Design of Concrete Made with Recycled Brick Waste and Its Environmental Performance
Total Page:16
File Type:pdf, Size:1020Kb
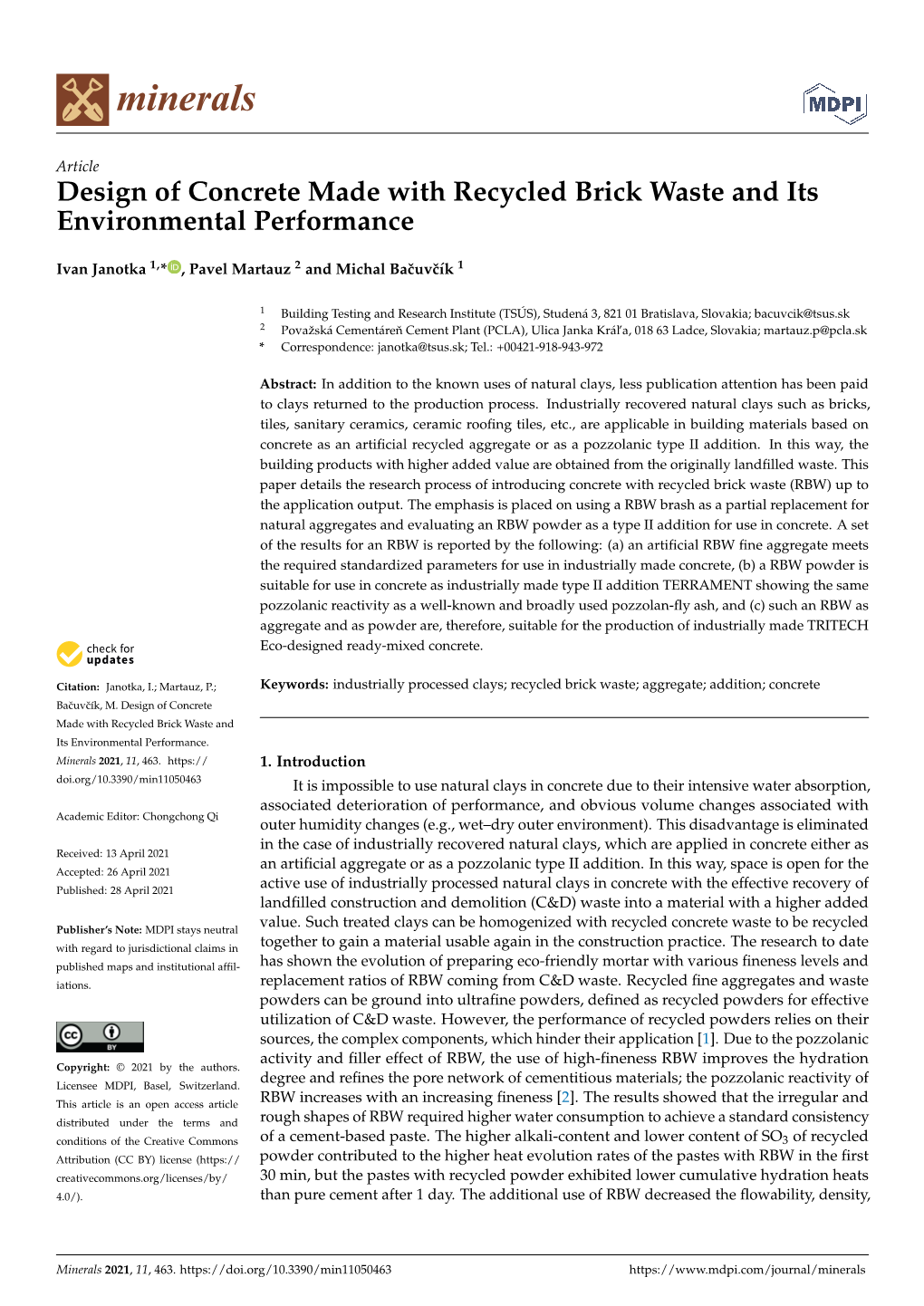
Load more
Recommended publications
-
CEMENT for BUILDING with AMBITION Aalborg Portland A/S Portland Aalborg Cover Photo: the Great Belt Bridge, Denmark
CEMENT FOR BUILDING WITH AMBITION Aalborg Portland A/S Cover photo: The Great Belt Bridge, Denmark. AALBORG Aalborg Portland Holding is owned by the Cementir Group, an inter- national supplier of cement and concrete. The Cementir Group’s PORTLAND head office is placed in Rome and the Group is listed on the Italian ONE OF THE LARGEST Stock Exchange in Milan. CEMENT PRODUCERS IN Cementir's global organization is THE NORDIC REGION divided into geographical regions, and Aalborg Portland A/S is included in the Nordic & Baltic region covering Aalborg Portland A/S has been a central pillar of the Northern Europe. business community in Denmark – and particularly North Jutland – for more than 125 years, with www.cementirholding.it major importance for employment, exports and development of industrial knowhow. Aalborg Portland is one of the largest producers of grey cement in the Nordic region and the world’s leading manufacturer of white cement. The company is at the forefront of energy-efficient production of high-quality cement at the plant in Aalborg. In addition to the factory in Aalborg, Aalborg Portland includes five sales subsidiaries in Iceland, Poland, France, Belgium and Russia. Aalborg Portland is part of Aalborg Portland Holding, which is the parent company of a number of cement and concrete companies in i.a. the Nordic countries, Belgium, USA, Turkey, Egypt, Malaysia and China. Additionally, the Group has acti vities within extraction and sales of aggregates (granite and gravel) and recycling of waste products. Read more on www.aalborgportlandholding.com, www.aalborgportland.dk and www.aalborgwhite.com. Data in this brochure is based on figures from 2017, unless otherwise stated. -
Design Efficiency, Characteristics, and Utilization of Reinforced Foamed
crystals Review Design Efficiency, Characteristics, and Utilization of Reinforced Foamed Concrete: A Review Mugahed Amran 1,2,*, Yeong Huei Lee 3,*, Nikolai Vatin 4 , Roman Fediuk 5, Shek Poi-Ngian 6, Yee Yong Lee 7 and Gunasekaran Murali 8 1 Department of Civil Engineering, College of Engineering, Prince Sattam Bin Abdulaziz University, Alkharj 11942, Saudi Arabia 2 Department of Civil Engineering, Faculty of Engineering and IT, Amran University, Quhal 9677, Amran, Yemen 3 Department of Civil and Construction Engineering, Faculty of Engineering and Science, Curtin University, CDT250, Miri 98009, Sarawak, Malaysia 4 Higher School of Industrial, Civil and Road Construction, Peter the Great St. Petersburg Polytechnic University, St. Petersburg 195251, Russia; [email protected] 5 School of Engineering, Far Eastern Federal University, Vladivostok 690950, Russia; [email protected] 6 Construction Research Centre (CRC), Universiti Teknologi Malaysia, Johor Bahru 81310, Malaysia; [email protected] 7 Department of Civil Engineering, Faculty of Engineering, Universiti Malaysia Sarawak, Kota Samarahan 94300, Sarawak, Malaysia; [email protected] 8 School of Civil Engineering, SASTRA Deemed to be University, Thanjavur 613404, Tamil Nadu, India; [email protected] * Correspondence: [email protected] or [email protected] (M.A.); [email protected] (Y.H.L.) Received: 27 August 2020; Accepted: 30 September 2020; Published: 17 October 2020 Abstract: Foam concrete (FC) serves as an efficient construction material that combines well thermal insulation and structural properties. The studies of material characteristics, including the mechanical, physical, rheological, and functional properties of lightweight concrete, have been conducted rigorously. However, a lack of knowledge on the design efficiency of reinforced FC (RFC) was found in current research trends, compared to reinforced lightweight aggregate concrete. -
