Specification for Welding Procedure And
Total Page:16
File Type:pdf, Size:1020Kb
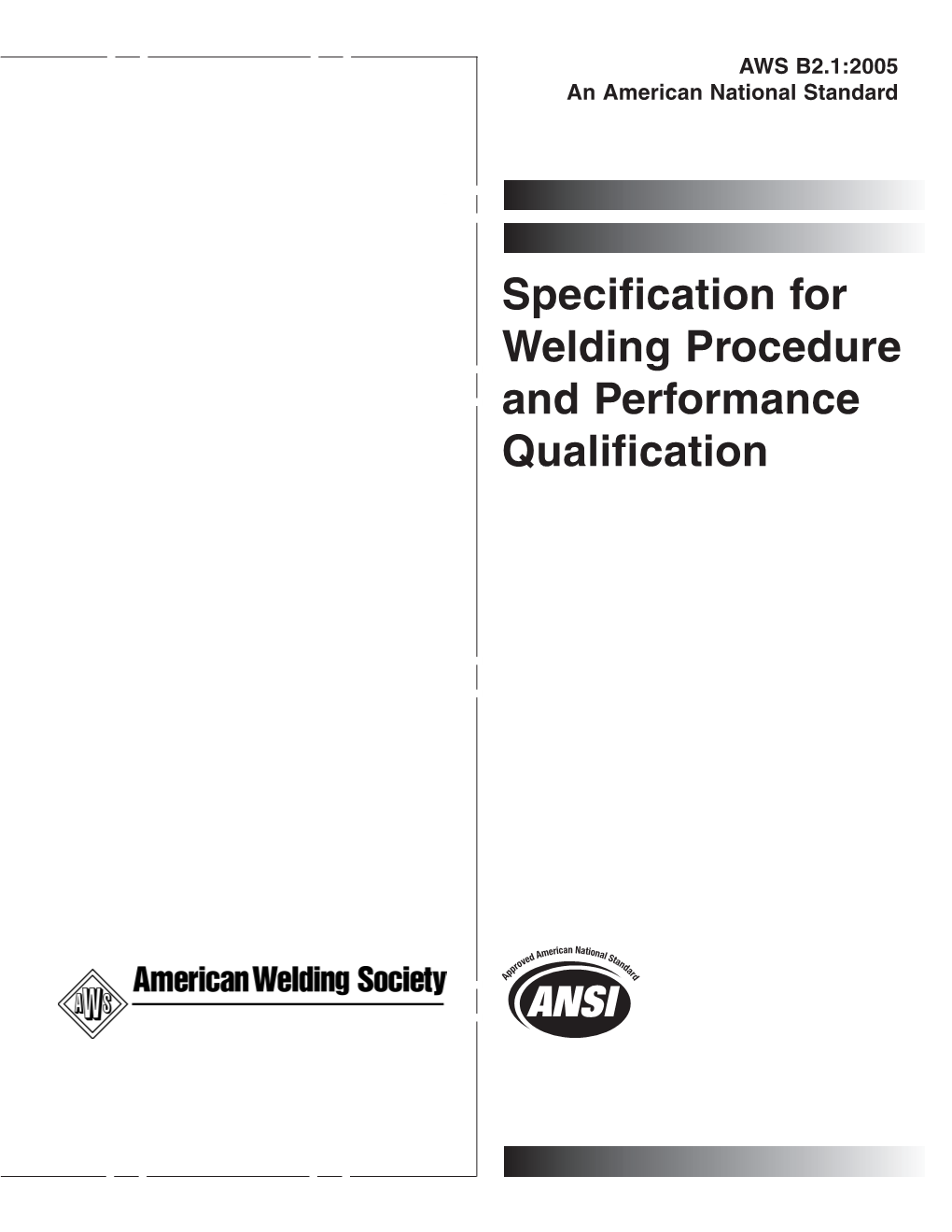
Load more
Recommended publications
-
Hardfacing Products and Guide
Hardfacing Products and Guide We Take the Hard Out of HARDFACING TABLE OF CONTENTS 2 EDUCATION .....................................................4 Introduction .............................................................7 Types of Wear ......................................................9 Common Hardfacing Processes ....................10 Procedures and Welding Techniques ................... 14 Process Selection ............................................... 15 General Guidelines ............................................. 15 General Welding Procedures ................................26 Preheat Recommendations .................................. 32 PRODUCTS .................................................... 34 Why Lincoln Electric Hardfacing Alloys ...............35 Hardfacing Product Selection Chart ....................36 Product Selection Build Up ...............................................................38 Metal-to-Metal Wear ........................................44 High Impact / Low Abrasion Wear ................ 50 Impact and Abrasion Wear .............................54 Severe Abrasion / Low Impact Wear ............ 56 High Temperature, Corrosion and Specialty Wear .................................................. 64 Submerged Arc Welding Fluxes for Hardfacing .................................................... 66 RESOURCES ..................................................68 Alloy Lot Certification ...........................................69 Common Package Types .......................................70 Contact -
Filler Metals for Repair, Hardfacing and Cladding Applications
Tailor-Made Protectivity™ FILLER METALS FOR REPAIR, HARDFACING AND CLADDING APPLICATIONS voestalpine Böhler Welding www.voestalpine.com/welding Tailor-Made Protectivity™ FILLER METALS FOR REPAIR, HARDFACING AND CLADDING APPLICATIONS voestalpine Böhler Welding www.voestalpine.com/welding Tailor-made Protectivity™ UTP Maintenance – provides lasting “protection” and “productivity” of the plant. “Protectivity” is the result of supporting our customers with maximum performance. Decades of industry experience and application know-how in the areas of repair as well as wear and surface protection, combined with innovative and tailored products, guarantee the customers increased productivity and in addition protection and the highest performance of their components under the UTP Maintenance brand. Solutions for demanding industries 3 Products of UTP Maintenance are focused on industries with high technical requirements and specialized applications. Metallurgical know-how for research & development International customers and distributors are supported by experienced welding engineers by voestalpine Böhler Welding. In addition our ambition to be best in class motivates constant evolution through our total dedication to research and development and guarantees our customers are using the most technically advanced welding products available today. The product portfolio of UTP Maintenance comprises of innovative and tailored welding consumables from own production facilities as follows … n Stick electrodes n Submerged arc wires and fluxes n Solid wires and rods n Submerged arc strips and fluxes n Flux cored wires n Spraying- and PTA-powders Our product range is comprehensive and covers the following steel alloys: Unalloyed and fine-grained steels, Low-alloy steels, Stainless and heat-resistant steels, Nickel-base alloys, Cast-iron, Copper and Copper-base alloys, Manganese steels, Tool steels and Cobalt alloys. -
