Quality Initiatives in the Air Force Development of Reusable Launch Vehicles
Total Page:16
File Type:pdf, Size:1020Kb
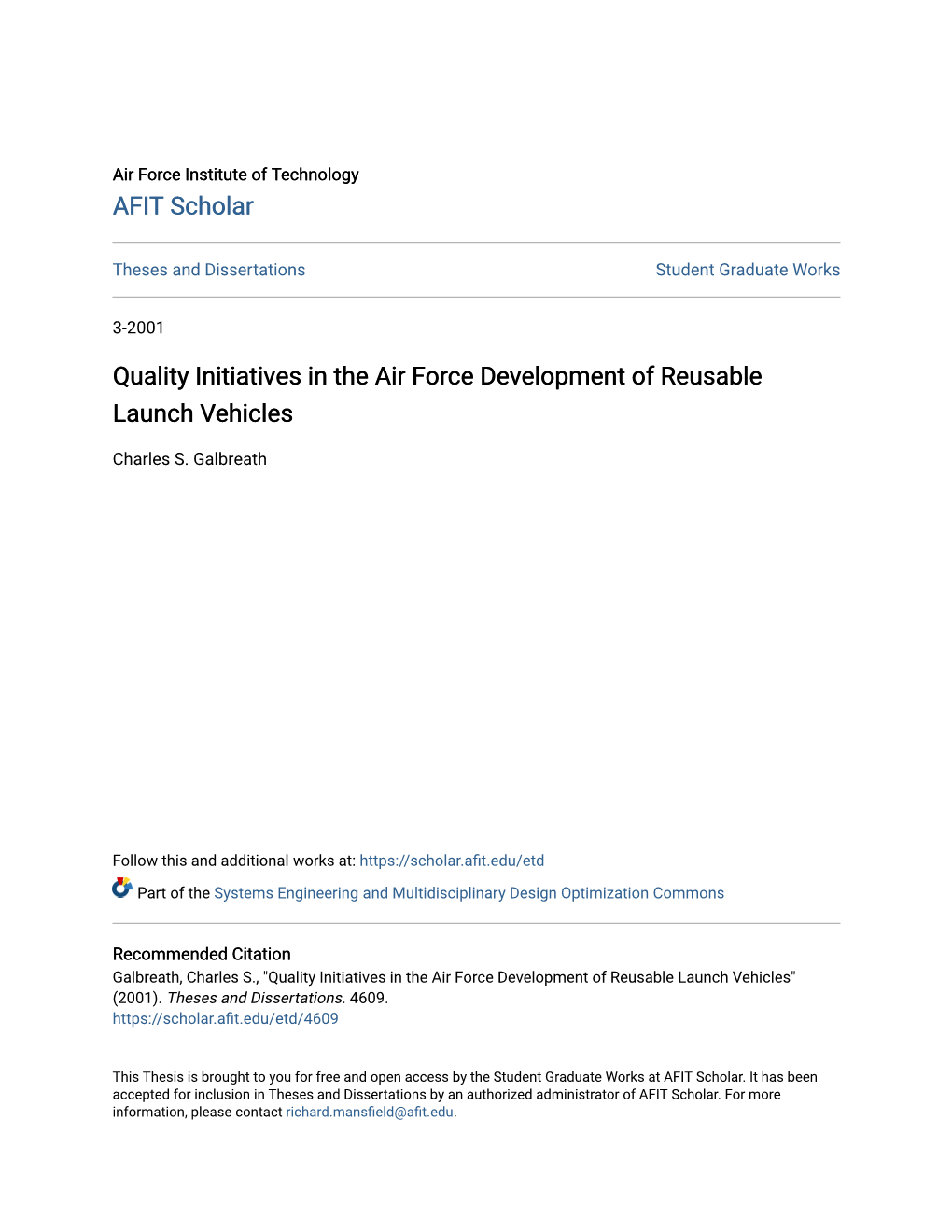
Load more
Recommended publications
-
50Th SCS Helps Build Veteran Retreat
Schriever Air Force Base VOL. 9, NO. 23 June 7, 2007 www.schriever.af.mil Asian-Pacific Heritage Cultural showcase brings month of activities to a close. Page 9 Base Briefs 50th SCS helps build veteran retreat Marian House seeks volunteers The Marian House Soup Kitchen in By Lorna Gutierrez Satellite Flyer Colorado Springs needs volunteers to help with food preparation, serving The setting is in the heart the Wet and cleanup June 9. Mountains, facing the Sangre de Cristo Volunteers may work either a 7 to Mountains, where a 160-acre ranch is com- 10 a.m. shift or a 10 a.m. to 1:30 p.m. ing together to serve injured soldiers in their shift. recuperation process. Eagle Summit Ranch, located near Anyone interested in volunteer- Westcliffe, Colo., will be open to service- ing should contact Len Packer of members who have been injured in the Global the National Reconnaissance Office War on Terrorism. Schriever’s 50th Space Operations Squadron at 567-7707. Communications Squadron is helping out with the project one weekend each month to Right turns have right-of-way make it ready for its ribbon cutting Sept. 11. Drivers making left turns from “The 7,300-square-foot Log-built lodge Curtis Road onto Irwin Road must literally sets atop a ridge where eagles soar yield right-of-way to vehicles turning and has many features specifically designed right onto Irwin Road. to accommodate the veterans’ physical limita- Turning in front of someone who has tions,” said Chief Master Sgt. Steve Alexander right-of-way increases the possibility who, along with Lt. -
Space Alert! Global Network Against Weapons and Nuclear Power in Space Spring/Summer 2020 [email protected] • Newsletter #39
Space Alert! Global Network Against Weapons and Nuclear Power in Space SPRING/SUMMER 2020 [email protected] • www.space4peace.org Newsletter #39 A Space Force in Times of Economic & Health Crisis by Karl Grossman Amid the scourge of coronavirus sweeping the US, the rising death toll and huge shortages in medical equip- ment needed to treat victims of the epidemic and protect doctors, nurses and other health care workers, the Space Force has gotten its “first new offensive weapon” and the government is getting ready to pour billions into the newly established sixth branch of its armed forces. “Space Force Just Received Its First New Offensive Weapon,” was the headline of a March 13th article on “The War Zone” section of the website “The Drive.” The sub-head: “This is just one of two acknowledged US ‘counterspace’ capabilities, but there are more in the classified realm.” The article said the “new offensive weapon system [is] an upgraded version of a ground-based satellite jamming sys- tem. It quoted Lt. Colonel Steven Brogan, the Combat Systems branch leader within the Space Force’s Special Programs Direc- based systems,” said the article. “The Trump administration’s $740.5 along with US neighbor Canada—have torate as saying: “This upgrade puts the It also quoted Space Force Vice Com- billion budget request for [the military] for decades been seeking to expand the ‘force’ in Space Force and is critical for mander Lt. General David Thomas in 2021 includes $15.4 billion for the US Outer Space Treaty, to ban any weapons Space as a warfighting domain.” speaking about how “the new service Space Force, according to documents in space. -
Combat Skills Prepare Airmen for Deployment Staff Sgt
