Belgian Navy Saves Big Money with Predictive Maintenance Based on Vibration Monitoring and Oil Analysis
Total Page:16
File Type:pdf, Size:1020Kb
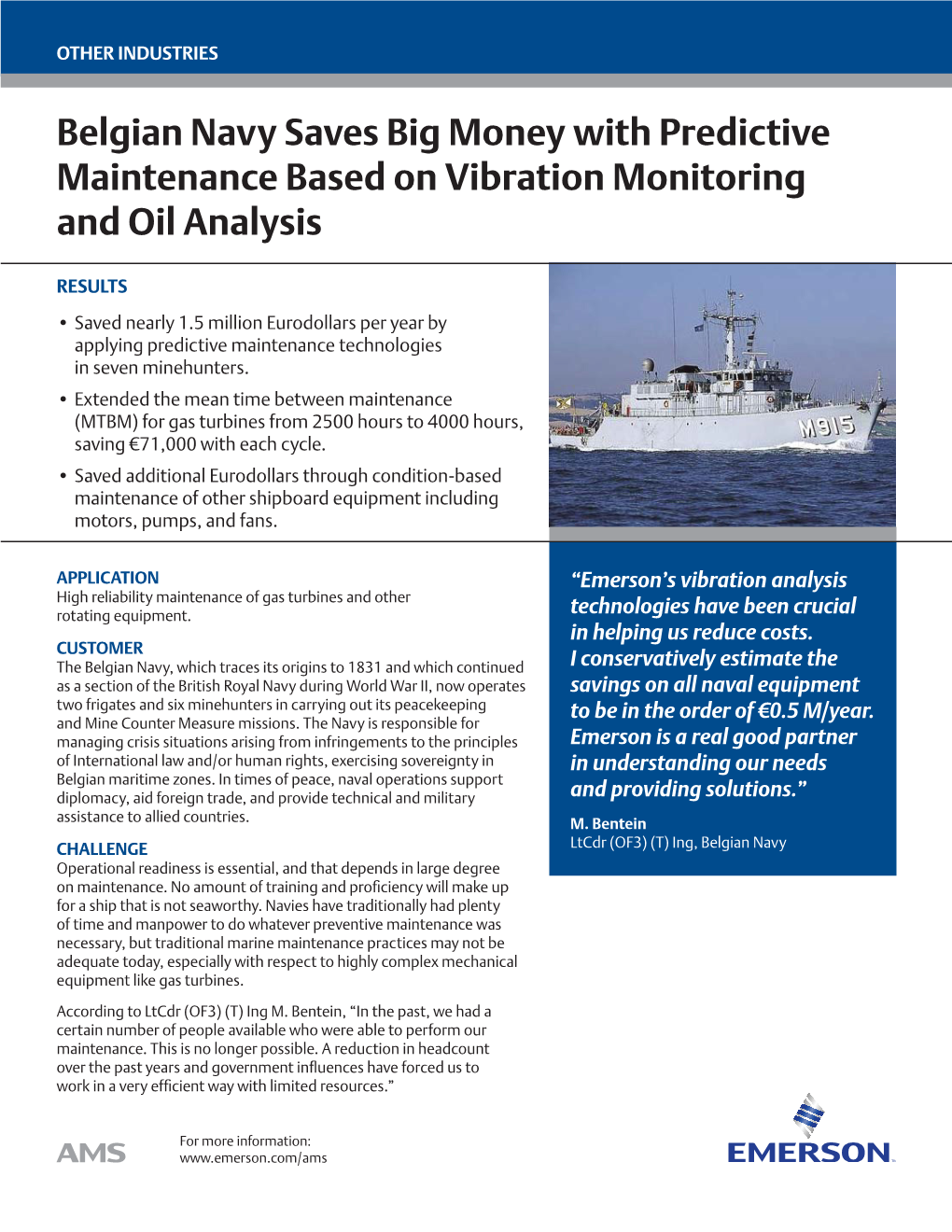
Load more
Recommended publications
-
Navy News Week 5-3
NAVY NEWS WEEK 5-3 30 January 2018 US Navy ship sails near disputed shoal claimed by China A U.S. Navy guided missile destroyer sailed within 12 miles of Scarborough Shoal, a small uninhabited reef in the South China Sea claimed by China and the Philippines, said a U.S. official. China's Foreign Ministry accused the United States of trespassing through its territorial waters. The USS Hopper carried out an "innocent passage" within 12 miles of Scarborough Shoal on Wednesday evening, said a U.S. official. The guided missile destroyer was shadowed during the operation by a Chinese Navy ship. The U.S. official described the Hopper’s patrol as an "innocent passage" and not a freedom of navigation operation (FONOP) under the strict legal definition, but "the message was the same." Under international law a nation's territorial waters extend 12 miles from its shoreline. Barely above sea level, the chain of reefs and rocks is located 120 miles west of the Philippines and is claimed by China and the Philippines. Since 2012, Chinese government ships have turned away Philippine fishing vessels near the rich fishing grounds surrounding the shoal.In 2016 an international court at The Hague ruled against China’s claim to Scarborough Shoal in a case filed by the Philippines. China's Foreign Ministry said in a statement that the Hopper had sailed within its 12 mile territorial limit "without gaining permission from the Chinese government." "What the U.S. vessel did violated China's sovereignty and security interests, put the safety of Chinese vessels and personnel who were in the relevant waters for official duties under grave threat, and contravened the basic norms for international relations," the statement added. -
Underwater-Defence-And-Security
Defence Leaders© Agenda subject to change due to speaker availability Page 1 of 21 Contents CHAIRMAN’S WELCOME NOTE ............................................................................................................................... 3 TUESDAY 3rd MARCH............................................................................................................................................... 4 PLENARY SESSION: INTERNATIONAL STRATEGY OVERVIEW .................................................................................. 4 EMERGING CHALLENGES IMPACTING UNDERWATER WARFARE ...................................................................... 4 OPENING CONFERENCE KEYNOTE FROM THE SECOND SEA LORD……………...…………………..............……….4 NEW CAPABILITY DEVELOPMENTS TO MEET EMERGING THREATS ................................................................... 5 THE EMERGENCE OF NEW TECHNOLOGIES FOR THE FUTURE OF UNDERWATER DEFENCE AND SECURITY ..... 5 UNDERWATER CONSIDERATIONS FOR FUTURE FLEETS ..................................................................................... 6 WEDNESDAY 4th MARCH ......................................................................................................................................... 7 STREAM A: MINE COUNTERMEASURES – In Association with ECA Group ............................................................. 7 CURRENT MCM CAPABILITY DEVELOPMENTS.................................................................................................... 7 OPTIMISING THE MCM TOOLBOX THROUGH OPERATIONAL -
