DURASTEEL Ducting-AP 12
Total Page:16
File Type:pdf, Size:1020Kb
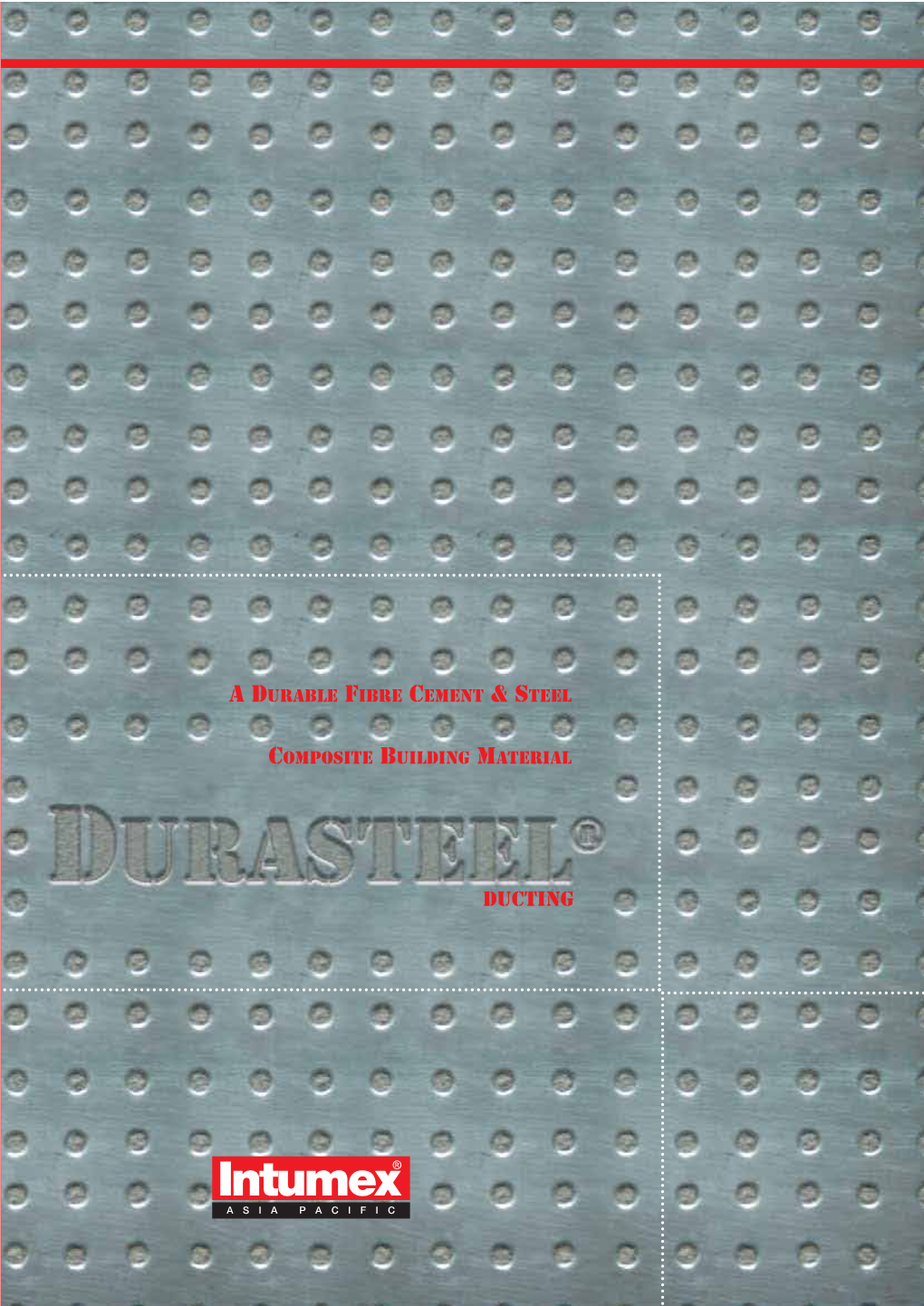
Load more
Recommended publications
-
A Comprehensive Review of Thermal Energy Storage
sustainability Review A Comprehensive Review of Thermal Energy Storage Ioan Sarbu * ID and Calin Sebarchievici Department of Building Services Engineering, Polytechnic University of Timisoara, Piata Victoriei, No. 2A, 300006 Timisoara, Romania; [email protected] * Correspondence: [email protected]; Tel.: +40-256-403-991; Fax: +40-256-403-987 Received: 7 December 2017; Accepted: 10 January 2018; Published: 14 January 2018 Abstract: Thermal energy storage (TES) is a technology that stocks thermal energy by heating or cooling a storage medium so that the stored energy can be used at a later time for heating and cooling applications and power generation. TES systems are used particularly in buildings and in industrial processes. This paper is focused on TES technologies that provide a way of valorizing solar heat and reducing the energy demand of buildings. The principles of several energy storage methods and calculation of storage capacities are described. Sensible heat storage technologies, including water tank, underground, and packed-bed storage methods, are briefly reviewed. Additionally, latent-heat storage systems associated with phase-change materials for use in solar heating/cooling of buildings, solar water heating, heat-pump systems, and concentrating solar power plants as well as thermo-chemical storage are discussed. Finally, cool thermal energy storage is also briefly reviewed and outstanding information on the performance and costs of TES systems are included. Keywords: storage system; phase-change materials; chemical storage; cold storage; performance 1. Introduction Recent projections predict that the primary energy consumption will rise by 48% in 2040 [1]. On the other hand, the depletion of fossil resources in addition to their negative impact on the environment has accelerated the shift toward sustainable energy sources. -
As One of the Leading Suppliers of Fire Protection
A DURABLE FIBRE CEMENT & STEEL COMPOSITE BUILDING MATERIAL s one of the leading suppliers of fire protection We, as a company, do not just manufacture products, products and systems world wide, Intumex Asia rather we provide a comprehensive service to achieve the AaPacific are acutely aware of the importance of best solution to specific fire or blast protection problems. product quality and consistency. These factors are critical for all fire protection products and systems as peoples We can offer advice at the design stage, provide lives may depend on them. construction detailing and where necessary, special project orientated product and system testing which will First produced in 1934, DURASTEEL® became part of our enable the manufacture of custom built solutions, tailored product range in 1980. As one of the world leaders and to your needs. specialists in passive fire protection, Intumex Asia Pacific have been instrumental in protecting life, the Our commitment to quality and to continual product and environment and financial investment, and as such offers system research, development and testing enable you to ® systems that are technically advanced and value- specify DURASTEEL systems with confidence. engineered to meet today s market needs. All Intumex products, therefore, are manufactured under We have used our specialist technical and engineering skills accredited EN ISO 9000 quality assurance procedures, to develop fire and blast protection for some of the worlds and our products and systems are extensively tested to most valuable industries. These include major projects for all relevant national standards for fire and impact nuclear power plants, gas terminals, offshore production resistance, and acoustic and thermal insulation. -
