Chasing and Repoussé
Total Page:16
File Type:pdf, Size:1020Kb
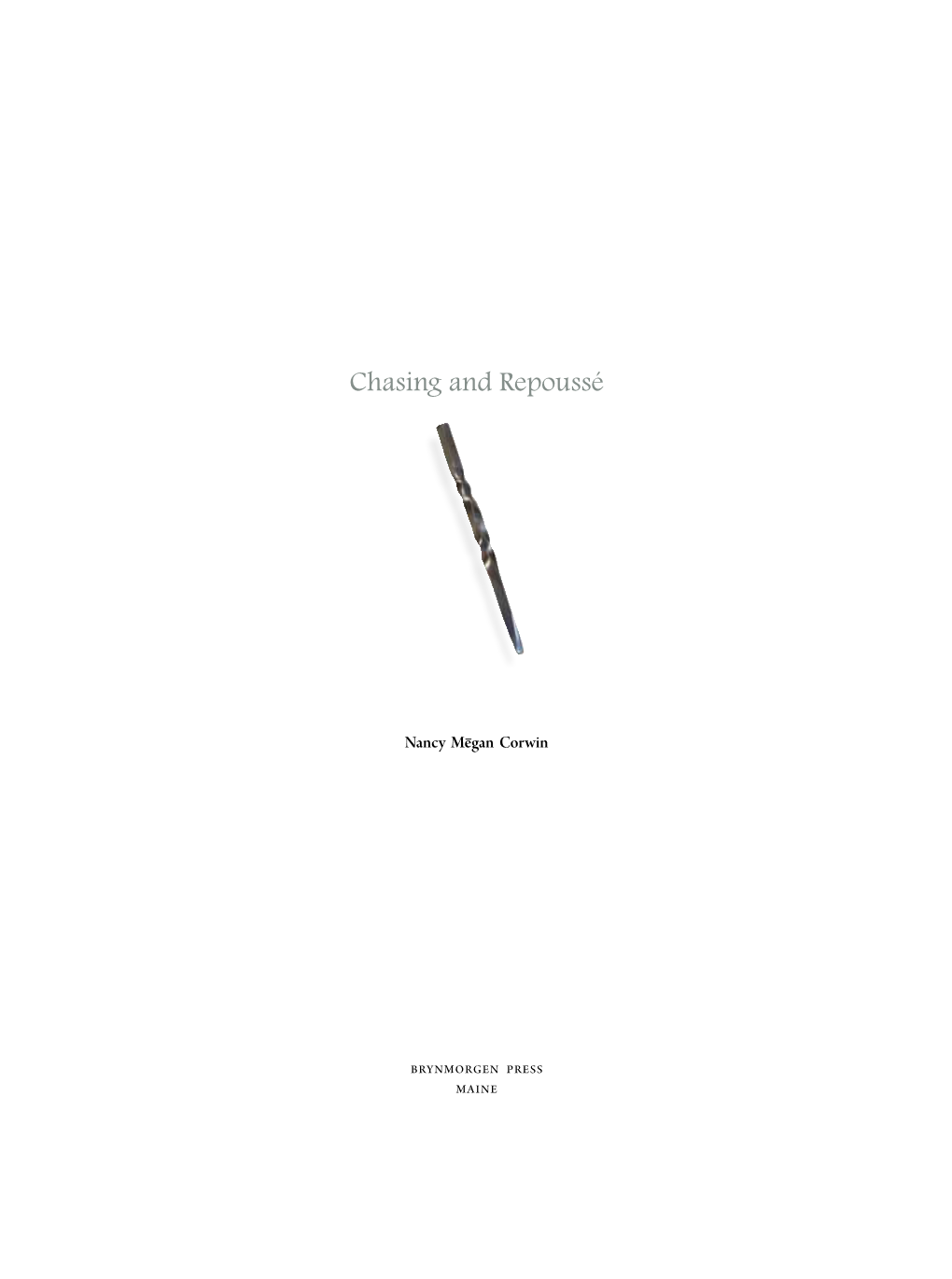
Load more
Recommended publications
-
Treatise on Combined Metalworking Techniques: Forged Elements and Chased Raised Shapes Bonnie Gallagher
Rochester Institute of Technology RIT Scholar Works Theses Thesis/Dissertation Collections 1972 Treatise on combined metalworking techniques: forged elements and chased raised shapes Bonnie Gallagher Follow this and additional works at: http://scholarworks.rit.edu/theses Recommended Citation Gallagher, Bonnie, "Treatise on combined metalworking techniques: forged elements and chased raised shapes" (1972). Thesis. Rochester Institute of Technology. Accessed from This Thesis is brought to you for free and open access by the Thesis/Dissertation Collections at RIT Scholar Works. It has been accepted for inclusion in Theses by an authorized administrator of RIT Scholar Works. For more information, please contact [email protected]. TREATISE ON COMBINED METALWORKING TECHNIQUES i FORGED ELEMENTS AND CHASED RAISED SHAPES TREATISE ON. COMBINED METALWORKING TECHNIQUES t FORGED ELEMENTS AND CHASED RAISED SHAPES BONNIE JEANNE GALLAGHER CANDIDATE FOR THE MASTER OF FINE ARTS IN THE COLLEGE OF FINE AND APPLIED ARTS OF THE ROCHESTER INSTITUTE OF TECHNOLOGY AUGUST ( 1972 ADVISOR: HANS CHRISTENSEN t " ^ <bV DEDICATION FORM MUST GIVE FORTH THE SPIRIT FORM IS THE MANNER IN WHICH THE SPIRIT IS EXPRESSED ELIEL SAARINAN IN MEMORY OF MY FATHER, WHO LONGED FOR HIS CHILDREN TO HAVE THE OPPORTUNITY TO HAVE THE EDUCATION HE NEVER HAD THE FORTUNE TO OBTAIN. vi PREFACE Although the processes of raising, forging, and chasing of metal have been covered in most technical books, to date there is no major source which deals with the functional and aesthetic requirements -
Castingmetal
CASTING METAL Sophistication from the surprisingly simple with a room casting. Hmmmm. I I asked Beth where in the world she BROOM pored through every new and learned how to cast metal using the Bvintage metals technique book Brad Smith offers a Broom business end of a broom. “It’s an old BY HELEN I. DRIGGS on my shelf and I couldn’t find a men- Casting Primer, page 32, hobbyist trick. I learned about it from a tion of the process anywhere. This and a project for using very talented guy named Stu Chalfant the elements you cast. transformed my curiosity into an who gave a demo for my rock group TRYBROOM-CAST IT YOURSELFE urgent and obsessive quest. I am an G — the Culver City [California] Rock & A TURQUOISE PENDANT P information junkie — especially Mineral Club. This was six or seven when it comes to studio jewelry — years ago, and I instantly fell in love and I love finding out new, old fash- with the organic, yet orderly shapes.” ioned ways of doing things. But, I am also efficient. So I A few years passed before Beth tried the technique her- knew the best way to proceed was to seek out Beth self. “The first of our club members to experiment with it Rosengard, who has transformed this delightfully low-tech was Brad 34Smith, who now includes the technique in the approach to molten metal into a sophisticated level of artis- classes he teaches at the Venice Adult School.” After admir- tic expression. I had made a mental note to investigate ing some early silver castings Brad had made, she begged broom casting when I saw her winning earrings in the 2006 him for a sample and later incorporated his work into her Jewelry Arts Awards. -
