Plasticiser Effect of Oleic Acid Polyester on Polyethylene and Polypropylene
Total Page:16
File Type:pdf, Size:1020Kb
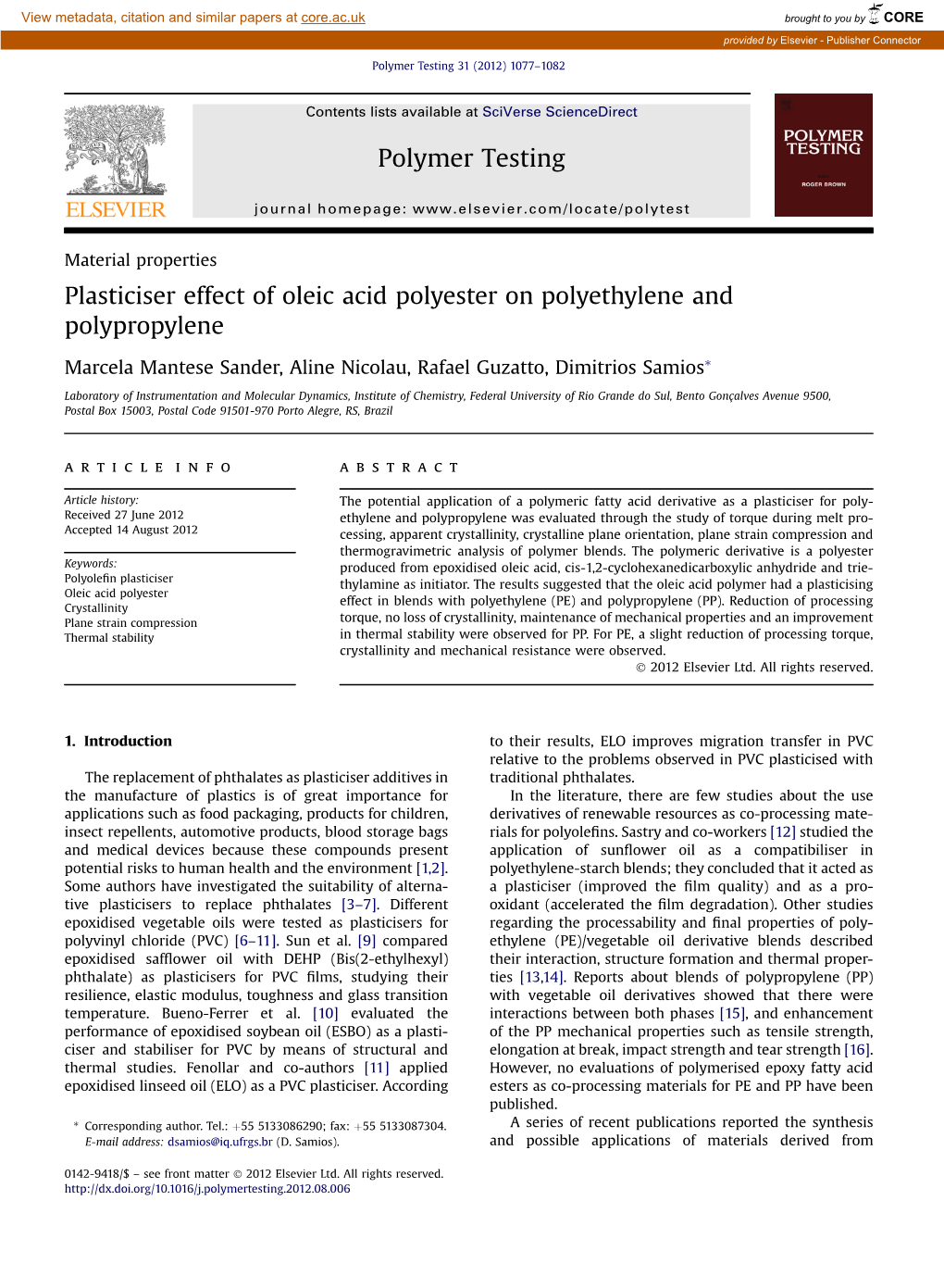
Load more
Recommended publications
-
II. Plasticizer-Free Polyvinyl Chloride, Plasticizer-Free Copolymers of Vinyl
This is an unofficial translation. Only the German version is binding. II. Plasticizer-free Polyvinyl Chloride, Plasticizer-free Copolymers of Vinyl Chlo- ride and Mixtures of these Polymers with other Copolymers and Chlorinated Polyolefins Containing Mainly Vinyl Chloride in the Total Mixture As of 01.01.2012 The monomers and other starting substances as well as additives used in the production of plasticizer-free polyvinyl chloride, plasticizer-free copolymers of vinyl chloride containing mainly vinyl chloride, mixtures of these polymers with other copolymers, and chlorinated polyolefins containing mainly vinyl chloride in the total mixture are subject to the requirements of the Commission Regulation (EU) No 10/2011. Otherwise, there are no objections to the use of these plastics for commodities in the sense of § 2, Para. 6, No 1 of the Food and Feed Code (Lebensmittel- und Futtermittelgesetzbuch), pro- vided they are suitable for their intended purpose and comply with the following conditions: 1. The use of monomers and other starting materials for polyethylene is subject to the stipula- tions of the Commission Regulation (EU) No 10/2011. The evaluation presented in the following refers to polymers from the following monomeric starting substances: a) Vinyl chloride b) Vinylidene chloride c) Trans-dichloroethylene d) Vinylesters of aliphatic carbonic acids C2-C18, in so far as covered by the positive list of the Commission Regulation (EU) No 10/2011 e) Esters of acrylic acid, methacrylic acid and/or maleic acid or fumaric acid with -
Using an Inhibitor to Prevent Plasticizer Migration from Polyurethane Matrix to EPDM Based Substrate Rezaei-Vahidian Hadi, Farajpour Tohid, Abdollahi Mahdi
Using an Inhibitor to Prevent Plasticizer Migration from Polyurethane Matrix to EPDM Based Substrate Rezaei-Vahidian Hadi, Farajpour Tohid, Abdollahi Mahdi Cite this article as: Rezaei-Vahidian Hadi, Farajpour Tohid, Abdollahi Mahdi. Using an Inhibitor to Prevent Plasticizer Migration from Polyurethane Matrix to EPDM Based Substrate[J]. Chinese J. Polym. Sci, 2019, 37(7): 681-686. doi: 10.1007/s10118-019-2251-y View online: https://doi.org/10.1007/s10118-019-2251-y Articles you may be interested in Antistatic PVC-graphene Composite through Plasticizer-mediated Exfoliation of Graphite Chinese J. Polym. Sci. 2018, 36(12): 1361 https://doi.org/10.1007/s10118-018-2160-5 SYNTHESIS OF POLYURETHANE MODIFIED BISMALEIMIDE (UBMI) AND POLYURETHANE-IMIDE ELASTOMER Chinese J. Polym. Sci. 2008, 26(1): 117 Synthesis and Properties of Reversible Disulfide Bond-based Self-healing Polyurethane with Triple Shape Memory Properties Chinese J. Polym. Sci. 2019, 37(11): 1119 https://doi.org/10.1007/s10118-019-2268-2 增塑剂对碱木质素/HDPE复合材料性能影响研究 The Effect of Plasticizer on the Properties of Alkali Lignin/HDPE Composites 高分子学报. 2014(2): 210 https://doi.org/10.3724/SP.J.1105.2014.13204 泊肃叶流中环形高分子的迁移行为及与线性高分子的差异 Migration of Ring Polymers in Poiseuille Flow and Comparison with Linear Polymers 高分子学报. 2019, 50(11): 1229 https://doi.org/10.11777/j.issn1000-3304.2019.19074 聚醚硅油表面迁移行为对聚苯乙烯表面极性的影响 THE IMPROVEMENT OF POLARITY OF POLYSTYRENE SURFACE BY THE SELECTIVE SURFACE MIGRATION OF POLYETHER SILICOME OIL 高分子学报. 2007(2): 165 Chinese Journal of POLYMER SCIENCE ARTICLE https://doi.org/10.1007/s10118-019-2251-y -
Recent Attempts in the Design of Efficient PVC Plasticizers With
