Wheels in Winter Preventing Corrosion
Total Page:16
File Type:pdf, Size:1020Kb
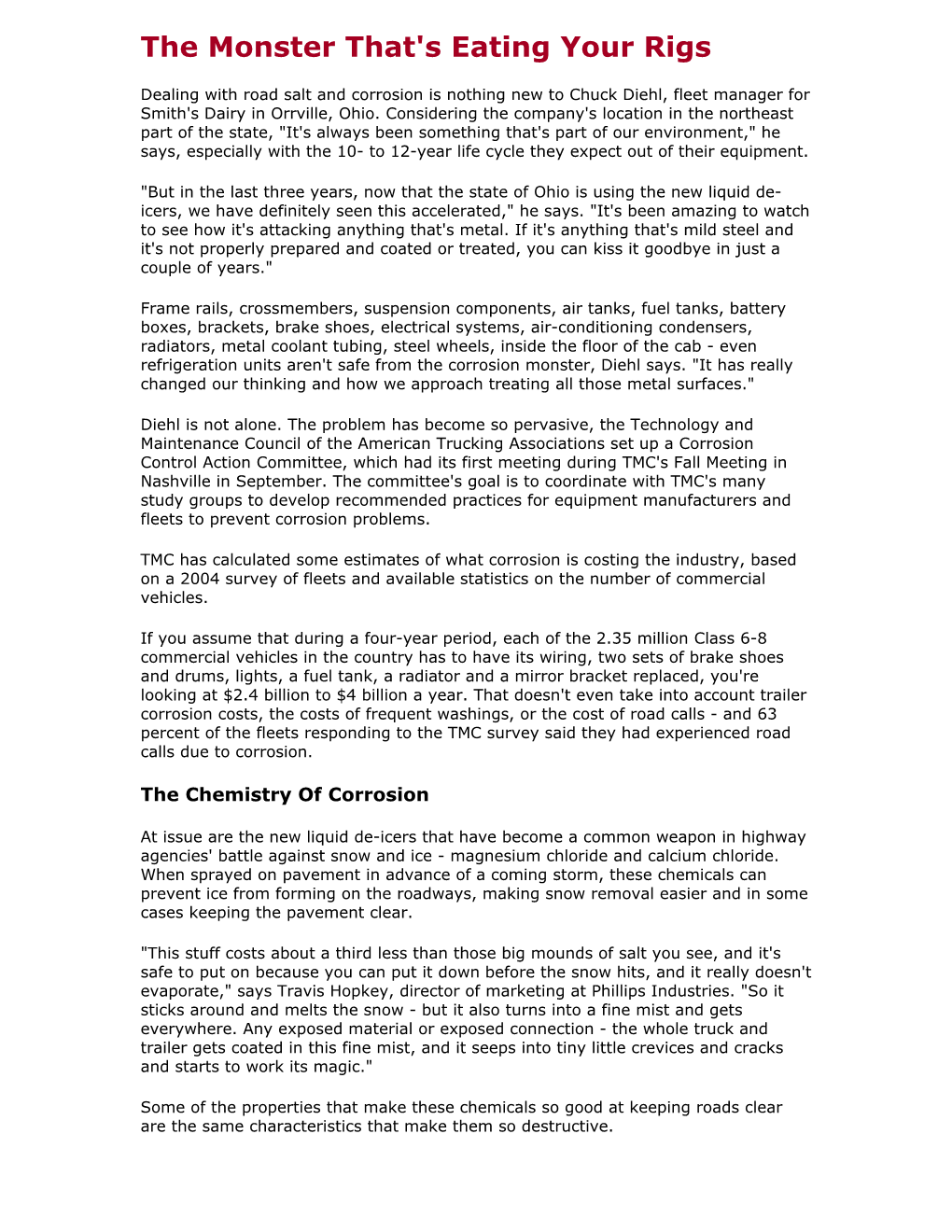
Load more
Recommended publications
-
Piccolo® General Chemistry 13
Piccolo® General Chemistry 13 For In Vitro Diagnostic Use and For Professional Use Only Customer and Technical Service: 1-800-822-2947 Applicable to US customers only Customers outside the US: +49 6155 780 210 CLIA Waived: Use lithium heparin whole blood, only Moderate Complexity: Use lithium heparin whole blood, lithium heparin plasma, or serum Abaxis, Inc. ABAXIS Europe GmbH 3240 Whipple Rd. Bunsenstr. 9-11 Union City, CA 94587 64347 Griesheim USA Germany 1. Intended Use The Piccolo® General Chemistry 13 used with the Piccolo blood chemistry analyzer or the Piccolo Xpress® chemistry analyzer, is intended to be used for the in vitro quantitative determination of alanine aminotransferase (ALT), albumin, alkaline phosphatase (ALP), amylase, aspartate aminotransferase (AST), calcium, creatinine, gamma glutamyltransferase (GGT), glucose, total bilirubin, total protein, blood urea nitrogen (BUN), and uric acid in heparinized whole blood, heparinized plasma, or serum in a clinical laboratory setting or point-of-care location. For US Customers Only The tests on this panel are waived under CLIA ’88 regulations. If a laboratory modifies the test system instructions, then the tests are considered high complexity and subject to all CLIA requirements. For CLIA waived labs, only lithium heparin whole blood may be tested. For use in moderate complexity labs, lithium heparinized whole blood, lithium heparinized plasma, or serum may be used. A CLIA Certificate of Waiver is needed to perform CLIA waived testing. A Certificate of Waiver can be obtained from the Centers for Medicare & Medicaid Services (CMS). Please contact the Commission on Laboratory Accreditation (COLA) at 1- 800-981-9883 for assistance in obtaining one. -
Re‐Evaluation of Sodium Ferrocyanide (E
SCIENTIFIC OPINION ADOPTED: 29 June 2018 doi: 10.2903/j.efsa.2018.5374 Re-evaluation of sodium ferrocyanide (E 535), potassium ferrocyanide (E 536) and calcium ferrocyanide (E 538) as food additives EFSA Panel on Food Additives and Nutrient Sources added to Food (ANS), Maged Younes, Peter Aggett, Fernando Aguilar, Riccardo Crebelli, Birgit Dusemund, Metka Filipic, Maria Jose Frutos, Pierre Galtier, David Gott, Ursula Gundert-Remy, Gunter Georg Kuhnle, Claude Lambre, Jean-Charles Leblanc, Inger Therese Lillegaard, Peter Moldeus, Alicja Mortensen, Agneta Oskarsson, Ivan Stankovic, Ine Waalkens-Berendsen, Matthew Wright, Alessandro Di Domenico, Henk Van Loveren, Alessandra Giarola, Zsuzsanna Horvath, Federica Lodi and Rudolf Antonius Woutersen Abstract The Panel on Food Additives and Nutrient Sources added to Food (ANS) provided a scientific opinion re-evaluating the safety of sodium ferrocyanide (E 535), potassium ferrocyanide (E 536), and evaluating the safety of calcium ferrocyanide (E 538) as food additives. The Panel considered that adequate exposure and toxicity data were available. Ferrocyanides (E 535–538) are solely authorised in two food categories as salt substitutes. To assess the dietary exposure to ferrocyanides (E 535–538) from their use as food additives, the exposure was calculated based on regulatory maximum level exposure assessment scenario (maximum permitted level (MPL)) and the refined exposure assessment scenario. Dietary exposure to ferrocyanides was calculated based on mean and high levels consumption of salts in both the regulatory maximum level and the refined scenario. In the MPL scenario, the exposure to ferrocyanides (E 535–538) from their use as a food additive was up to 0.009 mg/kg body weight (bw) per day in children and adolescents. -
