BMW Technology Communications. Technology Transfer from Formula One to Series Production. Contents
Total Page:16
File Type:pdf, Size:1020Kb
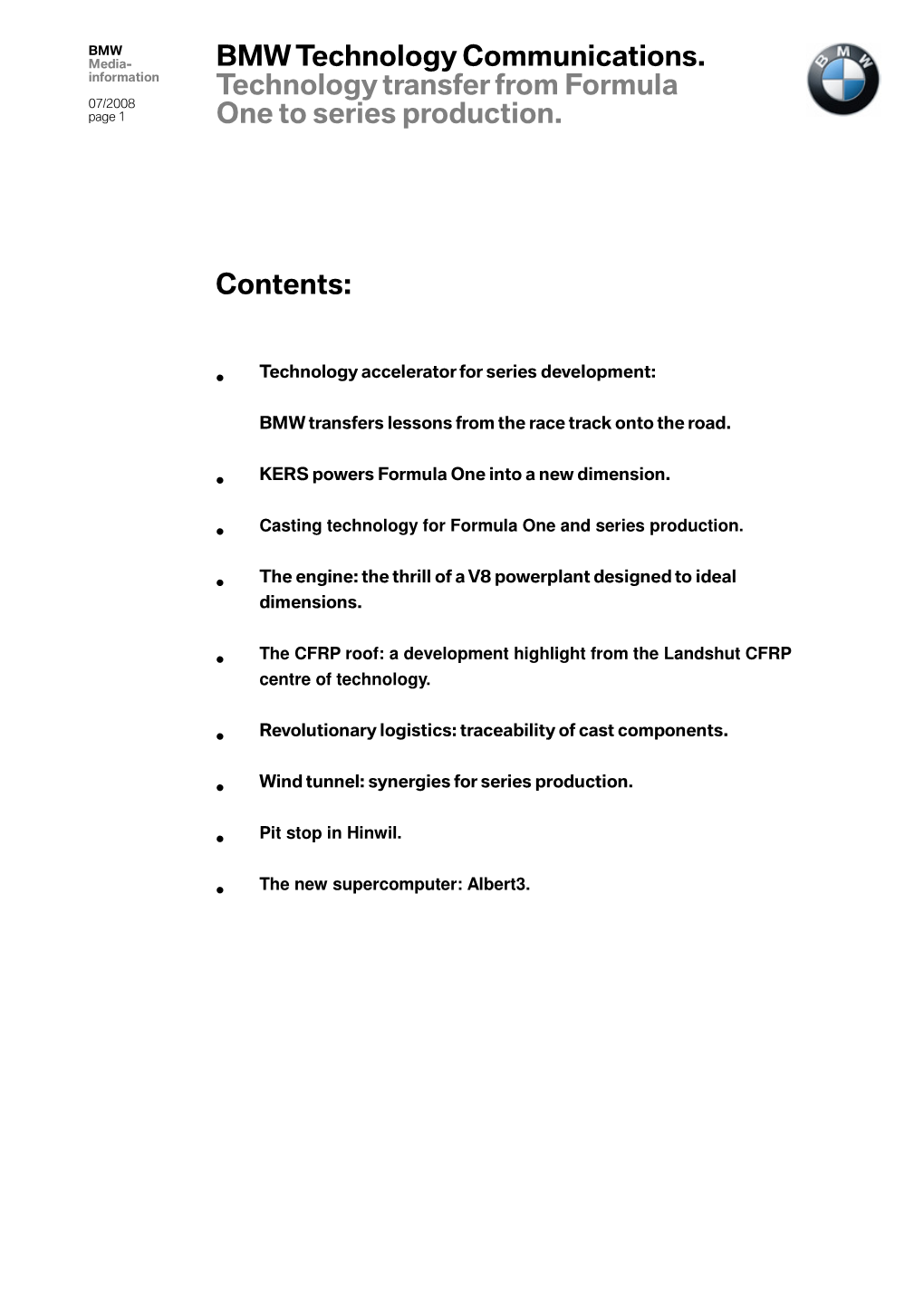
Load more
Recommended publications
-
Efficient Dynamics
A subsidiary of BMW AG BMW U.S. Press Information For Release: September 30, 2015. Contact: Rebecca Kiehne BMW Product & Technology Spokesperson 201-307-3709 / [email protected] Hector Arellano-Belloc BMW Product & Technology Spokesperson 201-307-3755 / [email protected] Alex Schmuck BMW Product & Technology Communications Manager 201-307-3783 / [email protected] The new BMW X4 M40i. World premiere of the new inline 6 cylinder TwinPower Turbo engine. Intelligent BMW xDrive: four-wheel drive with rear-wheel-drive characteristics. A sporty chassis specifically tuned to M Performance specifications. Woodcliff Lake, N.J.: September 30, 2015… Today, with the introduction of the new 2016 BMW X4 M40i, the successful BMW X4 has gained a new top model. In the Sports Activity Coupe segment (SAC), the BMW X4 M40i is setting new standards with enhanced driving dynamics and best-in-segment acceleration. The new BMW X4 M40i will be available at dealers starting February 2016 starting at $57,800 plus Delivery and Handling. Design. The exterior of the new BMW X4 M40i makes it stand out as a clear member of the BMW M Performance family. Exclusive Ferric Gray metallic accents on the front of the vehicle and side mirrors, as well as the exclusive 20-inch M light-alloy double-spoke wheels with optional Michelin Pilot Super Sport tires and the sport exhaust system with valve control and Black Chrome tailpipes on both sides emphasize the unique character of the new BMW X4 M40i. The M leather wrapped steering wheel, M gear shift lever, sport seats, model-specific door sills and “X4 M40i” digital lettering on the instrument cluster decorate the interior, assuring immediate recognition as a BMW M Performance model. -
BMW M Motorsport Presents the New BMW M4 GT3.Pdf
BMW Corporate Communications For Release: Immediate Contacts: Bill Cobb BMW of North America Motorsport Press Officer 215-431-7223 (cell) / [email protected] Oleg Satanovsky BMW of North America Product and Technology Spokesperson 201-414-8694 (cell) / [email protected] Thomas Plucinsky BMW of North America Motorsport Communications 201-406-4801 (cell) / [email protected] BMW M Motorsport presents the new BMW M4 GT3 • Newest addition to BMW Motorsport’s Customer Racing program. • Based on new M4 Competition Coupe. • Eligible for 2022 IMSA WeatherTech GTD and SRO GT Classes • $530,000 excluding shipping. • Competition Package available for $55,000. Woodcliff Lake, N.J. – June 2, 2021…BMW Motorsport is proud to announce the new state-of-the-art BMW M4 GT3 customer race car based on the recently launched 2021 M4 Competition Coupe. Powering the new Coupe is the P58 3.0-liter inline-6-cylinder M TwinPower Turbo engine producing up to 590 hp. The BMW M4 GT3 will retail for $530,000 in the US (excl. shipping). The Competition Package adds $55,000 and includes additional headlights, backlit door numbers, TPMS with 8 sensors, spring and brake pedal travel measurement systems, BOSCH CAS-M rear-view camera radar system, an additional set of rims, and one day of training on the BMW M Motorsport M4 GT3 simulator. In North America, the BMW M4 GT3 will be eligible to compete in the GT Daytona and GT Daytona Pro classes of the IMSA WeatherTech SportsCar Championship, as BMW Corporate Communications well as the GT class of the SRO Fanatec GT World Challenge America powered by AWS and SRO GT America powered by AWS series. -
10 Years of BMW F1 Engines Abstract