Idronics 6: Solar Thermal Combisystems
Idronics#6 Feat_rev2.indd 1 5/4/10 2:57:56 PM CaleffiCaleffi North North America, America, Inc. Inc. 98503883 South W. Milwaukee 54th Street Rd Franklin,Milwaukee, WI 53132 Wisconsin 53208 T:T: 414.421.1000414.238.2360 F: F: 414.421.2878 414.238.2366 Dear Hydronic Professional, Dear Hydronic Professional, Welcome to the 6th edition of idronics, Caleffi ’s semi-annual design journal Welcomefor hydronic to theprofessionals. 2nd edition of idronics – Caleffi’s semi-annual design journal for hydronic professionals. The global recession has slowed nearly all industries over the past year. TheHowever, 1st edition despite of idronicsdeclines was in construction, released in January solar water 2007 heater and distributed shipments to over 80,000in the US people increased in North 50% America. during 2008.It focused on the topic hydraulic separation. From the feedback received, it’s evident we attained our goal of explaining the benefits andAs more proper and application more HVAC of professionalsthis modern design become technique familiar forwith hydronic solar water systems. heating, many recognize opportunities to extend solar thermal technology A Technical Journal Iffor you combined haven’t domesticyet received hot a water copy andof idronics space heating#1, you applications.can do so by Thissending is a in the attachedtrend our reader parent response Caleffi SpA card, identifi or by ed registering several years online ago at in www.caleffi.us Europe, and is. The from publicationnow a topic willof growing be mailed interest to you here free inof North charge. America. You can For also this download reason, the Caleffi Hydronic Solutions completesolar “combisystems” journal as a PDF was fileselected from our as theWeb topic site. -
Best Practices Manual for Solar Hot Water Systems
Best Practices Manual for Solar Hot Water Systems Updated: 10-25-2011 Introduction: This manual was developed as a tool to assist solar thermal designers and installers as a guideline to provide the most reliable solar hot-water systems possible. The material presented here is not intended to be used as a list of system requirements or as a type of solar code. Rather, it was assembled with the input of many parties to share lessons learned in the field. It is not inclusive and is a work in progress. This manual was developed in Wisconsin where some parts of the state have over 10,000 heating degree days and where winter temperatures regularly fall below -30°F. In fact, the record coldest temperature recorded in Wisconsin was - 55°F. During the summer, temperatures can rise above 100°F. While most climates are not this severe, the practices outlined in this manual will be helpful for system designs in all cold climates as well as in warm climates. A properly designed solar hot-water system must not only function properly during extreme cold and hot environmental circumstances, it must also be able to safely endure sustained periods of low or no hot water draw without damage or overheating. A best practice is defined as: • A practice that is most appropriate under the circumstances. • A technique or methodology that, through experience and research, has reliably led to a desired or optimum result. Overview: A well-designed solar water heating system that is appropriate for the climate where it is located and is properly installed with appropriate solar rated components will last for many years. -