Reference Sheet
TACTICALL NAVY REFERENCES Internal Communication External Communication TactiCall gives you complete control and fast access to all net- TactiCall is a perfect match for Task- or coalition force operations, works on board your vessel. Be it Functional Nets including teleph- including other military arms. SOF teams, air force, marine detach- ony, public address, entertainment systems and the like or Fighting ments and even civil and NGO agencies can be important players Nets handling alarms, broadcasts and orders, weapon teams or in the operation. More often than not, this setup includes a multi- mission control. tude of different frequency bands, networks and radio equipment. TactiCall will integrate all these into one simple and easy to use TactiCall is highly flexible and scalable, it is platform independent solution that permits everybody to reach each other regardless of and will integrate seamlessly into your combat management sys- equipment and technology used. tem of choice. In other words TactiCall lets you control all internal communication on board your vessel and with features such as TactiCall will allow key features for modern day operations like red/ record and playback helps you log and later analyze your commu- black separation, multi-level security operations, global public ad- nication flows. dress and allowing government or task force commanders to com- municate directly with whoever needs to be addressed in a given situation - facilitating a much smoother and more rapid “Statement of No Objections” chain. Contact Porten -
European Security and Defence
Berlin BSC Security Conference 17th Congress on European Security and Defence European Security and Defence – remaining Transatlantic, acting more European 27 – 28 November 2018 About the Congress: » One of the largest yearly events on European Security and Defence Vienna House Andel’s Berlin » Meeting place for up to 1 000 participants from more than Landsberger Allee 106 50 countries D-10369 Berlin » International forum for members of parliament, politicians and representatives of the armed forces, security organisations and www.euro-defence.eu industry » Partner in 2018: The Netherlands » Former Partners: Russia, United Kingdom, Turkey, USA, France, Sweden » Exhibition with companies from Europe and abroad » Organised by the – Germany’s leading independent Newspaper for the Civil and Military Services Advisory Board Prof Ioan Mircea Pa s¸ cu Niels Annen Michel Barnier Wolfgang Hellmich MEP, Vice-President of the European Parliament, MP, Minister of State, Chief Negotiator, Head of MP, Chairman of former Defence Minister of Romania, Congress German Federal Foreign Task Force under Article the Defence Committee, President BSC 2018 Office 50 TEU with UK, former German Bundestag Advisor of President Juncker on Security and Defence, European Commission Dr Hans-Gert Pöttering Ambassador Ji r˘ í S˘ ediv´y Dr Peter Tauber Dr Karl von Wogau Robert Walter former President of the Permanent Represen- MP, Parliamentary State Secretary General of President of the European Parliament, tative of the Czech Secretary, German Federal the Kangaroo Group, -
J Assembly of Western European Union
