Flow of Particulate Material from a Topdressing Aircraft
Total Page:16
File Type:pdf, Size:1020Kb
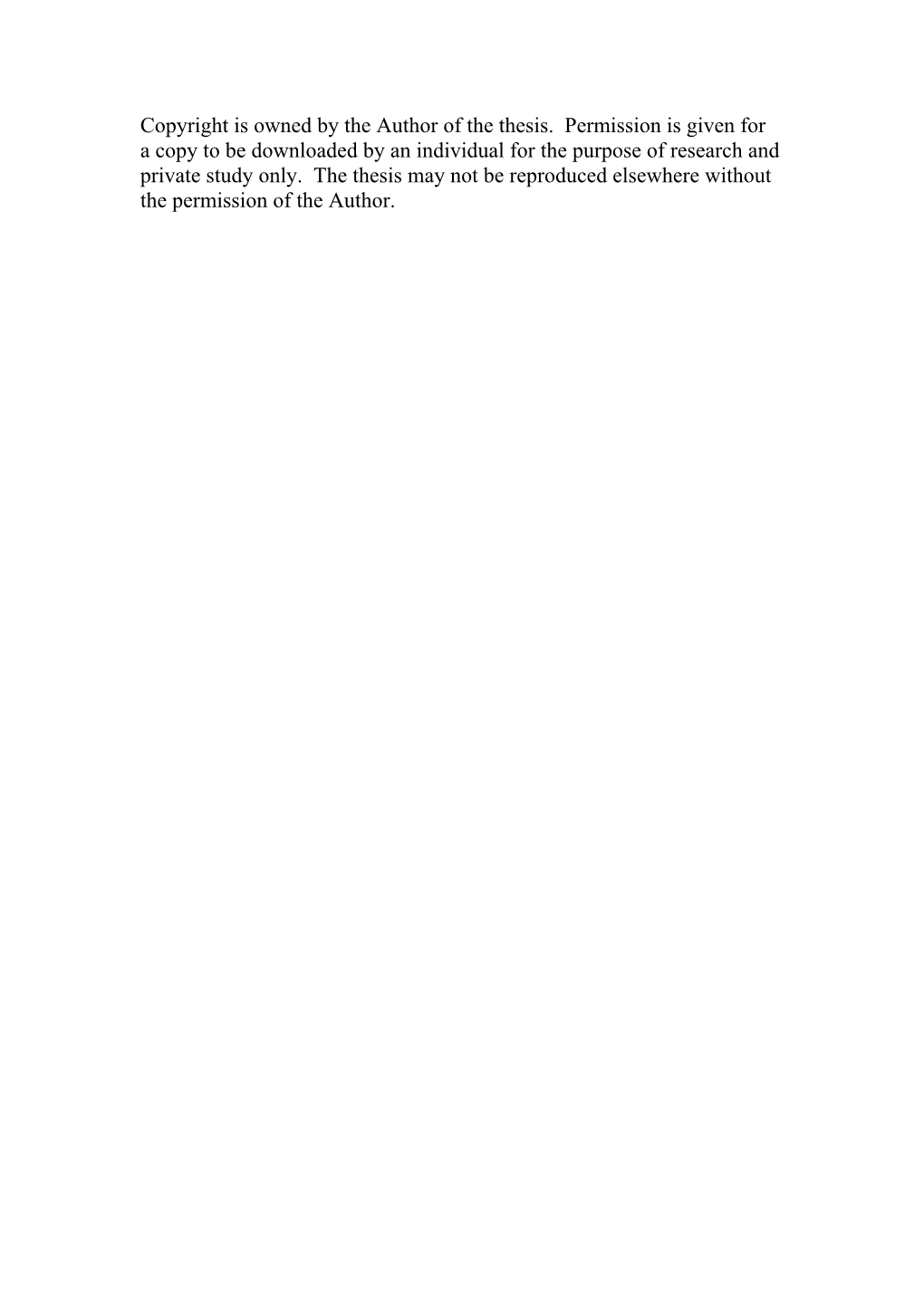
Load more
Recommended publications
-
Certification Process for Agricultural Aircraft Operators, Dated October 10, 2007, Is Cancelled
U.S. Department Advisory of Transportation Federal Aviation Administration Circular Subject: Certification Process for Agricultural Date: 8/21/17 AC No: 137-1B Aircraft Operators Initiated by: AFS-800 Change: This advisory circular (AC) describes an acceptable means, but not the only means, for an agricultural aircraft operator to apply for an Agricultural Aircraft Operator Certificate under Title 14 of the Code of Federal Regulations (14 CFR) part 137. The AC also addresses safety practices for agricultural aircraft operators. This AC is not mandatory and does not constitute a regulation. However, if you use the following means described, you must follow it in all important aspects. This AC does not change regulatory requirements; the provisions of applicable regulations control the AC. Interpretations of regulations are issued only under established agency procedures. This AC applies to the evaluation of applicants for an Agricultural Aircraft Operator Certificate. This AC also applies to agricultural aircraft operations using an Unmanned Aircraft System (UAS). A part 137 operator who wishes to use a UAS should have additional knowledge of Public Law (PL) 112-95, FAA Modernization and Reform Act of 2012, Section 333, Special Rules for Certain Unmanned Aircraft Systems; the 14 CFR part 11 exemption process; 14 CFR part 107; and Federal Aviation Administration (FAA) Order 8900.1, Volume 16, Unmanned Aircraft Systems. Please be aware, the operator of a UAS either cannot comply with several sections in part 137, or those requirements are not applicable to UAS operations. Therefore, an operator proposing to use a UAS must receive a grant of exemption with relief of the appropriate sections of part 137 before the certification process reaches the Demonstration and Inspection Phase. -
De Havilland Tiger Moth 47” Wing Span Plan
de Havilland Tiger Moth 47” Wing Span Plan The de Havilland DH 82 Tiger Moth is a 1930s biplane designed by Geoffrey de Havilland and was operated by the Royal Air Force (RAF) and others as a primary trainer. The Tiger Moth remained in service with the RAF until replaced by the de Havilland Chipmunk in 1952, when many of the surplus aircraft entered civil operation. Many other nations used the Tiger Moth in both military and civil applications, and it remains in widespread use as a recreational aircraft in many countries. It is still occasionally used as a primary training aircraft, particularly for those pilots wanting to gain experience before moving on to other tailwheel aircraft, although most Tiger Moths have a skid. Many are now employed by various companies offering trial lesson experiences. Those in private hands generally fly far fewer hours and tend to be kept in concours condition. The de Havilland Moth club founded 1975 is now a highly organized owners' association offering technical support and focus for Moth enthusiasts. de Havilland Tiger Moth 47” Wing Span Plan de Havilland Tiger Moth 47” Wing Span Plan Design and development The Tiger Moth trainer prototype was derived from the DH 60 de Havilland Gipsy Moth in response to Air Ministry specification 13/31 for an ab-initio training aircraft. The main change to the DH Moth series was necessitated by a desire to improve access to the front cockpit since the training requirement specified that the front seat occupant had to be able to escape easily, especially when wearing a parachute.[2] Access to the front cockpit of the Moth predecessors was restricted by the proximity of the aircraft's fuel tank directly above the front cockpit and the rear cabane struts for the upper wing. -
