of Science and Technology Beijing, Beijing 100083, China; [email protected] (T.Q.); [email protected] (Q.W.); [email protected] (M.C.); [email protected] (Z.L.) * Correspondence: [email protected] (B.L.); [email protected] (C.J.); Tel.: +86-15-210-565-349 (B.L.) Received: 30 October 2019; Accepted: 7 November 2019; Published: 11 November 2019 Abstract: In this study, the effect of tempering conditions on microstructure, grain size, and carbide phase compositions of spray-formed high-speed steel after quenching at 1180 ◦C was studied. The influence of carbide phase, size of carbides, and retained austenite content on secondary hardening of the steel was analyzed by field emission scanning electron microscope (FESEM), transmission electron microscope (TEM), electron backscattered diffraction (EBSD), and differential scanning calorimetry (DSC); the hardness, microhardness of carbide, and bending strength were tested. The results show that M3C, M6C, M7C3, and MC carbides may precipitate at different tempering temperatures and the transformation of the retained austenite can be controlled by tempering. The phase composition of carbides, microstructure, and retained austenite content strongly influences the performance characteristics of M42 high-speed steel after tempering. -
Ultra-Fast Boriding for Improved Energy Efficiency and Reduced Emissions in Materials Processing Industries
ANL/ESD/12-16 Ultra-fast Boriding for Improved Energy Efficiency and Reduced Emissions in Materials Processing Industries. Final Report. Project Period: 9/30/2008 – 9/30/2011 (extended to 12/31/2011) Energy Systems Division About Argonne National Laboratory Argonne is a U.S. Department of Energy laboratory managed by UChicago Argonne, LLC under contract DE-AC02-06CH11357. The Laboratory’s main facility is outside Chicago, at 9700 South Cass Avenue, Argonne, Illinois 60439. For information about Argonne and its pioneering science and technology programs, see www.anl.gov. Availability of This Report This report is available, at no cost, at http://www.osti.gov/bridge. It is also available on paper to the U.S. Department of Energy and its contractors, for a processing fee, from: U.S. Department of Energy Office of Scientific and Technical Information P.O. Box 62 Oak Ridge, TN 37831-0062 phone (865) 576-8401 fax (865) 576-5728 [email protected] Disclaimer This report was prepared as an account of work sponsored by an agency of the United States Government. Neither the United States Government nor any agency thereof, nor UChicago Argonne, LLC, nor any of their employees or officers, makes any warranty, express or implied, or assumes any legal liability or responsibility for the accuracy, completeness, or usefulness of any information, apparatus, product, or process disclosed, or represents that its use would not infringe privately owned rights. Reference herein to any specific commercial product, process, or service by trade name, trademark, manufacturer, or otherwise, does not necessarily constitute or imply its endorsement, recommendation, or favoring by the United States Government or any agency thereof. -
Böhler Edelstahl - General Information
Content . Böhler Edelstahl - General Information . Production Possibilities & New Additive Manufacturing . Product Portfolio Böhler Edelstahl - General Information MISSION We develop, produce and supply high-speed steels, tool steels and special materials for our worldwide customers to offer them optimal solutions. BÖHLER Edelstahl at a glance Worldwide 2016 Production 79 €622 137,000 points of sale million revenue tonnes Advanced 2114 production facilities employees Quality & technology Global 250 LEADER steel grades 100% recyclable Sales revenue by region (FY 2016) 1% 9% 12% Europe America Asia Rest of world 78% Sales revenue by business area (FY 2016) 11% Special materials 41% 21% Tool steel High speed steels Other 27% Business area revenue special materials Automotive Other Engineering 4% 11% 11% Special Oil & Gas, materials CPI High speed Power-Gen steel 21% 41% 43% 15% 27% Tool steel 27% Aerospace Production Possibilities BÖHLER EDELSTAHL Integrated plant configuration Whole melting and re-melting operations at one site Whole hot forming operations at one site Whole heat treatment operations at one site Whole ND-Testing and finishing operations at one site Standard mechanical, metallographic, chemical tests at one site Quality starts here Primary metallurgy EAF/50 t Electric arc furnace VIM Vacuum induction furnace AOD Argon oxygen decarburization VID/14 t Vacuum induction furnace REMELTING Remelting process for high- purity metallurgical materials • ESR • PESR • VAR FORGING TECHNOLOGY 5,200 t forging press Open die forge Bar steel -
