Powershield Sentinel
Total Page:16
File Type:pdf, Size:1020Kb
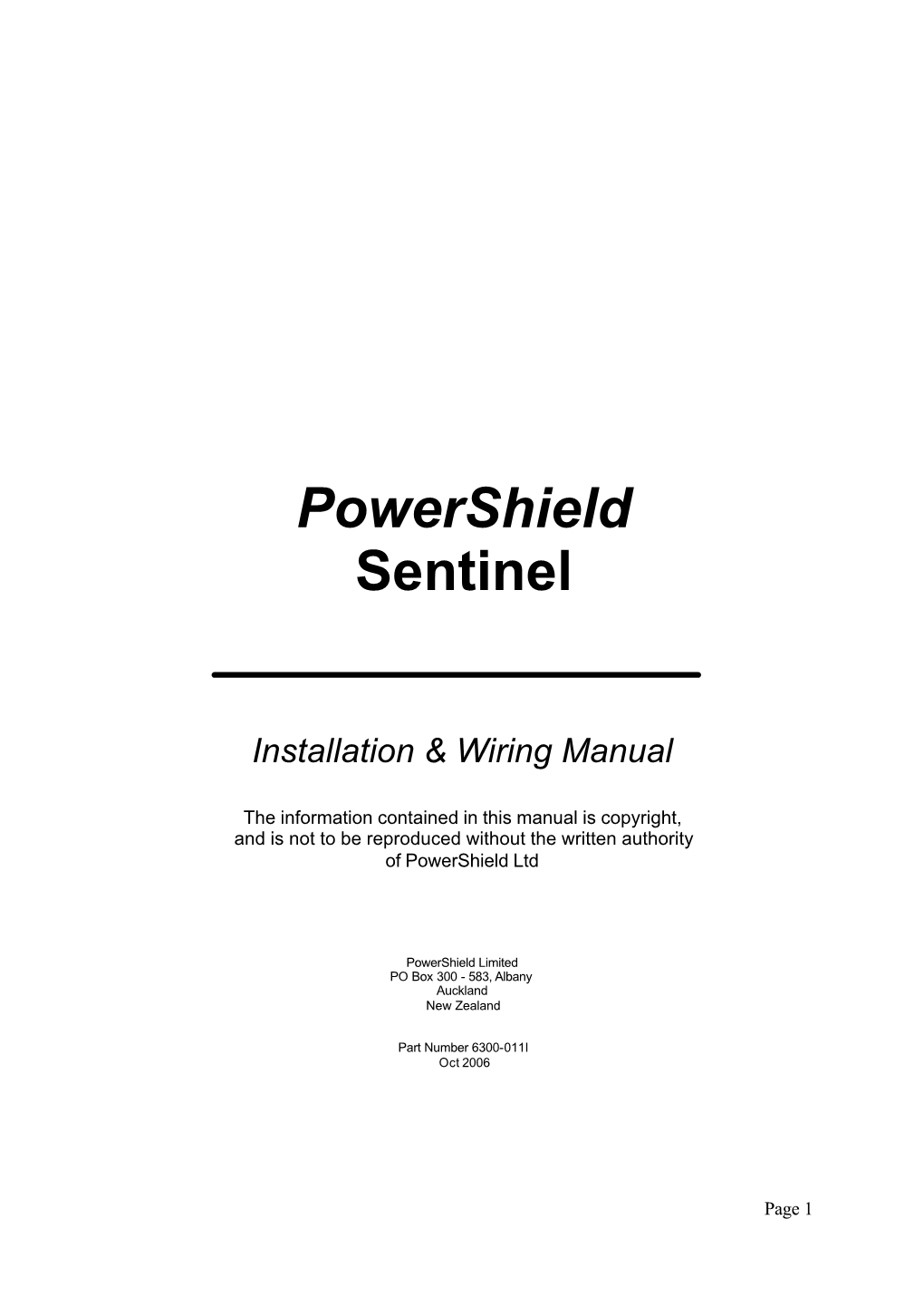
Load more
Recommended publications
-
The Motivational Mind of Magneto: Towards Jungian Discourse Analysis
Page 1 of 30 The motivational mind of Magneto: towards Jungian discourse analysis Jacquelyn Seerattan-Waldrom Supervised by: Dr Geoff Bunn April 2016 Page 2 of 30 The motivational mind of Magneto: towards Jungian discourse analysis ABSTRACT Discourse analysis has been a prominent area of psychology for 25 years. It traditionally focuses on society’s influence on the world through the rhetoric (implicit persuasion) and symbolism, dealing with important psychological areas such as ‘identity’ and many social justice issues. Graphic novel analyses is also increasingly more common. Social justice issues are especially prominent in analysis: particularly in X- Men, through metaphors of ‘oppression’, ‘sexuality and identity’ (Zullo, 2015). Psycho-discursive analysis focuses on the 'subject' neglected in traditional discourse analysis, which has been provided recent attention. A Freudian and Jungian psycho-discursive analysis of DC comic character, 'Batman' has been studied regarding motivation and psyche (Langley, 2012). However, ‘reflexivity’ in Freudian psycho-discursive analysis is a known problem that previous psycho-discursive analyses have been unable to tackle effectively. Therefore, this study proposed a step towards Jungian psycho-discursive analysis adapted from personality and motivation theory, ‘Psychological Types’ (1971) and theoretical expansions by Myers and Myers (1995). It was applied to fictional representations of psyche within the X-Men comic character, ‘Magneto’, due to fictional inspirations which commonly form Jungian theory. Magneto was interpreted as the type, ‘INTJ’, and future implications of further applications to psyche are discussed. KEY PSYCHO- JUNGIAN PERSONALITY X-MEN GRAPHIC DISCURSIVE PSYCHOLOGY NOVEL WORDS: ANALYSIS ANALYSIS Page 3 of 30 Background Discourse analysis For 25 years discourse analysis has been a prominent area of psychology (Stokoe, Hepburn & Antaki, 2012). -
Sentinel's "Miss Bronze" Contest Seeks Queen for '60 OHIO STAT* Mfteu* X5TH * Tuqh-8T.F THB OHIO C0LUH3US, OHIO' SENTINEL SATURDAY, JULY 2
, •»-•-»•_• .«-•»* • • • 'iMMfaeJ^jl i w-< ..• • •<<•- .- • T"i,*'8-g>H.y' "r*|L<i" "* V r THE ©W_•• • O Sentinel's "Miss Bronze" Contest Seeks Queen For '60 OHIO STAT* mftEU* X5TH * tUQH-8T.f THB OHIO C0LUH3US, OHIO' SENTINEL SATURDAY, JULY 2. 1*60 IP 111 H HP • WkM HP • THI PEOPLE'S Interest In Horses Gets Track Job •ENTINEL CHAMPTON SPORTS CLEANINGS : • By BILL BELL • Sport. Editor VOL. 12, No. 4 THURSDAY, JULY 7, 1960 20 CENTS COLUMBUS, OHIO • CONGRATULATIONS andAhanks to the Merry Makers club, for through their generosity the Ohio track club will be able to send its complete team of ten girls to the National AAU Wom en's Track and Field championships; also to the Olympic tryoute Local Families Hit By Drownings which will-be held in Texas in July. Eight of the ten girls already had sponsors but the club's two- ' — Story On Pagt 2 fastest sprinters were sponsorlcss until the Merry Makers came to the rescue. The two young ladies are Miss Rita Thompson, 689 S. Cham- pion av., and Miss Dolores Moore, 141 E. 8th av. • LAST SATURDAY In Cleveland, Rita ran the 75 yard dash • in 8.7 seconds, which is within three tenths of a second of the American record for women. She is a senior at Central High love End In school. Dolores is a sophomore at Sacred Heart. Both girls run an chor on their respective relay teams. ,. ' ' Story On Page 2 While it is fantastic tp hopa that the girls can defeat Tennes see State's great sprinter, we can hope and pray that they can be * good enough to make the squad. -
