Analysis of Chassis Frame for Solar Vehicle
Total Page:16
File Type:pdf, Size:1020Kb
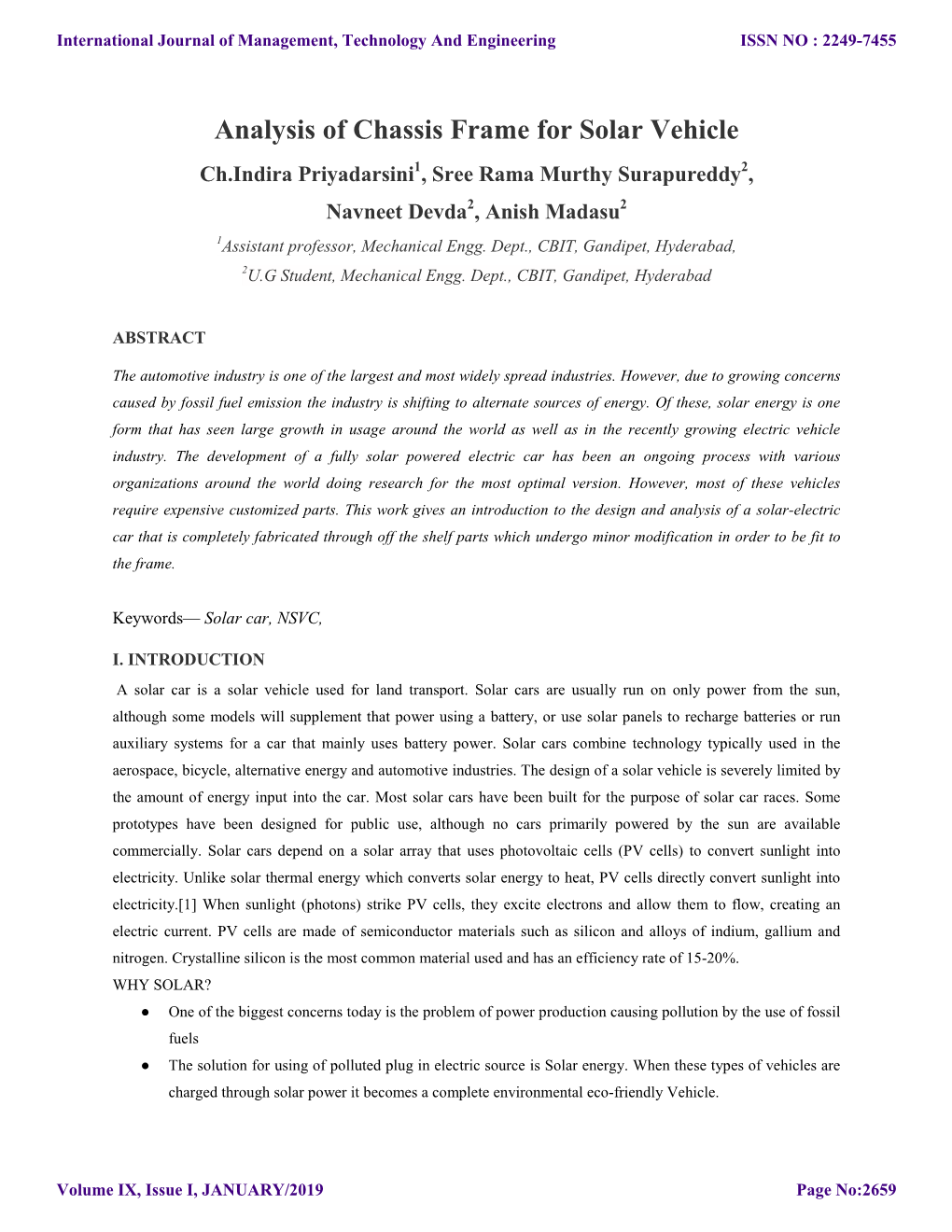
Load more
Recommended publications
-
Solar Vehicle Case Study
UNIVERSITY OF MINNESOTA SOLAR VEHICLE PROJECT Weather Data Vital for Solar-Powered Vehicle Race When the University of Minnesota Solar Vehicle Project (UMNSVP) team was looking for a weather station to compete in the 2017 Bridgestone World Solar Challenge, they contacted Columbia Weather Systems. “One of the most important resources for our race strategy is real-time weather data,” said Electrical Technical Advisor Spencer Berglund. Founded in 1990, UMNSVP is a student-administered, designed, and built project that teaches members about engineering and management in a complete product development environment. The diverse design and construction challenges help further the school’s mission to “create the best engineers possible.” Over the years they have built 13 solar cars, competing in over 30 racing events across three con- tinents. A new car is designed and built every two years. “One of the most important resources for our race strategy is real-time weather data.” The Challenge - Spencer Berglund, The biennial Bridgestone World Solar Challenge event challenges univer- Electrical Technical sity teams from around the world to engineer, build, and race a vehicle Advisor that is powered by the sun. In preparing for the 2017 race, Berglund said, “Our lack of accurate weather data is a large limiting factor in maxi- mizing our race performance.” The Solution A Magellan MX500™ Weather Station was mounted on a support vehicle providing met data to help optimize power for the new solar-powered, Cruiser-Class car dubbed “Eos II.” Besides speed, Cruiser-Class vehicles focus on practicality and number of people in the car. Gearing up for the race, Berglund related, “We’ve been test driving a lot for the past few days and have been using your weather station for gathering accurate power to drive data for our car. -
Three-Dimensional Metallo-Dielectric Selective Thermal Emitters With
View metadata, citation and similar papers at core.ac.uk brought to you by CORE provided by UPCommons. Portal del coneixement obert de la UPC Manuscript post-print for self-archiving purposes Solar Energy Materials and Solar Cells 134, 22—28 (2015) doi:10.1016/j.solmat.2014.11.017 Three-Dimensional Metallo-Dielectric Selective Thermal Emitters With High-Temperature Stability for Thermophotovoltaic Applications. Moisés Garín a*, David Hernández a, Trifon Trifonov a,b, Ramón Alcubilla a,b a Grup de Recerca en Micro i Nanotecnologies, Departament d’Enginyeria Electrònica, Universitat Politècnica de Catalunya, Jordi Girona 1-3 Mòdul C4, Barcelona 08034, Spain. b Centre de Recerca en Nanoenginyeria, Universitat Politècnica de Catalunya, Pascual i Vilà 15, Barcelona 08028, Spain. * E-mail: [email protected] Keywords: selective thermal emitters, thermophotovoltaics, photonic crystals, macroporous silicon ABSTRACT Selective thermal emitters concentrate most of their spontaneous emission in a spectral band much narrower than a blackbody. When used in a thermophovoltaic energy conversion system, they become key elements defining both its overall system efficiency and output power. Selective emitters' radiation spectra must be designed to match their accompanying photocell's band gap and, simultaneously, withstand high temperatures (above 1000 K) for long operation times. The advent of nanophotonics has allowed the engineering of very selective emitters and absorbers; however, thermal stability remains a challenge since 1 of 22 nanostructures become unstable at temperatures much below the melting point of the used materials. In this paper we explore an hybrid 3D dielectric-metallic structure that combines the higher thermal stability of a monocrystalline 3D Silicon scaffold with the optical properties of a thin Platinum film conformally deposited on top. -
