Heskin Website Feb 2011 1.3
Total Page:16
File Type:pdf, Size:1020Kb
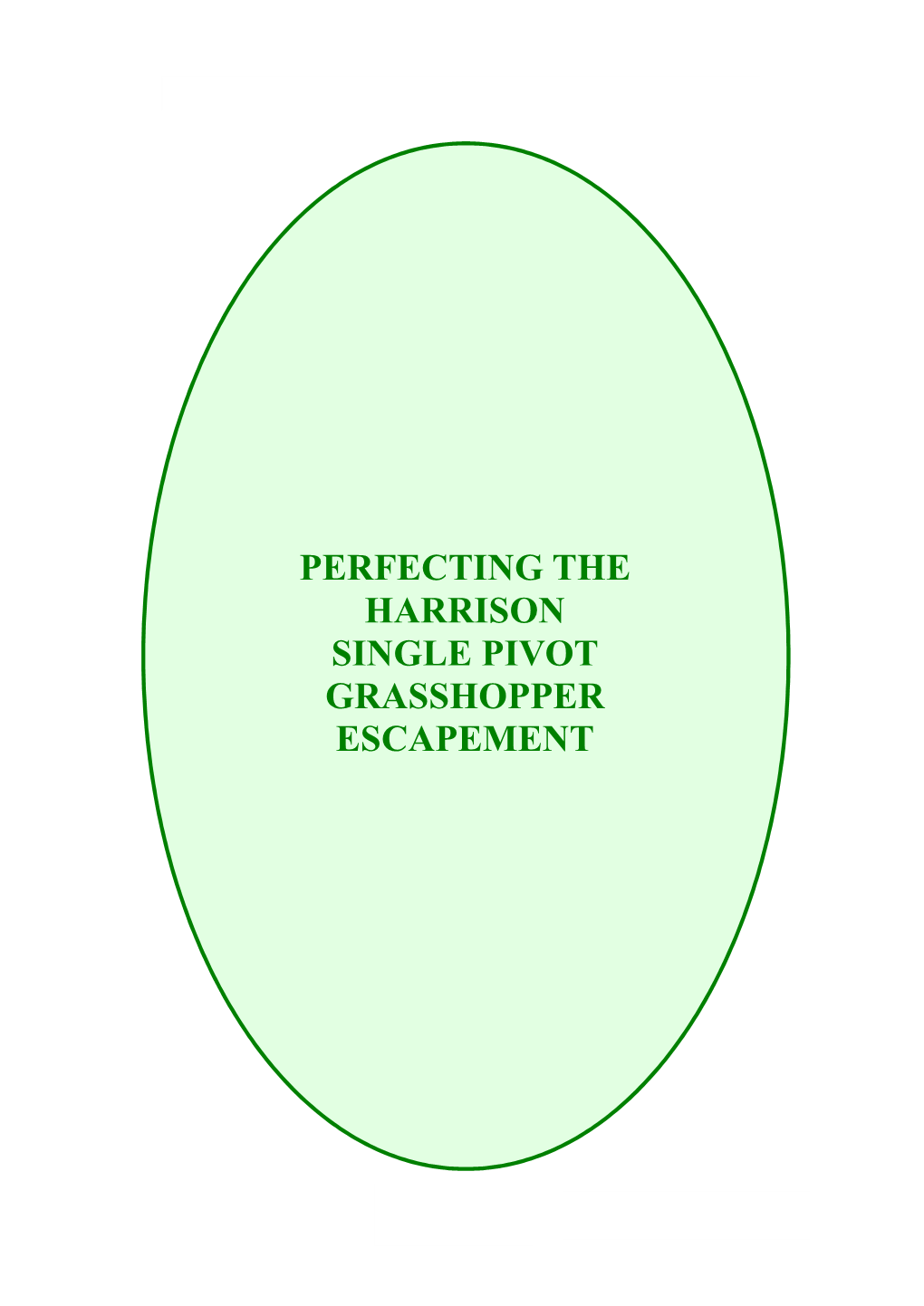
Load more
Recommended publications
-
The Unilateral Twin Pivot Grasshopper Escapement
NAWCC Chapter 161 Horological Science Newsletter 2014-1 www.hsn161.com THE UNILATERAL TWIN PIVOT GRASSHOPPER ESCAPEMENT David Heskin. 16th November 2013 All currently known written, illustrated and/or physical evidence attributable to John ‘Longitude’ Harrison (1693-1776) indicates that he invented and constructed three configurations of the grasshopper escapement: (1) The twin pivot. Almost certainly the first grasshopper escapement invented by Harrison and the first to be realised in physical form within his Brocklesby Park tower clock. The entry and exit pallet arms and their paired composers are mounted upon separate pivots, located to either side of the escapement frame arbor (crutch arbor) axis. This configuration could, therefore, be referred to as a ‘bilateral twin pivot’ or ‘BTP’ grasshopper escapement. Recent analysis1 has revealed that the deliberate incorporation of matching entry and exit start of impulse torque arms and matching entry and exit end of impulse torque arms is not only possible and arguably desirable, but is also of invaluable assistance during the geometrical design process. (2) The single pivot 2. Created by Harrison for his early wooden longcase regulators and his final land-based regulator, now commonly referred to as the ‘RAS Regulator’. Optimised in his 1775 manuscript ‘Concerning Such Mechanism…’ (CSM)3 and an untitled escapement illustration, catalogued by the Worshipful Company of Clockmakers as ‘MS3972/3’. The entry and exit pallet arms and both composers share a single pivot, located on the entry side of the escapement frame arbor axis. All realistic single pivot grasshopper escapement geometries unavoidably incorporate mismatched torque arms and asymmetrical entry versus exit impulse. -
The Magazine of Corpus Christi College
8 0 0 2 s a m l e a h c i M 6 1 e u s s I The magazine of Corpus Christi College Cambridge SttuarrttLaiing PaullWarrrren CorrpussCllocck FiirrssttTellephone New Mastterr New Burrsarr unveiilled Campaiign Contents 3 The Master’s Introduction Stuart Laing, Master 4 Stuart Laing takes up Mastership 8 The Office of Treasurer appointed 10 The Corpus Clock 12 Paul Warren, Bursar 14 Nick Danks, Director of Music 16 Alumni Fund & Telephone Campaign 18 Christopher Kelly: Attila the Hun 19 Paul Mellars receives an award 20 John Hatcher: The Black Death 21 Concert dates, for Ryan Wigglesworth 22 Twenty five years of the Admission of women 26 Student summer internship 27 New Junior Common Room Editor: Liz Winter Managing editor: Latona Forder-Stent Assistant editor: Lucy Gowans Photographers: Philip Mynott Andisheh Photography (Andisheh Eslamboil m2000) Stephen E Gross: Atllia the Hun Jeremy Pembrey: Corpus Clock Alexander Leiffheidt ( m2001): John Hatcher Greg E J Dickens: Chapel Organ Dr Marina Frasca-Spada Nigel Luckhurst: Ryan Wigglesworth Manni Mason Photography: Paul Mellars Jet Photographic Eden Lilley Photography Occasional Photography Produced by Cameron Design & Marketing Ltd www.cameronacademic.co.uk Master’s Introduction Dear Alumni and friends of Corpus, Gerard Duveen 4 March 1951 – 8 Nov 2008 I write having taken up the Mastership just three weeks ago. I am naturally delighted – and honoured – The Master and Fellows of Corpus Christi are to be here, at a desk looking out into New Court where sad to announce the death of Dr Gerard so many of my distinguished predecessors have Duveen, Fellow of the College and Reader in sat before. -
Tranquility Clock Kit and Plan Manual
