CFD Analysis of the Turbocharger Compressor Housing in Different Mass Flow Rate
Total Page:16
File Type:pdf, Size:1020Kb
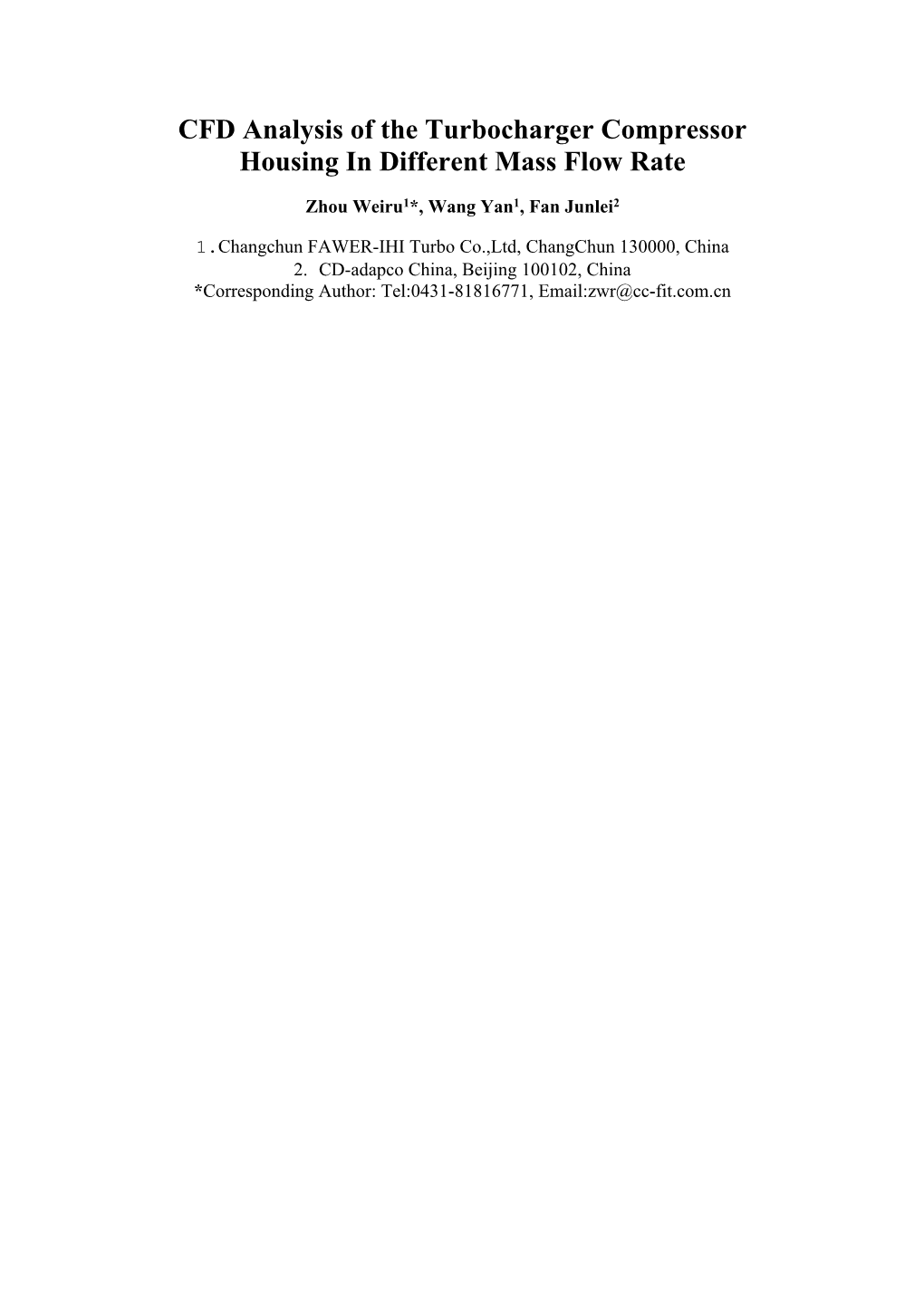
Load more
Recommended publications
-
Forced Induction Basics, Supercharging & Turbocharging; Engine Professional
EP Q2-12 10-27_Layout 1 4/19/12 11:45 AM Page 10 Forced Induction Basics BY MIKE MAVRIGIAN PHOTOS BY MIKE MAVRIGIAN UNLESS OTHERWISE NOTED Supercharging and turbocharging tidbits While this article may be a bit simplistic SUPERCHARGER BASICS for those familiar with forced induction, Superchargers (blowers) are offered in hopefully the information will be helpful three types, including the Roots type, to those who are not as experienced with centrifugal and the screw type. The Roots this approach. type is the least complex, functioning as an air pump. Instead of compressing air A naturally-aspirated engine uses inside the unit, pressurization takes place available (ambient) air to enter the in the manifold and combustion engine, mix with fuel and ignite in the chambers (referred to as external air combustion chamber. A forced induction compression). Centrifugal and screw type system (supercharger or turbocharger) superchargers compress air inside the does just what the term implies…it forces additional air into the combustion supercharger (internal compression), chamber. When mixed with the pushing the compressed air into the appropriate ratio of fuel, you create intake and combustion areas. A higher cylinder pressure, referred to as centrifugal unit mechanically functions boost, which makes more power. While much the same as a turbocharger, with an we certainly don’t have the room here to internal impeller. Instead of being driven delve into great detail, we’ll try to offer a by exhaust gas (as with a turbo), a few informational tidbits that will centrifugal supercharger impeller is hopefully help you to better understand driven mechanically by a drive belt. -
Forced Induction Technologies in an IC Engine: a Review
9 VI June 2021 https://doi.org/10.22214/ijraset.2021.35582 International Journal for Research in Applied Science & Engineering Technology (IJRASET) ISSN: 2321-9653; IC Value: 45.98; SJ Impact Factor: 7.429 Volume 9 Issue VI Jun 2021- Available at www.ijraset.com Forced Induction Technologies in an IC Engine: A Review Ranaji Arib Hafiz Ayyub Akbar Ahmedi PG Student, Heat Power Engineering Department, Shri Shankarprasad Agnihotri College of Engineering, Wardha, India Abstract: This study has been undertaken to show the performance enhancement of engines using different Forced induction technologies. Forced induction technology like turbocharging and supercharging can enhance the performance of an internal combustion engine by compressing inlet air charge, allowing full engine power to be produced efficiently. As the fuel economy and greenhouse emission standards are projected to be far more stringent globally, the use of a Forced induction engine in passenger cars and light-duty trucks has become an inevitable trend within the automotive industry. A turbocharger system can effectively improve the power and torque of an engine, but turbo hysteresis exists. A mechanical supercharging system can boost at low speed, but the efficiency is lower. An electric supercharger can effectively improve the intake air at the early stage of accelerated working conditions, however, an electric supercharger will consume the engine power. The addition of Forced induction technologies to an IC engine helps with the scope of downsizing it. This review brings forward all the aspects of Forced induction technologies Keywords: Forced Induction, Internal Combustion Engine, Turbocharging, Supercharging, Downsizing, Efficiency & Horsepower I. INTRODUCTION Forced induction technology enhances the performance of an internal combustion engine by compressing inlet air charge, allowing full engine power to be produced efficiently. -