15Th Workshop on Crystalline Silicon Solar Cells and Modules: Materials and Processes
A national laboratory of the U.S. Department of Energy Office of Energy Efficiency & Renewable Energy National Renewable Energy Laboratory Innovation for Our Energy Future th Proceedings 15 Workshop on Crystalline NREL/BK-520-38573 Silicon Solar Cells and Modules: November 2005 Materials and Processes Extended Abstracts and Papers Workshop Chairman/Editor: B.L. Sopori Program Committee: M. Al-Jassim, J. Kalejs, J. Rand, T. Saitoh, R. Sinton, M. Stavola, R. Swanson, T. Tan, E. Weber, J. Werner, and B. Sopori Vail Cascade Resort Vail, Colorado August 7–10, 2005 NREL is operated by Midwest Research Institute ● Battelle Contract No. DE-AC36-99-GO10337 th Proceedings 15 Workshop on Crystalline NREL/BK-520-38573 Silicon Solar Cells and Modules: November 2005 Materials and Processes Extended Abstracts and Papers Workshop Chairman/Editor: B.L. Sopori Program Committee: M. Al-Jassim, J. Kalejs, J. Rand, T. Saitoh, R. Sinton, M. Stavola, R. Swanson, T. Tan, E. Weber, J. Werner, and B. Sopori Vail Cascade Resort Vail, Colorado August 7–10, 2005 Prepared under Task No. WO97G400 National Renewable Energy Laboratory 1617 Cole Boulevard, Golden, Colorado 80401-3393 303-275-3000 • www.nrel.gov Operated for the U.S. Department of Energy Office of Energy Efficiency and Renewable Energy by Midwest Research Institute • Battelle Contract No. DE-AC36-99-GO10337 NOTICE This report was prepared as an account of work sponsored by an agency of the United States government. Neither the United States government nor any agency thereof, nor any of their employees, makes any warranty, express or implied, or assumes any legal liability or responsibility for the accuracy, completeness, or usefulness of any information, apparatus, product, or `process disclosed, or represents that its use would not infringe privately owned rights. -
Perovskite Solar Cells with Large Area CVD-Graphene for Tandem
View metadata, citation and similar papers at core.ac.uk brought to you by CORE provided by HZB Repository 1 Perovskite Solar Cells with Large-Area CVD-Graphene 2 for Tandem Solar Cells 3 Felix Lang *, Marc A. Gluba, Steve Albrecht, Jörg Rappich, Lars Korte, Bernd Rech, and 4 Norbert H. Nickel 5 Helmholtz-Zentrum Berlin für Materialien und Energie GmbH, Institut für Silizium 6 Photovoltaik, Kekuléstr. 5, 12489 Berlin, Germany. 7 8 ABSTRACT: Perovskite solar cells with transparent contacts may be used to compensate 9 thermalization losses of silicon solar cells in tandem devices. This offers a way to outreach 10 stagnating efficiencies. However, perovskite top cells in tandem structures require contact layers 11 with high electrical conductivity and optimal transparency. We address this challenge by 12 implementing large area graphene grown by chemical vapor deposition as highly transparent 13 electrode in perovskite solar cells leading to identical charge collection efficiencies. Electrical 14 performance of solar cells with a graphene-based contact reached those of solar cells with 15 standard gold contacts. The optical transmission by far exceeds that of reference devices and 16 amounts to 64.3 % below the perovskite band gap. Finally, we demonstrate a four terminal 17 tandem device combining a high band gap graphene-contacted perovskite top solar cell 18 (Eg=1.6 eV) with an amorphous/crystalline silicon bottom solar cell (Eg=1.12 eV). 19 1 1 TOC GRAPHIC. 2 3 4 Hybrid perovskite methylammonium lead iodide (CH3NH3PbI3) attracts ever-growing interest 5 for use as a photovoltaic absorber.1 Only recently, Jeon et al. -
