Use of Incineration MSW Ash: a Review
Total Page:16
File Type:pdf, Size:1020Kb
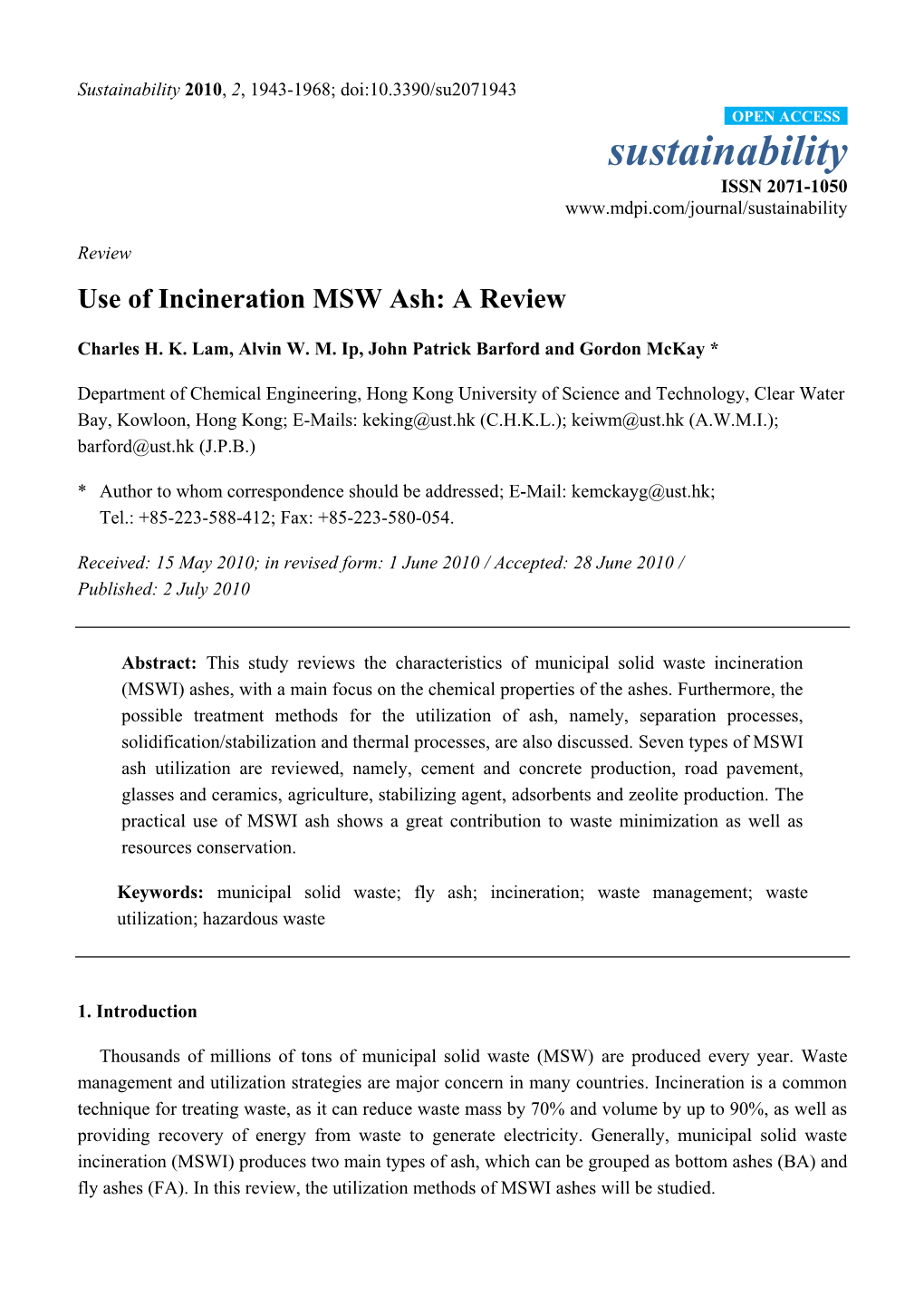
Load more
Recommended publications
-
Safe Use of Wastewater in Agriculture: Good Practice Examples
SAFE USE OF WASTEWATER IN AGRICULTURE: GOOD PRACTICE EXAMPLES Hiroshan Hettiarachchi Reza Ardakanian, Editors SAFE USE OF WASTEWATER IN AGRICULTURE: GOOD PRACTICE EXAMPLES Hiroshan Hettiarachchi Reza Ardakanian, Editors PREFACE Population growth, rapid urbanisation, more water intense consumption patterns and climate change are intensifying the pressure on freshwater resources. The increasing scarcity of water, combined with other factors such as energy and fertilizers, is driving millions of farmers and other entrepreneurs to make use of wastewater. Wastewater reuse is an excellent example that naturally explains the importance of integrated management of water, soil and waste, which we define as the Nexus While the information in this book are generally believed to be true and accurate at the approach. The process begins in the waste sector, but the selection of date of publication, the editors and the publisher cannot accept any legal responsibility for the correct management model can make it relevant and important to any errors or omissions that may be made. The publisher makes no warranty, expressed or the water and soil as well. Over 20 million hectares of land are currently implied, with respect to the material contained herein. known to be irrigated with wastewater. This is interesting, but the The opinions expressed in this book are those of the Case Authors. Their inclusion in this alarming fact is that a greater percentage of this practice is not based book does not imply endorsement by the United Nations University. on any scientific criterion that ensures the “safe use” of wastewater. In order to address the technical, institutional, and policy challenges of safe water reuse, developing countries and countries in transition need clear institutional arrangements and more skilled human resources, United Nations University Institute for Integrated with a sound understanding of the opportunities and potential risks of Management of Material Fluxes and of Resources wastewater use. -
Municipal Incinerated Bottom Ash (MIBA) Characteristics and Potential for Use in Road Pavements Lynn, Ciarán J.; Ghataora, Gurmel S.; Dhir, Ravindra
University of Birmingham Municipal incinerated bottom ash (MIBA) characteristics and potential for use in road pavements Lynn, Ciarán J.; Ghataora, Gurmel S.; Dhir, Ravindra DOI: 10.1016/j.ijprt.2016.12.003 License: Other (please provide link to licence statement Document Version Publisher's PDF, also known as Version of record Citation for published version (Harvard): Lynn, CJ, Ghataora, GS & Dhir, R 2017, 'Municipal incinerated bottom ash (MIBA) characteristics and potential for use in road pavements', International Journal of Pavement Research and Technology, vol. 10, no. 2, pp. 185- 201. https://doi.org/10.1016/j.ijprt.2016.12.003 Link to publication on Research at Birmingham portal General rights Unless a licence is specified above, all rights (including copyright and moral rights) in this document are retained by the authors and/or the copyright holders. The express permission of the copyright holder must be obtained for any use of this material other than for purposes permitted by law. •Users may freely distribute the URL that is used to identify this publication. •Users may download and/or print one copy of the publication from the University of Birmingham research portal for the purpose of private study or non-commercial research. •User may use extracts from the document in line with the concept of ‘fair dealing’ under the Copyright, Designs and Patents Act 1988 (?) •Users may not further distribute the material nor use it for the purposes of commercial gain. Where a licence is displayed above, please note the terms and conditions of the licence govern your use of this document. -
