Performance Variability Analysis of the Opensparc Architecture on Fpgas Richard Wiley Advisor: Prof
Total Page:16
File Type:pdf, Size:1020Kb
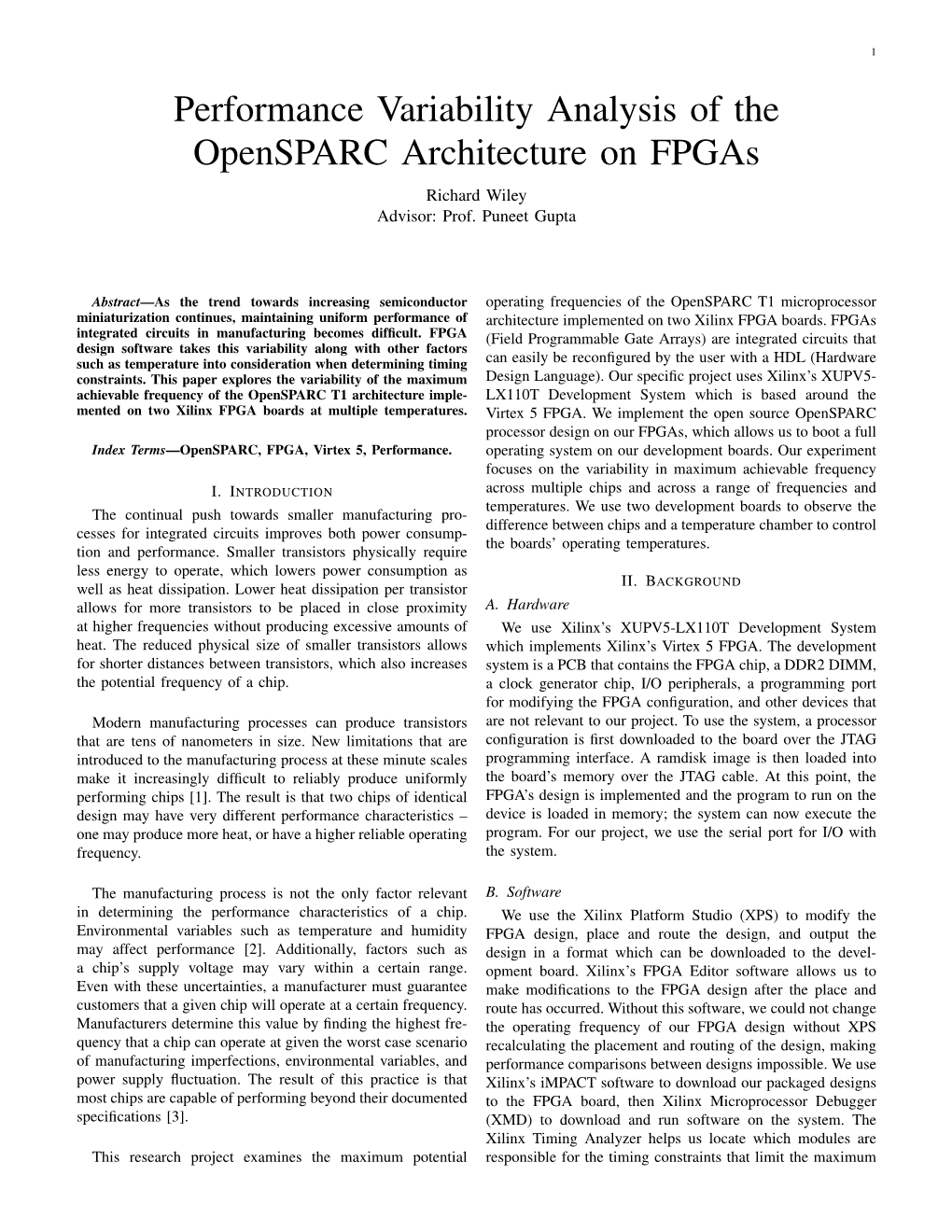
Load more
Recommended publications
-
SPARC/IOBP-CPU-56 Installation Guide
SPARC/IOBP-CPU-56 Installation Guide P/N 220226 Revision AB September 2003 Copyright The information in this publication is subject to change without notice. Force Computers, GmbH reserves the right to make changes without notice to this, or any of its products, to improve reliability, performance, or design. Force Computers, GmbH shall not be liable for technical or editorial errors or omissions contained herein, nor for indirect, special, incidental, or consequential damages resulting from the furnishing, performance, or use of this material. This information is provided "as is" and Force Computers, GmbH expressly disclaims any and all warranties, express, implied, statutory, or otherwise, including without limitation, any express, statutory, or implied warranty of merchantability, fitness for a particular purpose, or non−infringement. This publication contains information protected by copyright. This publication shall not be reproduced, transmitted, or stored in a retrieval system, nor its contents used for any purpose, without the prior written consent of Force Computers, GmbH. Force Computers, GmbH assumes no responsibility for the use of any circuitry other than circuitry that is part of a product of Force Computers, GmbH. Force Computers, GmbH does not convey to the purchaser of the product described herein any license under the patent rights of Force Computers, GmbH nor the rights of others. CopyrightE 2003 by Force Computers, GmbH. All rights reserved. The Force logo is a trademark of Force Computers, GmbH. IEEER is a registered trademark of the Institute for Electrical and Electronics Engineers, Inc. PICMGR, CompactPCIR, and the CompactPCI logo are registered trademarks and the PICMG logo is a trademark of the PCI Industrial Computer Manufacturer’s Group. -
ASIC Implemented Microblaze-Based Coprocessor for Data Stream
ASIC-IMPLEMENTED MICROBLAZE-BASED COPROCESSOR FOR DATA STREAM MANAGEMENT SYSTEMS A Thesis Submitted to the Faculty of Purdue University by Linknath Surya Balasubramanian In Partial Fulfillment of the Requirements for the Degree of Master of Science in Electrical and Computer Engineering May 2020 Purdue University Indianapolis, Indiana ii THE PURDUE UNIVERSITY GRADUATE SCHOOL STATEMENT OF THESIS APPROVAL Dr. John J. Lee, Chair Department of Electrical and Computer Engineering Dr. Lauren A. Christopher Department of Electrical and Computer Engineering Dr. Maher E. Rizkalla Department of Electrical and Computer Engineering Approved by: Dr. Brian King Head of Graduate Program iii ACKNOWLEDGMENTS I would first like to express my gratitude to my advisor Dr. John J. Lee and my thesis committee members Dr. Lauren A. Christopher and Dr. Maher E. Rizkalla for their patience, guidance, and support during this journey. I would also like to thank Mrs. Sherrie Tucker for her patience, help, and encouragement. Lastly, I must thank Dr. Pranav Vaidya and Mr. Tareq S. Alqaisi for all their support, technical guidance, and advice. Thank you all for taking time and helping me complete this study. iv TABLE OF CONTENTS Page LIST OF TABLES :::::::::::::::::::::::::::::::::: vi LIST OF FIGURES ::::::::::::::::::::::::::::::::: vii ABSTRACT ::::::::::::::::::::::::::::::::::::: ix 1 INTRODUCTION :::::::::::::::::::::::::::::::: 1 1.1 Previous Work ::::::::::::::::::::::::::::::: 1 1.2 Motivation :::::::::::::::::::::::::::::::::: 2 1.3 Thesis Outline :::::::::::::::::::::::::::::::: -