Compression Ring Gaps for High Performance Engines
ACL TECH TALK COMPRESSION RING GAPS FOR HIGH PERFORMANCE ENGINES Piston rings are usually pre-gapped to a formula related to the bore size of the engine. For normal road engines the ring gaps are 0.003” to 0.005” per inch of bore diameter plus 0.001”. So for a 4” bore V8 engine the compression ring gaps could be as small as 0.013” to 0.021” Metric equivalents are shown in the table below. The table shows typical minimum compression ring gap recommendations imperial and metric units. The figures must be taken as a guide only for any performance application since there are many possibilities in terms of usage and the extent of modifications, fuel used and whether turbo or supercharged. Imperial (inch) Metric (mm) Imperial (inch) Metric (mm) Nominal bore size 3 76.2 4 101.6 Standard engine .010 0.25 .012 0.30 Moderate output “street” performance .016 0.40 .021 0.53 engine High output performance or marine .018 0.45 .025 0.63 engine There are several reasons why piston ring gap specification may need to be changed for an engine being modified for higher output. Generally these engines require more gap in order to prevent the rings from butting. Here are some factors, which can affect ring gap 1. As output increases the heat flow through the piston increases. 2. If the rings are placed high in the piston (i.e. a short or narrow ring land) they will be exposed to higher temperatures than if the top ring land is longer (wider). -
Electric Boosting and Energy Recovery Systems for Engine Downsizing
energies Review Electric Boosting and Energy Recovery Systems for Engine Downsizing Mamdouh Alshammari 1,2, Fuhaid Alshammari 2 and Apostolos Pesyridis 1,* 1 Centre of Advanced Powertrain and Fuels (CAPF), Department of Mechanical, Aerospace and Civil Engineering, Brunel University London, Middlesex UB8 3PH, UK; [email protected] 2 Department of Mechanical Engineering, University of Hai’l, Hail 55476, Saudi Arabia; [email protected] * Correspondence: [email protected] Received: 31 October 2019; Accepted: 4 December 2019; Published: 6 December 2019 Abstract: Due to the increasing demand for better fuel economy and increasingly stringent emissions regulations, engine manufacturers have paid attention towards engine downsizing as the most suitable technology to meet these requirements. This study sheds light on the technology currently available or under development that enables engine downsizing in passenger cars. Pros and cons, and any recently published literature of these systems, will be considered. The study clearly shows that no certain boosting method is superior. Selection of the best boosting method depends largely on the application and complexity of the system. Keywords: engine downsizing; electrically assisted turbocharger; electric supercharger; e-turbo; waste heat recovery; turbocharging; supercharging; turbocompounding; organic Rankine cycle 1. Introduction Although internal combustion engines are getting more efficient nowadays, still the major part of fuel energy is transformed into wasted heat. In terms of harmful exhaust emissions, the transportation sector is responsible for the one-third of CO2 emissions worldwide and approximately 15% of the overall greenhouse gas emissions [1]. Moreover, owing to the limited amount of fossil fuels, prices fluctuate significantly, with consistent general rising trends, resulting in economic issues in non-oil-producing countries. -