The Sentinel UUP — Oneonta Local 2190
The Sentinel UUP — Oneonta Local 2190 Volume 11, Number 6 February 2011 Using SPI or SRFI to Compare Faculty Teaching Effectiveness: Is it Statistically Appropriate? By Jen-Ting Wang, Ph.D., Associate Professor of Statistics, De- partment of Mathematics, Computer Science, and Statistics Backgrounds and Problems of Faculty Evaluation through SRFI For the past few months, the new instrument for measuring teaching effec- tiveness known as SRFI (Student Response to Faculty Instruction), has been widely discussed among faculty members on campus and implemented in the Senate. After reviewing some of the available documents, I am compelled to address some concerns about the proposed instrument. As a statistician with a Ph.D. in Statistics and over 10 years of experience teaching and consulting in Statistics, I'd like to express my concerns regarding SRFI from the statistical point of view. When the SPI was first implemented on campus over 20 years ago, the main purpose was to provide faculty with feedback on their teaching. It was not to be incorporated into the evaluation of faculty teaching for re- appointment, tenure, promotion, or DSI. For some reason, it has now become one of the most important assess- ment tools, if not the primary one, for evaluating teaching effectiveness. Furthermore, teaching effectiveness is often reduced to only one number -- the mean score, which has been mistakenly used for comparative analyses of faculty members’ teaching effectiveness. It is also often being misinterpreted that, for example, one faculty mem- ber with an overall mean score of 3.8 has better teaching effectiveness than another faculty member with 3.7. -
Statues and Figurines
NEW STATUES! 1. The Thing Premium Format 550.00 2. Thor Premium Format 900.00 3. Hulk Premium Format 1500.00 4. Art Asylum Hulk 299.00 5. Juggernaut 450.00 6. Wolverine vs Sabretooth 699.00 7. Ironman Comiquette 449.00 8. Mark Newman Sabretooth 245.00 9. Planet Hulk Green Scar vs Silver Savage 500.00 10. Bowen Retro Green Hulk 279.99 11. Moonlight Silver 299.99 12. Hulk Planet Hulk Version 299.99 13. X-Men vs Sentinel 249.99 14. Red Hulk 225.99 15. Art Asylum Captain America 199.00 16. Kotobukiya Ltd Ed. Hulk 225.00 17. Kotobukiya Ltd Ed. Abomination 200.00 18. Bowen Wolverine Action 249.99 19. Sgt Rock 89.99 20. Bowen Shiflet Bros Hulk 299.00 21. Hulk Hard Hero 229.00 22. Superman 199.99 23. Wolverine Diorama 169.99 24. Dead pool 275.00 25. Dead pool 275.00 26. Wolverine with Whiskey 150.00 27. Hulk Marvel Origins 139.00 28. Captain America Resin Bank 24.99 29. Hulk Fine Art Bust 99.99 30. Captain America Mini Bust 89.99 31. Flash vs Gorilla Grodd 200.00 32. Bishoujo Batgirl 59.99 33. Harley Quinn 90.00 34. Swamp Thing 95.00 35. Flaming Carrot 229.99 36. Death 99.99 37. Sandman 99.99 38. BW Batman 79.99 39. ONI Chan 40.00 40. Umbrella Acsdemy 129.99 41. Lord Of The Rings 129.99 42. Silver Surfer 150.00 43. X-Men Origins Wolverine Bust Only 39.99 44. X-Men Origins Wolverine Bust Bluray 80.00 45. -
American Sentinel. Simple Justice