Repoussé Work for Amateurs
rf Bi oN? ^ ^ iTION av op OCT i 3 f943 2 MAY 8 1933 DEC 3 1938 MAY 6 id i 28 dec j o m? Digitized by the Internet Archive in 2011 with funding from Boston Public Library http://www.archive.org/details/repoussworkforamOOhasl GROUP OF LEAVES. Repousse Work for Amateurs. : REPOUSSE WORK FOR AMATEURS: BEING THE ART OF ORNAMENTING THIN METAL WITH RAISED FIGURES. tfjLd*- 6 By L. L. HASLOPE. ILLUSTRATED. LONDON L. UPCOTT GILL, 170, STRAND, W.C, 1887. PRINTED BY A. BRADLEY, 170, STRAND, LONDON. 3W PREFACE. " JjJjtfN these days, when of making books there is no end," ^*^ and every description of work, whether professional or amateur, has a literature of its own, it is strange that scarcely anything should have been written on the fascinating arts of Chasing and Repousse Work. It is true that a few articles have appeared in various periodicals on the subject, but with scarcely an exception they treated only of Working on Wood, and the directions given were generally crude and imperfect. This is the more surprising when we consider how fashionable Repousse Work has become of late years, both here and in America; indeed, in the latter country, "Do you pound brass ? " is said to be a very common question. I have written the following pages in the hope that they might, in some measure, supply a want, and prove of service to my brother amateurs. It has been hinted to me that some of my chapters are rather "advanced;" in other words, that I have gone farther than amateurs are likely to follow me. -
Hercules Jewelry Project
Hercules Knot Jewelry Series I thoroughly enjoyed my wire wrapping jewelry projects, but in the course of researching and building the class, I was inspired to learn real metalsmithing. I’ve been assembling earrings and necklaces for decades, but suddenly I really wanted to solder, and set gems, and fabricate! Fortunately, my good friend Fjorlief InHaga is a brilliant artisan, and she’s been teaching me and letting me use her studio. THE HERCULES KNOT aka HERAKLES, Reef Knot or Square Knot This motif represents strength and came to be associated with marriage. Brides wore their belts tied this way (see my paper on Roman Weddings). It was a common motif in the Greco-Roman world though the Republic and Early – Mid Empire. 1 2 3 Above, gold bracelet and ring from the 1st century BCE – 2nd CE. Silver mirror, 4th century CE. I imagine this would have been a lovely wedding present. Below: Necklaces dated to the 2nd-3rd century, an armband (#6), and rings from 5rd century BCE to 3rd CE . I have included only a small number of the large quantity of eXtant artifacts. Combined with the variations in assembly technique and clasps, the abundance of pieces shows that the Hercules Knot was a style that was widespread and made by many different artisans. 4 5 6 7 8 9 10 For my first project, I wanted to duplicate the look of these early Imperial necklaces of emerald and gold. For cost purposes, I used brass and glass, which was a commonly-used substitute for stones in period. -
2019 Pricing Grid Numismatic Gold Platinum Palladium Liberty