Supercharged Miata Determining the Effects of A
Supercharged Miata Determining the Effects of a Supercharger on a Spark Ignition Engine. By Carter Breckenridge and Niall Lynch 1 Supercharged Miata Determining the effects of a supercharger on a spark ignition engine. A Major Qualifying Project Submitted to the faculty of WORCESTER POLYTECHNIC INSTITUTE In partial fulfillment of the requirements for the Degree of Bachelor of Science By Carter Breckenridge Niall Lynch Adviser: Professor Robert Daniello Worcester Polytechnic Institute 20 October 2020 2 Table of Contents Table of Contents………………………………………………………………………………….3 Table of Figures…………………………………………………………………………………...5 1 Abstract………………………………………………………………………………………….6 2 Background……………………………………………………………………………………...7 2.1 History of the Internal combustion engine…………………………………………………….7 2.2 Four Stroke Engine……………………………………………………………………………8 2.2.1 Diesel Engine and Spark Ignited engines…………………………………………………...9 2.2.2 Engine Power and Fuel Efficiency……………………………………………………...…10 2.3 Turbo Charger………………………………………………………………………………..11 2.3.1 Turbo Function……………………………………………………………………………..11 2.3.2 Turbo Setup………………………………………………………………………………...11 2.3.3 Effects of a Turbocharger on an Engine…………………………………………………...12 2.3.4 Choosing a Turbocharger…………………………………………………………………..14 2.4 Supercharger…………………………………………………………………………………15 2.4.1 Roots Supercharger………………………………………………………………………...16 2.4.2 Twin Screw Supercharger………………………………………………………………….16 2.4.3 Centrifugal Supercharger…………………………………………………………………..17 2.4.4 Effects of a Supercharger on an Engine……………………………………………………17 2.4.5 -
Chapter 26 Engine Diagnosis
A8 Engine Performance 4th Edition Chapter 12 Turbocharging and Supercharging Opening Your Class KEY ELEMENT EXAMPLES Introduce Content This course or class covers operation and service ofAutomotive Engine Performance. It correlates material to task lists specified by ASE and NATEF. Motivate Learners Explain how the knowledge of how something works translates into the ability to use that knowledge to figure why the engine does not work correctly and how this saves diagnosis time, which translates into more money. State the learning Explain the chapter learning objectives to the students. objectives for the chapter 1. Prepare for Engine repair (A1) ASE certification test content or course you are about to cover and explain this is area “D” (Lubrication and Cooling Systems Diagnosis and what they should be able Repair). to do as a result of 2. Describe how coolant flows through an engine. attending this session or 3. Discuss the operation of the thermostat. class. 4. Explain the purpose and function of the radiator pressure cap. 5. Describe the various types of antifreeze and how to recycle and discard used coolant. 6. Discuss how to diagnose cooling system problems. Establish the Mood or Provide a WELCOME, Avoid put downs and bad jokes. Climate Complete Essentials Restrooms, breaks, registration, tests, etc. Clarify and Establish Do a round robin of the class by going around the room and having Knowledge Base each student give their backgrounds, years of experience, family, hobbies, career goals, or anything they want to share. ICONS Ch12 Turbocharging and Supercharging 1. SLIDE 1 CH8 Turbocharging and Supercharging Check for ADDITIONAL VIDEOS & ANIMATIONS @ http://www.jameshalderman.com/ WEB SITE REGULARLY UPDATED POWER POINTS DONE BY INDIVIDUAL LEARNING OBJECTIVES, SO THERE IS POWER POINT FILE FOR EACH LEARNING OBJECTIVE 2. -
