Report on the Results of the Estonian Case Regions
Total Page:16
File Type:pdf, Size:1020Kb
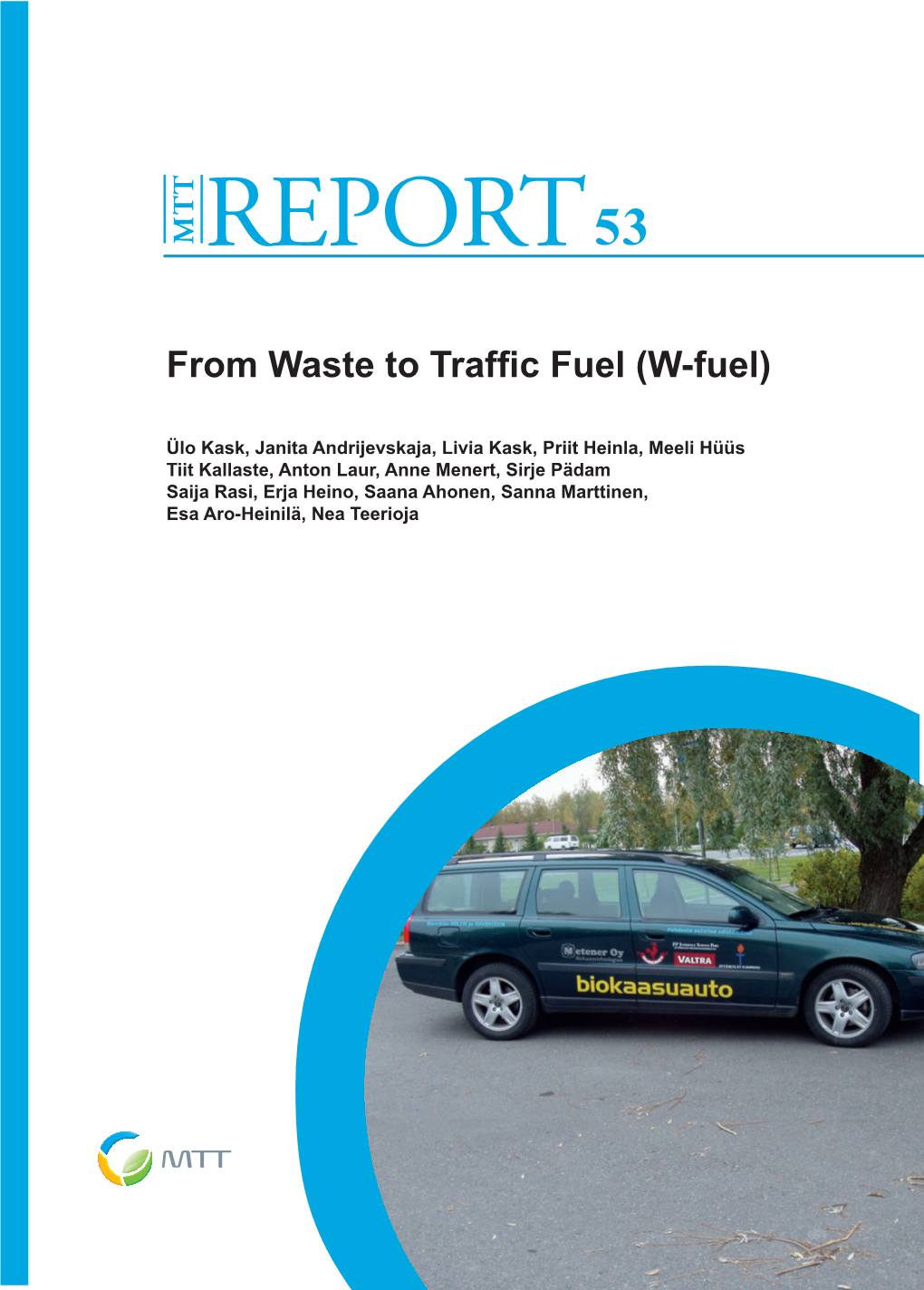
Load more
Recommended publications
-
The Baltic Republics
FINNISH DEFENCE STUDIES THE BALTIC REPUBLICS A Strategic Survey Erkki Nordberg National Defence College Helsinki 1994 Finnish Defence Studies is published under the auspices of the National Defence College, and the contributions reflect the fields of research and teaching of the College. Finnish Defence Studies will occasionally feature documentation on Finnish Security Policy. Views expressed are those of the authors and do not necessarily imply endorsement by the National Defence College. Editor: Kalevi Ruhala Editorial Assistant: Matti Hongisto Editorial Board: Chairman Prof. Mikko Viitasalo, National Defence College Dr. Pauli Järvenpää, Ministry of Defence Col. Antti Numminen, General Headquarters Dr., Lt.Col. (ret.) Pekka Visuri, Finnish Institute of International Affairs Dr. Matti Vuorio, Scientific Committee for National Defence Published by NATIONAL DEFENCE COLLEGE P.O. Box 266 FIN - 00171 Helsinki FINLAND FINNISH DEFENCE STUDIES 6 THE BALTIC REPUBLICS A Strategic Survey Erkki Nordberg National Defence College Helsinki 1992 ISBN 951-25-0709-9 ISSN 0788-5571 © Copyright 1994: National Defence College All rights reserved Painatuskeskus Oy Pasilan pikapaino Helsinki 1994 Preface Until the end of the First World War, the Baltic region was understood as a geographical area comprising the coastal strip of the Baltic Sea from the Gulf of Danzig to the Gulf of Finland. In the years between the two World Wars the concept became more political in nature: after Estonia, Latvia and Lithuania obtained their independence in 1918 the region gradually became understood as the geographical entity made up of these three republics. Although the Baltic region is geographically fairly homogeneous, each of the newly restored republics possesses unique geographical and strategic features. -
Piimaringide Korraldamise Rakendus
Piimaanalüsaatorite korraline hooldus ja remont toimub Hoolduspäeval laborisse toodud piimaproovid analüüsitakse sellele järgneval tööpäeval. SEPTEMBER 2019 T.03 Noorma 10 Valingu 11.00, Kumna 11.20, Alliku 11.45, Ääsmäe 12.10, Saku 12.40, Nabala 13.30, Pahkla küla 13.50, Juuru 14.30, Kaiu (laut) 515 3381 15.00, Pae 15.20, Keava 15.40, Kehtna 15.50, Lokuta 16.15 K.04 15 Kärasi 09.40, Edise 10.50, Uniküla 11.35, Purtse 12.00, Rannu 12.15, Viru-Nigula 13.00, Kohala 13.25, Kaarli 13.50, Vetiku 14.10, Vinni 14.25, Kakumäe 14.40, Viru-Jaagupi 14.55, Muuga 15.40, Laekvere 15.55, Venevere 16.10, Ulvi küla 16.20 N.05 Noorma 6 Kanaküla 10.00, Põld majapidamine 10.30, Surju 11.00, Pärivere 11.45, Kangru küla 11.50, Libatse 12.00, Tõnumaa 12.30, Maima 515 3381 13.00, Jööpre 13.30, Uulu küla 14.15, Kamara küla 15.00, Abja-Paluoja 15.15, Karksi-Nuia 15.30, Ainja küla 15.40, Halliste 16.00, Kaarli küla 16.15 N.05 Tamm 20 Laimjala 07.45, Kipi 08.00, Kotlandi 08.15, Lassi 09.00, Salme 09.15, Kuressaare 09.30, Tahula 09.35, Kõljala 10.00, Tornimäe 5332 4204 11.00, Liiva 11.15, Hellamaa 11.30 T.10 Noorma 4 Leie alev 10.30, Oiu k. 10.45, Tõnuküla 11.15, Ruudiküla 11.30, Intsu küla 11.45, Saimre 11.55, Suuga küla 12.10, Metsla küla 515 3381 12.30, Porsa 13.00, Villa küla 13.05, Jakobimõisa küla 13.20, Pikru küla 13.35, Tamme 14.45, Hummuli 15.15, Rannu 16.00, Kureküla 16.15, Koopsi küla 16.30, Meeri küla 17.00 K.11 Noorma 5 Kabala 10.30, Jaska I 11.00, Lõhavere küla 11.15, Sürgavere küla 11.40, Metsküla 12.10, Kõpu 12.30, Päri küla 13.00, Alustre küla 515 -
