Strain Hardening Behavior and Microstructure Evolution of High-Manganese Steel Subjected to Interrupted Tensile Tests
Total Page:16
File Type:pdf, Size:1020Kb
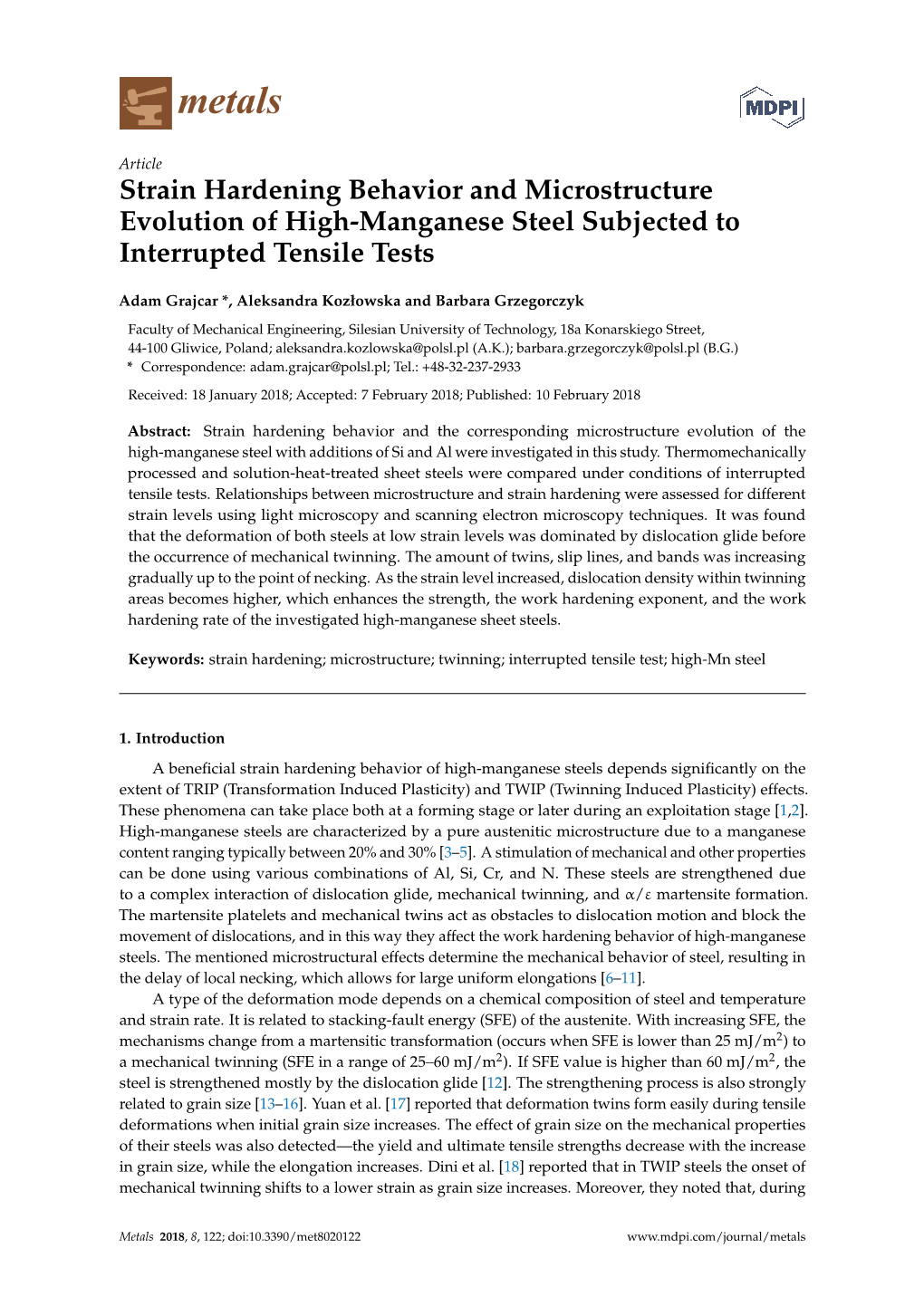
Load more
Recommended publications
-
Review on Different Hardening Models for Computation of Deep
S¯adhan¯a Vol. xx, No.x, xx xxxx, pp.xx–x c Indian Academy of Sciences DOI 12.3456/s78910-011-012-3 Review on Different Hardening Models for Computation of Deep Drawing Process Simulation A C S REDDY 1, C BHASKAR REDDY 2 and D V PALESWAR1 1 Department of Mechanical Engineering, Sreyas Institute of Engineering and Technology 2 Department of Mechanical Engineering, Srikalahsthi Institute of Engineering and Technology Abstract. we address herein various hardening models and their suitability in computational modelling of deep drawing process wherein magnesium alloy AZ31 as blank material. insight on all basic and advanced hardening models. The basic models as well as advanced models were illustrated in usefulness of them in metal forming. It is purely depends on the researcher to select the appropriate hardening model for extracting the real computational behavior resembling the true hardening property. MS received xxxx; revised xxxx; accepted xxxx Keywords. Strain hardening, Isotropic hardening, kinematic hardening, mixed hardening, deep drawing. 1 Introduction is of complex task in computational simulation of deep draw- ing and other processes had successfully implemented in the In practice, different metal forming processes such as deep last couple of decades. The finite Element Methods (FEM) is drawing, stamping, or bending operations are required in man- quite successful to simulate metal forming processes, but ac- ufacture of automotive parts, beverage or food cans, pan- curacy of the drawn parts depends upon the constitutive laws els of aerospace etc. In the last few decades the design of and their parameters identification. The development of ma- sheet metal manufacturing processes such as deep drawing terial models and their use in computational plasticity is of had been significantly influenced by modern tools, e.g. -
Work Hardening and Annealing of Copper
Work Hardening and Annealing of Copper Thomas Stoebe University of Washington Seattle, WA [email protected] Copyright Edmonds Community College 2007; Permission granted for use and reproduction for educational purposes only. Abstract: This experiment demonstrates the process of work hardening in a copper, that is, hardening the metal by deformation. If an appropriate furnace is available, it also demonstrates the softening process of annealing. Copper wire or tubing is quite soft in its initial state, allowing for a variety of uses where the tubing needs to be bent to a desired shape. Upon bending, the copper hardens due to work hardening (also called strain hardening). Enough bending will make it impossible to return it to its original shape. However, annealing at a high enough temperature causes new, strain-free material to form and the copper will return to its original soft condition. Objectives: Students will be able to Experience the process of work hardening Explain the effects of work hardening in metals Experience property changes affected by annealing MatEd core competencies addressed (most important in bold): 4A Demonstrate effective work with teams 7A Illustrate the general nature of metals 8B Apply mechanical testing processes to solid materials 16A Distinguish effects of processing on materials properties Key words: copper, work hardening, annealing, properties Type of Module: Demonstration with class participation or lab experiment Time required: 5 to 10 minutes for deformation and discussion 30 min. for annealing, 10 min for cooling 5 to 10 minutes for deformation of the annealed specimens Target Grade Levels: Grades 4 and up will appreciate the experiment as a demonstration. -
