BUDGE BUDGE GENERATING STATION (West Bengal)
Total Page:16
File Type:pdf, Size:1020Kb
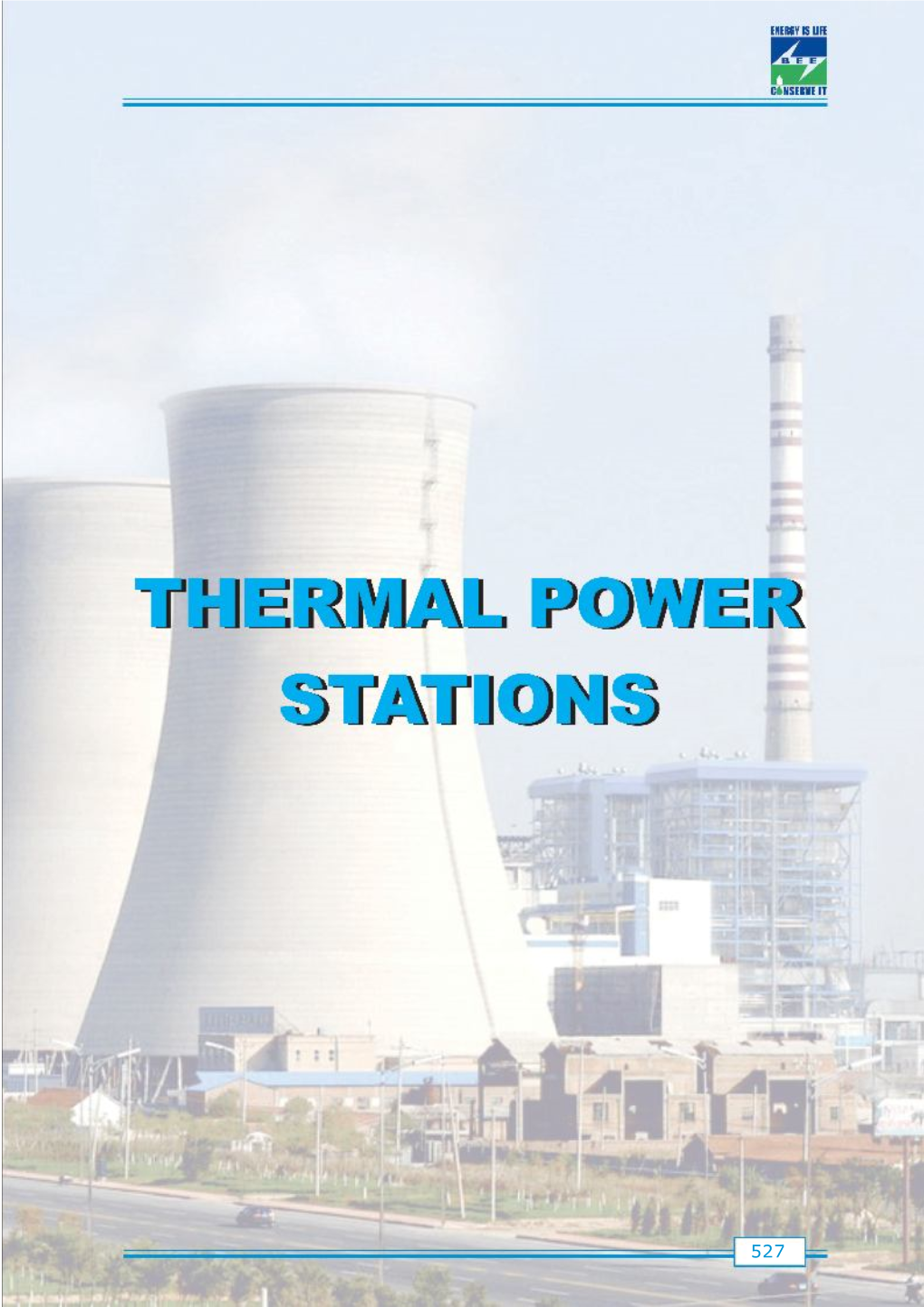
Load more
Recommended publications
-
Indiaghg-Aug15 0.Pdf
The India Greenhouse Gas (GHG) Program is a voluntary, industry-led partnership, focused on building institutional capabilities towards measuring and managing greenhouse gas emissions, based on the GHG Protocol WHO WE ARE The India GHG Program was launched in July 2013 by WRI India, The Energy and Resources Institute (TERI), and the Confederation of Indian Industry (CII), with support from India’s key businesses as founding member companies. Several progressive companies, including automotive, aviation, telecom, cement, chemicals, manufacturing, financial services, information technology, consumer, agri-business, textiles, and others are voluntary members of the Program. The total inventory managed by businesses under the India GHG Program ranges from 300 to 360 million TCO2e. This is equivalent to 15 to 25 percent of India’s total emissions. What climate change challenges does India face? While it is difficult to quantify the expected impact of climate change, a recent orldW Bank study indicates that countries like India will need USD 70 to 100 billion each year through 2050 to meet the current and future climate adaptation needs. However, our current spending is around USD 4.4 billion. The challenges, including water availability, changing rainfall patterns, resilience capabilities, disaster management, and others hold serious implications for communities, businesses, and for the country’s future growth and development. What role can the corporate sector play? Businesses are not only essential for continued economic growth, but they also have an immense opportunity in aiding large-scale reduction of emissions which can help mitigate the impacts of climate change. Approximately 38 percent of India’s greenhouse gas emissions come from energy generation and industrial and commercial users consume about 76 percent of that energy. -
Big Power Trade - Futuros National Stock Exchange of India (NSE)
BiG Power Trade - Futuros National Stock Exchange of India (NSE) País / Região Bolsa Produto Horário Futuros (Moeda, National Stock Exchange of India (NSE) Segunda-feira - Sexta-feira: Acções, Índices de 9:15-15:30 IST* Índia www.nseindia.com acções) IB Simbolo Instrumento Simbolo Moeda ACC ACC LIMITED ACC INR ADANIPOWE ADANI POWER LIMITED ADANIPOWER INR AJANTPHAR AJANTA PHARMA LTD AJANTPHARM INR ALBK ALLAHABAD BANK ALBK INR AMARAJABA AMARA RAJA BATTERIES LTD AMARAJABAT INR AMBUJACEM AMBUJA CEMENTS LIMITED AMBUJACEM INR ANDHRABAN ANDHRA BANK ANDHRABANK INR APOLLOHOS APOLLO HOSPITALS ENTERPRISE APOLLOHOSP INR APOLLOTYR APOLLO