Digital Twin Modeling of a Solar Car Based on the Hybrid Model Method with Data-Driven and Mechanistic
applied sciences Article Digital Twin Modeling of a Solar Car Based on the Hybrid Model Method with Data-Driven and Mechanistic Luchang Bai, Youtong Zhang *, Hongqian Wei , Junbo Dong and Wei Tian Laboratory of Low Emission Vehicle, Beijing Institute of Technology, Beijing 100081, China; [email protected] (L.B.); [email protected] (H.W.); [email protected] (J.D.); [email protected] (W.T.) * Correspondence: [email protected] Featured Application: This technology is expected to be used in energy management of new energy vehicles. Abstract: Solar cars are energy-sensitive and affected by many factors. In order to achieve optimal energy management of solar cars, it is necessary to comprehensively characterize the energy flow of vehicular components. To model these components which are hard to formulate, this study stimulates a solar car with the digital twin (DT) technology to accurately characterize energy. Based on the hybrid modeling approach combining mechanistic and data-driven technologies, the DT model of a solar car is established with a designed cloud platform server based on Transmission Control Protocol (TCP) to realize data interaction between physical and virtual entities. The DT model is further modified by the offline optimization data of drive motors, and the energy consumption is evaluated with the DT system in the real-world experiment. Specifically, the energy consumption Citation: Bai, L.; Zhang, Y.; Wei, H.; error between the experiment and simulation is less than 5.17%, which suggests that the established Dong, J.; Tian, W. Digital Twin DT model can accurately stimulate energy consumption. Generally, this study lays the foundation Modeling of a Solar Car Based on the for subsequent performance optimization research. -
Solar Decathlon 2009 Hours
The National Mall Washington, D.C. Oct. 9–13 and Oct. 15–18, 2009 www.solardecathlon.org 2009 U.S. Capitol Workshops Smithsonian Castle Natural History Museum University of Wisconsin-Milwaukee University of Louisiana at Lafayette Team Missouri (Missouri University of Science & Technology, The University of Arizona University of Missouri) Team Alberta (University of Calgary, SAIT Rice University Polytechnic, Alberta College of Art + Design, Team Ontario/BC (University of Mount Royal College) Waterloo, Ryerson University, Simon Iowa State University Fraser University) Penn State Team Spain (Universidad Politécnica de Madrid) 12th Street Metro Tent 12th Street University of Kentucky The Ohio State University Team Boston (Boston Architectural Team Germany (Technische Universität College, Tufts University) Darmstadt) Virginia Tech Cornell University Universidad de Puerto Rico DECATHLETE WAY University of Minnesota Team California (Santa Clara University, University of Illinois at Urbana-Champaign California College of the Arts) American History Museum Department of Agriculture Main Tent Information 14th Street Smithsonian Metro Station Restrooms Washington Picnic Area Washington, D.C. Monument First Aid SOLAR DECATHLON 2009 HOURS Oct. 9–13 and Oct. 15–18 11 a.m.–3 p.m., Weekdays 10 a.m.–5 p.m., Weekends Houses are closed Oct. 14 for competition purposes. Message From the Secretary of Energy Table of Contents Welcome to Solar Decathlon 2009.............................................2 Exhibits and Events .....................................................................3 -
Thin Crystalline Silicon Solar Cells Based on Epitaxial Films Grown at 165°C by RF-PECVD