materials Review Recent Attempts in the Design of Efficient PVC Plasticizers with Reduced Migration Joanna Czogała 1,2,3,* , Ewa Pankalla 2 and Roman Turczyn 1,* 1 Department of Physical Chemistry and Technology of Polymers, Silesian University of Technology, Strzody 9, 44-100 Gliwice, Poland 2 Research and Innovation Department, Grupa Azoty Zakłady Azotowe K˛edzierzynS.A., Mostowa 30A, 47-220 K˛edzierzyn-Ko´zle,Poland; [email protected] 3 Joint Doctoral School, Silesian University of Technology, Akademicka 2A, 44-100 Gliwice, Poland * Correspondence: [email protected] (J.C.); [email protected] (R.T.) Abstract: This paper reviews the current trends in replacing commonly used plasticizers in poly(vinyl chloride), PVC, formulations by new compounds with reduced migration, leading to the enhance- ment in mechanical properties and better plasticizing efficiency. Novel plasticizers have been divided into three groups depending on the replacement strategy, i.e., total replacement, partial replacement, and internal plasticizers. Chemical and physical properties of PVC formulations containing a wide range of plasticizers have been compared, allowing observance of the improvements in polymer per- formance in comparison to PVC plasticized with conventionally applied bis(2-ethylhexyl) phthalate, di-n-octyl phthalate, bis(2-ethylhexyl) terephthalate and di-n-octyl terephthalate. Among a variety of newly developed plasticizers, we have indicated those presenting excellent migration resistance and advantageous mechanical properties, as well as those derived from natural sources. A separate chapter has been dedicated to the description of a synergistic effect of a mixture of two plasticizers, primary and secondary, that benefits in migration suppression when secondary plasticizer is added to PVC blend. -
Cross Linked Sulphonated Poly(Ether Ether Ketone) for the Development of Polymer Electrolyte Membrane Fuel Cell
Cross Linked Sulphonated Poly(ether ether ketone) for the Development of Polymer Electrolyte Membrane Fuel Cell Abdul Ghaffar Al Lafi, MSc. A Thesis Submitted for the Degree of Doctor of Philosophy The School of Metallurgy and Materials, The College of Engineering and Physical Sciences, The University of Birmingham, Birmingham, UK. September 2009 University of Birmingham Research Archive e-theses repository This unpublished thesis/dissertation is copyright of the author and/or third parties. The intellectual property rights of the author or third parties in respect of this work are as defined by The Copyright Designs and Patents Act 1988 or as modified by any successor legislation. Any use made of information contained in this thesis/dissertation must be in accordance with that legislation and must be properly acknowledged. Further distribution or reproduction in any format is prohibited without the permission of the copyright holder. Synopsis Ion irradiation has been investigated as a route for the preparation of mechanically stable and highly durable cross linked sulphonated PEEK for fuel cell application. Ion irradiation was carried out using the University of Birmingham’s Scanditronix MC-40 Cyclotron operating at 11.7 MeV for H+ and 30 MeV for He2+ and the irradiated materials were characterized focusing on structural, thermal, morphological as well as dielectrical properties. Alterations produced in the molecular structure of amorphous PEEK by ion irradiation have been interpreted as due to chain scission and formation of cross links, as confirmed by sol-gel analysis in MSA using the well known Charlesby–Pinner equation. The thermal decomposition of irradiated PEEK was similar to that of untreated PEEK in that it occurred by a random chain scission process. -
High Performance Ester Plasticizers
