Hypersonic Speed Through Scramjet Technology
Total Page:16
File Type:pdf, Size:1020Kb
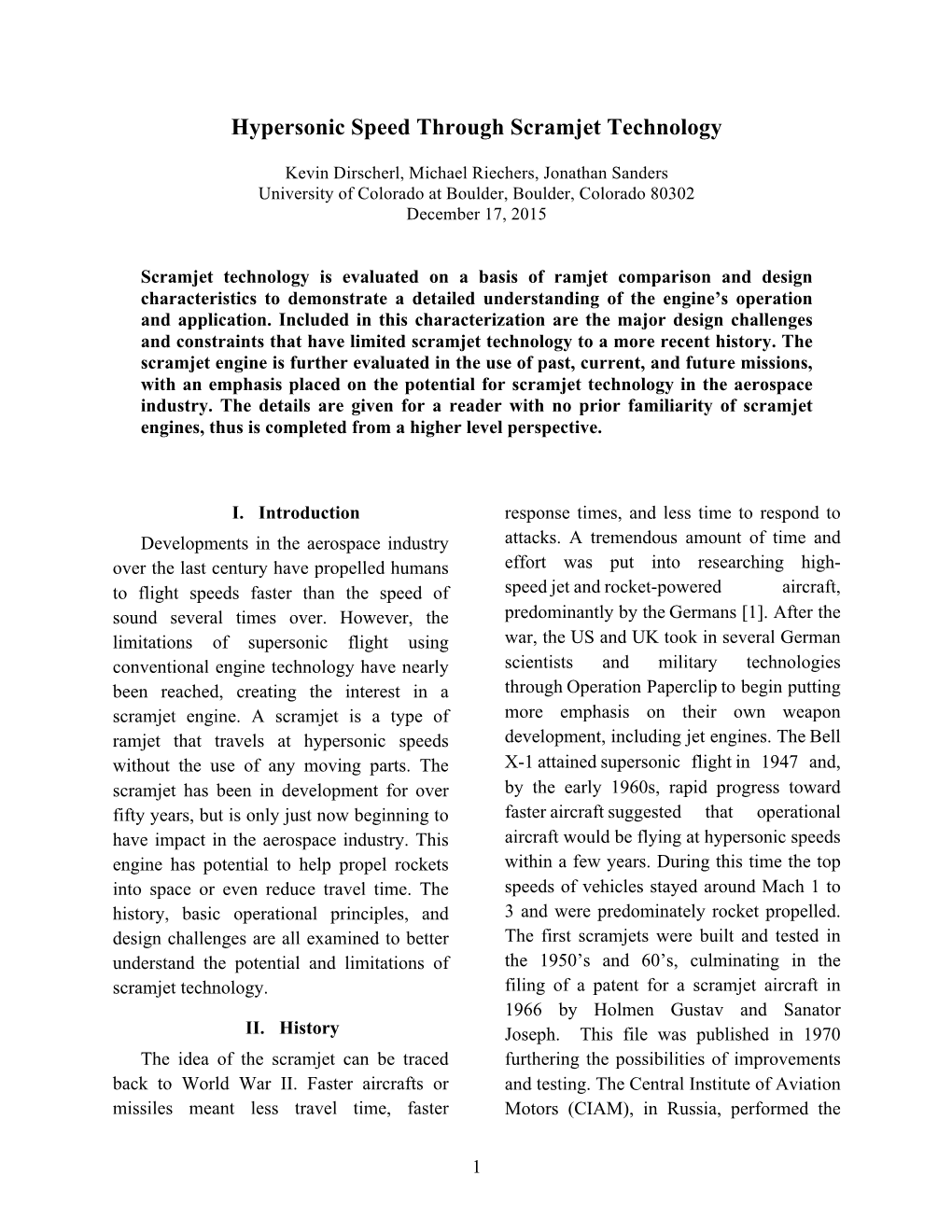
Load more
Recommended publications
-
Module 1: Hypersonic Atmosphere Lecture1: Characteristics of Hypersonic Atmosphere
NPTEL –Aerospace Module 1: Hypersonic Atmosphere Lecture1: Characteristics of Hypersonic Atmosphere 1.1 Introduction Hypersonic flight has special traits, some of which are seen in every hypersonic flight. Presence of these particular features during a flight is highly dependant on type of trajectory, configuration etc. In short it is the mission requirement which decides the nature of hypersonic atmosphere encountered by the flight vehicle. Some missions are designed for high deceleration in outer atmosphere during reentry. Hence, those flight vehicles experience longer flight duration at high angle of attacks due to which blunt nosed configuration are generally preferred for such aircrafts. On the contrary, some missions are centered on low flight duration with major deceleration closer to earth surface hence these vehicles have sharp nose and low angle of attack flights. Reentry flight path of hypersonic vehicle is thus governed by the parameters called as ballistic parameter and lifting parameter. These parameters are obtained by applying momentum conservation equation in the direction of the flight path and normal to it. Velocity-altitude map of the flight is thus made from the knowledge of these governing flight parameters, weight and surface area. Ballistic parameter is considered for non lifting reentry flights like flight path of Apollo capsule, however lifting parameter is considered for lifting reentry trajectories like that of space shuttle. Therefore hypersonic flight vehicles are classified in four different types based on the design constraints imposed from mission specifications. 1. Reentry Vehicles (RV): These vehicles are typically launched using rocket propulsion system. Reentry of these vehicles is controlled by control surfaces. -
Maintenance Strategy and Its Importance in Rocket Launching System-An Indian Prospective
ISSN(Online) : 2319-8753 ISSN (Print) : 2347-6710 International Journal of Innovative Research in Science, Engineering and Technology (An ISO 3297: 2007 Certified Organization) Vol. 5, Issue 5, May 2016 Maintenance Strategy and its Importance in Rocket Launching System-An Indian Prospective N Gayathri1, Amit Suhane2 M. Tech Research Scholar, Mechanical Engineering, M.A.N.I.T, Bhopal, M.P. India Assistant Professor, Mechanical Engineering, M.A.N.I.T, Bhopal, M.P. India ABSTRACT: The present paper mainly describes the maintenance strategies followed at rocket launching system in India. A Launch pad is an above-ground platform from which a rocket or space vehicle is vertically launched. The potential for advanced rocket launch vehicles to meet the challenging , operational, and performance demands of space transportation in the early 21st century is examined. Space transportation requirements from recent studies underscoring the need for growth in capacity of an increasing diversity of space activities and the need for significant reductions in operational are reviewed. Maintenance strategies concepts based on moderate levels of evolutionary advanced technology are described. The vehicles provide a broad range of attractive concept alternatives with the potential to meet demanding operational and maintenance goals and the flexibility to satisfy a variety of vehicle architecture, mission, vehicle concept, and technology options. KEY WORDS: Preventive Maintenance, Rocket Launch Pad. I. INTRODUCTION A. ROCKET LAUNCH PAD A Launch pad is associate degree above-ground platform from that a rocket ballistic capsule is vertically launched. A launch advanced may be a facility which incorporates, and provides needed support for, one or a lot of launch pads. -
