Holographic Optical Elements and Their Applications in Waveguide Display Technologies
Total Page:16
File Type:pdf, Size:1020Kb
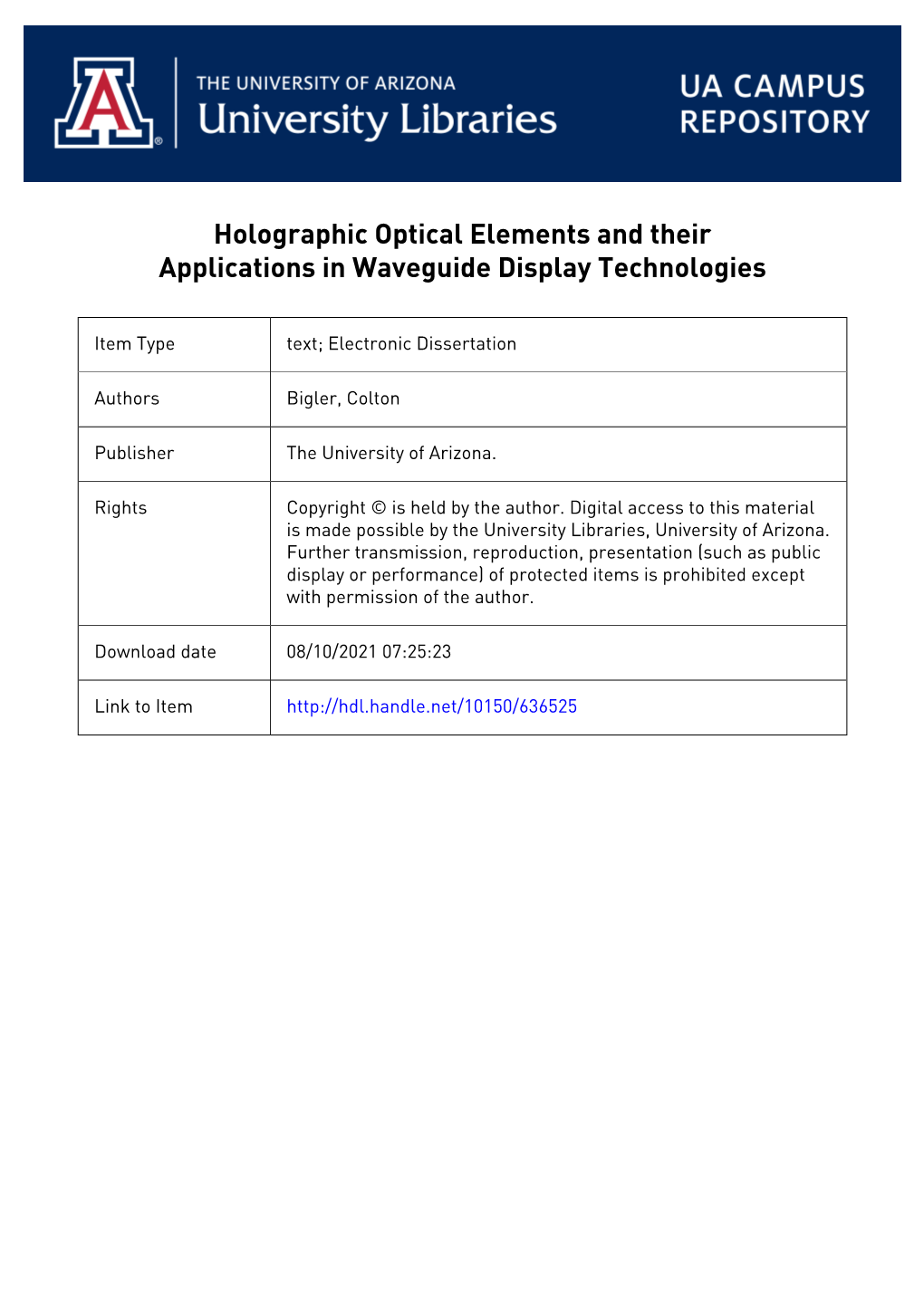
Load more
Recommended publications
-
The Artistic & Scientific World in 8K Super Hi-Vision
17th International Display Workshops 2010 (IDW 2010) Fukuoka, Japan 1-3 December 2010 Volume 1 of 3 ISBN: 978-1-61782-701-3 ISSN: 1883-2490 Printed from e-media with permission by: Curran Associates, Inc. 57 Morehouse Lane Red Hook, NY 12571 Some format issues inherent in the e-media version may also appear in this print version. Copyright© (2010) by the Society for Information Display All rights reserved. Printed by Curran Associates, Inc. (2012) For permission requests, please contact the Society for Information Display at the address below. Society for Information Display 1475 S. Bascom Ave. Suite 114 Campbell, California 95008-4006 Phone: (408) 879-3901 Fax: (408) 879-3833 or (408) 516-8306 [email protected] Additional copies of this publication are available from: Curran Associates, Inc. 57 Morehouse Lane Red Hook, NY 12571 USA Phone: 845-758-0400 Fax: 845-758-2634 Email: [email protected] Web: www.proceedings.com TABLE OF CONTENTS VOLUME 1 KEYNOTE ADDRESS The Artistic & Scientific World in 8K Super Hi-Vision.................................................................................................................................1 Yoichiro Kawaguchi INVITED ADDRESS TAOS-TFTs : History and Perspective............................................................................................................................................................5 Hideo Hosono LCT1: PHOTO ALIGNMENT TECHNOLOGY The UV2A Technology for Large Size LCD-TV Panels .................................................................................................................................9 -
Holographic Optics for Thin and Lightweight Virtual Reality
Holographic Optics for Thin and Lightweight Virtual Reality ANDREW MAIMONE, Facebook Reality Labs JUNREN WANG, Facebook Reality Labs Fig. 1. Left: Photo of full color holographic display in benchtop form factor. Center: Prototype VR display in sunglasses-like form factor with display thickness of 8.9 mm. Driving electronics and light sources are external. Right: Photo of content displayed on prototype in center image. Car scenes by komba/Shutterstock. We present a class of display designs combining holographic optics, direc- small text near the limit of human visual acuity. This use case also tional backlighting, laser illumination, and polarization-based optical folding brings VR out of the home and in to work and public spaces where to achieve thin, lightweight, and high performance near-eye displays for socially acceptable sunglasses and eyeglasses form factors prevail. virtual reality. Several design alternatives are proposed, compared, and ex- VR has made good progress in the past few years, and entirely perimentally validated as prototypes. Using only thin, flat films as optical self-contained head-worn systems are now commercially available. components, we demonstrate VR displays with thicknesses of less than 9 However, current headsets still have box-like form factors and pro- mm, fields of view of over 90◦ horizontally, and form factors approach- ing sunglasses. In a benchtop form factor, we also demonstrate a full color vide only a fraction of the resolution of the human eye. Emerging display using wavelength-multiplexed holographic lenses that uses laser optical design techniques, such as polarization-based optical folding, illumination to provide a large gamut and highly saturated color. -
A Review and Selective Analysis of 3D Display Technologies for Anatomical Education
