Redalyc.NOISE and VIBRATION of SPACECRAFT STRUCTURES
Total Page:16
File Type:pdf, Size:1020Kb
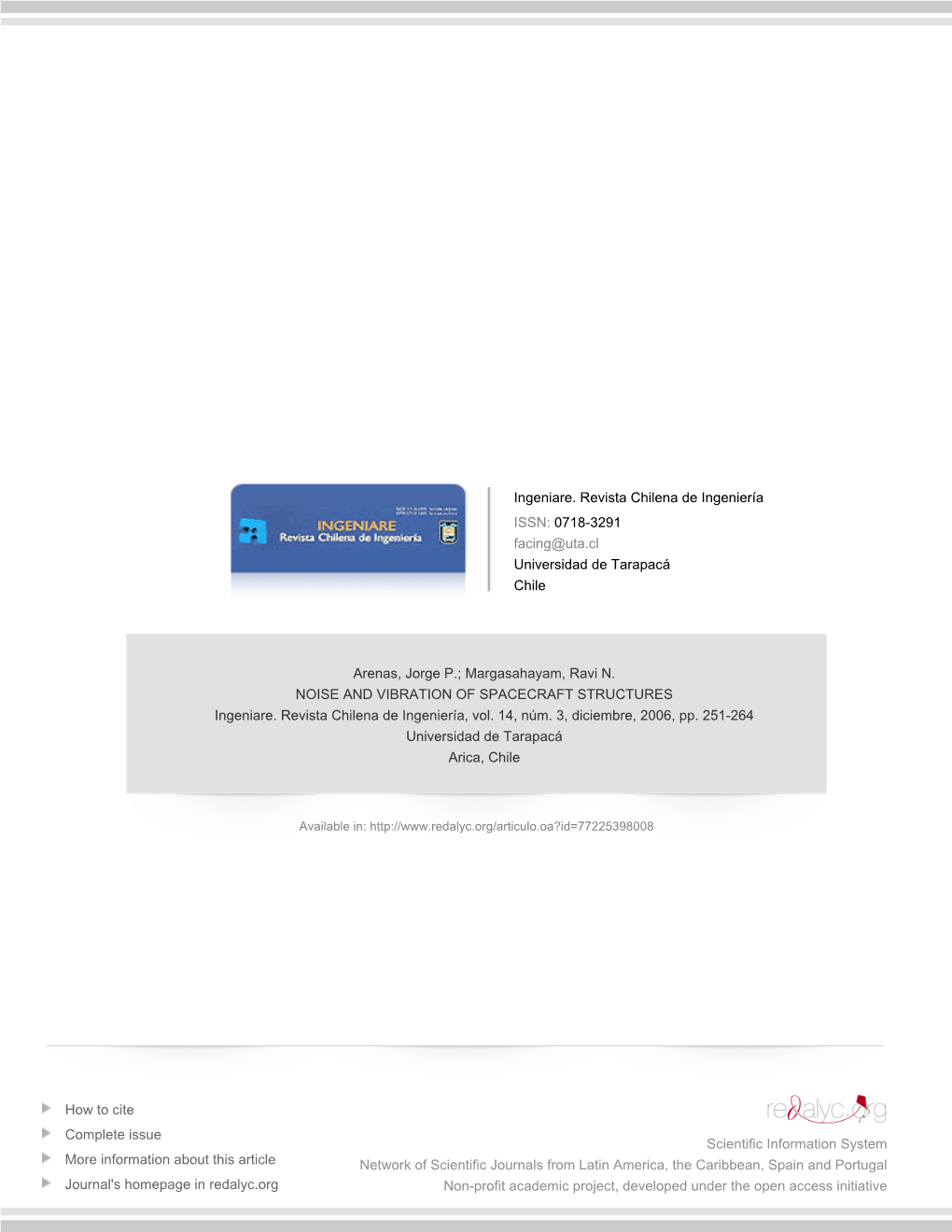
Load more
Recommended publications
-
New Pad Constructed for Smaller Rocket Launches
PROGRAM HIGHLIGHTS • JULY 2015 At NASA’s Kennedy Space Center in Florida, the Ground Systems Development and Operations (GSDO) Program Office is leading the center’s transfor- mation from a historically government-only launch complex to a spaceport bustling with activity involving government and commercial vehicles alike. GSDO is tasked with developing and using the complex equipment required to safely handle a variety of rockets and spacecraft during assembly, transport and launch. For more information about GSDO accomplishments happening around the center, visit http://go.nasa.gov/groundsystems. New Pad Constructed for Smaller Rocket Launches NASA's Kennedy Space Center in Florida took another step forward in its transformation to a 21st century multi-user spaceport with the completion of the new Small Class Vehicle Launch Pad, designated 39C, in the Launch Pad 39B area. This designated pad to test smaller rockets will make it more affordable for smaller aerospace companies to develop and launch from the center, and to break into the commercial spaceflight market. Kennedy Director Bob Cabana and representatives from the Ground Systems Development and Operations (GSDO) Program and the Center Planning and Development (CPD) and Engineering Directorates marked the completion of the new pad during a ribbon-cutting ceremony July 17. NASA Kennedy Space Center Director Bob Cabana, center, helps cut the ribbon on the new Small Class Vehicle Launch Pad, designated 39C, at Kennedy Space Center in Florida. Also helping to cut the ribbon are, from left, Pat Simpkins, director, Engineering and Technology Directorate; Rich Koller, senior vice president of design firm Jones Edmunds; Scott Col- loredo, director, Center Planning and Development; and Michelle Shoultz, president of Frazier Engineering. -
1993 (179Kb Pdf)
February 4, 1993 KSC Contact: Bruce Buckingham KSC Release No. 10-93 Notice To Editors/News Directors: KSC NEWS CENTER OFFICE HOURS FOR PEGASUS ARRIVAL The NASA B-52 aircraft carrying the Orbital Sciences Cor- poration Pegasus rocket is scheduled to arrive at KSC on Sunday, Feb. 7, with launch targeted for Feb. 9. The aircraft is currently scheduled to depart Edwards Air Force Base, Calif., at about 10:00 a.m. EST on Sunday with a single refueling stopover planned at Sheppard AFB, Texas. If weather permits, arrival of the aircraft at KSC's Shuttle Landing Facility should be about 4:30 p.m. EST. Status updates regarding the cross-country flight will be made on KSC's codaphone over the weekend. This can be reached by calling 407/867-2525. Public Affairs officers will be in the KSC Press Site office by 9:30 a.m. Sunday in order to provide status updates by phone. The office, however, will not officially open until it is deter- mined the aircraft will in fact be arriving at KSC. If it is determined that the aircraft will be successful in completing the day-long trip to KSC on Sunday, the office will officially open at 3:00 p.m. In that event, media interested in viewing the B-52/Pegasus arrival should plan on calling the KSC news center at 407/867-2468 for departure times to the Shuttle Landing Facility. News media who do not possess current credentials must con- tact the Public Information Office before close of business Friday, Feb. -
