Wind Turbine Tribology Seminar: a Recap
Total Page:16
File Type:pdf, Size:1020Kb
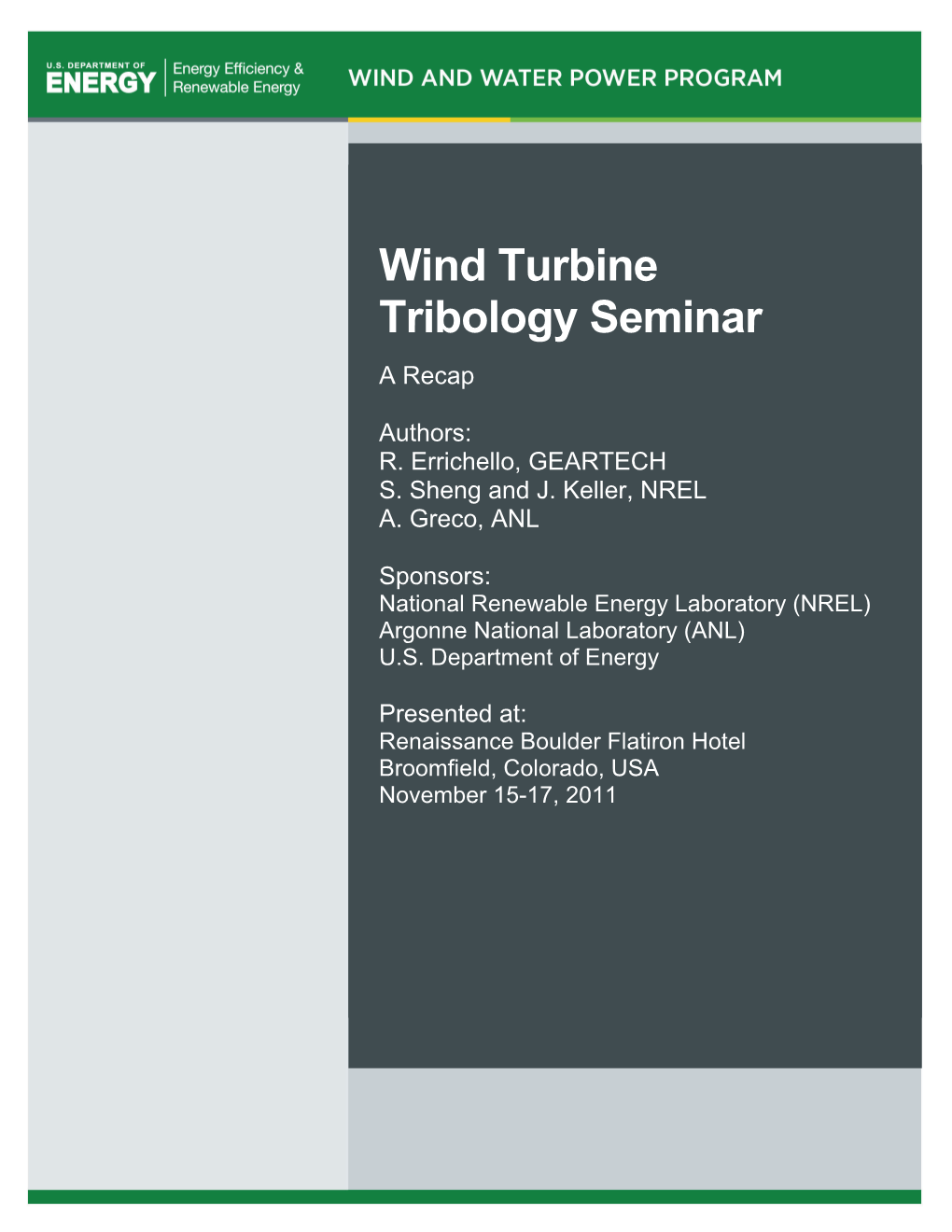
Load more
Recommended publications
-
Lubrication Chemistry Viewed from DFT-Based Concepts and Electronic Structural Principles
Int. J. Mol. Sci. 2004, 5, 13-34 International Journal of Molecular Sciences ISSN 1422-0067 © 2004 by MDPI www.mdpi.org/ijms/ Lubrication Chemistry Viewed from DFT-Based Concepts and Electronic Structural Principles Li Shenghua*, Yang He and Jin Yuansheng State Key Laboratory of Tribology, Tsinghua University, Beijing 100084, P.R. China Tel.: +86 (10) 62772509, Fax: +86 (10) 62784691, E-mail: [email protected] URL: http://www.pim.tsinghua.edu.cn/sklt/sklt.html *Author to whom correspondence should be addressed. Received: 16 April 2003 / Accepted: 16 October 2003 / Published: 26 December 2003 Abstract: Fundamental molecular issues in lubrication chemistry were reviewed under categories of solution chemistry, contact chemistry and tribochemistry. By introducing the Density Functional Theory(DFT)-derived chemical reactivity parameters (chemical potential, electronegativity, hardness, softness and Fukui function) and related electronic structural principles (electronegativity equalization principle, hard-soft acid-base principle, and maximum hardness principle), their relevancy to lubrication chemistry was explored. It was suggested that DFT, theoretical, conceptual and computational, represents a useful enabling tool to understand lubrication chemistry issues prior to experimentation and the approach may form a key step in the rational design of lubrication chemistry via computational methods. It can also be optimistically anticipated that these considerations will gestate unique DFT-based strategies to understand sophisticated tribology themes, such as origin of friction, essence of wear, adhesion in MEMS/NEMS, chemical mechanical polishing in wafer manufacturing, stress corrosion, chemical control of friction and wear, and construction of designer tribochemical systems. Keywords: Lubrication chemistry, DFT, chemical reactivity indices, electronic structural principle, tribochemistry, mechanochemistry. -
The Use of Artificial Intelligence in Tribology—A Perspective
lubricants Perspective The Use of Artificial Intelligence in Tribology—A Perspective Andreas Rosenkranz 1,*, Max Marian 2,* , Francisco J. Profito 3, Nathan Aragon 4 and Raj Shah 4 1 Department of Chemical Engineering, Biotechnology and Materials, University of Chile, Santiago 7820436, Chile 2 Engineering Design, Friedrich-Alexander-University Erlangen-Nuremberg (FAU), 91058 Erlangen, Germany 3 Department of Mechanical Engineering, Polytechnic School, University of São Paulo, São Paulo 17033360, Brazil; fprofi[email protected] 4 Koehler Instrument Company, Holtsville, NY 11742, USA; [email protected] (N.A.); [email protected] (R.S.) * Correspondence: [email protected] (A.R.); [email protected] (M.M.) Abstract: Artificial intelligence and, in particular, machine learning methods have gained notable attention in the tribological community due to their ability to predict tribologically relevant pa- rameters such as, for instance, the coefficient of friction or the oil film thickness. This perspective aims at highlighting some of the recent advances achieved by implementing artificial intelligence, specifically artificial neutral networks, towards tribological research. The presentation and discussion of successful case studies using these approaches in a tribological context clearly demonstrates their ability to accurately and efficiently predict these tribological characteristics. Regarding future research directions and trends, we emphasis on the extended use of artificial intelligence and machine learning concepts in the field of tribology including the characterization of the resulting surface topography and the design of lubricated systems. Keywords: artificial intelligence; machine learning; artificial neural networks; tribology 1. Introduction and Background Citation: Rosenkranz, A.; Marian, M.; There have been very recent advances in applying methods of deep or machine Profito, F.J.; Aragon, N.; Shah, R. -
