Release Agents and Release Liners
Total Page:16
File Type:pdf, Size:1020Kb
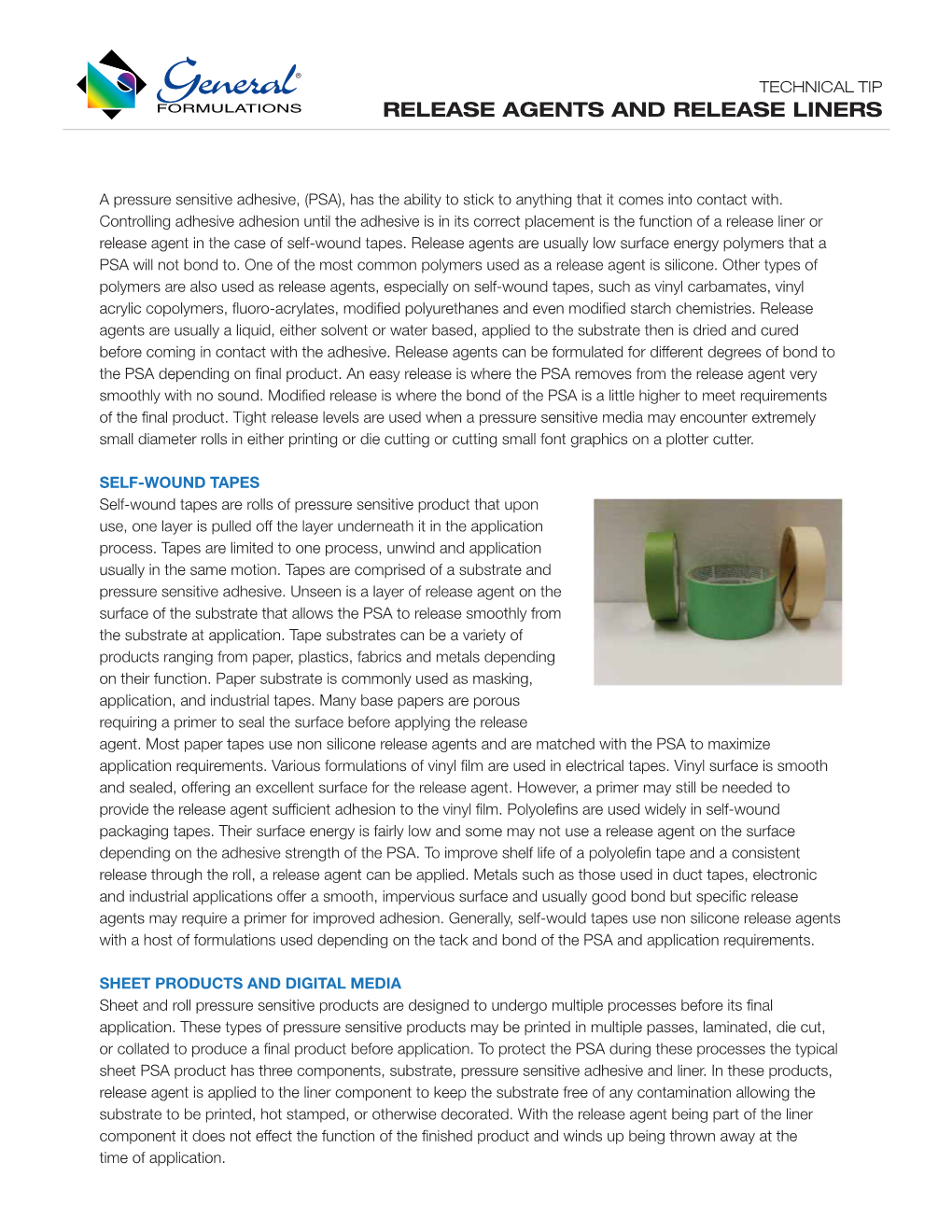
Load more
Recommended publications
-
Label Liners: Meeting the Sustainability Challenge
Label liners: meeting the sustainability challenge By Mariya Nedelcheva, Product Manager Film & With ever-greater emphasis placed on packaging and waste reduction, Jenny Wassenaar, Compliance & Sustainability brand owners are looking for solutions that secure their sustainability Director, Avery Dennison credentials. Consumers pay particularly close attention to packaging, where there are significant environmental gains to be made. For example, waste from labelling can create useful by-products and circular economies. Waste is not always visible on the final packaging, but its impact on brand reputation is no less real. Consumers’ perceptions of a brand can be enhanced when sustainability is improved. label.averydennison.com Matrix Liner Final White paper waste waste label 16% 35% 37% Start-up waste plus Challenge printed End-user The challenge of recycling waste from the labelling process in error scrap - and ideally creating useful by-products - is complex. Many 10% 1% different elements must be addressed in order to move towards the ultimate goal of zero waste. For example, the word ‘recyclable’ can mean many things, and should not be viewed in isolation. Today there is a chance that recyclable products will still end up in landfill, so what matters is establishing genuinely viable end-to-end recycling solutions. That means considering every component within packaging, including where it comes from, how much material has been used, and what happens at every stage of the package’s journey through the value chain. This paper discusses how the sustainability of labelling laminates can be improved, with a particular focus on the label release liners that are left behind once labels have been dispensed. -
The Basic Fundamentals of Labeling
THE BASIC FUNDAMENTALS OF LABELING Whitlam Label’s Resource Guide 01 www.whitlam.com Table of Contents 03 Basic Fundamentals of Labeling Checklist 04 Labeling Construction 05-07 Label Characteristics 08 Label Dimensions & Tooling 09 How will the label be applied? 10 Slitting & Cutting Options 11 Finishing Formats Styles 12 Finishing Format Options 13 Barcodes and Variable Printing 14 Barcodes and Variable Printing 15-21 Label Terminology 02 Basic Fundamentals of Labeling Checklist When getting started on a labeling project, ask yourself these questions to help guide you through the process: Label Performance ❑ What does the label adhere to? (Plastic, metal, glass, corrugated, aluminum) ❑ What are the surface conditions? (Smooth, or textured, flat or curved, clean or oily) ❑ What environment will the label be exposed to? ❑ At what temperature will the label be applied? ❑ Does the label need to be permanent or removable? ❑ Is there any imprinting? If imprinting, what method is being used? ❑ Is “PPAP” required? Label Characteristics ❑ Do you have a sample? If yes, do you want us to match your sample? ❑ Do you have a blueprint? If yes, please provide. ❑ What is the size of the label? Do you want exact size or is there a +/-? ❑ How many colors? (Spot color or CMYK) ❑ Material type?(Paper, Film, Polyester, Polypropylene, etc.) ❑ Is there a “Mandatory Liner “if yes what is it? ❑ Does the label need “Lamination” for protection? (Gloss, matte, etc.) ❑ How is it being applied? (Machine or hand-applied) ❑ Is there consecutive numbering? ❑ Are there any bar codes? If yes, what is the symbology? ❑ Any copy changes? If yes, how many? Finishing Requirements ❑ Is it die cut or butt cut? ❑ What’s the “finishing style”? ❑ How do you want your finished copy position? ❑ What’s the quantity per roll or stack? 03 Label Construction A typical label consists of a topcoat, facestock, adhesive and a liner GRAPHIC LAYERED INK Ink is laid down between the topcoat and the facestock. -