TYRES LIMITED APOLLOTYRE INR ARVIND ARVIND LTD ARVIND INR ASHOKLEY ASHOK LEYLAND LIMITED ASHOKLEY INR ASIANPAIN ASIAN PAINTS LTD ASIANPAINT INR AUROPHARM AUROBINDO PHARMA LTD AUROPHARMA INR AXISBANK AXIS BANK LTD AXISBANK INR BAJAJ-AUT BAJAJ AUTO LIMITED BAJAJ-AUTO INR BAJAJFINS BAJAJ FINSERV LTD BAJAJFINSV INR BAJFINANC BAJAJ FINANCE LTD BAJFINANCE INR BALKRISIN BALKRISHNA INDUSTRIES LTD BALKRISIND INR BALRAMCHI BALRAMPUR CHINI MILLS LTD BALRAMCHIN INR BANKBAROD BANK OF BARODA BANKBARODA INR BANKINDIA BANK OF INDIA BANKINDIA INR BANKNIFTY Nifty Bank BANKNIFTY INR BATAINDIA BATA INDIA LTD BATAINDIA INR BEL BHARAT ELECTRONICS LTD BEL INR BEML BEML LIMITED BEML INR BERGEPAIN BERGER PAINTS INDIA LTD BERGEPAINT INR BHARATFIN BHARAT FINANCIAL INCLUSION L BHARATFIN INR BHARATFOR BHARAT FORGE LIMITED BHARATFORG INR BHARTIART BHARTI AIRTEL LIMITED BHARTIARTL INR BHEL BHARAT HEAVY ELECTRICALS BHEL INR BIOCON BIOCON LTD BIOCON -
Overview of CESC - Kolkata Distribution Business
CESC Limited Powering India since 1899 1 This presentation has been prepared by and is the sole responsibility of CESC Limited (the “Company”). By accessing this presentation, you are agreeing to be bound by the trailing restrictions. This presentation does not constitute or form part of any offer or invitation or inducement to sell or issue, or any solicitation of any offer or recommendation to purchase or subscribe for, any securities of the Company, nor shall it or any part of it or the fact of its distribution form the basis of, or be relied on in connection with, any contract or commitment therefor. In particular, this presentation is not intended to be a prospectus or offer document under the applicable laws of any jurisdiction, including India. No representation or warranty, express or implied, is made as to, and no reliance should be placed on, the fairness, accuracy, completeness or correctness of the information or opinions contained in this presentation. Such information and opinions are in all events not current after the date of this presentation. There is no obligation to update, modify or amend this communication or to otherwise notify the recipient if information, opinion, projection, forecast or estimate set forth herein, changes or subsequently becomes inaccurate. Certain statements contained in this presentation that are not statements of historical fact constitute “forward-looking statements.” You can generally identify forward-looking statements by terminology such as “aim”, “anticipate”, “believe”, “continue”, “could”, “estimate”, “expect”, “intend”, “may”, “objective”, “goal”, “plan”, “potential”, “project”, “pursue”, “shall”, “should”, “will”, “would”, or other words or phrases of similar import. -