TRIBOLOGY Lecture 3: FRICTION
Video Course on Tribology Prof. Dr Harish Hirani Department of Mechanical Engineering Indian institute of Technology, Delhi Lecture No. # 03 Friction Welcome to the third lecture of video course on Tribology. Topic of this lecture is friction. It is interesting. We experience friction in day to day life when you walk we experience friction, when we cycle we experience friction, when we drive we experience friction. This is very common mode which we experience every day. TRIBOLOGY Lecture 3: FRICTION And often when you go to mall, we find this kind of signal or warning that slippery when the floor is wet. So, you need to be careful when you walk resending the water place as lubricant layer. Some Typical Values of Coefficient of Friction for Metals sliding on themselves Metals Sliding on themselves µ Aluminum 1.5 Copper 1.5 Copper((oxide film not penetrated) 0.5 Gold 2.5 Iron 1.2 Platinum 3 Silver 1.5 Steel(mild steel) 0.8 Steel(tool steel) 0.4 Observations: 1. μ > 1.0 2. Mild steel vs Tool steel 3. μ depends on environment. And it reduces the friction. So, we need to walk with more force. So, the overall the friction force turn out to be same. I have gone through number of books and found number of variation in coefficient of friction. So, I am just showing on the first slide of this course that typical value of coefficient friction which is often quoted in books. We say these values are static coefficient of friction or this value belongs to static coefficient of friction. -
Rolling Bearings and Seals in Electric Motors and Generators
Rolling bearings and seals in electric motors and generators ® SKF, @PTITUDE, BAKER, CARB, DUOFLEX, DURATEMP, ICOS, INSOCOAT, MARLIN, MICROLOG, MONOFLEX, MULTILOG, SEAL JET, SKF EXPLORER, SYSTEM 24 and WAVE are registered trademarks of the SKF Group. © SKF Group 2013 The contents of this publication are the copyright of the publisher and may not be reproduced (even extracts) unless permission is granted. Every care has been taken to ensure the accuracy of the information contained in this publication but no liability can be accepted for any loss or damage whether direct, indirect or consequential arising out of the use of the information contained herein. PUB 54/P7 13459 EN · August 2013 This publication supersedes publication 5230 E and 6230 EN. Certain image(s) used under license from Shutterstock.com. 1 Rolling bearings in electric machines 1 2 Bearing systems 2 3 Seals in electric machines 3 4 Tolerances and fits 4 5 Lubrication 5 6 Bearing mounting, dis mounting and motor testing 6 7 Bearing damage and corrective actions 7 8 SKF solutions 8 Rolling bearings and seals in electric motors and generators A handbook for the industrial designer and end-user 2 Foreword This SKF applications, lubrication and maintenance handbook for bearings and seals in electric motors and generators has been devel oped with various industry specialists in mind. For designers of electric machines1), this handbook provides the information needed to optimize a variety of bearing arrangements. For specialists working in various industries using electric machines, there are recommendations on how to maximize bearing service life from appropriate mounting, mainten ance and lubrication. -
