Design and Fabrication of a Modular Multi-Material 3D Printer by Justin
Total Page:16
File Type:pdf, Size:1020Kb
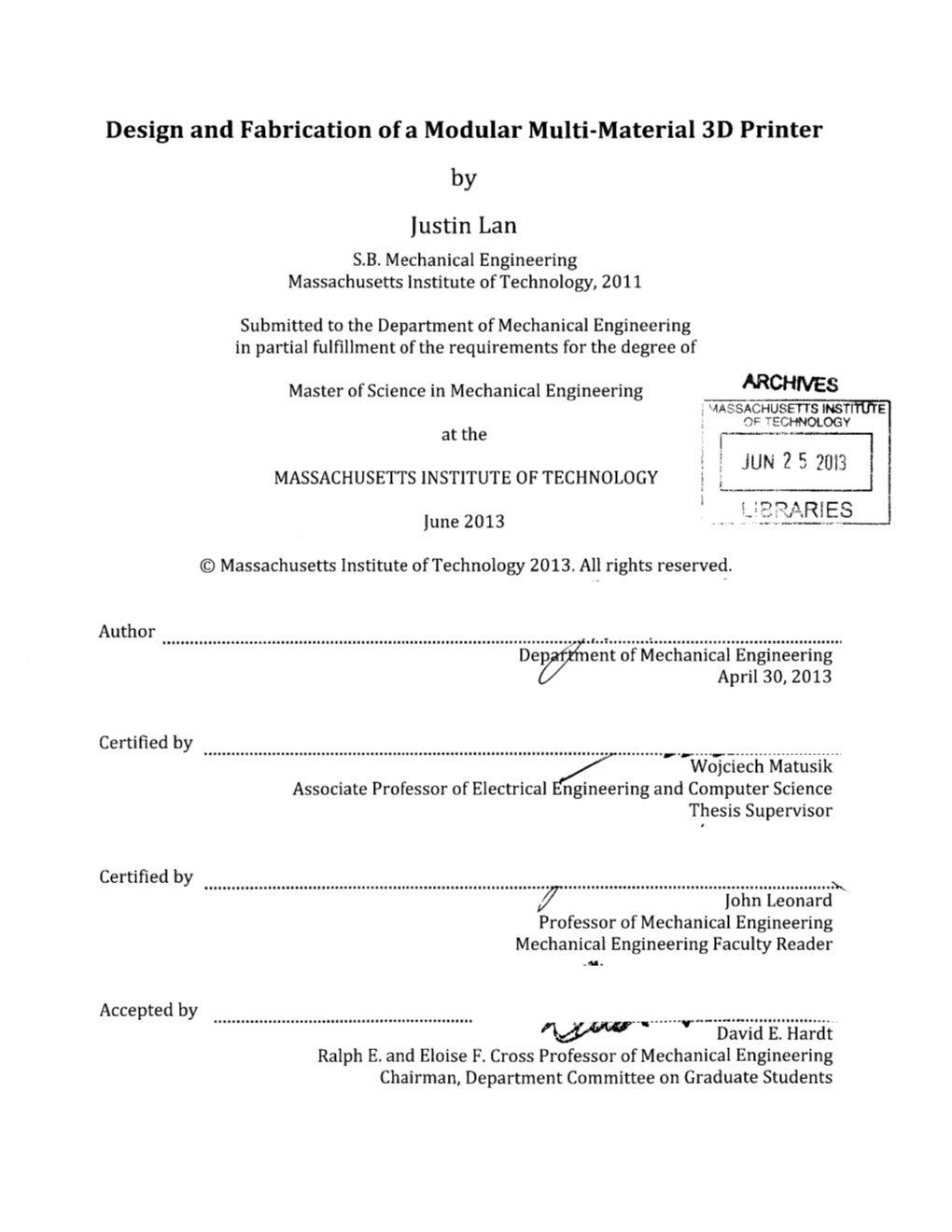
Load more
Recommended publications
-
Hackerspaces
d WP4 | CASE STUDY Report: Hackerspaces Theme [ssh.2013.3.2-1][Social Innovation- Empowering People, changing societies] Project Full Title: “Transformative Social Innovation Theory project” Grant Agreement n. 613169 This project has received funding from the European Union’s Seventh Framework Programme for research, technological development and demonstration under grant agreement no 613169 Suggested citation: Sabine Hielscher, Adrian Smith, Mariano Fressoli (2015) WP4 Case Study Report: Hackerspaces, Report For the TRANSIT FP7 Project, SPRU, University oF Sussex, Brighton. Acknowledgements: We wish to thank everyone in the Hackerspace scene who helped us with our research, whether through interviews, welcoming us to Hackerspaces and events, or putting us in touch with others. We also thank our colleagues in the TRANSIT project, at SPRU, at UNQ and Fundación Cenit For their help and encouragement with the research. Finally, we thank the European Commission and their FP7 research programme For Funding the TRANSIT project. Date: 14 January 2015 Authors: Sabine Hielscher, Adrian Smith, Mariano Fressoli Contact person: Adrian Smith Table of contents 1 Introduction to Hackerspaces 2 Methodology 2.1 Researcher relations to the case 2.2 Methods 3 Analysis of transnational network(ing) 3.1 Transnational networking: Hackerspaces 3.2 Aspects of ‘innovation’ and ‘change’ of the transnational network(ing) 3.3 Aspects of empowerment and disempowerment of the transnational network(ing) 3.4 Other issues about the transnational networking 4 Local initiative -
3D Printing at the Florida Public Library
Prepared by-Robert Persing April 2017 1 • What is 3D “printing” • A bit of HISTORY • Types of 3D printing technology • Really Interesting 3D printing Applications! • Bringing it Home Prepared by-Robert Persing April 2017 2 • “A process for making a physical object from a three-dimensional digital model, typically by laying down successive thin layers of a material”. • 3D Printing is also referred to as- “ADDITIVE MANUFACTURING” Prepared by-Robert Persing April 2017 3 A “Three-Dimensional Digital Model” (Paper ‘n Pencil holder designed by students in recent FPL class) Prepared by-Robert Persing April 2017 4 Finished product printed with the library’s 3D printer Student Product Prepared by-Robert Persing April 2017 5 • Invented in 1983, 3D printing is not all that new • Chuck Hull, recognized as the “inventor” of 3D printing, filed for a patent August 8, 1986 • Hull coined the phrase “Stereo Lithography” for the technology used in his 3D printer when applying for the patent (granted March 11, 1986) • Let’s watch a brief CNN interview with Chuck Hull Prepared by-Robert Persing April 2017 6 • The year 2005 is a notable point in the history of 3D printing. This marks the start of the RepRap Project by Dr. Adrian Bowyer at Bath University in England • RepRap is short for replicating rapid prototyper. RepRaps are 3D printers with the additional ability to produce most of the parts necessary to assemble another identical printer. Prepared by-Robert Persing April 2017 7 “Darwin” The First RepRap Printer Prepared by-Robert Persing April 2017 8 • With the history lesson covered, let’s look at 3D Printing in the 21st century • What Technology is used to print 3D? • How do you actually make a 3D printed object? Prepared by-Robert Persing April 2017 9 Concrete Type Technologies Materials Thermoplastics (e.g. -
3D Printing Focused Peer Production Acta Universitatis Tamperensis 2298