Utilisation of Two-Stage Waste Incinerator Bottom Ash As a Cement Substitute in Concrete
Waste Management and the Environment III 85 Utilisation of two-stage waste incinerator bottom ash as a cement substitute in concrete F. Kokalj & N. Samec University of Mariboru, Faculty of Mechanical Engineering, Slovenia Abstract Waste incineration still seems to be an essential technology in the concept of integrated waste management. However, the desirable quantity of waste incineration residue needs to be as low as possible. Therefore, related optimization of two-stage waste incineration technology has been performed with the main goal of producing lower amounts of boiler ash, fly ash and flue gas-treatment residue, all classified as hazardous waste. Most of the combustion residue should be incinerator bottom ash. Tests were performed on light fraction of municipal solid waste in a two-stage pilot scale waste incineration plant. The goal of this investigation is to present utilisation possibilities of waste light fraction incineration bottom ash as a cement substitute in concrete. The produced incinerator bottom ash, formed in the primary chamber of the two- stage incinerator, was analysed, tested and compared to other incinerator bottom ashes and cement. High resemblance of investigated bottom ash to cement was determined compared to other bottom ashes. Compressive and flexural strength and slump test were performed to characterise incinerator bottom ash and cement mixtures in concrete. It was found that after 28 days the flexural and compressive strengths of the binder linearly gradually decreases. The results show that it is possible to substitute 15 wt% of cement where low strength concrete is required. Keywords: incinerator bottom ash, waste incineration, two-stage incinerator, concrete. -
Five Facts About Incineration Five Facts About Incineration
Five facts about incineration Five facts about incineration Across the globe, cities are looking for ways to improve their municipal solid waste systems. In the search for services that are affordable, green and easy to implement, many cities are encouraged to turn to waste-to-energy (WtE) technologies, such as incineration.1 But, as found in WIEGO’s Technical Brief 11 (Waste Incineration and Informal Livelihoods: A Technical Guide on Waste-to-Energy Initiatives by Jeroen IJgosse), incineration is far from the perfect solution and, particularly in the Global South, can be less cost-effective, more complicated and can negatively impact the environment and informal waste workers’ livelihoods. Below, we have collected the top five issues highlighted in the study that show why this technology is a risky choice: 1. Incineration costs more than recycling. How incineration may be promoted: Incineration is a good economic decision because it reduces the costs associated with landfill operations while also creating energy that can be used by the community. The reality: • In 2016, the World Energy Council reported that, “energy generation from waste is a costly option, in comparison with other established power generation sources.” • Setting up an incineration project requires steep investment costs from the municipality. • For incineration projects to remain financially stable long-term, high fees are required, which place a burden on municipal finances and lead to sharp increases in user fees. • If incinerators are not able to collect enough burnable waste, they will burn other fuels (gas) instead. Contract obligations can force a municipality to make up the difference if an incinerator doesn’t burn enough to create the needed amount of energy. -