Farewell to the Chief! Come out to the Fitness Center Annex Friday starting at 9 a.m. to wish 50th Space Wing Command Chief Master Sgt. Russell Kuck a fond farewell! VOL. 8, NO. 14 APRIL 6, 2006 Colorado Springs, Colo. www.schriever.af.mil Combat skills prepare Airmen for deployment Staff Sgt. Don Branum 50th Space Wing Public Affairs What difference does Expeditionary Combat Skills train- ing make for Airmen who are preparing to deploy? For one satellite systems operator with the 4th Space Operations Squadron here, the answer is: a big one. “I feel better prepared now than before,” Senior Airman Dale Harris said. “If your career field doesn’t deploy, you should get this kind of refresher training every couple of years.” Airman Harris was one of 100 Airmen who participated in a Wing Expeditionary Readiness Inspection here March 14 to 16. He will deploy with Aerospace Expeditionary Forces 3 and 4. The WERI was the first deployment training environment Airman Harris had experienced since Basic Military Training’s Warrior Week at Lackland Air Force Base, Texas. The ECS training included convoy training, improvised explosive device awareness, individual tactical maneuvers, M-16 familiarization, rifle fighting and integrated base defense. “They made it realistic—like it would be out in the field, not like we were sitting in a tent all day,” he said. Airman Harris’ appraisal is not the only positive review the combat training has received. Several Airmen photo by Kim Kruis-Johnson approached Lt. Col. Paul Scholl, 50th Security Forces Airmen practice individual tactical maneuvers during a Wing Expeditionary Readiness Inspection here March 14 to 16. -
Strategic Master Plan FY06 and Beyond
Strategic Master Plan FY06 and Beyond AIR FORCE SPACE COMMAND STRATEGIC MASTER PLAN FY06 and Beyond AIR FORCE SPACE COMMAND Strategic Master Plan FY06 and Beyond For copies of this document or for more information on the AFSPC Integrated Planning Process contact: HQ AFSPC/XPXP 150 Vandenberg Street, Suite 1105 Peterson AFB, CO 80914-4610 719-554-5323 (DSN) 692-5323 e-mail: [email protected] AIR FORCE SPACE COMMAND 1 October 2003 Strategic Master Plan FY06 and Beyond TABLE OF CONTENTS FOREWORD ................................................................................................................................I TABLE OF CONTENTS................................................................................................................ II LIST OF FIGURES .....................................................................................................................IV 1 INTRODUCTION ................................................................................................................. 1 1.1 PURPOSE ........................................................................................................................................... 1 1.2 BACKGROUND .................................................................................................................................... 1 1.3 SMP OVERVIEW ................................................................................................................................. 2 2 AFSPC VISION....................................................................................................................3 -
Back on Paper Nizes Outstanding Air Force Dining Facili- to Act on Input from Customers
Vol. 46 Number 1 Patrick Air Force Base/Cape Canaveral Air Force Station, Fla. Jan. 9, 2004 INSIDE Launch success Delta II places new GPS satellite into proper orbit Page 3 Life saved Photo by Jim Laviska Frank De La Rosa, 45th Services Squadron, serves Staff Sgt. Institute student, a chili dog. The Riverside Dining Facility was Deshawn Jones, a Defense Equal Opportunity Management named the best dining hall for Air Force Space Command in 2003. Dining Facility wins AFSPC Hennessy Award Two 45th Space Wing airmen’s quick think- “The Hennessy Award is the biggest your-own-pizza bars” and a cyber café, By Marla Holbert ing rescues child one out there for food service,” said Peter he said. Page 8 45TH SERVICES SQUADRON King, food service officer for the Don Smith, Riverside manager, said Patrick’s Riverside Dining Facility has Riverside Dining Facility. “With more one of the facility’s most unique features all the right ingredients for success. The than 280 dining facilities Air Force wide, is “Fit-To-Go,” a satellite operation locat- Father tacks on 270-seat facility situated along the to be able to say that you are (one of) the ed above the Patrick Fitness Center. It is Banana River was recently named the best is a big honor – not just for people the only establishment like it in the Air Air Force Space Command’s Hennessy working in the dining facility but for our Force and has peaked interest from Award winner for 2003. customers, as well.” other bases. The award, sponsored annually by the Mr. -