The Tranquility Clock Copryight © 2014 Jeffrey A. Schierenbeck Introduction For hundreds of years, mechanical clocks have served as functional timekeepers. During that time, clocks have also been treasured for their artistic and aesthetic value. For most clocks, the artistry involves the shape and ornamentation of the clock’s exterior case. However, these cases hide the inner beauty of the clock–the clockwork mechanism. The Tranquility clock is a wooden gear clock that is a functional timekeeper with an open frame which exposes its mechanical elements. All the moving parts are clearly visible. It is intriguing to watch as the seconds and minutes tick away. Of particular interest is its ‘grasshopper’ escapement. It is based on the famous escapement which was developed by John Harrison. In the late 1700's, Harrison devised the grasshopper escapement in his quest to make an accurate, seaworthy clock and claim the “Longitude Prize”. The goal of his articulated escapement was to eliminate sliding friction at the pallets, which was a significant source of error in the days when effective lubrication had not been developed. It is enjoyable to see and hear this clock running. However, the most enjoyable part of this clock is the satisfaction gained by assembling the clock yourself, perhaps adding your own creative touches. And, through the process of building the clock, you will gain an understanding of the principles that govern how a clock works, including the operation of the unique grasshopper escapement. We truly hope you enjoy building your clock. Please contact us if there is any way that we can help you with your clockmaking project. -
John Taylor Contents
John Taylor Born 1936. Philanthropist, horologist, and inventor of thermostatic electric kettles. Autobiographical life story. Available online at www.livesretold.co.uk Contents 1. Life 2. Inventions 3. Passions 4. Business Life 5. Philanthropy 6. Art & Design 7. Horology & Clocks 8. Science & Engineering 9. The Corpus Chronophage 10. The Midsummer Chronophage 11. The Dragon Chronophage 12. Chronophage Commissions 13. Publications 14. Arragon Mooar 15. A Personal Tribute This life story was archived in 2021, with acknowledgement and thanks, from Dr. John Taylor's website at www.johnctaylor.com. Where additional internet material has been added the source is acknowledged. 1 1. Life I was lucky to be able to study Natural Sciences at Corpus Christi College at Cambridge University. I remember thinking I was very smart at school – until I got to university – when I realised that there were a lot of people much smarter than me! However, after a long career, I’m now immensely proud to be considered one of Britain’s greatest inventors. I returned to live on the Isle of Man 40 years ago after running the highly successful Otter Controls business in Buxton, Derbyshire. Many of the hundreds of patents that I hold are for domestic appliances, thermostats and electrical equipment. Probably my most famous invention is the thermostat controls for the cordless kettle, patented and used throughout the world. It’s been calculated that over two billion of my bi- metal blades – used in thermostats to switch off kettles – have been produced since their invention in the 1970s. Strix, a company I founded, now holds four Queen’s Awards, three for Export and one for Innovation, granted for my 360-degrees cordless kettle connector. -
Books on (Or Related To) Escapements for Mechanical Timepieces(An
This list generated 1/6/2004 Books on (or Related to) Escapements for Mechanical Timepieces (an ongoing list) Compiled by Daryl Bender but only with the magnanimous assistance of the following; Dr. David M. MacMillan, Fortunat F. Mueller-Maerki, Robert Miles, Ernest Martt, Bill Scolnik, Tony Roberts, Paul Middents, Bob Holmstrom and where all else was unknown then brief descriptions from the catalogs of Rita Shenton and G.K. Hadfield were used. May they live long and prosper. I take credit for all typos, incorrect spelling etc. Binding, Author Title Publisher Comments Year Pages Height On the Disturbances of Pendulums A classic paper. The first comprehensive theory on escapements and pendulums. Paper and Balances and on the Theory of Royal Society, Airy, George Biddell