Proposal to Construct and Operate a Satellite Launching Facility on Christmas Island
Environment Assessment Report PROPOSAL TO CONSTRUCT AND OPERATE A SATELLITE LAUNCHING FACILITY ON CHRISTMAS ISLAND Environment Assessment Branch 2 May 2000 Christmas Island Satellite Launch Facility Proposal Environment Assessment Report - Environment Assessment Branch – May 2000 3 Table of Contents 1 INTRODUCTION..............................................................................................6 1.1 GENERAL ...........................................................................................................6 1.2 ENVIRONMENT ASSESSMENT............................................................................7 1.3 THE ASSESSMENT PROCESS ...............................................................................7 1.4 MAJOR ISSUES RAISED DURING THE PUBLIC COMMENT PERIOD ON THE DRAFT EIS .................................................................................................................9 1.4.1 Socio-economic......................................................................................10 1.4.2 Biodiversity............................................................................................10 1.4.3 Roads and infrastructure .....................................................................11 1.4.4 Other.......................................................................................................12 2 NEED FOR THE PROJECT AND KEY ALTERNATIVES ......................14 2.1 NEED FOR THE PROJECT ..................................................................................14 2.2 KEY -
Space Launch System (Sls) Motors
Propulsion Products Catalog SPACE LAUNCH SYSTEM (SLS) MOTORS For NASA’s Space Launch System (SLS), Northrop Grumman manufactures the five-segment SLS heavy- lift boosters, the booster separation motors (BSM), and the Launch Abort System’s (LAS) launch abort motor and attitude control motor. The SLS five-segment booster is the largest solid rocket motor ever built for flight. The SLS booster shares some design heritage with flight-proven four-segment space shuttle reusable solid rocket motors (RSRM), but generates 20 percent greater average thrust and 24 percent greater total impulse. While space shuttle RSRM production has ended, sustained booster production for SLS helps provide cost savings and access to reliable material sources. Designed to push the spent RSRMs safely away from the space shuttle, Northrop Grumman BSMs were rigorously qualified for human space flight and successfully used on the last fifteen space shuttle missions. These same motors are a critical part of NASA’s SLS. Four BSMs are installed in the forward frustum of each five-segment booster and four are installed in the aft skirt, for a total of 16 BSMs per launch. The launch abort motor is an integral part of NASA’s LAS. The LAS is designed to safely pull the Orion crew module away from the SLS launch vehicle in the event of an emergency on the launch pad or during ascent. Northrop Grumman is on contract to Lockheed Martin to build the abort motor and attitude control motor—Lockheed is the prime contractor for building the Orion Multi-Purpose Crew Vehicle designed for use on NASA’s SLS. -
Constellation Program Overview