Holley GM LS1/2/6 Lo-Ram Modular Intake Manifold Kit
Holley GM LS1/2/6 Lo-Ram Modular Intake Manifold Kit 300-620 LS1/2/6 Lo-Ram Complete Intake Manifold Kit, Satin Finish (As Shot-Blast Aluminum): -Base Intake Manifold - Top-Feed Plenum, Single Fuel Injector per cylinder -Fuel Rail Kit – Single Fuel Injector per Cylinder, Black Anodized -Plenum Top – Hi-Ram EFI, 1 x 105mm LS Throttle Body (longitudinal mount) INSTALLATION INSTRUCTIONS 199R11813 (Before installation, please read these instructions completely.) NOTE: Holley EFI LS main harnesses have a map sensor connecter designed for use with an LS1/2 style map sensor. The 558-416 is an adapter harness that can be used to adapt any LS harness that uses a LS1/2 MAP sensor connection to a LS3 MAP, which is recommended for this manifold. APPLICATIONS: The Holley LS1/2/6 Lo-Ram intake manifold kits are designed for GM LS Gen III and IV engines equipped with GM LS1/2/6 (cathedral port) cylinder heads. These intake manifolds will work with OE or aftermarket cylinder heads as long as the head is made with the intake flange bolt pattern and intake port opening locations matching the OE LS1/2/6 cathedral port configuration. The Lo-Ram intake manifolds are designed mainly for forced induction (supercharged or turbocharged) engine applications. The base intake manifold is designed with a low height to aid the packaging of a plenum mounted air-to-water intercooler in a top-feed configuration or to fit under a stock or mildly modified hood in the front-feed configuration. Due to the modular design of the LS1/2/6 Lo-Ram intake manifold there are different configurations that can be built-up depending on the customer requirements. -
Engine Coolant Co-11
ENGINE COOLANT 4. Check drained engine coolant for contaminants such as rust, corrosion or discoloration. If contaminated, flush the engine cooling system. Refer to CO-12, "FLUSHING COOLING SYSTEM" . A REFILLING ENGINE COOLANT 1. Install reservoir tank, and radiator drain plug. CO CAUTION: Be sure to clean drain plug and install with new O-ring. Radiator drain plug: C : 0.78 - 1.6 N·m (0.08 - 0.16 kg-m, 7 - 14 in-lb) If cylinder block drain plugs are removed, close and tighten them. Refer to EM-114, "ASSEMBLY" . 2. Remove air relief plug on heater hose. D E F G PBIC0894E 3. Fill radiator and reservoir tank to specified level. ● Pour engine coolant through engine coolant filler neck H slowly of less than 2 (2-1/8 US qt, 1-3/4 lmp qt) a minute to allow air in system to escape. ● Use Genuine Nissan Long Life Antifreeze/ Coolant or I equivalent mixed with water (distilled or demineralized). Refer to GI-47, "RECOMMENDED CHEMICAL PRODUCTS AND SEALANTS" . J Engine coolant capacity (Approximate) (with reservoir tank at “MAX” level) SMA182B : 8.7 (9-1/4 US qt, 7-5/8 lmp qt) K Reservoir tank capacity (at “MAX” level) L : 0.8 (7/8 US qt, 3/4 lmp qt) ● When engine coolant overflows air relief hole on heater hose, install air relief plug with new O-ring. M Air relief plug: : 0.78 - 1.6 N·m (0.08 - 0.16 kg-m, 7 - 14 in-lb) SMA412B 4. Warm up engine to normal operating temperature with radiator cap installed. -
Turbocharging and Supercharging Supercharger Potential