Recovery of Waste Expanded Polystyrene in Lightweight Concrete Production
73 The Mining-Geology-Petroleum Engineering Bulletin Recovery of waste expanded polystyrene UDC: 624.01 in lightweight concrete production DOI: 10.17794/rgn.2019.3.8 Original scientifi c paper Gordan Bedeković1; Ivana Grčić2; Aleksandra Anić Vučinić2; Vitomir Premur2 1University of Zagreb, Faculty of Mining, Geology and Petroleum Engineering, Pierottijeva 6, 10000 Zagreb, Croatia 2University of Zagreb, Faculty of Geotechnical Engineering, Hallerova 7, 42000 Varaždin, Croatia Abstract Polystyrene concrete, as a type of lightweight aggregate concrete, has been used in civil construction for years. The use of waste expanded polystyrene (EPS) as a fi ll material in lightweight concrete production is highly recommended from the point of view of the circular economy. Published data shows that an increase in the proportion of lightweight aggre- gates, i.e. EPS, results in a decrease in strength, bulk density and thermal conductivity of the concrete. Utilizing large quantities of waste EPS in non-structural polystyrene concrete production is particularly important. Unlike structural polystyrene concrete, according to the published papers, non-structural polystyrene concrete has not been investigated suffi ciently. The purpose of this paper is to determine the infl uence of the ratios of the basic components in a concrete mixture on the bulk density and compressive strength of non-structural polystyrene concrete produced by utilizing waste EPS as a fi ll material. The test specimens, i.e. cubes with an edge length of 100 mm each, were prepared in labora- tory conditions by varying the proportions of EPS, sand up to 600 g and cement ranging from 300 g to 450 g per speci- men. -
Armorhab: Design Reference Architecture (DRA) for Human
Copyright © 2016 by Dark Sea Industries LLC and the University of New Mexico. Published by The Mars Society with permission ArmorHab: Design Reference Architecture (DRA) for human habitation in deep space Peter Vorobieff Professor and Assistant Chair, Assistant Chair of Facilities, Department of Mechanical Engineering University of New Mexico, Albuquerque, NM, 87131 Phone: (505) 277-8347 email: [email protected] Affiliation: University of New Mexico Craig Davidson Administrator 4808 Downey NE Albuquerque, NM 87109 Phone: 505-720-2321 email: [email protected] Affiliation: Dark Sea Industries LLC Dr. Mahmoud Reda Taha, Peng Professor and Chair, Department of Civil Engineering University of New Mexico, Albuquerque, NM 87131-0001 Office: (505) 277-1258, Cell: (505) 385-8930, Fax (505) 277-1988 http://civil.unm.edu/faculty-staff/faculty-profiles/mahmoud-taha.html www.unm.edu/~mrtaha/index.htm Affiliation: University of New Mexico Christos Christodoulou Associate Dean for Research Distinguished Professor, Electrical & Computer Engineering University of New Mexico Albuquerque, NM 87131 Tel: (505) 277-6580 www.ece.unm.edu/faculty/cgc www.cosmiac.org Affiliation: University of New Mexico Anil K. Prinja Professor and Chair Department of Nuclear Engineering University of New Mexico Albuquerque, NM 87131-1070 -1- Copyright © 2016 by Dark Sea Industries LLC and the University of New Mexico. Published by The Mars Society with permission Phone: (505)-277-4600, Fax: (505)-277-5433 [email protected] Affiliation: University of New Mexico Svetlana V. Poroseva Assistant Professor Department of Mechanical Engineering University of New Mexico, Albuquerque, NM, 87131 Phone: 1(505) 277-1493, Fax: 1(505) 277-1571 email: poroseva at unm.edu Affiliation: University of New Mexico Mehran Tehrani Assistant Professor Department of Mechanical Engineering University of New Mexico, Albuquerque, NM, 87131 Phone: 1(505) 277-1493, Fax: 1(505) 277-1571 email: [email protected] Affiliation: University of New Mexico David T. -