Method for Boriding of Coatings Using High Speed
(19) & (11) EP 2 222 898 B1 (12) EUROPEAN PATENT SPECIFICATION (45) Date of publication and mention (51) Int Cl.: of the grant of the patent: C25D 9/08 (2006.01) C23C 28/00 (2006.01) 08.06.2011 Bulletin 2011/23 C25D 3/66 (2006.01) C25D 9/04 (2006.01) (21) Application number: 08848442.3 (86) International application number: PCT/EP2008/065065 (22) Date of filing: 06.11.2008 (87) International publication number: WO 2009/060033 (14.05.2009 Gazette 2009/20) (54) METHOD FOR BORIDING OF COATINGS USING HIGH SPEED ELECTROLYTIC PROCESS VERFAHREN ZUM BORIEREN VON BESCHICHTUNGEN MIT HILFE EINES SCHNELLEN ELEKTROLYTISCHEN VERFAHRENS PROCÉDÉ DE BORURATION DE REVÊTEMENTS À L’AIDE D’UN TRAITEMENT ÉLECTROLYTIQUE HAUTE VITESSE (84) Designated Contracting States: (72) Inventors: AT BE BG CH CY CZ DE DK EE ES FI FR GB GR • Ürgen, Mustafa K. HR HU IE IS IT LI LT LU LV MC MT NL NO PL PT Istanbul (TR) RO SE SI SK TR • Timur, Servet I. Istanbul (TR) (30) Priority: 09.11.2007 EP 07120419 • Kazmanli, Kürsat M. Istanbul (TR) (43) Date of publication of application: • Kartal, Güldem 01.09.2010 Bulletin 2010/35 Istanbul (TR) (73) Proprietors: (74) Representative: Sevinç, Erkan • Ürgen, Mustafa K. Istanbul Patent & Trademark Consultancy Ltd. Istanbul (TR) Plaza-33, Büyükdere cad. No: 33/16 • Timur, Servet I. Sisli Istanbul (TR) 34381 Istanbul (TR) • Kazmanli, Kürsat M. Istanbul (TR) (56) References cited: • Kartal, Güldem DE-A1- 1 796 215 GB-A- 1 422 859 Istanbul (TR) JP-A- 5 161 090 US-A- 3 824 134 Note: Within nine months of the publication of the mention of the grant of the European patent in the European Patent Bulletin, any person may give notice to the European Patent Office of opposition to that patent, in accordance with the Implementing Regulations. -
AP-42 12.13 Final Background Document for Steel Foundries
BACKGROUND REPORT AP-42 SECTION 12.13 STEEL FOUNDRIES Prepared for U.S. Environmental Protection Agency OAQPS/TSD/EIB Research Triangle Park, NC 27711 1-103 Pacific Environmental Services, Inc. P.O. Box 12077 Research Triangle Park, NC 27709 919/941-0333 1-103 AP-42 Background Report TECHNICAL SUPPORT DIVISION U.S. ENVIRONMENTAL PROTECTION AGENCY Office of Air Quality Planning and Standards Research Triangle Park, NC 27711 ii This report has been reviewed by the Technical Support Division of the Office of Air Quality Planning and Standards, EPA. Mention of trade names or commercial products is not intended to constitute endorsement or recommendation for use. Copies of this report are available through the Library Services Office (MD-35), U.S. Environmental Protection Agency, Research Triangle Park, NC 27711. iii TABLE OF CONTENTS 1.0 INTRODUCTION ................................................. 1 2.0 INDUSTRY DESCRIPTION ......................................... 2 2.1 GENERAL ................................................... 2 2.2 PROCESS DESCRIPTION1 ..................................... 2 2.3 EMISSIONS AND CONTROLS1,19 ................................ 8 2.4 REVIEW OF REFERENCES ..................................... 9 2.5 REFERENCES FOR CHAPTER 2 ............................... 11 3.0 GENERAL EMISSION DATA REVIEW AND ANALYSIS PROCEDURES ... 13 3.1 LITERATURE SEARCH AND SCREENING ....................... 13 3.2 EMISSION DATA QUALITY RATING SYSTEM ................... 14 3.3 EMISSION FACTOR QUALITY RATING SYSTEM ................. 16 3.4 -
The Discovery of Strong Aluminum
