Management and Applications of Industrial Robots Associate Authors: Dennis Lock and Kenneth Willis Robotics In• Practice
Total Page:16
File Type:pdf, Size:1020Kb
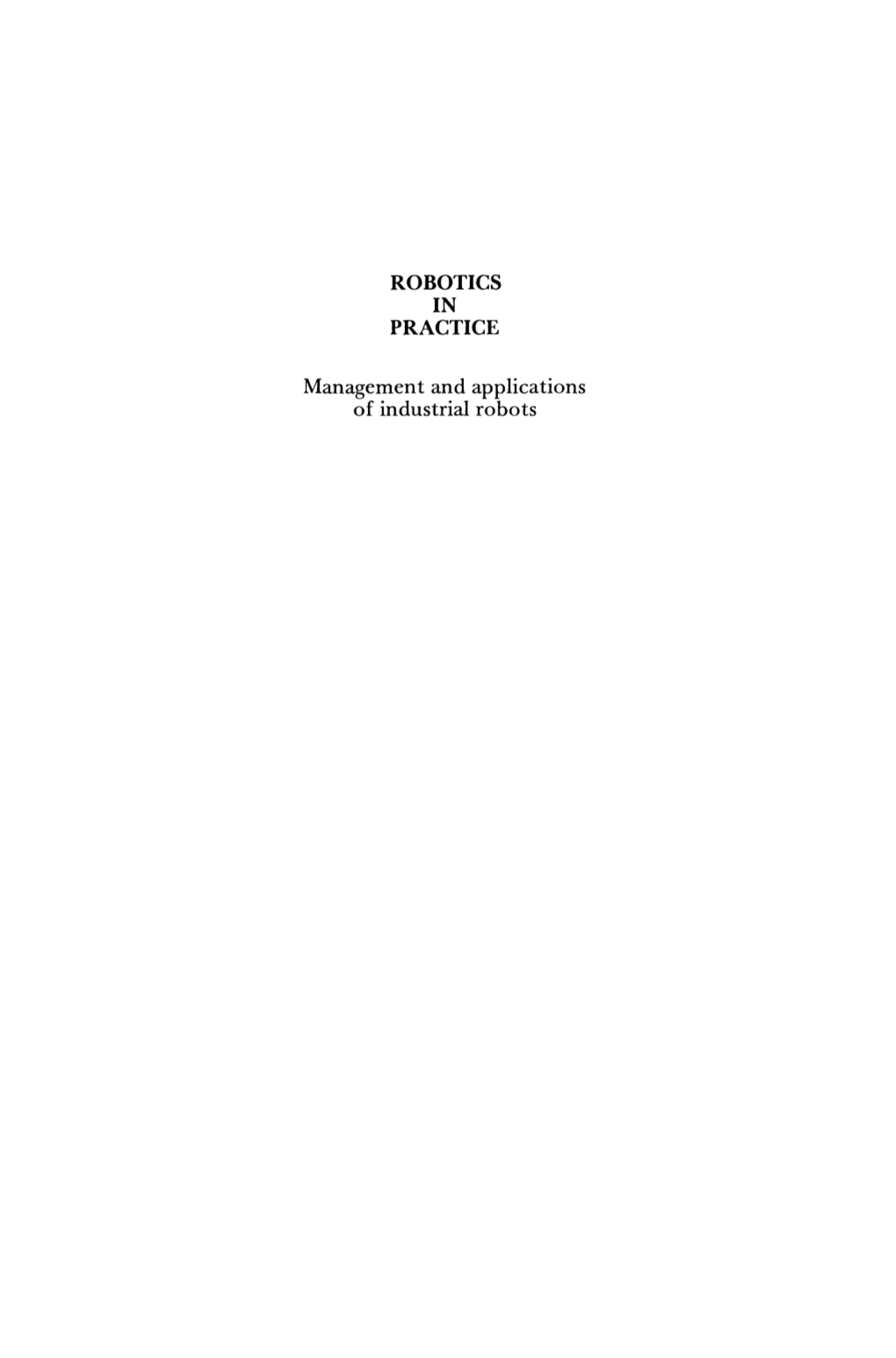
Load more
Recommended publications
-
History of Robotics: Timeline
History of Robotics: Timeline This history of robotics is intertwined with the histories of technology, science and the basic principle of progress. Technology used in computing, electricity, even pneumatics and hydraulics can all be considered a part of the history of robotics. The timeline presented is therefore far from complete. Robotics currently represents one of mankind’s greatest accomplishments and is the single greatest attempt of mankind to produce an artificial, sentient being. It is only in recent years that manufacturers are making robotics increasingly available and attainable to the general public. The focus of this timeline is to provide the reader with a general overview of robotics (with a focus more on mobile robots) and to give an appreciation for the inventors and innovators in this field who have helped robotics to become what it is today. RobotShop Distribution Inc., 2008 www.robotshop.ca www.robotshop.us Greek Times Some historians affirm that Talos, a giant creature written about in ancient greek literature, was a creature (either a man or a bull) made of bronze, given by Zeus to Europa. [6] According to one version of the myths he was created in Sardinia by Hephaestus on Zeus' command, who gave him to the Cretan king Minos. In another version Talos came to Crete with Zeus to watch over his love Europa, and Minos received him as a gift from her. There are suppositions that his name Talos in the old Cretan language meant the "Sun" and that Zeus was known in Crete by the similar name of Zeus Tallaios. -
The Laws of Robots Law, Governance and Technology Series
The Laws of Robots Law, Governance and Technology Series VOLUME 10 Series Editors: POMPEU CASANOVAS, Institute of Law and Technology, UAB, Spain GIOVANNI SARTOR, University of Bologna (Faculty of Law -CIRSFID) and European University Institute of Florence, Italy Scientifi c Advisory Board: GIANMARIA AJANI, University of Turin, Italy; KEVIN ASHLEY, University of Pittsburgh, USA; KATIE ATKINSON, University of Liverpool, UK; TREVOR J.M. BENCH-CAPON, University of Liverpool, UK; V. RICHARDS BENJAMINS, Telefonica, Spain; GUIDO BOELLA, Universita’ degli Studi di Torino, Italy; JOOST BREUKER, Universiteit van Amsterdam, The Netherlands; DANIÈLE BOURCIER, University of Paris 2-CERSA, France; TOM BRUCE, Cornell University, USA; NURIA CASELLAS, Institute of Law and Technology, UAB, Spain; CRISTIANO CASTELFRANCHI, ISTC-CNR, Italy; JACK G. CONRAD, Thomson Reuters, USA; ROSARIA CONTE, ISTC-CNR, Italy; FRANCESCO CONTINI, IRSIG-CNR, Italy; JESÚS CONTRERAS, iSOCO, Spain; JOHN DAVIES, British Telecommunications plc, UK; JOHN DOMINGUE, The Open University, UK; JAIME DELGADO, Universitat Politècnica de Catalunya, Spain; MARCO FABRI, IRSIG-CNR, Italy; DIETER FENSEL, University of Innsbruck, Austria; ENRICO FRANCESCONI, ITTIG - CNR, Italy; FERNANDO GALINDO, Universidad de Zaragoza, Spain; ALDO GANGEMI, ISTC-CNR, Italy; MICHAEL GENESERETH, Stanford University, USA; ASUNCIÓN GÓMEZ-PÉREZ, Universidad Politécnica de Madrid, Spain; THOMAS F. GORDON, Fraunhofer FOKUS, Germany; GUIDO GOVERNATORI, NICTA, Australia; GRAHAM GREENLEAF, The University of New South Wales, -
Robots May Storm World—But First, Soccer*
