Turbocharging Facts
Total Page:16
File Type:pdf, Size:1020Kb
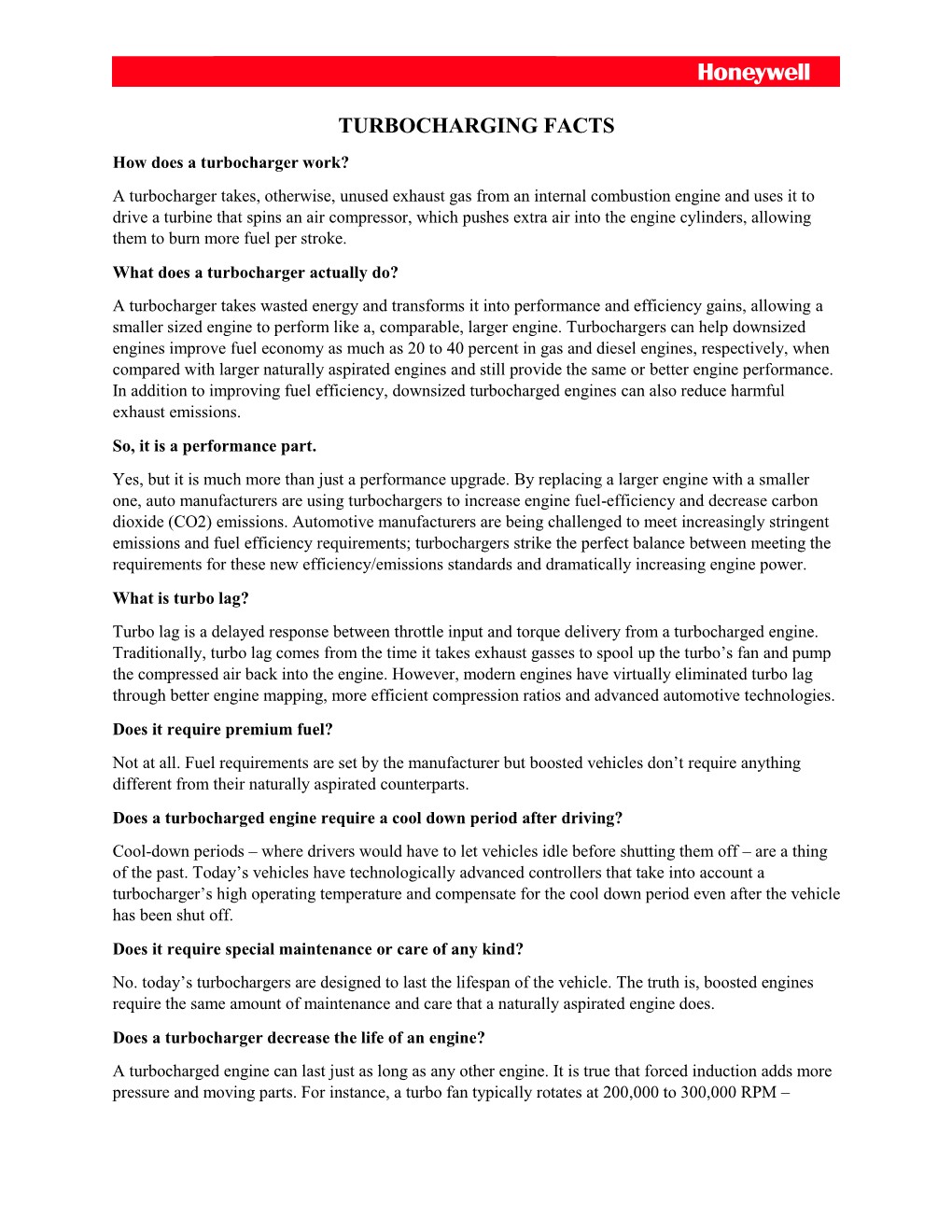
Load more
Recommended publications
-
Bentley Mulsanne Turbo and Turbo R Turbocharging System
Bentley Mulsanne Turbo and Turbo R Turbocharging System Extracts from Workshop Manuals TSD4400, TSD 4700, TSD4737 Basic Principles of Operation – Systems with Solex 4A-1 Carburettor The turbocharger is fitted to increase the power, and especially the low engine speed torque, of the engine. This it achieved by utilising the exhaust gas flow to pump pressurised air into the engine at wide throttle openings. Whenever this occurs, the turbocharger applies boost to the induction system. Under most conditions, the motor runs under naturally-aspirated principles. The inlet manifold may be under partial vacuum but the pressure chest partially pressurised under conditions of moderate power demand. The size of the turbocharger has been carefully chosen to give a substantial increase in torque at low engine speeds. The turbocharger is especially effective from 800rpm, with the engine achieving full torque at less than 1800RPM. Thus, maximum engine torque is available constantly between 1800RPM and 3800 RPM. By comparison to most turbocharging systems, the turbocharger capacity may appear decidedly oversized. This selection is intentional, and is fundamental to the achievement of full engine torque at low engine speeds and the absence of any noticeable delay when boost is demanded. It also minimises heating of exhaust gases by ensuring minimal resistance to gas flow under boost conditions. Furthermore, the design has been carefully chosen to avoid the need for the turbocharger to accelerate on demand, a feature commonly referred to as spool-up. By using a large turbocharger running but unloaded when not under demand, spool-up is not a phenomenon in the system. -
Diesel Turbo-Compound Technology
Diesel Turbo-compound Technology ICCT/NESCCAF Workshop Improving the Fuel Economy of Heavy-Duty Fleets II February 20, 2008 Volvo Powertrain Corporation Anthony Greszler Conventional Turbocharger What is t us Compressor ha Turbocompound? Ex Key Components of a Mechanical Turbocompound t us ha System Ex Conventional Turbocharger Turbine Axial Flow Final Gear Power reduction to Turbine crankshaft Speed Reduction Gears Fluid Coupling Volvo D12 500TC Volvo Powertrain Corporation Anthony Greszler How Turbocompound Works • 20-25% of Fuel energy in a modern heavy duty diesel is exhausted • By adding a power turbine in the exhaust flow, up to 20% of exhaust energy recovery is possible (20% of 25% = 5% of total fuel energy) • Power turbine can actually add approximately 10% to engine peak power output • A 400 HP engine can increase output to ~440 HP via turbocompounding • However, due to added exhaust back pressure, gas pumping losses increase within the diesel, so efficiency improvement is less than T-C power output • Maximum total efficiency improvement is 3-5% • Turbine output shaft is connected to crankshaft through a gear train for speed reduction • Typical maximum turbine speed = 70,000 RPM; crankshaft maximum = 1800 RPM • An isolation coupling is required to prevent crankshaft torsional vibration from damaging the high speed gears and turbine Volvo Powertrain Corporation Anthony Greszler Turbocompound Thermodynamics • When exhaust gas passes through the turbine, the pressure and temperature drops as energy is extracted and due to losses • The power taken from the exhaust gases is about double compared to a typical turbocharged diesel engine • To make this possible the pressure in the exhaust manifold has to be higher • This increases the pump work that the pistons have to do • The net power increase with a turbo-compound system is therefore about half the power from the second turbine • E.G. -