LSU EE 4720 Homework 1 Solution Due: 3 March 2006
LSU EE 4720 Homework 1 Solution Due: 3 March 2006 Several Web links appear below and at least one is long, to avoid the tedium of typing them view the assignment in Adobe reader and click. Problem 1: Consider these add instructions in three common ISAs. (Use the ISA manuals linked to the references page, http://www.ece.lsu.edu/ee4720/reference.html.) # MIPS64 addu r1, r2, r3 # SPARC V9 add g2, g3, g1 # PA RISC 2 add r1, r2, r3 (a) Show the encoding (binary form) for each instruction. Show the value of as many bits as possible. Codings shown below. For PA-RISC the ea, ec, and ed ¯elds are labeled e1, e2, and e3, respectively in the instruction descriptions. There is no label for the eb ¯eld in the instruction description of the add and yes it would make sense to use e0 instead of e1 but they didn't for whatever reason. opcode rs rt rd sa func MIPS64: 0 2 3 1 0 0x21 31 26 25 21 20 16 15 11 10 6 5 0 op rd op3 rs1 i asi rs2 SPARC V9: 2 1 0 2 0 0 3 31 30 29 25 24 19 18 14 13 13 12 5 4 0 OPCD r2 r1 c f ea eb ec ed d t PA-RISC 2: 2 3 2 0 0 01 1 0 00 0 1 0 5 6 10 11 15 16 18 19 19 20 21 22 22 23 23 24 25 26 26 27 31 (b) Identify the ¯eld or ¯elds in the SPARC add instruction which are the closest equivalent to MIPS' func ¯eld. -
Ross Technology RT6224K User Manual 1 (Pdf)
Full-service, independent repair center -~ ARTISAN® with experienced engineers and technicians on staff. TECHNOLOGY GROUP ~I We buy your excess, underutilized, and idle equipment along with credit for buybacks and trade-ins. Custom engineering Your definitive source so your equipment works exactly as you specify. for quality pre-owned • Critical and expedited services • Leasing / Rentals/ Demos equipment. • In stock/ Ready-to-ship • !TAR-certified secure asset solutions Expert team I Trust guarantee I 100% satisfaction Artisan Technology Group (217) 352-9330 | [email protected] | artisantg.com All trademarks, brand names, and brands appearing herein are the property o f their respective owners. Find the Ross Technology RT6224K-200/512S at our website: Click HERE 830-0016-03 Rev A 11/15/96 PRELIMINARY Colorado 4 RT6224K hyperSPARC CPU Module Features D Based on ROSS’ fifth-generation D SPARC compliant — Zero-wait-state, 512-Kbyte or hyperSPARC processor — SPARC Instruction Set Architec- 1-Mbyte 2nd-level cache — RT620D Central Processing Unit ture (ISA) Version 8 compliant — Demand-paged virtual memory (CPU) — Conforms to SPARC Reference management — RT626 Cache Controller, Memory MMU Architecture D Module design Management, and Tag Unit — Conforms to SPARC Level 2 MBus — MBus-standard form factor: 3.30” (CMTU) Module Specification (Revision 1.2) (8.34 cm) x 5.78” (14.67 cm) — Four (512-Kbyte) or eight D Dual-clock architecture — Provides CPU upgrade path at (1-Mbyte) RT628 Cache Data Units module level (CDUs) Ċ CPU scaleable up to -
SPARC Assembly Language Reference Manual