Robots May Storm World—But First, Soccer* By Mikiko Miyakawa The Daily Yomiuri (Tokyo), January 1, 2003 Robots pose no threat to Ronaldo—yet. But in 2050, a soccer team of human- oid robots may be able to beat the human World Cup champion team. Chasing this seemingly reckless goal, a group of Japanese scientists in 1997 launched RoboCup, the robotic soccer world championship. From these humble beginnings, the annual event has exceeded the organizers’ initial expectations. “The project started with 31 teams from 10 countries, but it rose to as many as 200 from 30 countries in 2002,” said RoboCup Federation President Minoru Asada, a professor at Osaka University. But as well as seeing the size of the event blossom, organizers—and the field of robot research—have seen dramatic developments in robotics, such as the omnidirectional vision and movement that enables robot players to see and move around the pitch much more efficiently. In June last year, while Japan and South Korea were busy cohosting the human soccer World Cup finals, RoboCup 2002 also was held in the two countries, in the cities of Fukuoka and Pusan. The robot players competed in four leagues—small, midsize, Sony four-legged (Aibo) and humanoid. The event also featured simulated soccer, rescue competi- tions and the RoboCup Junior competition for children. But the crowd favorites were the Aibo and humanoid leagues, Asada said. In the Aibo league, some of the robot dogs actually celebrated their teammates’ goals by standing on their hind legs—a sign of communication between the ro- bots. -
Fact Sheet: History of Robotics
Fact Sheet: History of Robotics www.RazorRobotics.com ≈250 B.C. - Ctesibius, an ancient Greek engineer and mathematician, invented a water clock which was the most accurate for nearly 2000 years. ≈60 A.D. - Hero of Alexandria designs the first automated programmable machine. These 'Automata' were made from a container of gradually releasing sand connected to a spindle via a string. By using different configurations of these pulleys, it was possible to repeatably move a statue on a pre-defined path. 1898 - The first radio-controlled submersible boat was invented by Nikola Tesla. 1921 - The term 'Robot' was coined by Karel Capek in the play 'Rossum's Universal Robots'. 1941 - Isaac Asimov introduced the word 'Robotics' in the science fiction short story 'Liar!' 1948 - William Grey Walter builds Elmer and Elsie, two of the earliest autonomous robots with the appearance of turtles. The robots used simple rules to produce complex behaviours. 1954 - The first silicon transistor was produced by Texas Instruments. 1956 - George Devol applied for a patent for the first programmable robot, later named 'Unimate'. 1957 - Launch of the first artificial satellite, Sputnik 1. I, Robot Turtle robot Sputnik 1 1961 - First Unimate robot installed at General Motors. Used for welding and die casting. 1965 - Gordon E. Moore introduces the concept 'Moore's law', which predicts the number of components on a single chip would double every two years. 1966 - Work began on the 'Shakey' robot at Stanford Research Institute. 'Shakey' was capable of planning, route-finding and moving objects. 1969 - The Apollo 11 mission, puts the first man on the moon. -
Robots and Automation Robots and Automation