JARKKO MOILANEN 3D Printing Focused Peer Production Acta Universitatis Tamperensis 2298 JARKKO MOILANEN 3D Printing Focused Peer Production Revolution in design, development and manufacturing AUT 2298 AUT JARKKO MOILANEN 3D Printing Focused Peer Production Revolution in design, development and manufacturing ACADEMIC DISSERTATION To be presented, with the permission of the Faculty Council of the Faculty of Communication Sciences of the University of Tampere, for public discussion in the auditorium Pinni B 1097, Kanslerinrinne 1, Tampere, on 12 July 2017, at 12 o’clock. UNIVERSITY OF TAMPERE JARKKO MOILANEN 3D Printing Focused Peer Production Revolution in design, development and manufacturing Acta Universitatis Tamperensis 2298 Tampere University Press Tampere 2017 ACADEMIC DISSERTATION University of Tampere Faculty of Communication Sciences Finland The originality of this thesis has been checked using the Turnitin OriginalityCheck service in accordance with the quality management system of the University of Tampere. Copyright ©2017 Tampere University Press and the author Cover design by Mikko Reinikka Acta Universitatis Tamperensis 2298 Acta Electronica Universitatis Tamperensis 1801 ISBN 978-952-03-0492-8 (print) ISBN 978-952-03-0493-5 (pdf) ISSN-L 1455-1616 ISSN 1456-954X ISSN 1455-1616 http://tampub.uta.fi Suomen Yliopistopaino Oy – Juvenes Print 441 729 Tampere 2017 Painotuote Acknowledgements I would like to express my special appreciation and thanks to my advisor Docent Dr. Tere Vad´en,you have been a tremendous mentor for me. I would like to thank you for encouraging my research and for allowing me to grow as a research scientist. Your advice on both have been priceless. I would also like to thank Professor Dr. -
Live Software for Reprap Assembly Workshops
Torbjørn Ludvigsen Live Software For RepRap Assembly Workshops MASTER'STHESIS SUPERVISOR:MARCINJAKUBOWSKI EXAMINER:MARTINROSVALL DEPARTMENTOFPHYSICS UME AUNIVERSITY˚ This document was compiled on June 16, 2016. Status: Defended and approved This work is licensed under a Attribution 4.0 International licence. Copyright © 2016 Torbjørn Ludvigsen Abstract A key step when initiating robot powered production is setting up the control software. This can be a threshold for operators, especially if the software is fragmented and system requirements are extensive. One way to address this is to pre-configure all the control programs and bundle them with a system that fulfills all the requirements. In this work a live Operating System (OS) is loaded with control software and configured to meet the needs of those who have just as- sembled their first 3D printer. The problem of downloading, configuring and installing various 3D printer controlling programs is reduced to the problem of distributing and booting the live OS. The solution of loading it onto bootable USB drives is tested and evaluated in the context of a commercial RepRap Assembly Workshop (RAW), an event where people pay for RepRap 3D printer parts as well as assembly and usage supervision. The RAW is unusually short, so the bootable USB drives' potential to help RAW hosts with particularly tight time schemes is tested. The results show a limited success. The USB drive is documented not to work for 3 participant groups out of a total of 11 groups. As a solution to fragmented software and diverse system requirements, the live OS is found to work well once booted. -
Belt-Driven Open Source Circuit Mill Using Low-Cost 3-D Printer Components
inventions Article Belt-Driven Open Source Circuit Mill Using Low-Cost 3-D Printer Components Shane Oberloier 1 and Joshua M. Pearce 1,2,3,* ID 1 Department of Electrical and Computer Engineering, Michigan Technological University, Houghton, MI 49931, USA; [email protected] 2 Department of Materials Science and Engineering, Michigan Technological University, Houghton, MI 49931, USA 3 Department of Electronics and Nano engineering, School of Electrical Engineering, Aalto University, FI-00076 Espoo, Finland * Correspondence: [email protected]; Tel.: +1-906-487-1466 Received: 13 August 2018; Accepted: 30 August 2018; Published: 5 September 2018 Abstract: Barriers to inventing electronic devices involve challenges of iterating electronic designs due to long lead times for professional circuit board milling or high costs of commercial milling machines. To overcome these barriers, this study provides open source (OS) designs for a low-cost circuit milling machine. First, design modifications for mechanical and electrical subsystems of the OS Distributed 3-D (D3D) Robotics prototyping system are provided. Next, Copper Carve, an OS custom graphical user interface, is developed to enable circuit board milling by implementing backlash and substrate distortion compensation. The performance of the OS D3D circuit mill is then quantified and validated for: positional accuracy, cut quality, feature accuracy, and distortion compensation. Finally, the return on investment is calculated for inventors using it. The results show by properly compensating for motion inaccuracies with Copper Carve, the machine achieves a motion resolution of 10 microns, which is more than adequate for most circuit designs. The mill is at least five times less expensive than all commercial alternatives and the material costs of the D3D mill are repaid from fabricating 20–43 boards. -