2019 Pricing of Numismatic Gold, Commemorative Gold, Platinum, and Palladium Products **Does not reflect $5 discount during introductory period Average American Eagle American Eagle American Buffalo American Eagle American Eagle American Liberty Commemorative Gold Commemorative Gold Size Price per Ounce Gold Proof Gold Uncirculated 24K Gold Proof Platinum Proof Palladium Reverse Proof 24K Gold Proof* Uncirculated* $500.00 to $549.99 1 oz $877.50 $840.00 $910.00 $920.00 $937.50 $940.00 1/2 oz $455.00 1/4 oz $240.00 1/10 oz $107.50 $135.00 4-coin set $1,627.50 commemorative gold $240.00 $230.00 commemorative 3-coin set $305.50 $550.00 to $599.99 1 oz $927.50 $890.00 $960.00 $970.00 $987.50 $990.00 1/2 oz $480.00 1/4 oz $252.50 1/10 oz $112.50 $140.00 4-coin set $1,720.00 commemorative gold $252.25 $242.25 commemorative 3-coin set $317.75 $600.00 to $649.99 1 oz $977.50 $940.00 $1,010.00 $1,020.00 $1,037.50 $1,040.00 1/2 oz $505.00 1/4 oz $265.00 1/10 oz $117.50 $145.00 4-coin set $1,812.50 commemorative gold $264.50 $254.50 commemorative 3-coin set $330.00 $650.00 to $699.99 1 oz $1,027.50 $990.00 $1,060.00 $1,070.00 $1,087.50 $1,090.00 1/2 oz $530.00 1/4 oz $277.50 1/10 oz $122.50 $150.00 4-coin set $1,905.00 commemorative gold $276.75 $266.75 commemorative 3-coin set $342.25 $700.00 to $749.99 1 oz $1,077.50 $1,040.00 $1,110.00 $1,120.00 $1,137.50 $1,140.00 1/2 oz $555.00 1/4 oz $290.00 1/10 oz $127.50 $155.00 4-coin set $1,997.50 commemorative gold $289.00 $279.00 commemorative 3-coin set $354.50 $750.00 to $799.99 1 oz $1,127.50 $1,090.00 -
The Use of Titanium in Dentistry
Cells and Materials Volume 5 Number 2 Article 9 1995 The Use of Titanium in Dentistry Toru Okabe Baylor College of Dentistry, Dallas Hakon Hero Scandinavian Institute of Dental Materials, Haslum Follow this and additional works at: https://digitalcommons.usu.edu/cellsandmaterials Part of the Dentistry Commons Recommended Citation Okabe, Toru and Hero, Hakon (1995) "The Use of Titanium in Dentistry," Cells and Materials: Vol. 5 : No. 2 , Article 9. Available at: https://digitalcommons.usu.edu/cellsandmaterials/vol5/iss2/9 This Article is brought to you for free and open access by the Western Dairy Center at DigitalCommons@USU. It has been accepted for inclusion in Cells and Materials by an authorized administrator of DigitalCommons@USU. For more information, please contact [email protected]. Cells and Materials, Vol. 5, No. 2, 1995 (Pages 211-230) 1051-6794/95$5 0 00 + 0 25 Scanning Microscopy International, Chicago (AMF O'Hare), IL 60666 USA THE USE OF TITANIUM IN DENTISTRY Toru Okabe• and HAkon Hem1 Baylor College of Dentistry, Dallas, TX, USA 1Scandinavian Institute of Dental Materials (NIOM), Haslum, Norway (Received for publication August 8, 1994 and in revised form September 6, 1995) Abstract Introduction The aerospace, energy, and chemical industries have Compared to the metals and alloys commonly used benefitted from favorable applications of titanium and for many years for various industrial applications, tita titanium alloys since the 1950's. Only about 15 years nium is a rather "new" metal. Before the success of the ago, researchers began investigating titanium as a mate Kroll process in 1938, no commercially feasible way to rial with the potential for various uses in the dental field, produce pure titanium had been found. -
THE DEGRADATION of PEWTER in ANTIQUE LACE BOBBINS Home Page