Agricultural Aviation a Strategy for Sustainable Food Production in Nigeria - Lessons from Brazil
ADENIRAN Adetayo Olaniyi and AKANBI Olawale Mojeed, AJTL, 2019; 2:11 Review Article AJTL 2019, 2:11 American Journal of Transportation and Logistics (ISSN:2637-6172) Agricultural Aviation a Strategy for Sustainable Food Production in Nigeria - Lessons from Brazil ADENIRAN Adetayo Olaniyia and AKANBI Olawale Mojeedb aDepartment of Transport Management Technology, Federal University of Technology Akure, Nigeria; bDepartment of Animal Production and Health, Federal University of Technology Akure, Nigeria ABSTRACT This paper presents a sweeping comparison of Nigeria and Bra- *Correspondence to Author: zil on their agricultural development performances with emphasis ADENIRAN Adetayo Olaniyi on agricultural aviation. Brazil is the fifth largest country in the Department of Transport Manage- world with 207.7 million people (2017 estimate); whereas Nigeria ment Technology, Federal Universi- is the most populous country in Africa with 188.7 million people ty of Technology Akure, Nigeria; (2017 estimate). Both countries were known to have good soil which enhances agriculture but at different level of tilling. Howev- er, Brazil has outperformed Nigeria most especially in agricultural How to cite this article: development with the approach of agricultural aviation, and has ADENIRAN Adetayo Olaniyia and earned world status; while Nigeria still struggles with low agricul- AKANBI Olawale Mojeedb. Agri- tural productivity with old technological involvement. Brazil has cultural Aviation a Strategy for Sus- large land mass with over 31% of land used in tilling. This study tainable Food Production in Nigeria examines the use of aviation in agriculture which increases the - Lessons from Brazil. American productivity of farm produce in Brazil, and with a view to identify- Journal of Transportation and Lo- ing the lessons for the improvement of agricultural development gistics, 2019,2:11. -
A Review of the Economic Impact of High Levels of Variance in Fertiliser Spreading Systems
139 A review of the economic impact of high levels of variance in fertiliser spreading systems M.C.E. GRAFTON1, I.J. YULE2 and M.J. MANNING1 1 Ravensdown Fertiliser Co-operative Ltd., Christchurch, New Zealand, 2 New Zealand Centre for Precision Agriculture, Institute of Agriculture and Environment, Massey University, Palmerston North, New Zealand. [email protected] Abstract be measured, which provides the transverse coefficient Recent technological improvements in Geographical of variation (CV). Søgaard & Kierkegaard (1994) Information Systems (GIS) have made it possible to established the theory of exponential increases in cost, measure the accuracy of fertiliser spreading in the field. in terms of reduced fertiliser efficacy and spreading This demonstrates that the field coefficient of variation, accuracy within a field crop or paddock with reduced “field CV”, of actual spread patterns on farms is spreading accuracy, which is referred to today as the significantly higher than appreciated by most end users field CV. and service providers. Levels of field CV greater than There is confusion as to what