SPARC Assembly Language Reference Manual 2550 Garcia Avenue Mountain View, CA 94043 U.S.A. A Sun Microsystems, Inc. Business 1995 Sun Microsystems, Inc. 2550 Garcia Avenue, Mountain View, California 94043-1100 U.S.A. All rights reserved. This product or document is protected by copyright and distributed under licenses restricting its use, copying, distribution and decompilation. No part of this product or document may be reproduced in any form by any means without prior written authorization of Sun and its licensors, if any. Portions of this product may be derived from the UNIX® system, licensed from UNIX Systems Laboratories, Inc., a wholly owned subsidiary of Novell, Inc., and from the Berkeley 4.3 BSD system, licensed from the University of California. Third-party software, including font technology in this product, is protected by copyright and licensed from Sun’s Suppliers. RESTRICTED RIGHTS LEGEND: Use, duplication, or disclosure by the government is subject to restrictions as set forth in subparagraph (c)(1)(ii) of the Rights in Technical Data and Computer Software clause at DFARS 252.227-7013 and FAR 52.227-19. The product described in this manual may be protected by one or more U.S. patents, foreign patents, or pending applications. TRADEMARKS Sun, Sun Microsystems, the Sun logo, SunSoft, the SunSoft logo, Solaris, SunOS, OpenWindows, DeskSet, ONC, ONC+, and NFS are trademarks or registered trademarks of Sun Microsystems, Inc. in the United States and other countries. UNIX is a registered trademark in the United States and other countries, exclusively licensed through X/Open Company, Ltd. OPEN LOOK is a registered trademark of Novell, Inc. -
Day 2, 1640: Leveraging Opensparc
Leveraging OpenSPARC ESA Round Table 2006 on Next Generation Microprocessors for Space Applications G.Furano, L.Messina – TEC-EDD OpenSPARC T1 • The T1 is a new-from-the-ground-up SPARC microprocessor implementation that conforms to the UltraSPARC architecture 2005 specification and executes the full SPARC V9 instruction set. Sun has produced two previous multicore processors: UltraSPARC IV and UltraSPARC IV+, but UltraSPARC T1 is its first microprocessor that is both multicore and multithreaded. • The processor is available with 4, 6 or 8 CPU cores, each core able to handle four threads. Thus the processor is capable of processing up to 32 threads concurrently. • Designed to lower the energy consumption of server computers, the 8-cores CPU uses typically 72 W of power at 1.2 GHz. G.Furano, L.Messina – TEC-EDD 72W … 1.2 GHz … 90nm … • Is a cutting edge design, targeted for high-end servers. • NOT FOR SPACE USE • But, let’s see which are the potential spin-in … G.Furano, L.Messina – TEC-EDD Why OPEN ? On March 21, 2006, Sun made the UltraSPARC T1 processor design available under the GNU General Public License. The published information includes: • Verilog source code of the UltraSPARC T1 design, including verification suite and simulation models • ISA specification (UltraSPARC Architecture 2005) • The Solaris 10 OS simulation images • Diagnostics tests for OpenSPARC T1 • Scripts, open source and Sun internal tools needed to simulate the design and to do synthesis of the design • Scripts and documentation to help with FPGA implementation -
Solaris Powerpc Edition: Installing Solaris Software—May 1996 What Is a Profile