CORE Metadata, citation and similar papers at core.ac.uk Provided by HAL-Polytechnique Thin crystalline silicon solar cells based on epitaxial films grown at 165 C by RF-PECVD Romain Cariou, Martin Labrune, Pere Roca I Cabarrocas To cite this version: Romain Cariou, Martin Labrune, Pere Roca I Cabarrocas. Thin crystalline silicon solar cells based on epitaxial films grown at 165 C by RF-PECVD. Solar Energy Materials and Solar Cells, Elsevier, 2011, 95 (8), pp.2260-2263. <10.1016/j.solmat.2011.03.038>. <hal-00749873v3> HAL Id: hal-00749873 https://hal-polytechnique.archives-ouvertes.fr/hal-00749873v3 Submitted on 14 May 2013 HAL is a multi-disciplinary open access L'archive ouverte pluridisciplinaire HAL, est archive for the deposit and dissemination of sci- destin´eeau d´ep^otet `ala diffusion de documents entific research documents, whether they are pub- scientifiques de niveau recherche, publi´esou non, lished or not. The documents may come from ´emanant des ´etablissements d'enseignement et de teaching and research institutions in France or recherche fran¸caisou ´etrangers,des laboratoires abroad, or from public or private research centers. publics ou priv´es. Thin crystalline silicon solar cells based on epitaxial films grown at 165°C by RF-PECVD Romain Carioua),*, Martin Labrunea),b), P. Roca i Cabarrocasa) aLPICM-CNRS, Ecole Polytechnique, 91128 Palaiseau, France bTOTAL S.A., Gas & Power, R&D Division, Tour La Fayette, 2 Place des Vosges, La Défense 6, 92 400 Courbevoie, France Keywords Low temperature, Epitaxy; PECVD; Si thin film; Solar cell Abstract We report on heterojunction solar cells whose thin intrinsic crystalline absorber layer has been obtained by plasma enhanced chemical vapor deposition at 165°C on highly doped p-type (100) crystalline silicon substrates. -
Metal Assisted Synthesis of Single Crystalline Silicon Nanowires At
dicine e & N om a n n a o t N e f c o h Md Asgar et al., J Nanomed Nanotechnol 2014, 5:4 l n Journal of a o n l o r g u DOI: 10.4172/2157-7439.1000221 y o J ISSN: 2157-7439 Nanomedicine & Nanotechnology Research Article Open Access Metal Assisted Synthesis of Single Crystalline Silicon Nanowires at Room Temperature for Photovoltaic Application Md Asgar A1, Hasan M2, Md Huq F3* and Zahid H Mahmood4 1Department of Electronics and Communication Engineering, Jatiya Kabi Kazi Nazrul Islam University, Trishal, Mymensingh, Bangladesh 2Department of Electrical and Electronic Engineering, Shahjalal University of Science and Technology, Kumargaon, Sylhet-3114, Bangladesh 3Department of Nuclear Engineering, University of Dhaka, Dhaka 1000, Bangladesh 4Department of Applied Physics Electronics and Communication Engineering, University of Dhaka, Dhaka-1000, Bangladesh Abstract Synthesis of single crystalline silicon nanowires (SiNWs) array at room temperature by metal assisted chemical etching and its optical absorption measurements have been reported in this article. It has been confirmed that, SiNWs were formed uniformly on p-type silicon substrate by electroless deposition of Cu and Ag nanoparticles followed by wet chemical etching in (Hydrogen Fluoride) HF based Fe(NO3)3 solution. Synthesized SiNW structures were analyzed and investigated by Scanning Electron Microscopy (SEM) and Ultraviolet-Visible (UV-VIS) spectrophotometer. Formation of SiNWs is evident from the SEM images and morphology of the structures depends upon the concentration of chemical solution and etching time. The synthesized SiNWs have shown strong broadband optical absorption exhibited from UV- spectroscopy. More than 82% absorption of incident radiation is found for Cu treated samples and a maximum of 83% absorption of incident radiation is measured for Ag synthesized samples which is considerably enhanced than that of silicon substrate as they absorbed maximum of 43% of incoming radiation only. -