THE BASIC FUNDAMENTALS of LABELING the BASIC FUNDAMENTALS of LABELING — Whitlam Group’S Resource Guide Index
WHITLAM GROUP Whitlam Group’s Resource Guide THE BASIC FUNDAMENTALS OF LABELING THE BASIC FUNDAMENTALS OF LABELING — Whitlam Group’s Resource Guide Index Basic Fundamentals of Labeling 3 Label Construction 4 Label Characteristics 5 Label Dimensions & Tooling 11 How Will the Label be Applied? 12 Slitting & Cutting Options 13 Finishing Formats & Options 14 Barcodes & Variable Printing 16 Label Materials & Descriptions 17 Label Terminology 18 Index 2 THE BASIC FUNDAMENTALS OF LABELING — Whitlam Group’s Resource Guide Basic Fundamentals of Labeling When getting started on a labeling project, 3 ask yourself these questions to help guide you 4 through the process: 5 Label Performance • What does the label adhere to? (Plastic, metal, glass, corrugated, aluminum) 11 • What are the surface conditions? (Smooth or textured, flat or curved, clean or oily) • What environment will the label be exposed to? • At what temperature will the label be applied? 12 • Does the label need to be permanent or removable? • Is there any imprinting? (If imprinting, what method is being used?) 13 • Is “PPAP” required? 14 Label Characteristics • Do you have a sample? (If yes, do you want us to match your sample?) 16 • Do you have a blueprint? (If yes, please provide.) • What is the size of the label? (Do you want exact size or is there a +/-?) 17 • How many colors? (Spot color or CMYK) • Material type? (Paper, Film, Polyester, Polypropylene, etc.) • Is there a “Mandatory Liner?” (If yes what is it?) 18 • Does the label need “Lamination” for protection? (Gloss, matte, -
Evidence Collection
Evidence Collection Evidence Containers/Storage - Bags 52 Evidence Containers/Storage - Boxes 60 Evidence Containers/Storage - Cans, Jars, Containers, & Tubes 62 Evidence Containers/Storage - Envelopes & Kraft Paper 64 Evidence Containers/Storage - Tools & Supplies 66 Swabs, Swab Boxes, & Swab Drying Racks 68 Evidence Tape, Labels, & Seals 71 Crime Scene Documentation 77 Evidence Photography 85 Crime Scene Evidence Protection 90 Bloodstain Identification 92 Evidence Drying Cabinets 95 Trace Evidence Collection 100 Evidence Collection Tools & Supplies 103 Investigation Kits 107 Our evidence collection products are used to aid in the collection of evidence at a crime scene or in the crime lab. Our vast array of products range from evidence tape and bags, to advanced crime scene investigation kits. 51 EVIDENCE CONTAINERS/STORAGE - BAGS Evidence Security Bags Our series of security bags shown on the following pages have unique, self-sealing adhesive strips that form an instantaneous and permanent seal, making it impossible to reopen the bags without destroying them. • Self-sealing • Tamper-evident • Leakproof (they’ll even hold water) • Strong - 4 mil. thick, tear and puncture resistant • White write-on area with chain of custody • Transparent for viewing bag contents • Tear-off receipt for investigating officer FEATURES • Preprinted control numbers on bag and investigating officer's receipt Evidence Collection - Evidence Containers/Storage - Bags Evidence Collection - Containers/Storage Simple Two-Step Sealing Process: STEP 1 Pull away blue release liner. STEP 2 Run your thumb along the red glue line to seal. 52 tritechforensics.com 800.438.7884 910.457.6600 (direct) 910.457.0094 (fax) [email protected] Other evidence security bags can’t hold water (or even a white, - Bags Evidence Collection - Containers/Storage powdery, unknown substance) compared to ours! We’re so sure our evidence security bags are the best on the market that we’ll send you a sample so you can compare it to the bags your department is now using. -
Tamper Indicative Labels, Tapes, and Anti-Counterfeit Products Tamper Evidence That’S Unmistakable
More Choices. More Solutions.™ Tamper Indicative Labels, Tapes, and Anti-Counterfeit Products Tamper Evidence That’s Unmistakable When applied, security tape and labels are of a single, To meet your specific security requirements, BROOKS uniform color with standard or custom imprinting. However, Tamper-Indicative Labels and Tape are available in many should an attempt be made to remove them, an unalterable varieties. Several of the most popular designs are featured here. message appears either on the tape, or on the taped BROOKS is known throughout the world as the premier supplier of surface, making it obvious that a tampering attempt has tamper evident and theft preventive security seals and locking occurred. The tape or label cannot be reapplied without the devices. We’re dedicated to providing you with the finest selection of tampering attempt being very obvious. quality products to meet your exacting security requirements. TAMPER EVIDENT SECURITY LABELS WITH SECURITY MESSAGE Type KNR (Unique Non-Residue) Common application: Wherever both security and aesthetics are required, for example, air cargo security doors. • Reveals prominent security message on label when lifted or removed without leaving a residue on the surface. • For metallic, plastic and smooth surfaces. • Mylar polyester with strong adhesive, labels supplied on a release liner in rolls. • Stock red and blue or custom printing and consecutive numbering. • Custom colors available. • Optional bar coding (any of 3 different symbologies) or dual number tab for tracking purposes. -
Release Liners, We Believe Every Customer May Have Unique Product Requirements
Phone: 978.686.0632 • USA Toll Free: 866.333.4886 • Fax: 978.683.5202 300 Canal Street, Building 7 • Lawrence, MA 01840-0785 USA www.innitytapes.com Oce Hours: 8am - 5pm EST Monday through Thursday | Fridays, 8am - 4pm Email: [email protected] U.S. Mail/Shipping Address: P. 0. Box 385 Lawrence, MA 01842-0785 USA Delivery (Including UPS) Address: 300 Canal Street, Building 7 Our Mission Infinity Tapes is committed to providing a consistently high quality product supported by the best possible customer service experience… Customer + Product + Quality = Infinite Possibilities Customer: We value the trust of you, our Customer. Our goal is to maintain that trust and meet all your tape application needs. Together, the possibilities are infinite! Product: From Double Coated to Transfer Tapes, Tamper Evident Tapes to Release Liners, we believe every customer may have unique product requirements. We are here to assist you in determining the best Product for your application. Quality: Our standard is to manufacture and supply our customers with the highest Quality products and customer service. DETAILED PRODUCT LISTING For downloadable Spec Sheets, visit our website at www.infinitytapes.com/quickspecs DOUBLE COATED TAPES (Adhesive & Carrier Thickness typical values) TRANSFER TAPES (Adhesive & Carrier Thickness typical values) To Our Customers, Distributors and Friends; PAPER LINER TAPES PAPER LINER TAPES DF-55 (3.1 mils) T-671 (1 mil) In 2012, we celebrated an important milestone in our company’s expanding Permanent General Purpose Economical -