Different Types of Rocket Nozzles
Different Types of Rocket Nozzles 5322- Rocket Propulsion Project Report By Patel Harinkumar Rajendrabhai(1001150586) 1. Introduction 1.1 What is Nozzle and why they are used? A nozzle is a device designed to control the direction or characteristics of a fluid flow (especially to increase velocity) as it exits (or enters) an enclosed chamber or Pipe[9]. Nozzles are frequently used to control the rate of flow, speed, direction, mass, shape, and/or the pressure of the stream that emerges from them. In nozzle velocity of fluid increases on the expense of its pressure energy. A Water Nozzle[9] Rotator Style Pivot Sprinkler[9] 1.2 What is Rocket Nozzle? A rocket engine nozzle is a propelling nozzle (usually of the de Laval type) used in a rocket engine to expand and accelerate the hot gases from combustion so as to produce thrust according to Newton’s law of motion. Combustion gases are produced by burning the propellants in combustor, they exit the nozzle at very high Speed (hypersonic). 1.3 Properties of Rocket Nozzle Nozzle produces thrust. Exhaust gases from combustion are pushed into throat region of nozzle. Throat is smaller cross-sectional area than rest of engine, gases are compressed to high pressure. Nozzle gradually increases in cross-sectional area allowing gases to expand and push against walls creating thrust. Convert thermal energy of hot chamber gases into kinetic energy and direct that energy along nozzle axis.[1] Mathematically, ultimate purpose of nozzle is to expand gases as efficiently as possible so as to maximize exit velocity.[1] Rocket Engine[1] F m eVe Pe Pa Ae Neglecting Pressure losses F m eVe 2 Different types of Rocket Nozzle Configuration(shape) The rocket nozzles can have many shapes configurations. -
Notes on Earth Atmospheric Entry for Mars Sample Return Missions
NASA/TP–2006-213486 Notes on Earth Atmospheric Entry for Mars Sample Return Missions Thomas Rivell Ames Research Center, Moffett Field, California September 2006 The NASA STI Program Office . in Profile Since its founding, NASA has been dedicated to the • CONFERENCE PUBLICATION. Collected advancement of aeronautics and space science. The papers from scientific and technical confer- NASA Scientific and Technical Information (STI) ences, symposia, seminars, or other meetings Program Office plays a key part in helping NASA sponsored or cosponsored by NASA. maintain this important role. • SPECIAL PUBLICATION. Scientific, technical, The NASA STI Program Office is operated by or historical information from NASA programs, Langley Research Center, the Lead Center for projects, and missions, often concerned with NASA’s scientific and technical information. The subjects having substantial public interest. NASA STI Program Office provides access to the NASA STI Database, the largest collection of • TECHNICAL TRANSLATION. English- aeronautical and space science STI in the world. language translations of foreign scientific and The Program Office is also NASA’s institutional technical material pertinent to NASA’s mission. mechanism for disseminating the results of its research and development activities. These results Specialized services that complement the STI are published by NASA in the NASA STI Report Program Office’s diverse offerings include creating Series, which includes the following report types: custom thesauri, building customized databases, organizing and publishing research results . even • TECHNICAL PUBLICATION. Reports of providing videos. completed research or a major significant phase of research that present the results of NASA For more information about the NASA STI programs and include extensive data or theoreti- Program Office, see the following: cal analysis. -
