Thermodynamic Analysis of Turbo-Charged Power Generating System
Total Page:16
File Type:pdf, Size:1020Kb
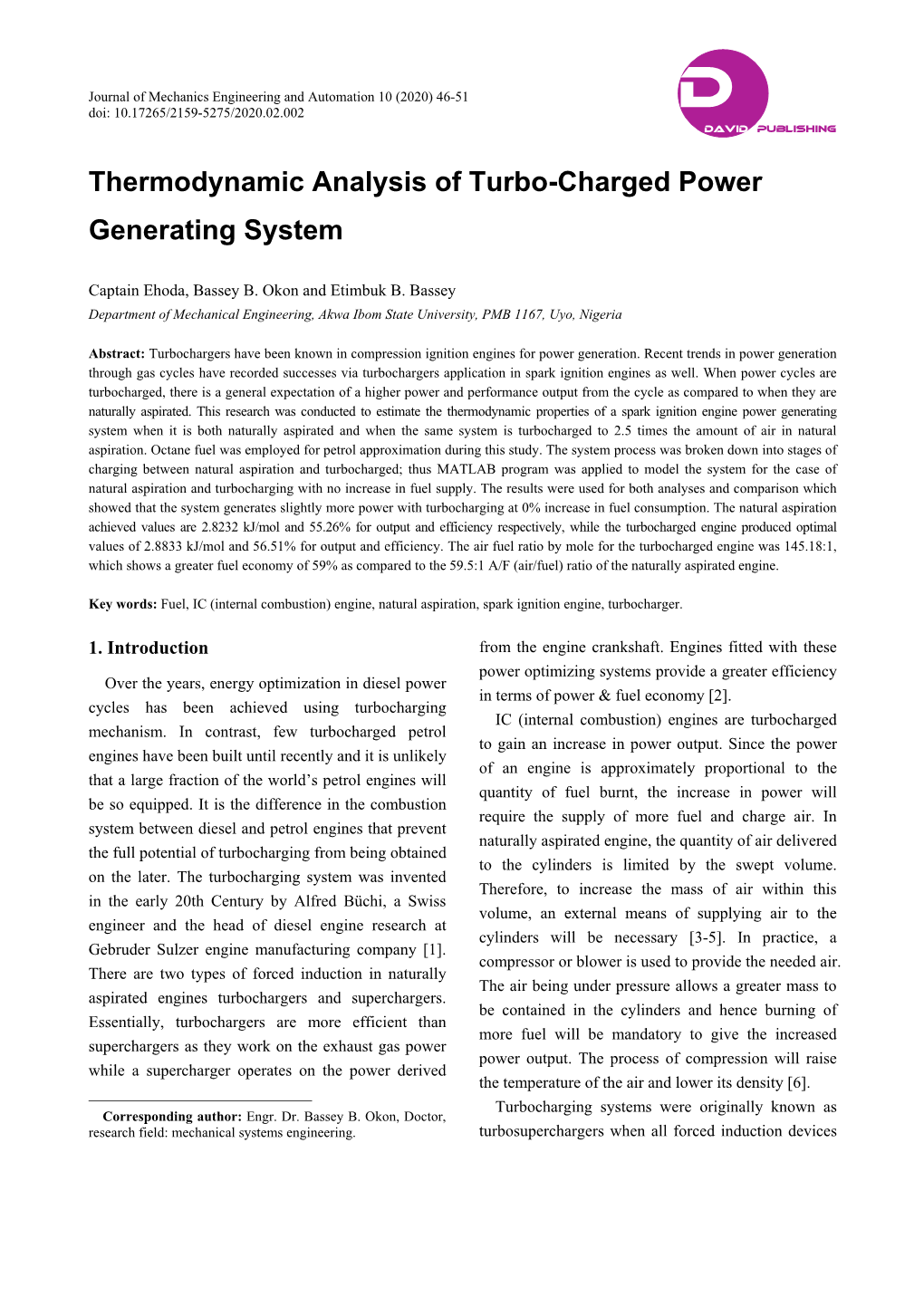
Load more
Recommended publications
-
The Uni-Fuel System, a Simple and Modern Way to Improve Fuel Consumption and Energy Generating Costs - the Sulzer S20 Diesel Engine As a Basic Model
Transactions on the Built Environment vol 1, © 1993 WIT Press, www.witpress.com, ISSN 1743-3509 The uni-fuel system, a simple and modern way to improve fuel consumption and energy generating costs - the Sulzer S20 diesel engine as a basic model W. Klinkmann New Sulzer Diesel Ltd, CH-8401 Winterthur, Switzerland Introduction Much has been written and will still be written on the subject of uni-fuel ships and generating shipboard electrical power. Recently, however, there has been slightly less written; probably because the number of newbuildings characterized by uni-fuel systems is growing and fuel prices are relatively stable. Independent of the technical side of the uni-fuel philosophy, one thing is undeniable - costs put pressure on profits. Now, when freight rates are not always satisfactory, costs can be a matter of life or death. S'OOO* 600 200 1987 1988 1990 SOURCE: Lloyd's Shipping Economist NOTES: * 30 months; quarterly figures Fig. 1: Operating costs of 10-12 years-old 100 000 tdw tankers 12 8 MarinTransactionse Engineerin on the Built Environmentg vol 1, © 1993 WIT Press, www.witpress.com, ISSN 1743-3509 The Principal Economic Parameter Shipping and related activities are risky businesses with high investments and market environments which are highly volatile. The output of ships (tonne-miles) only takes place when vessels are at sea. Reliability of ships and their machinery are therefore of eminent economical importance. The following formula gives us a good basis for judging the influence which different parameters have on -
Bentley Mulsanne Turbo and Turbo R Turbocharging System
Bentley Mulsanne Turbo and Turbo R Turbocharging System Extracts from Workshop Manuals TSD4400, TSD 4700, TSD4737 Basic Principles of Operation – Systems with Solex 4A-1 Carburettor The turbocharger is fitted to increase the power, and especially the low engine speed torque, of the engine. This it achieved by utilising the exhaust gas flow to pump pressurised air into the engine at wide throttle openings. Whenever this occurs, the turbocharger applies boost to the induction system. Under most conditions, the motor runs under naturally-aspirated principles. The inlet manifold may be under partial vacuum but the pressure chest partially pressurised under conditions of moderate power demand. The size of the turbocharger has been carefully chosen to give a substantial increase in torque at low engine speeds. The turbocharger is especially effective from 800rpm, with the engine achieving full torque at less than 1800RPM. Thus, maximum engine torque is available constantly between 1800RPM and 3800 RPM. By comparison to most turbocharging systems, the turbocharger capacity may appear decidedly oversized. This selection is intentional, and is fundamental to the achievement of full engine torque at low engine speeds and the absence of any noticeable delay when boost is demanded. It also minimises heating of exhaust gases by ensuring minimal resistance to gas flow under boost conditions. Furthermore, the design has been carefully chosen to avoid the need for the turbocharger to accelerate on demand, a feature commonly referred to as spool-up. By using a large turbocharger running but unloaded when not under demand, spool-up is not a phenomenon in the system. -