METALS HISTORY The Discovery of Strong Aluminum Charles R. Simcoe ow did aluminum, a metal that is light Interest in Wilm’s alloy spread throughout Watseka, Ill. H in weight (only one-third as heavy as the metal-making world. Samples of the alloy steel) and in its unalloyed form is were obtained, and studies were undertaken on The discovery among the weakest of all metals, become the the hardening mechanism at the United States structural material of modern airplanes? This Bureau of Standards in Washington, D.C. The of age story started in the very early 1900s, the in- research was performed by Paul Merica, hardening of fancy of the aluminum industry. At this time, Howard Scott, and R.G. Waltenberg, and they aluminum was the aluminum market was mostly in cooking would become famous as the next major con- a seminal utensils, pots, and pans. The leap from such tributors to the amazing story of age harden- small, mundane beginnings to building Zep- ing. They found that nature had held a secret event in the pelins in a few years, Douglas DC-3s in 25 on a method of hardening metals, and that history of years, and Boeing 747s in 60 years is a remark- Wilm’s alloy was just a single example of a uni- metals. able feat of engineering. versal behavior that was undiscovered since an- Read the The first character in this drama was a Ger- cient man had learned to make alloys during complete man engineer by the name of Alfred Wilm. He the age of bronze. -
Development of Guidelines for Warm Forging of Steel Parts
Development of Guidelines for Warm Forging of Steel Parts THESIS Presented in Partial Fulfillment of the Requirements for the Degree Master of Science in the Graduate School of The Ohio State University By Niranjan Rajagopal, B.Tech Graduate Program in Industrial and Systems Engineering The Ohio State University 2014 Master's Examination Committee: Dr.Taylan Altan, Advisor Dr.Jerald Brevick Copyright by Niranjan Rajagopal 2014 ABSTRACT Warm forging of steel is an alternative to the conventional hot forging technology and cold forging technology. It offers several advantages like no flash, reduced decarburization, no scale, better surface finish, tight tolerances and reduced energy when compared to hot forging and better formability, lower forming pressures and higher deformation ratios when compared to cold forging. A system approach to warm forging has been considered. Various aspects of warm forging process such as billet, tooling, billet/die interface, deformation zone/forging mechanics, presses for warm forging, warm forged products, economics of warm forging and environment & ecology have been presented in detail. A case study of forging of a hollow shaft has been discussed. A comparison of forging loads and energy required to forge the hollow shaft using cold, warm and hot forging process has been presented. ii DEDICATION This document is dedicated to my family. iii ACKNOWLEDGEMENTS I am grateful to my advisor, Prof. Taylan Altan for accepting me in his research group, Engineering Research Center for Net Shape Manufacturing (ERC/NSM) and allowing me to do thesis under his supervision. The support of Dr. Jerald Brevick along with other professors at The Ohio State University was also very important in my academic and professional development. -
Evaluation of the Mechanical Properties After Thermal Treatment of a Structural Hot Rolled Multiphase Steel(·)
REVISTA DE METALURGIA, 43 (6) NOVIEMBRE-DICIEMBRE, 448-457, 2007 ISSN: 0034-8570 Evaluation of the mechanical properties after thermal treatment of a structural hot rolled multiphase steel(·) J. Asensio-Lozano* and J.T. Panta-Mesones** Abstract The present paper corresponds to the experimental study conducted on a hot rolled (HR) multiphase (MP) steel, in which hardness, tensile and toughness properties were measured after the application of a series of subcritical and intercritical heat treatments (HT) to the hot rolled stock. The aforementioned values were compared to the corresponding ones in the as-rolled state and after normalizing. The microstructure in the longitudinal plane of the strip was analyzed by light optical microscopy in the as-rolled state and in the HT samples. Longitudinal (L) and transverse (T) tensile and toughness specimens were cut to characterize every condition studied. Toughness properties were evaluated by means of Charpy V-notch tests conducted at 20 °C, 0 °C, –20 °C, –40 °C, –60 °C and –80 °C . It was observed that the yield stress increased with the increase in the heat treatment temperature in the subcritical range, while the tensile strength decreased