Engineering Data Catalog
Total Page:16
File Type:pdf, Size:1020Kb
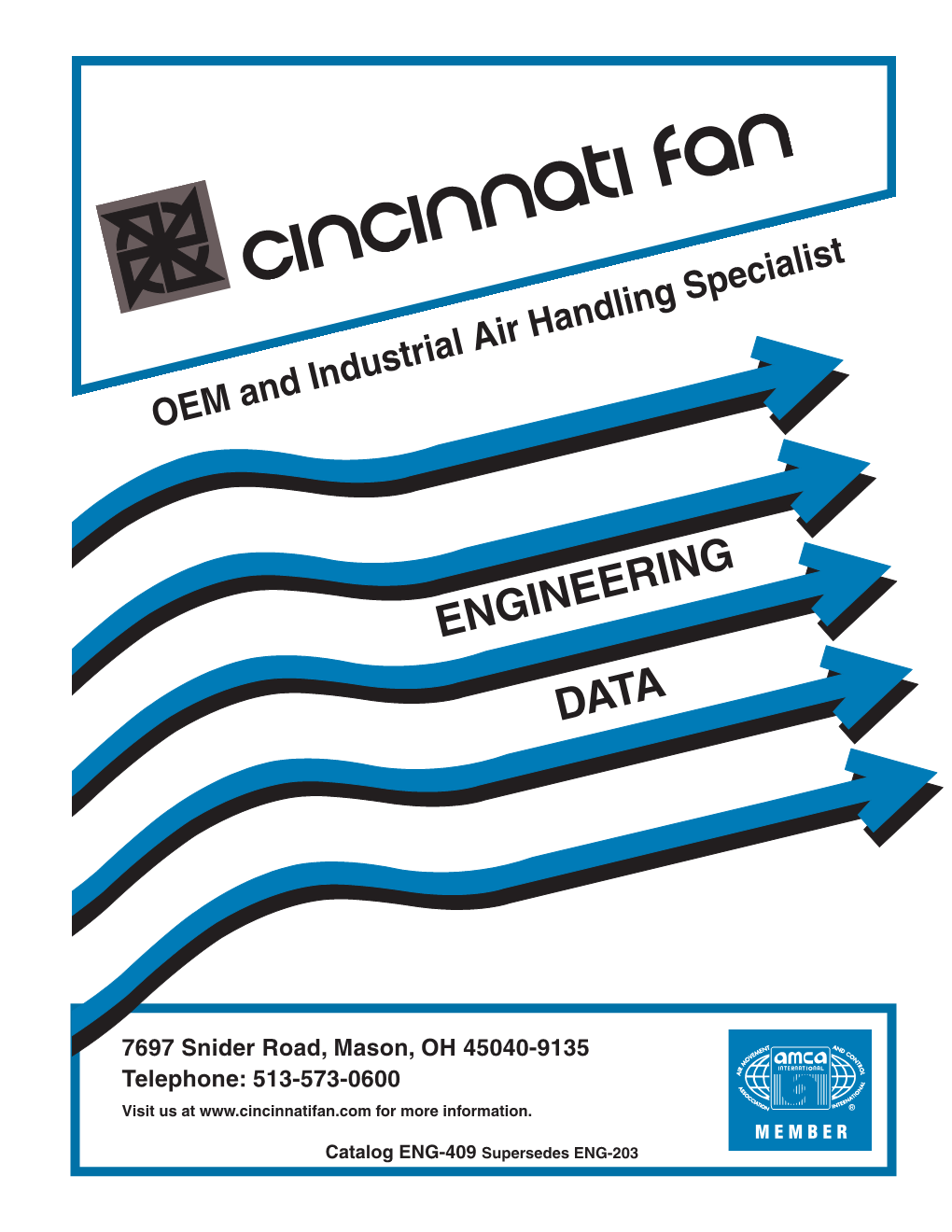
Load more
Recommended publications
-
Locomotive Dedication Ceremony
The American Society of Mechanical Engineers REGIONAL MECHANICAL ENGINEERING HERITAGE COLLECTION LOCOMOTIVE DEDICATION CEREMONY Kenefick Park • Omaha, Nebraska June 7, 1994 Locomotives 4023 and 6900 are examples of the world’s largest motive power in the steam and diesel eras. These locomotives are on permanent display at Kenefick Park, which was established in 1989 in honor of noted former Union Pacific chairman, John C. Kenefick. The 4023 was one of twenty-five famous “Big Boy” type simple articulated locomotives Locomotive 4023 was a feature display lauded in the industry and press as the highest horsepower, heaviest and longest steam at the Omaha Shops locomotives ever built, developing seven thousand horsepower at their seventy miles until being moved to per hour design speed. Kenefick Park. 2 World’s largest The Big Boy type was designed at the Omaha headquarters of Union Pacific under the single unit diesel personal direction of the road’s noted mechanical head, Otto Jabelmann. The original locomotives required four axle trucks to distribute twenty locomotives of this type were built by American Locomotive Company in their heavy weight and Schenectady, New York, in the fall of 1941. They were built in preparation for the nation’s keep within track probable entry into World War II because no proven diesel freight locomotive was yet loading limits. in production. These 4-8-8-4 type locomotives were specifically designed to haul fast, heavy eastbound freight trains between Ogden, Utah, and Green River, Wyoming, over the 1.14 percent eastbound grade. The 4023 was one of five additional units built in 1944 under govern- ment authority in preparation for a twenty-five percent increase in traffic due to the shift from European to Pacific war operations. -
Mean Value Modelling of a Poppet Valve EGR-System
Mean value modelling of a poppet valve EGR-system Master’s thesis performed in Vehicular Systems by Claes Ericson Reg nr: LiTH-ISY-EX-3543-2004 14th June 2004 Mean value modelling of a poppet valve EGR-system Master’s thesis performed in Vehicular Systems, Dept. of Electrical Engineering at Linkopings¨ universitet by Claes Ericson Reg nr: LiTH-ISY-EX-3543-2004 Supervisor: Jesper Ritzen,´ M.Sc. Scania CV AB Mattias Nyberg, Ph.D. Scania CV AB Johan Wahlstrom,¨ M.Sc. Linkopings¨ universitet Examiner: Associate Professor Lars Eriksson Linkopings¨ universitet Linkoping,¨ 14th June 2004 Avdelning, Institution Datum Division, Department Date Vehicular Systems, Dept. of Electrical Engineering 14th June 2004 581 83 Linkoping¨ Sprak˚ Rapporttyp ISBN Language Report category — ¤ Svenska/Swedish ¤ Licentiatavhandling ISRN ¤ Engelska/English ££ ¤ Examensarbete LITH-ISY-EX-3543-2004 ¤ C-uppsats Serietitel och serienummer ISSN ¤ D-uppsats Title of series, numbering — ¤ ¤ Ovrig¨ rapport ¤ URL for¨ elektronisk version http://www.vehicular.isy.liu.se http://www.ep.liu.se/exjobb/isy/2004/3543/ Titel Medelvardesmodellering¨ av EGR-system med tallriksventil Title Mean value modelling of a poppet valve EGR-system Forfattare¨ Claes Ericson Author Sammanfattning Abstract Because of new emission and on board diagnostics legislations, heavy truck manufacturers are facing new challenges when it comes to improving the en- gines and the control software. Accurate and real time executable engine models are essential in this work. One successful way of lowering the NOx emissions is to use Exhaust Gas Recirculation (EGR). The objective of this thesis is to create a mean value model for Scania’s next generation EGR system consisting of a poppet valve and a two stage cooler. -