Performances of a Small Hypersonic Airplane (Hyplane)
Politecnico di Torino Porto Institutional Repository [Proceeding] PERFORMANCES OF A SMALL HYPERSONIC AIRPLANE (HYPLANE) Original Citation: Savino R.; Russo G.; D’Oriano V.; Visone M.; Battipede M.; Gili P. (2014). PERFORMANCES OF A SMALL HYPERSONIC AIRPLANE (HYPLANE). In: 65th International Astronautical Congress„ Toronto, Canada, 29 September - 3 October 2014. pp. 1-13 Availability: This version is available at : http://porto.polito.it/2591763/ since: February 2015 Publisher: International Astronautical Federation (IAF) Terms of use: This article is made available under terms and conditions applicable to Open Access Policy Article ("Public - All rights reserved") , as described at http://porto.polito.it/terms_and_conditions. html Porto, the institutional repository of the Politecnico di Torino, is provided by the University Library and the IT-Services. The aim is to enable open access to all the world. Please share with us how this access benefits you. Your story matters. (Article begins on next page) 65th International Astronautical Congress, Toronto, Canada. Copyright ©2014 by the Authors. Published by the IAF, with permission and released to the IAF to publish in all forms. IAC-14-D2.4 PERFORMANCES OF A SMALL HYPERSONIC AIRPLANE (HYPLANE) Raffaele Savino Department of Industrial Engineering, University of Naples “Federico II”, Italy Gennaro Russo Trans-Tech srl and Space Renaissance Italia, Italy Vera D’Oriano*, Michele Visone Blue Engineering, Italy Manuela Battipede, Piero Gili Department of Mechanical and Aerospace Engineering, Polytechnic of Turin, Italy In the present work a preliminary performance study regarding a small hypersonic airplane named HyPlane is presented. It is designed for long duration sub-orbital space tourism missions, in the frame of the Space Renaissance (SR) Italia Space Tourism Program. -
SPEAKERS TRANSPORTATION CONFERENCE FAA COMMERCIAL SPACE 15TH ANNUAL John R
15TH ANNUAL FAA COMMERCIAL SPACE TRANSPORTATION CONFERENCE SPEAKERS COMMERCIAL SPACE TRANSPORTATION http://www.faa.gov/go/ast 15-16 FEBRUARY 2012 HQ-12-0163.INDD John R. Allen Christine Anderson Dr. John R. Allen serves as the Program Executive for Crew Health Christine Anderson is the Executive Director of the New Mexico and Safety at NASA Headquarters, Washington DC, where he Spaceport Authority. She is responsible for the development oversees the space medicine activities conducted at the Johnson and operation of the first purpose-built commercial spaceport-- Space Center, Houston, Texas. Dr. Allen received a B.A. in Speech Spaceport America. She is a recently retired Air Force civilian Communication from the University of Maryland (1975), a M.A. with 30 years service. She was a member of the Senior Executive in Audiology/Speech Pathology from The Catholic University Service, the civilian equivalent of the military rank of General of America (1977), and a Ph.D. in Audiology and Bioacoustics officer. Anderson was the founding Director of the Space from Baylor College of Medicine (1996). Upon completion of Vehicles Directorate at the Air Force Research Laboratory, Kirtland his Master’s degree, he worked for the Easter Seals Treatment Air Force Base, New Mexico. She also served as the Director Center in Rockville, Maryland as an audiologist and speech- of