Additive Manufacturing: Analysis of the Economic Context and Evaluation of the Indoor Air Quality, with a Total Quality Management Approach
DIPARTIMENTO DI ECONOMIA, SOCIETÀ, POLITICA CORSO DI DOTTORATO DI RICERCA IN Economia, Società, Diritto CURRICULUM Economia e Management CICLO XXXI Additive Manufacturing: analysis of the economic context and evaluation of the indoor air quality, with a Total Quality Management approach SETTORE SCIENTIFICO DISCIPLINARE: SECS-P/13-SCIENZE MERCEOLOGICHE RELATORE DOTTORANDA Chiar.ma Prof.ssa Federica Murmura Dott.ssa Laura Bravi CO TUTOR Ing. Francesco Balducci Anno Accademico 2017/2018 Summary INTRODUCTION CHAPTER 1: ADDITIVE MANUFACTURING: IS IT THE FUTURE? ABSTRACT .......................................................................................................................... 10 1.1 Additive and Subtractive Manufacturing ...................................................................... 10 1.2 The road towards Additive Manufacturing ................................................................... 13 1.2.1 Prehistory of AM .................................................................................................... 14 1.2.2 First attempts to modern AM ................................................................................. 16 1.2.3 The RepRap project ................................................................................................ 19 1.2.4 The Fab@Home project ......................................................................................... 23 1.3 AM today: 3D printing in the digitalization of manufacturing ..................................... 24 1.3.1 The main Additive Manufacturing -
Profit Open Source Hardware Projects
INTERNATIONAL CONFERENCE ON ENGINEERING DESIGN, ICED19 5-8 AUGUST 2019, DELFT, THE NETHERLANDS UNDERSTANDING COMMUNITY BEHAVIORS IN FOR- PROFIT OPEN SOURCE HARDWARE PROJECTS Li, Zhuoxuan (1); Seering, Warren (1); Tao, Tiffany (1); Cao, Shengnan (2) 1: Massachusetts Institute of Technology; 2: Northeastern University ABSTRACT Free contributors have successfully shown the potential in large/complex software co-creation in the Free and Open Source Software Movement, triggering many discussions and exploration ventures from academia to industry and to the government. Though many research efforts explored whether the same level of co-creation efforts could take place broadly in the hardware realm, very few research studies focus on profit-seeking hardware projects initiated by companies. In fact, the specific nature of being tangible and profitable makes company-led open source hardware projects suspicious to be really “open” to contributors. Community has been identified as the critical driver in many open projects. By reviewing the evolution of company-community interactions over time and different community behaviors in different open development context, authors in this paper hope to identify best community- company interaction forms for open source hardware companies. Using grounded theory and case studies, we construct a framework to describe and identify company community’s different behaviors and different roles. Keywords: Open source design, Open innovation, Design management, Collaborative design Contact: Li, Zhuoxuan Massachusetts Institute of Technology Mechanical Engineering United States of America [email protected] Cite this article: Li, Z., Seering, W., Tao, T., Cao, S. (2019) ‘Understanding Community Behaviors in For-Profit Open Source Hardware Projects’, in Proceedings of the 22nd International Conference on Engineering Design (ICED19), Delft, The Netherlands, 5-8 August 2019. -