Supercharger potential Supercharger market potential not blown out of proportion – supplier The market leader in automotive supercharging believes there is a new lease of life in store for the supercharger urbocharging has become a well-established Tstrategy to improve the performance, efficiency and cleanliness of an internal combustion engine (ICE), but the supercharger has yet to benefit from the gust of mass-market demand. The price of a turbocharger Both technologies are forms of forced induction, with a today has almost reached preamble to push greater air density into the engine. the point of a commodity But while traditional turbochargers run off exhaust gas, the supercharger is belt-driven and suffers limited ‘lag’ - Dan Ouwenga, Engineering Manager, Boosting, Eaton when accelerating. At a basic level, superchargers are “ also generally simpler to integrate into an ICE in comparison to a turbocharger. With a similar function and benefits, why then has the supercharger seen less automotive supercharger market to grow at a CAGR of success in the market? 14.34% between 2017 and 2021. Economy of scale accounts for a significant part of the Indeed, Brian Contat, Product Director of Boosting at equation. The simple fact is that the size of the turbo Eaton, is similarly optimistic on the outlook for market provides a scale benefit with which supercharging. “The supercharger is evolving in its supercharger technology struggles to compete. “The application,” he said. “We are at a transition point price of a turbocharger today has almost reached the where the traditional uses of a supercharger – which point of a commodity,” noted Dan Ouwenga, were for performance and transient response – are Engineering Manager, Boosting at Eaton. -
Simply Unstoppable Solidly Built, Simple to Use and Ready for Any Task
70 | 80 | 90 | 100 Simply unstoppable Solidly built, simple to use and ready for any task. The perfect all-rounder! SAME has updated its historic Argon range with trac- tors that are even more powerful than before, offering even better performance and packed with state of the art technology. For over 20 years, the Argon range has offered the smallest and most agile tractors in the SAME family for open field tasks, with practical and simple but effective solutions. These are the definitive multi-role machines: as well as being the perfect choice as an addition to the existing equipment pool of a medium to large scale farm, their extraordinary versatility and adaptability, and ability to tackle a wide variety of different tasks, also make them ideal as the main tractor for a smaller farm. The revised SAME Argon range consists of 4 models, available as 2WD and 4WD versions and with power outputs from 65 to 97 HP (48-71 kW). A high-tech, compact ENGINE compliant with the latest emissions control regulations. The latest technology at your service The beating heart of the new SAME Argon range is the innovative 3 cylinder FARMotion engine. The compact size of this engine accentuates the inherent- ly outstanding agility of these machines without sacrificing performance. The viscostatic fan, turbo-intercooler forced induction and, above all, the common rail injection system with injection pressures up to 2,000 bar contribute to the class-beating fuel economy of these tractors. The avant-garde FARMotion en- gine achieves compliance with Stage III B emissions regulations with just a DOC catalytic converter, while offering torque and power delivery tailored specifical- ly for farming applications. -
What Is a Forced Induction Interchiller?