Welcome to the Bengal Chamber Family! That's What We Would Like to Convey to GEE Limited, Whose Application for Membership
Vol 15 | No. 3 February 2021 18th February, 2021 The Financial Year 2020- 2021 has indeed been a very tough and testing economy back on track with increased Govt Expenditure. Meanwhile, year, but at the same time it has been the year of immense learnings The Bengal Chamber felt that The State Vote on Account was aimed which has helped businesses, communities and individuals to emerge towards sending a strong signal towards growth and social equity in the stronger on all fronts. The Chamber during the year has been able to state. takea series of initiatives towards the long-term sustainability and has stood against several adversities. In keeping with the same theme for growth of our State on all fronts, your Chamber has embarked upon building a long-term vision plan During the last month, The Chamber held several relevant programmes, Vision Bengal 2030, which would not only be a Vision Statement, but a as you would see from the Newsletter coverage. One of the Programmes living Document with an Implementable Roll Out Plan having a core vision on e-mobility - Infrastructure, Business Readiness Strategies and Green for the decade 2020 going towards 2030 to help the private sector, jobs creation, in partnership with The British Deputy Commission, Kolkata, government, academia and civil society to reimagine and seed the creation focusing on clean transportation, which incidentally happens to be one of the business of tomorrow in West Bengal (WB) through a supportive of the key themes of COP 26. The other programmes like The Bengal ecosystem that is inclusive, equitable, resilient, sustainable and good for Fashion Heritage and Annual Shipping and Logistics Conclave, 2020 were all. -
Dun & Bradstreet Infra Awards 2017
Dun & Bradstreet Infra Awards 2017 - Project Award Winners Project Company Segment 100 MW Sainj Hydro-electric Hindustan Construction Power: Hydro-electric Project Company Limited Chenani Nashri Tunnel Road IL&FS Transportation Networks Roads & Highways Project Limited "Bhupen Hazarika Setu" - Bridge Navayuga Engineering Company Bridges Between Dhola and Sadia Ghats Limited Ganga Bridge at Km. 219+500 of Agra Lucknow Expressway Afcons Infrastructure Limited Special Mention: Bridges Project (Package IV – Kannauj to Unnao Section) Wardha - Hyderabad 765 kV DC KEC International Limited Power: Transmission Line 400KV Multi Circuit Transmission Kalpataru Power Transmission Special Mention: Power Line from Ballari Pooling station Limited to Ramapura Limits Transmission The 8.5 km “Priority Corridor” of the North-South Corridor (Phase Lucknow Metro Rail Corporation Railways - Metro Rail 