A Comparison of Producer Gas, Biochar, and Activated Carbon from Two Distributed Scale Thermochemical Conversion Systems Used to Process Forest Biomass
Total Page:16
File Type:pdf, Size:1020Kb
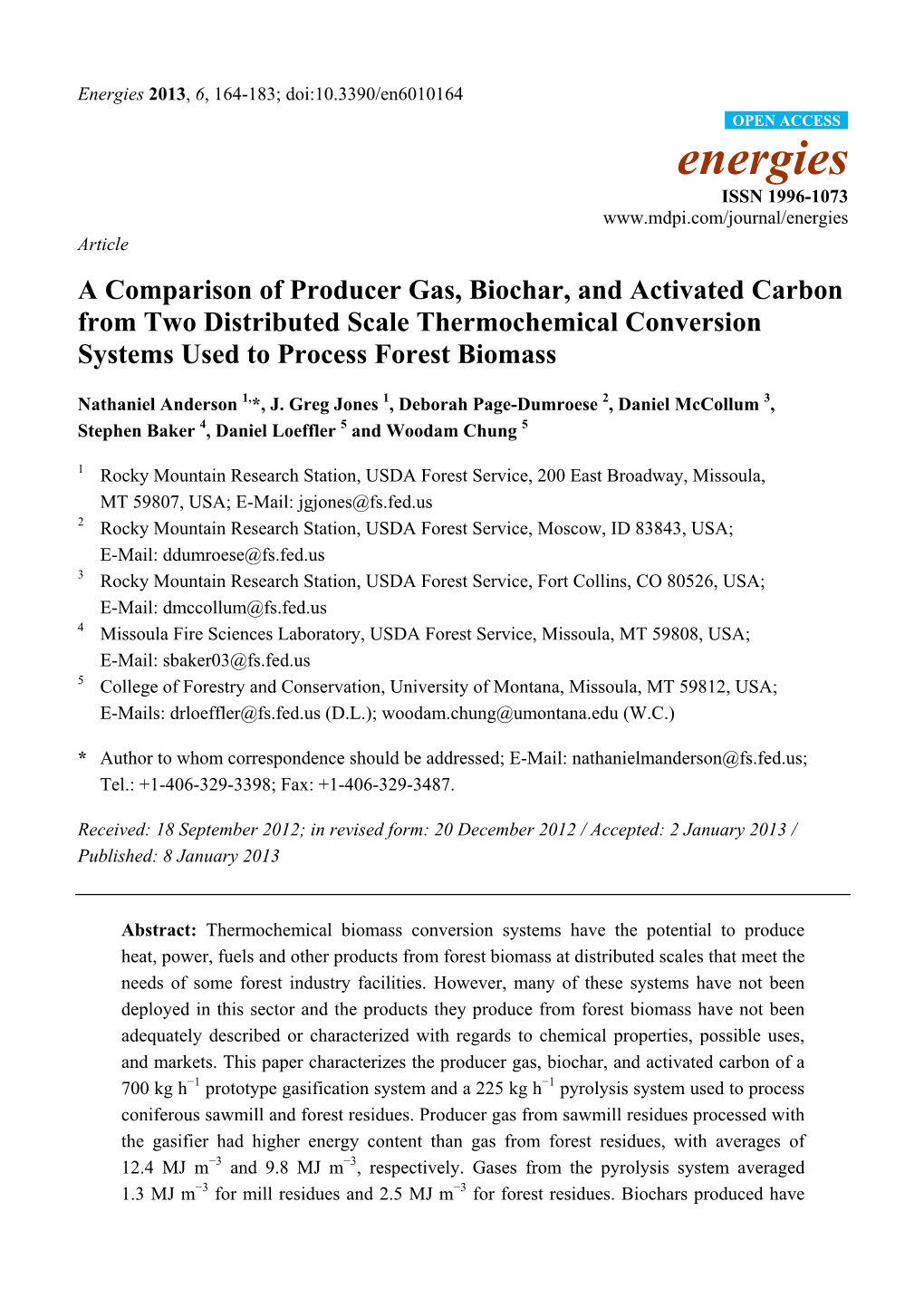
Load more
Recommended publications
-
FAOSTAT-Forestry Definitions
FOREST PRODUCTS DEFINITIONS General terms FAOSTAT - Forestry JOINT FOREST SECTOR QUESTIONNAIRE Item Item Code Definition code coniferous C Coniferous All woods derived from trees classified botanically as Gymnospermae, e.g. Abies spp., Araucaria spp., Cedrus spp., Chamaecyparis spp., Cupressus spp., Larix spp., Picea spp., Pinus spp., Thuja spp., Tsuga spp., etc. These are generally referred to as softwoods. non-coniferous NC Non-Coniferous All woods derived from trees classified botanically as Angiospermae, e.g. Acer spp., Dipterocarpus spp., Entandrophragma spp., Eucalyptus spp., Fagus spp., Populus spp., Quercus spp., Shorea spp., Swietonia spp., Tectona spp., etc. These are generally referred to as broadleaves or hardwoods. tropical NC.T Tropical Tropical timber is defined in the International Tropical Timber Agreement (1994) as follows: “Non-coniferous tropical wood for industrial uses, which grows or is produced in the countries situated between the Tropic of Cancer and the Tropic of Capricorn. The term covers logs, sawnwood, veneer sheets and plywood. Plywood which includes in some measure conifers of tropical origin shall also be covered by the definition.” For the purposes of this questionnaire, tropical sawnwood, veneer sheets and plywood shall also include products produced in non-tropical countries from imported tropical roundwood. Please indicate if statistics provided under "tropical" in this questionnaire may include species or products beyond the scope of this definition. Year Data are requested for the calendar year (January-December) indicated. 2 Transactions FAOSTAT - Forestry JOINT FOREST SECTOR QUESTIONNAIRE Element Element Code Definition code 5516 Production Quantity Removals The volume of all trees, living or dead, that are felled and removed from the forest, other wooded land or other felling sites. -
Quality Wood Chip Fuel Depends on the Size of the Installation in Which It Is to Be Used: Pieter D
Harvesting / Transportation No. 6 The quality requirements for wood chip Quality wood chip fuel depends on the size of the installation in which it is to be used: Pieter D. Kofman 1 Small boilers (<250 kW) require a high quality wood fuel with a low moisture content (<30%) and a small, even chip with few, if any, Quality wood fuel depends mainly on: oversize or overlong particles. A • moisture content, low level of fungal spores is required. • particle size distribution, Medium boilers (250 kW<X<1 MW) • tree species, are more tolerant of moisture content (30-40%) and can handle a • bulk density, coarser chip than small boilers. • level of dust and fungal spores in the fuel, and Still, the amount of oversize and overlong particles should be • ash content. limited. A low level of fungal spores is required. Good quality wood chip fuel is produced by machines with sharp knives, with the ability to vary the size of chip produced to meet end-user specifications. Other Large boilers (>1 MW) are tolerant machines use hammers or flails to reduce particle size and produce hogfuel, of both moisture content (30-55%) and chip quality. The level of fungal which is unsuitable for use in small installations. Large installations can, spores can be higher because however, also have problems in handling and combusting hogfuel. For forest these installations usually take thinnings and other roundwood, chipping is the preferred option. their combustion air from the chip silo which reduces spore This note deals with wood chips only, even though there are other wood fuels, concentrations in and around the such as hogfuel, sawdust, firewood, peelings from fence posts, etc. -
