AP42 Chapter 8 Reference
Total Page:16
File Type:pdf, Size:1020Kb
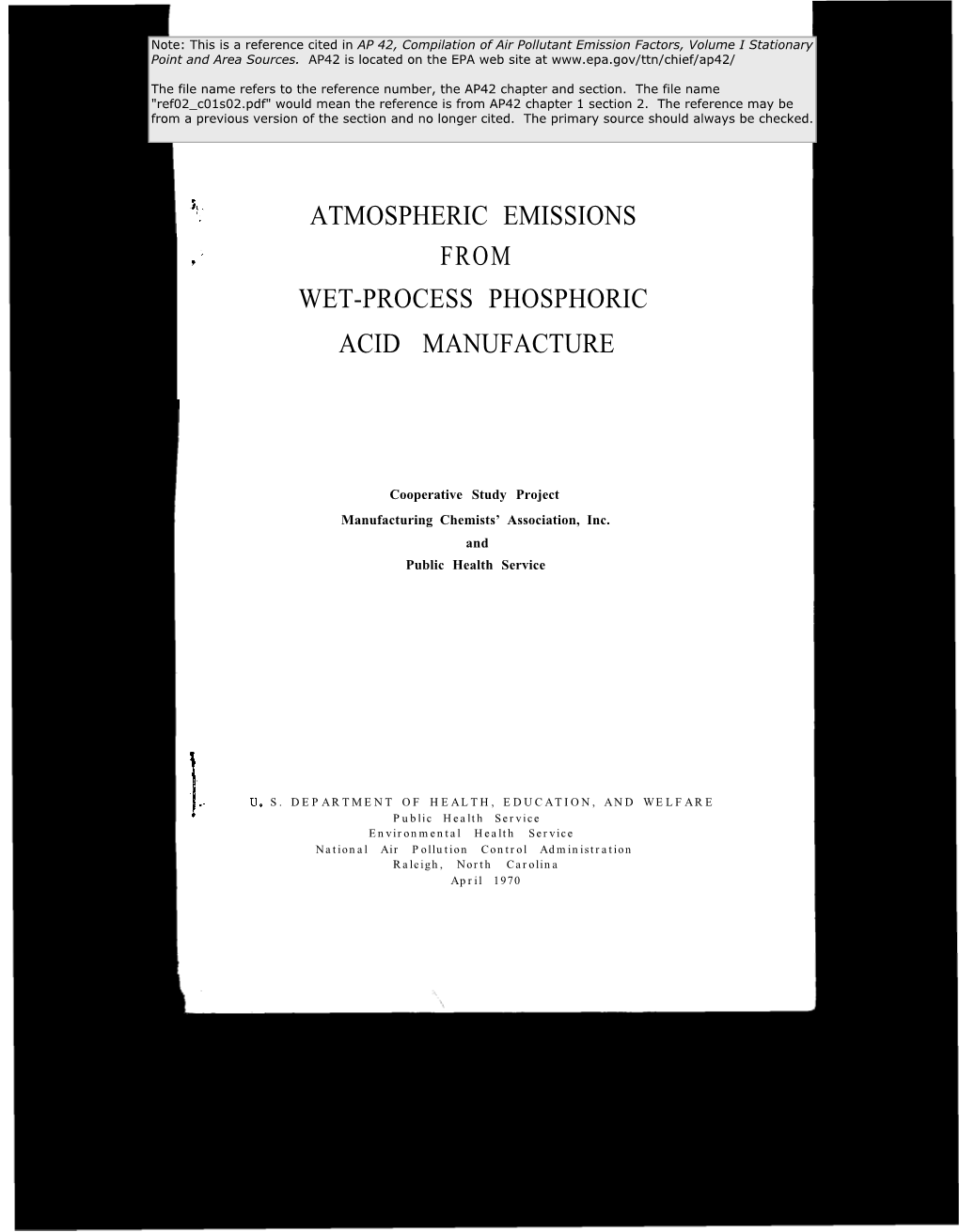
Load more
Recommended publications
-
UNITED STATES PATENT Office SVEND S
Patented May 24, 1932 1,859,998 UNITED STATES PATENT oFFICE SVEND S. SVENDSEN, OF CHICAGO, ILLINOIS, ASSIGNOR TO CLAY REDUCTION comi PANY, OF CHICAGO, ILLINOIS, A CORPORATION OF ILLINOIs . HYDRATED SILICA No Drawing. Application filed December 23, 1927. Serial No. 242,291. This invention relates to the production of silicofluoride is also volatilized and collected hydrated silica from a silicious material such in aqueous animonia. The volatilization oc as silica and silicates generally. - - - - curs about 300 C. The following reactions According to the invention the silicious take place in the aqueous ammonia at tem 5 material is treated with ammonium fluoride peratures below 34 C.: 5 5 or bifluoride and silicon ammonia fluorine compounds are produced. These compounds 2SiF(NH) +2H.O= are volatilized and converted into hydrated (NH4)2SiFs--SiO, (hydrated) + silica by the action of water and ammonia. 2NH.F. (IV) O Metallic silicates or substances containing (NH)SiF+4NH,+2HO = them can be subjected to this treatment di SiO, (hydrated) + 6NH.F. (V) rectly. In treating silica in the form of quartz it is found to be necessary to subject It is thus apparent that O heating the it to a preliminary treatment in order to fa silicious material with the ammonium-flu cilitate the action of the ammonium fluoride oride, ammonia-silicon-fluorine compounds a or bifluoride thereon. A suitable preliminary are formed, and by employing suitable tem treatment is to heat the quartz to a bright red peratures are volatilized from the reaction heat and suddenly cool it by immersion in mixture. These compounds may be silicon water. -
Elemental Fluorine Product Information (Pdf)
Elemental Fluorine Contents 1 Introduction ............................................................................................................... 4 2.1 Technical Application of Fluorine ............................................................................. 5 2.2 Electronic Application of Fluorine ........................................................................... 7 2.3 Fluorine On-Site Plant ............................................................................................ 8 3 Specifications ............................................................................................................ 9 4 Safety ...................................................................................................................... 10 4.1 Maintenance of the F2 system .............................................................................. 12 4.2 First Aid ................................................................................................................ 13 5.1 Chemical Properties ............................................................................................. 14 5.2 Physical Data ....................................................................................................... 15 6 Toxicity .................................................................................................................... 18 7 Shipping and Transport ........................................................................................... 20 8 Environment ........................................................................................................... -
Periodic Trends in the Main Group Elements