University of Central Florida STARS Electronic Theses and Dissertations, 2004-2019 2018 A Review and Selective Analysis of 3D Display Technologies for Anatomical Education Matthew Hackett University of Central Florida Part of the Anatomy Commons Find similar works at: https://stars.library.ucf.edu/etd University of Central Florida Libraries http://library.ucf.edu This Doctoral Dissertation (Open Access) is brought to you for free and open access by STARS. It has been accepted for inclusion in Electronic Theses and Dissertations, 2004-2019 by an authorized administrator of STARS. For more information, please contact [email protected]. STARS Citation Hackett, Matthew, "A Review and Selective Analysis of 3D Display Technologies for Anatomical Education" (2018). Electronic Theses and Dissertations, 2004-2019. 6408. https://stars.library.ucf.edu/etd/6408 A REVIEW AND SELECTIVE ANALYSIS OF 3D DISPLAY TECHNOLOGIES FOR ANATOMICAL EDUCATION by: MATTHEW G. HACKETT BSE University of Central Florida 2007, MSE University of Florida 2009, MS University of Central Florida 2012 A dissertation submitted in partial fulfillment of the requirements for the degree of Doctor of Philosophy in the Modeling and Simulation program in the College of Engineering and Computer Science at the University of Central Florida Orlando, Florida Summer Term 2018 Major Professor: Michael Proctor ©2018 Matthew Hackett ii ABSTRACT The study of anatomy is complex and difficult for students in both graduate and undergraduate education. Researchers have attempted to improve anatomical education with the inclusion of three-dimensional visualization, with the prevailing finding that 3D is beneficial to students. However, there is limited research on the relative efficacy of different 3D modalities, including monoscopic, stereoscopic, and autostereoscopic displays. -
Advance Program 2018 Display Week International Symposium
ADVANCE PROGRAM 2018 DISPLAY WEEK INTERNATIONAL SYMPOSIUM May 22-25, 2018 (Tuesday – Friday) Los Angeles Convention Center Los Angeles, California, US Session 1: Annual SID Business Meeting Tuesday, May 22 / 8:00 – 8:20 am / Concourse Hall 151-153 Session 2: Opening Remarks / Keynote Addresses Tuesday, May 22 / 8:20 – 10:20 am / Concourse Hall 151-153 Chair: Cheng Chen, Apple, Inc., Cupertino, CA, US 2.1: Keynote Address 1: Deqiang Zhang, Visionox 2.2: Keynote Address 2: Douglas Lanman, Oculus 2.3: Keynote Address 3: Hiroshi Amano, Nagoya University Session 3: AR/VR I: Display Systems (AI and AR & VR / Display Systems / Emerging Technologies and Applications) Tuesday, May 22, 2018 / 11:10 am - 12:30 pm / Room 515A Chair: David Eccles, Rockwell Collins Co-Chair: Vincent Gu, Apple, Inc. 3.1: Invited Paper: VR Standards and Guidelines Matthew Brennesholtz, Brennesholtz Consulting, Pleasantville, NY, US 3.2: Distinguished Paper: An 18 Mpixel 4.3-in. 1443-ppi 120-Hz OLED Display for Wide-Field-of-View High-Acuity Head-Mounted Displays Carlin Vieri, Google LLC, Mountain View, CA, US 3.3: Distinguished Student Paper: Resolution-Enhanced Light-Field Near-to-Eye Display Using E-Shifting with an Birefringent Plate Kuei-En Peng, National Chiao Tung University, Hsinchu, Taiwan, ROC 3.4: Doubling the Pixel Density of Near-to-Eye Displays Tao Zhan, College of Optics and Photonics, University of Central Florida, Orlando, FL, US 3.5: RGB Superluminescent Diodes for AR Microdisplays Marco Rossetti, Exalos AG, Schlieren, Switzerland Session 4: Quantum-Dot -
State-Of-The-Art in Holography and Auto-Stereoscopic Displays
State-of-the-art in holography and auto-stereoscopic displays Daniel Jönsson <Ersätt med egen bild> 2019-05-13 Contents Introduction .................................................................................................................................................. 3 Auto-stereoscopic displays ........................................................................................................................... 5 Two-View Autostereoscopic Displays ....................................................................................................... 5 Multi-view Autostereoscopic Displays ...................................................................................................... 7 Light Field Displays .................................................................................................................................. 10 Market ......................................................................................................................................................... 14 Display panels ......................................................................................................................................... 14 AR ............................................................................................................................................................ 14 Application Fields ........................................................................................................................................ 15 Companies ................................................................................................................................................. -