\&J Assembly of Western European Union DOCIIMENT 146t prh June 1995 FORTIETH ORDINARY SESSION (Third Part) European anned forces REPORT submitted on behalf of the Defence Committee by Mr.De Decker, Rapporteur ASSEMBLY OF WESTERN EUROPEAN UNION 4iI, avenue du Pr6sldent-Wlson, 7525 Paris Cedex 16 - Tel. 53.67.2.00 Docrrment 146E 12th June 1995 European armedforces REPORT ' submitted on behalf of the Defence Committee 2 by Mn De Decker, Rapporteur TABLE OF CONTENTS Pnepnce Dnar'-r RrcoumxnenoN on a European armed forces Expr-aNnronv Mguonmtnuvt submitted by Mr. De Decker, Rapporteur I. The European Corps (a) Membership (b) Relations with NATO (c) Relations with WEU (d) Missions (e) Composition (fl Training (g) Problems still to be resolved tr. ETJROFOR- EUROMARFOR (a) Goals and missions (b) Relations with NATO and WEU (c) Structure (d) Exercises Itr. The Dutch-British amphibious force (a) Missions (0) Composition (c) Relations with NATO and WEU (d) Exercises (e) New developments IV. The Allied Command Europe rapid reaction corps (ARRC) (a) Missions (0) Composition (c) Training (d) Shortcomings of the ARRC V. The Dutch-German army corps (a) Missions (b) Composition l. Adopted in committee by 13 votes to 0 with I abstention. 2. Members of the committee: Mr. Baumel (Chainnan); Mr. De Decker Mrs. Baarveld-Schlaman (Vice-Chairmen); Mr. Alloncle, Mrs. Beer, MM. Bianchi, Briane, Bito, Cox, Dees, Dumont, Femandes Marques, Mrs. Fernandez Ramiro, Ntrrll. Hardy, Hom, Jacquat, Kastanidis, Kelchtermans, La Russa, Mrs. t entz-Comette, MM. Lopez Valdivielso (Alternate: Inpez Henares), Marten, Lord Newall (Alternate: Sir Russell Johnston),lvM. Parisi, Pavlidis, P6criaux, Petruccioli (Alternate: Guidi),Reis Leite (Alter- nate: Aguiar), Scholten, Sir Dudley Smith, Nft. -
Burial Recording Mines: a Valid Technique to Study Bedform Migration and Storm Impact Above the Sea-Floor
Marine and River Dune Dynamics – MARID IV – 15 & 16 April 2013 - Bruges, Belgium Burial Recording Mines: a valid technique to study bedform migration and storm impact above the sea-floor Sonia Papili (1,2) , Thomas Wever (3) and Yves Dupont (4) 1. Belgian Navy, Zeebrugge, BE, - [email protected], 2. Ghent University, Ghent, BE - [email protected] 3. WTD 71 / FWG, Kiel, D - [email protected] 4. Belgian Navy, Zeebrugge, BE, - [email protected] Abstract Initially, Burial Recording Mines (BRMs) were used to understand the sea mine burial. It was a technique predominantly related to military purpose. The first experiment was made 1974. Now a day, it is used as a valid tool for marine science. This methodology gives the rare opportunity to observe and analyze the processes acting on the seafloor directly, making the estimation closer to the reality. During MARIDIV, we present the results of 3 months experiment using burial recording mines. The experiment was performed between September 2008 and January 2009. The Wandelaar region on the Belgian Continental Shelf was chosen as suitable test area. 10,000 measurements of the sediment height around the cylindrical object were recorded, each one of those every 15 minutes. The dataset collected, together with sediment characterization and hydrological and meteorological information, allowed the understanding of the bedform migration. During the experiment, 2 storms passed the test area, in October and November 2008. Using Burial Recording Mines gave the rare opportunity to observe and analyze the storm impact directly on the sea-floor. Processes during and after the second storm will be revealed. -
Country/Agency Organisation of CSG Representatives Website Austria Belgium Belgian Navy Belgium Federal Public Servic