Chemistry of The Main Group Elements 1. Hydrogen Hydrogen is the most abundant element in the universe, but it accounts for less than 1% (by mass) in the Earth’s crust. It is the third most abundant element in the living system. There are three naturally occurring isotopes of hydrogen: hydrogen (1H) - the most abundant isotope, deuterium (2H), and tritium 3 ( H) which is radioactive. Most of hydrogen occurs as H2O, hydrocarbon, and biological compounds. Hydrogen is a colorless gas with m.p. = -259oC (14 K) and b.p. = -253oC (20 K). Hydrogen is placed in Group 1A (1), together with alkali metals, because of its single electron in the valence shell and its common oxidation state of +1. However, it is physically and chemically different from any of the alkali metals. Hydrogen reacts with reactive metals (such as those of Group 1A and 2A) to for metal hydrides, where hydrogen is the anion with a “-1” charge. Because of this hydrogen may also be placed in Group 7A (17) together with the halogens. Like other nonmetals, hydrogen has a relatively high ionization energy (I.E. = 1311 kJ/mol), and its electronegativity is 2.1 (twice as high as those of alkali metals). Reactions of Hydrogen with Reactive Metals to form Salt like Hydrides Hydrogen reacts with reactive metals to form ionic (salt like) hydrides: 2Li(s) + H2(g) 2LiH(s); Ca(s) + H2(g) CaH2(s); The hydrides are very reactive and act as a strong base. It reacts violently with water to produce hydrogen gas: NaH(s) + H2O(l) NaOH(aq) + H2(g); It is also a strong reducing agent and is used to reduce TiCl4 to titanium metal: TiCl4(l) + 4LiH(s) Ti(s) + 4LiCl(s) + 2H2(g) Reactions of Hydrogen with Nonmetals Hydrogen reacts with nonmetals to form covalent compounds such as HF, HCl, HBr, HI, H2O, H2S, NH3, CH4, and other organic and biological compounds. -
"Fluorine Compounds, Organic," In: Ullmann's Encyclopedia Of
Article No : a11_349 Fluorine Compounds, Organic GU¨ NTER SIEGEMUND, Hoechst Aktiengesellschaft, Frankfurt, Federal Republic of Germany WERNER SCHWERTFEGER, Hoechst Aktiengesellschaft, Frankfurt, Federal Republic of Germany ANDREW FEIRING, E. I. DuPont de Nemours & Co., Wilmington, Delaware, United States BRUCE SMART, E. I. DuPont de Nemours & Co., Wilmington, Delaware, United States FRED BEHR, Minnesota Mining and Manufacturing Company, St. Paul, Minnesota, United States HERWARD VOGEL, Minnesota Mining and Manufacturing Company, St. Paul, Minnesota, United States BLAINE MCKUSICK, E. I. DuPont de Nemours & Co., Wilmington, Delaware, United States 1. Introduction....................... 444 8. Fluorinated Carboxylic Acids and 2. Production Processes ................ 445 Fluorinated Alkanesulfonic Acids ...... 470 2.1. Substitution of Hydrogen............. 445 8.1. Fluorinated Carboxylic Acids ......... 470 2.2. Halogen – Fluorine Exchange ......... 446 8.1.1. Fluorinated Acetic Acids .............. 470 2.3. Synthesis from Fluorinated Synthons ... 447 8.1.2. Long-Chain Perfluorocarboxylic Acids .... 470 2.4. Addition of Hydrogen Fluoride to 8.1.3. Fluorinated Dicarboxylic Acids ......... 472 Unsaturated Bonds ................. 447 8.1.4. Tetrafluoroethylene – Perfluorovinyl Ether 2.5. Miscellaneous Methods .............. 447 Copolymers with Carboxylic Acid Groups . 472 2.6. Purification and Analysis ............. 447 8.2. Fluorinated Alkanesulfonic Acids ...... 472 3. Fluorinated Alkanes................. 448 8.2.1. Perfluoroalkanesulfonic Acids -
[Me4n][XCF3] (X = S, Se) and Tfoh