the Space Technology Directorate at the Air Force Phillips language pathologist and received certification in both areas. Laboratory at Kirtland, and as the Director of the Military Satellite He joined the US Air Force in 1980, serving as Chief, Audiology Communications Joint Program Office at the Air Force Space at Andrews AFB, Maryland, and at the Wiesbaden Medical and Missile Systems Center in Los Angeles where she directed Center, Germany, and as Chief, Otolaryngology Services at the the development, acquisition and execution of a $50 billion Aeromedical Consultation Service, Brooks AFB, Texas, where portfolio. -
Brazilian 14-Xs Hypersonic Unpowered Scramjet Aerospace Vehicle
ISSN 2176-5480 22nd International Congress of Mechanical Engineering (COBEM 2013) November 3-7, 2013, Ribeirão Preto, SP, Brazil Copyright © 2013 by ABCM BRAZILIAN 14-X S HYPERSONIC UNPOWERED SCRAMJET AEROSPACE VEHICLE STRUCTURAL ANALYSIS AT MACH NUMBER 7 Álvaro Francisco Santos Pivetta Universidade do Vale do Paraíba/UNIVAP, Campus Urbanova Av. Shishima Hifumi, no 2911 Urbanova CEP. 12244-000 São José dos Campos, SP - Brasil [email protected] David Romanelli Pinto ETEP Faculdades, Av. Barão do Rio Branco, no 882 Jardim Esplanada CEP. 12.242-800 São José dos Campos, SP, Brasil [email protected] Giannino Ponchio Camillo Instituto de Estudos Avançados/IEAv - Trevo Coronel Aviador José Alberto Albano do Amarante, nº1 Putim CEP. 12.228-001 São José dos Campos, SP - Brasil. [email protected] Felipe Jean da Costa Instituto Tecnológico de Aeronáutica/ITA - Praça Marechal Eduardo Gomes, nº 50 Vila das Acácias CEP. 12.228-900 São José dos Campos, SP - Brasil [email protected] Paulo Gilberto de Paula Toro Instituto de Estudos Avançados/IEAv - Trevo Coronel Aviador José Alberto Albano do Amarante, nº1 Putim CEP. 12.228-001 São José dos Campos, SP - Brasil. [email protected] Abstract. The Brazilian VHA 14-X S is a technological demonstrator of a hypersonic airbreathing propulsion system based on supersonic combustion (scramjet) to fly at Earth’s atmosphere at 30km altitude at Mach number 7, designed at the Prof. Henry T. Nagamatsu Laboratory of Aerothermodynamics and Hypersonics, at the Institute for Advanced Studies. Basically, scramjet is a fully integrated airbreathing aeronautical engine that uses the oblique/conical shock waves generated during the hypersonic flight, to promote compression and deceleration of freestream atmospheric air at the inlet of the scramjet. -
Rocket Nozzles: 75 Years of Research and Development
Sådhanå Ó (2021) 46:76 Indian Academy of Sciences https://doi.org/10.1007/s12046-021-01584-6Sadhana(0123456789().,-volV)FT3](0123456789().,-volV) Rocket nozzles: 75 years of research and development SHIVANG KHARE1 and UJJWAL K SAHA2,* 1 Department of Energy and Process Engineering, Norwegian University of Science and Technology, 7491 Trondheim, Norway 2 Department of Mechanical Engineering, Indian Institute of Technology Guwahati, Guwahati 781039, India e-mail: [email protected]; [email protected] MS received 28 August 2020; revised 20 December 2020; accepted 28 January 2021 Abstract. The nozzle forms a large segment of the rocket engine structure, and as a whole, the performance of a rocket largely depends upon its aerodynamic design. The principal parameters in this context are the shape of the nozzle contour and the nozzle area expansion ratio. A careful shaping of the nozzle contour can lead to a high gain in its performance. As a consequence of intensive research, the design and the shape of rocket nozzles have undergone a series of development over the last several decades. The notable among them are conical, bell, plug, expansion-deflection and dual bell nozzles, besides the recently developed multi nozzle grid. However, to the best of authors’ knowledge, no article has reviewed the entire group of nozzles in a systematic and comprehensive manner. This paper aims to review and bring all such development in one single frame. The article mainly focuses on the aerodynamic aspects of all the rocket nozzles developed till date and summarizes the major findings covering their design, development, utilization, benefits and limitations. -