Constellation Program Overview October 2008 hris Culbert anager, Lunar Surface Systems Project Office ASA/Johnson Space Center Constellation Program EarthEarth DepartureDeparture OrionOrion -- StageStage CrewCrew ExplorationExploration VehicleVehicle AresAres VV -- HeavyHeavy LiftLift LaunchLaunch VehicleVehicle AltairAltair LunarLunar LanderLander AresAres II -- CrewCrew LaunchLaunch VehicleVehicle Lunar Capabilities Concept Review EstablishedEstablished Lunar Lunar Transportation Transportation EstablishEstablish Lunar Lunar Surface SurfaceArchitecturesArchitectures ArchitectureArchitecture Point Point of of Departure: Departure: StrategiesStrategies which: which: Satisfy NASA NGO’s to acceptable degree ProvidesProvides crew crew & & cargo cargo delivery delivery to to & & from from the the Satisfy NASA NGO’s to acceptable degree within acceptable schedule moonmoon within acceptable schedule Are consistent with capacity and capabilities ProvidesProvides capacity capacity and and ca capabilitiespabilities consistent consistent Are consistent with capacity and capabilities withwith candidate candidate surface surface architectures architectures ofof the the transportation transportation systems systems ProvidesProvides sufficient sufficient performance performance margins margins IncludeInclude set set of of options options fo for rvarious various prioritizations prioritizations of cost, schedule & risk RemainsRemains within within programmatic programmatic constraints constraints of cost, schedule & risk ResultsResults in in acceptable -
The SKYLON Spaceplane
The SKYLON Spaceplane Borg K.⇤ and Matula E.⇤ University of Colorado, Boulder, CO, 80309, USA This report outlines the major technical aspects of the SKYLON spaceplane as a final project for the ASEN 5053 class. The SKYLON spaceplane is designed as a single stage to orbit vehicle capable of lifting 15 mT to LEO from a 5.5 km runway and returning to land at the same location. It is powered by a unique engine design that combines an air- breathing and rocket mode into a single engine. This is achieved through the use of a novel lightweight heat exchanger that has been demonstrated on a reduced scale. The program has received funding from the UK government and ESA to build a full scale prototype of the engine as it’s next step. The project is technically feasible but will need to overcome some manufacturing issues and high start-up costs. This report is not intended for publication or commercial use. Nomenclature SSTO Single Stage To Orbit REL Reaction Engines Ltd UK United Kingdom LEO Low Earth Orbit SABRE Synergetic Air-Breathing Rocket Engine SOMA SKYLON Orbital Maneuvering Assembly HOTOL Horizontal Take-O↵and Landing NASP National Aerospace Program GT OW Gross Take-O↵Weight MECO Main Engine Cut-O↵ LACE Liquid Air Cooled Engine RCS Reaction Control System MLI Multi-Layer Insulation mT Tonne I. Introduction The SKYLON spaceplane is a single stage to orbit concept vehicle being developed by Reaction Engines Ltd in the United Kingdom. It is designed to take o↵and land on a runway delivering 15 mT of payload into LEO, in the current D-1 configuration. -
Low Power Energy Harvesting and Storage Techniques from Ambient Human Powered Energy Sources