1A) Waste Water Treatment Plant, VA Tech Wabag Limited Water Supply & Sanitation K&C Valley Renewable Energy - Solar Metro RESCO Solar PV Project Waaree Energies Limited Roof-Top Pre-Engineered Steel Building Kirby Building Systems India Pvt. Implementation Excellence - (PEB) Structure for Alstom Ltd Bharat Forge Pvt Ltd Industrial Buildings Implementation Excellence - Coker A Plant at Barauni Refinery Indian Oil Corporation Limited Industrial Projects 100 MW Solar Power Plant at Tata Power Solar Systems Renewable Energy - Solar Anantapur Limited Farms 100 MW Wind Energy Plant at Hero Future Energies Private Renewable Energy - Wind Ratlam Limited Dun & Bradstreet -
CESC Limited Powering India Since 1899
CESC Limited Powering India since 1899 October 2014 1 This presentation has been prepared by and is the sole responsibility of CESC Limited (the “Company”). By accessing this presentation, you are agreeing to be bound by the trailing restrictions. This presentation does not constitute or form part of any offer or invitation or inducement to sell or issue, or any solicitation of any offer or recommendation to purchase or subscribe for, any securities of the Company, nor shall it or any part of it or the fact of its distribution form the basis of, or be relied on in connection with, any contract or commitment therefor. In particular, this presentation is not intended to be a prospectus or offer document under the applicable laws of any jurisdiction, including India. No representation or warranty, express or implied, is made as to, and no reliance should be placed on, the fairness, accuracy, completeness or correctness of the information or opinions contained in this presentation. Such information and opinions are in all events not current after the date of this presentation. There is no obligation to update, modify or amend this communication or to otherwise notify the recipient if information, opinion, projection, forecast or estimate set forth herein, changes or subsequently becomes inaccurate. Certain statements contained in this presentation that are not statements of historical fact constitute “forward-looking statements.” You can generally identify forward-looking statements by terminology such as “aim”, “anticipate”, “believe”, “continue”, “could”, “estimate”, “expect”, “intend”, “may”, “objective”, “goal”, “plan”, “potential”, “project”, “pursue”, “shall”, “should”, “will”, “would”, or other words or phrases of similar import. -
FINAL DISTRIBUTION.Xlsx