Review on Hardfacing As Method of Improving the Service Life of Critical Components Subjected to Wear in Service
Nigerian Journal of Technology (NIJOTECH) Vol. 36, No. 4, October 2017, pp. 1095 – 1103 Copyright© Faculty of Engineering, University of Nigeria, Nsukka, Print ISSN: 0331-8443, Electronic ISSN: 2467-8821 www.nijotech.com http://dx.doi.org/10.4314/njt.v36i4.15 REVIEW ON HARDFACING AS METHOD OF IMPROVING THE SERVICE LIFE OF CRITICAL COMPONENTS SUBJECTED TO WEAR IN SERVICE C. Okechukwu 111,*1,*,*,* , O. A. Dahunsi 222., P. K. Oke 333, I. O. Oladele 444 and M. Dauda 555 111,1, 2, 3, 3 DEPT. OF MECHANICAL ENGINEERING , FEDERAL UNIVERSITY OF TECHNOLOGY , AKURE , ONDO STATE , NIGERIA. 444,4,,, DEPT. OF METALLURGICAL AND MATERIALS ENGR ., FED . UNIVERSITY OF TECH . AKURE , ONDO STATE , NIGERIA. 555,5,,, ADVANCED MANUFACTURING TECHNOLOGY PROGRAMME , JALINGO , TARABA STATE , NIGERIA. EEE-E---mailmail addresses ::: [email protected], 222 [email protected], [email protected], [email protected], [email protected] ABSTRACT A review on hardfacing is presented. Hardfacing involves applying a consumable with desired wear prpropertiesoperties over a soft base metal surface to enhance resistance to different wear mechanisms. Substrate materials used for hardfacing are mainly steel, while the alloys of carbide forming elements dominate the surfacing consumables. PowderPowder metallurgy, atomisation and granulation are methods of producing hardfacing alloy powder. Most welding methods were identified to be successfully used in applying consumable on substrate surfaces. Dilution decreases with iincreasencrease in the number of hardfacing layers. Buffers, butters and buildbuild----upup metals are used to compensate for composition differences to prevent spalling, overcome welding difficulties and make up for badly worn surfaces, respectively. Waffle, stringer and ddotot patterns are the existing hardfacing deposit patpatterns.terns. -
Elementary Study of Submerged Arc Welding for Hardfacing and Surface Engineering
May 2017, Volume 4, Issue 05 JETIR (ISSN-2349-5162) ELEMENTARY STUDY OF SUBMERGED ARC WELDING FOR HARDFACING AND SURFACE ENGINEERING 1 Sagar Kishor Waidande,2Dr. Kishor P. Kolhe 1PG Student 2Professor 1,2Department of Mechanical Engineering, 1,2JSPM’s Imperial College of Engineering & Research, Pune, India Abstract— This paper presents the review of submerged arc welding process for different industrial application like fabrication, erection, repairs, surfacing and hardfacing, etc. The review of literature was carried out, studied by many researcher’s for getting the better improvement in hardfacing and surface engineering characteristic, like mechanical properties, microstructures, resistance to wear and erosion of heavy duty welded structure under severe conditions joined by submerged arc welding. Most of the studies conclude the effect of welding variables, flux composition, power source, material composition etc, on the surface deposited by various welding processes like Shielded Metal Arc Welding (Covered Electrode), Flux Cored Arc Welding, Submerged Arc Welding, Gas hardfacing, Powder Spraying, Electric Arc Spraying, Plasma Transferred Arc (PTA), High Velocity Oxy-Fuel Process (HVOF). Hard surfacing is the deposition of a special alloy material on a metallic base part, by various welding processes, to obtain more desirable wear properties and/or dimensions. This paper gives the brief introduction to the process of submerged arc welding for hardfacing and surface engineering. The various consumables used in the SAW process i.e electrode and flux are described. The various base metals and hard facing alloys are also mentioned. Index Terms— Submerged Arc Welding, Hardfacing, Consumables, Alloys In Hardfacing, Mechanical Properties, Macro-Structure. I. INTRODUCTION In industrial manufacturing, maintenance, etc processes welding operations are essential tool. -