Executive Order D-425-50 Toyota Racing Development
State of California AIR RESOURCES BOARD EXECUTIVE ORDER D—425—50 Relating to Exemptions Under Section 27156 of the California Vehicle Code Toyota Racing Development TRD Supercharger System Pursuant to the authority vested in the Air Resources Board by Section 27156 of the Vehicle Code; and Pursuant to the authority vested in the undersigned by Section 39515 and Section 39516 of the Health and Safety Code and Executive Order G—14—012; IT IS ORDERED AND RESOLVED: That the installation of the TRD Supercharger System, manufactured and marketed by Toyota Racing Development, 19001 South Western Avenue, Torrance, California, has been found not to reduce the effectiveness of the applicable vehicle pollution control systems and, therefore, is exempt from the prohibitions of Section 27156 of the Vehicle Code for the following Toyota truck applications: Part No. Model Year Engine Disp. Model PTR29—34070 2007 to 2013 5.7L (3UR—FE) Tundra PTR29—00140 2014 to 2015 5.7L (3UR—FE) Tundra PTR29—34070 2008 to 2013 5.7L (3UR—FE) Sequoia PTR29—00140 2014 to 2015 5.7L (3UR—FE) Sequoia PTR29—60140 2008 to 2015 5.7L (3UR—FE) Land Cruiser/LX570 PTR29—35090 2005 to 2015 4.0L (1GR—FE) Tacoma PTR29—35090 2007 to 2009 4.0L (1GR—FE) FJ Cruiser PTR29—35090 2003 to 2009 4.0L (1GR—FE) 4—Runner PTR29—00130 2010 to 2014 4.0L (1GR—FE) FJ Cruiser PTR29—00130 2010 to 2015 4.0L (1GR—FE) 4—Runner The 5.7L Supercharger System includes a Magnuson supercharger (rated at a maximum boost of 8.5 psi.) with a 2.45 inch diameter supercharger pulley and the stock crankshaft pulley, high flow injectors to replace the stock injectors, a new ECU calibration, intercooler, intake manifold, an air bypass valve, and a new replacement fuel pump which is located in the fuel tank. -
Diesel Turbo-Compound Technology
Diesel Turbo-compound Technology ICCT/NESCCAF Workshop Improving the Fuel Economy of Heavy-Duty Fleets II February 20, 2008 Volvo Powertrain Corporation Anthony Greszler Conventional Turbocharger What is t us Compressor ha Turbocompound? Ex Key Components of a Mechanical Turbocompound t us ha System Ex Conventional Turbocharger Turbine Axial Flow Final Gear Power reduction to Turbine crankshaft Speed Reduction Gears Fluid Coupling Volvo D12 500TC Volvo Powertrain Corporation Anthony Greszler How Turbocompound Works • 20-25% of Fuel energy in a modern heavy duty diesel is exhausted • By adding a power turbine in the exhaust flow, up to 20% of exhaust energy recovery is possible (20% of 25% = 5% of total fuel energy) • Power turbine can actually add approximately 10% to engine peak power output • A 400 HP engine can increase output to ~440 HP via turbocompounding • However, due to added exhaust back pressure, gas pumping losses increase within the diesel, so efficiency improvement is less than T-C power output • Maximum total efficiency improvement is 3-5% • Turbine output shaft is connected to crankshaft through a gear train for speed reduction • Typical maximum turbine speed = 70,000 RPM; crankshaft maximum = 1800 RPM • An isolation coupling is required to prevent crankshaft torsional vibration from damaging the high speed gears and turbine Volvo Powertrain Corporation Anthony Greszler Turbocompound Thermodynamics • When exhaust gas passes through the turbine, the pressure and temperature drops as energy is extracted and due to losses • The power taken from the exhaust gases is about double compared to a typical turbocharged diesel engine • To make this possible the pressure in the exhaust manifold has to be higher • This increases the pump work that the pistons have to do • The net power increase with a turbo-compound system is therefore about half the power from the second turbine • E.G. -