Static Friction at Fractal Interfaces
Dorian Hanaor, Yixiang Gan and Itai Einav (2016). Static friction at fractal interfaces. Tribology International, 93, 229-238. DOI: 10.1016/j.triboint.2015.09.016 Static friction at fractal interfaces Dorian A. H. Hanaor, Yixiang Gan, Itai Einav School of Civil Engineering, University of Sydney, NSW 2006, Australia https://doi.org/10.1016/j.triboint.2015.09.016 Abstract: Tribological phenomena are governed by combined effects of material properties, topology and surface- chemistry. We study the interplay of multiscale-surface-structures with molecular-scale interactions towards interpreting static frictional interactions at fractal interfaces. By spline-assisted-discretization we analyse asperity interactions in pairs of contacting fractal surface profiles. For elastically deforming asperities, force analysis reveals greater friction at surfaces exhibiting higher fractality, with increasing molecular-scale friction amplifying this trend. Increasing adhesive strength yields higher overall friction at surfaces of lower fractality owing to greater true-contact-area. In systems where adhesive-type interactions play an important role, such as those where cold-welded junctions form, friction is minimised at an intermediate value of surface profile fractality found here to be in the regime 1.3-1.5. Our results have implications for systems exhibiting evolving surface structures. Keywords: Contact mechanics, friction, fractal, surface structures 1 Dorian Hanaor, Yixiang Gan and Itai Einav (2016). Static friction at fractal interfaces. Tribology -
Signature Redacted August 7, 2015 C Ifdb Y
Scale-up of a High-Technology Manufacturing Startup: Improving Product Reliability Through Systematic Failure Analysis and Accelerated Life Testing MASSACHUSETTS INSTITUTE by OF TECHNOLOGY, All Shabbir OCT 0 12015 B.A.Sc. Mechanical Engineering, University of Waterloo (2014) LIBRARIES Submitted to the Department of Mechanical Engineering in partial fulfillment of the requirements for the degree of Master of Engineering in Manufacturing at the MASSACHUSETTS INSTITUTE OF TECHNOLOGY September 2015 @ Ali Shabbir, MMXV. All rights reserved. The author hereby grants to MIT permission to reproduce and to distribute publicly paper and electronic copies of this thesis document in whole or in part in any medium now known or hereafter created. Signature redacted A uthor . ......... ........... Department of Mechanical Engineering Signature redacted August 7, 2015 C ifdb y...................------------ David E. Hardt Ralph E. and Eloise F. Cross Professor of echanical Engineering Accepted by ..... ............ Signature redacted ...... David E. Hardt Chairman, Department Committee on Graduate Theses Scale-up of a High-Technology Manufacturing Startup: Improving Product Reliability Through Systematic Failure Analysis and Accelerated Life Testing by Ali Shabbir Submitted to the Department of Mechanical Engineering on August 7, 2015, in partial fulfillment of the requirements for the degree of Master of Engineering in Manufacturing Abstract Ensuring product reliability is a key driver of success during the scale-up of a high- technology manufacturing startup. Reliability impacts the company image and its financial health, however most manufacturing startups do not have a solid under- standing of their product's reliability. The purpose of this thesis is to introduce systematic failure analysis to the engineering design process and to establish a frame- work for testing and analyzing product life so that imperative business decisions and design improvements could be made with regards to reliability. -