Alevist Vallamajani from Borough to Community House
Eesti Vabaõhumuuseumi Toimetised 2 Alevist vallamajani Artikleid maaehitistest ja -kultuurist From borough to community house Articles on rural architecture and culture Tallinn 2010 Raamatu väljaandmist on toetanud Eesti Kultuurkapital. Toimetanud/ Edited by: Heiki Pärdi, Elo Lutsepp, Maris Jõks Tõlge inglise keelde/ English translation: Tiina Mällo Kujundus ja makett/ Graphic design: Irina Tammis Trükitud/ Printed by: AS Aktaprint ISBN 978-9985-9819-3-1 ISSN-L 1736-8979 ISSN 1736-8979 Sisukord / Contents Eessõna 7 Foreword 9 Hanno Talving Hanno Talving Ülevaade Eesti vallamajadest 11 Survey of Estonian community houses 45 Heiki Pärdi Heiki Pärdi Maa ja linna vahepeal I 51 Between country and town I 80 Marju Kõivupuu Marju Kõivupuu Omad ja võõrad koduaias 83 Indigenous and alien in home garden 113 Elvi Nassar Elvi Nassar Setu küla kontrolljoone taga – Lõkova Lykova – Setu village behind the 115 control line 149 Elo Lutsepp Elo Lutsepp Asustuse kujunemine ja Evolution of settlement and persisting ehitustraditsioonide püsimine building traditions in Peipsiääre Peipsiääre vallas. Varnja küla 153 commune. Varnja village 179 Kadi Karine Kadi Karine Miljööväärtuslike Virumaa Milieu-valuable costal villages of rannakülade Eisma ja Andi väärtuste Virumaa – Eisma and Andi: definition määratlemine ja kaitse 183 of values and protection 194 Joosep Metslang Joosep Metslang Palkarhitektuuri taastamisest 2008. Methods for the preservation of log aasta uuringute põhjal 197 architecture based on the studies of 2008 222 7 Eessõna Eesti Vabaõhumuuseumi toimetiste teine köide sisaldab 2008. aasta teaduspäeva ettekannete põhjal kirjutatud üpris eriilmelisi kirjutisi. Omavahel ühendab neid ainult kaks põhiteemat: • maaehitised ja maakultuur. Hanno Talvingu artikkel annab rohkele arhiivimaterjalile ja välitööaine- sele toetuva esmase ülevaate meie valdade ja vallamajade kujunemisest alates 1860. -
Kanalisatsiooni Arendamise Kava Aastateks 2015-2026
Konsultant OÜ KESKKONNAPROJEKT A: Ringtee 12, 51013 Tartu T: +372 7305 060 E: [email protected] reg. kood 10769210 MTR nr EP10769210 Tellija OÜ LOO VESI Töö nr 0584.01 A: Saha tee 9F, Loo, 74201 T: +372 608 0677 E: [email protected] reg. kood 10451270 JÕELÄHTME VALLA ÜHISVEEVÄRGI JA –KANALISATSIOONI ARENDAMISE KAVA AASTATEKS 2015-2026 Projektijuht Reimo Alas Tartu juuni 2015 Jõelähtme valla ühisveevärgi ja –kanalisatsiooni arendamise kava aastateks 2015-2026 SISUKORD SISSEJUHATUS .............................................................................................. 6 1 ARENDAMISE KAVA KOOSTAMISEKS VAJALIKUD LÄHTEANDMED .................... 7 1.1 ÕIGUSLIK BAAS ........................................................................................ 7 1.1.1 Euroopa Liidu direktiivid .......................................................................... 7 1.1.2 Eesti seadused ...................................................................................... 8 1.1.3 Vabariigi valitsuse ja ministrite määrused ..................................................... 9 1.1.4 Veemajanduskavad ................................................................................ 11 1.1.5 Omavalitsuse arengukava ........................................................................ 11 1.1.6 Planeeringud, ehitusprojektid................................................................... 11 1.1.6.1 Harju maakonnaplaneering .................................................................... 11 1.1.6.2 Jõelähtme valla üldplaneeringud -