Intake Throttle and Pre-Swirl Device for LP EGR Systems
Intake Throttle and Pre-swirl Device for Low-pressure EGR Systems Knowledge Library Knowledge Library Intake Throttle and Pre-swirl Device for Low-pressure EGR Systems Low-pressure EGR systems to reduce emissions are state of the art for diesel engines. They offer efficiency benefits compared to high-pressure EGR systems and will gain further importance. BorgWarner shows the potential of a so-called Inlet Swirl Throttle to make use of the losses and turn them into a pre-swirl motion of the intake air entering the turbocharger to improve the aerodynamics of the compressor. By Urs Hanig, Program Manager for PassCar Systems at BorgWarner and a member of BorgWarner’s Corporate Advanced R&D Organisation Technology to meet future Emission the compressor. Obviously, pre-swirl will have a Standards positive impact on the compressor also in are- Low-pressure EGR systems (LP EGR sys- as where no throttling is required. So the IST tems), see Figure 1 , for gasoline engines yield can be used to improve engine efficiency and significant fuel consumption benefits, they are performance also in regions where no throttling also an important technology to meet future or EGR is required. emission standards (e.g. Real Driving Emissi- ons) [1 ]. To achieve the targeted EGR rates in Approach and Modes of Operation particular on diesel engines throttling the LP With IST the throttling effect is achieved by ad- EGR path is necessary in some areas of the justable inlet guide vanes in the fresh air duct. engine operating map. This can be done either In other words, IST is an intake throttle desi- on the exhaust or the intake side but to throttle gned as a compressor pre-swirl device. -
Forced Induction Basics, Supercharging & Turbocharging; Engine Professional
EP Q2-12 10-27_Layout 1 4/19/12 11:45 AM Page 10 Forced Induction Basics BY MIKE MAVRIGIAN PHOTOS BY MIKE MAVRIGIAN UNLESS OTHERWISE NOTED Supercharging and turbocharging tidbits While this article may be a bit simplistic SUPERCHARGER BASICS for those familiar with forced induction, Superchargers (blowers) are offered in hopefully the information will be helpful three types, including the Roots type, to those who are not as experienced with centrifugal and the screw type. The Roots this approach. type is the least complex, functioning as an air pump. Instead of compressing air A naturally-aspirated engine uses inside the unit, pressurization takes place available (ambient) air to enter the in the manifold and combustion engine, mix with fuel and ignite in the chambers (referred to as external air combustion chamber. A forced induction compression). Centrifugal and screw type system (supercharger or turbocharger) superchargers compress air inside the does just what the term implies…it forces additional air into the combustion supercharger (internal compression), chamber. When mixed with the pushing the compressed air into the appropriate ratio of fuel, you create intake and combustion areas. A higher cylinder pressure, referred to as centrifugal unit mechanically functions boost, which makes more power. While much the same as a turbocharger, with an we certainly don’t have the room here to internal impeller. Instead of being driven delve into great detail, we’ll try to offer a by exhaust gas (as with a turbo), a few informational tidbits that will centrifugal supercharger impeller is hopefully help you to better understand driven mechanically by a drive belt. -