a CV (the ratio of the 40% for spreading N fertiliser produces a 20% yield standard deviation to the mean) means in fertiliser reduction, which in terms of urea on dairy pasture is spread. Some of the confusion is a result of there being potentially around $170 million nationally, and is two commonly used terms when discussing fertiliser economically significant. Manufacturers of fertiliser CV, i.e., “transverse CV” and “field CV”. The most spreading equipment and ground-spread applicators commonly measured transverse CV is produced from have introduced improved delivery technologies which a transverse tray test and is used to calculate the appropriate bout or swath width for a spreading vehicle reduce field CV. -
Elementary Level
Grades: K - 5 ELEMENTARY LEVEL CURRICULUM GUIDE Permission to distribute any part or the whole of this material via e-mail or individual copies is automatically granted on the condition it will be used for non- commercial purposes and will not be sold. To reproduce the Elementary Curriculum Guide in any other format, including Internet websites, written permission is needed from the Women of the National Agricultural Aviation Association [WNAAA]. AGRICULTURAL AVIATION: Critical Assist for the World’s Food Supply Elementary Education Curriculum Guide Presentation Outline I. The intent and purpose of the elementary agricultural aviation curriculum guide. A. To introduce the service industry of agricultural aviation to educators and students. 1. The history of agricultural aviation. a. The development/need for the service in agriculture. b. The evolution of the industry. 2. The agricultural aviation industry as it exists today. a. The people involved in agricultural aviation. b. The importance of the industry of agricultural (forestry, disease control) 3. The future of agricultural aviation. a. The role it plays in the continued production of food and fiber. B. To provide insight into the usefulness and importance of agricultural aviation. 1. Agricultural aviation assists the growers of food and fiber. a. Agricultural aviation impacts the lives of people through the food they eat and the clothes they wear. 2. Agricultural aviation provides service to Federal, State and Local Governments. a. The industry assists in protecting the forests, therefore affecting the shelter of many people. b. When called upon, the agricultural aviation industry assists in controlling insects considered health threats. C. -
Download Issue 31 Complete
KiwiFlyer TM Magazine of the New Zealand Aviation Community Issue 31 2013 #6 Supply and Maintenance $ 5.90 inc GST ISSN 1170-8018 Supplement Edition Robinson R22 Overhaul A Taste of Venom: Flying the DH 112 Products, Services, News, Events, Warbirds, Recreation, Training and more. KiwiFlyer Issue 31 2013 #6 From the Editor In this issue Welcome to our holiday season issue of KiwiFlyer. 12 A Taste os Venom: Flying the DH 112 There’s plenty of reading in this one which runs Owner John Luff, Engineer Gerry Gaston, and to a bumper 72 pages, making it our largest edition Test Pilot Sean Perret share their impressions yet. This issue includes a Supply and Maintenance and the excitement of a warbird jet fighter. Supplement section, with editorial and business profiles on a wide variety of aviation maintenance 18. The Kiwi Flyer Interview: Chris Rudge providers and supply organisations. The supplement Jill McCaw talks to Chris Rudge, pilot of includes a detailed article about a Robinson R22 balloons, gliders, helicopters and an Ag-Cat. overhaul, including everything owners need to know 20. Saitek ProFlight Multi Panel Test of and think about when undertaking such a project. We try out some of the lastest flight sim This should be of interest to anyone completing an enhancement gear from Saitek. aircraft overhaul, whether for rotary or fixed wing, as many of the considerations and decisions required 22. The P-40 Kittyhawk are the same regardless of the aircraft type. Frank Parker explains just what it’s like inside the cockpit of a P-40 Kittyhawk. -