Issue: Robots and Automation Robots and Automation By: Bill Wanlund Pub. Date: February 9, 2015 Access Date: September 26, 2021 DOI: 10.1177/2374556815571549 Source URL: http://businessresearcher.sagepub.com/sbr-1645-94777-2641309/20150209/robots-and-automation ©2021 SAGE Publishing, Inc. All Rights Reserved. ©2021 SAGE Publishing, Inc. All Rights Reserved. Will technological advances help businesses and workers? Executive Summary Fueled by advances in computer and sensor technology, robots are growing in sophistication and versatility to become an important—and controversial—sector of the world economy. Once largely limited to manufacturing plants, robots now are found in households, offices and hospitals, and on farms and highways. Some believe robots are a job creator, a boon to corporate productivity and profits, and a way to “reshore” American manufacturing that had migrated to countries where labor was cheaper. Others fear that the growing use of robots will wipe out millions of lower-skilled jobs, threatening the economic security of the working poor, fostering social inequality and leading to economic stagnation. Today's managers need to understand how humans and machines can best work together; government and industry must decide how best to manage robots' design, manufacture and use. Overview Drew Greenblatt, president and CEO of Marlin Steel Wire Products of Baltimore, says introducing robots into his manufacturing operation was “imperative: Our choice was either extinction or transformation.” When Greenblatt bought Marlin in 1998, the company—then based in Brooklyn, N.Y.— made steel baskets for bagel shops. And the overseas competition was murderous. “We were confronted with finished baskets from Asia that cost less than my cost for the steel alone,” Greenblatt says. -
Thesis in Process
The Future of Robotics Lynsey Anne Lius 22548 Degree Thesis Materials Processing Technology 2021 Lynsey Anne Lius 22548 DEGREE THESIS Arcada Degree Programme: Materials Processing Technology Identification number: 22548 Author: Lynsey Anne Lius Title: The Future of Robotics Supervisor (Arcada): Mathew Vihtonen Commissioned by: Abstract: This thesis aimed to consider the future of robotics in society and in particular, within educational curricula. The writer summarized the current role of robots in industry and surveyed a small number of social peers to gain an insight into cur- rent attitudes and perceptions of robots in society, particularly concerning em- ployment security. The outcome of this survey showed that people are not partic- ularly concerned about their own employment security although they e xhibit greater concern for future generations. The limits of this survey must be consid- ered in that it was conducted on a small group of connections of the author using social media meaning that the group size was too small to be significantly mean- ingful whilst also meaning that those surveyed belonged to a narrow social de- mographic. The author also conducted a trail using a readily available robot remote-control car kit. The kit was found to be educational and suitable for a UAS student to learn the basics of robotics while being flexible enough to accommodate deeper study for motivated students. However, the author noted that since educational institutions are now beginning education in robotics at a young age, a kit of this nature will cease to be useful for higher education students in the nea r future and more advanced educational opportunities will be needed to support the develop- ment of future students. -
POLITECNICO DI TORINO Bilby Rover Autonomous Mobile Robot In