SHELTON RESEARCH, INC. 1517 Pacheco St
SHELTON RESEARCH, INC. 1517 Pacheco St. P.O. Box 5235 Santa Fe, NM 87502 505-983-9457 EVALUATim OF LOW-EMISSION WOOD STOVES by I Jay W. Shelton and Larry W. Gay Shelton Research, Inc. P.O. Box 5235 ! 1517 Pacheco Street Santa Fe, New Mexico 87501 [ June 23, 1986 FINAL REPORT I OON1RACT A3-122-32 Prepared for CALIFORNIA AIR RESOURCES BOARD P.O. Box 2815 1102 Q Street Sacramento, California 95812 Shelton Research, Ince Research Report No. 1086 I, TABLE CF CDmN.rS la PAGE 1' 1 LIST Clii' T~S••••••••••••••••••••••••••••• I~ LIST OF FIGURES •••••••••••••••••••••••••••• ii r } 1. SlM'v1ARY AND CINa.,USICNS •••••••••••••••••••• 1 ~- 2. RE~T1rns•••••••••••••••••••••••••••• 3 ! 3. I N'IRmJCTI. rn••••••••••••••••••••••••••••••• 4 4. APPLIANCE AND FUEL SELECTirn••••••••••••••• 5 5. 'IEa-IN"I oo_, JI'IIDAOI. •••.•••••...•.•••••.•••. 14 Test cycles •••••••••••••••••••••••••••••• 14 Installation••••••••••••••••••••••••••••• 16 Stove Q?eration•••••••••••••••••••••••••• 16 Fuel Properties•••••••••••••••••••••••••• 16 Measursnent Methods •••••••••••••••••••••• 18 Data Acquisition and Processing•••••••••• 29 r; 6. RESlJI..,TS. • • • • • • • • • • • • • • • • • • • • • • • • • • • • • • • • • • • 30 J Introduction••••••••••••••••••••••••••••• 30 Units for Fmissions •••••••••••••••••••••• 30 E:x: tra Tes ts •• ., •• "•••••••••••••••••••••••• 30 Particulate Matter ••••••••••••••••••••••• 31 Oeosote•••••• ., •••••••••••••••••••••••••• 32 P.AII. ••••••••••• o • •••••••••••••••••••••••• 32 l NOx •••••••••• t.10••·········· ............. 32 .Amoonia and cyanide•••••••••••••••••••••• -
Bibliography of Wood Distillation
Bibliography of WoodDistillation T.CL[). Compiled by Gerald A.Walls Arranged by Morrie Craig BibliographY 5 October 1966 For.stProductsResearch FOREST RESEARCHLABORATORY OREGON STATEUNIVERSITY Corvallis PROGRAM AND PURPOSE The Forest Research Laboratoryof the School of Forestry combines a well-equipped laboratory witha staff of forest and wood scientists in program designed to improve the forestresource and promote full uti- lization of forest products. Theextensive research done by the Labora tory is supported by the forest industryand by state and federal funds. The current report results fromstudies in forest products, where wood scientists and technologists,chemists, and engineers are con- cerned with properties, processing,utilization, and marketing of wood and of timber by-products. The PROGRAM of research includes identifying and developing chemicals fromwood, improving pulping of wood and woodresidues, investigating and improving manufacturingtechniques, extending life of wood by treating, developing better methods ofseasoning wood for higher quality and reduced costs, cooperating with forest scientists to determineeffects of growing conditionson wood properties, and evaluating engineering properties ofwood and wood- based materials and structures. The PURPOSE of researchon forest products is to expand markets, create new jobs, and bringmore dollar returns, thus advancing the interests of forestry and forestindustries, by > developing products from residuesand timber now wasted, and > improving treatment and designof present wood products. Table of Contents INTRODUCTION 3 BOOKS 4 ARTICLES AND BULLETINS 5 PATENTS 46 Australia 46 Austria 46 Be1giun 46 Canada 47 Czechoslovakia 47 Denmark 47 France 47 Germany 51 Great Britain 52 India 55 Italy 55 Japan 55 Netherlands 56 Norway 56 Poland 56 Russia 56 Spain 57 Sweden 57 Switzerland 58 United States 59 Bibliography of Wood Distillation INTRODUCTION This bibliography is a revision and extension to1964 of Bibli- ography of Wood Distillation, 1907-1953published in 1955. -