Annexure-1A 1)Taxpayers with turnover above Rs 1.5 Crores a) Taxpayers falling under the jurisdiction of the Centre Taxpayer's Name SL NO GSTIN Registration Name TRADE_NAME 1 EASTERN COAL FIELDS LTD. EASTERN COAL FIELDS LTD. 19AAACE7590E1ZI 2 SAIL (D.S.P) SAIL (D.S.P) 19AAACS7062F6Z6 3 CESC LTD. CESC LIMITED 19AABCC2903N1ZL 4 MATERIALS CHEMICALS AND PERFORMANCE INTERMEDIARIESMCC PTA PRIVATE INDIA CORP.LIMITED PRIVATE LIMITED 19AAACM9169K1ZU 5 N T P C / F S T P P LIMITED N T P C / F S T P P LIMITED 19AAACN0255D1ZV 6 DAMODAR VALLEY CORPORATION DAMODAR VALLEY CORPORATION 19AABCD0541M1ZO 7 BANK OF NOVA SCOTIA 19AAACB1536H1ZX 8 DHUNSERI PETGLOBAL LIMITED DHUNSERI PETGLOBAL LIMITED 19AAFCD5214M1ZG 9 E M C LTD 19AAACE7582J1Z7 10 BHARAT SANCHAR NIGAM LIMITED BHARAT SANCHAR NIGAM LIMITED 19AABCB5576G3ZG 11 HINDUSTAN UNILEVER LIMITED 19AAACH1004N1ZR 12 GUJARAT COOPERATIVE MILKS MARKETING FEDARATION LTD 19AAAAG5588Q1ZT 13 VODAFONE MOBILE SERVICES LIMITED VODAFONE MOBILE SERVICES LIMITED 19AAACS4457Q1ZN 14 N MADHU BHARAT HEAVY ELECTRICALS LTD 19AAACB4146P1ZC 15 JINDAL INDIA LTD 19AAACJ2054J1ZL 16 SUBRATA TALUKDAR HALDIA ENERGY LIMITED 19AABCR2530A1ZY 17 ULTRATECH CEMENT LIMITED 19AAACL6442L1Z7 18 BENGAL ENERGY LIMITED 19AADCB1581F1ZT 19 ANIL KUMAR JAIN CONCAST STEEL & POWER LTD.. 19AAHCS8656C1Z0 20 ELECTROSTEEL CASTINGS LTD 19AAACE4975B1ZP 21 J THOMAS & CO PVT LTD 19AABCJ2851Q1Z1 22 SKIPPER LTD. SKIPPER LTD. 19AADCS7272A1ZE 23 RASHMI METALIKS LTD 19AACCR7183E1Z6 24 KAIRA DISTRICT CO-OP MILK PRO.UNION LTD. KAIRA DISTRICT CO-OP MILK PRO.UNION LTD. 19AAAAK8694F2Z6 25 JAI BALAJI INDUSTRIES LIMITED JAI BALAJI INDUSTRIES LIMITED 19AAACJ7961J1Z3 26 SENCO GOLD LTD. 19AADCS6985J1ZL 27 PAWAN KR. AGARWAL SHYAM SEL & POWER LTD. 19AAECS9421J1ZZ 28 GYANESH CHAUDHARY VIKRAM SOLAR PRIVATE LIMITED 19AABCI5168D1ZL 29 KARUNA MANAGEMENT SERVICES LIMITED 19AABCK1666L1Z7 30 SHIVANANDAN TOSHNIWAL AMBUJA CEMENTS LIMITED 19AAACG0569P1Z4 31 SHALIMAR HATCHERIES LIMITED SHALIMAR HATCHERIES LTD 19AADCS6537J1ZX 32 FIDDLE IRON & STEEL PVT. -
List of Exempted Establishment
LIST OF P.F. EXEMPTED ESTABLISHMENTS S.No Est. Id Est. Name 1 MHBAN0000024000 EMPIRE INDUSTRIES 2 MPJBP0001251000 UNIVERSAL CABLES LTD. 3 SRBRH0014401000 GUJARAT NARMADA VALLEY FERTILIZERS & CHEMICALS LIMITED 4 DLCPM0002805000 ALL INDIA MANAGEMENT ASSOCIATION 5 PYPNY0000964000 BHARAT ELECTRONICS LIMITED 6 SRSRT000523800B GUJARAT STATE FERTILISERS - CHEMICAL LTD 7 RJRAJ0005060000 BIRLA INSTITUTE OF TECHNOLOGY AND SCIENCE PILANI DISTT JHUNJHUNU 8 RJRAJ0001475000 RAJASTHAN STATE IND. DEV. - INVEST. CORPORATION 9 DLCPM0004398000 NESTLE INDIA LTD. 10 PYPNY0003435000 I P R I T I 11 PYKRP002341900X VOLVO INDIA PVT LTD 12 WBCAL002689100E WELLAND GOULDSMITH SCHOOL 13 PYKRP000986600X COATS INDIA LTD 14 WBPRB0028002000 STEEL AUTHORITY OF INDIA 15 DSNHP003369100E NIIT TECHNOLOGIES LTD 16 PUPUN0005674000 ATLAS COPCO [I] LTD 17 THTHA0001616000 CENTURY RAYON 18 WBCAL0026974000 WEST BENGAL POWER DEVELOPMENT CORPORATION LIMITED 19 