Towards Mobile Embodied 3D Avatar As Telepresence Vehicle
Towards Mobile Embodied 3D Avatar as Telepresence Vehicle Yutaka Tokuda1, Atsushi Hiyama2, Takahiro Miura2, Tomohiro Tanikawa2, and Michitaka Hirose2 1 Graduate School of Engineering, The University of Tokyo, 4-6-1, Komaba, Meguro-ku, Tokyo 153-8904, Japan 2 Graduate School of Information Science and Technology, The University of Tokyo, 7-3-1, Hongo, Bunkyo-ku, Tokyo 113-8656, Japan {ytokuda,atsushi,miu,tani,hirose}@cyber.t.u-tokyo.ac.jp Abstract. In this paper, we present mobile embodied 3D avatar to shift a rich experience of avatar from a virtual world to our real life with a new style of te- lepresence. Conventional telepresence research have focused on the exact re- creation of face-to-face communication at a fixed position in a specialized room, so there have been much less research on a life-sized mobile telepresence system despite many off-the-shelf mobile telepresence robots available. We propose various scalable holographic displays to visualize a life-sized avatar in an actual life. In addition, we introduce architecture to control embodied avatar according to user’s intention by extending popular architecture for a multimodal virtual human, namely SAIBA. Our primitive prototype system was tested with 5 simple avatar animations to embody with a wheeled platform robot and a life- sized transparent holographic display and proved realistic avatar’s movement complying user’s intention and the situation at the remote location of avatar. Keywords: interaction techniques, avatar, telepresence, telework, mobility, transparent display, -
Holographic Three-Dimensional Virtual Reality and Augmented Reality Display Based on 4K-Spatial Light Modulators
applied sciences Article Holographic Three-Dimensional Virtual Reality and Augmented Reality Display Based on 4K-Spatial Light Modulators Hongyue Gao †, Fan Xu † , Jicheng Liu *,†, Zehang Dai , Wen Zhou , Suna Li and Yingjie Yu and Huadong Zheng Ultra-precision Optoelectronic Metrology and Information Display Technologies Research Center, Department of Precision Mechanical Engineering, School of Mechatronic Engineering and Automation, Shanghai University, Shanghai 200072, China; [email protected] (H.G.); [email protected] (F.X.); [email protected] (Z.D.); [email protected] (W.Z.); [email protected] (S.L.); [email protected] (Y.Y.); [email protected] (H.Z.) * Correspondence: [email protected] † These authors contributed equally to this work. Received: 11 January 2019; Accepted: 11 March 2019; Published: 20 March 2019 Abstract: In this paper, we propose a holographic three-dimensional (3D) head-mounted display based on 4K-spatial light modulators (SLMs). This work is to overcome the limitation of stereoscopic 3D virtual reality and augmented reality head-mounted display. We build and compare two systems using 2K and 4K SLMs with pixel pitches 8.1 µm and 3.74 µm, respectively. One is a monocular system for each eye, and the other is a binocular system using two tiled SLMs for two eyes. The viewing angle of the holographic head-mounted 3D display is enlarged from 3.8◦ to 16.4◦ by SLM tiling, which demonstrates potential applications of true 3D displays in virtual reality and augmented reality. Keywords: holography; holographic display; digital holography; virtual reality 1. Introduction Virtual reality (VR) and augmented reality (AR) have been hot topics recently, and 3D technology is an important part of VR technology [1]. -
3D Display System
