Propulsion and Cryogenic Systems
Total Page:16
File Type:pdf, Size:1020Kb
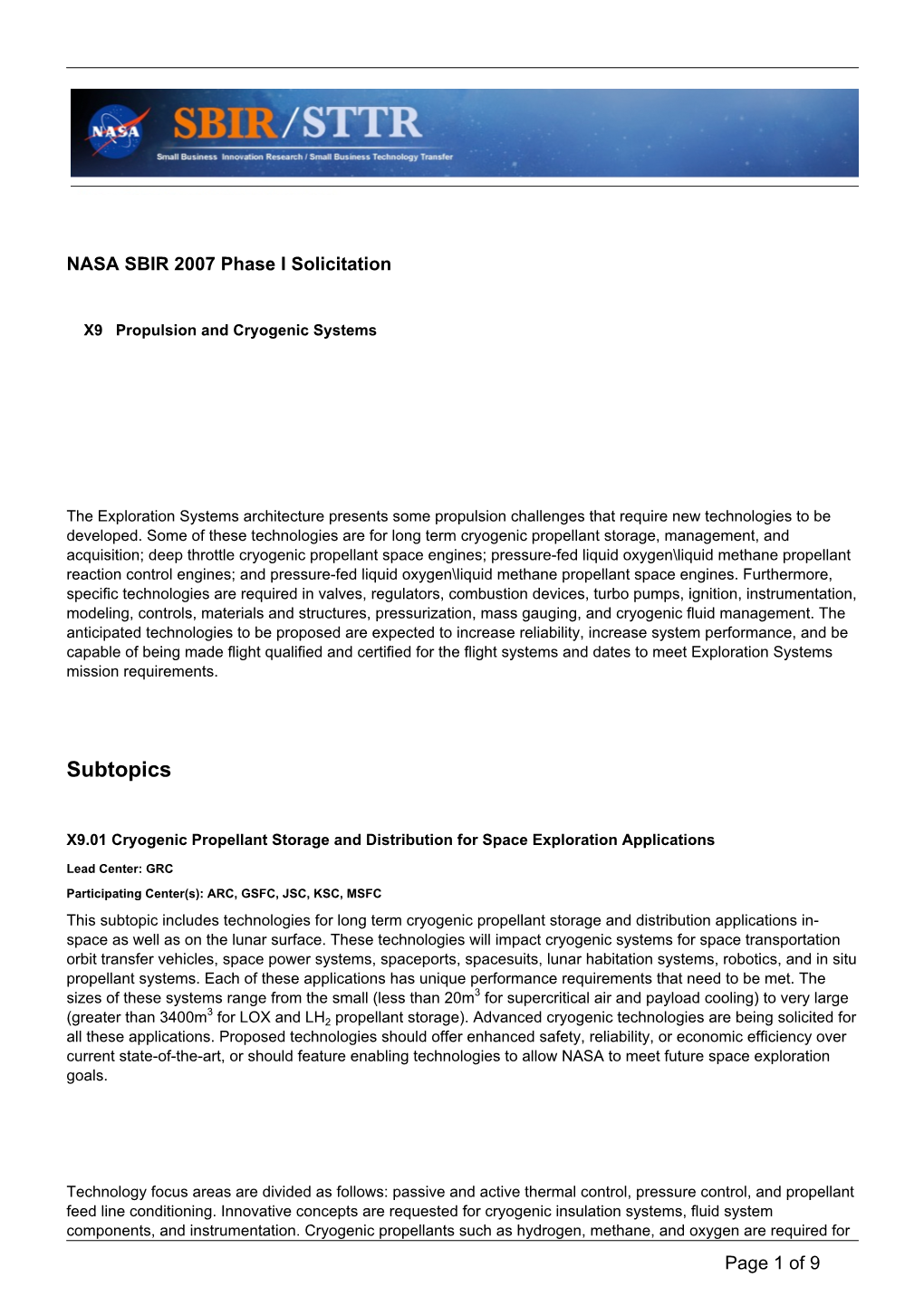
Load more
Recommended publications
-
Safety Consideration on Liquid Hydrogen
Safety Considerations on Liquid Hydrogen Karl Verfondern Helmholtz-Gemeinschaft der 5/JULICH Mitglied FORSCHUNGSZENTRUM TABLE OF CONTENTS 1. INTRODUCTION....................................................................................................................................1 2. PROPERTIES OF LIQUID HYDROGEN..........................................................................................3 2.1. Physical and Chemical Characteristics..............................................................................................3 2.1.1. Physical Properties ......................................................................................................................3 2.1.2. Chemical Properties ....................................................................................................................7 2.2. Influence of Cryogenic Hydrogen on Materials..............................................................................9 2.3. Physiological Problems in Connection with Liquid Hydrogen ....................................................10 3. PRODUCTION OF LIQUID HYDROGEN AND SLUSH HYDROGEN................................... 13 3.1. Liquid Hydrogen Production Methods ............................................................................................ 13 3.1.1. Energy Requirement .................................................................................................................. 13 3.1.2. Linde Hampson Process ............................................................................................................15 -
Materials for Liquid Propulsion Systems
https://ntrs.nasa.gov/search.jsp?R=20160008869 2019-08-29T17:47:59+00:00Z CHAPTER 12 Materials for Liquid Propulsion Systems John A. Halchak Consultant, Los Angeles, California James L. Cannon NASA Marshall Space Flight Center, Huntsville, Alabama Corey Brown Aerojet-Rocketdyne, West Palm Beach, Florida 12.1 Introduction Earth to orbit launch vehicles are propelled by rocket engines and motors, both liquid and solid. This chapter will discuss liquid engines. The heart of a launch vehicle is its engine. The remainder of the vehicle (with the notable exceptions of the payload and guidance system) is an aero structure to support the propellant tanks which provide the fuel and oxidizer to feed the engine or engines. The basic principle behind a rocket engine is straightforward. The engine is a means to convert potential thermochemical energy of one or more propellants into exhaust jet kinetic energy. Fuel and oxidizer are burned in a combustion chamber where they create hot gases under high pressure. These hot gases are allowed to expand through a nozzle. The molecules of hot gas are first constricted by the throat of the nozzle (de-Laval nozzle) which forces them to accelerate; then as the nozzle flares outwards, they expand and further accelerate. It is the mass of the combustion gases times their velocity, reacting against the walls of the combustion chamber and nozzle, which produce thrust according to Newton’s third law: for every action there is an equal and opposite reaction. [1] Solid rocket motors are cheaper to manufacture and offer good values for their cost. -
Cryogenic Technology & Rocket Engines