GNGGN0009476000 DELPHI AUTOMOTIVE SYSTEM LIMITED 20 PUPUN0007319000 JAYA HIND INDUSTRIES LTD. 21 DSSHD0004360000 MOTHER DAIRY 22 PUPUN0002885000 J N MARSHALL PVT LTD 23 VDBRD0003574000 THE PANCHMAHAL DIST. CO-OP. MILK PRODUCERS 24 MHBAN000633300X HAWKINS COOKERS LIMITED 25 KRKCH0003188000 SUD-CHEMIE INDIA PVT. LIMITED 26 MRMRT0000227000 TRIVENI ENGG. - INDUSTRIES LTD. 27 VDBRD0005238000 GUJARAT STATE FERTILIZERS CO. LTD., 28 GJRAJ000523800A GSFC LTD. 29 DSNHP0007658000 NIIT LTD. 30 DSNHP0019614000 AMERICAN EXPRESS INDIA PVT LTD 31 MHBAN0020972000 HOUSING DEVELOPMENT FINANCE CORP LTD 32 GJAHD001692300E THE UMRETH URBAN CO-OPERATIVE BANK LTD. 33 MPBPL000344800A HINDUSTAN ELECTRO GRAPHITE LTD. 34 MHBAN000710800X THE MUNICIPAL CO-OP.BANK LTD. 35 BGBNG002411700X MERCEDES BENZ RESEARCH AND DEVELOPMENT INDIA PVT LTD 36 RJRAJ0001004000 GANDHI SEWA SADAN BAYANA BHARATPUR 37 UPLKO0000180000 BAJAJ HINDUSTAN LTD. 38 TNMAS0007835000 BHARAT HEAVY ELECTRICALS 39 NESHG0000941000 NORTH EASTERN ELECTRICAL POWER CORPORATION LTD 40 DSNHP0000932000 NATIONAL SMALL IND CORPN. -
1 Reliance Industries Limited 2 Tata Consultancy Services (TCS)
1 Reliance Industries Limited 2 Tata Consultancy Services (TCS) 3 Infosys Technologies Ltd 4 Wipro Limited 5 Bharti Tele-Ventures Limited 6 ITC Limited 7 Hindustan Lever Limited 8 ICICI Bank Limited 9 Housing Development Finance Corp. Ltd. 10 TATA Steel Limited 11 Ranbaxy Laboratories Limited 12 HDFC Bank Ltd 13 Tata Motors Limited 14 Larsen & Toubro Limited (L&T) 15 Satyam Computer Services Ltd. 16 Maruti Udyog Limited 17 Bajaj Auto Ltd. 18 HCL Technologies Ltd. 19 Hero Honda Motors Limited 20 Hindalco Industries Ltd 21 Reliance Energy Limited 22 Grasim Industries Limited 23 Jet Airways (India) Ltd. 24 Sun Pharmaceuticals Industries Ltd 25 Cipla Ltd. 26 Gujarat Ambuja Cements Ltd. 27 Videsh Sanchar Nigam Limited 28 The Tata Power Company Limited 29 Sterlite Industries (India) Ltd. 30 Associated Cement Companies Ltd. 31 Nestlé India Ltd. 32 Hindustan Zinc Limited 33 GlaxoSmithKline Pharmaceuticals Limited 34 Siemens India Ltd. 35 Motor Industries Company Limited 36 Mahindra & Mahindra Limited 37 UTI Bank Ltd. 38 Zee Telefilms Limited 39 Bharat Forge Limited 40 ABB Limited 41 i-Flex Solutions Ltd. 42 Dr. Reddy's Laboratories Ltd. 43 Nicholas Piramal India Limited 44 Kotak Mahindra Bank Limited 45 Reliance Capital Ltd. 46 Ultra Tech Cement Ltd. 47 Patni Computer Systems Ltd. 48 Wockhardt Limited 49 Indian Petrochemicals Corporation Limited 50 Biocon India Limited 51 Essar Oil Limited. 52 Asian Paints Ltd. 53 Dabur India Limited 54 Jaiprakash Associates Limited 55 JSW Steel Limited 56 Tata Chemicals Limited 57 Tata Tea Limited 58 Tata Teleservices (Maharashtra) Limited 59 The Indian Hotels Co. Ltd. 60 Glenmark Pharmaceuticals Limited 61 NIRMA Limited 62 Jindal Steel & Power Ltd 63 HCL Infosystems Ltd. -