100 Years of Aerial Crop Dusting By: FAA Historian Terry Kraus in August
100 Years of Aerial Crop Dusting By: FAA Historian Terry Kraus In August, the agricultural and aviation th communities quietly celebrated the 100 anniversary of the first use of the airplane for crop dusting. On August 3, 1921, Army Air Corps pilot Lieutenant John A. Macready, piloting a specially modified Curtiss JN4 Jenny, spread lead arsenate over a six acre grove of 6,000 catalpa trees at Postmaster Harry Carver’s farm Troy, Ohio. Catalpa trees First known crop dusting effort, 1921 were harvested for their hardwood used for Courtesy: National Agricultural Association of America (NAAA) railroad ties and fence posts. The plane, fitted with a small makeshift hopper (a metal container) and a release mechanism attached to the side of the plane, flew 20 to 35 feet over the orchard, spreading the powdered insecticide in an attempt to kill caterpillars eating the leaves of the trees. Macready relied on the wind and currents from the propeller to carry the poisonous power to the rear of the plane and then down to the grove. The plane landed five times to refill the hopper. The dusting proved successful, demonstrating a plane could do in minutes what it would take ground-based workers days to complete. The idea of using an airplane for crop dusting came at the suggestion of Charles R. Nellie, an Ohio Department of Agriculture forester in Cleveland, who shared his thoughts with entomologist John S. Houser at the Ohio Agricultural Experiment Station in Wooster, Ohio. Wooster officials contacted the Army at McCook Field to see if they could create a device for spreading insecticide from a plane. -
Aircraft Towing Vehicle Ap88 Series Ap89 Series
AIRCRAFT TOWING VEHICLE AP88 SERIES AP89 SERIES TABLEProperty OF ofCAPTURE American METHOD Airlines BY AIRCRAFT TYPE Capture Table 01 Nov. 2016 TABLE OF CAPTURE METHOD BY AIRCRAFT TYPE - AP88 - AP89 SERIES Chapter 2b Intentionally left blank Property of American Airlines LEKTRO PAGE 2b - 2 01 Nov. 2016 TABLE OF CAPTURE METHOD BY AIRCRAFT TYPE - AP88 - AP89 SERIES Chapter 2b TABLE OF CAPTURE 1 Table Key ........................................................................................................................3 2 Table of Capture by Aircraft type ...................................................................................5 Property of American Airlines LEKTRO PAGE 2b - 3 01 Nov. 2016 TABLE OF CAPTURE METHOD BY AIRCRAFT TYPE - AP88 - AP89 SERIES Chapter 2b 2b Table of Capture Method by Aircraft Type: .01 Table Key The table on the following pages is intended to provide general planning and operational guidelines to define tug model capability, capture method and special adapters and / or precautions for specific aircraft model, weight range and nose/tail wheel design. CAUTION: Final verification must be based on the actual aircraft weight, load distribution, undercarriage condition and ramp condition at the time of towing. Table Key: MAKE = Manufacturer (Original Equipment