"IF ANY MAN HEAR MY WORDS, AND BELIEVE NOT, / JUDGE HIM NOT; FOR I CAME NOT- TO JUDGE THE WORLD, BUT TO SAYE THE WORLD." Vol. 11, No. 1. NEW YORK, JANUARY 2, 1896. Price, three cents. prayer of the Seventh-day Adventists for respect law-abiding citizens have been haled American Sentinel. simple justice. before courts, and have been tried and unjustly PUBLISHED WEEKLY BY THE In England religious persecution, waged convicted. And but for an appeal to the Su- PACIFIC PRESS PUBLISHING COMPANY, against the same people, has run about the preme Court, now pending, these men would No. 43 BOND STREET, NEW YORK. same course. Here, as in Basel, it was car- be suffering imprisonment at the present Entered at the New York Post-Office. ried on under color of the Factory Act; and, moment for the exercise of their God-given, as appears from the statement which we take constitutional, and statutory rights. from the Daily Graphic, published upon page And what has been the attitude of the peo- r".42,0 T. JONES, 1. EDITORS. .7„..GYIN P. BOLLMAN, 4,* the greatest sufferers have been those ple toward these persecutions? Largely one Leh)/ A. SMITH, ASSISTANT EDITOR. whom the act styles " protected persons." of indifference. This has been especially true The facts, as set forth in the appeal of the in foreign lands. In London it is said by a RETROSPECTIVE AND PROSPECTIVE. Board of Directors to the Home Secretary, to high government official that the numbers which we have just referred, unmistakably concerned were too insignificant to justify 4ITH this number the AMERICAN SENTINEL stamp the action of the authorities in this in- any action looking to relief, by the govern- en ers upon the eleventh year of its publica- stance as religious persecution. -
Creating a Superheroine: a Rhetorical Analysis of the X-Men Comic Books
CREATING A SUPERHEROINE: A RHETORICAL ANALYSIS OF THE X-MEN COMIC BOOKS by Tonya R. Powers A Thesis Submitted in Partial Fulfillment Of the Requirements for the Degree MASTER OF ARTS Major Subject: Communication West Texas A&M University Canyon, Texas August, 2016 Approved: __________________________________________________________ [Chair, Thesis Committee] [Date] __________________________________________________________ [Member, Thesis Committee] [Date] __________________________________________________________ [Member, Thesis Committee] [Date] ____________________________________________________ [Head, Major Department] [Date] ____________________________________________________ [Dean, Fine Arts and Humanities] [Date] ____________________________________________________ [Dean, Graduate School] [Date] ii ABSTRACT This thesis is a rhetorical analysis of a two-year X-Men comic book publication that features an entirely female cast. This research was conducted using Kenneth Burke’s theory of terministic screens to evaluate how the authors and artists created the comic books. Sonja Foss’s description of cluster criticism is used to determine key terms in the series and how they were contributed to the creation of characters. I also used visual rhetoric to understand how comic book structure and conventions impacted the visual creation of superheroines. The results indicate that while these superheroines are multi- dimensional characters, they are still created within a male standard of what constitutes a hero. The female characters in the series point to an awareness of diversity in the comic book universe. iii ACKNOWLEDGEMENTS I wish to thank my thesis committee chair, Dr. Hanson, for being supportive of me within the last year. Your guidance and pushes in the right direction has made the completion of this thesis possible. You make me understand the kind of educator I wish to be. You would always reply to my late-night emails as soon as you could in the morning. -