117001 Tiertwo Cp6 14.Pdf
This is what it takes to be a PRO. Performance enhancing features like a heavy-duty air cleaner, forged-steel crankshaft, electronic ignition and cast-iron cylinder liner. KOHLER® Command PRO® is the standard for professional-grade power and performance. COURAGE XT COMMAND PRO® DEPENDABLE OPERATI COURAGE SINGLE ON • Quad-Clean ™ all-season four-stage cyclonic air filter – effective COURAGE TWINS engine protection for tough-and-dirty conditions. COURAGE XT • Protects from airborne contaminants that can easily clog COURAGE PRO TWINS COMMAND PRO® traditional air filters. LoNGER RUN TIMES COURAGE SINGLE • Large-capacity fuel tank means more time working, less time filling. COURAGE XT COURAGE TWINS • Electronic ignition and an advanced combustion system design help COMMAND PRO® reduce fuel consumption. COURAGE PRO TWINS COURAGE XT EASIER REPOWERING COURAGE SINGLE COMMAND PRO® • Power or repower your equipment without expensive modifications. COURAGE TWINS ALL-WEATHER P COURAGE SINGLE ERFORMANCE COURAGE PRO TWINS • Quad-Clean air filter reconfigures in seconds to recycle engine heat. COURAGE XT COURAGE TWINS • Command PRO starts effortlessly in all weather conditions, from COMMAND PRO® 0 to 110 degrees. COURAGE PRO TWINS BUILT TO LAST COURAGE SINGLE • Forged-steel crankshafts and tough Stellite ®-faced exhaust valves with COURAGE TWINS Tufftride ®-coated stems and cast-iron cylinder bores. • Oil Sentry ™ automatically shuts engine down in low-oil conditions. COURAGE PRO TWINS 6-HP HORIZONTAL-SHAFT ENGINES 6-HP HORIZONTAL-SHAFT ENGINES TOP VIEW -
Engineering Info
Engineering Info To Find Given Formula 1. Basic Geometry Circumference of a circle Diameter Circumference = 3.1416 x diameter Diameter of a circle Circumference Diameter = Circumference / 3.1416 2. Motion Ratio High Speed & Low Speed Ratio = RPM High RPM Low RPM Feet per Minute of Belt RPM = FPM and Pulley Diameter .262 x diameter in inches Belt Speed Feet per Minute RPM & Pulley Diameter FPM = .262 x RPM x diameter in inches Ratio Teeth of Pinion & Teeth of Gear Ratio = Teeth of Gear Teeth of Pinion Ratio Two Sprockets or Pulley Diameters Ratio = Diameter Driven Diameter Driver 3. Force - Work - Torque Force (F) Torque & Diameter F = Torque x 2 Diameter Torque (T) Force & Diameter T = ( F x Diameter) / 2 Diameter (Dia.) Torque & Force Diameter = (2 x T) / F Work Force & Distance Work = Force x Distance Chain Pull Torque & Diameter Pull = (T x 2) / Diameter 4. Power Chain Pull Horsepower & Speed (FPM) Pull = (33,000 x HP)/ Speed Horsepower Force & Speed (FPM) HP = (Force x Speed) / 33,000 Horsepower RPM & Torque (#in.) HP = (Torque x RPM) / 63025 Horsepower RPM & Torque (#ft.) HP = (Torque x RPM) / 5250 Torque HP & RPM T #in. = (63025 x HP) / RPM Torque HP & RPM T #ft. = (5250 x HP) / RPM 5. Inertia Accelerating Torque (#ft.) WK2, RMP, Time T = WK2 x RPM 308 x Time Accelerating Time (Sec.) Torque, WK2, RPM t = WK2 x RPM 308 x Torque WK2 at motor WK2 at Load, Ratio WK2 Motor = WK2 Ratio2 6. Gearing Gearset Centers Pd Gear & Pd Pinion Centers = ( PdG + PdP ) / 2 Pitch Diameter No. of Teeth & Diametral Pitch Pd = Teeth / DP Pitch Diameter No. -