~~ RP- Sanjiv Goenka , ~ Group
~~ RP- Sanjiv Goenka , ~ Group 10 July, 2020 SEC:12464 Manager (Listing) National Stock Exchange of India Limited Exchange Plaza, 5th Floor, Plot No. C/1, G- Block, Bandra - Kurla Complex, Bandra (East), Mumbai - 400 051 SCRIP CODE: CESC The Secretary Bombay Stock Exchange Limited Phiroze Jeejeebhoy Towers, Dalal Street, Mumbai - 400 001 SCRIP CODE: 500084 The Secretary The Calcutta Stock Exchange Limited 7, Lyons Range, Kolkata - 700 001 SCRIP CODE: 10000034 Dear Sir, Forty-second Annual General Meetin,: & Book Closure Further to our letter no. SEC: 12463 dated 6 July, 2020, we write to inform you that the Register of members will remain closed from 27 July, 2020 to 3 August, 2020 (both days inclusive) for the purpose of Forty-second Annual General Meeting of the Company to be held through Video Conferencing/ Other Audio Visual Means on Monday, 3 August, 2020 at 10.00 am (1ST). Copies of the Notice and Annual Report being dispatched to the shareholders are attached herewith. Yours faitj) lly, COMPANY SECRETARY Encl: CESC Limited CIN : L31901WB1978PLC031411 □ e-mai l: [email protected] Regd. Office: CESC House, Chowringhee Square, Kolkata - 700 001, India Tel : +91 33 2225 6040 Fax : +91 33 2236 3868 Web : www.cesc.co.in RP-Sanjiv Goenka Group Growing Legacies Energising Lives -Since 1899 Board of Directors Sanjiv Goenka, Chairman Shashwat Goenka, Vice Chairman Pradip Kumar Khaitan Chandra Kumar Dhanuka Rekha Sethi Kalaikuruchi Jairaj Pratip Chaudhuri Sunil Mitra Rabi Chowdhury, Managing Director (Generation) Debasish Banerjee, Managing Director (Distribution) Company Secretary Subhasis Mitra Executive Director & CFO Rajarshi Banerjee Auditors S. R. -
Stock Code Company Long Name
STOCK CODE COMPANY LONG NAME ADAPOR ADANI PORT AND SPECIAL ECONO AMBCE AMBUJA CEMENTS LTD ASIPAI ASIAN PAINTS INDIA LTD AURPHA AUROBINDO PHARMA LTD AXIBAN AXIS BANK LIMITED BAAUTO BAJAJ AUTO LIMITED BAJFI BAJAJ FINANCE LIMITED BHAAIR BHARTI AIRTEL LTD BHAINF BHARTI INFRATEL LIMITED BHAPET BHARAT PETROLEUM CORPN LTD BOSLIM BOSCH LIMITED CIPLA CIPLA LIMITED COALIN COAL INDIA LIMITED DRREDD DR REDDY'S LABORATORIES LTD EICMOT EICHER MOTORS LTD GAIL GAIL (INDIA) LIMITED HCLTEC HCL TECHNOLOGIES LIMITED HDFBAN HDFC BANK LIMITED HDFC HOUSING DEVELOPMENT FINANCE CO HERHON HERO MOTOCORP LIMITED HINDAL HINDALCO INDUSTRIES LIMITED HINLEV HINDUSTAN UNILEVER LIMITED HINPET HINDUSTAN PETROLEUM CORP ICIBAN ICICI BANK LIMITED INDBA INDUSIND BANK LIMITED INDOIL INDIAN OIL CORPORATION LIMITED INFTEC INFOSYS LTD ITC ITC LIMITED INDHO JAIN IRRIGATION SYSTEMS LTD KOTMAH KOTAK MAHINDRA BANK LTD