Portugal Is the Major Producer of Cork (Bark of Quercus Suber L.) and the Major Manufacturer of Cork Products
View metadata, citation and similar papers at core.ac.uk brought to you by CORE provided by Repositório da Universidade Nova de Lisboa Cement- cork mortars for thermal bridges correction. Comparison with cement-EPS mortars performance Construction and Building Materials 49 (2013), 315-327 ANA BRÁS1, MÁRCIO LEAL1, PAULINA FARIA2 1 Construction and Environment Section, ESTB – Polytechnic Institute of Setúbal, Portugal 2 Department of Civil Engineering, NOVA University of Lisbon, 2829-516 Caparica Portugal Corresponding author: Ana Margarida Armada Brás. Tel: +351212064660, Fax: +351 212 075 002, e-mail: [email protected] ABSTRACT The aim of this paper is to demonstrate the advantage of cork-mortars for renderings when compared to EPS- mortars, from a thermal characteristics point of view, namely in steady and unsteady conditions. It was intended to develop specific rendering mortars able to be applied in thermal bridges to reduce condensation effects and heat transfer in buildings envelopes. The impact of this solution is significant, especially in building typologies as framed reinforced concrete structures. Cement mortars and cement-EPS mortars are used as a reference as their properties are easily recognized compared to cement-cork mortars, which are made with by-products from the cork industry. Several studies were made concerning fresh and hardened state behaviour of mortars, namely: rheological and mechanical properties, microstructure evolution with time and thermal behaviour. For a cement based mortar, different cork dosages (from 0% to 80%) were tested (as sand replacement by mass). Microstructural analyses show that the mechanical properties of cement-cork blends are not only controlled by cork’s low density, but also by interaction of cork extractives with the cement hydration process. -
Making Concrete Change: Innovation in Low-Carbon Cement and Concrete
Chatham House Report Johanna Lehne and Felix Preston Making Concrete Change Innovation in Low-carbon Cement and Concrete #ConcreteChange Chatham House Report Johanna Lehne and Felix Preston Energy, Environment and Resources Department | June 2018 Making Concrete Change Innovation in Low-carbon Cement and Concrete The Royal Institute of International Affairs Chatham House 10 St James’s Square London SW1Y 4LE T: +44 (0) 20 7957 5700 F: + 44 (0) 20 7957 5710 www.chathamhouse.org Charity Registration No. 208223 Copyright © The Royal Institute of International Affairs, 2018 Chatham House, the Royal Institute of International Affairs, does not express opinions of its own. The opinions expressed in this publication are the responsibility of the author(s). All rights reserved. No part of this publication may be reproduced or transmitted in any form or by any means, electronic or mechanical including photocopying, recording or any information storage or retrieval system, without the prior written permission of the copyright holder. Please direct all enquiries to the publishers. ISBN 978 1 78413 272 9 A catalogue record for this title is available from the British Library. Printed and bound in Great Britain by Latimer Trend. The material selected for the printing of this report is manufactured from 100% genuine de-inked post-consumer waste by an ISO 14001 certified mill and is Process Chlorine Free. Typeset by Soapbox, www.soapbox.co.uk Cover image: Staircase, Benesse Museum House, Naoshima, Japan. Copyright © Education Images/UIG via Getty Images -