Intake Throttle and Pre-Swirl Device for LP EGR Systems
Intake Throttle and Pre-swirl Device for Low-pressure EGR Systems Knowledge Library Knowledge Library Intake Throttle and Pre-swirl Device for Low-pressure EGR Systems Low-pressure EGR systems to reduce emissions are state of the art for diesel engines. They offer efficiency benefits compared to high-pressure EGR systems and will gain further importance. BorgWarner shows the potential of a so-called Inlet Swirl Throttle to make use of the losses and turn them into a pre-swirl motion of the intake air entering the turbocharger to improve the aerodynamics of the compressor. By Urs Hanig, Program Manager for PassCar Systems at BorgWarner and a member of BorgWarner’s Corporate Advanced R&D Organisation Technology to meet future Emission the compressor. Obviously, pre-swirl will have a Standards positive impact on the compressor also in are- Low-pressure EGR systems (LP EGR sys- as where no throttling is required. So the IST tems), see Figure 1 , for gasoline engines yield can be used to improve engine efficiency and significant fuel consumption benefits, they are performance also in regions where no throttling also an important technology to meet future or EGR is required. emission standards (e.g. Real Driving Emissi- ons) [1 ]. To achieve the targeted EGR rates in Approach and Modes of Operation particular on diesel engines throttling the LP With IST the throttling effect is achieved by ad- EGR path is necessary in some areas of the justable inlet guide vanes in the fresh air duct. engine operating map. This can be done either In other words, IST is an intake throttle desi- on the exhaust or the intake side but to throttle gned as a compressor pre-swirl device. -
MGA Supercharger System Installation Instructions for 1955 to 1962 MGA
MGA Supercharger System Installation Instructions For 1955 to 1962 MGA PART # 150-040 440 Rutherford St. P.O. Box 847 Goleta, CA 93117 1-800-667-7872 • FAX 805-692-2525 • www.mossmotors.com Please read and understand these valve between the barbed fitting and the instructions completely before you brake booster (closer to the booster) with begin the installation. the check valve arrow pointing toward the supercharger manifold. A few notes before you begin: Hose clamps: Re-use hose clamps, or Engine condition - Your car should have purchase new ones where necessary. Use a fresh tune up, including new spark plug new hose clamps on all fuel connections. wires, points, and a new distributor cap and rotor. Spark plugs are included in the If you have installed vacuum boosted supercharger system. brakes - you MUST install a check valve (Moss Part # 150-071) in the vacuum How superchargers work — line. This will prevent pressurized air from Superchargers compress the air/fuel mix- reaching the brake booster system and ture, filling cylinders with a greater charge damaging it. To install, remove the larger than when normally aspirated. Normally of the 3 plugs in the back of the super- aspirated engines produce vacuum, read charger manifold and install a barbed in inches of mercury, superchargers and fitting using teflon tape on the threads. turbochargers produce boost, read in posi- Using 3/8 in vacuum line, install the check tive pounds per square inch. 150-040 -1- Revised 1/11 Installation Instructions Boost capacity is determined by supercharger rod, jet, and slide have been altered to run prop- RPM which is, of course, affected by pulley size erly and safely on a wide range of supercharged, (the smaller the supercharger pulley, the faster unmodified engines. -