Tribology of Polymer Blends PBT + PTFE
materials Article Tribology of Polymer Blends PBT + PTFE Constantin Georgescu 1,* , Lorena Deleanu 1,*, Larisa Chiper Titire 1 and Alina Cantaragiu Ceoromila 2 1 Department of Mechanical Engineering, Faculty of Engineering, “Dunarea de Jos” University of Galati, 800008 Galati, Romania; [email protected] 2 Department of Applied Sciences, Cross-Border Faculty, “Dunarea de Jos” University of Galati, 800008 Galati, Romania; [email protected] * Correspondence: [email protected] (C.G.); [email protected] (L.D.); Tel.: +40-743-105-835 (L.D.) Abstract: This paper presents results on tribological characteristics for polymer blends made of polybutylene terephthalate (PBT) and polytetrafluoroethylene (PTFE). This blend is relatively new in research as PBT has restricted processability because of its processing temperature near the degradation one. Tests were done block-on-ring tribotester, in dry regime, the variables being the PTFE concentration (0%, 5%, 10% and 15% wt) and the sliding regime parameters (load: 1, 2.5 and 5 N, the sliding speed: 0.25, 0.5 and 0.75 m/s, and the sliding distance: 2500, 5000 and 7500 m). Results are encouraging as PBT as neat polymer has very good tribological characteristics in terms of friction coefficient and wear rate. SEM investigation reveals a quite uniform dispersion of PTFE drops in the PBT matrix. Either considered a composite or a blend, the mixture PBT + 15% PTFE exhibits a very good tribological behavior, the resulting material gathering both stable and low friction coefficient and a linear wear rate lower than each component when tested under the same conditions. Keywords: polybutylene terephthalate (PBT); polytetrafluoroethylene (PTFE); blend PBT + PTFE; block-on-ring test; linear wear rate; friction coefficient Citation: Georgescu, C.; Deleanu, L.; Chiper Titire, L.; Ceoromila, A.C. -
3Rd Edition A.R
WEAR – MATERIALS, MECHANISMS AND PRACTICE Editors: M.J. Neale, T.A. Polak and M. Priest Guide to Wear Problems and Testing for Industry M.J. Neale and M. Gee Handbook of Surface Treatment and Coatings M. Neale, T.A. Polak, and M. Priest (Eds) Lubrication and Lubricant Selection – A Practical Guide, 3rd Edition A.R. Lansdown Rolling Contacts T.A. Stolarski and S. Tobe Total Tribology – Towards an integrated approach I. Sherrington, B. Rowe and R. Wood (Eds) Tribology – Lubrication, Friction and Wear I.V. Kragelsky, V.V. Alisin, N.K. Myshkin and M.I. Petrokovets Wear – Materials, Mechanisms and Practice G. Stachowiak (Ed.) WEAR – MATERIALS, MECHANISMS AND PRACTICE Edited by Gwidon W. Stachowiak Copyright © 2005 John Wiley & Sons Ltd, The Atrium, Southern Gate, Chichester, West Sussex PO19 8SQ, England Telephone (+44) 1243 779777 Chapter 1 Copyright © I.M. Hutchings Email (for orders and customer service enquiries): [email protected] Visit our Home Page on www.wiley.com Reprinted with corrections May 2006 All Rights Reserved. No part of this publication may be reproduced, stored in a retrieval system or transmitted in any form or by any means, electronic, mechanical, photocopying, recording, scanning or otherwise, except under the terms of the Copyright, Designs and Patents Act 1988 or under the terms of a licence issued by the Copyright Licensing Agency Ltd, 90 Tottenham Court Road, London W1T 4LP, UK, without the permission in writing of the Publisher. Requests to the Publisher should be addressed to the Permissions Department, John Wiley & Sons Ltd, The Atrium, Southern Gate, Chichester, West Sussex PO19 8SQ, England, or emailed to [email protected], or faxed to (+44) 1243 770620. -