ISSN (O): 2393-8609 International Journal of Aerospace and Mechanical Engineering Volume 2 – No.5, August 2015 Cryogenic Technology & Rocket Engines AKHIL GARG KARTIK JAKHU KISHAN SINGH ABHINAV B.Tech – Aerospace B.Tech – Aerospace B.Tech – Aerospace MAURYA Engg. Engg. Engg. B.Tech – Aerospace PUNJAB PUNJAB PUNJAB Engg. TECHNICAL TECHNICAL TECHNICAL PUNJAB UNIVERSITY, UNIVERSITY, UNIVERSITY, TECHNICAL JALANDHAR JALANDHAR JALANDHAR UNIVERSITY, akhilgarg.313@g kartik.lphawk@g kishansngh1996 JALANDHAR mail.com mail.com @gmail.com abhinavguru123 @gmail.com ABSTRACT 3.2 What is Cryogenic Rocket Engine? This paper is all about the rocket engine involving the use of A cryogenic rocket engine is a rocket engine that cryogenic technology at a cryogenic temperature (123K). This uses a cryogenic fuel or oxidizer, that is, its fuel or basically uses the liquid oxygen and liquid hydrogen as an oxidizer (or both) is gases liquefied and stored at oxidizer and fuel, which are very clean and non-pollutant very low temperatures. Notably, these engines were fuels compared to other hydrocarbon fuels like petrol, diesel, one of the main factors of the ultimate success in gasoline, LPG, CNG, etc., sometimes, liquid nitrogen is also reaching the Moon by the Saturn V rocket. used as an fuel. During World War II, when powerful rocket engines were first considered by the German, American and Keywords Soviet engineers independently, all discovered that Rocket engine, Cryogenic technology, Cryogenic temperature, rocket engines need high mass flow rate of both Liquid hydrogen and Oxygen. oxidizer and fuel to generate a sufficient thrust. At that time oxygen and low molecular weight 1. -
Cryogenics Unit- I
Department of Aeronautical Engineering Sem ;VII SAEX1041- CRYOGENICS UNIT- I Cryogenics is the branch of physics that deals with the production and effects of very low temperatures. The Large Hadron Collider (LHC) is the largest cryogenic system in the world and one of the coldest places on Earth. All of the magnets on the LHC are electromagnets – magnets in which the magnetic field is produced by the flow of electric current. The LHC's main magnets operate at a temperature of 1.9 K (-271.3°C), colder than the 2.7 K (-270.5°C) of outer space. The LHC's cryogenic system requires 40,000 leak-tight pipe seals, 40 MW of electricity – 10 times more than is needed to power a locomotive – and 120 tonnes of helium to keep the magnets at 1.9 K. Extreme cold for exceptional performances Magnets produce a magnetic field of 8.33 tesla to keep particle beams on course around the LHC's 27-kilometre ring. A current of 11,850 amps in the magnet coils is needed to reach magnetic fields of this amplitude. The use of superconducting materials – those that conduct electricity with no resistance – has proven to be the best way of avoiding overheating in the coils and of keeping them as small as possible. Superconductivity could not happen without the use of cryogenic systems. The coils' niobium-titanium (NbTi) wires must be kept at low temperatures to reach a superconducting state. The LHC's superconducting magnets are therefore maintained at 1.9 K (-271.3°C) by a closed liquid-helium circuit. -
Technology for Fuel Depots (Cont.) Subcooling Propellant