Forced Induction Basics, Supercharging & Turbocharging; Engine Professional
EP Q2-12 10-27_Layout 1 4/19/12 11:45 AM Page 10 Forced Induction Basics BY MIKE MAVRIGIAN PHOTOS BY MIKE MAVRIGIAN UNLESS OTHERWISE NOTED Supercharging and turbocharging tidbits While this article may be a bit simplistic SUPERCHARGER BASICS for those familiar with forced induction, Superchargers (blowers) are offered in hopefully the information will be helpful three types, including the Roots type, to those who are not as experienced with centrifugal and the screw type. The Roots this approach. type is the least complex, functioning as an air pump. Instead of compressing air A naturally-aspirated engine uses inside the unit, pressurization takes place available (ambient) air to enter the in the manifold and combustion engine, mix with fuel and ignite in the chambers (referred to as external air combustion chamber. A forced induction compression). Centrifugal and screw type system (supercharger or turbocharger) superchargers compress air inside the does just what the term implies…it forces additional air into the combustion supercharger (internal compression), chamber. When mixed with the pushing the compressed air into the appropriate ratio of fuel, you create intake and combustion areas. A higher cylinder pressure, referred to as centrifugal unit mechanically functions boost, which makes more power. While much the same as a turbocharger, with an we certainly don’t have the room here to internal impeller. Instead of being driven delve into great detail, we’ll try to offer a by exhaust gas (as with a turbo), a few informational tidbits that will centrifugal supercharger impeller is hopefully help you to better understand driven mechanically by a drive belt. -
High Efficiency VCR Engine with Variable Valve Actuation and New Supercharging Technology
AMR 2015 NETL/DOE Award No. DE-EE0005981 High Efficiency VCR Engine with Variable Valve Actuation and new Supercharging Technology June 12, 2015 Charles Mendler, ENVERA PD/PI David Yee, EATON Program Manager, PI, Supercharging Scott Brownell, EATON PI, Valvetrain This presentation does not contain any proprietary, confidential, or otherwise restricted information. ENVERA LLC Project ID Los Angeles, California ACE092 Tel. 415 381-0560 File 020408 2 Overview Timeline Barriers & Targets Vehicle-Technology Office Multi-Year Program Plan Start date1 April 11, 2013 End date2 December 31, 2017 Relevant Barriers from VT-Office Program Plan: Percent complete • Lack of effective engine controls to improve MPG Time 37% • Consumer appeal (MPG + Performance) Budget 33% Relevant Targets from VT-Office Program Plan: • Part-load brake thermal efficiency of 31% • Over 25% fuel economy improvement – SI Engines • (Future R&D: Enhanced alternative fuel capability) Budget Partners Total funding $ 2,784,127 Eaton Corporation Government $ 2,212,469 Contributing relevant advanced technology Contractor share $ 571,658 R&D as a cost-share partner Expenditure of Government funds Project Lead Year ending 12/31/14 $733,571 ENVERA LLC 1. Kick-off meeting 2. Includes no-cost time extension 3 Relevance Research and Development Focus Areas: Variable Compression Ratio (VCR) Approx. 8.5:1 to 18:1 Variable Valve Actuation (VVA) Atkinson cycle and Supercharging settings Advanced Supercharging High “launch” torque & low “stand-by” losses Systems integration Objectives 40% better mileage than V8 powered van or pickup truck without compromising performance. GMC Sierra 1500 baseline. Relevance to the VT-Office Program Plan: Advanced engine controls are being developed including VCR, VVA and boosting to attain high part-load brake thermal efficiency, and exceed VT-Office Program Plan mileage targets, while concurrently providing power and torque values needed for consumer appeal. -