Firemaster® Fire Protection Systems
FireMaster ® fire protection systems THERMAL CERAMICS Fire Protection product range Thermal Ceramics FireMaster ® products are used all over the world to protect people and structures against fire. Products FireMaster XLS Blanket The new ultra lightweight fire protection blanket from For more than 30 years, FireMaster insulation materials have Thermal Ceramics. Saving even more weight than FireMaster Marine Plus Blanket utilizing a new, innovative, provided effective fire insulation for structures exposed to cellulosic, low thermal conductivity fibre manufacturing process. hydrocarbon and jet fires in oil & gas, marine, transportation and FireMaster Marine Plus blanket construction industries. Lightweight fire insulation designed for weight sensitive applications. Weight savings of 20 to 30% are typical compared to standard FireMaster blanket and alternative The wide variety of FireMaster Fire Protection Systems are insulation solutions. Systems are available for composite, comprehensively certified and extensively tested to meet national steel and aluminium structures. and international standards, offering our customers the security of FireMaster Marine Plus faced blanket global proven fire performance in various market sectors. Our product FireMaster Marine Plus blanket is available with surface range includes FireMaster Marine Plus blanket developed especially coatings of aluminium or glass cloth. for weight-sensitive applications in offshore and marine featuring: FireMaster Marine Plus water repellent blanket FireMaster Marine Plus blanket is available with a water repellent treatment through the entire blanket thickness to • Lower weight designs that minimise weight inhibit water ingress. contribution to structures FireMaster RES system • Improved, simpler, installation techniques leading A rigid metallic enclosure for jet fire protection of valves, to easier installation actuators and flanges. • Combined fire, thermal and acoustic insulation FireMaster cable tray wrap and explosion resistance FireMaster blanket totally encapsulated in aluminium foil. -
Fire Rated Ductwork and Service Enclosures
The Passive Fire Protection Handbook The UK’s comprehensive guide to passive ire protection Chapter 6 Fire Rated Ductwork and Service Enclosures AUGUST 2017 The Passive Fire Protection Handbook Contents Chapter 1: Introduction Chapter 2: User guide Chapter 3: Structural Steel Chapter 4: Ceilings, Floors and Roofs Chapter 5: Partitions and External Walls Chapter 6: Fire Rated Ductwork and Service Enclosures 165 Ventilation and Smoke Extraction Ducts ��������������������������������������� 166 Cladding of Existing Sheet Metal Ducts ���������������������������������������������� 171 Self-Supporting Ducts ���������������������������� 172 Promat DURADUCT® LT ������������������������� 175 DURADUCT® SMT Fireblast ������������������ 177 DURADUCT® SR �������������������������������������� 179 Cable Protection �������������������������������������� 180 Cable Protection - External or Internal Fires ���������������������������������������� 184 Service Enclosures ���������������������������������� 185 Horizontal Service Enclosures, Suspended Services ������������������������������� 186 Ventilation and Smoke Extraction Ducts ��������������������������������������� 187 Chapter 7: Penetration Seals Chapter 8: Smoke Barriers and Doors CHAPTER 6: FIRE RATED DUCTWORK AND SERVICE ENCLOSURES Fire Rated Ductwork and Service Enclosures TECHNICAL SERVICES T: 0800 1456033 E: [email protected] 165 The Passive Fire Protection Handbook | 2017 Chapter 6: Fire Rated Ductwork and Service Enclosures Ventilation and Smoke Extraction Ducts FIRE TESTING METHODS -