Sentinel NEWSLETTER of the QUIET PROFESSIONALS SPECIAL FORCES ASSOCIATION CHAPTER 78 the LTC Frank J
Sentinel NEWSLETTER OF THE QUIET PROFESSIONALS SPECIAL FORCES ASSOCIATION CHAPTER 78 The LTC Frank J. Dallas Chapter VOLUME 11, ISSUE 12 • DECEMBER 2020 The Army Gets WEIRD The Wedding Crashers From the Editor VOLUME 11, ISSUE 12 • DECEMBER 2020 This will be my last Sentinel as editor. I filled IN THIS ISSUE: some big shoes as Lonnie left for Las Vegas. He built it into the best newsletter in the SFA, President’s Page .............................................................. 1 and I like to think it still is. US ARMY SPECIAL OPS COMMAND The Army Gets WEIRD .................................................... 2 I’ll be relocating somewhere in Oklahoma, The Wedding Crashers .................................................... 6 Arkansas, or Missouri early in January. The leading contender is the Fayetteville, AR area Book Review: Murphy’s Law: My Journey from Army where I went to grad school in the late ‘70s US ARMY Ranger and Green Beret to Investigative Journalist ....... 12 Jim Morris JFK SWCS Sentinel Editor and early ‘80s. It is for my money the most November 2020 Chapter Meeting .................................. 14 beautiful area of the United States, and, coin- cidentally, very much resembles the Central Highlands of Vietnam. 1ST SF COMMAND FRONT COVER: A C-17 from the Hawaii National Guard banks right by the Dolomite Mountains as paratroopers In the meanwhile I have a book to finish, one that I started more than from the 173rd Airborne Brigade parachute onto Juliet ten years ago, and then put aside to nurse my wife, Myrna, through Drop Zone in northern Italy. (U.S. Air National Guard photo her final illness. I had put off joining Chapter 78 for those years, 1ST SF GROUP by Senior Airman John Linzmeier) because I could not leave her side long enough to attend meetings. -
Uncanny Xmen Box
Official Advanced Game Adventure CAMPAIGN BOOK TABLE OF CONTENTS What Are Mutants? ....... .................... ...2 Creating Mutant Groups . ..... ................ ..46 Why Are Mutants? .............................2 The Crime-Fighting Group . ... ............. .. .46 Where Are Mutants? . ........ ........ .........3 The Tr aining Group . ..........................47 Mutant Histories . ................... ... ... ..... .4 The Government Group ............. ....... .48 The X-Men ..... ... ... ............ .... ... 4 Evil Mutants ........................... ......50 X-Factor . .......... ........ .............. 8 The Legendary Group ... ........... ..... ... 50 The New Mutants ..... ........... ... .........10 The Protective Group .......... ................51 Fallen Angels ................ ......... ... ..12 Non-Mutant Groups ... ... ... ............. ..51 X-Terminators . ... .... ............ .........12 Undercover Groups . .... ............... .......51 Excalibur ...... ..............................12 The False Oppressors ........... .......... 51 Morlocks ............... ...... ......... .....12 The Competition . ............... .............51 Original Brotherhood of Evil Mutants ..... .........13 Freedom Fighters & Te rrorists . ......... .......52 The Savage Land Mutates ........ ............ ..13 The Mutant Campaign ... ........ .... ... .........53 Mutant Force & The Resistants ... ......... ......14 The Mutant Index ...... .... ....... .... 53 The Second Brotherhood of Evil Mutants & Freedom Bring on the Bad Guys ... ....... -