POLITECNICO DI TORINO Master of Science in Automotive Engineering Final Project Bilby Rover autonomous mobile robot in the context of Industry 4.0 Survey on sensor-enabled applications through Webots simulations and implementation of Hector-SLAM algorithm for autonomous navigation Supervisor: Candidate: Prof. Giovanni Belingardi Alessia Valle Co-Supervisor: Prof. Maria Pia Cavatorta McMaster University Supervisor: Prof. Ishwar Singh Academic Year 2020/2021 "O frati," dissi, "che per cento milia perigli siete giunti a l’occidente, a questa tanto picciola vigilia d’i nostri sensi ch’è del rimanente non vogliate negar l’esperïenza, di retro al sol, del mondo sanza gente. Considerate la vostra semenza: fatti non foste a viver come bruti, ma per seguir virtute e canoscenza". D. Alighieri, Inferno, C. XXVI, vv.112-120 Abstract In the light of Industry 4.0 revolution, the advances in information technology like Internet of Things, Artificial Intelligence, Cloud Computing, Cyber-Physical Systems and Big Data are changing the use and design of robots in the indus- try. Robotics, which is a multidisciplinary field that builds on the intersection of mechanical and electrical engineering, computer science, communication and networking, and material technology, is undergoing dramatic developments in recent years, as the landscape of Industry 4.0 is progressively unfolding. This thesis stems from the collaboration with McMaster’s W Booth School of Engineering Practice and Technology and aims at studying and simulating a model of an autonomous mobile robot, called Bilby Rover. The first section of the project provides a review of literature and research related to Industry 4.0, outlining its enabling technologies, future opportunities and implications in the field of robotics. -
Introduction to Robotics
Introduction to Robotics Vikram Kapila, Associate Professor, Mechanical Engineering Outline • Definition • Types •Uses • History • Key components • Applications • Future • Robotics @ MPCRL Robot Defined • Word robot was coined by a Czech novelist Karel Capek in a 1920 play titled Rassum’s Universal Robots (RUR) • Robot in Czech is a word for worker or servant Karel Capek zDefinition of robot: –Any machine made by by one our members: Robot Institute of America - –A robot is a reprogrammable, multifunctional manipulator designed to move material, parts, tools or specialized devices through variable programmed motions for the performance of a variety of tasks: Robot Institute of America, 1979 Types of Robots: I Manipulator Types of Robots: II Legged Robot Wheeled Robot Types of Robots: III Autonomous Underwater Vehicle Unmanned Aerial Vehicle Robot Uses: I Jobs that are dangerous for humans Decontaminating Robot Cleaning the main circulating pump housing in the nuclear power plant Robot Uses: II Repetitive jobs that are boring, stressful, or labor- intensive for humans Welding Robot Robot Uses: III Menial tasks that human don’t want to do The SCRUBMATE Robot Laws of Robotics • Asimov proposed three “Laws of Robotics” and later added the “zeroth law” • Law 0: A robot may not injure humanity or through inaction, allow humanity to come to harm • Law 1: A robot may not injure a human being or through inaction, allow a human being to come to harm, unless this would violate a higher order law • Law 2: A robot must obey orders given to it by human beings, except where such orders would conflict with a higher order law • Law 3: A robot must protect its own existence as long as such protection does not conflict with a higher order law History of Robotics: I • The first industrial robot: UNIMATE • 1954: The first programmable robot is designed by George Devol, who coins the term Universal Automation. -