SolarisPowerPC Edition: Installing Solaris Software 2550 Garcia Avenue Mountain View, CA 94043 U.S.A. A Sun Microsystems, Inc. Business Copyright 1996 Sun Microsystems, Inc., 2550 Garcia Avenue, Mountain View, California 94043-1100 U.S.A. All rights reserved. This product or document is protected by copyright and distributed under licenses restricting its use, copying, distribution, and decompilation. No part of this product or document may be reproduced in any form by any means without prior written authorization of Sun and its licensors, if any. Portions of this product may be derived from the UNIX® system, licensed from Novell, Inc., and from the Berkeley 4.3 BSD system, licensed from the University of California. UNIX is a registered trademark in the United States and other countries and is exclusively licensed by X/Open Company Ltd. Third-party software, including font technology in this product, is protected by copyright and licensed from Sun’s suppliers. RESTRICTED RIGHTS LEGEND: Use, duplication, or disclosure by the government is subject to restrictions as set forth in subparagraph (c)(1)(ii) of the Rights in Technical Data and Computer Software clause at DFARS 252.227-7013 and FAR 52.227-19. Sun, Sun Microsystems, the Sun logo, Solaris, Solstice, SunOS, OpenWindows, ONC, NFS, DeskSet are trademarks or registered trademarks of Sun Microsystems, Inc. in the United States and other countries. All SPARC trademarks are used under license and are trademarks or registered trademarks of SPARC International, Inc. in the United States and other countries. Products bearing SPARC trademarks are based upon an architecture developed by Sun Microsystems, Inc. -
V850 Series Development Environment Pamphlet
To our customers, Old Company Name in Catalogs and Other Documents On April 1st, 2010, NEC Electronics Corporation merged with Renesas Technology Corporation, and Renesas Electronics Corporation took over all the business of both companies. Therefore, although the old company name remains in this document, it is a valid Renesas Electronics document. We appreciate your understanding. Renesas Electronics website: http://www.renesas.com April 1st, 2010 Renesas Electronics Corporation Issued by: Renesas Electronics Corporation (http://www.renesas.com) Send any inquiries to http://www.renesas.com/inquiry. Notice 1. All information included in this document is current as of the date this document is issued. Such information, however, is subject to change without any prior notice. Before purchasing or using any Renesas Electronics products listed herein, please confirm the latest product information with a Renesas Electronics sales office. Also, please pay regular and careful attention to additional and different information to be disclosed by Renesas Electronics such as that disclosed through our website. 2. Renesas Electronics does not assume any liability for infringement of patents, copyrights, or other intellectual property rights of third parties by or arising from the use of Renesas Electronics products or technical information described in this document. No license, express, implied or otherwise, is granted hereby under any patents, copyrights or other intellectual property rights of Renesas Electronics or others. 3. You should not alter, modify, copy, or otherwise misappropriate any Renesas Electronics product, whether in whole or in part. 4. Descriptions of circuits, software and other related information in this document are provided only to illustrate the operation of semiconductor products and application examples. -
A Soft Processor Microblaze-Based Embedded System for Cardiac Monitoring