2.2 Sewage Sludge Incineration
2.2 Sewage Sludge Incineration There are approximately 170 sewage sludge incineration (SSI) plants in operation in the United States. Three main types of incinerators are used: multiple hearth, fluidized bed, and electric infrared. Some sludge is co-fired with municipal solid waste in combustors based on refuse combustion technology (see Section 2.1). Refuse co-fired with sludge in combustors based on sludge incinerating technology is limited to multiple hearth incinerators only. Over 80 percent of the identified operating sludge incinerators are of the multiple hearth design. About 15 percent are fluidized bed combustors and 3 percent are electric. The remaining combustors co-fire refuse with sludge. Most sludge incinerators are located in the Eastern United States, though there are a significant number on the West Coast. New York has the largest number of facilities with 33. Pennsylvania and Michigan have the next-largest numbers of facilities with 21 and 19 sites, respectively. Sewage sludge incinerator emissions are currently regulated under 40 CFR Part 60, Subpart O and 40 CFR Part 61, Subparts C and E. Subpart O in Part 60 establishes a New Source Performance Standard for particulate matter. Subparts C and E of Part 61--National Emission Standards for Hazardous Air Pollutants (NESHAP)--establish emission limits for beryllium and mercury, respectively. In 1989, technical standards for the use and disposal of sewage sludge were proposed as 40 CFR Part 503, under authority of Section 405 of the Clean Water Act. Subpart G of this proposed Part 503 proposes to establish national emission limits for arsenic, beryllium, cadmium, chromium, lead, mercury, nickel, and total hydrocarbons from sewage sludge incinerators. -
Energy Recovery from Sewage Sludge: the Case Study of Croatia
energies Article Energy Recovery from Sewage Sludge: The Case Study of Croatia Dinko Đurđevi´c 1,* , Paolo Blecich 2 and Željko Juri´c 1 1 Energy Institute Hrvoje Požar, 10000 Zagreb, Croatia; [email protected] 2 Faculty of Engineering, University of Rijeka, 51000 Rijeka, Croatia; [email protected] * Correspondence: [email protected] Received: 26 April 2019; Accepted: 16 May 2019; Published: 20 May 2019 Abstract: Croatia produced 21,366 tonnes of dry matter (DM) sewage sludge (SS) in 2016, a quantity expected to surpass 100,000 tonnes DM by 2024. Annual production rates for future wastewater treatment plants (WWTP) in Croatia are estimated at 5.8–7.3 Nm3/people equivalent (PE) for biogas and 20–25 kgDM/PE of sewage sludge. Biogas can be converted into 12–16 kWhel/PE of electricity and 19–24 kWhth/PE of heat, which is sufficient for 30–40% of electrical and 80–100% of thermal autonomy. The WWTP autonomy can be increased using energy recovery from sewage sludge incineration by 60% for electricity and 100% of thermal energy (10–13 kWhel/PE and 30–38 kWhth/PE). However, energy for sewage sludge drying exceeds energy recovery, unless solar drying is performed. 2 The annual solar drying potential is estimated between 450–750 kgDM/m of solar drying surface. The lower heating value of dried sewage sludge is 2–3 kWh/kgDM and this energy can be used for assisting sludge drying or for energy generation and supply to WWTPs. Sewage sludge can be considered a renewable energy source and its incineration generates substantially lower greenhouse gases emissions than energy generation from fossil fuels. -