High Performance Ester Plasticizers Abstract Traditional elastomer polymers, such as nitrile, polychloroprene, chlorinated polyethylene and chlorosulfonated polyethylene, have for years used moderate- to low- performance ester plasticizers. However, longevity requirements for rubber articles made from these elastomers have created a need for higher-performance ester plasticizers. With the increasing high-temperature demands required by automotive, other elastomers such as acrylic, high-saturated nitrile, epichlorohydrin and ethylene propylene diene monomer EPDM are replacing the more traditional elastomers. Plasticizers commonly used for the traditional and the high-temperature polymers are extractable, incompatible or too volatile. This paper provides information on plasticizers that are designed for traditional elastomers and high-performance polymers. The test data will include heat aging, extraction by hydrocarbons and low-temperature as molded after aging. The information provided indicates that the permanence of the plasticizer after these various agings is the key to the retention of physical properties. Introduction End uses for elastomer compounds are quite diverse, but they can be loosely categorized as being either general performance or higher performance applications. Each of these performance categories requires a different set of considerations in terms of compounding with ester plasticizers. An ester plasticizer, in its simplest concept, is a high-boiling organic solvent that when added to an elastomeric polymer reduces stiffness and permits easier processing.1 For general performance applications, compounders require moderate performance in several areas without particular emphasis on any one. Some general performance ester plasticizers used in the marketplace today are DOA, DIDA, DIDP, DOP, DINP and other phthalates and adipates made from straight-chain alcohols of 7–11 carbons in length. -
Microporous Membranes from Poly\Ether-Etherketone\-Type
Europa,schesP_ MM M M M M MINI M MM I M I M J European Patent Office a At* w%n © Publication number: 0 492 446 B1 Office europeen, desJ brevets © EUROPEAN PATENT SPECIFICATION © Date of publication of patent specification: 29.11.95 © Int. CI.6: B01 D 71/52, B01D 67/00, C08J 9/26 © Application number: 91121801.4 @ Date of filing: 19.12.91 The file contains technical information submitted after the application was filed and not included in this specification Mlcroporous membranes from poly(ether-etherketone)-type polymers and low melting point crystalllzable polymers, and a process for making the same. ® Priority: 21.12.90 US 633600 California 94526 (US) Inventor: Beck, H. Nelson @ Date of publication of application: 390 La Vista Road 01.07.92 Bulletin 92/27 Walnut Creek, California 94598 (US) © Publication of the grant of the patent: Inventor: Lundgard, Richard A. 29.11.95 Bulletin 95/48 2441 Whltetall Drive Antloch, © Designated Contracting States: California 94509 (US) DE DK FR GB IT NL Inventor: Wan, Hawk S. 4627 Fleldcrest Way © References cited: Antloch, EP-A- 0 297 744 California 94509 (US) EP-A- 0 337 626 Inventor: Kawamoto, Jlro EP-A- 0 409 416 2348 Benham Court EP-A- 0 417 908 Walnut Creek, California 94596 (US) © Proprietor: THE DOW CHEMICAL COMPANY Inventor: Sonnenscheln, Mark F. 2030 Dow Center, 3512 Blythe Drive Abbott Road Antloch, Midland, California 94509 (US) 00 Michigan 48640 (US) CO @ Inventor: Mahoney, Robert D. 240 Daylight Palace Danville, CM Oi Note: Within nine months from the publication of the mention of the grant of the European patent, any person may give notice to the European Patent Office of opposition to the European patent granted. -
Biodegradable Polymeric Film for Food Packaging