slightly over the same range of temperatures. Uniform and total elongation only showed a slight improvement when the treatment was conducted at 620 °C and 700 °C, while the best toughness response corresponded to the sample treated at 500 °C for operating temperatures comprised between –40 °C and room temperature (RT). Keywords Multiphase steels. Heat treatment. Tempering. Normalizing. Mechanical properties. Hardness. Tension test. Charpy impact toughness. Evaluación de las propiedades mecánicas tras tratamiento térmico de un acero multifase estructural laminado en caliente Resumen El presente estudio corresponde al trabajo experimental desarrollado en un acero multifase laminado en caliente, en el que se evaluaron las propiedades de dureza, tracción y tenacidad a impacto, tras realizar tratamientos térmicos subcríticos e intercríticos al material laminado en caliente. -
Final Exam Questions Generated by the Class
Final Exam Questions Generated by the Class Module 8 – Iron and Steel Describe some of the business practices that Carnegie employed that allowed him to take command of the steel industry. Hard driving, vertical integration, price making Which of the following was/is NOT a method used to make steel? A. Puddling B. Bessemer process C. Basic oxygen process D. Arc melting E. None of the above What are the three forms of iron, and what is the associated carbon content of each? Wrought <.2% Steel .2-2.3% Cast Iron 2.3-4.2% How did Andrew Carnegie use vertical integration to gain control of the steel market? Controlled the entire steel making process from mining to final product Who created the best steel for several hundred years while making swords during the 1500’s? A. Syria B. Egypt C. Japan D. England Describe the difference between forging and casting. When forging, you beat and hammer the material into the desired shape. When casting, you pour liquid into a mold to shape it. Describe the difference between steel and wrought iron. Steel has less carbon Which of the following forms of iron has a low melting point and is not forgeable? A. Steel B. Pig Iron C. Wrought Iron D. None of the Above What two developments ushered in the transition from the Bronze Age to the Iron Age? More iron ore and greater ability to change its properties using readily available alloying agent (carbon) 1 Final Exam Questions Generated by the Class What is the difference between ferrite and austenite? A. -
High Purity Inorganics
High Purity Inorganics www.alfa.com INCLUDING: • Puratronic® High Purity Inorganics • Ultra Dry Anhydrous Materials • REacton® Rare Earth Products www.alfa.com Where Science Meets Service High Purity Inorganics from Alfa Aesar Known worldwide as a leading manufacturer of high purity inorganic compounds, Alfa Aesar produces thousands of distinct materials to exacting standards for research, development and production applications. Custom production and packaging services are part of our regular offering. Our brands are recognized for purity and quality and are backed up by technical and sales teams dedicated to providing the best service. This catalog contains only a selection of our wide range of high purity inorganic materials. Many more products from our full range of over 46,000 items are available in our main catalog or online at www.alfa.com. APPLICATION FOR INORGANICS High Purity Products for Crystal Growth Typically, materials are manufactured to 99.995+% purity levels (metals basis). All materials are manufactured to have suitably low chloride, nitrate, sulfate and water content. Products include: • Lutetium(III) oxide • Niobium(V) oxide • Potassium carbonate • Sodium fluoride • Thulium(III) oxide • Tungsten(VI) oxide About Us GLOBAL INVENTORY The majority of our high purity inorganic compounds and related products are available in research and development quantities from stock. We also supply most products from stock in semi-bulk or bulk quantities. Many are in regular production and are available in bulk for next day shipment. Our experience in manufacturing, sourcing and handling a wide range of products enables us to respond quickly and efficiently to your needs. CUSTOM SYNTHESIS We offer flexible custom manufacturing services with the assurance of quality and confidentiality.