Energy Evaluation of Biochar Obtained from the Pyrolysis of Pine Pellets
J Therm Anal Calorim (2016) 126:1879–1887 DOI 10.1007/s10973-016-5683-4 Energy evaluation of biochar obtained from the pyrolysis of pine pellets 1 2 3 3 Lidya B. Santos • Maria V. Striebeck • Marisa S. Crespi • Jorge M. V. Capela • 3 1 Clovis A. Ribeiro • Marcelo De Julio Received: 1 June 2015 / Accepted: 3 July 2016 / Published online: 22 July 2016 Ó Akade´miai Kiado´, Budapest, Hungary 2016 Abstract The wood pellets are mainly used in heating compared to pellets in nature, showing a greater amount of environments, commercial and residential, as well as fuel energy per unit, high stability, reduced moisture content for production of thermal and electric energy in industrial and reduced ash content. The kinetic of combustion to plants. Furthermore, the heterogeneity and variable mois- biochar in oxygen-rich atmosphere showed the dependence ture content, combined with the high cost of transport, are between the activation energy and conversion degree, with limiting challenges that must be overcome with new a continuous decrease in the activation energy, character- technologies and new products. In this context, torrefaction istic of complex processes comprised by initial reversible and pyrolysis are attractive alternatives for increasing reaction followed by an irreversible one. energy density and decreasing the moisture content of the samples, based on thermochemical conversion in a non- Keywords Energetic characterization Á Torrefaction Á oxidizing atmosphere. Samples were produced to perform Pyrolysis Á Pine pellets Á Biochar Á Non-isothermal kinetic the energetic characterization of biochar from pine pellet using different heating rates 5–30 °C min-1, different residence temperatures 200, 280 and 570 °C and different Introduction residence time (1 and 0.5 h). -
Interaction of Biochar Type and Rhizobia Inoculation Increases the Growth and Biological Nitrogen Fixation of Robinia Pseudoacacia Seedlings
Article Interaction of Biochar Type and Rhizobia Inoculation Increases the Growth and Biological Nitrogen Fixation of Robinia pseudoacacia Seedlings Qiaoyu Sun 1, Yong Liu 2, Hongbin Liu 1 and R. Kasten Dumroese 3,* 1 Key Laboratory of Non-Point Source Pollution Control, Ministry of Agriculture, Institute of Agricultural Resources and Regional Planning, Chinese Academy of Agricultural Sciences, No. 12 Zhongguancun South Street, Haidian District, Beijing 10081, China; [email protected] (Q.S.); [email protected] (H.L.) 2 Key Laboratory for Silviculture and Conservation, Ministry of Education, Beijing Forestry University, No. 35 Tsinghua East Road, Haidian District, Beijing 100083, China; [email protected] 3 US Department of Agriculture, Forest Service, Rocky Mountain Research Station, 1221 South Main Street, Moscow, ID 83843, USA * Correspondence: [email protected]; Tel.: +1-208-883-2324; Fax: +1-208-882-3915 Received: 29 May 2020; Accepted: 23 June 2020; Published: 26 June 2020 Abstract: Adding biochar to soil can change soil properties and subsequently affect plant growth, but this effect can vary because of different feedstocks and methods (e.g., pyrolysis or gasification) used to create the biochar. Growth and biological nitrogen fixation (BNF) of leguminous plants can be improved with rhizobia inoculation that fosters nodule development. Thus, this factorial greenhouse study examined the effects of two types of biochar (i.e., pyrolysis and gasification) added at a rate of 5% (v:v) to a peat-based growth substrate and rhizobia inoculation (yes or no) on 15 15 Robinia pseudoacacia (black locust) seedlings supplied with NH4 NO3. Seedling and nodule growth, nitrogen (N) content, and δ15N 1000 were evaluated after 3 months. -