THE DEGRADATION OF PEWTER IN ANTIQUE LACE BOBBINS Home Page Parent Page THE DEGRADATION OF PEWTER IN ANTIQUE LACE BOBBINS. This article needs a couple of pics. Pewter Degradation Introduction The pewter used in bobbins is one of the prettiest decorative processes that makers used. Unfortunately during the passage of time much of the pewter by some makers has degraded and has either fallen off the bobbin or has become swollen, misshapen and even crumbly. The following is my attempt, with the help of many people on the web and especially my friend Neil Keats, to explain this phenomenon. Pewter. Pewter is an alloy (i.e. a mixture) of tin and lead. The better the quality of pewter the higher the percentage of tin is in the alloy. Tin exists in three forms, depending on the temperature. This is called polymorphism (poly-many, morphism-shapes). At temperatures between 13 and 160 degrees C, it is called White tin, and the atoms (think of them as little balls in this description) are packed closely together to form the metal. Hence, it is a dense metal, i.e. it is hard. file:///C|/Documents%20and%20Settings/My%20Docu...s/Pewter%20degredation/Pewter%20degredation.htm (1 of 4) [6/9/2003 8:15:25 PM] THE DEGRADATION OF PEWTER IN ANTIQUE LACE BOBBINS Below 13 degrees C the atoms rearrange to become more loosely packed (actually in the same configuration as diamond). This shows first as wart-like structures on the surface, and eventually leads to the tin crumbling into a powder. This is called "tin pest", and is what happened to the buttons on Napoleon's soldiers coats. -
Rene Lalique Shaun Leane
In your written exam you will have to compare and contrast the work of two designers. Remember the following sentence it will help you remember the similarities and differences in the designer’s work that you should discuss. “St Paul’s Pupils’ Can Make Tasty Sausage Sandwiches On Toast!!!” Rene Lalique THE Shaun Leane b.1860 – 1945 DESIGNERS Began working in 1980’s to France present day – London, UK Lalique was an important figure in ‘This is my signature; something the “Art nouveau” movement. that’s refined, delicate, but This movement was inspired by powerful.’ natural, organic forms, like Organic forms are one of Leane’s flowers and plants; favourite inspirations. He Lalique’s work consisted of soft, describes nature as beautiful and flowing curved lines. fragile yet there are hidden He also liked to use female figures elements of strength and and faces in his work; danger. He like to create balance Feminine, detailed, realistic. in his pieces Many of Lalique’s design were Soft flowing lines paired with symmetrical. sharp points S for SHAPE Dragonfly woman corsage ornament, 1898. Gold, enamel, moonstones, and diamonds Tahitian pearl and pheasant claw earrings by for McQueen, 2001 Detailed, feminine, Art Nouveau P Statement jewellery, wearable art, Statement jewellery. for Detailed. Avant Garde (meaning PRODUCT experimental & innovative) Very detailed, fairly large, heavy Larger fashion pieces which were pieces so not very easy to wear. P commissioned by McQueen were for made from lightweight materials PRACTICALITY which made them easy to wear down the runway. Not for everyday wear, were designed to complement and add extra drama to fashion pieces. -
Testing Gold Platinum Silver.Qxp