Glossary of Terms for Pressure Sensitive Labels
Glossary of Terms for Pressure Sensitive Labels Prepared by Tag and Label Manufacturers Institute, Inc. ©Copyright 1992 Term Description Abhesive A material that resists adhesion. Abhesive coatings are applied to surfaces to prevent sticking, heat sealing, etc. The inherent ability of a surface to inhibit deterioration or destruction by friction. Also called 'rub or scuff resistance,' it Abrasion Resistance relates to the toughness of an ink or coating. Abrasiveness The tendency of a paper, coating or ink to abrade or wear away die edges, slitting blades, printing type, etc., by friction. Absorbency That property of a porous material which causes it to take up liquids or vapors. Absorption The penetration of one substance into the mass of another. To hasten the natural progress of an event or a series of events. This can be accomplished by using heat, fast drying Accelerate solvents or by increasing the volume of air. Procedures for subjecting pressure sensitive label stock to special environmental conditions in order to predict the course of Accelerated Aging natural aging. A material added to a liquid compound to convert the whole mass into a solid, or speed up its cure. Accelerators differ from Accelerator catalysts in that they participate in the reaction and lose their chemical identity as a result. A plastic synthesized from cellulose dissolved in acetic acid which exhibits rigidity, dimensional stability and ink receptivity. Acetate Transparent or matte films, sometimes used for label stocks. Acetate Film A clear film made from cellulose acetate. Acrylate Resins A type of copolymer used in UV inks, adhesives and coating formulations. -
Industrial Division
Industrial Division Specialty & Industrial Tapes www.ProTapes.com ISO 9001:2008 CERTIFIED ProTapes ® Products at a Glance INDUSTRIAL GRADE CLOTH & DUCT TAPES FOIL & ELECTRICAL TAPES Pro® Duct 100 Economy Tape .................................................... 3 Pro® Plus Electrical Tape ........................................................... 14 Pro® Duct 110 General Purpose Tape ........................................ 3 Pro® Friction Abrasion Protection Tape .................................. 14 Pro® Duct 120 Industrial Grade Tape ......................................... 3 Pro® 603 Pipe Wrap Tape ......................................................... 14 Pro® Duct 139 Specialty Grade Tape .......................................... 3 Pro® 882L Copper Foil Tape ..................................................... 14 Pro® 130 Premium Grade Duct Tape ......................................... 4 Pro® 804L Aluminum Foil Tape ................................................ 15 Pro® 132 Heavy-Duty Grade Duct Tape ..................................... 4 Pro® 808L Aluminum Foil Tape ................................................ 15 Pro® 140 Polyester Cotton Cloth ................................................ 4 Pro® 730 Glass Cloth Tape ........................................................ 15 Pro® 160 Transparent Duct Tape ................................................ 4 Pro® 950 Kapton Polyimide Tape ............................................. 15 Pro® Camo Duct Tape ................................................................ -