Prediction of Producer Gas Composition for Small Scale Commercial Downdraft Gasifiers
PREDICTION OF PRODUCER GAS COMPOSITION FOR SMALL SCALE COMMERCIAL DOWNDRAFT GASIFIERS H Roesch*, J Dascomb, B Greska, A Krothapalli *Corresponding Author email: [email protected] *Corresponding Author phone: +18504967682 Energy and Sustainability Center, Florida State University 2525 Pottsdamer St, #229A, Tallahassee, Fl 32310 ABSTRACT: The goal of this study was to produce a model predicting the composition and heating value of producer gas made from a small scale (20-250 kWth), down-draft gasifier. Due the non-ideal conditions in this type of gasifier, classical thermodynamic equilibrium models are inaccurate. A more reliable prediction model for gas produced in a system of this size and type is needed. Eight biomass feedstocks were gasified and analyzed for this study. The pelletized feedstocks chosen were; alfalfa, algae, field grass, hemp, miscanthus, peanut shells, pine, and municipal solid waste. The feedstocks were chosen for their wide ranging availability and low costs. The commercial downdraft gasifier used was an Ankur Scientific WBG-20. This air-fed gasifier is capable of producing synthesis gas at a rate of up to 60 Nm3/hr (50 kWth). Each feedstock was first characterized by proximate and ultimate analysis, and then the synthesis gas was analyzed by gas chromatography. The large variation of reaction temperatures and equivalence ratios occurring in the economic downdraft gasifier reduced the accuracy of the conventional thermodynamic equilibrium simulation. The synthesis gas produced in these tests was used to create a more applicable model for estimating composition and heating value for this type of system. The model developed from these tests estimates the heating value of the synthesis gas produced from the ultimate and proximate analysis of the feedstock with an average error of 5% over all feedstocks tested. -
Cleaning Ucg Synthesis
Underground Coal Gasification (UCG), its Potential Prospects and its Challenges Dr. Duncan Seddon, FRACI, CChem, MSPE, Duncan Seddon & Associates Pty Ltd Email: [email protected] Dr. Mike Clarke, FIEAust, CPEng, FAusIMM, RPEQ, M.E.T.T.S. Pty Ltd Email: [email protected] Abstract: Coal is widely available in most parts of the world. Underground Coal Gasification (UCG) gives the promise of turning many poor quality coal resources into exploitable reserves by delivering energy in the form of synthesis gas, potentially at very low cost. The synthesis gas can be used for generation of electricity and the production of fuels and chemicals by commercially proven technology. Furthermore, any carbon present in the synthesis gas not used for downstream products could be easily separated and geo-sequestrated. This could extend the Fossil Fuel Age by providing low cost energy for developing and developed countries alike. Unfortunately, as Australian experience has shown, UCG also comes with technical and environmental challenges that are still not fully resolved. The paper outlines key developments in UCG and issues raised by Australian experience, particularly in regard to the contamination of acquifers. The paper discusses the quality of UCG synthesis gas and its potential use in downstream applications. The clean-up steps required for various downstream applications are described. A key hurdle to up-take of UCG is the overall cost of clean-up which has to be added to the cost of UCG production. This cost is discussed and the potential of UCG as a major new feedstock described. 1.0 Introduction Underground Coal Gasification (UCG) as a source of synthesis gas (syn-gas) for power generation, liquid fuels production and/or chemicals and fertiliser manufacture has been made to look beguilingly simple and straightforward by many of it proponents. -