National Food Safety Standard on Sodium Ferrocyanide China
THIS REPORT CONTAINS ASSESSMENTS OF COMMODITY AND TRADE ISSUES MADE BY USDA STAFF AND NOT NECESSARILY STATEMENTS OF OFFICIAL U.S. GOVERNMENT POLICY Voluntary - Public Date: 2/2/2012 GAIN Report Number: China - Peoples Republic of Post: Beijing National Food Safety Standard on Sodium Ferrocyanide Report Categories: FAIRS Subject Report Approved By: Scott Sindelar Prepared By: M. Melinda Meador and Ma Jie Report Highlights: On November 17, 2011, China notified the WTO of National Food Safety Standard: Food Additive Sodium Ferrocyanide as SPS/N/CHN/485. This standard applies to food additive sodium ferrocyanide made from sodium cyanide and ferrous sulfate or ferrum reductum, sodium hydroxide and hydrogen cyanide. It specifies the scope, technical requirements and testing methods for food additive sodium ferrocyanide. The date for submission of final comments to China is January 16, 2012. The proposed date of entry is to be determined. Comments can be sent to China’s SPS Enquiry Point at [email protected]. This report is an INFORMAL translation of this document. General Information: BEGIN TRANSLATION GB National Food Safety Standard GB XXXX XXXX National Food Safety Standard Food Additive Sodium Ferrocyanide (Draft for Soliciting Opinions) Date of Issue: XXXX-XX-XX Date of Effectiveness: XXXX-XX-XX Issued by the Ministry of Health of the People’s Republic of China National Food Safety Standard Food Additive Sodium Ferrocyanide 1. Scope This standard applies to food additive sodium ferrocyanide made from sodium cyanide and ferrous sulfate or ferrum reductum, sodium hydroxide and hydrogen cyanide. 2. Molecular formula, constitutional formula and relative molecular mass 2.1 Molecular formula Na4Fe CN 6·10H2O 2.2 Relative molecular mass 484. -
Research on Best Practices for Winter Weather Operations
Research on Best Practices for Winter Weather Operations Technical Report 0-6669-1 Cooperative Research Program PRAIRIE VIEW A&M UNIVERSITY PRAIRIE VIEW, TEXAS TEXAS A&M TRANSPORTATION INSTITUTE COLLEGE STATION, TEXAS in cooperation with the Federal Highway Administration and the Texas Department of Transportation http://tti.tamu.edu/documents/0-6669-1.pdf Technical Report Documentation Page 1. Report No. 2. Government Accession No. 3. Recipient's Catalog No. FHWA/TX-12/0-6669-1 4. Title and Subtitle 5. Report Date RESEARCH ON BEST PRACTICES FOR WINTER WEATHER December 2011 OPERATIONS Published: October 2012 6. Performing Organization Code 7. Author(s) 8. Performing Organization Report No. Judy A. Perkins, Judith Mwakalonge, Debbie Jasek, Jodi Carson, Report 0-6669-1 Kwaku Obeng-Boampong, and Geza Pesti 9. Performing Organization Name and Address 10. Work Unit No. (TRAIS) Prairie View A&M University & Texas A&M Transportation Institute 11. Contract or Grant No. Prairie View, Texas 77446 Project 0-6669 12. Sponsoring Agency Name and Address 13. Type of Report and Period Covered Texas Department of Transportation Technical Report: Research and Technology Implementation Office November 2010–October 2011 P.O. Box 5080 14. Sponsoring Agency Code Austin, Texas 78763-5080 15. Supplementary Notes Project performed in cooperation with the Texas Department of Transportation Project Title: Best Practices for Emergency Operations URL: http://tti.tamu.edu/documents/0-6669-1.pdf 16. Abstract There is a growing need to identify actionable practices relative to winter weather operations. Because of the potential and inherent hazards during cold weather, it has become increasingly important to ensure that these practices can be effectively employed as well as protect the health and safety of employees working in extreme conditions. -