CHARACTERIZATION of TURBOCHARGER PERFORMANCE and SURGE in a NEW EXPERIMENTAL FACILITY
CHARACTERIZATION of TURBOCHARGER PERFORMANCE and SURGE in a NEW EXPERIMENTAL FACILITY Thesis Presented in Partial Fulfillment of the Requirements for the Degree Master of Science in the Graduate School of The Ohio State University By Gregory David Uhlenhake, B.S. Graduate Program in Mechanical Engineering The Ohio State University 2010 Master‟s Examination Committee: Dr. Ahmet Selamet, Advisor Dr. Rajendra Singh Dr. Philip Keller Copyright by Gregory David Uhlenhake 2010 ABSTRACT The primary goal of the present study was to design, develop, and construct a cold turbocharger test facility at The Ohio State University in order to measure performance characteristics under steady state operating conditions and to investigate surge for a variety of automotive turbocharger compression systems. A specific turbocharger is used for a thermodynamic analysis to determine facility capabilities and limitations as well as for the design and construction of the screw compressor, flow control, oil, and compression systems. Two different compression system geometries were incorporated. One system allowed performance measurements left of the compressor surge line, while the second system allowed for a variable plenum volume to change surge frequencies. Temporal behavior, consisting of compressor inlet, outlet, and plenum pressures as well as the turbocharger speed, is analyzed with a full plenum volume and three impeller tip speeds to identify stable operating limits and surge phenomenon. A frequency domain analysis is performed for this temporal behavior as well as for multiple plenum volumes with a constant impeller tip speed. This analysis allows mild and deep surge frequencies to be compared with calculated Helmholtz frequencies as a function of impeller tip speed and plenum volume. -
Boosting Your Knowledge of Turbocharging
Reprinted with permission from Aircraft Maintenance Technology, July 1999 BoostingBoosting YourYour KnowledgeKnowledge ofof TurbochargingTurbocharging (Part 1 of a 2 part Series) By Randy Knuteson short 15 years after Orville fully boosted this 350 hp Liberty engine to a strength of blowers being tested during and Wilbur made their his- remarkable 356 hp (a normally aspirated engine WWII. The B-17 and B-29 bombers along toric flight at Kitty Hawk, would only develop about 62 percent power at with the P-38 and P-51 fighters were all fit- General Electric entered the this altitude). ted with turbochargers and controls. Aannals of aviation history. In 1918, GE strapped An astounding altitude record of 38,704 Turbocharging had brought a whirlwind of an exhaust-driven turbocharger to a Liberty feet was achieved three years later by Lt. J.A. change to the ever-broadening horizons of engine and carted it to the top of Pike’s Peak, Macready. flight. CO — elevation 14,000 feet. There, in the crys- This new technology began immediately Much of the early developments in recip talline air of the majestic Rockies, they success- experiencing a rapid evolution with the full turbocharging came as a result of demands Aircraft Maintenance Technology • OCTOBER 1999 2 Recip Technology from the commercial industrial diesel engine market. It wasn’t until the mid-1950s that this Percentage of HP Available At Altitude technology was seriously applied to general avi- 100% ation aircraft engines. It all started with the pro- totype testing of an AiResearch turbocharger for 90% Turbocharge the Model 47 Bell helicopter equipped with the Franklin 6VS-335 engine. -