Fatigue Behavior of Linear Friction Welded Ti-6Al-4V and Ti-6Al-2Sn-4Zr-2Mo-0.1Si Dissimilar Welds
materials Article Fatigue Behavior of Linear Friction Welded Ti-6Al-4V and Ti-6Al-2Sn-4Zr-2Mo-0.1Si Dissimilar Welds Sidharth Rajan 1,2,* , Priti Wanjara 1 , Javad Gholipour 1 and Abu Syed Kabir 2 1 National Research Council Canada (NRC), Aerospace Research Center, 2107 Chemin de la Polytechnique, Campus de l’Université de Montréal, Montréal, QC H3T 1J4, Canada; [email protected] (P.W.); [email protected] (J.G.) 2 Mechanical and Aerospace Department, Carleton University, Ottawa, ON K1S 5B6, Canada; [email protected] * Correspondence: [email protected] Abstract: The use of joints fabricated from dissimilar titanium alloys allows the design of structures with local properties tailored to different service requirements. To develop welded structures for aerospace applications, particularly under critical loading, an understanding of the fatigue behavior is crucial, but remains limited, especially for solid-state technologies such as linear friction welding (LFW). This paper presents the fatigue behavior of dissimilar titanium alloys, Ti–6Al–4V (Ti64) and Ti–6Al–2Sn–4Zr–2Mo–0.1Si (Ti6242), joined by LFW with the aim of characterizing the stress versus number of cycles to failure (S-N) curves in both the low- and high-cycle fatigue regimes. Prior to fatigue testing, metallurgical characterization of the dissimilar alloy welds indicated softening in the heat-affected zone due to the retention of metastable β, and the typical practice of stress relief annealing (SRA) for alleviating the residual stresses was effective also in transforming the metastable β α β to equilibrated levels of + phases and recovering the hardness. -
Yield Strength Increase of Cold Formed Sections Due to Cold Work of Forming
Missouri University of Science and Technology Scholars' Mine International Specialty Conference on Cold- (2000) - 15th International Specialty Conference Formed Steel Structures on Cold-Formed Steel Structures Oct 19th, 12:00 AM Yield Strength Increase of Cold Formed Sections Due to Cold Work of Forming P. A. Sloof R. M. Schuster Follow this and additional works at: https://scholarsmine.mst.edu/isccss Part of the Structural Engineering Commons Recommended Citation Sloof, P. A. and Schuster, R. M., "Yield Strength Increase of Cold Formed Sections Due to Cold Work of Forming" (2000). International Specialty Conference on Cold-Formed Steel Structures. 4. https://scholarsmine.mst.edu/isccss/15iccfss/15iccfss-session9/4 This Article - Conference proceedings is brought to you for free and open access by Scholars' Mine. It has been accepted for inclusion in International Specialty Conference on Cold-Formed Steel Structures by an authorized administrator of Scholars' Mine. This work is protected by U. S. Copyright Law. Unauthorized use including reproduction for redistribution requires the permission of the copyright holder. For more information, please contact [email protected]. Fifteenth International Specialty Conference on Cold-Formed Steel Structures St. Louis, Missouri U.S.A., October 19-20, 2000 Yield Strength Increase of Cold Formed Sections Due to Cold Work of Forming P. A. Sioor, P.Eng. and R.M. Schuster2, P.Eng. Abstract The design approach for predicting the increase in yield strength due to cold work of fonning in the AISI 1996 Specification for the Design of Cold-Fonned Steel Structural members is different from the approach used by the CSA Standard, CSA SI36-94, Cold Fonned Steel Structural Members. -