Tribology Module3: Wear
Tribology Module3: Wear Q.1. Why subsurface cracks are formed due to cyclic load? Ans: Cyclic loading often causes repetitive reversal of stresses, such as compressive stress to tensile stress. Due to such change in stresses, material experiences tiredness. Microstructure in-homogeneity, under tiring load condition, helps the formation of subsurface cracks. Q.2. What is zero wear limits? Ans: “Zero wear” means wear of material surfaces remains within the order of the surface finish. In other words “Zero wear limit” is the initial surface roughness of the material. Q.3. If indium has so high affinity that causes adhesive wear then why do we use it? Can indium be used as lubricant between two steel surfaces? Ans: Because of high affinity of indium, it is used to bond certain non-metallic such as glass, glazed, xeramics, mica, quartz, various metallic oxides, etc. It can be used as solid lubricant between two steel surfaces. Q.4. In adhesion wear taking place between similar materials, which surface is likely to get more damage? Won’t the chuck of particles be with the lower surface in case of similar surface? Ans: The outcome of adhesive wear is growing roughness and creation of lumps above the original surface. Lose of material from the surface depends on the softness of material. Softer material loses more material compared to harder material. In other words nothing can be said about which surface (lower/upper) will lose more material. Lose of material will depend on local hardness of the material. Q.5. What is “back transfer”? Ans: In adhesive wear, material is transferred from one material to other. -
Molecular Tribology
R.M. Overney Molecular Tribology Friction, wear and adhesion, the three major aspects of Tribology play an important role in mankind’s efforts to conserve energy. Friction and drag alone account for about one third of the energy needed to run our machines in the industrialized World. This does not account for energy losses due to consequential wear and failure of equipment. It is argued that about 1-2 percent of the GDP could be recovered with appropriate tribological solutions that entail besides liquid phase lubrication also effective solid phase solutions. The challenge is still to connect rational molecular designs to the phenomenological process parameters that attempt to describe the energy dissipation during frictional sliding. Historical Developments The Laws of Friction The Science of Tribology (Greek tribos : rubbing ) encompasses the study of adhesion , friction , lubrication and wear . All of these rate dependent processes are dissipative in nature. They involve interfaces that are transient. While adhesion studies are concerned with the formation and destruction of interfaces involving motions normal to the interface, friction studies concentrate on lateral motions of adjacent surfaces in contact. One very important aspect of friction studies has been the behavior of the third medium, referred to as lubricant. In contrast to lubrication that typically concentrates on fluid media (the exception are solid lubricants), wear is the visual manifestation of plastic deformations in solid material that occur in the course of dynamic contact. Leonardo da Vinci (1452-1519)) can be named as the father of modern Tribology . He studied a wide variety of subtopics form friction, lubrication and wear, to bearing materials and geometries, gears, screw-jacks, and rolling-element bearings. -
A High-Temperature, Self-Lubricating, Powder Metallurgy Composite