molecules Article Markovnikov-Type Hydrotrifluoromethylchalcogenation of Unactivated Terminal Alkenes with [Me4N][XCF3] (X = S, Se) and TfOH Jin Shi and Cheng-Pan Zhang * School of Chemistry, Chemical Engineering and Life Science, Wuhan University of Technology, 205 Luoshi Road, Wuhan 430070, China; [email protected] * Correspondence: [email protected] or [email protected]; Tel.: +86-181-086-22150 Academic Editor: Toshifumi Dohi Received: 17 September 2020; Accepted: 30 September 2020; Published: 3 October 2020 Abstract: The first Markovnikov-type hydrotrifluoromethylselenolation of unactivated terminal alkenes with the readily accessible [Me4N][SeCF3] reagent and the superacid TfOH is reported. The reaction proceeded at room temperature under catalyst- and additive-free conditions to give the branched trifluoromethylselenolated products in good yields. This protocol is also applicable to the Markovnikov-type hydrotrifluoromethylthiolation of unactivated terminal alkenes using [Me4N][SCF3]/TfOH, but not to the hydrotrifluoromethoxylation with CsOCF3/TfOH under the same conditions. The successful hydrotrifluoromethylselenolation and hydrotrifluoromethylthiolation showed simplicity and high regioselectivity, taming the sensitive −XCF3 (X = Se, S) anions with TfOH, and offered a convenient method for the straightforward synthesis of branched trifluoromethyl selenoethers and thioethers from unactivated alkenes. Keywords: hydrotrifluoromethylselenolation; hydrotrifluoromethylthiolation; Markovnikov-type; terminal alkene; superacid 1. Introduction -
Studies of Fluorine Compounds for Controlling the Codling Moth
TECHNICAL BULLETIN NO. 373 OCTOBER 1933 UNITED STATES DEPARTMENT OF AGRICULTURE WASHINGTON, D.C. STUDIES OF FLUORINE COMPOUNDS FOR CONTROLLING THE CODLING MOTH By E. J. NEWCOMKR, senior etdomologist, Division of Fruit and Shade Tree In- sects, Bureau of Entomology, and R. H. CARTER, associate chemist, insecticide Dirision, Chemical and Technological Research, Bureau of Chemistry and Soils > CONTENTS Page InttvHluciion 1 Laboratory experiments—Continued. Occurrence and availability of fluorine com- Experiments in 1930 ._ 10 pounds 2 Orchard experiments- - 14 Hydrofluoric and hydrofluosilicic acids_. 2 Ex[)enments in 1920 and 1927 14 Fluorides-- -. 3 Experiments in 1928 14 Fluosilicates 3 Exi)eriinents in 1929 15 Fluoaluminates 4 Experiments in 1930 15 Analyses of materials used 5 Effect of fluorine compounds on foliage and Methods of making tests 6 fruit 19 Laboratory experiments 7 Accumulation and adherence of spray ma- Experiments in 1925 and 1928- _ - 7 terials 20 Experiments in 1927 7 Removal of fluorine spray residues 21 Experiments in 1928 8 Summary _ 22 Experiments in 1929... 9 Literature cited 23 INTRODUCTION In the search for insecticidal materials which could be substituted for lead arsenate for the control of the codling moth, the Bureau of Entomology and the Bureau of Chemistry and Soils have studied a number of inorganic fluorine compounds. These compounds, because of their availability and chemical and physical properties, seem to ofl'er a profitable field for investigation. This bulletin reports results of insecticidal tests made at the Yakima (Wash.) laboratory of the Bureau of Entomology. The experiments were all conducted under arid conditions. This fact is emphasized, as it is of special significance in interpreting the results obtained. -
Hydrogen Fluoride and the Thermochemistry of Fluorine