Release Liners • Liner Substrates • Silicone Release Coatings • Coating Technology • Release Liner Properties
Release liners • Liner substrates • Silicone release coatings • Coating technology • Release liner properties Alexander Knott Senior TS&D Scientist, Dow and Chairman of the Technical Committee and Board Member, FINAT Self adhesive labels – release liner component • A ‘typical’ self-adhesive label is produced from a ‘laminate’ consisting of a face material against which a PSA layer and a release liner are laminated. • The release liner consists of a base paper (or film) on which the release coating is applied in liquid form and then crosslinked & dried to leave a silicone elastomer release coating. The release coating is a very thin layer ~ 1 micron thick (0.001mm). As thin as is possible but still maintaining as complete a covering of the base substrate as possible Release liners • Liner substrates • Silicone release coatings • Coating technology • Release liner properties Release liner - substrate Two aspects of the release liner substrate are critical for optimum performance; A. Surface properties; - Closed & smooth surface (to limit penetration of silicone, and need for silicone). - Minimal impact on silicone cure (poisoning), allows cost advantages - Encourage robust anchorage (especially at high speed) of silicone to surface, to prevent loss/abrasion of silicone impacting release. B. Mechanical properties; - Hard surface (enables better die cutting of labels) - Reproducible thickness/caliper (allows reliable setting of die cut) - Tensile strength & tear strength (withstand the stresses applied at high speed). Both must be balanced vs basic demands on COST. Release Liner - Substrate Typical Substrates; A.Glassine & SCK (Super-Calendared Kraft) - Very smooth surface, High level of surface refinement (closed) - Excellent mechanical and chemical properties. B. CCK (Clay-coated Kraft - Highly closed surface, Excellent lay-flat properties C. -
Paper Based Silicone Release Liners from Labels Can & Should Be
LABEL PAPER RELEASE LINERS PAPER BASED SILICONE RELEASE LINERS FROM LABELS CAN & SHOULD BE RECYCLED November 2020 CONTENTS INTRODUCTION 3 PART A – WHAT IS A PAPER BASED SILICONE RELEASE LINER? 4 WHAT KINDS OF SUBSTRATES ARE USED FOR PAPER BASED SILICONE RELEASE LINERS? . 4 PART B – CAN SILICONE COATED RELEASE PAPERS BE RECYCLED? 4 RECYCLING RELEASE LINER AS A SEPARATE STREAM ......................................................... 5 RECYCLING RELEASE LINER WITH OTHER PAPER GRADES .................................................. 5 EUROPE ............................................................................................................................... 5 USA ...................................................................................................................................... 6 PART C – IMPORTANCE OF RECYCLING OF PAPER SILICONE RELEASE LINER 6 RECYCLING OF RELEASE LINER WITH DEDICATED RECYCLING STREAMS ........................... 6 RECYCLING OF LINER WITH STANDARD PAPER WASTE ...................................................... 6 REFERENCES 7 ABOUT CELAB 7 2 INTRODUCTION CELAB: Toward a Circular Economy for Labels, is publishing this white paper to provide basic technical information on recycling on a ‘global’ basis. CELAB’s Technical Workstream, under the leadership of Alex Knott, Senior Scientist at The Dow Chemical Company, conducted a technical review of release liner recycling to understand existing recycling technology. CELAB collected non-proprietary information on current processes by obtaining input -