Joining of Refractory Metals and Its Application B. Tabernig, N. Reheis
Tabernig and Reheis 17th Plansee Seminar 2009, Vol. 4 GT 12/1 Joining of Refractory Metals and its Application B. Tabernig, N. Reheis PLANSEE SE, Reutte, Austria Abstract In this work fusion and solide state welding techniques for joining PM refractory metals are adressed. The weldability is discussed and evaluated by electron beam and friction welding experiments. EB welding experiments were performed on rolled sheets made of different Mo-based materials. While a significant decrease in the mechanical properties was found for the weldments of unalloyed molybedenum and the alloy TZM, good weldability is given for Mo41Re. A welding procedure was established and used for the manufacturing of thin walled tubes. Rotary friction welding experiments were carried out on rod material of the Mo-alloys TZM and MHC. Suitable process parameter were determined and successfully transferred for the joining of tubular TZM parts. Keywords Refractory metals, molybdenum, joining, EB-welding, friction welding Introduction Refractory metals such as Mo and W are used in components of several high tech industries due to their high temperature and / or physical properties. One challenge for the industrial application of these specialty materials is the development of dedicated joining technologies. Joining can be achieved by conventional mechanical methods e.g. riveting and fastening as well as by advanced brazing and welding techniques for temperature resistant, strong and tight joints. This study is focused on the joining of refractory metals produced by powder metallurgy (PM) and adresses fusion welding as well as solide state welding techniques. Refractory metals generally exhibit limited weldability. Issues for fusion welding are the embrittlement of the weldment due to impurities and the grain growth in the heat affected zone. -
Effect of Friction Welding Parameters on Mechanical and Microstructural Properties of Dissimilar AISI 1010-ASTM B22 Joints
Kurt et al Supplement May 2011:Layout 1 4/11/11 11:16 AM Page 102 Effect of Friction Welding Parameters on Mechanical and Microstructural Properties of Dissimilar AISI 1010-ASTM B22 Joints In this study, the characteristic of structures, tensile properties, hardness values, and microstructural changes of friction joints were investigated BY A. KURT, I. UYGUR, AND U. PAYLASAN ABSTRACT it is necessary to produce high-quality joints between them. Typical solid-state Rotary friction welding is one of the most economical and efficient production meth- joining applications of diffusion welding ods for joining similar and dissimilar materials. It is widely used with metals and thermo- for various content of the aluminum metal matrix composites (Refs. 5–7) and friction WELDING RESEARCH plastics in a wide variety of aviation, transport, and aerospace industrial component de- signs. Individually, mild steel to mild steel and copper to copper are normally easy to weld stir welding (Ref. 8) have been studied in by fusion welding methods, but the joint of mild steel to copper can be extremely difficult detail. Welding copper alloys is usually dif- due to the differences in the two materials’ melting temperature, density, strength, and ficult using a conventional fusion welding thermal conductivity. Thus, these kinds of problems can be eliminated by a solid-state fric- process because copper has high thermal tion welding technique. Hence, the current study attempts to understand the friction weld- diffusivity, which is about 10 to 100 times ing characteristics of mild steel-bronze dissimilar parts. This study looks into the influence higher than in many steels and nickel al- of process parameters, which includes friction pressure, upsetting pressure, and upset time loys. -