HOW TO: Salt and Preservatives in Organic Food
What should I know about using salt and preservatives in organic food? Salt plays an important role in processed food products both for its flavoring properties and as a preservative. For those reasons both salt and sea salt are allowed in organic products as long as the salt or sea salt does not have any prohibited additives. Here we discuss the use of salt, prohibited additives, and answer common questions. Are additives allowed in the salt I use in my organic products? Though salt and sea salt are allowed in all categories of organic products, anti-caking/free-flow agents and whiteners are generally not allowed in these products. Common anti-caking/free- flow agents that are not allowed include: • Calcium silicate • Ferric ammonium citrate • Sodium ferrocyanide • Magnesium silicate • Magnesium carbonate • Propylene glycol • Aluminum calcium silicate • Sodium aluminosilicate Makers of organic products must be able to show that the salt does not contain any of the above flow agents, anti-caking agents, or any whiteners. The producer may need to contact the manufacturer of the salt to get a statement of what is in the salt, or may be required to locate a salt that is free of whiteners and anti-caking and flow agents. There is one exception to this rule, salt formulated with magnesium carbonate is allowed in products labeled as “made with organic ingredients.” However, using salt formulated with magnesium carbonate is prohibited in products labeled “organic” (products containing at least 95% organic ingredients) or “100% organic”. It is possible that salt could be formulated with an anti-caking or flow agent not on the list above. -
Turning Water Into Ink Student Worksheet
Turning Water into Ink Student Worksheet Name______________________________________________________________________ Overview You will look like a true magician as you pour two clear solutions together and make something that looks like real ink! What to Learn By the end of this experiment you will understand how to make a saturated solution, and how to identify a chemical reaction. Materials sodium ferrocyanide (MSDS) ferric ammonium sulfate (MSDS) 2 test tubes distilled water goggles and gloves water Lab Time CAUTION: Do not mix sodium ferrocyanide with any other chemical other than specified here, as it can produce hydrogen cyanide gas, which is lethal. Handle this chemical with care, wear gloves, and keep it locked away when not in use. 1. Measure out a tiny bit of sodium ferrocyanide into a test tube filled partway with water. You want to add enough of the crystals so that when you shake the solution (with the cap on), all of the crystals dissolve into the water and make a saturated solution. 2. Into a second test tube, dissolve another tiny bit of ferric ammonium sulfate in water, adding just enough to make a saturated solution. * 3. When you’re ready, pour one test tube into the other and note the change! 4. When finished, rinse with plenty of water and make sure to clean up lab area thoroughly. *NOTE: You can use this as real ink by using it BEFORE you combine them together like this: dip a toothpick into the first solution (sodium ferrocyanide solution) and with the tip write onto a sheet of paper. While the writing is drying, dip a piece of paper towel in the other solution (ferric ammonium sulfate solution) and gently blot along where you wrote on the paper… and the color appears as blue ink. -