RESEARCH ARTICLE Biodegradable Polymeric Film for Food Packaging Raminder Kaur Neelam Yadav* Delhi Technological University Delhi Technological University PREFACE API 2015 ABSTRACT Food packaging films that show post-consumer biodegradability are rarely explored by researchers. The present study was carried out to investigate the physicomechanical characteristics of ethyl cellulose (EC) based films to be used in food packaging. Ethyl cellulose was plasticized with different percentage of polyethylene glycol (PEG). The samples of standard dimensions were subjected to different testing such as soluble matter content, moisture content, oil permeability, surface morphology, mechanical testing etc. The data obtained was analysed to decide the moderate percentage of plasticizer that can be used to provide a rational explanation of a perfect quality specimen. It has been revealed that too high or too low percentage of plasticizer was not appropriate for a good film. Tensile stress analysis was used to estimate the mechanical properties of the films. The results have shown an increase in tensile properties with increase in coalescence temperature. Temperature-dependent plastic deformation was observed for coalescence temperatures above 50oC. KEY WORDS Ethyl cellulose, Plasticizer, Biopolymers, Food packaging. *Raminder Kaur Corresponding Author [email protected] Biodegradable Polymeric Film for Food Packaging 21 INTRODUCTION on protein, lipid and polysaccharide, which provide barrier to the volatile component of food as well as its Packaging protects food from the external envi- moisture content [17,18]. However, the main concern ronment and provides information to the consumers is that, these bio-degradable packaging films lack about the food inside the package. Foods are packaged many desirable characteristics of packaging materials to deliver safe, wholesome and nutritious food to the to be used at a commercial scale. -
A Acrylonitrile-Butadiene-Styrene (ABS) Plastics, 44, 179 Active
Index A Cationic polymerization Acrylonitrile-butadiene-styrene (ABS) alkene monomer, 286 plastics, 44, 179 carbonyl monomer, 213, 215 Active material, 76 chain transfer reaction, 151, 197 Additive co-initiator, 193 lubricant, 85, 287 commercial applications, 290 odorant, 85 friedel-crafts catalyst, 187 pigment, 85 initiators, 185 plasticizer, 85 kinetic chain length, 198 Anionic copolymerization, 236, 237, 259, 296, kinetics, 283 297 rate constant, 155, 205 Anionic polymerization reaction mechanisms, 191 carbonyl monomer, 213, 215 termination reaction, 162 chain transfer, 45, 197, 276, 280, 283 Cationic polymerization of epoxides initiator, 143, 170, 193, 198, 200, 201, 204, initiation, 277, 278, 280 208, 209, 211, 214, 215, 273 propagation, 278, 279, 280 kinetics, 196, 267 termination and transfer processes, 280 rate constant, 192 Chain copolymerization, 233, 236, reaction mechanisms, 191, 211, 231, 299 297 termination, 162, 188, 199, 200, 201, 203, Chain polymerization 204, 271, 285 free radical, 3, 9, 138, 150 Anionic polymerization of epoxides ionic, 3, 187, 276 chain transfer to monomer, 276 Chemical property degree of polymerization, 2, 171, 197, 198, chemical permeation, 61 274, 284, 285 chemical resistance, 61 exchange reaction, 274 moisture permeation, 62, 63 kinetics, 196, 204 moisture resistance, 62 reaction mechanisms, 191, 201, 211, 231, Chemical structure analysis by 299 chemical reaction method, 90 Arrhenius equation, 47, 169 electron spin resonance, 98 infrared spectroscopy (IR), 90–92 mass spectroscopy of MALDI-TOF MS, B 18, 19 Bond strength, 70 nuclear magnetic resonance spectroscopy (NMR), 95, 96, 98 Raman spectroscopy, 92, 93 C UV-visible spectroscopy, 93 Cardo polymer, 83, 87 Chromophores, 82, 93 Cationic copolymerization, 236, 237, 256–259, Cohesive energy density, 12 296 Commercial copolymers, 263 W.-F. -
Blends of Polyimides with Poly(Ether Ether Ketone) and PEEK Derivatives/ Robert J