given at the Royal society , London 1826, technical and mathematical. Available at 1826 Escapements - Read at the Royal United Kingdom http://www.marcdatabase.com/~lemur/dmh-airy-1826.html Society November 26, 1826 Horologerie et Chronometrie - HB, burgundy, Bailliere, Paris 192 Illustrations, "Contains much information on chronometers. Tends to be Antrades, Jules Grandes encyclopedies industrielles - 1924 582 3/4leather, France advanced and technical, but is an important work." J.B. Bailliere marb, 24cm Les Organes regulants des Magron, Bienne HB, orange, Antrades, Jules 1922 146 Chronometres Switzerland 20cm Supplement #8 to the Bulletin of the NAWCC. A very detailed review of the dead-beat A Review of George Graham's with respect to theory and design. Contains a brief biography, some observations, basic Saddlestapled, Aydlett, Guy D Classic Escapement - Dead-Beat by NAWCC 1973 52 geometry, the action, the layout procedure, symbols, the tables, some finer points, some green 23cm. -
Readingsample
History of Mechanism and Machine Science 21 The Mechanics of Mechanical Watches and Clocks Bearbeitet von Ruxu Du, Longhan Xie 1. Auflage 2012. Buch. xi, 179 S. Hardcover ISBN 978 3 642 29307 8 Format (B x L): 15,5 x 23,5 cm Gewicht: 456 g Weitere Fachgebiete > Technik > Technologien diverser Werkstoffe > Fertigungsverfahren der Präzisionsgeräte, Uhren Zu Inhaltsverzeichnis schnell und portofrei erhältlich bei Die Online-Fachbuchhandlung beck-shop.de ist spezialisiert auf Fachbücher, insbesondere Recht, Steuern und Wirtschaft. Im Sortiment finden Sie alle Medien (Bücher, Zeitschriften, CDs, eBooks, etc.) aller Verlage. Ergänzt wird das Programm durch Services wie Neuerscheinungsdienst oder Zusammenstellungen von Büchern zu Sonderpreisen. Der Shop führt mehr als 8 Millionen Produkte. Chapter 2 A Brief Review of the Mechanics of Watch and Clock According to literature, the first mechanical clock appeared in the middle of the fourteenth century. For more than 600 years, it had been worked on by many people, including Galileo, Hooke and Huygens. Needless to say, there have been many ingenious inventions that transcend time. Even with the dominance of the quartz watch today, the mechanical watch and clock still fascinates millions of people around the, world and its production continues to grow. It is estimated that the world annual production of the mechanical watch and clock is at least 10 billion USD per year and growing. Therefore, studying the mechanical watch and clock is not only of scientific value but also has an economic incentive. Never- theless, this book is not about the design and manufacturing of the mechanical watch and clock. Instead, it concerns only the mechanics of the mechanical watch and clock. -
London Metropolitan Archives Daniels, George
LONDON METROPOLITAN ARCHIVES Page 1 DANIELS, GEORGE {DR} {HOROLOGIST} LMA/4636 Reference Description Dates WATCH AND CHRONOMETER MAKER, INVENTOR AND CONSULTANT TRAINING LMA/4636/A/01/001 Northampton Polytechnic, St John Street, 1951 - 1952 Not available for online ordering. Islington Evening Course 'H.3' on horology: Please see staff Exercise book Containing Daniels' calculations, diagrams and formula concerning balance, motions and other topics. Includes receipt for fees paid 1 volume LMA/4636/A/01/002 National Physical Laboratory Certificate of 1952 Feb 8 Not available for online ordering. Examination of a silver split-seconds Please see staff chronograph watch Movement number 201172. With results of test and performance 1 document WATCH AND CHRONOMETER MAKER AND RESTORER, AGENT FOR BREGUET OF PARIS LMA/4636/A/02/001 Duke of Wellington, Apsley House, Piccadilly, 1965 - 1966 Not available for online ordering. Westminster Please see staff Letters to Daniels concerning his orders for Breguet watch repairs 2 documents LMA/4636/A/02/002 'Harrison number 5' test rates 1967 Nov - Not available for online ordering. On letter head 1967 Dec Please see staff 3 documents