Country/Agency Organisation of CSG Representatives Website Austria Belgium Belgian Navy www.mil.be Belgium Federal Public Service Mobility and Transport www.mobilit.fgov.be Bulgaria Executive Agency Maritime Administration www.marad.bg Croatia Ministry of Sea, Transport and Infrastructure https://mmpi.gov.hr/ Cyprus Shipping Deputy Ministry www.dms.gov.cy Czech Republic Denmark Estonia Estonian Police and Border Guard Board www.politsei.ee Estonia Estonian Maritime Administration www.vta.ee Finland The Finnish Border Guard www.raja.fi www.gouvernement.fr/secretariat-general-de-la-mer- France Secrétariat général de la mer (SGMer) sgmer Germany German Federal Ministry of Transport and Digital Infrastructure https://www.bmvi.de Germany German Federal Ministry of Defence https://www.bmvg.de Greece Hellenic Coast Guard www.hcg.gr Greece Hellenic Navy www.navy.mil.gr Hungary Permanent Representation of Hungary to the European Union www.kormany.hu Ireland Department of Foreign Affairs and Trade www.dfa.ie Italy Italian Navy www.marina.difesa.it Italy Italian Space Agency www.asi.it Latvia Lithuania Lithuanian Navy https://kam.lt/ Luxemburg Norway Norweigan Ministry of Transport www.regjeringen.no Norway BarentsWatch www.barentswatch.no Malta Malta Marittima Agency www.maltamarittima.org.mt Poland Ministry of Maritime Economy and Inland Navigation www.mgm.gov.pl DGRM - Directorate-General for Natural Resources, Safety and Maritime Portugal Services https://www.dgrm.mm.gov.pt/ Portugal Marinha - Portuguese Navy www.marinha.pt Romania Romanian Border -
Deep Cooperation by Belgian Defence : Absorbing the Impact of Declining Defence Budgets on National Capabilities
This item is the archived peer-reviewed author-version of: Deep cooperation by Belgian defence : absorbing the impact of declining defence budgets on national capabilities Reference: Sauer Tom.- Deep cooperation by Belgian defence : absorbing the impact of declining defence budgets on national capabilities Defence Studies - ISSN 1470-2436 - 15:1(2015), p. 46-62 DOI: http://dx.doi.org/doi:10.1080/14702436.2015.1005900 Institutional repository IRUA Deep cooperation by Belgian defence: absorbing the impact of declining defense budgets on national capabilities Pieter-Jan Parrein and Tom Sauer1 Since the end of the Cold War, Belgian Defence has been used by the Belgian government as an important tool for foreign policy. The accompanying strategic plan 2000-2015, however, that was aimed to adapt the capabilities of the armed forces to the new reality has never been seen as an essential guidance by the Belgian decision-makers. Instead, the Belgian armed forces have been adapted due to budget cuts, and only in a minor way because of strategic considerations. This has resulted in an imbalance between the budget for personnel, operating costs and investments. The result is a smaller but still broad force adapted to collective security/crisis management with land forces specialized in (medium and) light infantry tasks. The air and naval capabilities have been made suitable to the lower intensity of collective security operations although they were designed for the higher part of the violence spectrum. Interestingly, the small Belgian navy has been able to maintain its two major capabilities - maritime mine counter measures vessels, and surface combatants -. -
News from Rohde & Schwarz Number 151 (1996/II) 53