3D Display System [email protected] 3D Display Human Visual System 3D Display Systems • Stereoscopic display • Autostereoscopic display • Holographic display Stereo Disparity 2 [email protected] 5/7/2020 Classification of 3D Display Glasses Non-glasses Stereoscopic display Autostereoscopic display - Polarization method - Lenticular-type - Barrier-type - Sutter glasses method Floating Integral imaging Holography Real 3D 3 [email protected] 5/7/2020 3D Display Stereoscopic display Reasons for not buying 3D TV (NPD Group, 2011) Multiview display Integral Image display Holographic display 4 [email protected] 5/7/2020 3D Display Stereoscopic display 15 views 50” 1999 Multiview display Integral Image display Holographic display Cambridge Univ. 5 [email protected] 5/7/2020 http://www.uv.es/imaging3/Structure.htm 3D Display Stereoscopic display Multiview display Integral Image display Holographic display Super multi-view camera system M x N CCD Camera [1024X768] Resolution : 1024 x 768 x M x N 6 [email protected] 5/7/2020 3D Display Stereoscopic display Multiview display Integral Image display Holographic display Ideal 3D Display Technique • Based on Wave Optics • Real images in space • Full parallax • Continuous viewing points • Coherent illumination • Color images Fig. 4–1 Chart of the principle of holographic display operation 1 – computer, 2 – RF processor, 3 – RF signal, 4 – acoustic-optical modulator, 5 – laser, 6 – lens, 7 – vertical scanner, 8 – beam splitter, 9 – horizontally connected scanners, 10 – output lens, 11 – -
Interview Dec, 2002 Holovizio, the Holographic 3D Display of the Future
Interview Dec, 2002 HoloVizio, the holographic 3D display of the future At this year’s radiology convention’s technical exhibition in Szeged, visitors could marvel a real world sensation, a display of the third dimension, the display which works on the basis of holography. On a 32 inch monitor, similar to the television monitor, vein conjunctions, ribs, a skull cut horizontally at the crown, and other anatomic formulas appeared one after the other. By standing opposite the monitor it became clear what the sensation was, the formulas appeared floating in the air, rising in front of the monitor’s flat screen, giving a real spatial experience. Stepping aside and looking behind the image, more and more details appeared to the viewer. We asked the inventor, Tibor Balogh, a Dennis Gabor-prize winner engineer and owner of the Holografika company about his invention. The interview was prepared by Dr. Éva Németh. What were the antecedents of you developing a real three dimensional display? To display something as if it was really there was an old dream. Looking at the hologram everyone asks, is the object really there? We would almost love to touch it. It is the concurrence of reality and imagination. Today’s displays are flat and everyone has got used to them. When we are looking at the TV screen, we know that we are seeing an artificial picture, no matter how much we improve the resolution, the colour and the quality of the picture, the image still appears artificial, meanwhile, if I look out the window we can see the real world. -
A Low-Power Head-Mounted Phase-Only Holographic Display by Light-Weight Compression
1 Realizing a Low-Power Head-Mounted Phase-Only Holographic Display by Light-Weight Compression Burak Soner, Erdem Ulusoy, A. Murat Tekalp and Hakan Urey Abstract— Head-mounted holographic displays (HMHD) are projected to be the first commercial realization of holographic video display systems. HMHDs use liquid crystal on silicon (LCoS) spatial light modulators (SLM), which are best suited to display phase-only holograms (POH). The performance/watt requirement of a monochrome, 60 fps Full HD, 2-eye, POH HMHD system is about 10 TFLOPS/W, which is orders of magnitude higher than that is achievable by commercially available mobile processors. To mitigate this compute power constraint, display-ready POHs shall be generated on a nearby server and sent to the HMHD in compressed form over a wireless link. This paper discusses design of a feasible HMHD-based augmented reality system, focusing on compression requirements and per-pixel rate-distortion trade-off for transmission of display-ready POH from the server to HMHD. Since the decoder in the HMHD needs to operate on low power, (a) only coding methods