University of Northern Iowa UNI ScholarWorks Dissertations and Theses @ UNI Student Work 2008 Low power energy harvesting and storage techniques from ambient human powered energy sources Faruk Yildiz University of Northern Iowa Copyright ©2008 Faruk Yildiz Follow this and additional works at: https://scholarworks.uni.edu/etd Part of the Power and Energy Commons Let us know how access to this document benefits ouy Recommended Citation Yildiz, Faruk, "Low power energy harvesting and storage techniques from ambient human powered energy sources" (2008). Dissertations and Theses @ UNI. 500. https://scholarworks.uni.edu/etd/500 This Open Access Dissertation is brought to you for free and open access by the Student Work at UNI ScholarWorks. It has been accepted for inclusion in Dissertations and Theses @ UNI by an authorized administrator of UNI ScholarWorks. For more information, please contact [email protected]. LOW POWER ENERGY HARVESTING AND STORAGE TECHNIQUES FROM AMBIENT HUMAN POWERED ENERGY SOURCES. A Dissertation Submitted In Partial Fulfillment of the Requirements for the Degree Doctor of Industrial Technology Approved: Dr. Mohammed Fahmy, Chair Dr. Recayi Pecen, Co-Chair Dr. Sue A Joseph, Committee Member Dr. John T. Fecik, Committee Member Dr. Andrew R Gilpin, Committee Member Dr. Ayhan Zora, Committee Member Faruk Yildiz University of Northern Iowa August 2008 UMI Number: 3321009 INFORMATION TO USERS The quality of this reproduction is dependent upon the quality of the copy submitted. Broken or indistinct print, colored or poor quality illustrations and photographs, print bleed-through, substandard margins, and improper alignment can adversely affect reproduction. In the unlikely event that the author did not send a complete manuscript and there are missing pages, these will be noted. -
View / Download
www.arianespace.com www.starsem.com www.avio Arianespace’s eighth launch of 2021 with the fifth Soyuz of the year will place its satellite passengers into low Earth orbit. The launcher will be carrying a total payload of approximately 5 518 kg. The launch will be performed from Baikonur, in Kazakhstan. MISSION DESCRIPTION 2 ONEWEB SATELLITES 3 Liftoff is planned on at exactly: SOYUZ LAUNCHER 4 06:23 p.m. Washington, D.C. time, 10:23 p.m. Universal time (UTC), LAUNCH CAMPAIGN 4 00:23 a.m. Paris time, FLIGHT SEQUENCES 5 01:23 a.m. Moscow time, 03:23 a.m. Baikonur Cosmodrome. STAKEHOLDERS OF A LAUNCH 6 The nominal duration of the mission (from liftoff to separation of the satellites) is: 3 hours and 45 minutes. Satellites: OneWeb satellite #255 to #288 Customer: OneWeb • Altitude at separation: 450 km Cyrielle BOUJU • Inclination: 84.7degrees [email protected] +33 (0)6 32 65 97 48 RUAG Space AB (Linköping, Sweden) is the prime contractor in charge of development and production of the dispenser system used on Flight ST34. It will carry the satellites during their flight to low Earth orbit and then release them into space. The dedicated dispenser is designed to Flight ST34, the 29th commercial mission from the Baikonur Cosmodrome in Kazakhstan performed by accommodate up to 36 spacecraft per launch, allowing Arianespace and its Starsem affiliate, will put 34 of OneWeb’s satellites bringing the total fleet to 288 satellites Arianespace to timely deliver the lion’s share of the initial into a near-polar orbit at an altitude of 450 kilometers. -
Evaluation of Electric Energy Generation from Sound Energy Using Piezoelectric Actuator