Panorama New radio stations for Belgian Navy The new radio stations installed by ciated transmitting/receiving anten- Rohde & Schwarz onboard the na is installed on the vessel platform Belgian ships Zinnia and Godetia are (FIG 2). used to ensure a permanent link between national authorities and Teletype signals from a receiver are naval forces as well as other vessels, routed through a matrix in one of the search and rescue organizations, air- three MERLIN system processors, high- craft and helicopters. These two end terminals for RTTY networks to command vessels of the Belgian NATO standard, and then output on a naval forces, which also perform printer or teleprinter. In the other direc- logistic tasks, are named after the tion, the messages coded by MERLIN two escort planes of the British Flower are sent via the transmitters. It is also Class. The two giant vessels that possible to pass on messages received were used to transport the Belgian from another vessel via MERLIN. troops of the British Royal Navy and offered to Belgium at the end The system has plenty more to offer. of WW2 are also in operation as Thanks to an automatic alarm receiving minehunters and minesweepers and system operating on the international proved to be very successful during frequency 2.182 kHz, Godetia has FIG 2 Antenna system of maritime radio station the Iraq-Iran conflict, the Gulf War an automatic distress signal. PSTN Photos: Force Navale and during a mission in Somalia. hookup is also possible so that mem- “Thanks to the excellent technical bers of the crew can ring home. -
TUESDAY 12Th OCTOBER 2021 the FUTURE of NAVAL WARFARE
TUESDAY 12th OCTOBER 2021 THE FUTURE OF NAVAL WARFARE Farnborough International Exhibition and Conference Centre, UK ‘Aligning priorities to become an interoperable force’ Global instability is focusing the lens on the maritime environment, particularly freedom of navigation and as a competed global common. Future Surface Fleet development, ensuring comprehensive Underwater Defence and Security, and maintaining world beating Submarine Technology are central to this. The combination of the three help countries to develop their maritime capabilities, ensuring freedom of navigation is not threatened and when necessary sea control and denial can be achieved. Those with both a responsibility and interest in the Naval domain need to keep abreast of developments both technical and geopolitical if advantage in this competed domain is to be maintained; failing to do so could have dire consequences. Underwater Defence & Security returns for its ninth year running alongside Submarine Technology and Future Surface Fleet, welcoming an international audience of submariners, MCM and ASW experts, surface ship operators, aviators, R&D organisations, procurements teams, academia and industry to discuss the key issues affecting this community. We thank you for making the time in your diary to attend, particularly with the current situation and look forward to hosting you in a safe, collaborative environment where we can best serve the needs of you and your organisation. 0600 – 5km run Industry sponsor slot available 0800 – Registration Hosted by Babcock International 0855 – Chairman’s opening remarks Vice Admiral (Ret’d) Duncan Potts CB, Former Commander UK Maritime Forces, Royal Navy ALIGNING UK STRATEGY AROUND A GLOBAL FORCE The importance of the maritime domain and consequently competition and potentially confrontation at sea is growing. -
MARITIME Teledyne Marine Belgian Navy Trials Recovering