Specification for Welding Procedure and Performance Qualification AWS B2.1/B2.1M:2009 an American National Standard
AWS B2.1/B2.1M:2009 An American National Standard Specification for Welding Procedure and Performance Qualification AWS B2.1/B2.1M:2009 An American National Standard Approved by the American National Standards Institute August 22, 2008 Specification for Welding Procedure and Performance Qualification 5th Edition Supersedes AWS B2.1:2005 Prepared by the American Welding Society (AWS) B2 Committee on Procedure and Performance Qualification Under the Direction of the AWS Technical Activities Committee Approved by the AWS Board of Directors Abstract This specification provides the requirements for qualification of welding procedure specifications, welders, and welding operators for manual, semiautomatic, mechanized, and automatic welding. The welding processes included are electro- gas welding, electron beam welding, electroslag welding, flux cored arc welding, gas metal arc welding, gas tungsten arc welding, laser beam welding, oxyfuel gas welding, plasma arc welding, shielded metal arc welding, stud arc welding, and submerged arc welding. Base metals, filler metals, qualification variables, welding designs, and testing requirements are also included. 550 N.W. LeJeune Road, Miami, FL 33126 AWS B2.1/B2.1M:2009 International Standard Book Number: 978-0-87171-512-8 American Welding Society 550 N.W. LeJeune Road, Miami, FL 33126 © 2009 by American Welding Society All rights reserved Printed in the United States of America Photocopy Rights. No portion of this standard may be reproduced, stored in a retrieval system, or transmitted in any form, including mechanical, photocopying, recording, or otherwise, without the prior written permission of the copyright owner. Authorization to photocopy items for internal, personal, or educational classroom use only or the internal, personal, or educational classroom use only of specific clients is granted by the American Welding Society provided that the appropriate fee is paid to the Copyright Clearance Center, 222 Rosewood Drive, Danvers, MA 01923, tel: (978) 750-8400; Internet: <www.copyright.com>. -
Hardfacing Alloys
HARDFACING ALLOYS www.deloro.com 2 DELORO WEAR SOLUTIONS GMBH Deloro Wear Solutions is a global world-class provider and manufacturer of innovative metallic wear solutions. We put at your disposal our metallurgical and process technology expertise to enhance performance of your critical components or processes exposed to any combination of mechanical, corrosive or heat related wear. Your productivity is our mission! Our wide range of hard facing consumables comes in the form of rods, wires, powder and electrodes and can be custom engineered to meet individual customer needs. In addition to hard facing alloys, Deloro Wear Solutions also offers solid and coated wear and corrosion-resistant components which we can finish – machine in-house to your drawing. Germany Switzerland Italy 3 TABLE OF CONTENTS HARDFACING ALLOYS 4 ALLOYS FOR WELDED OVERLAYS TIG AND OXY-ACETYLENE WELDING 6 MMA WELD DEPOSITION 8 MIG WELD DEPOSITION, SUBMERGED ARC WELDING 10 PTA WELD DEPOSITION 12 LASER WELD DEPOSITION 13 ALLOYS FOR SPRAYED COATINGS PLASMA SPRAYING 16 HVOF SPRAY 18 SPRAY AND FUSE 21 POWDER WELDING 22 ALLOYS FOR GENERATIVE PROCESSES ADDITIVE LAYER MANUFACTURING 24 PTA POWDER CLADDING SYSTEMS 26 4 HARDFACING ALLOYS Stellite™ Alloys Deloro™ Alloys The cobalt-based Stellite™ alloys are our most well- The Deloro™ alloys are nickel based with additions of known and successful alloys, with the best “all-round” typically Cr, C, B, Fe and Si. They cover a very wide properties. They combine excellent mechanical wear range of hardness from soft, tough, build-up alloys that resistance, especially at high temperatures, with very are easily machined or hand finished to exceptionally good corrosion resistance. -