History of a Forgotten Engine Alex Cannella, News Editor
POWER PLAY History of a Forgotten Engine Alex Cannella, News Editor In 2017, there’s more variety to be found un- der the hood of a car than ever. Electric, hybrid and internal combustion engines all sit next to a range of trans- mission types, creating an ever-increasingly complex evolu- tionary web of technology choices for what we put into our automobiles. But every evolutionary tree has a few dead end branches that ended up never going anywhere. One such branch has an interesting and somewhat storied history, but it’s a history that’s been largely forgotten outside of columns describing quirky engineering marvels like this one. The sleeve-valve engine was an invention that came at the turn of the 20th century and saw scattered use between its inception and World War II. But afterwards, it fell into obscurity, outpaced (By Andy Dingley (scanner) - Scan from The Autocar (Ninth edition, circa 1919) Autocar Handbook, London: Iliffe & Sons., pp. p. 38,fig. 21, Public Domain, by the poppet valves we use in engines today that, ironically, https://commons.wikimedia.org/w/index.php?curid=8771152) it was initially developed to replace. Back when the sleeve-valve engine was first developed, through the economic downturn, and by the time the econ- the poppet valves in internal combustion engines were ex- omy was looking up again, poppet valve engines had caught tremely noisy contraptions, a concern that likely sounds fa- up to the sleeve-valve and were quickly becoming just as miliar to anyone in the automotive industry today. Charles quiet and efficient. -
MODULE 11: GLOSSARY and CONVERSIONS Cell Engines
Hydrogen Fuel MODULE 11: GLOSSARY AND CONVERSIONS Cell Engines CONTENTS 11.1 GLOSSARY.......................................................................................................... 11-1 11.2 MEASUREMENT SYSTEMS .................................................................................. 11-31 11.3 CONVERSION TABLE .......................................................................................... 11-33 Hydrogen Fuel Cell Engines and Related Technologies: Rev 0, December 2001 Hydrogen Fuel MODULE 11: GLOSSARY AND CONVERSIONS Cell Engines OBJECTIVES This module is for reference only. Hydrogen Fuel Cell Engines and Related Technologies: Rev 0, December 2001 PAGE 11-1 Hydrogen Fuel Cell Engines MODULE 11: GLOSSARY AND CONVERSIONS 11.1 Glossary This glossary covers words, phrases, and acronyms that are used with fuel cell engines and hydrogen fueled vehicles. Some words may have different meanings when used in other contexts. There are variations in the use of periods and capitalization for abbrevia- tions, acronyms and standard measures. The terms in this glossary are pre- sented without periods. ABNORMAL COMBUSTION – Combustion in which knock, pre-ignition, run- on or surface ignition occurs; combustion that does not proceed in the nor- mal way (where the flame front is initiated by the spark and proceeds throughout the combustion chamber smoothly and without