The Global E-Waste Monitor 2020 Quantities, Flows, and the Circular Economy Potential
The Global E-waste Monitor 2020 Quantities, flows, and the circular economy potential Authors: Vanessa Forti, Cornelis Peter Baldé, Ruediger Kuehr, Garam Bel Contributions by: S. Adrian, M. Brune Drisse, Y. Cheng, L. Devia, O. Deubzer, F. Goldizen, J. Gorman, S. Herat, S. Honda, G. Iattoni, W. Jingwei, L. Jinhui, D.S. Khetriwal, J. Linnell, F. Magalini, I.C. Nnororm, P. Onianwa, D. Ott, A. Ramola, U. Silva, R. Stillhart, D. Tillekeratne, V. Van Straalen, M. Wagner, T. Yamamoto, X. Zeng Supporting Contributors: 2 The Global E-waste Monitor 2020 Quantities, flows, and the circular economy potential Authors: Vanessa Forti, Cornelis Peter Baldé, Ruediger Kuehr, Garam Bel Contributions by: S. Adrian, M. Brune Drisse, Y. Cheng, L. Devia, O. Deubzer, F. Goldizen, J. Gorman, S. Herat, S. Honda, G. Iattoni, W. Jingwei, L. Jinhui, D.S. Khetriwal, J. Linnell, F. Magalini, I.C. Nnororm, P. Onianwa, D. Ott, A. Ramola, U. Silva, R. Stillhart, D. Tillekeratne, V. Van Straalen, M. Wagner, T. Yamamoto, X. Zeng 3 Copyright and publication information 4 Contact information: Established in 1865, ITU is the intergovernmental body responsible for coordinating the For enquiries, please contact the corresponding author C.P. Baldé via [email protected]. shared global use of the radio spectrum, promoting international cooperation in assigning satellite orbits, improving communication infrastructure in the developing world, and Please cite this publication as: establishing the worldwide standards that foster seamless interconnection of a vast range of Forti V., Baldé C.P., Kuehr R., Bel G. The Global E-waste Monitor 2020: Quantities, communications systems. From broadband networks to cutting-edge wireless technologies, flows and the circular economy potential. -
Waste Management
10 Waste Management Coordinating Lead Authors: Jean Bogner (USA) Lead Authors: Mohammed Abdelrafie Ahmed (Sudan), Cristobal Diaz (Cuba), Andre Faaij (The Netherlands), Qingxian Gao (China), Seiji Hashimoto (Japan), Katarina Mareckova (Slovakia), Riitta Pipatti (Finland), Tianzhu Zhang (China) Contributing Authors: Luis Diaz (USA), Peter Kjeldsen (Denmark), Suvi Monni (Finland) Review Editors: Robert Gregory (UK), R.T.M. Sutamihardja (Indonesia) This chapter should be cited as: Bogner, J., M. Abdelrafie Ahmed, C. Diaz, A. Faaij, Q. Gao, S. Hashimoto, K. Mareckova, R. Pipatti, T. Zhang, Waste Management, In Climate Change 2007: Mitigation. Contribution of Working Group III to the Fourth Assessment Report of the Intergovernmental Panel on Climate Change [B. Metz, O.R. Davidson, P.R. Bosch, R. Dave, L.A. Meyer (eds)], Cambridge University Press, Cambridge, United Kingdom and New York, NY, USA. Waste Management Chapter 10 Table of Contents Executive Summary ................................................. 587 10.5 Policies and measures: waste management and climate ....................................................... 607 10.1 Introduction .................................................... 588 10.5.1 Reducing landfill CH4 emissions .......................607 10.2 Status of the waste management sector ..... 591 10.5.2 Incineration and other thermal processes for waste-to-energy ...............................................608 10.2.1 Waste generation ............................................591 10.5.3 Waste minimization, re-use and -