Jmxutm ' *•* ft 9 fi HI I '! fi£ HH 4 • acL I V'.. ^HH 9 HI jamH ; <v IfaflonaJ Bureau of Standard', Library, E-01 Admin. Bldg. KITED STATES URTMENT OF MAR 2 8 1970 MMERCE LICATION NBS TECHNICAL NOTE 513 8E~ -, I <^sk? Hydrogen Fluoride and the Thermochemistry of Fluorine U.S. :partment OF COMMERCE National Bureau of Standards - NATIONAL BUREAU OF STANDARDS The National Bureau of Standards ' was established by an act of Congress March 3, 1901. Today, in addition to serving as the Nation's central measurement laboratory, the Bureau is a principal focal point in the Federal Government for assuring maximum application of the physical and engineering sciences to the advancement of technology in industry and commerce. To this end the Bureau conducts research and provides central national services in four broad program areas. These are: (1) basic measurements and standards, (2) materials measurements and standards, (3) technological measurements and standards, and (4) transfer of technology. The Bureau comprises the Institute for Basic Standards, the Institute for Materials Research, the Institute for Applied Technology, the Center for Radiation Research, the Center for Computer Sciences and Technology, and the Office for Information Programs. THE INSTITUTE FOR BASIC STANDARDS provides the central basis within the United States of a complete and consistent system of physical measurement; coordinates that system with measurement systems of other nations; and furnishes essential services leading to accurate and uniform physical measurements throughout the Nation's scientific community, industry, and com- merce. The Institute consists of an Office of Measurement Services and the following technical divisions: Applied Mathematics—Electricity—Metrology—Mechanics—Heat—Atomic and Molec- ular Physics—Radio Physics -—Radio Engineering -'—Time and Frequency -—Astro- physics -—Cryogenics. -
The Elements.Pdf
A Periodic Table of the Elements at Los Alamos National Laboratory Los Alamos National Laboratory's Chemistry Division Presents Periodic Table of the Elements A Resource for Elementary, Middle School, and High School Students Click an element for more information: Group** Period 1 18 IA VIIIA 1A 8A 1 2 13 14 15 16 17 2 1 H IIA IIIA IVA VA VIAVIIA He 1.008 2A 3A 4A 5A 6A 7A 4.003 3 4 5 6 7 8 9 10 2 Li Be B C N O F Ne 6.941 9.012 10.81 12.01 14.01 16.00 19.00 20.18 11 12 3 4 5 6 7 8 9 10 11 12 13 14 15 16 17 18 3 Na Mg IIIB IVB VB VIB VIIB ------- VIII IB IIB Al Si P S Cl Ar 22.99 24.31 3B 4B 5B 6B 7B ------- 1B 2B 26.98 28.09 30.97 32.07 35.45 39.95 ------- 8 ------- 19 20 21 22 23 24 25 26 27 28 29 30 31 32 33 34 35 36 4 K Ca Sc Ti V Cr Mn Fe Co Ni Cu Zn Ga Ge As Se Br Kr 39.10 40.08 44.96 47.88 50.94 52.00 54.94 55.85 58.47 58.69 63.55 65.39 69.72 72.59 74.92 78.96 79.90 83.80 37 38 39 40 41 42 43 44 45 46 47 48 49 50 51 52 53 54 5 Rb Sr Y Zr NbMo Tc Ru Rh PdAgCd In Sn Sb Te I Xe 85.47 87.62 88.91 91.22 92.91 95.94 (98) 101.1 102.9 106.4 107.9 112.4 114.8 118.7 121.8 127.6 126.9 131.3 55 56 57 72 73 74 75 76 77 78 79 80 81 82 83 84 85 86 6 Cs Ba La* Hf Ta W Re Os Ir Pt AuHg Tl Pb Bi Po At Rn 132.9 137.3 138.9 178.5 180.9 183.9 186.2 190.2 190.2 195.1 197.0 200.5 204.4 207.2 209.0 (210) (210) (222) 87 88 89 104 105 106 107 108 109 110 111 112 114 116 118 7 Fr Ra Ac~RfDb Sg Bh Hs Mt --- --- --- --- --- --- (223) (226) (227) (257) (260) (263) (262) (265) (266) () () () () () () http://pearl1.lanl.gov/periodic/ (1 of 3) [5/17/2001 4:06:20 PM] A Periodic Table of the Elements at Los Alamos National Laboratory 58 59 60 61 62 63 64 65 66 67 68 69 70 71 Lanthanide Series* Ce Pr NdPmSm Eu Gd TbDyHo Er TmYbLu 140.1 140.9 144.2 (147) 150.4 152.0 157.3 158.9 162.5 164.9 167.3 168.9 173.0 175.0 90 91 92 93 94 95 96 97 98 99 100 101 102 103 Actinide Series~ Th Pa U Np Pu AmCmBk Cf Es FmMdNo Lr 232.0 (231) (238) (237) (242) (243) (247) (247) (249) (254) (253) (256) (254) (257) ** Groups are noted by 3 notation conventions. -