- 1 - Prof. Dr.-Ing. Mario Theissen, Dipl.-Ing. Markus Duesmann, Dipl.-Ing. Jan Hartmann, Dipl.-Ing. Matthias Klietz, Dipl.-Ing. Ulrich Schulz BMW Group, Munich 10 Years of BMW F1 Engines Abstract BMW engines gave the company a presence in Formula One from 2000 to 2009. The overall project can be broken down into a preparatory phase, its years as an engine supplier to the Williams team, and a period competing under the banner of its own BMW Sauber F1 Team. The conception, design and deployment of the engines were defined by the Formula One regulations, which were subject to change virtually every year. Reducing costs was the principal aim of these revisions. Development expenditure was scaled down gradually as a result of the technical restrictions imposed on the teams and finally through homologation and a freeze on development. Engine build costs were limited by the increased mileage required of each engine and the restrictions on testing. A lower number of engines were therefore required for each season. A second aim, reduced engine output, was achieved with the switch from 3.0-litre V10 engines to 2.4-litre V8s for the 2006 season. In the early years of its involvement in F1, BMW developed and built a new engine for each season amid a high-pressure competitive environment. This process saw rapid improvements made in engine output and weight, and the BMW powerplant soon attained benchmark status in F1. In recent years, development work focused on raising mileage capability and reliability without changing the engine concept itself. The P86/9 of the 2009 season achieved the same engine output, despite a 20% reduction in displacement, of the E41/4 introduced at the beginning of the 2000 season. -
BMW M4 GT4 Information Brochure
Sheer Driving Pleasure SHEER RACING PLEASURE. THE BMW M4 GT4 IN DETAIL. Motorsport FOREWORD. BMW MOTORSPORT DIRECTOR JENS MARQUARDT. Dear BMW Motorsport customers, I am delighted to present the “Race Car of the Year 2018”* in detail: the BMW M4 GT4. Developing a classic customer racing car such as this, and making it available to private customer teams has always been one of BMW Motorsport’s core competencies. The BMW M4 Coupé production model is the perfect foundation for the development of our latest GT4 contender. Building upon it, our engineers have closed the gap between our entry-level car, the BMW M240i Racing, and our top model, the BMW M6 GT3. The BMW M4 GT4 is designed for use by private customer teams, and in 2018, for its debut season, already obtained considerable success around the world in the booming GT4 class. Using advanced technical solutions and characterized by its high build quality, the BMW M4 GT4 remains affordable, making it a compelling offer within the class. We are grateful to our customers around the world who, like us, believed in the car early on and chose to partner with us on the track. As a new racing season dawns, we believe the best is yet to come for the BMW M4 GT4 and the car has a lot more potential for success around the world. Interested? Look no further than this brochure for more information on the BMW M4 GT4. Kind regards, This is an interactive brochure. Click on the tabs below for example to choose a specific chapter. -
Bmw Sports Trophy. Terms of Participation 2019/2020
BMW SPORTS TROPHY. TERMS OF PARTICIPATION 2019/2020. BMW M Customer Racing TERMS OF PARTICIPATION FOR THE “BMW SPORTS TROPHY DRIVERS’ COMPETITION” AND THE “BMW SPORTS TROPHY TEAM COMPETITION”. PREAMBLE Within the registration process, the participant also receives The BMW Sports Trophy Drivers’ Competition and the BMW a personal driver ID or team ID number. This serves solely Sports Trophy Team Competition allow BMW M Customer to uniquely identify a participant. Racing to honour the performances of privateer drivers and teams, who successfully compete with BMW racing cars in The driver ID number and team ID number must be specified selected international and national racing events and series of in any communication with the organiser. It also serves as the considerable significance. login name for the online portal of the BMW Sports Trophy Drivers’ Competition and the BMW Sports Trophy Team Competition, as well as identification for purchasing BMW I. ORGANISER Sports Trophy Race Wear. The BMW Sports Trophy Drivers’ Competition and BMW Sports Trophy Team Competition are organised by BMW M GmbH, Employees of BMW Group or service providers, agencies Daimlerstr. 19 , 85748 Garching-Hochbrück, hereinafter called and other companies and any other persons involved in the organiser or “BMW M Customer Racing”. conception and implementation of the BMW Sports Trophy Drivers’ Competition and BMW Sports Trophy Team Competition, as well as their family members, are not permitted to participate. II. PARTICIPATION All drivers using BMW vehicles to compete in certain (see point Minors under the age of 16 and those not yet of the age of legal III) national and/or international racing events are authorised competence are not eligible to register for or participate in the to enter the BMW Sports Trophy Drivers’ Competition. -