EPA Source Water Protection Practices Bulletins
United States Office of Water EPA 816-F-02-019 Environmental Protection (4606) August 2002 Agency Source Water Protection Practices Bulletin Managing Highway Deicing to Prevent Contamination of Drinking Water We depend on clear roads and highways for safe travel and the continual flow of goods and services. Deicing chemicals are used to clear roads covered by snow and ice during winter weather. The runoff associated with highway deicing may contain various chemicals and sediment which have the potential to enter surface and ground water sources. This bulletin focuses on the management of highway deicing chemicals. See the bulletin on storm water runoff for additional management measures. USE OF HIGHWAY DEICING CHEMICALS Each winter, state, county, and local transportation departments stock their arsenal with the tools necessary to face whatever winter storms may bring. This arsenal includes a variety of chemicals to melt snow and ice. This preparedness has a high price tag; in the U.S., an estimated $2 billion is spent each year on chemicals, materials, labor, and equipment for winter road maintenance. The most commonly used and economical deicer is sodium chloride, better known as salt;15 million tons of deicing salt are used in the U.S. each year. Salt is effective because it lowers the freezing point of water, preventing ice and snow from bonding to the pavement and allowing easy removal by plows. However, the use of salt is not without problems. Salt contributes to the corrosion of vehicles and infrastructure, and can damage water bodies, ground water, and roadside vegetation. These issues have led to the investigation and use of other chemicals as substitutes for and supplements to salt. -
Comparison of Actual and Simulated Ferrocyanide Waste Properties
PNL- 10175 UC-72 1 Ferrocyanide Safety Project: Comparison of Actual and Simulated Ferrocyanide Waste Properties R. D. Scheele L. L. Burger R. L. Sell P. R. Bredt R. J. Barrington September 1994 Prepared for the U.S. Department of Energy under Contract DE-AC06-76RLO 1830 Pacific Northwest Laboratory Richland, Washington 99352 DISCLAIMER This report was prepared as an account of work sponsored by an agency of the United States Government. Neither the United States Government nor any agency thereof, nor any of their employees, make any warranty, express or implied, or assumes any legal liability or responsibility for the accuracy, completeness, or usefulness of any information, apparatus, product, or process disclosed, or represents that its use would not infringe privately owned rights. Reference herein to any specific commercial product, process, or service by trade name, trademark, manufacturer, or otherwise does not necessarily constitute or imply its endorsement, recommendation, or favoring by the United States Government or any agency thereof. The views and opinions of authors expressed herein do not necessarily state or reflect those of the United States Government or any agency thereof. DISCLAIMER Portions of this document may be illegible in electronic image products. Images are produced from the best available original document. Summary In the 1950s, additional high-level radioactive waste storage capacity was needed to accommodate the wastes that would result from the production of recovery of additional nuclear defense materials. To provide this additional waste storage capacity, the Hanford Site operating contractor developed a process to decontaminate aqueous wastes by precipitating radiocesium as an alkali nickel ferrocyanide; this process allowed disposal of the aqueous waste. -
