Guide to the Description and Classification of Glass Beads Oundf in the Americas
Total Page:16
File Type:pdf, Size:1020Kb
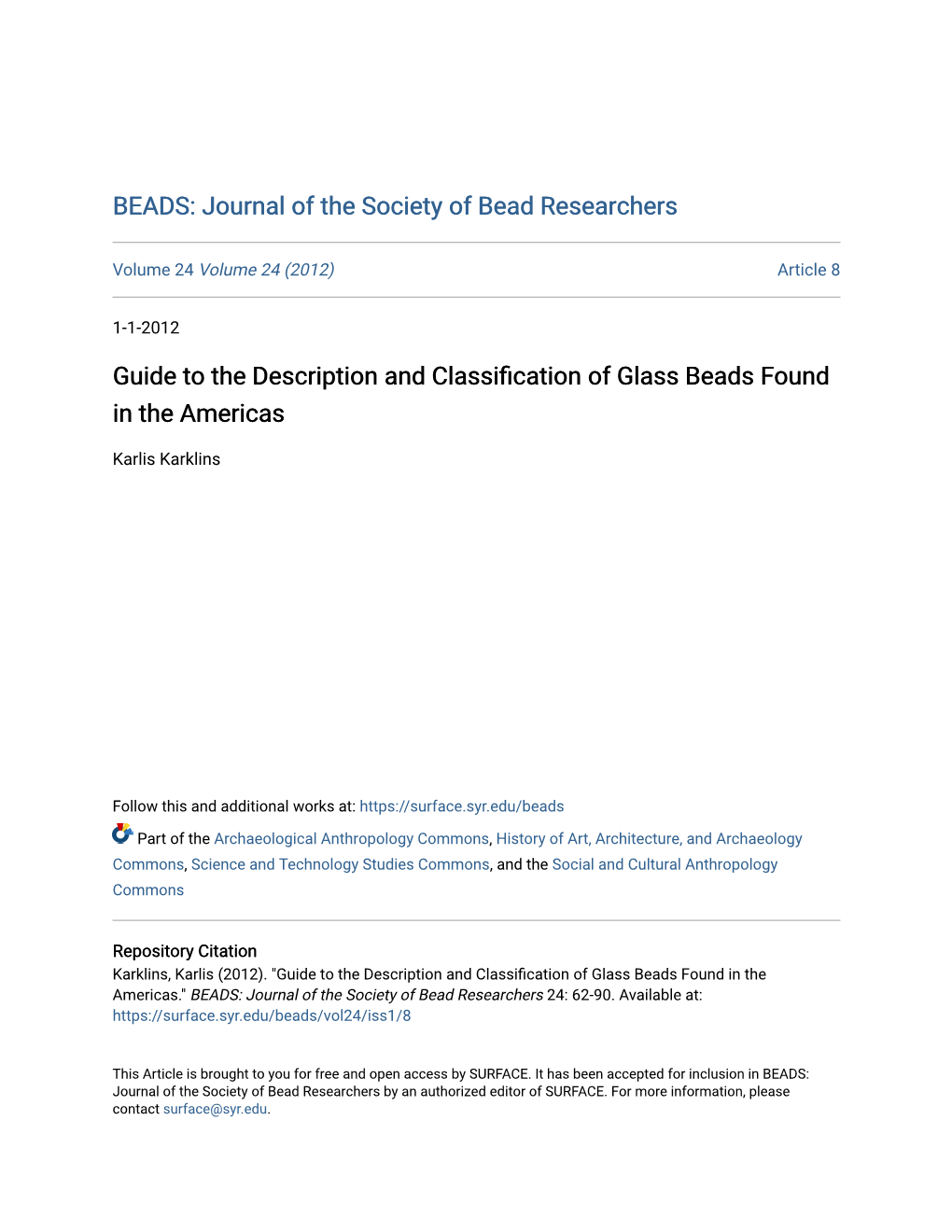
Load more
Recommended publications
-
Frame Design by David Lantrip, MCPF, GCF Framing Stained Glass
Frame Design by David Lantrip, MCPF, GCF Framing Stained Glass skilled framer needs to be prepared to han- dle just about any form of artwork a cus- Atomer presents. Artwork that is seen less often can test a framer’s nerves since the particular needs and framing methods of that type of art might not come readily to mind. This is precisely why framers need to be prepared beforehand. After all, the design counter is not the place to learn about framing new type of artwork if the customer is to have confidence that the job will be done right. One such type of art is stained glass. Despite the fact that stained glass as an art has existed for 1,000 years, it’s not every day that someone brings a piece in to be framed. Displaying stained glass Traditional stained glass work, such as may seem intimidating, that found in but it can be framed churches and important build- and handled routinely ings, is worked in Stained glass worked in the Tiffany method midway through the lead came the soldering process. Once the soldering is complete, a small by following a few metal frame is applied, the solder has a patina applied, and the method. Relatively entire piece is cleaned and polished. basic design principles large pieces of glass, cut to shape, are held within H-shaped channels of lead known as foil strip, usually about ¼” wide, to the edge of the “came.” The ends of the came are soldered to adja- individual pieces of glass, burnishing and folding it cent pieces, and the glass is held tight with mastic to either side of the glass. -
Ghana's Glass Beadmaking Arts in Transcultural Dialogues
Ghana’s Glass Beadmaking Arts in Transcultural Dialogues Suzanne Gott PHOTOS BY THE AUTHOR EXCEPT WHERE OTHERWISE NOTED hanaian powder-glass beads first captured spread of West African strip-weaving technologies. my attention in 1990, when closely examin- With the beginnings of European maritime trade in the late ing a strand of Asante waist beads purchased fifteenth century, an increasing volume of glass beads and glass in Kumasi’s Central Market. Looking at the goods were shipped to trade centers along present-day Ghana’s complex designs of different colored glasses, Gold Coast,1 stimulating the growth of local beadworking and I was struck with the realization that each powder-glass beadmaking industries. The flourishing coastal bead had been skillfully and painstakingly crafted. This seem- trade achieved a more direct engagement between European Gingly humble and largely unexamined art merited closer study merchants and trading communities than had been possible and greater understanding (Fig. 1). I worked with Christa Clarke, with the trans-Saharan trade, and enhanced European abilities Senior Curator for the Arts of Global Africa at the Newark to ascertain and respond to local West African consumer pref- Museum, to develop the 2008–2010 exhibition “Glass Beads of erences. This interactive trade environment also facilitated the Ghana” at the Newark Museum to introduce the general public impact of the demands of Gold Coast consumers on European to this largely overlooked art (Fig. 2). The following study pro- product design and production, a two-way dynamic similar to vides a more in-depth examination of Ghanaian glass beadmak- the trade in African-print textiles (Nielsen 1979; Steiner 1985). -