Cryogenic Propellant Depots Design Concepts and Risk Reduction Activities Future InIn--SpaceSpace Operations ((FISOFISO)) March 2, 2011 Christopher McLean 303303--939939--71337133 [email protected] Introduction The capability to provide on-orbit cryogenic refueling for LEO departure stages represents a paradigm shift in the architecture required to support: ─ NASA’s Exploration program ─ Deep-space robot missions ─ National security missions ─ Commercial missions Fuel depots enables large, beyond LEO missions without super heavy lift vehicles This discussion covers an evolutionary approach to flight demonstrate key technologies required for operational fuel depots: ─ Low cost Missions of Opportunity ($50M – $100M) ─ Technology Demonstration Missions (TDM’s) ($150M – $250M) ─ Flagship Technology Demos (FTD’s) ($400M - $1B) Technology developed for these cryogenic fuel depots also increases robustness and capacity of existing launch platforms ─ Technologies to reduce cryogenic propellant boil-off also enhance long-term (>24 hours) storage of cryogenic propellants ─ Increases operational flexibility Page_2 State of the Art Cryogenic Propulsion Systems Current cryogenic propulsion stages rapidly lose residual propellant once on orbit Studies for the Exploration EDS resulted in changing ConOps ─ Initial goal was launch with 90 day on-orbit dwell in LEO ─ Final goal reduced to 4 days due to boil-off rates, desire not to employ active cooling ─ 4 day LEO dwell results in significant system level constraints Cryogenic boost vehicles employ -
Methods and Models for the Concept Design of Liquefied Natural Gas Fuel Systems on Ships Jonas Thiaucourt
Methods and models for the concept design of liquefied natural gas fuel systems on ships Jonas Thiaucourt To cite this version: Jonas Thiaucourt. Methods and models for the concept design of liquefied natural gas fuel systems on ships. Thermics [physics.class-ph]. École centrale de Nantes, 2019. English. NNT : 2019ECDN0032. tel-02462527 HAL Id: tel-02462527 https://tel.archives-ouvertes.fr/tel-02462527 Submitted on 31 Jan 2020 HAL is a multi-disciplinary open access L’archive ouverte pluridisciplinaire HAL, est archive for the deposit and dissemination of sci- destinée au dépôt et à la diffusion de documents entific research documents, whether they are pub- scientifiques de niveau recherche, publiés ou non, lished or not. The documents may come from émanant des établissements d’enseignement et de teaching and research institutions in France or recherche français ou étrangers, des laboratoires abroad, or from public or private research centers. publics ou privés. THESE DE DOCTORAT DE L'ÉCOLE CENTRALE DE NANTES COMUE UNIVERSITE BRETAGNE LOIRE ECOLE DOCTORALE N° 602 Sciences pour l'Ingénieur Spécialité : « Energétique-Thermique-Combustion » Par Jonas THIAUCOURT Méthodes et modèles pour l’étude de faisabilité des navires propulsés au gaz naturel liquéfié Thèse présentée et soutenue à Nantes, le 30 septembre 2019 Unité de recherche : UMR 6598 Laboratoire de recherche en Hydrodynamique, Energétique et Environnement Atmosphérique Rapporteurs avant soutenance Laura A. Pellegrini Professeure, Ecole Polytechnique de Milan Christelle Perilhon Maitre de conférences HDR, Conservatoire National des Arts et Métiers (CNAM) Composition du Jury Président Sofiane Khelladi Professeur, Arts et Métiers ParisTech Examinateur Gordon Paker Professeur, Université Technologique du Michigan Dir. -
Marshall Space Flight Center