detonation). ABSOLUTE PRESSURE – Pressure shown on the pressure gauge plus at- mospheric pressure (psia). At sea level atmospheric pressure is 14.7 psia. Use absolute pressure in compressor calculations and when using the ideal gas law. See also psi and psig. ABSOLUTE TEMPERATURE – Temperature scale with absolute zero as the zero of the scale. In standard, the absolute temperature is the temperature in ºF plus 460, or in metric it is the temperature in ºC plus 273. Absolute zero is referred to as Rankine or r, and in metric as Kelvin or K. -
Jennings: Two-Stroke Tuner's Handbook
Two-Stroke TUNER’S HANDBOOK By Gordon Jennings Illustrations by the author Copyright © 1973 by Gordon Jennings Compiled for reprint © 2007 by Ken i PREFACE Many years have passed since Gordon Jennings first published this manual. Its 2007 and although there have been huge technological changes the basics are still the basics. There is a huge interest in vintage snowmobiles and their “simple” two stroke power plants of yesteryear. There is a wealth of knowledge contained in this manual. Let’s journey back to 1973 and read the book that was the two stroke bible of that era. Decades have passed since I hung around with John and Jim. John and I worked for the same corporation and I found a 500 triple Kawasaki for him at a reasonable price. He converted it into a drag bike, modified the engine completely and added mikuni carbs and tuned pipes. John borrowed Jim’s copy of the ‘Two Stoke Tuner’s Handbook” and used it and tips from “Fast by Gast” to create one fast bike. John kept his 500 until he retired and moved to the coast in 2005. The whereabouts of Wild Jim, his 750 Kawasaki drag bike and the only copy of ‘Two Stoke Tuner’s Handbook” that I have ever seen is a complete mystery. I recently acquired a 1980 Polaris TXL and am digging into the inner workings of the engine. I wanted a copy of this manual but wasn’t willing to wait for a copy to show up on EBay. Happily, a search of the internet finally hit on a Word version of the manual. -
Feeling Joules and Watts
FEELING JOULES AND WATTS OVERVIEW & PURPOSE Power was originally measured in horsepower – literally the number of horses it took to do a particular amount of work. James Watt developed this term in the 18th century to compare the output of steam engines to the power of draft horses. This allowed people who used horses for work on a regular basis to have an intuitive understanding of power. 1 horsepower is about 746 watts. In this lab, you’ll learn about energy, work and power – including your own capacity to do work. Energy is the ability to do work. Without energy, nothing would grow, move, or change. Work is using a force to move something over some distance. work = force x distance Energy and work are measured in joules. One joule equals the work done (or energy used) when a force of one newton moves an object one meter. One newton equals the force required to accelerate one kilogram one meter per second squared. How much energy would it take to lift a can of soda (weighing 4 newtons) up two meters? work = force x distance = 4N x 2m = 8 joules Whether you lift the can of soda quickly or slowly, you are doing 8 joules of work (using 8 joules of energy). It’s often helpful, though, to measure how quickly we are doing work (or using energy). Power is the amount of work (or energy used) in a given amount of time. http://www.rdcep.org/demo-collection page 1 work power = time Power is measured in watts. One watt equals one joule per second. -