Industry Terms Abrasion Resistance - the Ability of a Fiber Or Fabric to Withstand Surface Wear and Rubbing
Industry Terms Abrasion Resistance - The ability of a fiber or fabric to withstand surface wear and rubbing. ACRYLIC A synthetic polymer with excellent aging characteristics that can be used as either a single component adhesive or a coating composition. ADHESION A bond produced between a pressure sensitive adhesive and a surface. ADHESIVE Any material that will usefully hold two or more objects together solely by intimate surface contact. ADHESIVE PROMOTER (adhesive primer) Adhesion promoter is most often used to increase the adhesion levels of low surface energy plastics such as: TPO, PP, PPO, PC, ABS and other plastic blends for bonding with pressure sensitive adhesives. ASTM D 1056-07 - American Society For Testing and Materials. This specification (D 1056) covers flexible cellular rubber products known as sponge rubbers and expanded rubbers. It is designed to provide certain physical property parameters and test methods for cellular rubber. BACK-SLIT RELEASE LINER a release liner which is supplied split into multiple pieces, either by the act of slitting, or by laminating multiple strips of release liner. Often used as an alternative to a release tab. BLOCKING Adhesion between the sheets of the plies of rolls of coated material, usually due to extreme conditions of pressure, temperature, or humidity. BUTT CUT PARTS Rectangular or square parts in continuous form separated by a cut to the liner across the web. BUZZ, SQUEAK, and RATTLE (BSR application) Undesirable noises typically caused by vibration between mating automotive components. Bun - A cellular rubber product that is manufactured in a mold and is usually rectangular in appearance. Also known as a block and/or plank. -
2018 Labels in the Spotlight
UPM PULP • CUSTOMER NEWSLETTER Labels in the spotlight. 2/ 2018 #pulpdirect Understanding The Rolls-Royce Lifesaving New life for label papers of papers labels packaging PULPACTION UNDERSTANDING LABEL PAPERS What has UPM Pulp to offer release liner and label face WHAT MAKES LABEL PAPER PRODUCERS Our pulps have been successfully used SPECIAL? in label papers for years. We understand paper producers? To find out, we had a Q&A session “They are demanding and good customers. the fibre’s impact on problem-free and cost- with Mats Backman, their Director of Technical Customer Label base and face paper producers must efficient label production. It’s important to Service (TCS). be very customer focused as the value of choose the right pulp for the right product their products increases step by step. In my from the beginning.” opinion our multi-fibre offering suits their needs well. Consistent properties such as WHAT DOES THAT MEAN IN PRACTICE? cleanliness, pH and predictability of how “For example, with our UPM Betula birch pulp develops strength and density are of pulp you will reach high air resistance greatest importance to them.” – a key parameter for label paper as it decreases the consumption of silicon HOW WOULD YOU DESCRIBE THE surface coating in converting. The birch LABELLING VALUE CHAIN? pulp has fast tensile strength development. “The value chain is long. Most of our It will consume less energy to refine and label paper customers sell their products can enable extra capacity if refining is a to converters for siliconizing, laminating bottleneck. You can also take advantage of and applying adhesive.