LARTOU LARSEN AND TOUBRO LIMITED LUPIN LUPIN LIMITED MAHMAH MAHINDRA & MAHINDRA LIMITED MARUTI MARUTI SUZUKI INDIA LTD NTPC NTPC LIMITED ONGC OIL AND NATURAL GAS CORPORATIO POWGRI POWER GRID CORPORATION OF INDI RELIND RELIANCE INDUSTRIES STABAN STATE BANK OF INDIA SUNPHA SUN PHARMACEUTICAL INDUSTRIES TATMOT TATA MOTORS LIMITED TATSTE TATA STEEL LIMITED TCS TATA CONSULTANCY SERVICES LTD TECMAH TECH MAHINDRA LIMITED ULTCEM ULTRATECH CEMENT LIMITED UNIP UPL LIMITED VEDLIM VEDANTA LIMITED WIPRO WIPRO LTD YESBAN YES BANK LIMITED ZEEENT ZEE ENTERTAINMENT ENTERPRISES ACC ACC LIMITED ADAENT ADANI ENTERPRISES LIMITED ADAPOW ADANI POWER LIMITED AJAPHA AJANTA PHARMA LTD ALLBAN -
Equity Derivatives Circular No: MSE/TRD/8639/2020 Date
Department: Market Operations Segment: Equity Derivatives Circular No: MSE/TRD/8639/2020 Date: February 07, 2020 Subject: Introduction of Weekly Derivatives contracts on Stocks and SX40 Index To All Members, In terms of provisions of the Rules, Bye-Laws and Regulations of the Exchange and on the basis of approval received from SEBI; members of the Exchange are hereby notified about the introduction of Weekly Futures and Options Contracts in Equity Derivatives segment. The Exchange shall launch the following products with effect from March 2, 2020: Weekly Future & Option contracts on 140 Stocks Weekly Future & Option contracts on SX40 The Product Description and Trading Parameters of above contracts are specified in the Annexure 1. The Weekly contracts will be available for trading in the Mock Trading Session of February 8, 2020. (Refer Mock Trading Circular no. MSE/TRD/ 8621/2020 dated February 4, 2020). For any clarifications, contact Customer Service on 022-61129010 or send an email at [email protected]. For and on behalf of Metropolitan Stock Exchange of India Limited Shalini Rebeiro Asst. Vice President Registered Office: 4th Floor, Vibgyor Tower, Plot No. C-62, G Block, Opp Trident Hotel, Bandra Kurla Complex, Bandra East, Mumbai 400098 Tel.: +91-22-6112 9000 • [email protected] • www.msei.in • CIN: U65999MH2008PLC185856 Annexure 1 Weekly Equity Derivatives Contract Specifications DESCRIPTION SECURITY DESCRIPTION Instrument Type FUTSTK OPTSTK FUTIDX OPTIDX Underlying 140 140 SX40 SX40 Underlying Symbol Symbol of Symbol of SX40 SX40 Underlying Stock Underlying Stock Futures Futures (Annexure) (Annexure) Type of Option - Premium styled - Premium styled European Call and European Call Put Options and Put Options Quotation/Price Price in INR (Rs.) Price in INR (Rs.) Price in INR (Rs.) Price in INR (Rs.) Quote Tick size INR (Rs.) 0.05 INR (Rs.) 0.05 INR (Rs.) 0.05 INR (Rs.) 0.05 Strike Price - Depending on - 100 Intervals underlying price Contract trading Every Thursday of the week.