Chapter 9 Agricultural Waste Management Systems
Part 651 Agricultural Waste Management Field Handbook Chapter 9 Agricultural Waste Management Systems (210–VI–AWMFH, Amend. 47, December 2011) Chapter 9 Agricultural Waste Management Systems Part 651 Agricultural Waste Management Field Handbook Issued December 2011 The U.S. Department of Agriculture (USDA) prohibits discrimination in all its programs and activities on the basis of race, color, national origin, age, disability, and where applicable, sex, marital status, familial status, parental status, religion, sexual orientation, genetic information, political beliefs, reprisal, or because all or a part of an individual’s income is derived from any public assistance program. (Not all prohibited bases apply to all pro- grams.) Persons with disabilities who require alternative means for commu- nication of program information (Braille, large print, audiotape, etc.) should contact USDA’s TARGET Center at (202) 720-2600 (voice and TDD). To file a complaint of discrimination, write to USDA, Director, Office of Civil Rights, 1400 Independence Avenue, SW., Washington, DC 20250–9410, or call (800) 795-3272 (voice) or (202) 720-6382 (TDD). USDA is an equal opportunity provider and employer. (210–VI–AWMFH, Amend. 47, December 2011) Acknowledgments Chapter 9 was originally prepared and printed in 1992 under the direction of James N. Krider (retired), national environmental engineer, Soil Conser- vation Service (SCS), now Natural Resources Conservation Service (NRCS). James D. Rickman (retired), environmental engineer, NRCS, Fort Worth, Texas, provided day-to-day coordination in the development of the hand- book. Authors for chapter 9 included L.M. “Mac” Safley, North Carolina State University, Raleigh, NC; William H. Boyd, environmental engineer, Lincoln, Nebraska; A. -
Bottom Ash-Boiler Slag Separate (Huang 1990)
USER GUIDELINE FOR COAL BOTTOM ASH and BOILER SLAG IN GREEN INFRASTRUCTURE CONSTRUCTION by Principal Investigators: Craig H. Benson and Sabrina Bradshaw Decemeber 2011 Recycled Materials Resource Center University of Wisconsin-Madison Madison, WI 53706 USA USING COAL BOTTOM ASH AND BOILER SLAG IN GREEN INFRASTRUCTURE CONSTRUCTION INTRODUCTION This document provides a comprehensive overview of the engineering and construction properties of bottom ash and boiler slag for use in asphalt concrete aggregate, granular base, stabilized base aggregate, and embankment/backfill material. Studies addressing environmental concerns of using bottom ash and boiler slag, both industrial by-products, as construction materials are reviewed. Some case studies are presented to demonstrate successful applications of bottom ash and boiler slag. With the goal of advancing the use of bottom ash and boiler slag in construction application, references to resources and tools are made available. Coal bottom ash and boiler slag are coarse, granular, incombustible materials that are collected from the bottom of coal burning furnaces. The majority of coal bottom ash and boiler slag are produced at coal-fired electric utility generation stations, with some coming from coal-fired boilers or independent coal-burning electric generation facilities. The type of bottom ash or boiler slag produced depends on the type of coal-burning furnace. Bottom ash is produced as a result of burning coal in a dry bottom pulverized coal boiler. Unburned material from a dry bottom boiler consists of about 20 percent bottom ash Bottom ash is a porous, glassy, dark gray material with a grain size similar to that of sand or gravelly sand (Steam 1978). -