The Last Road Race
The Last Road Race ‘A very human story - and a good yarn too - that comes to life with interviews with the surviving drivers’ Observer X RICHARD W ILLIAMS Richard Williams is the chief sports writer for the Guardian and the bestselling author of The Death o f Ayrton Senna and Enzo Ferrari: A Life. By Richard Williams The Last Road Race The Death of Ayrton Senna Racers Enzo Ferrari: A Life The View from the High Board THE LAST ROAD RACE THE 1957 PESCARA GRAND PRIX Richard Williams Photographs by Bernard Cahier A PHOENIX PAPERBACK First published in Great Britain in 2004 by Weidenfeld & Nicolson This paperback edition published in 2005 by Phoenix, an imprint of Orion Books Ltd, Orion House, 5 Upper St Martin's Lane, London WC2H 9EA 10 987654321 Copyright © 2004 Richard Williams The right of Richard Williams to be identified as the author of this work has been asserted by him in accordance with the Copyright, Designs and Patents Act 1988. All rights reserved. No part of this publication may be reproduced, stored in a retrieval system, or transmitted, in any form or by any means, electronic, mechanical, photocopying, recording or otherwise, without the prior permission of the copyright owner. A CIP catalogue record for this book is available from the British Library. ISBN 0 75381 851 5 Printed and bound in Great Britain by Clays Ltd, St Ives, pic www.orionbooks.co.uk Contents 1 Arriving 1 2 History 11 3 Moss 24 4 The Road 36 5 Brooks 44 6 Red 58 7 Green 75 8 Salvadori 88 9 Practice 100 10 The Race 107 11 Home 121 12 Then 131 The Entry 137 The Starting Grid 138 The Results 139 Published Sources 140 Acknowledgements 142 Index 143 'I thought it was fantastic. -
2016 Bmw Motorsport Junior Programme
BMW Motorsport 2016 BMW MOTORSPORT www.bmw- Sheer JUNIOR PROGRAMME. motorsport.com Driving Pleasure BMW MOTORSPORT MEDIA INFORMATION. TALENT PROMOTION IN GT RACING. The development of promising talented drivers enjoys a long tradition at BMW Motorsport. In 2014 a new multi-level GT junior concept had been introduced: the BMW Motorsport Junior Programme. This realignment saw BMW Motorsport shift its development of young drivers back to the GT and touring car sector. In Formula racing the concept bore fruit for many years in Formula BMW and the Formula BMW Talent Cup and kick-started the racing career of many successful drivers like Sebastian Vettel, Nico Rosberg and Nico Hülkenberg. The focus is on GT and touring car drivers who already have some racing experience. Outings in the BMW M235i Racing are an integral part of the comprehensive training programme. As well as race starts and test drives, intensive theory courses dealing with fitness and PR are planned, as are mental and simulator training. The potential candidates for this year’s class were put to the test in a shootout in the BMW M235i Racing in Dijon on 10th/11th March. Ricky Collard and Nico Menzel proved to be the most promising talents. They are the 2016 BMW Motorsport Juniors. A decision as to which of the young drivers showed the most potential is made by a jury of experts, headed by BMW Motorsport Director Jens Marquardt. BMW works driver Dirk Adorf will act as a mentor for the junior programme. At the end of the year, the most successful BMW Motorsport Junior of the season will be given the opportunity to continue his training for a second year in a higher racing category. -
2021 Rules Q2 Update New New!