(IJACSA) International Journal of Advanced Computer Science and Applications, Vol. 4, No. 9, 2013 A Soft Processor MicroBlaze-Based Embedded System for Cardiac Monitoring El Hassan El Mimouni Mohammed Karim University Sidi Mohammed Ben Abdellah University Sidi Mohammed Ben Abdellah Fès, Morocco Fès, Morocco Abstract—this paper aims to contribute to the efforts of recent years, and has become also an important way to assert design community to demonstrate the effectiveness of the state of the heart’s condition [5 - 9]. the art Field Programmable Gate Array (FPGA), in the embedded systems development, taking a case study in the II. SYSTEM OVERVIEW biomedical field. With this design approach, we have developed a We have designed and implemented a prototype of basic System on Chip (SoC) for cardiac monitoring based on the soft embedded system for cardiac monitoring, whose functional processor MicroBlaze and the Xilkernel Real Time Operating block diagram is shown in the figure 2; it exhibits a modular System (RTOS), both from Xilinx. The system permits the structure that facilitates the development and debugging. Thus, acquisition and the digitizing of the Electrocardiogram (ECG) analog signal, displaying heart rate on seven segments module it includes 2 main modules: and ECG on Video Graphics Adapter (VGA) screen, tracing the An analog module intended for acquiring and heart rate variability (HRV) tachogram, and communication conditioning of the analog ECG signal to make it with a Personal Computer (PC) via the serial port. We have used appropriate for use by the second digital module ; the MIT_BIH Database records to test and evaluate our implementation performance. -
Sparc Enterprise T5440 Server Architecture
SPARC ENTERPRISE T5440 SERVER ARCHITECTURE Unleashing UltraSPARC T2 Plus Processors with Innovative Multi-core Multi-thread Technology White Paper July 2009 TABLE OF CONTENTS THE ULTRASPARC T2 PLUS PROCESSOR 0 THE WORLD'S FIRST MASSIVELY THREADED SYSTEM ON A CHIP (SOC) 0 TAKING CHIP MULTITHREADED DESIGN TO THE NEXT LEVEL 1 ULTRASPARC T2 PLUS PROCESSOR ARCHITECTURE 3 SERVER ARCHITECTURE 8 SYSTEM-LEVEL ARCHITECTURE 8 CHASSIS DESIGN INNOVATIONS 13 ENTERPRISE-CLASS MANAGEMENT AND SOFTWARE 19 SYSTEM MANAGEMENT TECHNOLOGY 19 SCALABILITY AND SUPPORT FOR INNOVATIVE MULTITHREADING TECHNOLOGY21 CONCLUSION 28 0 The UltraSPARC T2 Plus Processors Chapter 1 The UltraSPARC T2 Plus Processors The UltraSPARC T2 and UltraSPARC T2 Plus processors are the industry’s first system on a chip (SoC), supplying the most cores and threads of any general-purpose processor available, and integrating all key system functions. The World's First Massively Threaded System on a Chip (SoC) The UltraSPARC T2 Plus processor eliminates the need for expensive custom hardware and software development by integrating computing, security, and I/O on to a single chip. Binary compatible with earlier UltraSPARC processors, no other processor delivers so much performance in so little space and with such small power requirements letting organizations rapidly scale the delivery of new network services with maximum efficiency and predictability. The UltraSPARC T2 Plus processor is shown in Figure 1. Figure 1. The UltraSPARC T2 Plus processor with CoolThreads technology 1 The UltraSPARC -
Performance Evaluation of FPGA Based Embedded ARM Processor