Heat Treatment and Properties of Iron and Steel
National Bureau of Standards Library, N.W. Bldg NBS MONOGRAPH 18 Heat Treatment and Properties of Iron and Steel U.S. DEPARTMENT OF COMMERCE NATIONAL BUREAU OF STANDARDS THE NATIONAL BUREAU OF STANDARDS Functions and Activities The functions of the National Bureau of Standards are set forth in the Act of Congress, March 3, 1901, as amended by Congress in Public Law 619, 1950. These include the development and maintenance of the national standards of measurement and the provision of means and methods for making measurements consistent with these standards; the determination of physical constants and properties of materials; the development of methods and instruments for testing materials, devices, and structures; advisory services to government agencies on scientific and technical problems; inven- tion and development of devices to serve special needs of the Government; and the development of standard practices, codes, and specifications. The work includes basic and applied research, develop- ment, engineering, instrumentation, testing, evaluation, calibration services, and various consultation and information services. Research projects are also performed for other government agencies when the work relates to and supplements the basic program of the Bureau or when the Bureau's unique competence is required. The scope of activities is suggested by the listing of divisions and sections on the inside of the back cover. Publications The results of the Bureau's work take the form of either actual equipment and devices or pub- lished papers. -
Effect of Cold Work Hardening on Stress Corrosion Cracking of Stainless Steels in Primary Water of Pressurized Water Reactors
Effect of cold work hardening on stress corrosion cracking of stainless steels in primary water of pressurized water reactors O. Raquet (1),*, E. Herms (2), F. Vaillant (3), T. Couvant (4), J. M. Boursier (5) (1-2) CEA/Saclay, DEN/DPC – 91191 Gif sur Yvette Cedex – France, Telephone/FAX: 33 (0)1 69 08 15 92 / 15 86, E-mail: [email protected] Telephone/FAX: 33 (0)1 69 08 59 27 / 15 86, E-mail: [email protected] (3-5) EDF/Les Renardières, R&D/MMC – 77250 Moret sur Loing – France E-mail: [email protected], Telephone/FAX: 33 (0)1 60 73 63 03 / 68 89, E-mail: [email protected], Telephone/FAX: 33 (0)1 60 73 62 92 / 68 89, E-mail: [email protected], Telephone/FAX: 33 (0)1 60 73 63 45 / 68 89, Abstract A R&D program is carried out in CEA and EDF laboratories to investigate separately the effects of factors which could contribute to IASCC mechanism. In the framework of this study, the influence of cold work on SCC of ASSs in primary water is studied to supply additional knowledge concerning the contribution of radiation hardening on IASCC of ASSs. Solution annealed ASSs, essentially of type AISI 304(L) and AISI 316(L), are generally considered very resistant to SCC in nominal primary water. However, Constant Extension Rate Tests (CERTs), performed on cold pressed humped specimens in nominal primary water at 360°C, reveal that these materials can exhibit a high SCC susceptibility: deepest cracks reach 1 mm (mean crack growth rate about 1 µm.h-1) and propagation is mainly intergranular for 304L and mainly transgranular for 316L. -
Modeling of Elastic-Viscoplastic Bahavior and Its Finite Element Implementation