Section 2.3 – Linear and Angular Velocities
Section 2.3 – Linear and Angular Velocities The most intuitive measure of the rate at which the rider is traveling around the wheel is what we call linear velocity. Another way to specify how fast the rider is traveling around the wheel is with what we call angular velocity. Linear Speed Definition If P is a point on a circle of radius r, and P moves a distance s on the circumference of the circle in an amount of time t, then the linear velocity, v, of P is given by the formula speed distance time v s t Example A point on a circle travels 5 cm in 2 sec. Find the linear velocity of the point. Solution Given: s = 5cm t = 2 sec v s 5 cm t 2 sec 2.5 cm/ sec 21 Angular Speed Definition If P is a point moving with uniform circular motion on a circle of radius r, and the line from the center of the circle through P sweeps out a central angle in an amount of time t, then the angular velocity, (omega), of P is given by the formula where is measured in radians t Example A point on a circle rotates through 3 radians in 3 sec. Give the angular velocity of the point. 4 Solution Given: = rad t = 3sec 3 rad 4 3 sec rad/ sec 4 Example A bicycle wheel with a radius of 13.0 in. turns with an angular velocity of 3 radians per seconds. Find the distance traveled by a point on the bicycle tire in 1 minute. -
AP-42, Vol. I, 3.3: Gasoline and Diesel Industrial Engines
3.3 Gasoline And Diesel Industrial Engines 3.3.1 General The engine category addressed by this section covers a wide variety of industrial applications of both gasoline and diesel internal combustion (IC) engines such as aerial lifts, fork lifts, mobile refrigeration units, generators, pumps, industrial sweepers/scrubbers, material handling equipment (such as conveyors), and portable well-drilling equipment. The three primary fuels for reciprocating IC engines are gasoline, diesel fuel oil (No.2), and natural gas. Gasoline is used primarily for mobile and portable engines. Diesel fuel oil is the most versatile fuel and is used in IC engines of all sizes. The rated power of these engines covers a rather substantial range, up to 250 horsepower (hp) for gasoline engines and up to 600 hp for diesel engines. (Diesel engines greater than 600 hp are covered in Section 3.4, "Large Stationary Diesel And All Stationary Dual-fuel Engines".) Understandably, substantial differences in engine duty cycles exist. It was necessary, therefore, to make reasonable assumptions concerning usage in order to formulate some of the emission factors. 3.3.2 Process Description All reciprocating IC engines operate by the same basic process. A combustible mixture is first compressed in a small volume between the head of a piston and its surrounding cylinder. The mixture is then ignited, and the resulting high-pressure products of combustion push the piston through the cylinder. This movement is converted from linear to rotary motion by a crankshaft. The piston returns, pushing out exhaust gases, and the cycle is repeated. There are 2 methods used for stationary reciprocating IC engines: compression ignition (CI) and spark ignition (SI). -