10.1109/ULTSYM.2013.0135 Performance Evaluation of FPGA based Embedded ARM Processor for Ultrasonic Imaging Spenser Gilliland, Pramod Govindan, Thomas Gonnot and Jafar Saniie Department of Electrical and Computer Engineering Illinois Institute of Technology, Chicago IL, U.S.A. Abstract- This study evaluates the performance of an FPGA based embedded ARM processor system to implement signal processing for ultrasonic imaging and nondestructive testing applications. FPGA based embedded processors possess many advantages including a reduced overall development time, increased performance, and the ability to perform hardware- software (HW/SW) co-design. This study examines the execution performance of split spectrum processing, chirplet signal decomposition, Wigner-Ville distributions and short time Fourier transform implementations, on two embedded processing platforms: a Xilinx Virtex-5 FPGA with embedded MicroBlaze processor and a Xilinx Zynq FPGA with embedded ARM processor. Overall, the Xilinx Zynq FPGA significantly outperforms the Virtex-5 based system in software applications I. INTRODUCTION Figure 1. RUSH SoC setup Generally, ultrasonic imaging applications use personal computers or hand held devices. As these devices are not frequency diverse flaw detection [1], parametric echo specifically designed for efficiently executing estimation [2], and joint time-frequency distribution [3]) on computationally intensive ultrasonic signal processing the RUSH platform using a Xilinx Virtex-5 FPGA with an algorithms, the performance of these applications can be embedded soft-core MicroBlaze processor [4,5] and a improved by executing the algorithms using a dedicated Xilinx Zynq 7020 FPGA with an embedded ARM processor embedded system-on-chip (SoC) hardware. However, [6,7] as shown in Figure 2. porting these applications onto an embedded system requires deep knowledge of the processor architecture and RUSH embedded software development tools. -
Opensparc – an Open Platform for Hardware Reliability Experimentation
OpenSPARC – An Open Platform for Hardware Reliability Experimentation Ishwar Parulkar and Alan Wood Sun Microsystems, Inc. James C. Hoe and Babak Falsafi Carnegie Mellon University Sarita V. Adve and Josep Torrellas University of Illinois at Urbana- Champaign Subhasish Mitra Stanford University IEEE SELSE 4 - March 26, 2008 www.OpenSPARC.net Outline 1.Chip Multi-threading (CMT) 2.OpenSPARC T2 and T1 processors 3.Reliability in OpenSPARC processors 4.What is available in OpenSPARC 5.Current university research using OpenSPARC 6.Future research directions IEEE SELSE 4 – March 26, 2008 2 www.OpenSPARC.net World's First 64-bit Open Source Microprocessor OpenSPARC.net Governed by GPLv2 Complete processor architecture & implementation Register Transfer Level (RTL) Hypervisor API Verification suite and architectural models Simulation model for operating system bringup on s/w IEEE SELSE 4 – March 26, 2008 3 www.OpenSPARC.net Chip Multithreading (CMT) Instruction- Low Low Low Medium Low High level Parallelism Thread-level Parallelism High High High High High Instruction/Data Large Large Medium Large Large Working Set Data Sharing Low Medium High Medium High Medium IEEE SELSE 4 – March 26, 2008 4 www.OpenSPARC.net Memory Bottleneck Relative Performance 10000 CPU Frequency DRAM Speeds 1000 2 Years 100 Every Gap 2x -- CPU 6 10 -- 2x Every DRAM Years 1 1980 1985 1990 1995 2000 2005 Source: Sun World Wide Analyst Conference Feb. 25, 2003 IEEE SELSE 4 – March 26, 2008 5 www.OpenSPARC.net Single Threading HURRY Up to 85% Cycles Waiting for Memory