Manufacturer (OEM) /licensee/ upgrader). MODEL= Specific aircraft model or comparable / derivative series. MTOW= Maximum take off weight. Highest weight in each series is used. NOTE: Max Ramp Weight (including taxi fuel) which exceeds MTOW by a small margin may be substituted. (See note 1). OEW = Operating empty weight. Heaviest version is shown. E.g.: Passenger version over cargo version. If the OEW is not avail- able, empty weight with equipment is used. NOTE 1: If two (2) values, separated by a "-" or "/" are shown, the values are interpreted in the following manner: - = Multiple values within the weight range. -
Valid Business Aircraft Types for Toronto Pearson
Valid Business Aircraft Types for Toronto Pearson type mfgr model JUN1 KAMINSKAS Jungster 1 JUN2 KAMINSKAS Jungster 2 A002 IRKUT A-002 A1 DOUGLAS AD Skyraider A10 FAIRCHILD (1) OA-10 Thunderbolt 2 A109 AGUSTA Grand A119 AGUSTA AW-119 Koala A122 AEROTEC (1) A-122 Uirapuru A124 ANTONOV An-124 Ruslan A129 AGUSTA T-129 A139 AGUSTAWESTLAND AW-139 A140 ANTONOV An-140 A148 ANTONOV An-148 A149 AGUSTA AW-149 A158 ANTONOV An-158 A16 AVIADESIGN A-16 Sport Falcon A169 AGUSTAWESTLAND AW-169 A178 ANTONOV An-178 A189 AGUSTAWESTLAND AW-189 A19 AEROPRACT A-19 A19N AIRBUS A-319neo A20 DOUGLAS A-20 Havoc A205 OSKBES-MAI MAI-205 A20J SCHLEICHER ASW-20J A20N AIRBUS A-320neo A21 AEROPRACT Solo A210 AQUILA AT-01 A211 ALFA-M A-211 A21N AIRBUS A-321neo A22 SADLER Piranha A223 OSKBES-MAI Kityonok A225 ANTONOV An-225 Mriya A23 AEROPRACT Dragon A25 AEROPRACT A-25 Breeze A251 AVIATIK-ALYANS Aleks-251 A27 AEROPRACT A-27 A270 AERO (2) Ibis A29 AVANTAGE A-29 A2RT KAZAN Ansat 2RT A3 DOUGLAS A-3 Skywarrior A306 AIRBUS A-300B4-600 A30B AIRBUS A-300B2 A31 AVANTAGE Spectrum A310 AIRBUS Polaris A318 AIRBUS Elite A319 AIRBUS VC-1 ACJ A320 AIRBUS A-320 Prestige A321 AIRBUS A-321 A33 AEROPRACT A-33 A332 AIRBUS Voyager A333 AIRBUS A-330-300 A337 AIRBUS A-330-700 Beluga XL A338 AIRBUS A-330-800 A339 AIRBUS A-330-900 A342 AIRBUS A-340-200 Prestige A343 AIRBUS A-340-300 Prestige A345 AIRBUS A-340-500 Prestige A346 AIRBUS A-340-600 Prestige A35 AVANTAGE A-35 Scanner A359 AIRBUS A-350-900 XWB A35K AIRBUS A-350-1000 XWB A37 CESSNA Dragonfly A388 AIRBUS A-380-800 Prestige A3ST AIRBUS -
Brisbane Valley Flyer
35 785 BRISBANE VALLEY FLYER October- 2020 www.wattsbridge.com.au www.bvsac.org.au Watts Bridge Memorial Airfield, Cressbrook-Caboonbah Road, Toogoolawah, Q’ld 4313. Rob Knight (Editor) Tel: 0400 89 3632 Teaching formation flying across the ditch. With my flaps down to control my speed, I just slipped into position as formation leader. Peter Ratcliffe (Pres.) 0418 159 429 Ian Ratcliffe(Treasurer) 0418 728 328 Vern Grayson (Vice Pres.) 0431 465 874 Jackie Daley (Secretary) 0438 783 740 - Brisbane Valley Flyer - From the Club Pre Covid‐19 Hello everyone, We have changed the key code to door anybody that needing it to access the Clubrooms will need to ring me so I can pass to them The Convid‐19 requirements have changed again and we are now permitted to have 30 people at meetings. However, those 30 people will need to maintain normal social distancing and keep at least 1.5 metres apart from each other. All the best Peter Ratcliffe BVSAC President Page 2 Issue 85 October – 2020 - Brisbane Valley Flyer – Wheelbarrowing is a NO NO NO NO NO! By Rob Knight Scene 1: A fine day with a light wind blowing across the runway at about 5 knots. A light aircraft is on short finals, hot and high, with its airspeed a few knots fast and the aircraft too high to flare at the desired flare point. Ultimately the aircraft finally reaches the flare point further into the runway than the pilot likes so he decides to get the wheels onto the ground where he will have some braking. -