The Traveling Beads
The Traveling Beads What does this colorful 21st century Venetian glass necklace have in common with glass beads found by archeologists at Manzanar? A close look reveals that all the found beads were made of the same material, of similar color and shape, served the same functions, and originated from the same part of the world. How could beads from southern Europe appear thousands of miles away in the sand at Manzanar amongst American Indian artifacts? What do they reveal about the Owens Valley Paiute (Numu) who inhabited Manzanar long before it was a WWII War Relocation Center? For centuries, Europeans have created beautiful glass objects that have served as beads, jewelry, money, vases, lamps and art objects. As early as 1291, there is evidence that artisans working in the glass factories of Italy have molded some of the most beautiful glass products in the world. When European explorers from Spain, Portugal, Italy and France began their land explorations in the New World, they brought these beautiful objects with them to trade with the people they hoped to find in the new land. Archeologists have documented many American Indian sites in all parts of California that contain glass objects and beads of European origin. Trade networks existed throughout the country along river ways and trails allowing indigenous people to exchange resources (or goods) including manufactured items, such as beads. Regional exchanges must have occurred between the Spaniards and the Indians as the missions were built along the west coast of California. The establishment of the mission system was most likely responsible for the mass distribution of glass beads throughout California. -
Glassblowers of Venice Kept Their Art So Secret That It Almost Died out by Associated Press, Adapted by Newsela Staff on 02.11.16 Word Count 620
Glassblowers of Venice kept their art so secret that it almost died out By Associated Press, adapted by Newsela staff on 02.11.16 Word Count 620 Glassblower William Gudenrath puts enamel on a bowl with techniques used by Renaissance Venetians at the Corning Museum of Glass in Corning, New York, Jan. 22, 2016. Gudenrath spent decades researching how Renaissance glassmakers produced objects that are now considered works of art. Photo: AP/Mike Groll ALBANY, N.Y. — A modern-day glassblower believes he has unraveled the mysteries of Venetian glassmaking that was crafted during the Renaissance. The Renaissance was a cultural movement in Europe that lasted from the 1300s to the 1600s. During that period, glassmakers' secrets were closely guarded by the Venetian government. Anyone who spoke of them could be killed. Specially Skilled Craftsmen Today's glassblowers work with gas-fired furnaces and electric-powered ovens called kilns. Their studios are well lit and have proper air ventilation. The craftsmen of Murano, an island near Venice, Italy, did not have such technology. Yet they turned out pieces of art popular in museums today. The techniques, or the methods they used to make the objects, remained sought after for centuries. William Gudenrath spent years studying Venetian glass collections at American and European museums. He compared them with newer glasswork from Venice. He experimented on his own and traveled to Italy many times. Gudenrath combined all of his knowledge to produce an online guide. Guiding Modern Artists The guide is called "The Techniques of Renaissance Venetian Glassworking." It was recently posted on the website of the Corning Museum of Glass in New York. -