Thin Film Silicon Solar Cells: Advanced Processing and Characterization - 26 101191 / 151399
April 2008 Photovoltaic Programme Edition 2008 Summary Report, Project List, Annual Project Reports 2007 (Abstracts) elaborated by: NET Nowak Energy & Technology Ltd. Cover: Zero-Energy Building: Support Office of Marché International, Kemptthal / ZH 44,6 kWp Solar Power System with Thin Film Solar Cells (Photos: Front cover: SunTechnics Fabrisolar, Back cover: Büro für Architektur Beat Kämpfen, Photo Willi Kracher) Prepared by: NET Nowak Energy & Technology Ltd. Waldweg 8, CH - 1717 St. Ursen (Switzerland) Phone: +41 (0) 26 494 00 30, Fax. +41 (0) 26 494 00 34, [email protected] on behalf of: Swiss Federal Office of Energy SFOE Mühlestrasse 4, CH - 3063 Ittigen postal addresse: CH- 3003 Bern Phone: 031 322 56 11, Fax. 031 323 25 00 [email protected] www.bfe.admin.ch Photovoltaic Programme Edition 2008 Summary Report, Project List, Annual Project Reports 2007 (Abstracts) Contents S. Nowak Summary Report Edition 2008 Page 5 Annual Project Reports 2007 (Abstracts) Page C. Ballif, J. Bailat, F.J. Haug, S. Faÿ, R. Tscharner Thin film silicon solar cells: advanced processing and characterization - 26 101191 / 151399 F.J. Haug, C. Ballif Flexible photovoltaics: next generation high efficiency and low cost thin 27 film silicon modules - CTI 8809 S. Olibet, C. Ballif High efficiency thin-film passivated silicon solar cells and modules - 28 THIFIC: Thin film on crystalline Si - Axpo Naturstrom Fonds 0703 C. Ballif, F. J. Haug, V. Terrazzoni-Daudrix FLEXCELLENCE: Roll-to-roll technology for the production of high efficiency 29 low cost thin film silicon photovoltaic modules - SES-CT-019948 N. Wyrsch, C. Ballif ATHLET: Advanced Thin Film Technologies for Cost Effective Photovoltaics - 30 IP 019670 A. -
A New Direction for Renewable Energy
A New Direction For Renewable Energy . Conserving the worlds carbon . At our current usage of carbon their will be no carbon left on this planet in approx 7000 years time. Carbon is the building block of life. This is why we need renewable energy & electric propulsion. AUSI, Australien Universal Space Industries have developed the latest state of the art robotic systems for constructing renewable energy infrastructure. Robotic Renewable Energy Infrastructure Construction . Evolutionary swarm robotics basics . In days gone by & still in these days & hopefully for many years into the future the demoscene has stamped its way into computer immortality. Using complex discrete mathamatics computer programmers are able to push the limits of computational power & produce awe inspiring display hacks. http://www.demoscene.tv/ What started out as abit of tinkering with computers by enthusiasts & hobbyists resulted in attaining government & corporate sponsorship, however has government & corporate sponsorship reduced the creativity of the demoscene ? The demoscene was around before youtube or googlevid & even the internet. What makes the Demoscene stand out from the rest is that computer generated music was blended with computer generated graphics. Three types of ppl make a demo work. [1] coders [2] graphicians [3] musicians And these days many old demo group groupies now work with mathematicians, data miners, scientists & engineers to create EEA Exploratory Engineering Applications . The Magical Seven These Days Comprise Of . [1] coders [2] graphicians [3] musicians [4] mathematicians [5] data miners [6] scientists [7] engineers EEA Exploratory Engineering Applications are still esoteric but do provide humanity a possible alternative reality apart from the traditional highway to hell. -