May Jun07 Departments
panies provided goods and services to the government- run factories. So when the factories closed their doors, the private companies’ customer bases dried up, and they too were forced to close. In the News The U.S. government’s economic effort in Iraq initially focused on reconstruction, with an assumption that Iraq’s private sector would eventually take over the idle gov- AMERICAN FORCES PRESS SERVICE ernment-owned businesses, Brinkley explained. But that (JAN. 5, 2007) never happened. TASK FORCE HELPS REVITALIZE IRAQ’S INDUSTRIES So the Task Force for Improved Business and Stability Donna Miles Operations in Iraq, which was working to improve DoD ASHINGTON—A team of 25 industrial lead- contracting operations in Iraq, shifted its focus in May ers and business analysts is headed to Iraq 2006 to stepping up the process. Wto join 35 others already there working to get almost 200 idle Iraqi factories up and running. “We quickly came to the conclusion that we had a huge, near-idle industrial base that, re-engaged, could put a lot The industrial revitalization initiative is part of a sweep- of people back to work and restore normalcy to a size- ing plan to get Iraqis back to work, restore their liveli- able amount of the population,” Brinkley said. “So we hoods, and jump-start Iraq’s economic base, Paul Brink- immediately embarked on turning that industrial base ley, deputy under secretary of defense for business back on.” transformation, told Pentagon reporters. Initial plans call for opening the first 10 factories quickly, Brinkley said the effort has another equally important with the estimated $5 million in start-up costs to be paid objective: to ensure that Iraqis don’t turn to terrorism by the Iraqi government, he said. -
GPSOC to Encompass Satellite C² Operations Staff Sgt
Congrats, selectees! Schriever’s newest selectees for technical and master sergeant cele- brated their achievements at the Main Fitness Center. See Page 4 VOL. 8, NO. 25 JUNE 22, 2006 Colorado Springs, Colo. www.schriever.af.mil for the base-wide selection list. Watery Welcome First Lt. Michael Adams endures a gauntlet of obsta- cles, water guns and water-bal- loon grenades on his way to the grog bowl during the 50th Network Operations Group's combat dining-in Friday. Lieutenant Adams is a member of the 50th Space Communi- cations Squadron. For story and more photos, see Page 10. photo by Alex Groves GPSOC to encompass satellite C² operations Staff Sgt. Don Branum “I’ll always have a special place in my 50th Space Wing Public Affairs heart for GPS,” Colonel Hamilton said. “Once you work with it, you develop a real The Global Positioning System passion for it because you know how Operations Center will now include the important it is for users in the field.” space operations professionals inside the Other milestones for 2nd SOPS under 2nd Space Operations Squadron’s opera- Colonel Hamilton’s tenure have included tions floor here, the 2nd SOPS commander bringing the GPSOC online 24 hours a day, said at a plaque dedication Tuesday. seven days a week, so people in the field “In my view, GPS Operations is more can call whenever they need support. than a small room—it also includes our In addition, the Legacy Accuracy Im- constellation operations element,” Lt. Col. provement Initiative integrated National photo by Skip Grubelnik Stephen Hamilton said. -
Who Has Attended the AMOS Conference?