University of Massachusetts Amherst ScholarWorks@UMass Amherst Doctoral Dissertations 1896 - February 2014 1-1-1990 Blends of polyimides with poly(ether ether ketone) and PEEK derivatives/ Robert J. Karcha University of Massachusetts Amherst Follow this and additional works at: https://scholarworks.umass.edu/dissertations_1 Recommended Citation Karcha, Robert J., "Blends of polyimides with poly(ether ether ketone) and PEEK derivatives/" (1990). Doctoral Dissertations 1896 - February 2014. 769. https://scholarworks.umass.edu/dissertations_1/769 This Open Access Dissertation is brought to you for free and open access by ScholarWorks@UMass Amherst. It has been accepted for inclusion in Doctoral Dissertations 1896 - February 2014 by an authorized administrator of ScholarWorks@UMass Amherst. For more information, please contact [email protected]. BLENDS OF POLYIMIDES WITH POLY (ETHER ETHER KETONE) AND PEEK DERIVATIVES A Dissertation Presented by ROBERT J, KARCHA Submitted to the Graduate School of the University of Massachusetts in partial fulfillment of the requirements for the degree of DOCTOR OF PHILOSOPHY September 1990 Polymer Science and Engineering Copyright by Robert J. Karcha 1990 All Rights Reserved / BLENDS OF POLYIMIDES WITH POLY (ETHER ETHER KETONE) AND PEEK DERIVATIVES A Dissertation Presented By ROBERT J. KARCHA Approved as to style and content by Roger S C/Porter , Chairman William J. MacXnignt, Memb er C. Peter Li llya, 1^1iiber William J^. MacKnight, department head Polymer Science and Engineering Dedicated to the memory of my uncle and namesake Robert Glasser, whose untimely death prevented the completion of his dissertation. ACKNOWLEDGEMENTS I would like to thank my advisor, Prof. Roger S. Porter, for his support, guidance and encouragement during the course of my work. -
PROCESSING and STRUCTURE G. Menges and N. Berndtsen Institut
Pure & Appt. Chem.~ Vol. 49, pp. 597-613. Pergamon Press, 1977. Printed in Great Britain. · POLYVINYL CHLORIDE - PROCESSING AND STRUCTURE G. Menges and N. Berndtsen Institut ffir Kunststoffverarbeitung, 51 Aachen Abstract - Widely different procedures for the processing of PVC have proved themselves and have succeeded in practice on the basis of the special physical and chemical properties of PVC. In this connection a distinction must be made between the processing of plasticized PVC and the relatively difficult processing of rigid PVC. A survey of the most important methods of preparation and processing is given here. The special, rather abnormal properties of PVC in comparison with other thermoplastics are partly. a result of its characteristic structure. The consequences for preparation and processing must therefore be considered anew. Of course, the globular structure of PVC has an effect on the behaviour of the solid-state material and the melt, too, so that great importance must be attributed to the processes at the parttele interface. 1. INTRODUCTION Though polyvinyl chloride has been in existence for a long time far less is known about it than about the comparatively new polyolefins. It is incom parably more difficult to process because of its low decomposition tempe rature, a fact which impedes laboratory tests, too. M8ny research workers say that chlorine begins splitting off just above 100 C (1,2,3). It shows the lowest activation eriergy for decomposition of all plastics, except for PVA (4). It can be attributed to its low raw-material price - it is a typical recyclinq product of the chemical joint utilities - as well as. -
The Function and Selection of Ester Plasticizers