NASA Technical Memorandum 102355 Tribological Properties of PM212: A High-Temperature, Self-Lubricating, Powder Metallurgy Composite Christopher DellaCorte and Harold E. Sliney Lewis Research Center Cleveland, Ohio Prepared for the 1990 Annual Meeting of the Society of Tribologists and Lubrication Engineers Denver, Colorado, May 7-11, 1990 (_ASA-T,A-I02)55) TRI_UtOGICAL PRqP_RTIES OF N90-12o_9 PM212: A HIGh-TEMPERATURE, SLLF-LUBRICATING, P_W_ER M_TALLU_Y C_MPuSITE (NASA) 22 p CSCL OTA UnC|dS GSIZ] 0243Z48 NASA Technical Memorandum 102355 Tribological Properties of PM212: A High-Temperature, Self-Lubricating, Powder Metallurgy Composite Christopher DellaCorte and Harold E. Sliney Lewis Research Center Cleveland, Ohio Prepared for the 1990 Annual Meeting of the Society of Tribologists and Lubrication Engineers Denver, Colorado, May 7-11, 1990 (NASA-T'_-IO2355) TRI_ULOGICAL PRQPERTIES OF Ngo-12059 P_212: _ HIGo-TfMO_RATURE, SCLF-LU6_ICATING, P_N_ER METALLIJK_Y C_M_OS[TE (NASA) ZZ p CSCL _TA G._/Z] TRIBOLOGICAL PROPERTIES OF PM212: A HIGH-TEMPERATURE, SELF-LUBRICATING, PONDER METALLURGY COMPOSITE Christopher DellaCorte and Harold E. Sliney National Aeronautics and Space Administration Lewis Research Center Cleveland, Ohio 44135 ABSTRACT This paper describes a research program to develop and evaluate a new high temperature, self-lubricating powder metallurgy composite, PM212. PM212 has the same composition as the plasma-sprayed coating, PS212, which contains 70 wt % metal-bonded chromium carbide, 15 wt % silver and 15 wt % barium fluoride/calcium fluoride eutectic. The carbide acts as a wear resistant matrix and the silver and fluorides act as low and high temperature lubricants, respectively. The material is prepared by sequential cold press, cold isostatic pressing and sintering techniques. -
Recent Advances in the Tribology and Bioengineering of the Skin
RECENT ADVANCES IN THE TRIBOLOGY AND BIOENGINEERING OF THE SKIN 25 November 2014 Tribology Group and Biomedical One Birdcage Walk, London Division www.imeche.org/events/S6128 Seminar RECENT ADVANCES IN THE TRIBOLOGY AND BIOENGINEERING OF THE SKIN 25 November 2014, One Birdcage Walk, London RECENT ADVANCES IN THE TRIBOLOGY AND BIOENGINEERING BENEFITS OF ATTENDANCE: OF THE SKIN WILL PRESENT CUTTING EDGE SOLUTIONS AND • Analyse how modelling techniques are RADICAL NEW THINKING THAT used to elucidate the complex mechanics CHARACTERISE AND PREDICT of the skin with Dr. Georges Limbert THE BIOPHYSICS OF THE SKIN IN HEALTH AND DISEASE. • Understand how microclimate factors influence the integrity of the loaded skin This seminar will explore modelling techniques interface with Prof. Dan Bader for biotribology, including the latest advanced computational models for skin biophysics. • Learn how to tackle current challenges The principal goal is to explore how they in healthcare and personal care device are developed and can be implemented in development with Dr. Steve Franklin commercial, finite element codes to accelerate product development. • Study the prospects of consultant engineers in the high-growth ‘engineering for life sciences’ market AGENDA SNAPSHOT: (For the full programme, see page 2) • Predictive modelling of the static and dynamic friction behaviour of human skin • Biotribology: challenges in healthcare and personal care device development • Evaluation of the impact of sun exposure on the skin barrier using a biomechanics framework • Mechanical properties of the top-layers of human skin SPONSORSHIP & EXHIBITION OPPORTUNITIES GET INVOLVED Attending this event as either an exhibitor or sponsor will give you the opportunity to display your solutions, services and products to the right people at the right time.