Att 2 183106ME31800 ROOF HVAC LAYOUT
1 2 3 4 5 6 7 NOTE: • ALL INTERNAL INSULATION FOR ROOF LEVEL AND RISER SHAFT. • EXTERNAL INSULATION AFTER RISER PENETRATION. A VOID TO COMMUNAL OPEN SPACE 500X200 GRABAGE ROOMS EXHAUST DUCT FROM MECHANICAL SWITCHBOARDS BELOW TO DISCHARGE VIA ROOF MOUNTED FAN. BELOW TO BE WEATHERPROOF. B SHELTER TO BE PROVIDED BY PV ARRAYS EXTENT PV ARRAYS EXTENT BUILDER. (INDICATIVE ONLY) (INDICATIVE ONLY) 850x1900 SHAFT SIZE. CONTROL CENTRE FOR GLASS 500x1350 DUCT SIZE LOUVERS FOR LEVEL 1 -17 CORRIDORS. PROVIDE WEATHERPROOF ENCLOSURE. STAIR PRESSURISATION SUPLLY C AIR SYSTEMS, FAN TO HAVE A MSSB-R MSSB-E-1 VSD. NOTES - 1. FOR EACH STAIRWELL, PROVIDE STAIRWELL PRESSURE CONTROLLER D COMPLETE WITH TWO (2) DIFFERENTIAL PRESSURE SENSORS AND CC AVERAGING MODULE. DIFFERENTIAL PRESSURE SENSORS SHALL BE LOCATED AT LEVEL 5 1000x1000 AND LEVEL 14 (ALLOW FOR RELOCATION OF SENSORS TO SUIT). 2. PROVIDE DUCT MOUNTED SMOKE DETECTORS AND CONTROLS FOR GEF-G LIFT SHAFT STAIR PRESSURISATION SYSTEMS TO THE REQUIREMENTS OF 500x1350 OA R3.0 AS1668.1 -2015. NRD ATT-1 3. PROVIDE ACOUSTIC INSULATION TO STAIR PRESSURISATION DUCTWORK INDICATIVE LOCATION S01 D ON THE ROOF. DUCTWORK SHALL BE WEATHERPROOF COMPLETE WITH 800x800 OA R3.0 Section / Elevation A 301 SSL SF-2 STAIR PRESSURISATION SUPLLY CROSS BREAKS. NRD OF FIRE TANKS +82,830 AIR SYSTEMS, FAN TO HAVE A 4. OUTDOOR AIR SUPPLY DUCTS ON THE ROOF SHALL BE ATT-1 1000x1000 PA VSD. WEATHERPROOF TYPE HAVING CROSS BREAKS. 1000x1000 PA E ATT-2 5. ROOF PENETRATIONS SHALL BE PROVIDED WITH 150MM HIGH ROOF ATT-2 1000x1000 CURB BY THE BUILDING TRADE. -
Passive Fire Protection
passive fire protection Date of Issue: November 2018 FIREMAC FM Fire Ducts Fire resistant ventilation, kitchen extract, smoke extract & pressurisation ductwork. firemac.com passive fire protection PA FIREMAC FM® Fire Ducts PB firemac.com COMPANY PROFILE Firemac was established in 1989 and has grown to become a major provider of passive fire protection products, both in the UK and internationally. Passive fire protection (PFP) is a key part of the structural integrity and fire safety in a building. PFP contains or slows the spread of a fire through the use of fire resistant ductwork, walls, floors, and doors. Firemac has been at the forefront in product design for the PFP sector for over 25 years, and has extensive experience advising a broad range of clients from solution selection through to designing and installing ductwork protection systems, fire walls and ceilings, and fire resistant services enclosures. Firemac’s market leading product range for ductwork, Firemac FM Firemac Project: Fire Duct systems, has a proven track record in builds in the UK, Queen Elizabeth Hospital, Glasgow the Middle East, Africa, India and Asia. More recently, Firemac has introduced FM Blue – an impact- resisting, steel-faced non combustible board that can be used to form fire resisting walls, ceilings, ducts, and enclosures. As our customers would expect of a company working in safety critical systems Firemac is ISO 9001 registered and Third Party Accredited. Firemac Project: Anfield Stadium, Liverpool FIREMAC FM® Fire Ducts FIREMAC FM FIRE DUCT SYSTEMS Building Regulations require that new buildings must be divided into fire compartments and provide means of escape in order that the spread of fire in the building is contained. -