Reprap Colour Mixing Project
Department of Mechanical Engineering FACULTY OF ENGINEERING AND DESIGN FINAL YEAR MEng PROJECT Reprap Colour Mixing Project James Corbett 1st May 2012 “I certify that I have read and understood the entry in the Student Handbook for the Department of Mechanical Engineering on Cheating and Plagiarism and that all material in this assignment is my own work, except where I have indicated with appropriate references. I agree that, in line with Regulation 15.3(e), if requested I will submit an electronic copy of this work for submission to a Plagiarism Detection Service for quality assurance purposes” Author’s signature: Supervisor: Adrian Bowyer Assessor: Andrew Dent RepRap Colour Mixing James Corbett Abstract: With recent technological advances the cost of 3D printing has been driven down to make the technology widely available for home users and projects such as RepRap have become much more widespread. RepRap is an open source project started by Adrian Bowyer of Bath University in 2005 which was designed around the ideal of creating a low cost home printer that could self replicate a larger proportion of its own parts and is the only current project of its type. The printing process uses a fused filament fabrication method which melts a strand of plastic which is deposited in fine layers to build up a 3D object. The current models of printers are rather limited to using the plastics that can be bought from a supplier so a nozzle has been designed and developed in this report to enable the home user to print in any colour from only having to purchase a few colours. -
3D Printing Consumer Vs Professional
3D Printing Consumer vs Professional TABLE OF CONTENTS Introduction ............................................................................. 2 A Brief History of 3D Printing ............................................. 2 The 3D Printing Process ..................................................... 3 3D Printing Technologies ................................................... 3 Consumer vs. Professional 3D Printing .............................. 4 Consumer 3D Printing ......................................................... 4 Features ........................................................................... 5 Limitations and Challenges .......................................... 6 Professional 3D Printing ..................................................... 7 Features ........................................................................... 7 Applications ..................................................................... 8 Limitations and Challenges ............................................... 9 Key Takeaways ................................................................. 10 SUMMARY ............................................................................. 11 1 Introduction 3D printing is the process of manufacturing three- dimensional objects by depositing successive layers of Additive vs. Subtractive material via a 3D printer. By using an additive manufacturing Manufacturing technique, 3D printing departs radically from conventional subtractive manufacturing processes. As a result, 3D Additive manufacturing is the -
Searching for That Killer App! a New Type of 3D Printing: a 25-Year-Old Technology Has Caught the Fancy of a New Generation of Designers and Engineers
Searching For That Killer App! A New Type of 3D Printing: A 25-year-old technology has caught the fancy of a new generation of designers and engineers. From iPhone cases to customized sake sets, will anything ever be the same again? by Alan S. Brown ALL IT THE Pocket Factory Tour. This past Hornstein spent time at Idealab, a technology incubator January, Bilal Ghalib and Alex Hornstein, two that launched dozens of companies, then moved to Hong A New Type of 3D Printing..... 