The TireRack BMW CCA Club Racing Series 2021 RULES Q2 Copyright 2021 BMW Car Club of America, Inc. Copyright 2021 BMW Car Club of America, Inc. Table of Contents I. INTRODUCTION ............................................................................................................................................................ 1 A. CLUB PURPOSE ..................................................................................................................................................................... 1 B. INTENTION .......................................................................................................................................................................... 1 C. CAR CLASSIFICATIONS ............................................................................................................................................................ 1 D. INTERPRETATION OF RULES ..................................................................................................................................................... 1 E. RACERS ADVISORY COMMITTEE (RAC) ..................................................................................................................................... 2 II. GENERAL RULES ........................................................................................................................................................... 3 A. PHILOSOPHY ....................................................................................................................................................................... -
Efficient Dynamics
A subsidiary of BMW AG BMW U.S. Press Information For Release: Immediate Contact: Oleg Satanovsky BMW Product & Technology Spokesperson 201-307-3755 / [email protected] Alex Schmuck BMW Product & Technology Communications Manager 201-307-3783 / [email protected] The 2020 BMW X5 M50i and BMW X7 M50i Sports Activity Vehicles New M Performance variants of BMW X5 and X7 SAV’s. 523 hp and 553 lb-ft of torque and M GmbH model specific tuning. 0 to 60 mph in 4.1 seconds for X5 M50i and 4.5 seconds for X7 M50i. Pricing: $82,150 for X5 M50i and $99,600 for X7 M50i. Plus $995 Destination. Production to begin August 2019. 2019 BMW X5 Press Information 2019 BMW X7 Press Information Woodcliff Lake, NJ – May 22, 2019…Today, BMW introduces two new M Performance models, the BMW X5 M50i and BMW X7 M50i, which join the X5 and X7 lineups this fall when production begins in BMW Plant Spartanburg, SC. Both models feature the new top version of the N63 4.4L TwinPower Turbo V8 engine backed by an eight-speed sport automatic transmission, BMW’s xDrive intelligent all-wheel drive , M Sport differential, M Sport exhaust system and model-specific M GmbH suspension tuning. Offering true sports car performance, both BMW Sports Activity Vehicles offer excellent handling and traction across varied surfaces and weather conditions complemented by luxurious interior appointments and the same towing capabilities as their non-M Performance siblings. - more - - 2 - Power and performance The latest generation of the 4.4-liter eight-cylinder engine features numerous detailed improvements. -
The Bmw Series Saloon
The BMW Series Saloon www.bmw.co.uk The Ultimate www.bmw.ie Driving Machine THE BMW SERIES SALOON. BMW EFFICIENTDYNAMICS. LESS EMISSIONS. MORE DRIVING PLEASURE. A PICTURE WORTH A THOUSAND WORDS. Editorial EVERY MOMENT IS PERFECTION. Achieving the best possible results, has always been the objective of BMW Series Saloon. This is what makes it so much more than a straightforward executive vehicle. Whatever the discipline, this car exudes composure and strength of character. Be it design, handling, interior comfort or functionality, the BMW Series Saloon is perfect for anyone who expects more than a stylish appearance from their saloon. The attributes: sportiness, elegance, commanding poise – and, of course, a pioneering outlook. This is convincingly demonstrated by a host of technological innovations from BMW ConnectedDrive. This BMW Series Saloon is the best BMW Series ever – a vehicle in which perfection is a given. And you don’t just feel this on the drive The BMW Series Saloon Technology Equipment Overview to the office. You feel it on every journey. And every mile. PASSION INNOVATION AS INDIVIDUAL AS THE ENTIRE RANGE FOR PRECISION. IN MOTION. YOUR IMAGINATION. AT A GLANCE. www.bmw.co.uk/seriesSaloon Exterior BMW ConnectedDrive The BMW Series SE Saloon Technical data and information on Aesthetic perfection. In touch with your world. fuel consumption and CO emissions Luxury Interior BMW Effi cientDynamics BMW Service and Comfort at the highest level. Making light work of lower fuel M Sport BMW Brand highlights consumption. Exclusive offers for BMW customers. BMW Effi cientDynamics BMW Individual Takes little, gives a lot. -