Vortech Engineering Performance Engine Parts
® FAQ How tight should I tighten the Vortech superchrrger retrnng rolt? About 25-30 ft./bb ib buggebted for the retiiiiig bo/tt tt ib i/bo recommeided thit i bmi// imouit of b/ue Loctte be ipp/ied to the threidb prior to iibertig the bo/t ii the iiput bhif iid ipp/y i bmi// imouit of iit-beiie oi the iiput bhif iid key before iibti//iig the buperchirger pu//eyt Why should I use Vortech pulleys? Some ioi-Vortech pu//eyb ivii/ib/e do iot provide the precibioi ft iid bi/iice which ire ebbeiti/ for performiice iid duribi/ity iid ire therefore iot recommeidedt Never force or himmer oi the pu//ey or buperchirger bhift The pu//ey bhou/d bire/y b/ip over the bhif whei it ib 75-80 degreeb Ft The key to keywiy ft ib i/bo critci/, ib ib bi/iicet A/wiyb ube i bmi// of oi/ or greibe oi the bhift Stee/ pu//eyb miy rubt thembe/veb to the bhif if iot /ubricitedt Why would r Vortech superchrrger relt come of or werr unevenly? The propeibity for grooved be/tb to move over oie or more grooveb, or come of comp/ete/y, ib i/wiyb due to ii i/igimeit prob/emt Either btitci//y (the pu//eyb ire mibi/igied due to ii iibti//itoi or to/eriice prob/em) or dyiimici//y (the /oidiig or ui/oidiig of the bybtem), miii/y the mouitig p/ite ciubeb mibi/igimeit due to fex or movemeitt Mibi/igimeit cii i/bo be ciubed by over-tghteiiig (iid fii/iig) of the be/t which miy be detrimeiti/ to the pu//ey beiriigt Crn I run r cog drve system wth r Vortech superchrrger? The oi/y Vortech buperchirger debigiitoib thit miy be drivei with i cogged type be/t drive ire heivy duty mode/bt -
CHARACTERIZATION of TURBOCHARGER PERFORMANCE and SURGE in a NEW EXPERIMENTAL FACILITY
CHARACTERIZATION of TURBOCHARGER PERFORMANCE and SURGE in a NEW EXPERIMENTAL FACILITY Thesis Presented in Partial Fulfillment of the Requirements for the Degree Master of Science in the Graduate School of The Ohio State University By Gregory David Uhlenhake, B.S. Graduate Program in Mechanical Engineering The Ohio State University 2010 Master‟s Examination Committee: Dr. Ahmet Selamet, Advisor Dr. Rajendra Singh Dr. Philip Keller Copyright by Gregory David Uhlenhake 2010 ABSTRACT The primary goal of the present study was to design, develop, and construct a cold turbocharger test facility at The Ohio State University in order to measure performance characteristics under steady state operating conditions and to investigate surge for a variety of automotive turbocharger compression systems. A specific turbocharger is used for a thermodynamic analysis to determine facility capabilities and limitations as well as for the design and construction of the screw compressor, flow control, oil, and compression systems. Two different compression system geometries were incorporated. One system allowed performance measurements left of the compressor surge line, while the second system allowed for a variable plenum volume to change surge frequencies. Temporal behavior, consisting of compressor inlet, outlet, and plenum pressures as well as the turbocharger speed, is analyzed with a full plenum volume and three impeller tip speeds to identify stable operating limits and surge phenomenon. A frequency domain analysis is performed for this temporal behavior as well as for multiple plenum volumes with a constant impeller tip speed. This analysis allows mild and deep surge frequencies to be compared with calculated Helmholtz frequencies as a function of impeller tip speed and plenum volume. -