Energy and Power Units and Conversions
Energy and Power Units and Conversions Basic Energy Units 1 Joule (J) = Newton meter × 1 calorie (cal)= 4.18 J = energy required to raise the temperature of 1 gram of water by 1◦C 1 Btu = 1055 Joules = 778 ft-lb = 252 calories = energy required to raise the temperature 1 lb of water by 1◦F 1 ft-lb = 1.356 Joules = 0.33 calories 1 physiological calorie = 1000 cal = 1 kilocal = 1 Cal 1 quad = 1015Btu 1 megaJoule (MJ) = 106 Joules = 948 Btu, 1 gigaJoule (GJ) = 109 Joules = 948; 000 Btu 1 electron-Volt (eV) = 1:6 10 19 J × − 1 therm = 100,000 Btu Basic Power Units 1 Watt (W) = 1 Joule/s = 3:41 Btu/hr 1 kiloWatt (kW) = 103 Watt = 3:41 103 Btu/hr × 1 megaWatt (MW) = 106 Watt = 3:41 106 Btu/hr × 1 gigaWatt (GW) = 109 Watt = 3:41 109 Btu/hr × 1 horse-power (hp) = 2545 Btu/hr = 746 Watts Other Energy Units 1 horsepower-hour (hp-hr) = 2:68 106 Joules = 0.746 kwh × 1 watt-hour (Wh) = 3:6 103 sec 1 Joule/sec = 3:6 103 J = 3.413 Btu × × × 1 kilowatt-hour (kWh) = 3:6 106 Joules = 3413 Btu × 1 megaton of TNT = 4:2 1015 J × Energy and Power Values solar constant = 1400W=m2 1 barrel (bbl) crude oil (42 gals) = 5:8 106 Btu = 9:12 109 J × × 1 standard cubic foot natural gas = 1000 Btu 1 gal gasoline = 1:24 105 Btu × 1 Physics 313 OSU 3 April 2001 1 ton coal 3 106Btu ≈ × 1 ton 235U (fissioned) = 70 1012 Btu × 1 million bbl oil/day = 5:8 1012 Btu/day =2:1 1015Btu/yr = 2.1 quad/yr × × 1 million bbl oil/day = 80 million tons of coal/year = 1/5 ton of uranium oxide/year One million Btu approximately equals 90 pounds of coal 125 pounds of dry wood 8 gallons of -
Internal Combustion Engines Collection of Stationary
ASME International THE COOLSPRING POWER MUSEUM COLLECTION OF STATIONARY INTERNAL COMBUSTION ENGINES MECHANICAL ENGINEERING HERITAGE COLLECTION Coolspring Power Museum Coolspring, Pennsylvania June 16, 2001 The Coolspring Power Museu nternal combustion engines revolutionized the world I around the turn of th 20th century in much the same way that steam engines did a century before. One has only to imagine a coal-fired, steam-powered, air- plane to realize how important internal combustion was to the industrialized world. While the early gas engines were more expensive than the equivalent steam engines, they did not require a boiler and were cheap- er to operate. The Coolspring Power Museum collection documents the early history of the internal- combustion revolution. Almost all of the critical components of hundreds of innovations that 1897 Charter today’s engines have their ori- are no longer used). Some of Gas Engine gins in the period represented the engines represent real engi- by the collection (as well as neering progress; others are more the product of inventive minds avoiding previous patents; but all tell a story. There are few duplications in the collection and only a couple of manufacturers are represent- ed by more than one or two examples. The Coolspring Power Museum contains the largest collection of historically signifi- cant, early internal combustion engines in the country, if not the world. With the exception of a few items in the collection that 2 were driven by the engines, m Collection such as compressors, pumps, and generators, and a few steam and hot air engines shown for comparison purposes, the collection contains only internal combustion engines.