TARTU ÜLIKOOL VILJANDI KULTUURIAKADEEMIA Rahvusliku
TARTU ÜLIKOOL VILJANDI KULTUURIAKADEEMIA Rahvusliku käsitöö osakond Pärandtehnoloogia magistriõppekava Liis Veersalu KUUSALU KIHELKONNA VANEM PULMAKOMBESTIK JA SELLE TAASLOOMINE TÄNAPÄEVAL Magistritöö Juhendajad: Kristi Jõeste, MA Kaitsmisele lubatud ................................... Piret Õunapuu, PhD Kaitsmisele lubatud ................................... Viljandi 2016 SISUKORD SISSEJUHATUS........................................................................................................................ 4 METOODIKA............................................................................................................................ 9 1 PÄRIMUSLIK PULMAMAASTIK EESTIS 2015–2016............................................... 12 1.1 Avalik info................................................................................................................ 14 1.2 Pärimuspulmaseminarid Pärnus 2014. ja 2015. aastal ............................................. 16 1.3 Pulmaisade ja peopaikade omanike kogemus.......................................................... 17 1.4 Isiklik kogemus ........................................................................................................ 18 1.5 Pärimuspulma taasloojate kogemused ..................................................................... 20 2 KUUSALU VANEM PULMAKOMBESTIK................................................................. 24 2.1 Noorte teineteise leidmine........................................................................................ 25 2.2 Pulmategelased........................................................................................................ -
ABP Loetelu 27.07.2021
Last amendment of this list /viimati muudetud nimekirja: 27.07.2021 Section XIII Other registered operators Teised registreeritud käitlejad Associated Approval/Reg No Name Town/Region Category Activities Product types activities Remarks CHAN Tunnustamise/reg. nr Nimi Aadress Kategooria Tegevusalad Toote tüüp Lisategevusalad Märkused Piibumäe küla, Peipsiääre vald, R/04/ABP/002 FIE Tiit Vene 3 TRANS 49413 Tartumaa Aude talu, Alamõisa küla, Tõrva OTHER (lay out R/13/ABP/001 Ülle Parek Aude Talu 2 DTC; MANU vald, 68403 Valgamaa to land) Tehase 21-63, Aseri, Viru-Nigula in package of not R/03/ABP/001 Kaja Tinnuri 2 UFERT FERT (Cat II MBM) vald, 43401 Ida-Virumaa more than 50 kg Käru mnt 2, Simuna, Väike-Maarja in big bags of not R/07/ABP/003 OÜ Simuna Ivax 2 UFERT FERT (Cat II MBM) vald, 46401 Lääne-Virumaa more than 1000 kg R/02/ABP/002 OÜ Hiiu Autotrans Rookopli 17, 92413 Kärdla, Hiiumaa 1; 2; 3 TRANS Operating in remote R/02/ABP/003 OÜ Hiiu Autotrans Rookopli 17, 92413 Kärdla, Hiiumaa 1; 2; 3 OTHER area (Hiiumaa) Muuli tee 8, Miiduranna küla, 74015 R/01/ABP/008 Selteret OÜ 2 OTHER (retail) FERT (MANP) Viimsi vald, Harjumaa Pärnasalu põik 11, 76505 Saue R/01/ABP/007 Arco Transport AS 2 TRANS linn, Saue vald, Harjumaa Jõgeva MÜ kauplus Jõgeva Suur 11, 48306 Jõgeva, R/04/ABP/004 2 OTHER (retail) FERT (MANP) Ehitusmaterjalid Jõgevamaa Väike-Ameerika 30, 10129 Tallinn, R/01/ABP/011 Workshop OÜ 2 OTHER (retail) FERT (MANP) Harjumaa Puuri küla, Põlva vald, 63220 R/08/ABP/002 OÜ Bestran 2 TRANS FERT Põlvamaa Põlgaste küla, Kanepi vald, 63108 OTHER -