The SKYLON Spaceplane
The SKYLON Spaceplane Borg K.⇤ and Matula E.⇤ University of Colorado, Boulder, CO, 80309, USA This report outlines the major technical aspects of the SKYLON spaceplane as a final project for the ASEN 5053 class. The SKYLON spaceplane is designed as a single stage to orbit vehicle capable of lifting 15 mT to LEO from a 5.5 km runway and returning to land at the same location. It is powered by a unique engine design that combines an air- breathing and rocket mode into a single engine. This is achieved through the use of a novel lightweight heat exchanger that has been demonstrated on a reduced scale. The program has received funding from the UK government and ESA to build a full scale prototype of the engine as it’s next step. The project is technically feasible but will need to overcome some manufacturing issues and high start-up costs. This report is not intended for publication or commercial use. Nomenclature SSTO Single Stage To Orbit REL Reaction Engines Ltd UK United Kingdom LEO Low Earth Orbit SABRE Synergetic Air-Breathing Rocket Engine SOMA SKYLON Orbital Maneuvering Assembly HOTOL Horizontal Take-O↵and Landing NASP National Aerospace Program GT OW Gross Take-O↵Weight MECO Main Engine Cut-O↵ LACE Liquid Air Cooled Engine RCS Reaction Control System MLI Multi-Layer Insulation mT Tonne I. Introduction The SKYLON spaceplane is a single stage to orbit concept vehicle being developed by Reaction Engines Ltd in the United Kingdom. It is designed to take o↵and land on a runway delivering 15 mT of payload into LEO, in the current D-1 configuration. -
Nasa X-15 Program
5 24,132 6 9 NASA X-15 PROGRAM By: T.D. Barnes - NASA Contractor - 1960s NASA contractors for the X-15 program were Bendix Field Engineering followed by Unitec, Inc. The NASA High Range Tracking stations were located at Ely and Beatty Nevada with main control being at Dryden/Edwards AFB in California. Personnel at the tracking stations consisted of a Station Manager, a Technical Advisor, and field engineers for the Mod-2 Radar, Data Transmission System, Communications, Telemetry, and Plant Maintenance/Generators. NASA had a site monitor at each tracking station to monitor our contractor operations. Though supporting flights of the X-15 was their main objective, they also participated in flights of the XB-70, the three Lifting Bodies, experimental Lunar Landing vehicles, and an occasional A-12/YF-12/SR-71 Blackbird flight. On mission days a NASA van picked up each member of the crew at their residence for the 4:20 a.m. trip to the tracking station 18 miles North of Beatty on the Tonopah Highway. Upon arrival each performed preflight calibrations and setup of their various systems. The liftoff of the B-52, with the X-15 tucked beneath its wing, seldom occurred after 9:00 a.m. due to the heat effect of the Mojave Desert making it difficult for the planes to acquire altitude. At approximately 0800 hours two pilots from Dryden would proceed uprange to evaluate the condition of the dry lake beds in the event of an emergency landing of the X-15 (always buzzing our station on the way up and back). -