Forced Induction Technologies in an IC Engine: a Review
9 VI June 2021 https://doi.org/10.22214/ijraset.2021.35582 International Journal for Research in Applied Science & Engineering Technology (IJRASET) ISSN: 2321-9653; IC Value: 45.98; SJ Impact Factor: 7.429 Volume 9 Issue VI Jun 2021- Available at www.ijraset.com Forced Induction Technologies in an IC Engine: A Review Ranaji Arib Hafiz Ayyub Akbar Ahmedi PG Student, Heat Power Engineering Department, Shri Shankarprasad Agnihotri College of Engineering, Wardha, India Abstract: This study has been undertaken to show the performance enhancement of engines using different Forced induction technologies. Forced induction technology like turbocharging and supercharging can enhance the performance of an internal combustion engine by compressing inlet air charge, allowing full engine power to be produced efficiently. As the fuel economy and greenhouse emission standards are projected to be far more stringent globally, the use of a Forced induction engine in passenger cars and light-duty trucks has become an inevitable trend within the automotive industry. A turbocharger system can effectively improve the power and torque of an engine, but turbo hysteresis exists. A mechanical supercharging system can boost at low speed, but the efficiency is lower. An electric supercharger can effectively improve the intake air at the early stage of accelerated working conditions, however, an electric supercharger will consume the engine power. The addition of Forced induction technologies to an IC engine helps with the scope of downsizing it. This review brings forward all the aspects of Forced induction technologies Keywords: Forced Induction, Internal Combustion Engine, Turbocharging, Supercharging, Downsizing, Efficiency & Horsepower I. INTRODUCTION Forced induction technology enhances the performance of an internal combustion engine by compressing inlet air charge, allowing full engine power to be produced efficiently. -
Development of an Improve Turbocharger Dynamic Seal
Development of an Improved Turbocharger Dynamic Seal Matthew J Purdeya,1 a) Cummins Turbo Technologies St Andrews Road, Huddersfield, HD1 6RA Abstract: Emissions regulation continually drives the automotive industry to innovate and develop. The industry must push the limits of engine/ turbocharger interaction to meet this changing regulation. Changes to the way a turbocharger is used, to help meet emission regulation, can impact the pressure balance over the compressor and turbine end seals. Seal capability can place constraints on the acceptable operating conditions. Market trends indicate that, in the near future, turbocharger operating conditions will be challenging for today’s compressor side seal systems. The need for improved compressor end sealing is greater than ever. This market intelligence drove Cummins Turbo Technologies to develop a robust seal system that meets the future demands of our customers. There are many benefits to the slinger/ collector seals systems used today and cutting-edge analysis has helped us generate the next level of understanding required to unleash further performance. This report gives insight to the market requirements and the approach to developing a seal to meet this need. Key Words: Turbocharger Seal, Multiphase Computational Fluid Dynamics, CFD, Compressor Oil Leakage 1E-mail: [email protected] 1 Introduction The majority of the turbocharger market uses a similar approach to sealing with piston rings to control gas leakage and a slinger/collector seal system to handle oil. The slinger/collector seal system is used to keep oil away from these piston rings. In normal operation the pressure in the end housings is higher than the bearing housing and gas flows into the bearing housing, through the oil drain to the crankcase. -