PROCEDURES FOR TESTING GOLD, PLATINUM AND SILVER To test for the karat value of gold, platinum and silver, you will need the following materials and tools: • Black acid testing stone that is washed thoroughly with water prior to each test. • Acids. • Gold testing needles with gold tips - used for comparison with test pieces. Testing for 10K, 12K, 14K Scratch the gold piece to be tested on the stone. Next to this position, scratch the appropriate needle (10, 12 or 14K). Place a drop of the appropriate acid on the stone where the gold was rubbed off. If the gold is the same karat or higher, the color of the scratch mark for the gold piece will appear the same as the mark from the needle. If that gold piece is a lower karat, the scratched deposit will become fainter and eventually disappear. Testing for 18K Scratch the test piece on the stone and apply 18K acid. Any gold that is less than 18K will disappear in less than 30 seconds. Gold that remains on the stone is 18K or higher. Testing for 20K and 24K Scratch the gold piece on the stone. Next, scratch any item of know karat (coin or needle) on the stone. Apply one drop of acid to area. The material that starts to disappear has the lower karat. Testing for Platinum Scratch the test item on the stone and apply one drop of acid to the application on the stone. If the material is platinum, it should keep its white, bright color. White Gold The same procedure for platinum can be used for 18K white gold. -
Titanium Alloy Data Sheet
M Titanium Alloy Data Sheet Description Titanium equipment is often used in severe corrosive environments encountered in the chemical processing industries. Titanium has been considered an exotic “wonder metal” by many. This was particularly true in reference to castings. However, increasing demands and rapidly advancing technology have permitted titanium castings to be commercially available at an economical cost. The combination of its cost, strength, corrosion resistance, and service life in very demanding corrosive environments suggest its selection in applications where titanium castings have never been considered in the past. Specifications Flowserve’s commercially pure titanium (C.P.-Ti) castings conform to ASTM Specification B367, Grade C-3. Flowserve’s palladium stabilized titanium (Ti-Pd) castings conform to Grade Ti-Pd 8A. Composition C.P.-Ti (C-3) Ti-Pd (8A) Element Percent Percent Nitrogen 0.05 max. 0.05 max. Carbon 0.10 max. 0.10 max. Hydrogen 0.015 max. 0.015 max. Iron 0.25 max. 0.25 max. Oxygen 0.40 max. 0.40 max. Titanium Remainder Remainder Palladium –– 0.12 min. Minimum C.P.-Ti (C-3) & Mechanical Ti-Pd (8A) and Physical Tensile Strength, psi 65,000 Properties MPa 448 Yield Strength, psi 55,000 MPa 379 Elongation, % in 1" (25 mm), min. 12 Brinell Hardness, 3000 kg, max. 235 Modulus of Elasticity, psi 15.5 x 106 MPa 107,000 Coefficient of Expansion, in/in/°F@ 68-800°F 5.5 x 10-6 m/m/°C @ 20-427°C 9.9 x 10-6 Thermal Conductivity, Btu/hr/ft/ft2/°F @ 400° 9.8 WATTS/METER-KELVIN @ 204°C 17 Density lb/cu in 0.136 kg/m3 3760 Melting Point, °F (approx.) 3035 °C 1668 Titanium Alloy Data Sheet (continued) Corrosion The outstanding mechanical and physical properties of titanium, combined with its Resistance unexpected corrosion resistance in many environments, makes it an excellent choice for particularly aggressive environments like wet chlorine, chlorine dioxide, sodium and calcium hypochlorite, chlorinated brines, chloride salt solutions, nitric acid, chromic acid, and hydrobromic acid. -
The Platinum/Palladium Process