Biochar As an Innovative Wood Product: a Look at Barriers to Realization of Its Full Potential
BIOCHAR AS AN INNOVATIVE WOOD PRODUCT: A LOOK AT BARRIERS TO REALIZATION OF ITS FULL POTENTIAL May 2017 Harry Groot Jeff Howe, Ph. D Jim Bowyer, Ph. D Ed Pepke, Ph. D. Richard A. Levins, Ph. D. Kathryn Fernholz DOVETAIL PARTNERS, INC. Biochar as an Innovative Wood Product A Look at Barriers to Realization of its Full Potential Executive Summary In the previous Dovetail Report Biochar 101: An Introduction to an Ancient Product Offering Modern Opportunities (Groot et al. 20161) the bottom line was: “Biochar is a product with clear benefits but many questions yet to be answered.” That remains the case. However, ongoing research has expanded the knowledge base, and the debate about biochar’s value and cost effectiveness is narrowing as more is known. A barrier to further market growth is that the industry producing biochar is unsettled, with Photo 1. Biochar made from Pecan Hulls (photo by H. Groot) little agreement regarding product standards, message, or carbon accounting. There is an opportunity for more collaboration to resolve these issues, especially among the mid to large-scale producers. The most common use of biochar is as a soil amendment for high-value fruit and vegetable crops, including use in greenhouse and nursery operations, and there is already significant market acceptance in this sector. Biochar is also used to remove impurities and toxins in water filtration and soil remediation, and these applications appear to offer significant growth potential. Commodity crop production conceivably offers the potential for use of the greatest volume of biochar, but there is little information available about the relative cost and benefits of biochar in this application. -
Non-Timber Forest Products in Brazil: a Bibliometric and a State of the Art Review
sustainability Review Non-Timber Forest Products in Brazil: A Bibliometric and a State of the Art Review Thiago Cardoso Silva * , Emmanoella Costa Guaraná Araujo, Tarcila Rosa da Silva Lins , Cibelle Amaral Reis, Carlos Roberto Sanquetta and Márcio Pereira da Rocha Department of Forestry Engineering and Technology, Federal University of Paraná, 80.210-170 Curitiba, Brazil; [email protected] (E.C.G.A.); [email protected] (T.R.d.S.L.); [email protected] (C.A.R.); [email protected] (C.R.S.); [email protected] (M.P.d.R.) * Correspondence: [email protected]; Tel.: +55-8199-956-6178 Received: 4 July 2020; Accepted: 22 August 2020; Published: 2 September 2020 Abstract: Non-timber forest products (NTFPs) are a consolidated source of income and acquisition of inputs from forest environments. Therefore, the objective of this work was to carry out a collection of publications on NTFPs in Brazil, until 2019, available in the Scopus database, presenting a bibliometric review and the state of the art of this theme from the evaluation of these publications, discussing the challenges of Brazilian legislation on NTFPs. After screening the articles of interest, 196 documents were evaluated, in which they were observed institutions and authors, analyzing networks of citations and terms used, areas of forest sciences and sciences that encompass the most explored biomes and the most studied species. The results showed that the concern to research on NTFPs in Brazil began in the 1990s, with an increase in the number of publications over the years. Besides that, the research on NTFPs is multidisciplinary, with emphasis on the areas of Agricultural and Biological Sciences and Environmental Science. -