National Aeronautics and Space Administration Marshall Space Flight Center Structural Test Stands 4693 and 4697 Two new test stands are changing both the Getting the Data skyline at NASA’s Marshall Space Flight Center in Huntsville, Alabama, and the future of space Inside the SLS core stage, huge cryogenic fuel exploration. tanks, which are also primary vehicle structure, will feed more than 730,000 gallons of super- The first mission for Structural Test Stands 4693 cooled propellant to four RS-25 engines at the and 4697 is to push, pull and apply pressure rocket’s base. The Boeing Co., headquartered loads to the huge propellant tank structures in Chicago, is developing the core stage, which and hardware designed for the core stage of is being built at NASA’s Michoud Assembly facts NASA’s new heavy-lift rocket, the Space Launch Facility in New Orleans. Test versions of the fuel System, subjecting them to the stresses they tanks will be built there and carried by barge to must endure during liftoff and flight. SLS will Marshall for testing. be the world’s most powerful rocket for human space exploration, able to launch astronauts in The liquid hydrogen tank test article, which the Orion spacecraft on deep-space missions, includes the tank, is 149 feet tall and 28 feet including a journey to Mars. in diameter. It will undergo trials in Test Stand 4693, which features twin steel towers with a Data collected from series of tests at Marshall crosshead between them that can be lowered will validate the accuracy and quality of the to accommodate different configurations and computer models and advanced manufacturing future test needs. -
Review on Cryogenic and Jet Engine
International Research Journal of Engineering and Technology (IRJET) e-ISSN: 2395-0056 Volume: 08 Issue: 07 | July 2021 www.irjet.net p-ISSN: 2395-0072 Review on Cryogenic and Jet Engine Abhishiktha Pagadala1, G Ritvik2, Lagumavarapu Venkata Guru Abhiram3 1,2,3Student, Dept. of Aerospace Engineering, Amrita School of Engineering, Tamil Nadu, India. ---------------------------------------------------------------------***--------------------------------------------------------------------- Abstract - This paper gives an insight to the technology Jet engines are reaction engines. They are mainly used behind jet and cryogenic engines. A cryogenic engine uses to propel aircrafts. They draw air from the atmosphere, liquid fuel and oxidizer stored at extremely low temperatures increase its pressure by squeezing it and hence, use it for combustion, whereas a jet engine burns its fuel with the for the most required combustion reaction. The help of air sucked in from the atmosphere. This paper gives resulting hot gases are released from the nozzle of the an overview on how a cryogenic engine is different from a jet engine, providing enough thrust to the aircraft to move forward. engine. Also, the components and working of both cryogenic Jet aircrafts use turbojet engines which usually utilize engine and jet engine have been discussed. The liquid fuel and an afterburn, which is a second combustion chamber, oxidizer, when stored at extreme conditions, gives high placed between the turbine and the nozzle of the enthalpy of combustion on reaction, which makes it more engine. An afterburn elevates the temperature of the efficient when compared to jet engine. CE-20 is the first hot gases, thereby increasing the thrust of the aircraft indigenous cryogenic engine, which has proved to be highly by almost 40% during take-off and much higher during effective when used in GSLV MK-III. -
Cryogenics (Helium Liquefaction)