Agricultural Aircraft Operations on Municipal Airports
Agricultural Aircraft Operations on Municipal Airports A Guidebook for Municipal Airport Managers Agricultural Aircraft Operations on Municipal Airports A Guidebook for Municipal Airport Managers Published by: Minnesota Airport Technical Assistance Program (AirTAP) Center for Transportation Studies (CTS) University of Minnesota 511 Washington Ave. S.E. Minneapolis, MN 55455 612-626-1077 www.airtap.umn.edu The University of Minnesota is an equal opportunity educator and employer. This publication is available in alternative formatsby calling 612-626-1077. Printed on recycled paper with 10 percent postconsumer waste. Table of Contents Chapter 1. Overview 1 Chapter 2. Laws 3 Federal Laws 3 Federal Insecticide, Fungicide, and Rodenticide Act 3 Federal Aviation Regulations Part 137 3 State Regulations 3 Pesticide Control 3 Fertilizer, Soil Amendment, and Plant Amendment 3 Agricultural Chemical Liability 4 Agricultural Chemical Response and Reimbursement 4 Bulk Pesticide Storage 4 Security Guidelines 4 Chapter 3. Basic Information Requirements and Record Keeping 5 Airport Operator Records 5 Applicator Requirements 5 Chapter 4. Ag Aircraft—Pesticide Mixing and Loading Areas 7 Establishing a Mixing and Loading Area 7 Load Pad Requirements and Recommended Practices 7 Pesticide Containment 9 Mixing and Loading 9 Rinsate Management 9 Load Pad Design and Location 10 Load Pad Use 10 Multiple Operators 11 Multi-Purpose Load Pads 11 Chapter 5. Pesticide Storage 13 Chapter 6. Emergency Response 15 Emergency Response Plans 15 Spill Reporting 15 Chapter 7. Insurance/ACRRA 17 Chapter 8. Internet Resources 19 Attachments Sample Material Safety Data Sheet (MSDS) Attachment 1 Incident Response Plan and Sample Report Attachment 2 Guidelines for Reporting Incidents Attachment 3 Sample Operator Agreement Attachment 4 Chapter 1. -
Mp Anguished by Epidemic Crime, Alive and Well
part I was down and in bed for 9 days. I was in hopes of escaping but was attending to duties in the House during the day and nursing influenza patients at night. I had been up for three nights in succession and then went down. My temperature did not go Above: An official health poster of 1919 argues beyond 103, and I came through that alcoholic stimulants are the most useful without any complications, save remedy in the primary stages of the influenza for feeling very weak. However, I outbreak, and warns the public about the am glad to say that I am now back efforts of prohibitionists to ban alcohol. to normal. I had a chat to Hickey and I suggested to him that he send you along a few pars just to indicate to you the quality of his work in the meantime, until such Above: J.A. Young, Member of Parliament MP time as you were ready to engage for Waikato. ANGUISHED him definitely. I was sorry to see by the press BY and from information which has reached me from Te Awamutu EPIDEMIC that you have had a most CRIME, unfortunate and sad experience No doubt there were many letters, at Te Awamutu. It has been ALIVE AND telegrams and notes passed up and down pretty well the same everywhere. the nation as the flu epidemic ravaged cities Splendid fellows went down WELL and rural areas alike across New Zealand, right and left. People simply died leaving in its short-lived wake a trail of wholesale here in Wellington.