The Protohistoric Period in the Western Great Basin
UC Merced Journal of California and Great Basin Anthropology Title The Protohistoric Period in the Western Great Basin Permalink https://escholarship.org/uc/item/7xp393zf Journal Journal of California and Great Basin Anthropology, 12(1) ISSN 0191-3557 Author Arkush, Brooke S Publication Date 1990-07-01 Peer reviewed eScholarship.org Powered by the California Digital Library University of California Journal of California and Great Basin Anthropology Vol. 12, No. 1, pp. 28-36 (1990). The Protohistoric Period in the Western Great Basin BROOKE S. ARKUSH, Dept. of Sociology and Anthropology, Weber State Univ., Ogden, UT 84408-1208. X HE cultural historical framework for the types and cultural developments. The study western Great Basin derives from a of protohistoric sites and components can compilation of archaeological data which improve our understanding of native cultures identifies time-sensitive artifact types, most as they stood on the brink of intensive contact notably series of projectile points, styles of with Euroamerican society. Moreover, these basketry, marine shell beads, and aboriginal investigations will aid in the identification of ceramics (Elston 1986). The four major subsequent changes in aboriginal material and divisions of the western Great Basin cultural nonmaterial culture and the impacts these chronology (Pre-Archaic, Early Archaic, changes had on ethnographically documented Middle Archaic, and Late Archaic) were groups. This paper is primarily concerned made on the basis of perceived changes in with the protohistory of the western region, as adaptive strategies, which are assumed to be the author is most familiar with its archaeolo reflected in artifact assemblages. Generally gy, ethnography, and history. -
Venetian Beads
BEADS: Journal of the Society of Bead Researchers Volume 10 Volume 10-11 (1998-1999) Article 9 1998 Venetian Beads Frank Hird Follow this and additional works at: https://surface.syr.edu/beads Part of the Archaeological Anthropology Commons, History of Art, Architecture, and Archaeology Commons, Science and Technology Studies Commons, and the Social and Cultural Anthropology Commons Repository Citation Hird, Frank (1998). "Venetian Beads." BEADS: Journal of the Society of Bead Researchers 10: 57-62. Available at: https://surface.syr.edu/beads/vol10/iss1/9 This Article is brought to you for free and open access by SURFACE. It has been accepted for inclusion in BEADS: Journal of the Society of Bead Researchers by an authorized editor of SURFACE. For more information, please contact [email protected]. VENETIAN BEADS Frank Hird Interesting accounts of the manufacture of Venetian glass It was in the thirteenth or fourteenth centuries beads turn up in the most unlikely places. The one repro historians do not agree upon the exact date-that duced here was published in The Girl's Own Paper for Febru bead-making was established at Murano, and through ary 1, 1896 (Vol. 17, No. 840, pp. 292-294). In addition to all the years during which Ven ice exercised her almost presenting a decent description ofthe manufacture ofdrawn and blown beads during the latter part of the 19th century, imperial sway, the glass manufacture, on this ugly and Mr. Hird gives us details concerning the setting in which the dirty little island, was one of her glories. The beadmakers and bead stringers worked. -