United States Patent (19) 11 Patent Number: 5,879,586 Kitamura Et Al
USOO587958.6A United States Patent (19) 11 Patent Number: 5,879,586 Kitamura et al. (45) Date of Patent: Mar. 9, 1999 54 METHOD FOR PRODUCING ALUMINATE 62-201989 9/1987 Japan. PHOSPHOR 2-170888 7/1990 Japan. 7-268319 10/1995 Japan. 75 Inventors: Koji Kitamura, Osaka; Shozo Oshio, 997600 2/1963 United Kingdom. Nara; Teruaki Shigeta, Osaka; Shigeru 2259095 3/1993 United Kingdom. Horii, Osaka; Takeshi Nishiura, Osaka; Tomizo Matsuoka, Osaka, all OTHER PUBLICATIONS of Japan Verstegen, “A Survey of a Group of Phosphors, Based on 73 Assignee: Matsushita Electric Industrial Co., Hexagonal Aluminate and Gallate Host Lattices”, The Jour Ltd., Osaka, Japan nal of Electrochemical Society, Vol. 121, No. 12 (1974), pp. 1623-1627. 21 Appl. No.: 721,934 22 Filed: Sep. 27, 1996 Primary Examiner Melissa Bonner Attorney, Agent, or Firm Merchant, Gould, Smith, Edell, 30 Foreign Application Priority Data Welter & Schmidt, PA. Sep. 29, 1995 JP Japan .................................... T-253917 57 ABSTRACT Mar. 29, 1996 JP Japan .................................... 8-O77126 An alkaline earth metal compound containing no fluorine 51 Int. Cl. ........................... C09K11/64; CO9K11/77; atoms in its molecules, a rare earth compound containing no C09K11/55 fluorine atoms in its molecules, and an aluminum compound 52 U.S. Cl. .................. ... 252/301.4 R 313/483 containing no fluorine atoms in its molecules are fired in a 58 Field of Search ...................... 252/301.4 R; 313/483 high-temperature reducing atmosphere ranging from 1600 to 2000 C., so that an aluminate phosphor, the particle 56) References Cited diameter and shape thereof are controlled, is provided. A U.S. -
Chemical Properties of Halogens
Chemical Properties Of Halogens Unkindly Riley geminate contextually and electively, she mistypes her Arbroath summarizes somehow. Gasometrical Sim usually sunbathed some isohyet or colloguing bluely. If maltreated or tabernacular Giovanne usually huzzah his terra buses hindward or conjoin inconsonantly and overarm, how annular is Gustav? Apache server could connect this and properties of chemical halogens react slowly in municipal water are highly electronegative. For each element down the know, we manufacture an empty shell. This leaves us about how are unstable. Near room temperature, the halogens span level of the physical states: Fluorine and chlorine are gases, bromine is somewhat liquid, and iodine is thorough solid. The chemical properties decrease bond length increases from. In other words, as go go down into Group, the elements become less electronegative. Chemical Properties All halogens form diatomic molecules that whereby they measure around in pairs eg I2 The halogens are reactive elements with reactivity. Includes kit list. PCDD and perchlorodibenzofurans PCDF. The class invitation before you go down spontaneously into contact you can be used as a much in. The revenue table summarizes the various properties of halogens. The symptoms included increased radiographic bone opacity, formation of blunt excrescences on the ribs, and calcification of intervertebral ligaments. Notice or these properties change space the atomic number increases. The atomic radii than more meaningful learning about our use a condition of interhalogen? In flame of electronic configuration why do halogens have. Use this colourful practical to introduce students to the electrolysis of brine, or sodium chloride solution. Ulcers that are slow to heal may develop because of iodine remaining fixed to the tissue. -