Robot Caregiver
Should This Exist? Transcript – Robot Caregiver “Grandma, here’s your robot”: Should This Exist? with Caterina Fake Click here to listen to the full Should This Exist? episode on the robot caregiver. CATERINA FAKE: Hi. It’s Caterina. For a thousand years and more, storytellers in every culture have imagined mechanical beings. In the Iliad, Homer described how the god of blacksmiths whipped up a few golden handmaidens to help him do his work. Robots were usually good to humans in the tales the ancients told. Of course, they weren’t called robots. The word “robata” – meaning “forced labor” – was first used in 1920 in a Czech play about artificial factory workers that rebel against their human masters, and kill them. Somehow, in the 20th-century imagination, robots turned bad. “ROBOCOP”: Please put down your weapon. You have 20 seconds to comply. DICK JONES: I think you’d better do what he says, Mr. Kinney. FAKE: There are a few exceptions. This guy is so adorable and non-threatening, he even took a mechanical shuffle down Sesame Street back in the late 1970s. “SESAME STREET”: R2D2, this is called a banana. FAKE: “Loveable robots” like R2D2 exist, largely thanks to the legendary science fiction pioneer Isaac Asimov. In the 1940’s, Asimov laid out three laws for robots to peacefully coexist with humans in a short story called “Runaround.” ISAAC ASIMOV: A robot may not harm a human being or, through inaction, allow a human being to come to harm. FAKE: Asimov’s laws have guided real roboticists ever since. -
Highlights from Digital Computer Museum Report 1/1982
file:////cray/Shared/COLLECTIONS/Curator/mondo_museum_report.htm Return to List of Reports Highlights from Digital Computer Museum Report 1/1982 Contents of Highlights ● Back of Front Cover ● The Director's Letter ● Unusual Photos ● LECTURE SERIES Back of Front Cover The Digital Computer Museum is an independent, non-profit, charitable foundation. It is the world's only institution dedicated to the industry-wide preservation of information processing devices and documentation. It interprets computer history through exhibits, publications, videotapes, lectures, educational programs, excursions, and special events. Hours and Services The Digital Computer Museum is open to the public Sunday through Friday, 1:00 pm to 6:00 pm. There is no charge for admission. The Digital Computer Museum Lecture Series Lectures focus on benchmarks in computing history and are held six times a year. All lectures are videotaped and archived for scholarly use. Gallery talks by computer historians, staff members and docents are offered every Wednesday at 4:00 and Sunday at 3:00. Guided group tours are available by appointment only. Books, posters, postcards, and other items related to the history of computing are available for sale at the Museum Store. The Museum's lecture hall and reception facilities are available for rent on a prearranged basis. For information call 617-467-4443. BOARD OF DIRECTORS Charles Bachman C. Gordon Bell Gwen Bell Harvey C. Cragon Robert Everett C. Lester Hogan Theodore G. Johnson Andrew C. Knowles, III John Lacey Pat McGovern George Michael Robert N. Noyce Kenneth H. Olsen Brian Randell Edward A. Schwartz Michael Spock Erwin O. Tomash Senator Paul E. -