The Function and Selection of Ester Plasticizers Plasticizer basics As defined by ASTM, a plasticizer is a substance incorporated into a plastic or elastomer to increase its flexibility, workability or distensibility.1 In its simplest concept, it is a high-boiling organic solvent that, when added to a rigid substance, imparts flexibility. Plasticizers include a large variety of organic liquids, such as petroleum fractions, coal tar distillates, animal fats and plant extracts, and reacted products made of those materials. Ester plasticizers, the subject of this paper, are the latter. Elastomer and plastic polymers may be tough, dry or rigid materials that, for many applications, have a need for plasticizers. A plasticizer, among other contributions, will reduce the melt viscosity, lower the temperature of a second order glass transition (Tg) or lower the elastic modulus of a polymer. This paper discusses ester plasticizers, one of the more common and important plasticizer classes. Function Plasticizers are polymer modifiers, as are all the other ingredients included for the formation of an elastomer compound. Plasticizers may be thought of according to their function in a compound or by their type. Some of those classifications might be internal, external, chemical, physical, esters, oils, primary, secondary, etc. Internal plasticizers include flexible monomers (soft segments) incorporated regularly or irregularly between inflexible monomers (hard segments) of a polymer chain. Flexible polymers may be added to rigid polymers, for example, nitrile rubber to polyvinyl chloride (PVC), or grafted as side chains that reduce crystallinity and Tg through the reduction of intermolecular forces. External plasticizers are materials that interact physically with the elastomer but that do not chemically react with the polymer. -
Thermal Analysis of Polyvinyl Chloride TA N0.65 FEB.1995 - Influence of Plasticizer on Glass Transition
Thermal Analysis of Polyvinyl Chloride TA N0.65 FEB.1995 - Influence of Plasticizer on Glass Transition - 1. Introduction Polyvinyl chloride (PVC) is used as an all-purpose plastic in a wide variety of fields ranging from industrial materials such as pipes and wire coating materials to general consumable materials such as film and sheets. One characteristic that makes PVC different from other polymers is the ability to greatly adjust the elasticity and hardness of end products through the addition of plasticizer. Differential scanning calorimetry (DSC) and thermo-mechanical analysis (TMA) can evaluate the fluctuations of the glass transition points of plasticized PVC. This brief introduces examples of DSC and TMA measurements of the glass transition point fluctuations of plasticized PVC with different dioctyl phthalate (DOP) concentrations. 2. Measurements Three types of PVC samples were used: non-plasticized PVC and plasticized PVC containing 10wt% and 20wt% DOP. DSC220C and TMA210C units were connected to a SSC5200H Desk Station for the measurements. For the DSC measurement conditions, a 10mg sample was placed an aluminum open type sample container. The measurement temperature range was -20°C to 120°C and a heating rate of 10°C/min was used. For the TMA measurements, an expansion/compression probe was used and the load was 3g. The measurement temperature range was -40°C to 120°C with a heating rate of 5°C/min. Figure 1 DSC Measurement Data Figure 2 TMA Measurement Data for Each PVC Samples for Each PVC Samples - 1 - Table 1 Analysis Results of the Glass Transition Temperature of PVC Samples By DSC, TMA and DMS Measurements DOP DSC TMA*5 DMS*6 (wt%) Tig (°C )*1 Tmg (°C )*2 Teg (°C )*3 ΔCp (J/g°C )*4 (°C ) (°C ) 0 71.0 76.0 80.2 0.311 75.6 76.8 10 40.8 51.2 59.2 0.273 53.6 52.9 20 16.8 30.7 42.6 0.191 29.6 32.5 *1 Onset temperature of Tg *2 Mid-point temperature of Tg *3 End temperature of Tg *4 Specific Heat Capacity difference before and after Tg *5 Intersection of the extrapolation line *6 Peak temperature of loss modulus (E”) at measurement frequency 1Hz 3.