Turbocharger Seal
Turbocharger Seal TURBOCHARGER SEAL Turbocharged gasoline and diesel engines contribute to a drop in VALUES FOR THE CUSTOMER CO2 emissions while the engine output is held constant. y Eliminates oil leakage and reduces blow by up to 90% Freudenberg Sealing Technologies offers a turbocharger seal in y the form of a gas-lubricated mechanical face seal that replaces Almost no friction losses due to gas film between the sealing the standard piston ring. The turbocharger seal can be used on surfaces the compressor side of all mechanical charger, electric charger, y Contact-less sealing: leads to very low abrasion and increased and turbocharger designs. product life y Easy assembly: the turbocharger seal is delivered as a complete unit y Wide range of rotational speeds of up to 250.000 rpm y Extreme resistance to high temperature with the ability to handle short heat bursts of up to 200° C y Ideally suited for applications with fast-rotating shafts with a Turbocharger Seal construction scheme: centrifugal speed v ≥ 30 m/s Housing Static Seal Seal Ring Static Seal Mating Ring Spring Turbocharger Seal FEATURES & BENEFITS Reduction in oil leakage Alternative applications: Oil leakage leads to a reduction in engine efficiency due to the The turbocharger seal can also be used in a wide variety of appli- soiling of the charge air cooler and can lead to a total breakdown cations with similarly high rotational speeds when a gas is avail- of the engine. Oil burned in the engine tends to accelerate the able as a “lubricant,” such as, turbo tools and compressors in fuel incineration of the particle filter and thus its design must be en- cells applications. -
1986 Caterpillar Hhdd-Mhdd A-013-0043
(Page 1 of 2) State of California AIR RESOURCES BOARD EXECUTIVE ORDER A-13-43 Relating to Certification of New Motor Vehicle Heavy-Duty Engines CATERPILLAR TRACTOR COMPANY Pursuant to the authority vested in the Air Resources Board by Sections 43100, 43102, and 43103 of the Health and Safety Code; and Pursuant to the authority vested in the undersigned by Sections 39515 and 39516 of the Health and Safety Code and Executive Order G-45-3; IT IS ORDERED AND RESOLVED: That the following Caterpillar Tractor Company 1986 model-year heavy-duty diesel engines have shown compliance with the optional transient test procedure and standards and are certified for use in motor vehicles with a manufacturer's gross vehicle weight rating greater than 8500 pounds : Displacement Exhaust Emission Control Systems Engine Family Cubic Inches (Liters) Special Features) GCTC636EPA6 636 ( 10.4) Engine Modifications Code B Diesel Injection - Direct) (Turbocharger) GCTO6 3SFPA6 538 ( 10.5) Engine Modifications (Aftercooler) (Diesel Injection - Prechamber) (Turbocharger) GCT0893FPA6 893 ( 14.6) Engine Modifications Codes H & J (Aftercooler) (Diesel Injection - Direct) (Turbocharger) GCTO893FPB7 893 (14.6) Engine Modifications Codes D & E (Aftercooler) (Diesel Injection - Direct) Turbocharger) Engine models and codes are listed on attachments. The following are the certification emission values for these engine families: CATERPILLAR TRACTOR COMPANY EXECUTIVE ORDER A-13-43 (Page 2 of 2) Carbon Hydrocarbons Monoxide Nitrogen Oxides Engine Family gm/bhp-hr gm/bhp-hr gm/bhp-hr GCTO636EPA6 0.73 1.8 4.2 Code B GCTO638F PA6 0.47 1.7 4.6 GCTO893F PA6 0.40 2.4 5.1 Codes H & J GCTO893FPB7 0.28 2.4 5.1 Codes D & E BE IT FURTHER RESOLVED: That the Executive Officer has been provided all material required to demonstrate certification compliance with the Board's emission control system warranty regulations including the aftercooler in the turbocharger system (Title 13, California Administrative Code, Section 2036). -