Achievements Booklet
ACHIEVEMENTS BOOKLET This booklet lists a series of achievements players can pursue while they play Marvel United: X-Men using different combinations of Challenges, Heroes, and Villains. Challenge yourself and try to tick as many boxes as you can! Basic Achievements - Win without any Hero being KO’d with Heroic Challenge. - Win a game in Xavier Solo Mode. - Win without the Villain ever - Win a game with an Anti-Hero as a Hero. triggering an Overflow. - Win a game using only Anti-Heroes as Heroes. - Win before the 6th Master Plan card is played. - Win a game with 2 Players. - Win without using any Special Effect cards. - Win a game with 3 Players. - Win without any Hero taking damage. - Win a game with 4 Players. - Win without using any Action tokens. - Complete all Mission cards. - Complete all Mission cards with Moderate Challenge. - Complete all Mission cards with Hard Challenge. - Complete all Mission cards with Heroic Challenge. - Win without any Hero being KO’d. - Win without any Hero being KO’d with Moderate Challenge. - Win without any Hero being KO’d with Hard Challenge. MARVEL © Super Villain Feats Team vs Team Feats - Defeat the Super Villain with 2 Heroes. - Defeat the Villain using - Defeat the Super Villain with 3 Heroes. the Accelerated Villain Challenge. - Defeat the Super Villain with 4 Heroes. - Your team wins without the other team dealing a single damage to the Villain. - Defeat the Super Villain without using any Super Hero card. - Your team wins delivering the final blow to the Villain. - Defeat the Super Villain without using any Action tokens. -
MENDING JUSTICE: Sentinel Event Reviews U.S
U.S. Department of Justice SPECIAL REPORT Office of Justice Programs National Institute of Justice SEPTEMBER SEPTEMBER NATIONAL INSTITUTE OF JUSTICE 2014 MENDING JUSTICE: Sentinel Event Reviews U.S. Department of Justice Office of Justice Programs 810 Seventh St. N.W. Washington, DC 20531 Eric H. Holder, Jr. Attorney General Karol V. Mason Assistant Attorney General William J. Sabol, Ph.D. Acting Director, National Institute of Justice This and other publications and products of the National Institute of Justice can be found at: National Institute of Justice http://www.nij.gov Office of Justice Programs Innovation • Partnerships • Safer Neighborhoods http://www.ojp.usdoj.gov The National Institute of Justice is the research, development and evaluation agency of the U.S. Department of Justice. NIJ’s mission is to advance scientific research, development and evaluation to enhance the administration of justice and public safety. The National Institute of Justice is a component of the Office of Justice Programs, which also includes the Bureau of Justice Assistance; the Bureau of Justice Statistics; the Office for Victims of Crime; the Office of Juvenile Justice and Delinquency Prevention; and the Office of Sex Offender Sentencing, Monitoring, Apprehending, Registering, and Tracking. The findings and conclusions in this publication are those of the authors and do not necessarily reflect the official position or policies of the U.S. Department of Justice. Photo Source: ThinkStock NCJ 247141 Mending Justice Contents 1 Introduction Learning From -