Who has attended the AMOS Conference? The following is a sampling of the companies, universities, and government organizations that attended AMOS since its inception in 1999 A program of Maui Economic Development Board, Inc. 14th Air Force Aerospace Policy Solus, LLC Apogee Engineering LLC (AFRL/RDSM) 17th Test Squadron Aerospace Systems, Germany Applied Defense Solution 18th Space Control Squadron Aerospace Technical Alliance Applied Optimization, Inc. 18th Space Surveillance Squadron Aerospace Technical Services Applied Science Innovations, Inc. 1st Command and Control Squadron Aerospace Testing Alliance Applied Technology Associates 1st Space Control Squadron Aerotek Aptima, Inc. 1st Space Operations Squadron AFGSC/A3IT Arecibo Observatory (USRA) 20th Space Control Squadron (20 SPCS) AFLCMC Arete 21 Operations Support Squadron AFLCMC/HBQB ARINC Engineering Services, LLC 21 Space Wing AFLCMC/HBQC Arizona State University 21st Century Systems Inc. (21 CSI) AFMC/AFLCMC Armed Forces General Command 21st Operations Group AFRCO Armor Group LLC 222 Command and Control Squadron AFRL/Assurance Technology Corp Army Research Laboratory 3 SES AFRL/RD Army SMDBL-W/SETA 30th Space Communications Squadron AFRL/RVSW Arnold Engineering Development 3C Systems Company Agency for Defence Development Complex (AEDC) 3rd Space Experimentation Squadron AGI artSCI, LLC 3rd Space Operations Squadron Agilametrics AS&T, Inc. 412th Test Wing, U.S. Air Force Agilation Solutions, LLC ASA Astrosysteme GmbH 46 Test Squadron Agilex ASC/TM 4th Space Operations Squadron -
Altitude Adjustment Reinstated for Fitness Assessment RAIDRS Space
COMMANDER’S CORNER: TAKING CARE OF AIRMEN - PAGE 3 Peterson Air Force Base, Colorado Thursday, February 2, 2012 Vol. 56 No. 5 Altitude adjustment reinstated for fitness assessment By Lea Johnson 21st Space Wing Public Affairs staff writer PETERSON AIR FORCE BASE, Colo. — Acclimating to the altitude in Colorado Springs can take several months, but even after the acclimation period fitness assessment scores can still suffer. Effective Jan. 1, Airmen taking a fitness assessment will have an altitude adjustment added to their run or walk time. “It applies to any of the bases that are over 5,000 feet,” said Senior Master Sgt. Jennifer Brembah, Air Force Space Command’s command functional for food, fitness and lodging. The Air Force Academy’s Human Performance Laboratory initiated a study of the cardio-respiratory performance at sea level versus 7,200 feet, the altitude at the Academy. “Due to atmospheric pressure, there is a significant difference in oxygen content at sea level (26.5 percent) than there is at 7,200 feet (20.9 percent),” said A.L. Wile, director of the Human Performance Laboratory. “The (Colorado Altitude Tent) gives us the capability to simu- late 26.5 percent oxygen content at sea level and test our subjects in both environments.” The test was conducted with 55 non-smoking male and female participants who had lived in Colorado Springs for at least six weeks. The participants each ran 1.5 miles in the CAT, which can simulate both sea level and high- (U.S. Air Force photo/Abner Guzman) See Altitude page 11 The Air Force has reinstated an altitude adjustment for Airmen testing in high-altitude locations. -
26 Airmen Inducted Into SNCO Ranks
COLORADO SPRING S MILITARY NEW S PAPER GROUP Thursday, July 30, 2009 www.csmng.com Vol. 3 No. 30 Base Briefs 26 Airmen inducted into SNCO ranks Concert in the Park July 31 By 50th Space Wing The Peterson Air and Space Museum Public Affairs Foundation will sponsor Concert in the Schriever and Peterson’s newest senior Park 2009 July 31 at Peterson Airpark non-commissioned officers were honored (150 East Ent Avenue). Active duty and in an induction ceremony at the Peterson retired military, DoD civilians and all Consolidated Club here July 24. their family members are welcome. The senior NCO induction ceremony hon- The 2009 Concert in the Park is an ored 21 Schriever Airmen and five Peterson expression of appreciation for members Airmen who have been selected for promotion of the military community who have to