Compression Ring Gaps for High Performance Engines
ACL TECH TALK COMPRESSION RING GAPS FOR HIGH PERFORMANCE ENGINES Piston rings are usually pre-gapped to a formula related to the bore size of the engine. For normal road engines the ring gaps are 0.003” to 0.005” per inch of bore diameter plus 0.001”. So for a 4” bore V8 engine the compression ring gaps could be as small as 0.013” to 0.021” Metric equivalents are shown in the table below. The table shows typical minimum compression ring gap recommendations imperial and metric units. The figures must be taken as a guide only for any performance application since there are many possibilities in terms of usage and the extent of modifications, fuel used and whether turbo or supercharged. Imperial (inch) Metric (mm) Imperial (inch) Metric (mm) Nominal bore size 3 76.2 4 101.6 Standard engine .010 0.25 .012 0.30 Moderate output “street” performance .016 0.40 .021 0.53 engine High output performance or marine .018 0.45 .025 0.63 engine There are several reasons why piston ring gap specification may need to be changed for an engine being modified for higher output. Generally these engines require more gap in order to prevent the rings from butting. Here are some factors, which can affect ring gap 1. As output increases the heat flow through the piston increases. 2. If the rings are placed high in the piston (i.e. a short or narrow ring land) they will be exposed to higher temperatures than if the top ring land is longer (wider). -
A Review on Turbocharger and Supercharger
International Journal of Emerging Trends in Engineering and Development Issue 6, Vol. 5 (September 2016) _________________________Available online on http://www.rspublication.com/ijeted/ijeted_index.htm ISSN 2249-6149 A REVIEW ON TURBOCHARGER AND SUPERCHARGER N.R.KARTHIK1, B.GAUTAM2 1Assistant Professor, Mechanical Engineering Department, Sri Ramakrishna Engineering College, Coimbatore, India, 641045 2Student, Mechanical Engineering Department, Sri Ramakrishna Engineering College, Coimbatore, India, 641045 ABSTRACT As a demand of new efficient and eco friendly engines is incrementing new technologies are developing. Due to the rich air fuel mixture combustion emission will increase hence by turbocharging the engine more power can be obtained with low emission. In this paper review on various application of turbo charging and super charging technology is made. The behavior of IC engine with application of turbo/super charger and need of turbo/super charger installation is studied. KEYPOINTS Turbocharger, Supercharger, Exhaust gas recovery, Inter cooler. INTRODUCTION IJETED The present energy need of the world is met from fossil fuel. The automobiles mainly uses petrol and diesel as fuel. The population of automobile is increasing rapidly due to economic development of developing countries. Due to this, the rate of fossil fuel depletion is increasing rapidly. Based on statistical report, if the current rate of depletion continues, the fossil fuel will get exhausted in a span of 10 to 30 years. To solve this problem electric automobiles is under development. Commercial proven electric automobiles will be available only after 15 years to 20 years. So we have to economize the use of petrol and diesel particularly in automobile sector. Till the commercialization of electric cars.