Incineration, Pyrolysis and Gasification of Electronic Waste
E3S Web of Conferences 22, 00060 (2017) DOI: 10.1051/e3sconf/20172200060 ASEE17 Incineration, pyrolysis and gasification of electronic waste Agnieszka Gurgul1,*, Włodzimierz Szczepaniak1, and Monika Zabłocka-Malicka2 1Wrocław University of Science and Technology, Faculty of Environmental Engineering, Wybrzeże Wyspiańskiego 27, 50-370 Wrocław, Poland 2Wrocław University of Science and Technology, Faculty of Chemistry, Wybrzeże Wyspiańskiego 27, 50-370 Wrocław, Poland Abstract. Three high temperature processes of the electronic waste processing: smelting/incineration, pyrolysis and gasification were shortly discussed. The most distinctive feature of electronic waste is complexity of components and their integration. This type of waste consists of polymeric materials and has high content of valuable metals that could be recovered. The purpose of thermal treatment of electronic waste is elimination of plastic components (especially epoxy resins) while leaving non-volatile mineral and metallic phases in more or less original forms. Additionally, the gaseous product of the process after cleaning may be used for energy recovery or as syngas. 1 Electronic waste Rapid economic growth has resulted in an increase of production of electrical and electronic equipment (EEE) which is one of the fastest growing global manufacturing and it is still developing. Waste electric and electronic equipment (WEEE) is now considered as one of the fastest growing waste streams in EU, approximately 3–5% per year [1]. The amount of electric and electronic equipment put on market in 2013 in EU reached 8.1 million tonnes. In 2013, 3.6 million tonnes of WEEE were treated, of which 2.7 million tonnes were recovered. The electric and electronic equipment includes a broad range of goods. -
Energy Recovery of Metallic Aluminium in MSWI Bottom Ash
Energy recovery of metallic aluminium in MSWI bottom ash Different approaches to hydrogen production from MSWI bottom ash: A case study Rasmus Larsson Supervisor at Umeå University: Tekniska Högskolan Umeå Universitet Docent Thomas Wågberg EN1416 Examensarbete för civilingenjörsexamen i Department of Physics energiteknik, 30 hp, VT 2014 Supervisor at Umeå Energi AB EN1416 Thesis work for Master of Science in Energy Engineering, 30 ECTS, Spring 2014 Niklas Jakobsson Planning engineer Abstract Most of the wastes in Sweden end up in incinerator plants. These trashes are full of metals, especially aluminium, which will not oxidize, they can’t always be recycled and they will instead oxidize in water and leak hydrogen gas to its surrounding. Estimations calculate it could be an average potential of around 40-50 kWh/ton of burnt trash. Ignoring the imported trash, the national recovery potential of Sweden’s 4,3 million tonnes of trash would then be equal to 170- 220 GWh/year due to non-recyclable metals, which are currently going to temporary landfills. The requirements to harness this potential are technically simple, and can be achieved by a quick separation of the recyclables and the non- recyclables. This report will review the factors which increase the rate of reaction and study different ways of extracting the energy, by electrolysis, thermal treatment and mechanical mixing. This was done by taking small samples from the MSWI, owned by Umeå Energi AB, and putting them in small containers. While using the different methods, electrolysis, thermal treatment and mechanichal mixing, the amount of developed H2 gas over time was measured.