The Sentinel Voice of the ECC Faculty Association Local 3791/IFT September 2006
The Sentinel Voice of the ECC Faculty Association Local 3791/IFT www.eccfaculty.org September 2006 Officers Linda Hefferin, President Rick Green, First Vice-President Sue Ford, Second Vice-President Linda McEwan, Treasurer Crystal Kerwin, Secretary William Demaree, Sentinel Editor Armando Trejo, Webmaster Senators BUS/TECH Rick Green Clark Hallpike Roger Ramey CABS From the President Shawn Mikulay Rachael Tecza Carol Szabo Where Are We Going? LR/CON Linda McEwan And How Will We Get There? LVPA These are important questions for Robert Harmon the ECCFA to think about as we begin a Howard Russo new semester, contract negotiations, and a MSEH search for a new president. Yet it’s difficult Mary Arndt to determine our path for the future until we Daniel Kernler examine our past and see what we can learn. Miroslav Rezac Many of our faculty members are new to UAF ECC and new to the ECCFA. We provide an Rick Bonnom historical overview of the ECCFA for new Lynn Ducar faculty members upon their hire, but the real Sue Ford Crystal Kerwin message of how our hard-earned benefits Marcia Luptak were obtained doesn’t always come across Chris Newman in a short PowerPoint presentation. We must Mary Peterhans continually remind each other of the Cathy Tomasik struggle for each and every right we have Inside… (CRTL+Click to go to gained, as well as be ready to speak up and the story) hold each other accountable to fulfill our . Outreach Programs Planned for responsibilities in the workplace. Especially Area HS Students as our contact nears expiration, we all . -
Children of the Atom Is the First Guidebook Star-Faring Aliens—Visited Earth Over a Million Alike")
CONTENTS Section 1: Background............................... 1 Gladiators............................................... 45 Section 2: Mutant Teams ........................... 4 Alliance of Evil ....................................... 47 X-Men...................................... 4 Mutant Force ......................................... 49 X-Factor .................................. 13 Section 3: Miscellaneous Mutants ........................ 51 New Mutants .......................... 17 Section 4: Very Important People (VIP) ................. 62 Hellfire Club ............................. 21 Villains .................................................. 62 Hellions ................................. 27 Supporting Characters ............................ 69 Brotherhood of Evil Mutants ... 30 Aliens..................................................... 72 Freedom Force ........................ 32 Section 5: The Mutant Menace ................................79 Fallen Angels ........................... 36 Section 6: Locations and Items................................83 Morlocks.................................. 39 Section 7: Dreamchild ...........................................88 Soviet Super-Soldiers ............ 43 Maps ......................................................96 Credits: Dinosaur, Diamond Lil, Electronic Mass Tarbaby, Tarot, Taskmaster, Tattletale, Designed by Colossal Kim Eastland Converter, Empath, Equilibrius, Erg, Willie Tessa, Thunderbird, Time Bomb. Edited by Scintilatin' Steve Winter Evans, Jr., Amahl Farouk, Fenris, Firestar,