master sergeant. made and are still making so many The induction ceremony marked a signifi- sacrifices for their country. cant milestone in the careers of these enlisted The Air Force Academy Stellar Brass Airmen. The promotion to the senior ranks Band will provide musical entertain- demonstrates their ability to assume greater re- ment from 6 to 7:45 p.m. The program sponsibilities while setting a positive example will also include free hot dogs, ham- for Airmen and NCOs under their charge. burgers and bottled water.Bring your Schriever’s newest senior NCO inductees own lawn chairs or blankets. are: For more information on this enter- Master Sgt. James Bates, 50th Space taining and relaxing event, call 556- Communications Squadron U.S. -
Laws Allowing Establishment of AEDC Turn 70 by Bradley Hicks Years Before the Passage of These Laws
PRSRT STD US POSTAGE PAID TULLAHOMA TN Vol. 66, No. 20 Arnold AFB, Tenn. PERMIT NO. 29 October 21, 2019 Team members’ innovative methods advance test operations for AEDC hypersonic propulsion facility By Deidre Ortiz AEDC Public Affairs Improvements by team members of the AEDC Aerodynamics and Propulsion Test Unit (APTU) at Arnold Air Force Base have prevented unscheduled downtime and avoided equipment damage at the facility. Adam Webb, an electrical engineer for the Test Operations and Sustainment (TOS) contractor, National Aerospace Solutions, improved upon software for the rectifiers by enabling it to detect an unsafe condition and restore the rectifier to normal operations, preventing damage to expensive equipment. A rectifier is an electrical device that con- verts alternating current to direct current. The software was successful during a re- cent APTU test, when one of the rectifiers went into an un-commanded runaway. “A runaway is when the output current increases significantly above the set point value,” Webb said. “If left unchecked, it can cause the APTU Facility Control Sys- tem to trip the heated fuel system offline. This results in an unplanned early test ter- mination, possible damage to the Heated Fuel System and a required repeat of the test conditions. A repeat test at APTU can be expensive and could cause additional Electricians Lon Britt, left, and Robert Campbell, right, along with electrical engineer Adam Webb look at a rectifier, like degradation to the test article.” one that was responsible for an un-commanded “runaway” condition, outside the AEDC Aerodynamic and Propulsion Test Unit at Arnold Air Force base. -
U.S. Air Force Honor Guard Visits Team Pete by Tech
TEAM PETE MEMBERS EARN CCAF DEGREES – PAGE 6 Peterson Air Force Base, Colorado Thursday, May 4, 2006 Vol. 50 No. 18 SECDEF announces nomination for commander of AFSPC Secretary of Defense Donald Command Joint Functional Component Rumsfeld announced today that the commander for Space and Global Strike, Recent Assignments president has nominated Lt. Gen. Kevin P. Offutt AFB, Neb. n April 2002 - Aug. 2004, Director of Chilton to the U.S. Senate for appoint- A distinguished graduate of the U.S. Programs, Deputy Chief of Staff for Plans and ment to the grade of general with assign- Air Force Academy class of 1976, the gen- Programs, Headquarters U.S. Air Force, ment as commander, Air Force Space eral flew operational assignments in the Washington, D.C. Command. RF-4C and F-15 and is a graduate of the n Aug. 2004 - Aug. 2005, acting Assistant If confirmed, General Chilton will U.S. Air Force Test Pilot School. Prior to Vice Chief of Staff, Headquarters U.S. Air become the 13th commander of Air assuming his current position, he was act- Force, Washington, D.C. Force Space Command since its creation ing Assistant Vice Chief of Staff, n Aug. 2005 - present, Commander, 8th Air Sept. 1, 1982. Headquarters U.S. Air Force. Force, Barksdale AFB, La., and Joint Functional Component Commander for General Chilton is currently the Lt. Gen. Additional biographical information Kevin Chilton Space and Global Strike, U.S. Strategic 8th Air Force commander at Barksdale is available at www.af.mil/bios . Command, Offutt AFB, Neb. Air Force Base, La., and the U.S.