Rochester Institute of Technology RIT Scholar Works Theses 12-1-1988 Modeling of elastic-viscoplastic bahavior and its finite element implementation Ted Diehl Follow this and additional works at: https://scholarworks.rit.edu/theses Recommended Citation Diehl, Ted, "Modeling of elastic-viscoplastic bahavior and its finite element implementation" (1988). Thesis. Rochester Institute of Technology. Accessed from This Thesis is brought to you for free and open access by RIT Scholar Works. It has been accepted for inclusion in Theses by an authorized administrator of RIT Scholar Works. For more information, please contact [email protected]. MODELING OF ELASTIC-VISCOPLASTIC BEHAVIOR AND ITS FINITE ELEMENT IMPLEMENTATION TED DIEHL A Thesis Submitted in Partial Fulfillment of the Requirements for the Degree of MASTER OF SCIENCE in Mechanical Engineering Rochester Institute of Technology Rochester, New York December 1988 Approved by: Dr. Hany Ghoneim (Advisor) Associate Professor Department of Mechanical Engineering Rochester Institute of Technology Dr. Surendra K. Gupta Assistant Professor Department of Mechanical Engineering Rochester Institute of Technology Dr. Mark Kempski Assistant Professor Department of Mechanical Engineering Rochester Institute of Technology Dr. Bhalchandra V. Karlekar Professor and Department Head Department of Mechanical Engineering Rochester Institute of Technology I, Ted Diehl, do hereby grant Walla,ce Memorial Library permission to reproduce my thesis in whole or in part. Any reproduction by Wallace Memorial Library will not be used for commercial use or profit. 11 Abstract A state variable approach is developed to simulate the isothermal quasi-static me chanical behavior of elastic-viscoplastic materials subject to small deformations. Modeling of monotonic/cyclic loading, strain-rate effect, work hardening, creep, and stress relaxation are investigated. -
Syllabus for ME463/MSC408 Spring 2014 Jan 15 Organization of The
Syllabus for ME463/MSC408 Spring 2014 Jan 15 Organization of the course. Organization of atoms, bonding, energy levels and density of states, lattices and crystal structures. Jan 20 MLK day Jan 22: Crystal directions and planes (Miller indices), stereographic projections. Crystal structures of Metals. Diamond and graphite structures. Coordination in ionic compounds. AB compounds. Imperfections: point, line, plane, volume. This is all of Chapter 1. Start chapter 2. Phase concept, Phase stability. Hypothetical phases. Free energy and temperature. Free energy and composition. Mechanisms of phase changes. Kinetics. Jan 27: Nucleation in liquids. Nucleation in solids. Interfaces between phases. Interphases. Two phase equilibria. Three phase equilibria—eutectic reaction. Peritectic reactions. Intermediate phases. Limitations of phase diagrams. Example phase diagrams: Cu-Zn, Fe-C (oh no, not again), Cu-Pb and the monotectic reaction L1α + L2.(like a eutectic but one product is still liquid) Jan 29: Ternary phase diagrams: fully miscible and ternary eutectics. Ternary eutectics with solid solutions. Ternaries with peritectic. Ternaries with intermetallics Alloy theory: Size, electrochemical, valency effects. Primary solubility boundary. Electronic structure affects the phases. Interstitial solid solutions. Feb 3: Electrochemical compounds. Size factor compounds. AB2 Laves phases. Ordering and disorder This finishes chapter 2. Start Chapter 3 on solidification. Freezing of a pure metal. Latent heat. Subcritical and supercritical nuclei. Nucleation and Growth. Undercooling. Homogeneous nucleation. Heterogeneous nucleation. Feb 5: Continuous growth vs lateral growth vs dendritic growth. Screw dislocation perpetual spiral step. Dendrite growth and the stability of planar fronts. Temperature gradients. Forms of cast structure. Columnar growth, equiaxed cores. Dissolved gasses and pores. Segregation. -
Novel Modeling of the Work-Hardening Curve