International Research Journal of Engineering and Technology (IRJET) e-ISSN: 2395 -0056 Volume: 04 Issue: 04 | Apr -2017 www.irjet.net p-ISSN: 2395-0072 Cryogenics (Helium Liquefaction) Gagandeep Singh1, Er. Jasvinder Singh2, Er. Jagdish Singh3, Amandeep Singh4 1Student, Department of Mechanical Engineering, DIET, Kharar 2Assistant Professor, Department of Mechanical Engineering, DIET, Kharar 3Assistant Professor, Department of Mechanical Engineering, DIET, Kharar 4Scientific Assistant C, Pelletron LINAC Facility, TIFR, Mumbai ---------------------------------------------------------------------***--------------------------------------------------------------------- Table No.1: Abstract- This paper represents process for liquefaction of Cryogen fluids and refrigeration fluids boiling helium. Helium becomes liquid at cryogenic temperature so this paper includes the study of cryogenics. Liquefaction of temperature gases is physical conversion of a gas into a liquid state (condensation). We all are familiar with the different phases of Cryogenics Refrigeration matter viz. gas, liquid and solid. The basic difference between these phases is the strength of intermolecular attraction O2 (90.19 K) R134a (246.8 K) between their molecules. By changing the strength of intermolecular attraction between molecules of any phase we Air(78.6 K) R12 (243.3 K) can transform it to another phase. By reducing volume of gases we can change their phase. Most of the gases becomes N2 (77.36 K) R22 (233 K) liquid below -150 ℃ e.g. Helium, nitrogen, oxygen etc. In physics production or working with these super cold temperatures (below -150 ℃) is known as ‘Cryogenics’. H2 (20.39 K) Propane (231.1 K) Liquefaction is used for analyzing the fundamental properties of gas molecules (intermolecular forces), for storage of gases, He (4.2 K) Ethane (184 K) heat treatment, superconductivity, used as cryogenic fuel, food industry and used in medical science. -
Resource Guide for Heavy-Duty LNG Vehicles, Infrastructure, and Support Operations
GRI-02/0105 Resource Guide for Heavy-Duty LNG Vehicles, Infrastructure, and Support Operations FINAL REPORT March, 2002 Prepared by Kevin L. Chandler Matthew T. Gifford Brian S. Carpenter BATTELLE 505 King Avenue Columbus, Ohio 43201 For Brookhaven National Laboratory 75 Rutherford Avenue Upton, NY 11973 and Gas Technology Institute 1700 Mount Prospect Road Des Plaines, IL 60018 GRI Project Manger Mark Perry LEGAL NOTICE This report was prepared by Battelle as work sponsored by the U.S. Department of Energy (DOE) for Brookhaven Science Associates, LLC (Brookhaven), and Gas Technology Institute (GTI). Neither DOE, Brookhaven, GTI, members of these organizations, nor any person acting on behalf of them: a. Makes any warranty or representation, express or implied, with respect to the accuracy, completeness, or usefulness of the information contained in this report, or that the use of any apparatus, method, or process disclosed in this report may not infringe on privately-owned rights; nor b. Assumes any liability with respect to the use of, or for damages resulting from the use of any information, apparatus, method, or process disclosed in this report. Furthermore, any reference to trade names or specific commercial products, commodities or services in this report does not represent or constitute an endorsement, recommendation, or favoring by the sponsors or Battelle of the specific commercial product, commodity, or service. ii REPORT 1. REPORT NO. 2. 3. Recipient’s Accession No. DOCUMENTATION GRI –02/0105 PAGE 4. Title and Subtitle 5. Report Date March 2002 Resource Guide for Heavy-Duty LNG Vehicles, Infrastructure, 6. and Support Operations 7. -
Cryogenic Propellants