Agroforestry News Index Vol 1 to Vol 22 No 2
Agroforestry News Index Vol 1 to Vol 22 No 2 2 A.R.T. nursery ..... Vol 2, No 4, page 2 Acorns, edible from oaks ..... Vol 5, No 4, page 3 Aaron, J R & Richards: British woodland produce (book review) ..... Acorns, harvesting ..... Vol 5, No 4, Vol 1, No 4, page 34 page 3 Abies balsamea ..... Vol 8, No 2, page Acorns, nutritional composition ..... 31 Vol 5, No 4, page 4 Abies sibirica ..... Vol 8, No 2, page 31 Acorns, removing tannins from ..... Vol 5, No 4, page 4 Abies species ..... Vol 19, No 1, page 13 Acorns, shelling ..... Vol 5, No 4, page 3 Acca sellowiana ..... Vol 9, No 3, page 4 Acorns, utilisation ..... Vol 5, No 4, page 4 Acer macrophyllum ..... Vol 16, No 2, page 6 Acorus calamus ..... Vol 8, No 4, page 6 Acer pseudoplatanus ..... Vol 3, No 1, page 3 Actinidia arguta ..... Vol 1, No 4, page 10 Acer saccharum ..... Vol 16, No 1, page 3 Actinidia arguta, cultivars ..... Vol 1, No 4, page 14 Acer saccharum - strawberry agroforestry system ..... Vol 8, No 1, Actinidia arguta, description ..... Vol page 2 1, No 4, page 10 Acer species, with edible saps ..... Vol Actinidia arguta, drawings ..... Vol 1, 2, No 3, page 26 No 4, page 15 Achillea millefolium ..... Vol 8, No 4, Actinidia arguta, feeding & irrigaton page 5 ..... Vol 1, No 4, page 11 3 Actinidia arguta, fruiting ..... Vol 1, Actinidia spp ..... Vol 5, No 1, page 18 No 4, page 13 Actinorhizal plants ..... Vol 3, No 3, Actinidia arguta, nurseries page 30 supplying ..... Vol 1, No 4, page 16 Acworth, J M: The potential for farm Actinidia arguta, pests and diseases forestry, agroforestry and novel tree .... -
Wood Fuel Supply Interventions
BIOMASS ENERGY STRATEGY (BEST) WOOD FUEL SUPPLY INTERVENTIONS LESSONS LEARNED AND RECOMMENDATIONS Dr. Steve Sepp, Dr. Stefan Mann (ECO Consult, Germany) April 2009 “Lessons Learned and Policy Recom‐ mendations for Woodfuel Supply Inter‐ ventions” Dr. Steve Sepp, Dr. Stefan Mann (ECO Consult , Germany) Table of Content 1 EXECUTIVE SUMMARY ........................................................................................................................... 5 2 INTRODUCTION ................................................................................................................................... 10 3 LINKAGES TO THE BIOMASS ENERGY STRATEGY (BEST) ........................................................................ 11 4 SPECIFICS OF THE FOREST SECTOR ....................................................................................................... 12 4.1 CURRENT BARRIERS TO THE SUSTAINABLE SUPPLY OF WOOD‐BASED SOLID FUELS ................................................... 14 4.1.1 Discrimination of wood‐based solid fuels in national energy sector policies and strategies .......... 14 4.1.2 Informal, unregulated and non‐sustainable use of wood‐based solid fuels .................................... 15 4.1.3 Growing complexity of societal demand for forest resources ......................................................... 16 5 ROLES AND POTENTIALS OF DIFFERENT STAKEHOLDERS ...................................................................... 17 6 RECOMMENDATIONS FOR WOODFUEL SUPPLY ..................................................................................