that have low-power decoder implementation are considered. Effects of 2D phase unwrapping and flat quantization on compression performance are also reported. We next propose a versatile PCM-POH codec with progressive quantization that can adapt to SLM-dynamic-range and available bitrate, and features per-pixel rate-distortion control to achieve acceptable POH quality at target rates of 60-200 Mbit/s that can be reliably achieved by current wireless technologies. Our results demonstrate feasibility of realizing a low-power, quality-ensured, multi-user, interactive HMHD augmented reality system with commercially available components using the proposed adaptive compression of display-ready POH with light-weight decoding. -
Augmented Reality Smart Glasses in the Smart Factory: Product Evaluation Guidelines and Review of Available Products
Received March 29, 2017, accepted May 8, 2017, date of publication May 12, 2017, date of current version June 28, 2017. Digital Object Identifier 10.1109/ACCESS.2017.2703952 Augmented Reality Smart Glasses in the Smart Factory: Product Evaluation Guidelines and Review of Available Products ANNA SYBERFELDT, OSCAR DANIELSSON, AND PATRIK GUSTAVSSON Department of Engineering Science, University of Skövde, 54128 Skövde, Sweden Corresponding author: Anna Syberfeldt ([email protected]) ABSTRACT Augmented reality smart glasses (ARSG) are increasingly popular and have been identified as a vital technology supporting shop-floor operators in the smart factories of the future. By improving our knowledge of how to efficiently evaluate and select the ARSG for the shop-floor context, this paper aims to facilitate and accelerate the adoption of the ARSG by the manufacturing industry. The market for ARSG has exploded in recent years, and the large variety of products to select from makes it not only difficult but also time consuming to identify the best alternative. To address this problem, this paper presents an efficient step-by-step process for evaluating the ARSG, including concrete guidelines as to what parameters to consider and their recommended minimum values. Using the suggested evaluation process, manufacturing companies can quickly make optimal decisions about what products to implement on their shop floors. This paper demonstrates the evaluation process in practice, presenting a comprehensive review of currently available products along with a recommended best buy. This paper also identifies and discusses topics meriting research attention to ensure that the ARSG are successfully implemented on the industrial shop floor. -
Autostereoscopic Transparent Display Using a Wedge Light
Autostereoscopic transparent display using a wedge light guide and a holographic optical element: implementation and results Thomas Crespel, Patrick Reuter, Adrian Travis, Yves Gentet, Xavier Granier To cite this version: Thomas Crespel, Patrick Reuter, Adrian Travis, Yves Gentet, Xavier Granier. Autostereoscopic trans- parent display using a wedge light guide and a holographic optical element: implementation and results. Applied optics, Optical Society of America, 2019, 58 (34), 10.1364/AO.58.00G293. hal- 02352672 HAL Id: hal-02352672 https://hal.inria.fr/hal-02352672 Submitted on 6 Nov 2019 HAL is a multi-disciplinary open access L’archive ouverte pluridisciplinaire HAL, est archive for the deposit and dissemination of sci- destinée au dépôt et à la diffusion de documents entific research documents, whether they are pub- scientifiques de niveau recherche, publiés ou non, lished or not. The documents may come from émanant des établissements d’enseignement et de teaching and research institutions in France or recherche français ou étrangers, des laboratoires abroad, or from public or private research centers. publics ou privés. Research Article Applied Optics 1 Autostereoscopic transparent display using a wedge light guide and a holographic optical element: implementation and results THOMAS CRESPEL1,2,3,*,P ATRICK REUTER1,3,4,A DRIAN TRAVIS6,Y VES GENTET7, AND XAVIER GRANIER2,5 1Inria Bordeaux Sud-Ouest 200 Avenue de la Vieille Tour, 33405 Talence, France 2 LP2N / Institut d’Optique d’Aquitaine, Rue François Mitterrand, 33400 Talence,