Beaded Jewelry Designs Class-A Piece of Delicate Valentines Day Gifts For
Beaded jewelry designs class-a piece of delicate valentines day gifts for her Via learning today’s beaded jewelry designs class, you will gain another method to bead some delicate valentines day gifts for her. While practicing the tutorial, you only need several inches of Tiger tail wire and a few pearlized Acrylic Beads and 12/0 Seed Beads. Giving peculiar valentines day gifts for her, to the special women, is an unexceptionable chance to get her a little bit more wild with joy. Not only for the Valentine’s Day on routine, but also for her birthday or Christmas, etc. Valentine’s Day is about romantic, but never underestimates the significant value of individual gifts. Hence, in this article, I will show you one of the numerous beaded jewelry designs classes relate to the unique occasion. Things you will need: 8mm Acrylic Beads-Imitation Shell & Pearl 8mm Rondelle Swarovski Crystal Beads 12/0 Seed Beads Crimp bead Earring hooks Tiger tail wire Side Cutting Plier Wire-cutter Plier How to make valentines day gifts for her? Step1: bead the first flower portion 1. Prepare 50cm long Tiger tail wire and then form a loop with 6 pieces of 12/0 Seed Beads; 2. Slide the following beads on outer wire tip in order: 8mm Pearlized Acrylic Bead*1, 12/0 Seed Bead, 8mm Pearlized Acrylic Bead*1, 12/0 Seed Bead. Next, cross both tips through another 8mm Pearlized Acrylic Bead; 3. Do the same with outer wire. Further, thread the inner tip through its adjacent seed bead. At last, cross both tips through one 8mm Pearlized Acrylic Bead again; 4. -
ORNAMENT 30.3.2007 30.3 TOC 2.FIN 3/18/07 12:39 PM Page 2
30.3 COVERs 3/18/07 2:03 PM Page 1 992-994_30.3_ADS 3/18/07 1:16 PM Page 992 01-011_30.3_ADS 3/16/07 5:18 PM Page 1 JACQUES CARCANAGUES, INC. LEEKAN DESIGNS 21 Greene Street New York, NY 10013 BEADS AND ASIAN FOLKART Jewelry, Textiles, Clothing and Baskets Furniture, Religious and Domestic Artifacts from more than twenty countries. WHOLESALE Retail Gallery 11:30 AM-7:00 PM every day & RETAIL (212) 925-8110 (212) 925-8112 fax Wholesale Showroom by appointment only 93 MERCER STREET, NEW YORK, NY 10012 (212) 431-3116 (212) 274-8780 fax 212.226.7226 fax: 212.226.3419 [email protected] E-mail: [email protected] WHOLESALE CATALOG $5 & TAX I.D. Warehouse 1761 Walnut Street El Cerrito, CA 94530 Office 510.965.9956 Pema & Thupten Fax 510.965.9937 By appointment only Cell 510.812.4241 Call 510.812.4241 [email protected] www.tibetanbeads.com 1 ORNAMENT 30.3.2007 30.3 TOC 2.FIN 3/18/07 12:39 PM Page 2 volumecontents 30 no. 3 Ornament features 34 2007 smithsonian craft show by Carl Little 38 candiss cole. Reaching for the Exceptional by Leslie Clark 42 yazzie johnson and gail bird. Aesthetic Companions by Diana Pardue 48 Biba Schutz 48 biba schutz. Haunting Beauties by Robin Updike Candiss Cole 38 52 mariska karasz. Modern Threads by Ashley Callahan 56 tutankhamun’s beadwork by Jolanda Bos-Seldenthuis 60 carol sauvion’s craft in america by Carolyn L.E. Benesh 64 kristina logan. Master Class in Glass Beadmaking by Jill DeDominicis Cover: BUTTERFLY PINS by Yazzie Johnson and Gail Bir d, from top to bottom: Morenci tur quoise and tufa-cast eighteen karat gold, 7.0 centimeters wide, 2005; Morenci turquoise, lapis, azurite and fourteen karat gold, 5.1 centimeters wide, 1987; Morenci turquoise and tufa-cast eighteen karat gold, 5.7 centimeters wide, 2005; Tyrone turquoise, coral and tufa- cast eighteen karat gold, 7.6 centimeters wide, 2006; Laguna agates and silver, 7.6 centimeters wide, 1986. -