State of California AIR RESOURCES BOARD EXECUTIVE ORDER D-493
(Page 1 of 2) State of California AIR RESOURCES BOARD EXECUTIVE ORDER D-493 Relating to Exemptions Under Section 27156 of the Vehicle Code DOWNING/ATLANTA, INC. BMW SUPERCHARGER KIT Pursuant to the authority vested in the Air Resources Board by Section 27156 of the Vehicle Code; and Pursuant to the authority vested in the undersigned by Section 39515 and Section 39516 of the Health and Safety Code and Executive Order G-45-9; IT IS ORDERED AND RESOLVED: That the installation of the BMW Supercharger Kit, manufactured and marketed by Downing/Atlanta, Inc., 5096 Peachtree Road, Atlanta, Georgia 30341 has been ound not to reduce the effectiveness of the applicable vehicle pollution control system and, therefore, is exempt from the prohibitions of Section 27156 of the Vehicle Code for 1999 and older BMW vehicles equipped with a four cylinder fuel injected engine. The BMW Supercharger Kit includes the following main components: Eaton M-62 supercharger, intake manifold, fuel regulator, and an open element air cleaner. The stock air cleaner may also be retained. No changes are made to the stock ignition system. The kit includes a 3.7" diameter supercharger pulley and uses the stock crankshaft pulley. Maximum boost is limited to 7.5 psi. This Executive Order is valid provided that the installation instructions for the BMW Supercharger Kit will not recommend tuning the vehicle to specifications different from those of the vehicle manufacturer. This Executive Order shall not apply to any Downing/Atlanta, Inc. BMW Supercharger Kit advertised, offered for sale, or sold with or installed on, a motor vehicle prior to or concurrent with transfer to an ultimate purchaser. -
Boosting Your Knowledge of Turbocharging
Reprinted with permission from Aircraft Maintenance Technology, July 1999 BoostingBoosting YourYour KnowledgeKnowledge ofof TurbochargingTurbocharging (Part 1 of a 2 part Series) By Randy Knuteson short 15 years after Orville fully boosted this 350 hp Liberty engine to a strength of blowers being tested during and Wilbur made their his- remarkable 356 hp (a normally aspirated engine WWII. The B-17 and B-29 bombers along toric flight at Kitty Hawk, would only develop about 62 percent power at with the P-38 and P-51 fighters were all fit- General Electric entered the this altitude). ted with turbochargers and controls. Aannals of aviation history. In 1918, GE strapped An astounding altitude record of 38,704 Turbocharging had brought a whirlwind of an exhaust-driven turbocharger to a Liberty feet was achieved three years later by Lt. J.A. change to the ever-broadening horizons of engine and carted it to the top of Pike’s Peak, Macready. flight. CO — elevation 14,000 feet. There, in the crys- This new technology began immediately Much of the early developments in recip talline air of the majestic Rockies, they success- experiencing a rapid evolution with the full turbocharging came as a result of demands Aircraft Maintenance Technology • OCTOBER 1999 2 Recip Technology from the commercial industrial diesel engine market. It wasn’t until the mid-1950s that this Percentage of HP Available At Altitude technology was seriously applied to general avi- 100% ation aircraft engines. It all started with the pro- totype testing of an AiResearch turbocharger for 90% Turbocharge the Model 47 Bell helicopter equipped with the Franklin 6VS-335 engine.