Haljala Valla Arengukava 2018 – 2030 Lisa 1 |
Haljala valla arengukava 2018 – 2030 Lisa 1 | Lisa 1. Haljala valla lähteolukorra analüüs Sisukord 1. Väliskeskkonna poliitilised tegurid ........................................................................................ 3 1.1 Euroopa Liidu dokumendid .............................................................................................. 3 1.1.1 Euroopa 2020 ............................................................................................................ 3 1.1.2 Euroopa Liidu Läänemere strateegia ......................................................................... 4 1.2 Riiklikud dokumendid ...................................................................................................... 5 1.2.1 Konkurentsivõime kava „Eesti 2020“ ....................................................................... 5 1.2.2 Üleriigiline planeering Eesti 2030+ .......................................................................... 5 1.3 Regionaalsed dokumendid ............................................................................................... 6 1.3.1 Lääne-Virumaa arengustrateegia 2030 ...................................................................... 6 1.3.2 Lääne-Virumaa maakonnaplaneering ....................................................................... 7 2. Väliskeskkonna majanduslikud tegurid ................................................................................. 9 3. Väliskeskkonna sotsiaalsed tegurid ..................................................................................... -
Benchmarking Session Between Pilots
Benchmarking session between pilots Valkla and Kolgaküla Village Pilots Kalle Küngas Kuusalu Soojus Ltd Estonia 14th of March 2018, Riga, Latvia 2 Project Partners, Estonia • Tallinn University of Technology/Tallinna Tehnikaülikool as Project Partner No 14 • Kuusalu Municipality/Kuusalu vallavalitsus as Project Partner No 15 • Kuusalu Soojus Ltd/Kuusalu Soojus OÜ as Project Partner No 16 3 • Field of activity - Utilities Kuusalu parish • 100% of shares belongs to Municipality of Kuusalu • Employees - 11 • Drinking Water - 11 regions • Wastewater - 5 regions • District Heating - 2 regions 4 Drinking Water – 11 regions 5 Wastewater – 5 regions 6 District Heating – 2 regions 7 Valkla village pilot • The pilot plant is located in the northern Estonia village of Valkla, Kuusalu parish, Harju county. • The pilot object is the sewage treatment system of two apartment buildings (49 inhabitants in total) • The existing (not used for years) wastewater treatment systems were constructed in the end of the 1970s • Until the construction of the new pilot, the households’ sewage was collected into concrete holding tank and gully- emptier trucks transport it to the nearest WWTP. 8 Valkla village pilot Situation before 9 Valkla village pilot Situation before 10 Valkla village pilot • Biological wastewater treatment system, Sequence Batch Reactors (SBR), with activated sludge process • Construction of new WWTP and renovation of local pipelines was conducted in November 2017 • TTÜ is responsible for monitoring the treatment efficacy of new system and for -