International Journal of Science and Research (IJSR) ISSN (Online): 2319-7064 Index Copernicus Value (2013): 6.14 | Impact Factor (2014): 5.611 Evaluation of Electric Energy Generation from Sound Energy Using Piezoelectric Actuator Mohana Faroug Saeed Attia1, Afraa Ibraheim Mohmmed Abdalateef2 1Department of Physics, University of Dongola, Sudan 2Collaborator Instructor University of Khartoum, Sudan Abstract: This paper presents the work done on the conversion techniques and methodologies of converting sound energy to its electrical counterpart, and focuses on the future of this type of energy sources than wind energy, solar energy, and biogas. Also, it includes the increase in energy consumption due to ever growing number of electronic devices, and the harvesting energy from humans and using of piezoelectricity. In the experimental work, a piezoelectric generator lead zirconate titante (PZT actuator) is used to extract sound energy from the loudspeaker from various distances and then to convert this energy into electrical energy. The maximum voltage generated by the piezoelectric generator occurs when its resonant frequency is operating near the frequency of sound. The result shows that the maximum output voltage of 28.8 mVrms was obtained with the sound intensity of 80.5 dB resonant frequency of 65 Hz at 1 cm distance in the first mode. In the second mode, the maximum output voltage of 94 m Vrms was obtained with the sound intensity of 105.7 dB at resonant frequency of 378 Hz at 1 cm which is larger than that of the first mode. However, for both modes, voltage decreases as distance increases. Keywords: piezoelectric effect, sound energy, piezoelectric material, resonant frequency, PZT actuator, electricity 1. -
Silencing Nasa's Space Shuttle Crawler
SILENCING NASA’S SPACE SHUTTLE CRAWLER TRANSPORTER R. MacDonalda, C. Faszerb, and R. Margasahayamc aNoise Solutions Inc., #310 605 – 1st Street SW, Calgary, Alberta, Canada T2P 3S9 bFaszer Farquharson & Associates, #304 605 – 1st Street SW, Calgary, Alberta, Canada T2P 3S9 cNASA, John F. Kennedy Space Center, Florida, United States of America 32899 [email protected]; [email protected]; [email protected] Abstract. The crawler transporter (CT) is the world’s second largest known tracked vehicle, weighing 6 million pounds with a length of 131 feet and a width of 113 feet. The Kennedy Space Center (KSC) has two CTs that were designed and built for the Apollo program in the 1960’s, maintained and retrofitted for use in the Space Shuttle program. As a key element of the Space Shuttle ground systems, the crawler transports the entire 12-million-pound stack comprising the orbiter, the mobile launch platform (MLP), the external tank (ET), and the solid rocket boosters (SRB) from the Vehicle Assembly Building (VAB) to the launch pad. This rollout, constituting a 3.5 to 5.0 mile journey at a top speed of 0.9 miles-per-hour, requires over 8 hours to reach either Launch Complex 39A or B. This activity is only a prelude to the spectacle of sound and fury of the Space Shuttle launch to orbit in less than 10 minutes and traveling at orbital velocities of Mach 24. This paper summarizes preliminary results from the Crawler Transporter Sound Attenuation Study, encompassing test and engineering analysis of significant sound sources to measure and record full frequency spectrum and intensity of the various noise sources and to analyze the potential for noise mitigation. -
7. Operations