Optimum Mix Design for 3D Concrete Printing Using Mining Tailings: a Case Study in Spain
sustainability Article Optimum Mix Design for 3D Concrete Printing Using Mining Tailings: A Case Study in Spain Martina-Inmaculada Álvarez-Fernández 1,*, María-Belén Prendes-Gero 2 , Celestino González-Nicieza 1, Diego-José Guerrero-Miguel 1 and Juan Enrique Martínez-Martínez 2 1 Mining Exploitation Department, EIMEM, University of Oviedo, 33003 Oviedo, Spain; [email protected] (C.G.-N.); [email protected] (D.-J.G.-M.) 2 Construction Department, EPM, University of Oviedo, 33003 Oviedo, Spain; [email protected] (M.-B.P.-G.); [email protected] (J.E.M.-M.) * Correspondence: [email protected] Abstract: A mix design, using a mixture of sand and mine tailings as aggregates, was selected to produce a cement-based 3D printing material suitable for building purposes. Different dosage rates of mine tailings, water, superplasticizers, and accelerators were added to the mixture with the end of looking for the optimum strength, workability and buildability. The term buildability includes aspects such as pumpability and printability. Different tests were carried out in order to compare homogeneous material strength with printed material strength, to evaluate the bonding strength between filaments, and to establish the relationship between fresh behaviour and build- ability for printing applications. Finally, a mixture with 20% of recycled materials demonstrated its ability to be used as concrete printing material in the construction industry in the frame of circular economy concept. Citation: Álvarez-Fernández, M.-I.; Keywords: concrete printing; printing buildability; rheological properties; fresh concrete Prendes-Gero, M.-B.; González-Nicieza, C.; Guerrero-Miguel, D.-J.; Martínez-Martínez, J.E. Optimum 1. -
Influence of Aggregates Grading and Water/Cement Ratio in Workability and Hardened Properties of Mortars
View metadata, citation and similar papers at core.ac.uk brought to you by CORE provided by Universidade do Minho: RepositoriUM Influence of aggregates grading and water/cement ratio in workability and hardened properties of mortars Vladimir G. Haach1 Graça Vasconcelos2 Paulo B. Lourenço3 Abstract. Mortar is the material responsible for distribution of stresses in masonry structures. Knowledge about the fresh and hardened properties of mortar is fundamental to ensure a good performance of masonry walls. Water/cement ratio and aggregates grading are among several variables that influence physical and mechanical behaviour of mortars. An experimental program is presented in order to evaluate the influence of aggregates grading and water/cement ratio in workability and hardened properties of mortars. Eighteen compositions of mortar are prepared using three relations cement:lime:sand, two types of sand and three water/cement ratios. Specimens are analyzed through flow table test, compressive and flexural strength tests. Results indicate that the increase of water/cement ratio reduces the values of hardened properties and increases the workability. Besides, sands grading has no influence in compressive strength. On the other hand, significant differences in deformation capacity of mortars were verified with the variation of the type of sand. Finally, some correlations are presented among hardened properties and the compressive strength. Key words: mortar, water/cement ratio, sand grading, masonry. Introduction Mortar is one of the constituents of the composite anisotropic material denominated “masonry”. Mortar is responsible for creating a uniform stress distribution correcting the irregularities of blocks and accommodating deformations associated to thermal expansions and shrinkage. In case of mortar, it is well known that its influence on compressive strength of masonry is much reduced. -
Civil Engineering Journal