9 The Platinum/Palladium Process OVERVIEW AND EXPECTATIONS In the majority of the classes and workshops that I’ve taught over the years, “the platinum/palladium process” is the answer that surfaces first when I ask the question, “What process do you want to learn the most?” In this chapter you will learn how, and, as in previous chapters, I begin with a little history. Then you will learn the chemistry and sequence of the various stages to a finished print. This chapter gives you alternatives to traditional platinum/palladium chemistry and provides you with a simple sensitizer “drop chart” that is based on the type of negative you are working with, rather than the print you would like to make. I also provide the beginnings of a trouble-shooting list to assist in hunting down problems that may be showing up in your work. Finally, you’ll get some brief alternative ideas for combining platinum/palladium with other techniques such as Van Dyke and gum bichromate. A LITTLE HISTORY Like most refined non-silver and alternative photographic processes, the art of platinum/palladium printing was developed in pieces over time by a number of dedicated artists and scientists. In 1830, Ferdinand Gehlen recorded the action and effects of light on platinum chloride, noting that UV light would alter the color of platinum salts and cause the ferric salts to precipitate out into a ferrous state. At around the same time, Johann Wolfgang Dobereiner (1780–1849) observed the decomposition of ferric oxalate on exposure to UV light and scientifically defined its sensitivity. -
Fully-Integ Supplier O
Fully-integrated Supplier of Titanium Now safely and effectively etch/prepare titanium For Aerospace for anodizing without using Hydrofluoric Acid! In use since 1993, join the growing number of Applications medical, dental and jewelry users who’ve made the switch to a more environmentally sound process. AIRFRAME • ENGINES • LANDING GEAR Developed as a safe alternative to the dangers of Bar • Billet • Sheet • Plate • Ingot • Forgings • Wire • Seamless Tube Hydrofluoric acid, Multi Etch, with its pH of 6.8, has quickly become the favored safer etch to: ISO 9001 and AS9100 certified US, UK, Germany and China sales and distribution locations. •Remove surface oxides & contaminants on titanium Inventory in stock and available today. which cause dull colors and block the full color range VSMPO-AVISMA is the World’s Largest Producer of Titanium. •Erase anodizing mistakes on titanium & niobium Holding more than 300 international quality certifications and customer approvals, VSMPO-Tirus operations provide sales, distribution and service center processing of VSMPO-AVISMA titanium mill products to the aerospace, military, •Prepare platinum for soldering/welding consumer and medical markets. VSMPO has approvals at all major airframe and engine OEMs and produces titanium for every major commercial aerospace program in production today. •Enhance patterns on mokume and meteorite Anodized titanium treated with Multi Etch (top) and untreated (bottom) PO Box 890, Clarkdale, AZ 86324 [email protected], www.reactivemetals.com 928-634-3434 • 928-634-6734 fx [email protected] Fully-integrated Fully-integrated SupplierSupplier ofof TitaniumTitanium For For Aerospace Aerospace Applications Applications AIRFRAMEAIRFRAME • • ENGINES ENGINES •• LANDINGLANDING GEARGEAR BarBar • Billet • Billet • Sheet • Sheet • Plate• Plate • Ingot• Ingot • •Forgings Forgings •• WireWire • Seamless TubeTube ISO ISO9001 9001 and and AS9100 AS9100 certified certified US, US,UK, UK, Germany Germany and and China China sales sales and and distribution distribution locations.