Hardfacing Welded ASTM A572-Based, High-Strength, Low-Alloy Steel: Welding, Characterization, and Surface Properties Related to the Wear Resistance
metals Article Hardfacing Welded ASTM A572-Based, High-Strength, Low-Alloy Steel: Welding, Characterization, and Surface Properties Related to the Wear Resistance Nakarin Srisuwan 1,2, Nuengruetai Kumsri 3, Trinet Yingsamphancharoen 2,3 and Attaphon Kaewvilai 3,* 1 Thai-French Innovation Institute, King Mongkut’s University of Technology North Bangkok, Bangkok 10800, Thailand; nakrin.s@tfii.kmutnb.ac.th 2 Welding Engineering and Metallurgical Inspection, Science and Technology Research Institute, King Mongkut’s University of Technology North Bangkok, Bangkok 10800, Thailand; [email protected] 3 Department of Welding Engineering Technology, College of Industrial Technology, King Mongkut’s University of Technology North Bangkok, Bangkok 10800, Thailand; [email protected] * Correspondence: [email protected]; Tel.: +66-2-555-2000 (ext. 6417) Received: 31 December 2018; Accepted: 13 February 2019; Published: 19 February 2019 Abstract: This work presents the improvement of hardfacing welding for American Society for Testing and Materials (ASTM) A572-based high-strength, low-alloy steel by controlling the heating/cooling conditions of welding process. In the welding process, the buffer and hardfacing layers were welded onto A572-based material by a nickel–chromium electrode and chromium carbide electrode, respectively. The base metal and electrode materials were controlled by the heating/cooling process during the welding to reduce excessive stress, which could result in a crack in the specimens. The welded specimens were examined by visual and penetrant inspections for evaluating the welding quality. The macro–micro structure of the deposited layer was investigated; scanning electron microscope with an energy-dispersive X-ray spectrometer (SEM-EDS) and XRD were used to characterize structural properties, elemental compositions, and crystallite sizes of the welded specimens. -
For Hardfacing
Shielded Metal Arc Welding, Flux Cored Arc Welding, Gas Metal Arc Welding, Submerged Arc Welding For Hardfacing █ A guide for selecting welding consumables Weld metal microstructure and main alloying elements determine the performances of welding consumables for hardfacing as summarized in Table 1. In addition, PF-200S/US-63B is good for reclamation of mill rolls. Table 1 Welding consumables and their characteristics Weld metal Type of wear (1) microstructure Hv Features SMAW FCAW GMAW SAW and alloying formula MTM ABR HTW CAV COR HRT IMP HF-240 200- ▪Good crack resistance HF-260 DWH-250 MG-250 G-50 ⁄ USH-250N Pearlite ○ △ × - - × ○ 400 ▪Good machinability HF-330 DWH-350 MG-350 G-50 ⁄ USH-350N HF-350 HF-450 G-50 ⁄ USH-400N HF-500 DWH-450 G-50 ⁄ USH-450N 350- HF-600 DWH-600 Martensite ▪Good wear resistance ○ ○ △ - × △ △ - G-50 ⁄ USH-500N 800 HF-650 DWH-700 MF-30 ⁄ USH-550N HF-700 DWH-800 MF-30 ⁄ USH-600N HF-800K ▪Good resistance to 13%Cr stainless 350- oxidation, heat and ○ △ ○ ○ ○ ○ △ HF-13 - - - steel type 500 corrosion ▪Good wear resistance 500- ▪High toughness and Semi-Austenite ○ ○ △ △ △ △ △ HF-12 - - - 700 good wear resistance ▪High toughness and 150- good impact wear 13%Mn × ○ × △ × × ◎ HF-11 DWH-11 - - 500 resistance High Mn ▪High work hardenability Austenite ▪High hardness at high 16%Mn- 200- temperatures ○ △ ○ ○ ○ ○ ○ HF-16 DWH-16 - - 16%Cr 400 ▪High toughness ▪Excellent erosion 600- resistance DWH-30 High Cr-Fe △ ◎ ◎ × ○ ○ × HF-30 - - 800 ▪Good resistance to DWH-30MV corrosion and heat 800- ▪Excellent resistance to Tungsten carbide type × ◎ × × × × × HF-950 - - - 1200 heavy abrasion Note (1) MTM: Metal-to-metal wear, ABR: Abrasion, HTW: High temp. -