Available online at www.CivileJournal.org Civil Engineering Journal Vol. 3, No. 8, August, 2017 Absorption Characteristics of Lightweight Concrete Containing Densified Polystyrene Bengin M. A. Herki a* a Faculty of Engineering, Soran University, Soran, Erbil, Kurdistan Region-Iraq. Received 29 July 2017; Accepted 28 August 2017 Abstract The environmental impacts of the construction industry can be minimised through using waste and recycled materials to replace natural resources. Results are presented of an experimental study concerning capillary transport of water in concrete incorporating densified expanded polystyrene (EPS) as a novel aggregate. A new environmentally friendly technique of densifying was used to improve the resistance to segregation of EPS beads in concrete. Twelve concrete mixes with three different water/cement ratios of 0.6, 0.8 and 1.0 with varying novel aggregate content ratios of 0, 30, 60 and 100% as partial replacement for natural aggregate by equivalent volume were prepared and tested. Total absorption, absorption by capillary action, and compressive strength was determined for the various concrete mixes at different curing times. The results indicated that there is an increase in total water absorption (WA) and capillary water absorption (CWA) and a decrease in compressive strength with increasing amounts of the novel aggregate in concrete. However, there is no significant difference between the CWA of control and concretes containing lower replacement level. Keywords: Capillary Water Absorption; Compressive Strength; Concrete; Environment; Recycling; Waste Expanded Polystyrene. 1. Introduction The environmental impacts of the construction industry have been a major contributor to the environment pollution all over the world. However, these impacts can be minimized through using waste and recycled materials e.g. -
Study on Recycling of Concrete in Sweden
1 RE:Concrete - Study on Recycling of Concrete in Sweden Madumita Sadagopan, M.Sc. Department of Resource Recovery and Building Technology University of Borås, S-50190 Borås, Sweden [email protected] Katarina Malaga Adjunct Professor, PhD. Department of Resource Recovery and Building Technology, University of Borås, S-50190 Borås, Sweden C.E.O, CBI Swedish Cement and Concrete Research Institute [email protected] Agnes Nagy Ph.D., Senior Lecturer, Department of Resource Recovery and Building Technology, University of Borås, S-50190 Borås, Sweden Email: [email protected] ABSTRACT Sweden’s concrete waste is recycled for use in low-utility purposes such as in the construction of sub-bases in roads but hardly as aggregates in new concrete. To analyse the potential for high-utility recycling, a literature study was conducted on the regulatory instruments, building standards, production and properties of recycled concrete aggregates and the recycled aggregate concrete for Sweden and European countries. Results urge statistics to quantify recycled concrete; regulations like source sorting of waste and selective demolition could potentially optimize recycled aggregate production. Also, the compressive strength of recycled concrete aggregate’s parent concrete influences the properties of the new concrete. Key words: Recycled concrete aggregate, Structural applications, Closed-loop recycling, Sustainability 2 1. BACKGROUND Recycled Concrete Aggregates (RCA) are aggregates produced from the crushing and recycling of only concrete or concrete combined with mineral waste sourced from demolition waste, rejects from prefabrication and concrete spill. RCA is useful in road construction and as aggregates in new concrete. The new concrete produced using RCA or a combination of RCA and other aggregates is called Recycled Aggregate Concrete (RAC) [1]. -
Engineering Properties of Sustainable Lightweight Concrete Using Waste