Promat Ductwork Solutions Technical Services Telephone 01344 381400
Uniclass EPIC L751:P2:N324 L1:X2:Y421 CI/SfB (57.9) Rf9 (K2) July 2003 DUCTWORK SOLUTIONS l DURADUCT LT® l DURADUCT SMT® l DURADUCT SR® INTRODUCTION TRIED AND TESTED SYSTEMS FOR LIFE SAFETY DURADUCT SMT® and LT® ductwork systems are made from DURASTEEL® sheet; a non-combustible composite of fibre cement, reinforced by mechanically bonded galvanised steel sheeting. DURASTEEL® is highly resistant to moisture and retains its mechanical integrity even 2 when saturated. It will not absorb combustible fluids such as cooking oil in kitchen extract ducts and has exceptional fire resistant qualities. Systems are available which will provide up to four hours protection to suit the demands of modern developments. DURASTEEL® withstands hose stream action and, because of its very low moisture absorption, it can be used externally. It is not susceptible to the damage often caused by moisture or sprinkler activation during the early stages of delivery and installation of a fire-rated ductwork system. DURASTEEL® has a tremendous resistance to impact and has high flexural strength, giving added protection in the early stages of construction and throughout the life of the building. DURADUCT SMT® DURADUCT LT® THE FIT AND FORGET DUCTWORK SYSTEM FOR THE LIFE OF YOUR BUILDING DURADUCT SMT/LT Promat Ductwork Solutions Technical Services Telephone 01344 381400 . Fax 1344 381401 DURADUCT LT® THE NEXT GENERATION OF FIRE RATED DUCTWORK CONSTRUCTION DURADUCT LT® consists of a galvanised steel inner duct overboarded with 6.0mm DURASTEEL® and finishing trim angles. The system is installed using a proprietary flange. The total thickness of standard DURADUCT LT® is nominally 7.5mm. -
The Passive Fire Protection Handbook
V5FPH Cover.qxd 12/11/03 9:00 am Page 1 Uniclass EPIC L5:P2:N32 E:X2:Y421 CI/SfB Rf9 (K2)+(K3) December 2003 NBSPlus The Passive Fire Protection Handbook FIRE RATED DUCTWORK ● Ventilation and Smoke Extraction Ducts ● Cable Protection ● Mechanical and Electrical Service Enclosures 6 VENTILATION & SMOKE EXTRACTION DUCTS The Fire Protection Handbook The relative complexity of any ductwork system which is extract, should also have this criterion for the inner surface of passing through different fire compartments and the relevance the duct within the fire compartment when the duct is exposed of the system’s function in ambient and fire conditions can to external fire (Duct A). make the selection of a suitable ductwork system difficult. For smoke extraction, the guidance in the standard states that This section of the handbook aims to give guidance on the the cross sectional area of a duct required to extract smoke in fire performance requirements of ductwork and offers a wide the event of a fire should not be reduced by more than 25%. range of solutions for proprietary “off the shelf” fire rated ductwork, the protection of steel ductwork and for self- Design Considerations supporting systems using PROMATECT®-L500 and The following points are some of the factors which should VICUCLAD®. be considered when determining the correct specification to ensure a ductwork system will provide the required fire For particularly onerous conditions e.g. where a high performance. Further advice can be obtained from the Promat impact strength is required or for use in aggressive Technical Services Department. -
Performance of HVAC System with Solar Reheat William Hutzel Purdue University