MARITIME Teledyne Marine Belgian Navy trials recovering the Gavia AUV. (Copyright Teledyne Marine) Defence Procurement International - Winter 2016/17 72 MARITIME Taking The Man Out Of The Minefield The year 2016 saw significant milestones achieved in the fielding of a system of robots for mine countermeasures (MCM), which is likely to see traditional minehunter vessels in future perform more of a stand-off role. The coming months promise even more developments in terms of collaboration between different unmanned systems, but full autonomy is still some years away. By Anita Hawser he “weapon that waits”—sea are activated by a ship’s magnetic mines—are reminiscent of signature, but they are costly to acquire Tconflicts past. In World War and maintain and slow moving. II, the Germans reportedly laid “Navies don’t want to buy minehunting more than 120,000 mines and vessles any more,” remarks Dominique 30,000 minesweeping obstructors in Mallet, mine warfare business manager Northwestern Europe alone, which sunk at French company, ECA Group, which hundreds of British warships. But sea manufactures a range of robotic mine mines have been used as recently as countermeasures (MCM) solutions. the 2011 Libyan conflict and the First “They [minehunters] are not designed Gulf War, which saw hundreds of mines to go far, whereas unmanned systems laid in the waters off Kuwait and Iraq’s offer additional operational capabilities Fao peninsula. and can go far away for a long time.” During minesweeping operations in the First Gulf War, the US cruiser A SYSTEM OF ROBOTS Princeton and the helicopter carrier Navies first dipped their toes in Tripoli, were damaged by mines believed ‘robotics’ using remotely-operated to have been planted by Iraq. -
Another Example of a Mission Ready Ship Because of a U.S. Navy Port Engineer
Another example of a mission ready ship because of a U.S. Navy Port Engineer USS Gridley Joins NATO Allies in Visit to Halifax Before Joint Exercise Story Number: NNS190909-25Release Date: 9/9/2019 3:31:00 PM By Mass Communication Specialist 2nd Class Cameron Stoner, Standing NATO Maritime Group One Public Affairs HALIFAX, Nova Scotia (NNS) -- U.S. Navy guided-missile destroyer USS Gridley (DDG 101) joined allies from Standing NATO Maritime Group One (SNMG1) in a scheduled port visit to Halifax, Nova Scotia, Sept. 5-6, before exercise Cutlass Fury 2019, hosted by the Royal Canadian Navy. SNMG1 also includes Royal Norwegian Navy frigate HNoMS Thor Heyerdahl (F-314), Belgian Navy frigate Leopold I (F930), Portuguese Navy frigate NRP D. Francisco de Almeida (F334) and Royal Netherlands Navy frigate HNLMS Van Speijk (F 828). To avoid potential rough weather in Halifax Harbor resulting from Hurricane Dorian, most ships participating in Cutlass Fury 2019 departed port two days earlier than planned. Going to sea and maneuvering to avoid bad weather generally reduces the risk of damage to ships and equipment. SNMG1 is one of four standing maritime task groups composed of ships from various Allied countries. These task groups form the core maritime capabilities of NATO’s Very High Readiness Joint Task Force (VJTF). They provide a continuous maritime capability to execute NATO missions across the spectrum of operations, demonstrate solidarity, and strengthen diplomatic and professional links among Allied naval forces. For more news from Navy Public Affairs Support Element, visit www.navy.mil/local/npasehq/. Webmaster’s Note: The fourth USS Gridley (DDG-101) is the 51st Arleigh Burke-class destroyer in the United States Navy.