ROBERT C.N. PILAWA-PODGURSKI Assistant Professor, Department of Electrical and Computer Engineering University of Illinois Urbana-Champaign 4042 ECE Building • 306 N
Robert Pilawa-Podgurski Curriculum Vitae, October 2016 1 of 18 ROBERT C.N. PILAWA-PODGURSKI Assistant Professor, Department of Electrical and Computer Engineering University of Illinois Urbana-Champaign 4042 ECE Building • 306 N. Wright Street • Urbana, IL 61801 Tel. +1 (217) 244-0181 • E-mail: [email protected] • Web: http://pilawa.ece.illinois.edu EDUCATION Massachusetts Institute of Technology Electrical Engineering Ph.D. 2012 Massachusetts Institute of Technology Electrical Engineering and Computer Science M.Eng. 2007 Massachusetts Institute of Technology Electrical Engineering and Computer Science B.S. 2005 Massachusetts Institute of Technology Physics B.S. 2005 ACADEMIC POSITIONS 2012 - present Assistant Professor Department of Electrical and Computer Engineering University of Illinois at Urbana-Champaign, Urbana, IL 2012 – present Affiliate Faculty Information Trust Institute, University of Illinois at Urbana-Champaign, Urbana, IL 2016 (summer) Visiting Professor KTH – Royal Institute of Technology, Stockholm, Sweden 2007 – 2011 Research Assistant Laboratory for Electromagnetic and Electronic Systems, Research Laboratory of Electronics, MIT, Cambridge, MA SELECTED HONORS AND AWARDS 2016 IEEE Energy Conversion Congress & Exposition (ECCE) Best Paper Award 2016 Top Innovation Award, IEEE International Future Energy Challenge (Advisor) 2016 UIUC List of Teachers Ranked as Excellent by Their Students (with distinction of ‘outstanding’) – ECE 598RPP Advanced Power Electronics 2016 IEEE Workshop on Control and Modeling for Power Electronics -
Next-Generation Solar Power Dutch Technology for the Solar Energy Revolution Next-Generation High-Tech Excellence
Next-generation solar power Dutch technology for the solar energy revolution Next-generation high-tech excellence Harnessing the potential of solar energy calls for creativity and innovative strength. The Dutch solar sector has been enabling breakthrough innovations for decades, thanks in part to close collaboration with world-class research institutes and by fostering the next generation of high-tech talent. For example, Dutch student teams have won a record ten titles in the World Solar Challenge, a biennial solar-powered car race in Australia, with students from Delft University of Technology claiming the title seven out of nine times. 2 Solar Energy Guide 3 Index The sunny side of the Netherlands 6 Breeding ground of PV technology 10 Integrating solar into our environment 16 Solar in the built environment 18 Solar landscapes 20 Solar infrastructure 22 Floating solar 24 Five benefits of doing business with the Dutch 26 Dutch solar expertise in brief 28 Company profiles 30 4 Solar Energy Guide The Netherlands, a true solar country If there’s one thing the Dutch are remarkably good at, it’s making the most of their natural circumstances. That explains how a country with a relatively modest amount of sunshine has built a global reputation as a leading innovator in solar energy. For decades, Dutch companies and research institutes have been among the international leaders in the worldwide solar PV sector. Not only with high-level fundamental research, but also with converting this research into practical applications. Both by designing and refining industrial production processes, and by developing and commercialising innovative solutions that enable the integration of solar PV into a product or environment with another function.