Screening Assessment Cyanides
Draft Screening Assessment Cyanides Environment and Climate Change Canada Health Canada February 2018 Synopsis Pursuant to sections 68 and 74 of the Canadian Environmental Protection Act, 1999 (CEPA), the Minister of the Environment and the Minister of Health have conducted a screening assessment of cyanides. Ten of these substances were identified as priorities for assessment as they met categorization criteria under subsection 73(1) of CEPA or were considered a priority based on other human health concerns. The Chemical Abstracts Service Registry Numbers (CAS RN1), their Domestic Substances List (DSL) names and their common names are listed in the table below. Cyanides identified as priorities for assessment under subsection 73(1) of CEPA CAS RN DSL name Common name 74-90-8 Hydrocyanic acid Hydrogen Cyanide 143-33-9 Sodium cyanide Sodium cyanide Potassium 506-61-6 Argentate(1-), bis(cyano-c)-, potassium dicyanoargentate Tetrasodium Ferrate(4-), hexakis(cyano-c)-, 13601-19-9 ferrocyanide (yellow tetrasodium, (oc-6-11) prussiate of soda) Ferrate(3-), hexakis(cyano-c)-, Tripotassium 13746-66-2 tripotassium, (oc-6-11)- ferricyanide Ferrate(4-), hexakis(cyano-c)-, Tetrapotassium 13943-58-3 tetrapotassium, (oc-6-11)- ferrocyanide Potassium 13967-50-5 Aurate(1-), bis(cyano-c)-, potassium dicyanoaurate Ferric ferrocyanide Ferrate(4-), hexakis(cyano-c)-, iron(3+) 14038-43-8 (Prussian blue, (3:4), (oc-6-11)- insoluble) Ferrate(4-), hexakis(cyano-c)-, Ferric ammonium 25869-00-5 ammonium iron(3+) (1:1:1),(oc-6-11)- ferrocyanide Potassium ferric Ferrate(4-), hexakis(cyano-c)-, iron(3+) ferrocyanide 25869-98-1 potassium (1:1:1), (oc-6-11)- (Prussian blue, soluble or Turnbull’s blue) The ecological screening assessment uses a moiety-based approach that focuses on free cyanide (HCN and CN-),and precursors of free cyanide as the forms of primary ecotoxicological significance, which includes the 10 substances listed above that were 1. -
Review of Effects and Costs of Road De-Icing with Recommendations for Winter Road Management in the Adirondack Park
Review of Effects and Costs of Road De-icing with Recommendations for Winter Road Management in the Adirondack Park Prepared by Daniel L. Kelting Executive Director and Corey L. Laxson Research Associate Adirondack Watershed Institute Paul Smith's College Routes 86 & 30 P.O. Box 265 Paul Smiths, NY 12970 Adirondack Watershed Institute Report # AWI2010-01 February 2010 Underwritten and distributed by AdkAction.org, a citizen-led political action committee dedicated to preserving and improving the Adirondacks www.AdkAction.org / [email protected] / PO Box 655, Saranac Lake NY 12983 • this page was intentionally left blank • Acknowledgements We gratefully acknowledge the membership of ADKACTION.org for their financial support of this project and for providing us with the opportunity to conduct this important review and synthesis. • this page was intentionally left blank • Table of Contents 1. Executive Summary 1 1.1 Environmental and Infrastructural Effects of Road 1 Salt 1.2 Recommended Actions and Best Management 4 Practices 2. Introduction 6 3. Characteristics of Deicers 10 4. Deicer Use in North America 14 5. Cost of Deicers 18 6. Road Salt Effects on the Environment 25 6.1 Soils 25 6.2 Groundwater 29 6.3 Surface Water 31 6.3.1 Running Water 33 6.3.2 Standing Water 34 6.4 Vegetation 35 6.4.1 Spread of Halophytic and Non-native Plant 37 Species 6.5 Aquatic Biota 37 6.5.1 Laboratory Studies 38 6.5.2 Field Studies 40 6.6 Wildlife 41 6.6.1 Amphibians 41 6.6.2 Mammals 42 6.6.3 Birds 42 6.7 Use and Fate of Ferrocyanides 43 7. -