Available online at www.ilcpa.pl International Letters of Chemistry, Physics and Astronomy 4 (2013) 73-90 ISSN 2299-3843 Novel Modeling of the Work-Hardening Curve Zdzisław Pluta, Tadeusz Hryniewicz* Koszalin University of Technology, Raclawicka 15-17, PL 75-620 Koszalin, Poland *E-Mail address: [email protected] „Scientific explanation does not rely on getting from the complexity to simplicity, but on substituting the less understood complexity by more comprehensible.” Lévi-Strauss ABSTRACT The paper aims at a critical analysis of the existent description of plastic strengthening/ work- hardening curve. The adequate description of the curve, having a physical sense, has been proposed. The description begins from the very source which is the primary, general differential equation. That source was used to formulate the characteristics of the studied system. Then the analytical solution of the dependence between the yield stress and the relative deformation is provided. The description of the work-hardening curve has been developed to further form a proper dependence of the yield force on the absolute yield strain. Other functional characteristics, namely the coefficient of the plastic rigidity, yield work, and the plastic potentials, have also been formed. Keywords: Hardening curve; Yield stress; Relative deformation; Relative deformation constant; Absolute strain constant; Stress potential fields; Strain potential fields; Yield force; Plastic rigidity; Plastic energy; Yield work 1. INTRODUCTION There is an increasing tendency observed to simplify the descriptions of natural systems, relying on the creating of models being some approximation of the systems. Physical phenomena are described by various mathematical functions. These functions are often represented by lines connecting experimental points characteristic with a dispersion. -
Friction Welding for Cladding Applications: Processing, Microstructure
FRICTION WELDING FOR CLADDING APPLICATIONS: PROCESSING, MICROSTRUCTURE AND MECHANICAL PROPERTIES OF INERTIA FRICTION WELDS OF STAINLESS STEEL TO LOW CARBON STEEL AND EVALUATION OF WROUGHT AND WELDED AUSTENITIC STAINLESS STEELS FOR CLADDING APPLICATIONS IN ACID- CHLORIDE SERVICE by Nathan Switzner Copyright by Nathan Switzner 2017 All Rights Reserved A thesis submitted to the Faculty and the Board of Trustees of the Colorado School of Mines in partial fulfillment of the requirements for the degree of Doctor of Philosophy (Metallurgical and Materials Engineering). Golden, Colorado Date _______________________________ Signed: _______________________________ Nathan Switzner Signed: _______________________________ Dr. Zhenzhen Yu Thesis Advisor Golden, Colorado Date _______________________________ Signed: _______________________________ Dr. Angus Rockett Professor and Head George S. Ansell Department of Metallurgical and Materials Engineering ii ABSTRACT Friction welding, a solid-state joining method, is presented as a novel alternative process step for lining mild steel pipe and forged components internally with a corrosion resistant (CR) metal alloy for petrochemical applications. Currently, fusion welding is commonly used for stainless steel overlay cladding, but this method is costly, time-consuming, and can lead to disbonding in service due to a hard martensite layer that forms at the interface due to partial mixing at the interface between the stainless steel CR metal and the mild steel base. Firstly, the process parameter space was explored for inertia friction butt welding using AISI type 304L stainless steel and AISI 1018 steel to determine the microstructure and mechanical properties effects. A conceptual model for heat flux density versus radial location at the faying surface was developed with consideration for non-uniform pressure distribution due to frictional forces.