7. Operations 7.1 Ground Operations The Exploration Systems Architecture Study (ESAS) team addressed the launch site integra- tion of the exploration systems. The team was fortunate to draw on expertise from members with historical and contemporary human space flight program experience including the Mercury, Gemini, Apollo, Skylab, Apollo Soyuz Test Project, Shuttle, and International Space Station (ISS) programs, as well as from members with ground operations experience reaching back to the Redstone, Jupiter, Pershing, and Titan launch vehicle programs. The team had a wealth of experience in both management and technical responsibilities and was able to draw on recent ground system concepts and other engineering products from the Orbital Space Plane (OSP) and Space Launch Initiative (SLI) programs, diverse X-vehicle projects, and leadership in NASA/Industry/Academia groups such as the Space Propulsion Synergy Team (SPST) and the Advanced Spaceport Technology Working Group (ASTWG). 7.1.1 Ground Operations Summary The physical and functional integration of the proposed exploration architecture elements will occur at the primary launch site at the NASA Kennedy Space Center (KSC). In order to support the ESAS recommendation of the use of a Shuttle-derived Cargo Launch Vehicle (CaLV) and a separate Crew Launch Vehicle (CLV) for lunar missions and the use of a CLV for ISS missions, KSC’s Launch Complex 39 facilities and ground equipment were selected for conversion. Ground-up replacement of the pads, assembly, refurbishment, and/or process- ing facilities was determined to be too costly and time-consuming to design, build, outfit, activate, and certify in a timely manner to support initial test flights leading to an operational CEV/CLV system by 2011. -
Energy Efficiency As a Low-Cost Resource for Achieving Carbon Emissions Reductions
Energy Effi ciency as a Low-Cost Resource for Achieving Carbon Emissions Reductions A RESOURCE OF THE NATIONAL ACTION PLAN FOR ENERGY EFFICIENCY SEPTEMBER 2009 About This Document This paper, Energy Effi ciency as a Low-Cost Resource for Achieving Carbon Emissions Reductions, is provided to assist utility regulators, gas and electric utilities, and others in meeting the National Action Plan for Energy Effi ciency’s goal of achieving all cost-effective energy effi ciency by 2025. This paper summarizes the scale and economic value of energy effi - ciency for reducing carbon emissions and discusses the barriers to achieving the potential for cost-effective energy effi ciency. It also reviews current regional, state, and local approaches for including energy effi ciency in climate policy, using these approaches to inform a set of recommendations for leveraging energy effi ciency within state climate policy. The paper does not capture federal climate policy options or recommendations, discussion of tradable energy effi ciency credits, or emissions impacts of specifi c energy effi ciency measures or programs. The intended audience for the paper is any stakeholder interested in learning more about how to advance energy effi ciency as a low-cost resource to reduce carbon emissions. All stakeholders, including state policy-makers, public utility commissions, city councils, and utilities, can use this paper to understand the key issues and terminology, as well as the approaches that are being used to reduce carbon emissions by advancing energy effi ciency policies and programs. Energy Efficiency as a Low-Cost Resource for Achieving Carbon Emissions Reductions A RESOURCE OF THE NATIONAL ACTION PLAN FOR ENERGY EFFICIENCY SEPTEMBER 2009 The Leadership Group of the National Action Plan for Energy Efficiency is committed to taking action to increase investment in cost-effective energy efficiency.