Water Pollution and Associated Effects from Street Salting
WATER POLLUTION AND ASSOCIATED EFFECTS FROM STREET SALTING Richard Field, Hugh E. Masters, and Anthony N. Tafuri, Edison Water Quality Research Laboratory, U.S. Env~ronmental Protection Agency, Edison, New Jersey; and Edmund J. Struzeski, Jr., National Field Investigations Center, U.S. Environmental Protection Agency, Denver, Colorado ABRIDGMENT •MOST of the sodium chloride and calcium chloride (hereafter called "salt" or "road salt") used for deicing purposes eventually has a detrimental effect on our environ ment. The high levels of salt in our drinking water and the effect of the salt on the flora adjacent to highways and roadways have produced doubts about the heavy use of salt to provide "bare pavement". The "bare pavement" policy of highway maintenance is popular because it is an easy guide for highway crews and because most people believe that it reduces wintertime accidents. The problem with this policy, however, is that is specifies the minimum of salt needed but not the maximum and that it spoils motorists by leading them to expect "June travel in January". When skidding is the possible cause of an accident, the highway department is at once blamed, regardless of other important possible causes. Because of this, foremen tend to salt heavily and early, even though statistics do not clearly show a positive cor relation between road salting and accidents. Several researchers have suggested that heavy salting may even increase or worsen accidents by giving drivers a false sense of security. Also, a bare pavement, especially_ on bridges and ledge cuts, in cold weather can develop a thin sheet of ice that is invisible to the motorist. -
PRODUCTION of SODIUM CYANIDE a Thesis Presented to the Faculty of the Division of Graduate Studies Georgia Institute of Technolo
PRODUCTION OF SODIUM CYANIDE A Thesis Presented to the Faculty of the Division of Graduate Studies Georgia Institute of Technology In Partial Fulfillment of the Requirements for the Degree Master of Science in Chemical Engineering by Lewis Cleveland Latimer June 1951 .401 n ts k a/ ii r r PRODUCTION OF SODIUM CYAHIDE Approved: . ~£>. 7T T=£ Date Approved by Chairma* fkfi~* Zy / / $ / ACKNOWLEDGMENTS Om the completion of this work I wish to express my sincerest thanks to Dr. H. C. Lewis for his most valuable aid and guidance. I should also like to express my gratitude to Margaret Latimer, my wife, for her most valuable assistance in the preparation of the manuscript. iv TABLE OF CONTENTS CHAPTER PAGE I. INTRODUCTION 1 II. DESCRIPTION OF APPARATUS 8 III. REACTING MATERIALS 9 IV. EXPERIMENTAL PROCEDURE 10 V. ANALYSES 11 VI. DISCUSSION OF RESULTS 12 VII. RECOMMENDATIONS 13 BIBLIOGRAPHY" 14 APPENDIX 16 V LIST OF TABLES Bag* Table I Data Sheet - Run No. 12 17 Table II Data Sheet - Run No. 13 19 Table III Data Sheet - Run No. 14 21 vi LIST OF FIGURES Page Figure I Flow Diagram 6 Figure II Diagram of Reactor 7 vii ABSTRACT A preliminary study of the adaptability of the Bucher proceas (Na2003 4- 4 C 4. N„ _ 2 Na CN 4. 3 CO) to the fluidizsd bed technique was made* Fourteen runs were attempted, of which eleven resulted in failure due to operational difficulties. The major difficulties experienced were in introducing the charge into the reactor, maintaining smooth fluidiza- tion, obtaining a significant reaction time, and maintaining isothermal conditions.