Mead Art Museum Andrew W. Mellon Faculty Seminar: Jan 15 and 16, 2015
Mead Art Museum Andrew W. Mellon Faculty Seminar: Jan 15 and 16, 2015 Looking at Glass through an Interdisciplinary Lens: Teaching and Learning with the Mead’s Collection Books: Bach, Hans and Norbert Neuroth, eds. The Properties of Optical Glass. Berlin: Springer-Verlag, 1995. Barr, Sheldon. Venetian Glass: Confections in Glass, 1855-1914. New York: Harry N. Abrams, 1998. Battie, David and Simon Cottle, eds. Sotheby's Concise Encyclopedia of Glass. London: Conran Octopus, 1991. Blaszczyk, Regina Lee. Imagining Consumers, Design and Innovation from Wedgwood to Corning. Baltimore: Johns Hopkins University Press, 2000. Bradbury, S. The Evolution of the Microscope. Oxford: Pergamon Press, 1967. Busch, Jason T., and Catherine L. Futter. Inventing the Modern World: Decorative Arts at the World’s Fairs, 1951-1939. New York, NY: Skira Rizzoli, 2012. Carboni, Stefano and Whitehouse, David. Glass of the Sultans. New York: Metropolitan Museum of Art; Corning, NY: The Corning Museum of Glass; Athens: Benaki Museum; New Haven and London: Yale University Press, 2001. Charleston, Robert J. Masterpieces of glass: a world history from the Corning Museum of Glass. 2nd ed.: New York, Harry N. Abrams, 1990. The Corning Museum of Glass. Innovations in Glass. Corning, New York: The Corning Museum of Glass, 1999. Lois Sherr Dubin. The History of Beads: from 30,000 B.C. to the present. London: Thames & Hudson, 2006. Fleming, Stuart. Roman Glass: Reflections of Everyday Life. Philadelphia: University of Pennsylvania Museum, 1997. ----Roman Glass: Reflections on Cultural Change. Philadelphia: University of Pennsylvania Museum of Archaeology and Anthropology, 1999. 1 Frelinghuysen, Alice Cooney. Louis Comfort Tiffany at the Metropolitan Museum. -
Japanning 101. Japanning in a Can, Easy Peasy
Japanning 101. Japanning in a Can, Easy Peasy For a full discussion on various japanning mixes, quality of finish, durability and tips and techniques for success, refer to my earlier article, Japanning, or The Art of Embracing the Arcane at www.aPlaneLife.us. I highly recommend reading this article before beginning your project to understand the various mixtures and results. Have proper expectations goes a long way toward success. At the request of some readers, this series of articles will serve as a condensed, “how-to” for japanning an antique cast iron hand plane using various japanning products and mixtures. This series will start with the easiest method, commercially available japanning mix. This article will only cover the use of commercially available Rio Grande Asphaltum Varnish, although the tips and techniques should apply equally well to another commercially available pre-mixed japanning, Old PontyPool. I have chosen to focus on the Rio Grande product as I have significant experience using it, and it is very favorably priced compared to Old PontyPool. Affordable, economically sized and delivered to your door, easy. This product delivers a very deep, rich finish. Absolutely beautiful. Rio Grande Jewelers Asphaltum Varnish is available in pint cans online for about $17.00 plus shipping. Old PontyPool is sold by the quart at around $84.00 plus shipping. A pint of asphaltum varnish should cover about 15 size 4 hand planes. Old PontyPool may have more favorable performance, I have not used it, but given a limited shelf life and the quantity sold, I believe more people will be satisfied with the Rio Grande product. -