International Journal of Engineering Research and General Science Volume 6, Issue 4, July-August, 2018 ISSN 2091-2730 COMPARITIVE STUDY OF SPECIES ANALYSIS OF SEMI- CRYOGENIC PROPELLANTS Danish Parvez, Samadarshi Adhikari Amity University Gurugram, [email protected] Abstract— Different computational software’s were used for species analysis of various semi-cryogenic propellants. After analyzation the ideal and estimated values of various different parameters were calculated. Rocket Propulsion Analysis, a software developed by NASA was used for computing the ideal and estimated values as well as plotting of graphs with respect to different species. The adiabatic temperature of the species was also calculated by performing calculations on Microsoft Excel. In the end 1,1,1,2- tetraflouroethane, a semi-cryogenic propellant was used in order to draw comparison with other species such as Hydrogen, Methane, RPA-1. Graphical representation of the main variables such as pressure, temperature, density, specific heat etc. with respect to the different nozzle positions was also done. Keywords— Cryogenics, Cryogenic Engines, Cryogenic Propellants, Semi-Cryogenic Propellants, Species Analysis, RPA Analysis, Hydrogen (H2), Methane (CH4), RP1(C13H28), 1,1,1,2-Tetra Floro Ethane (CH2FCF3). INTRODUCTION The branch of physics dealing with the production of very low temperature as well as their effect on matter is known as cryogenics. In Cryogenics the gas is cooled by compressing the gas, which in turn releases heat and later when allowed to expand produces ultra-low temperatures. Cooling can also be accomplished by magnetocaloric effect which is a magneto thermodynamic phenomenon in which exposing the material to a changing magnetic field causes a change in temperature. -
Delft University of Technology Cryogenic Rocket Engine
Delft University of Technology Cryogenic rocket engine development at Delft aerospace rocket engineering Wink, J; Hermsen, R.; Huijsman, R; Akkermans, C.; Denies, Luka; Barreiro, F.; Schutte, A.; Cervone, Angelo; Zandbergen, Barry Publication date 2016 Document Version Accepted author manuscript Published in Space propulsion 2016 Citation (APA) Wink, J., Hermsen, R., Huijsman, R., Akkermans, C., Denies, L., Barreiro, F., Schutte, A., Cervone, A., & Zandbergen, B. (2016). Cryogenic rocket engine development at Delft aerospace rocket engineering. In Space propulsion 2016 [SP2016-3124644] Important note To cite this publication, please use the final published version (if applicable). Please check the document version above. Copyright Other than for strictly personal use, it is not permitted to download, forward or distribute the text or part of it, without the consent of the author(s) and/or copyright holder(s), unless the work is under an open content license such as Creative Commons. Takedown policy Please contact us and provide details if you believe this document breaches copyrights. We will remove access to the work immediately and investigate your claim. This work is downloaded from Delft University of Technology. For technical reasons the number of authors shown on this cover page is limited to a maximum of 10. Space Propulsion Conference, Rome, Italy. Copyright c 2016 by 3AF. All rights reserved. SP2016-3124644 CRYOGENIC ROCKET ENGINE DEVELOPMENT AT DELFT AEROSPACE ROCKET ENGINEERING Jeroen Wink,1 Rob Hermsen,1 Ralph Huijsman,1 Christ Akkermans,1 Luka Denies,1 Filipe Barreiro,2 Adriaan Schutte,3 Angelo Cervone,4 Barry Zandbergen5 Corresponding adress: [email protected] 1 Msc.