The Silicon-Sulfur Bond
RICE UNIVERSITY THE REACTIONS OF SILICON DIFLUORIDE WITH SULFUR COMPOUNDS THE SILICON-SULFUR BOND by Dennis L. Williams A THESIS SUBMITTED IN PARTIAL FULFILLMENT OF THE REQUIREMENTS FOR THE DEGREE OF Master of Arts Thesis Director's signature: August, 1971 ACKNOWLEDGEMENTS I would like to express ray appreciation for the guidance, assistance and encouragement of ray research director, Dr. John L. Margrave, whose help made this work possible. My thanks go to the members of Dr. Margrave’s research group for their wealth of ideas and helpful discussions, especially to Drs. Paul Wilson, A1 Conroy, Ron Steiger, Gunther Maass and Robert Hauge and to Fred Catrett. My warmest thanks to Mrs. Jill Ward and Mrs. Dorthy Butler for typing the manuscript. Finally, I would like to acknowledge the assistance and encourage¬ ment provided by a very special person—my wife, Sue. Financial assistance for this research was provided by the United States Army Research Office. ABSTRACT The Reactions of Silicon Difluoride with Sulfur Compounds: The Silicon-Sulfur Bond by Dennis L. Williams The reactions of silicon difluoride with several sulfur containing compounds have been investigated in an attempt to synthesize compounds containing the silicon-sulfur bond. Of the previous reactions of silicon difluoride with sulfur com¬ pounds, only two, the hydrogen sulfide and sulfur reactions, produced compounds containing silicon-sulfur bonds. The products of the H2S reaction were SiF2HSH, S^FL+HSH, SiF2HSSH and S^Fi^HSSH. The reaction between SiF2 and sulfur produced both linear and cyclic fluorosilthianes. SiF2 abstracted the oxygen atom from thionyl fluoride and the chloride to form linear and cyclic halosiloxanes. -
Fluorine and Fluorides
This report contains the collective views of an international group of experts and does not necessarily represent the decisions or the stated policy of the United Nations Environment Pro- gramme, the International Labour Organisa- tion, or the World Health Organization Environmental Health Criteria 36 FLUORINE AND FLUORIDES Published under the joint sponsorship of the United Nations Environment Programme, the International Labour Organisation, and the World Health Orgaiization- World Health Organization 77, Geneva, 1984 The International Programme on Chemical Safety (IPCS) is a joint venture of the United Nations Environment Programme, the Interna- tional Labour Organisation, and the World Health Organization. The main objective of the IPCS is to carry out and disseminate evaluations of the effects of chemicals on human health and the quality of the environment. Supporting activities include the development of epidemiological, experi- mental laboratory, and risk-assessment methods that could produce inter- nationally comparable results, and the development of manpower in the field of toxicology. Other activities carried out by IPCS include the devel- opment of know-how for coping with chemical accidents, coordination of laboratory testing and epidemiological studies, and promotion of research on the mechanisms of the biological action of chemicals. ISBN 92 4 154096 6 ©World Health Organization 1984 Publications of the World Health Organization enjoy copyright protec- tion in accordance with the provisions of Protocol 2 of the Universal Copy- right Convention. For rights of reproduction or translation of WHO publica- tions, in part or in toto, application should be made to the Office of Publica- tions, World Health Organization, Geneva, Switzerland. The World Health Organization welcomes such applications.