Efficientdynamics 2007 – the Intelligent Route to Lower Emissions
BMW Group information EfficientDynamics 2007 – the intelligent route to lower emissions. The BMW Group is presenting a raft of innovations in its current model range aimed at drastically reducing emissions. Underpinning these innovations is a clear development strategy dedicated to securing individual mobility for the future. BMW Group Visionary technological developments have played consumption and CO2 emissions levels. This is The BMW Group supports the drive purpose-fully to play its part in fulfilling the voluntary a role in the success of the BMW Group ever since based on the conviction that excellent driving for environmental protection. agreement made by the European Automobile the company was founded over 90 years ago. dynamics and impressive cost-effectiveness need Reductions in fuel consumption are directly linked Manufacturers Association (ACEA). Reliable prognoses on future market requirements not be mutually exclusive. With its principle of to cuts in CO2 emissions. For example, the The common goal of all the ACEA members is to and the timely introduction of tailor-made solutions efficient dynamics, the BMW Group has therefore combustion of one litre of petrol per 100 kilometres cut European fleet average CO2 emissions for new have secured BMW a sustained and pre-eminent placed two equal-priority goals at the centre-point releases approximately 23.8 grams of CO2 per passenger cars to 140 g per kilometre by the end position among the world’s leading car manufacturers. of each new car development project: optimising kilometre, and a vehicle burning 5.0 litres of petrol of 2008. This means capping the average fuel A development strategy initiated by the BMW the use of resources and raising performance per 100 kilometres therefore emits approximately consumption of all vehicles produced by European Group back in the 1990s has yielded a constant characteristics vis-á-vis the outgoing model. -
South Shore Jaguar Land Rover. 219-245-2500
Year: 2013 Engine: Straight 6 Cylinder Engine Make: BMW Transmission: 6-Speed Model: 1 Series 2dr Conv 128i SULEV Colors: Alpine White (300) / Black VIN: WBAUN1C54DVR01197 Mileage: 87,770 Stock #: J20278C · Tilt/telescopic steering-wheel column CITY MPG HIGHWAY MPG MECHANICAL · Power front windows -inc: "one- touch" up/down operation · 3.0-liter dual overhead cam (DOHC), · Check control vehicle monitor system 19 26 24-valve inline 230-hp 6-cylinder w/pictogram display, oil status display, engine w/composite condition Based Service indicator Actual mileage will vary with options, driving conditions, driving habits and vehicle's condition magnesium/aluminum engine block, · On-board computer w/check control Valvetronic, Double-VANOS provides feedback on the vehicle's steplessly variable valve timing operating status: oil level indicator and · Electronic throttle control distance to next service appointment/oil New · Rear-wheel drive change, as well as other detailed · Aluminum double-pivot spring and information, such as spark plug and MSRP $36,900.00 micro-filter status. It also provides strut-type front suspension INSTALLED OPTIONS · Extensive aluminum componentry, travel information travel range on including front suspension remaining fuel, external temperature, [205] Steptronic Automatic Trans. $0 components (forged-aluminum lower and more normal arms); subframe; steering rack; and · Service interval indicator w/miles-to- sport & manual shift modes brake components service readout [300] Alpine White $0 · Cruise control · Five-link fully