Turning any temperature into freezing cold winter! Race Track Safe Improves fuel consumption No condensation leaks Gain back ignition timing Below ambient intake air temps Stealthy Installation 0c (32f) or less intake air temps No cutting into the car No performance loss with cabin AC Patent Pending Design Dyno and race track proven HP gains Entire System Warranty Protects engine from pre ignition Great Customer Support Thank you for your enquiry about purchasing one of our Forced Induction Interchiller Systems. We provide full customer/technical support to all installations, we are only a phone call or email away The Interchiller system includes every nut and bolt you will require we even include highly detailed step by step photo and Video instructions. Yes this is condensation that has turned into ice on the intercooler fluid lines of a Magnuson Heartbeat supercharger. What is a Forced Induction Interchiller? In simple terms we are T-Piecing into the cars AC system and the refrigerant is being split 50/50 between the cabin AC and our interchiller. Our interchiller has a patent pending design for its distribution of refrigerant into the core, which is one of the reasons why we are able to get so cold. The core is made up of 2 channels each consisting of 20 plates, in the first channel your intercooler fluid flows through, in the second your AC which supercools your intercooler fluid extremely cold as low as minus -15c (5f) the cabin AC is not affected if anything it is colder than stock since we almost double the refrigerant capacity of the system. -
Catalog Download
WWW.ROSSPISTONS.COM WWW.FACEBOOK.COM/ROSSPISTONS | SINCE 1979 RACING PERFORMANCE IMPORT CLASSICS ANTIQUES DIESEL TRACTOR PULLING MARINE World Class Piston Manufacturer ROSS PISTONS YES. WE HAVE A PISTON FOR THAT! Drawing on over 35 years of piston design and manufacturing for all forms of motor sports, ROSS Racing Pistons has met the continual need for the most advanced forged pistons in the racing industry. Utilizing some of the most sophisticated design and analysis software, along with ultra modern CNC machining centers, ROSS has developed the most sophisticated line of piston forgings in the performance industry. TABLE OF CONTENTS SECTION PAGE Import / Sport Compact 04 - 07 Chevy Small Block / LS 08 - 16 Chevy Big Block 17 - 22 Chrysler 23 - 25 Ford 26 - 31 Custom Pistons 32 - 39 Rings 40 - 43 Wrist Pins 44 - 45 Piston Accessories 46 - 47 CONTACT US PHONE: 310.536.0100 FAX: (310)536-0333 WEBSITE www.rosspistons.com FACEBOOK facebook.com/RossPistons E-MAIL [email protected] 02 World Class Piston Manufacturer ROSS PISTONS IF YOU CAN RACE IT WE HAVE THE PISTON FOR IT. ROSS Racing Pistons began production of high-end forged aluminum racing pistons in 1979. In an era where most manufacturing factories have been gobbled up by large multinational holding companies, our founder, Ken Roble continues to work full time at ROSS and oversee the day to day operations of the company. SINCE1979 DID YOU KNOW? Over 25% of our work force has been with the company for over 10 years! And, several Ross Pistons team leaders have been with Ross for over 25 years.