No Acoustical Change” for Propeller-Driven Small Airplanes and Commuter Category Airplanes
4/15/03 AC 36-4C Appendix 4 Appendix 4 EQUIVALENT PROCEDURES AND DEMONSTRATING "NO ACOUSTICAL CHANGE” FOR PROPELLER-DRIVEN SMALL AIRPLANES AND COMMUTER CATEGORY AIRPLANES 1. Equivalent Procedures Equivalent Procedures, as referred to in this AC, are aircraft measurement, flight test, analytical or evaluation methods that differ from the methods specified in the text of part 36 Appendices A and B, but yield essentially the same noise levels. Equivalent procedures must be approved by the FAA. Equivalent procedures provide some flexibility for the applicant in conducting noise certification, and may be approved for the convenience of an applicant in conducting measurements that are not strictly in accordance with the 14 CFR part 36 procedures, or when a departure from the specifics of part 36 is necessitated by field conditions. The FAA’s Office of Environment and Energy (AEE) must approve all new equivalent procedures. Subsequent use of previously approved equivalent procedures such as flight intercept typically do not need FAA approval. 2. Acoustical Changes An acoustical change in the type design of an airplane is defined in 14 CFR section 21.93(b) as any voluntary change in the type design of an airplane which may increase its noise level; note that a change in design that decreases its noise level is not an acoustical change in terms of the rule. This definition in section 21.93(b) differs from an earlier definition that applied to propeller-driven small airplanes certificated under 14 CFR part 36 Appendix F. In the earlier definition, acoustical changes were restricted to (i) any change or removal of a muffler or other component of an exhaust system designed for noise control, or (ii) any change to an engine or propeller installation which would increase maximum continuous power or propeller tip speed. -
Chapter 5 Dimensional Analysis and Similarity
Chapter 5 Dimensional Analysis and Similarity Motivation. In this chapter we discuss the planning, presentation, and interpretation of experimental data. We shall try to convince you that such data are best presented in dimensionless form. Experiments which might result in tables of output, or even mul- tiple volumes of tables, might be reduced to a single set of curves—or even a single curve—when suitably nondimensionalized. The technique for doing this is dimensional analysis. Chapter 3 presented gross control-volume balances of mass, momentum, and en- ergy which led to estimates of global parameters: mass flow, force, torque, total heat transfer. Chapter 4 presented infinitesimal balances which led to the basic partial dif- ferential equations of fluid flow and some particular solutions. These two chapters cov- ered analytical techniques, which are limited to fairly simple geometries and well- defined boundary conditions. Probably one-third of fluid-flow problems can be attacked in this analytical or theoretical manner. The other two-thirds of all fluid problems are too complex, both geometrically and physically, to be solved analytically. They must be tested by experiment. Their behav- ior is reported as experimental data. Such data are much more useful if they are ex- pressed in compact, economic form. Graphs are especially useful, since tabulated data cannot be absorbed, nor can the trends and rates of change be observed, by most en- gineering eyes. These are the motivations for dimensional analysis. The technique is traditional in fluid mechanics and is useful in all engineering and physical sciences, with notable uses also seen in the biological and social sciences.