26-year-old computer science graduates of Kong to start the city’s first private hacker space. After University of Michigan and MIT, respectively, it went belly up, he and Ghalib decided to take their 3D c set out from San Francisco with four inexpensive printers on the road. They called the project Pocket Fac- 3D printers in the back of their Prius. tory. They wanted to discover whether they could make a They had met years ago over the Internet. Ghalib was living by designing, producing, and selling products made building a $50 laser cutter, Hornstein a computer-controlled on their hand-assembled 3D printers. Etch-a-Sketch. Ghalib went on to work on autonomous ve- “We set up in art galleries, parks, and flea markets hicles and set up Egypt’s first hacker space, where people and we make custom belt buckles, iPhone cases, and 3D with common technology interests shared resources and portraits. People could talk to us about the uses they see ideas. for the technology, and we see what they are willing to pay for,” Hornstein said from Salt Lake City. -
Supplementary Appendix: the History of the 3D Printing Industry The
Supplementary Appendix: The History of the 3D Printing Industry The advent of 3D printing can be traced back to a Frenchmen in Paris in 1859 named François Willème who created photo sculptures of real people using similar techniques of that to the techniques used by 3D printing in today’s world (Norman, 2016: Walters and Thirkell, 2007). In 1892 J.E. Blanther, a manufacturer of contour relief maps, proposed a layering method to make a mold for topographical relief maps. The method involved impressing topographical contour lines on a number of wax plates that were stacked, cut and smoothed to form a three-dimensional surface that created a raised relief map. In 1972, Matsubara of Mitsubishi Motors suggested a topographical process that used photo-hardening materials to produce layered parts (Bourell et al, 2009). Until the late 1970s the alternative primary manufacturing idea - adding material – had received comparatively little attention (except in the electronics industry for chip manufacture, where it was, and still is, ubiquitous, if microscopic). According to Bradshaw et al (2010) the advent of 3D printing started with a joke written in 1974 and a patent granted in 1977. David Jones a writer by the pen name ‘Daedalus’ described 3D printing as joke in the New Scientist. He gave a descriptive yet imaginative technique that proposed creation of solid objects. Coincidently, in 1977 Wyn Kelly Swainson was granted a patent for the similar idea. However, the patent was filed way before Jones piece was published. It wasn’t until 1981 that Hideo Kodama of Nagoya Municipal Industrial Research Institute published the first account of a functional photopolymer rapid prototyping system (Kodama, 1981: Bourell et al, 2009: AV plastics). -
Live Software for Reprap Assembly Workshops
UMEA˚ UNIVERSITY May 24, 2016 Department of Physics Masters Thesis, 30 hp Live Software For RepRap Assembly Workshops Torbjørn Ludvigsen [email protected] Supervisor: Marcin Jakubowski Abstract Contents 1 Introduction 3 1.1 Copyability and Structural Virality . .4 1.2 RepRap ..............................4 1.2.1 Structural Virality of RepRap Spread . .6 1.3 RepRap Assembly Workshops . .7 1.3.1 RepRap Assembly Workshop Software Procedures . .7 1.4 Live Operating Systems . .8 1.5 Research Question . .9 2 Method 10 2.1 Overview . 10 2.2 Subjects.............................. 10 2.2.1 Open Source Ecology . 10 2.2.2 D3D-Porteus Live Operating System . 11 2.2.3 Programs . 12 2.2.4 Hardware . 12 2.2.5 Participants ........................ 12 2.3 Measures . 12 2.3.1 The Web Survey . 13 2.3.2 Boot Testing . 13 2.4 Procedures............................. 14 2.4.1 Transmission of D3D-Porteus to OSE . 14 2.4.2 Workshop Execution . 14 2.4.3 The Web Survey . 14 2.4.4 Boot Testing . 14 3 Results 15 3.1 Pre-Workshop Copyability . 15 3.2 TheWorkshop........................... 15 3.3 Thematic Analysis of Survey Responses . 16 1 3.3.1 Time Shortage . 16 3.3.2 Long-Term Motivation . 16 3.3.3 Copyability . 18 3.3.4 D3D-Porteus Functionality . 18 3.4 Instructor Comments . 19 3.5 Boot Testing . 19 4 Discussion 20 4.1 Result Discussion . 20 4.2 Method Discussion . 21 4.3 FurtherWork ........................... 21 4.4 Author's Last Words And Recommendations . 22 A Acronyms 24 B Web Search Investigation of RepRap Assembly Workshop Plans 25 C Approximating the Number of Prusa Machines in May 2016 29 D Porteus 31 D.1 Basic Configuration .