Esitatud Ettepanekud Eelarvesse 2021
Esitatud ettepanekud eelarvesse 2021 Eelarves 2021 arvestatud / Ettepaneku esitaja Ettepanek Selgitus mitte arvestatud Maigi Päären, Haljava Haljava-Raasiku kergliiklustee. mitte arvestatud Puudub programm, millest rahastada. külavanem Haljava tee remondi jätkumine. arvestatud Jooksva remondi korras. Täiendava tänavavalgustuslambi paigaldamine külaplatsile. arvestatud Jooksva remondi korras. Mänguväljakule hakkepuidu lisamine. arvestatud Jooksva remondi korras. Tiigi puhastamine (et täis ei kasvaks). Võimalusel liivaranna mitte arvestatud Ettepanek realiseerida projektitoetuse kaasabil. loomine ühte külge. arvestatud Erinevate külaseltsi projektide kaasfinantseerimine (KOP jne) Kert Veiper, Ihasalu küla Prügikonteineritele prügimaja ehitus koos betoonalusega. mitte arvestatud Ettepanek realiseerida projektitoetuse kaasabil. külavanem Külaplatsi elektriliitumine (3x20A) arvestatud Jooksva remondi korras. Külaplatsi tee projekteerimine vastavalt kehtesstatud DP-le II mitte arvestatud Ettepanek realiseerida projektitoetuse kaasabil. etapp Külaplatsi tee väljaehitamine II etapp mitte arvestatud Ettepanek realiseerida projektitoetuse kaasabil. Külaplatsi valgustuse projekteerimine ja väljaehitamine mitte arvestatud Ettepanek realiseerida projektitoetuse kaasabil. Tiia Välk, Vandjala küla Külaplatsi niitmine ja hooldamine. arvestatud MTÜ-de toetuse alt külavanem Vandjala tuletõrjeveevõtukoha hooldamine. arvestatud MTÜ-de toetuse alt Vana Vandjala külatee äärte hoolduseks summa 600 eurot. arvestatud MTÜ-de toetuse alt Rajada Raasiku-Kostivere -
Veljo Tormis — Works
VELJO TORMIS — WORKS Tormis himself prepared two work lists: the first, in 1989, chronologically, by genre, is published with his Personaalnimestik; the second, in 2000, in chronological order from 1956 to 2000, is unpublished. It also lists a few youthful and student works of 1949 to 1955 and was prepared for Priit Kuusk’s book. Tormis excluded some works from these lists “because they are just arrangements of someone else’s song. They are not creative work.” But he was inconsistent in this policy. Those arrangements which he excluded I have placed at the end of the present works list, along with student and youthful works. Shortly before going to press Tormis gave me a hand-written list of 54 works dating from 1948 to 1951, which are included in the final sections of this list. The title of the work is given in Estonian in this list, except when a current publication gives another language first. The choice of which language to give as the main entry is complicated because Tormis generally used the Estonian title in his list of 1989, but occasionally used another language in his list of 2000. Multi-language titles are cross-referenced. The title is in italics if it is a multi-movement work. Other language title is in (). English trans. of title is in [ ]. If there is a number in parentheses immediately following the translation of the title it represents the position of that work in a multi-movement composition where the title follows. Lack of such information means it is a single, stand-alone work. -