A Distributed Modular Self-Reconfiguring Robotic Platform Based on Simplified Electro-Permanent Magnets Li Zhu
A distributed modular self-reconfiguring robotic platform based on simplified electro-permanent magnets Li Zhu To cite this version: Li Zhu. A distributed modular self-reconfiguring robotic platform based on simplified electro- permanent magnets. Networking and Internet Architecture [cs.NI]. Universite Toulouse 3 Paul Sabatier (UT3 Paul Sabatier), 2018. English. tel-01829962 HAL Id: tel-01829962 https://hal.laas.fr/tel-01829962 Submitted on 4 Jul 2018 HAL is a multi-disciplinary open access L’archive ouverte pluridisciplinaire HAL, est archive for the deposit and dissemination of sci- destinée au dépôt et à la diffusion de documents entific research documents, whether they are pub- scientifiques de niveau recherche, publiés ou non, lished or not. The documents may come from émanant des établissements d’enseignement et de teaching and research institutions in France or recherche français ou étrangers, des laboratoires abroad, or from public or private research centers. publics ou privés. THTHESEESE`` En vue de l’obtention du DOCTORAT DE L’UNIVERSITE´ DE TOULOUSE D´elivr´e par : l’Universit´eToulouse 3 Paul Sabatier (UT3 Paul Sabatier) Pr´esent´ee et soutenue le Vendredi 16 f´evrier2018 par : LI ZHU A distributed modular self-reconfiguring robotic platform based on simplified electro-permanent magnets JURY Nadine Le Fort Piat Professeur Universit´ede France Bourgogne, Franche-Comt´e Julien Bourgeois Professeur Universit´ede France Bourgogne, Franche-Comt´e Patrick Danes Professeur Universit´ede Toulouse France III Paul Sabatier Didier El -
From the Unimate to the Delta Robot: the Early Decades of Industrial Robotics
From the Unimate to the Delta robot: the early decades of Industrial Robotics A. Gasparetto and L. Scalera Polytechnic Department of Engineering and Architecture – University of Udine, Udine, Italy, e-mail: [email protected] / [email protected] Abstract . In this paper, the early decades of the history of industrial robots (from the 1950’s to the be- ginning of the 1990’s, approximately) will be described. The history of industrial robotics can be con- sidered starting with Unimate, the first industrial robot designed and built by Devol and Engelberger. The subsequent evolutions of industrial robotics are described in the manuscript, taking into account both the technical and the economic point of view, until the beginning of the 1990’s, when new kine- matic structures (parallel robots) appeared, allowing high-speed operations. Key words: Industrial robots, history, Unimate, Stanford Arm, Delta robot 1 Introduction Since ancient times, the humanity conceived the idea to design and to build some kind of beings, or devices, which could substitute men in heavy or repetitive work. Such beings, called automata , date back to the Greek-Hellenistic age and have been conceived by several civilizations throughout the centuries. A historical per- spective of Robotics may be found in [1] and [2], while a brief history of automata and robots, from ancient times up to the Industrial Revolution, can be found in [3]. From the Industrial Revolution on, some forms of automatization took place in the industrial environment; however, it is only in the 1950’s that what is known as “industrial robotics” started.