Purdue University Purdue e-Pubs International High Performance Buildings School of Mechanical Engineering Conference 2010 Performance of HVAC System With Solar Reheat William Hutzel Purdue University Scott iW lson Purdue University Jacob Faiola Purdue University Follow this and additional works at: http://docs.lib.purdue.edu/ihpbc Hutzel, William; Wilson, Scott; and Faiola, Jacob, "Performance of HVAC System With Solar Reheat" (2010). International High Performance Buildings Conference. Paper 4. http://docs.lib.purdue.edu/ihpbc/4 This document has been made available through Purdue e-Pubs, a service of the Purdue University Libraries. Please contact [email protected] for additional information. Complete proceedings may be acquired in print and on CD-ROM directly from the Ray W. Herrick Laboratories at https://engineering.purdue.edu/ Herrick/Events/orderlit.html 3126, Page 1 PERFORMANCE OF HVAC SYSTEM WITH SOLAR REHEAT William J. Hutzel*, Scott A. Wilson, and Jacob Faiola Department of Mechanical Engineering Technology, Purdue University, West Lafayette, IN, USA 765-494-7528, [email protected] *Corresponding Author ABSTRACT This project demonstrated a method for using solar energy to control humidity in buildings during summer operation. This was accomplished by adding a secondary coil in the reheat position of a small commercial single zone air handler. A water/glycol mixture transferred heat from flat plate solar panels located on the roof of the building to the air handler. Preliminary tests showed that solar energy could replace much of the electric reheat that was used prior to the solar retrofit. This project is significant because the 2007 version of ASHRAE Standard 90.1 “Energy Standard for Buildings Except Low-Rise Residential Buildings” only allows air handling equipment with reheat in certain situations, such as when 75% of the heating energy is from reclaimed or renewable sources. -
Applications and Technical Manual Introduction
Issue | 02 | July 2018 BW11 Fire Rated Ductwork Applications and Technical Manual Introduction Firespray International Limited is internationally recognised in the design and manufacture of an extensive range of specialist fire and acoustical systems into a diverse range of industrial disciplines encompassing the general construction, transportation, power generation and bespoke manufacturing industries. Accredited to ISO 9002 and ISO 9001:2015, Firespray International is committed to the highest standards in products development, manufacture and customer support. Since its formation in the early nineties, Firespray International Ltd has become recognised as a world authority in the design and manufacture of Fire Ducting Systems under the brand name FLAMEBAR. With a primary manufacturing base in the UK, Firespray International Ltd has now developed a highly specialised international Licensees network encompassing the world. This Manual has been produced for everyone associated with the design and installation of fire rated ductwork systems and illustrates how to satisfy the requirements of the regulatory bodies. It also clearly emphasises our own commitment to fire safety. FLAMEBAR BW11 FIRE RATED DUCT SYSTEMS SATISFY ANY REQUIREMENT FOR FIRE RATED DUCTWORK FOR VENTILATION, KITCHEN OR SMOKE EXTRACT APPLICATIONS. 2 Contents 1. Understanding the New European Test Standards 4 2. Fire Rated Ductwork - Analysis and Performance 6 2.1 FLAMEBAR BW11 - Single Source Responsibility - Certificate of Conformity 6 2.2 FLAMEBAR BW11 - Flexibility in Design 6 2.3 FLAMEBAR BW11 - Construction of Fire Duct 7 2.4 FLAMEBAR BW11 - System Integrity - Ancillary Components 7 2.5 FLAMEBAR BW11 - Air Temperatures at Various Distances from Duct 8 2.6 FLAMEBAR BW11 - Supports and Hangers 9 3.