Victorian Heritage Database Place Details - 30/9/2021 St Paul's Cathedral & Organ
Victorian Heritage Database place details - 30/9/2021 St Paul's Cathedral & Organ Location: 22-40 Swanston Street, cnr Flinders Street, MELBOURNE VIC 3000 - Property No B1163 Heritage Inventory (HI) Number: Listing Authority: HI Extent of Registration: Statement of Significance: Church One of the later and larger works of the important English architect William Butterfield, who never visited Australia. The cathedral dates from 1880 to 1891, and as conceived had an octagonal crossing tower and two saddle - backed west towers which would have given it a High Victorian Rhenish air. These were not built, and the present conventional Gothic spires are the work of the Sydney architect James Barr. Characteristic Butterfield details including the contrasting texture of the Waurn Ponds and Barrabool stone cladding, and the horizontally striped interior ultimately derived from Siena Cathedral (though used by Butterfield at Rugby and elsewhere). The interior is lavishly fitted out with encaustic tile floor and wainscoting, stained glass by Clayton & Bell of London, a reredos of Derbyshire spa, Devonshire marble and Venetian glass mosaic, organ by T.C. Lewis, and furniture and fittings of blackwood. What had not been completed at the time of Butterfield's premature 1 resignation in 1888 was carried forward with sympathy and competence by the Melbourne architect Joseph Reed. The classification also embraces the vestry, administrative and Chapter House complex, shop frontages, covered walkways, and iron railings on stone plinths. Classified:State: 08/12/1977 St Paul's Cathedral Organ, A four-manual organ, originally of 50 speaking stops, built by the renowned London organbuilder Thomas C Lewis in 1890. -
The Complete Illustrated Guide to Shaping Wood / Lonnie Bird
The COMPLETE ILLUSTRATED Guide to ShapingWood LONNIE BIRD ➤ Squares, Circles, and Ellipses ➤ Edge Treatments and Moldings ➤ Coves, Reeds, and Flutes ➤ Bent and Laminated Curves ➤ Turned and Carved Shapes The COMPLETE ILLUSTRATED Guide to ShapingWood TJ51-1-2008 IMUS 7/UOA0069-Shaping Wood W:9.25”xH:10.875” Wood TJ51-1-2008 IMUS 7/UOA0069-Shaping 175L EX 128White A M/A(D) The COMPLETE ILLUSTRATED Guide to ShapingWood LONNIE B IRD t TJ51-1-2008 IMUS 7/UOA0069-Shaping Wood W:9.25”xH:10.875” Wood TJ51-1-2008 IMUS 7/UOA0069-Shaping 175L EX 128White A M/A Magenta(D) Text © 2001 by Lonnie Bird Photographs © 2001 by Lonnie Bird Illustrations © 2001 by The Taunton Press, Inc. All rights reserved. Pp The Taunton Press, Inc., 63 South Main Street, PO Box 5506, Newtown, CT 06470-5506 e-mail: [email protected] DESIGN: Lori Wendin LAYOU T: Suzi Yannes ILLUSTRATOR: Mario Ferro PHOTOGRAPHER: Lonnie Bird LIBRARY OF CONGRESS CATALOGING-IN-PUBLICATION DATA: Bird, Lonnie. The complete illustrated guide to shaping wood / Lonnie Bird. p. cm. Includes index. ISBN-13: 978-1-56158-400-0 ISBN-10: 1-56158-400-2 1. Woodwork. I. Title. TT180 .B57 2001 TJ51-1-2008 IMUS 7/UOA0069-Shaping Wood W:9.25”xH:10.875” Wood TJ51-1-2008 IMUS 7/UOA0069-Shaping 175L EX 128White A M/A Magenta(D) 684’.08--dc21 2001027430 Printed in Thailand 1098765 About Your Safety: Working with wood is inherently dangerous. Using hand or power tools improperly or ignoring safety practices can lead to permanent injury or even death.