COBALT & NICKEL Based Hardfacing Alloys
COBALT & NICKEL Based Hardfacing Alloys Stoody.com COBALT & NICKEL-BASED RODS, ELECTRODES AND WIRE Stoody has a long history of being a leading supplier of wear and corrosion resistant cobalt and nickel-based alloys for commercial and military use. For generations the Stoodite family of cobalt-based bare rods and coated electrodes, open and gas shielded wire, and submerged arc wire have been trusted by manufacturers and government agencies alike to protect against mechanical and chemical degradation due to corrosion, heat, and other wear factors. Many of these AWS and military-certifiable cobalt and nickel-based hardfacing alloys are commonly utilized today in power generation, chemical and petrochemical production, fluid handling and transportation, pulp and paper production, agricultural and food-related production, and steel manufacturing to name just a few of the many industrial applications. The Stoodite® line of cobalt-based alloys are individually designed to deliver specific characteristics and performance in harsh environments - typically those involving mechanical and chemical degradation with the potential for other contributing wear factors including heat. With SMAW, GMAW, and SAW process options available, Stoodite cobalt-based alloys typically offer anti-galling, high temperature hardness, and resistance to cavitation erosion while bonding well with weldable alloy steels and stainless steels. The Stoody line of nickel-based alloys are also designed for use on low and medium carbon steels, stainless steels, and cast irons. These superior nickel-based products offer abrasion and impact resistance and typically maintain a high level of hardness at temperature with resistance to galling, pitting, and corrosion. The Stoody alloys presented here are the most popular cobalt and nickel-based hardfacing and high alloy products currently being utilized in real world applications. -
Filler Metal Welding
WELDING FILLER METAL DATABOOKUSA 2016 WELDING FILLER METAL DATABOOK TABLE OF CONTENTS COVERED (STICK) ELECTRODES (SMAW) ........................................................................1-1 MIG/MAG WIRES (GMAW) ...................................................................................................2-1 TIG RODS (GTAW) .................................................................................................................3-1 CORED WIRE (FCAW) (MCAW) ...........................................................................................4-1 SUBMERGED ARC WIRES AND FLUXES (SAW) ...............................................................5-1 FILLER METAL CALCULATIONS .........................................................................................6-1 FILLER METAL RECOMMENDATIONS FOR WELDING ASTM STEELS .........................7-1 esab.com I Covered (Stick) Electrodes (SMAW) COVERED (STICK) ELECTRODES (SMAW) TABLE OF CONTENTS COVERED (STICK) ELECTRODES (SMAW) ...................................................................................................................1-4 MILD STEEL ELECTRODES ............................................................................................................................................1-4 Sureweld 10P ...................................................................................................................................................................... 1-6 Sureweld 10P Plus ............................................................................................................................................................. -