Hara, Virve, Tapurla, Juminda, Tammistu, Leesi, Kiiu-Aabla, Kolga-Aabla, Pedaspea, Pudisoo, Tsitre, Andineeme) Kohta
2016 Kultuurilooline kirjeldus Juminda poolsaarel ja Kolga lahe ääres asuvate külade (Hara, Virve, Tapurla, Juminda, Tammistu, Leesi, Kiiu-Aabla, Kolga-Aabla, Pedaspea, Pudisoo, Tsitre, Andineeme) kohta PROJEKTI „LAHEMAA RANNAKÜLADE MÄLUMAASTIKUD“ I ETAPP MELIKA KINDEL SISUKORD SISUKORD ..................................................................................................................................................... 2 SISSEJUHATUS ............................................................................................................................................ 4 JUMINDA POOLSAARE PAIKNEMINE JA LOODUSLIKUD OLUD ............................................................................ 6 KÜLADE ADMINISTRATIIVSEST KUULUVUSEST JA KULTUURILISTEST ERIPÄRADEST ........................................... 7 ÜLEVAADE ARHIIVIALLIKATEST ......................................................................................................................... 11 RAHVALUULE JA ETNOGRAAFILISE AINESE KOGUMINE KOLGA RANNAST ........................................................ 12 1. HARA KÜLA ........................................................................................................................................ 14 1.1 ÜLEVAADE KÜLA AJALOOST JA TRADITSIOONILISTEST TEGEVUSTEST ................................................. 14 1.2 ÜLEVAADE KULTUURILOOLISELT OLULISTEST PAIKADEST ................................................................... 15 1.3 ÜLEVAADE KULTUURILOOLISELT OLULISTEST ISIKUTEST JA PÄRIMUSEKANDJATEST -
Eesti ANK Liikmed
Eesti ANK liikmed 14 juriidilist HARJUMAA 14 KOV 38 noortekeskust isikut Tallinna linn Tallinna Spordi- ja Noorsooamet Pääsküla noortekeskus Valdeku noortekeskus Mustamäe Avatud Noortekeskus Haabersti noortekeskus Põhja-Tallinna Noortekeskus Kristiine noortekeskus Kesklinna noortekeskus Lasnamäe Noortekeskus Kose Vaba Aja Keskus Mähe avatud noortekeskus Keila linn Keila Linnavalitsus Keila Noortekeskus Loksa linn Loksa Linnavalitsus Loksa Noortekeskus Saue vald Saue Saue Valla Noortekeskus Noortekeskus Haiba noortetuba Laagri Noortetuba Riisipere Noortetuba Raasiku vald Raasiku Vallavalitsus Aruküla Noortekeskus Raasiku Noortekeskus Maardu linn MTÜ Maardu noortekeskus MTÜ Maardu noortekeskus Lääne-Harju Lääne-Harju vald kultuurikeskus Klooga Kultuuri- ja Noortekeskus Kose vald Kose Vallavalitsus Kose Avatud Noortekeskus Oru Noortekeskus Ravila Noortekeskus Habaja Noortekeskus Ardu Noortekeskus Saku vald Saku Valla Saku Noortekeskus Noortekeskus Kiisa Noortekeskus Kiili vald Kiili Vallavalitsus Kiili Valla Noortekeskus Kuusalu vald Kuusalu Vallavalitsus Kuusalu Noortekeskus Jõelähtme vald Jõelähtme Vallavalitsus Loo Noortekeskus Kostivere Noortekeskus Anija vald Anija Valla Noortekeskus (Anija Vallavalitsus) Kehra noortekesus Alavere noortekeskus Rae vald Rae Noortekeskus (Rae Vallavalitsus) Vaida Noortekeskus Järveküla Noortekeskus Rae Noortekeskus Lagedi Noortekeskus Jüri Noortekeskus Hiiumaa 1 KOV 1 juriidilist isikut 3 noortekeskust Hiiumaa vald Kärdla Noortekeskus (Kärdla Osavalla Kärdla noortemaja Valitsus) Kõrgessaare noortemaja