ISSN: 2277-3754 ISO 9001:2008 Certified International Journal of Engineering and Innovative Technology (IJEIT) Volume 5, Issue 12, June 2016 Engineering Properties of Sustainable Lightweight Concrete Using Waste Polystyrene Bengin A Herki, Zrar Safary, Osama Khalid Faculty of Engineering, Soran University, Soran, Erbil, Kurdistan-Iraq may improve fire resistance [4]. The main aim of the present Abstract— It is well known that the continued extraction of study is to investigate the influence of WP based lightweight natural aggregates and increasing waste materials not only in the aggregate (LWA) on the properties of lightweight aggregate Kurdistan region of Iraq but cross the world is accompanied by concrete (LWAC) and produce a sustainable material for serious environmental problems. Therefore, alternative sources of recycled materials are required as substitute for natural construction industry. The specific objectives of this study are aggregates. Due to these issues this paper investigated the results investigating mechanical properties (e.g. compressive of an experimental study on the effects of waste polystyrene (WP) strength) and durability properties (e.g. water absorption) of in concrete. Polystyrene is used as a packaging material or concrete containing different WP replacement levels at insulating material in construction industry and in other different curing times and identify relationship between industrial fields. A large quantity of polystyrene is disposed in landfills as a waste. Collecting WP before disposed in landfill sites investigated concrete properties. in crushed and graded form can be used as a lightweight aggregate (LWA) to produce lightweight aggregate concrete II. PREVIOUS WORK (LWAC). In this study the WP was shredded to different sizes. -
Factors Affecting Workability
UNIT 3 PROPERTIES OF FRESH CONCRETE Fresh concrete - Workability - Factors affecting workability - Measurement of workability - Segregation Bleeding - Concrete manufacturing - Convention - Ready mix and Advantage of Ready mix - Finishing. Compaction Curing - Strength of concrete - Elasticity - Creep - Shrinkage - elastic behavior of concrete - Durability of concrete Factors affecting strength of concrete and Durability of concrete - Cracks in concrete - Chemical attacks-carbonation. Durability of concrete: effect of Admixtures on properties of concrete causes of concrete deterioration, alkali aggregate reaction, deterioration by chemical actions, concrete in marine environment What is concrete? Concrete is one of the most commonly used building materials. Concrete is a composite material made from several readily available constituents (aggregates, sand, cement, water). Concrete is a versatile material that can easily be mixed to meet a variety of special needs and formed to virtually any shape. Concrete solidifies and hardens after mixing with water and placement due to a chemical process known as hydration. The water reacts with the cement, which bonds the other components together, eventually creating a stone-like material. In order to increase the strength of concrete chemical admixtures are also added. Chemical admixtures like; 1. Super plasticizers – Salts of organic sulphonates Ligno sulphonates, Sulphonated melamine formaldehyde (SMF), Sulphonated naphthalene formaldehyde (SNF) Polycarboxylic ether (PCE) 2. Air-entraining agents - Natural wood resins , Synthetic detergents and Salts of petroleum acids) , 3. Accelerators - Inorganic Calcium chloride, Formates, Nitrates Thiocyanates Silicates Aluminates 4. Retarders - Organic Chemicals- Carbohydrates Hydroxycarboxylic acids and salts Phosphates Few Admixtures can be classified by function as follows: 1. Air-entraining admixtures 2. Water-reducing admixtures 3. Plasticizers 4.