A Review Paper on Research Work Done in Hardfacing
International Journal of Application or Innovation in Engineering & Management (IJAIEM) Web Site: www.ijaiem.org Email: [email protected] Volume 5, Issue 9, September 2016 ISSN 2319 - 4847 A REVIEW PAPER ON RESEARCH WORK DONE IN HARDFACING Rupendra Kumar1, Pratibha Kumari2, Dr. K.L.A. Khan3 1M.Tech Scholar, Department of Mechanical Engineering, Krishna Institute of Engineering & Technology, Ghaziabad, U.P. 2 Associate professor, Department of Mechanical Engineering, Krishna Institute of Engineering & Technology, Ghaziabad, U.P. 3Head of department, Department of Mechanical Engineering, Krishna Institute of Engineering & Technology, Ghaziabad, U.P. ABSTRACT Wear is the biggest factor that controls the performance and life of any machine part. The interaction between functional surfaces in their relative motion causes adverse effects in the surface layers, leading to their deterioration. Most worn parts don't fail from a single mode of wear, but from a combination of modes, such as abrasion and erosion etc. Research is going on over years to reduce the wear either in the form of using a new wear resistant material or by improving the wear resistance of the existing material by the addition of any wear resistant alloying elements. According to researchers hardfacing is the best method for overcoming wear problems of machine parts as it increases the life of machine part and also protects from damage. We can use many types of hardfacing alloys according to requirement, which may be cheap or costly. In this paper an attempt has been made to review the work of some researchers who conducted the experimental studies on different wear resistant hardfacing alloys, which are employed on the substrate surface of material by different welding processes. -
Hardfacing and Wear Resistant Use Hardfacing and Wear Many Abrasions Occur Not Just Due to a Singular Cause, but Possibly Two Or More Welding Layers Limitation
Hardfacing General Review Hardfacing process is the most economical way to allow a work to achieve maximum application and usage longevity. As it name suggests, hardfacing is to build up upon the softer base metals’ surface one or multi-layers of hardfacing alloys according to specifi c needs. There are commonly three types of welding process to restore abrasive of wear out work : 1. Build-up If the project base metal suffers great abrasion, use the proper fi ller metal to restore the base metal back to its original dimension on the working piece prior to hardfacing Resistant Use Hardfacing and Wear welding. 2. Buttering When the fi ller metal for hardfacing layer and the base metal’s mechanical properties along with physical property have great variation, it is difficult to weld the two together; hence, it is essential to select the proper fi ller metal for the project base metal to serve as a buffer in reducing the incompatibility. 3. Hardfacing Hardfacing and Wear Hardfacing also known as surface hardening welding is achieved by welding the wear resistant layer onto base metal or surface layer for the purpose of extending the longevity Resistant Use of mechanical equipment. It is normally limited to two to three welding layers. How to select the proper hardfacing fi ller metal : Hardfacing General Review Welding fi ller metal is selected according to the following criteria : 1.Base metal will affect the selection of fi ller metal for base (root ) layer, for example: a. Mn Steel: for equipment suffered severe impact condition. Use high Mn content filler metal to restore the base metal to its original size.