LMA/4636/A/02/003 Watch rate certificate for automatic centre 1969 Apr 29 Not available for online ordering. second calendar watch Please see staff Certificate number 2722211, issued by Swiss Institute for Official Chronometer tests. Maker: Ulysse Nardin SA, Le Locle, Switzerland 1 document DRAWINGS AND TECHNICAL INFORMATION Co-axial escapement LMA/4636/A/03/01/001 Showing the action of the escapement 1981 - 1999 Not available for online ordering. Original drawings by Daniels, prints and Please see staff photocopies, early designs showing balance turning and layout for Patek Phillipe (1981). -
570 NATURE Differences Are Due to One Or Many Factor-Differences ; John Harrison
570 NATURE differences are due to one or many factor-differences ; John Harrison. and when one remembers the initial difficulty in some I TRUST that you will allow an admirer of John of the most carefully-controlled experiments, even Harrison to be a little indignant with your reviewer, in Drosophila itself, of distinguishing between the " R. A. s.," of Lt.-Comdr. Gould's book (NATURE, effects of " nature " and " nurture," one can only March 22, p. 417). "To some he [Harrison] appears. feel that to lay down on such evidence, whether or ... incurably clumsy. His taste for making clocks. not the inheritance of acquired characters has been of wood, his complications, his retrograde inventions. operative, is a temerity the magnitude of which the like the grasshopper escapement and the gridiron author has probably not realised. pendulum ... stand to his debit." These are I have mentioned Dr. Annandale because I have surely strange words for a man who (unless I mis just happened to read and be interested in his eco interpret the initials) has been president of the Royal logical observations : but similar instances abound. Astronomical Society, in the house of which stands Per contra, as mentioned in a recent number of that exquisite piece of mechanism, the Harrison clock, NATURE, Dr. F. M. Chapman (Bull. American Museum lovingly restored and enthusiastically described by of Natural History, vol. 48, 1923, No. 9) has recently Mr. E . T. Cottingham (Monthly Notices, R. A. S., been attempting to utilise Mendelian conceptions lxx. 25, Nov. 1909). Harrison, it must be remem in the taxonomy of birds. -
Sidney Sussex College, Cambridge 2016 Visit Hamaas Hassan
Sidney Sussex College, Cambridge 2016 Visit Hamaas Hassan From Thursday 17th March to Friday 18th March, I had the opportunity to visit Sidney Sussex College in Cambridge, as part of an experience to understand varsity life. The trip entailed various programmes, held over the course of the two days, which aimed to give us an insight into the unique lifestyle of Cambridge University and its local area. Thursday 17th: Our day officially began at 7 am where we made the departure from West Hill School and set off for our visit. After a nauseating 4-hour journey, and several noisy complaints on my behalf, we soon arrived at Cambridge. As a group of students residing on the outskirts of Manchester, Cambridge in comparison was a wonderland, with archaic yet awe-inspiring structures and sublime scenery of freshly cut, uniform green grass and a scenic river. Thereafter, we reached Sidney Sussex and having been welcomed by staff, our focus was to settle into the accommodation. We each received keys for our residential rooms, unpacked and regrouped at the Porters’ Lodge. A ‘Welcome and Introduction’ presentation followed next with the Director of Admissions, Dr Kirsten Dickers. She introduced the talk by highlighting general information regarding Cambridge University, such as covering the fees, social/academic lifestyle and the courses available. Towards the end, we were able to ask questions and gain further insight about the collegiate system and the varied extra-curricular activities offered at Cambridge - all of which was immensely beneficial. The rest of the day was based around a provisional programme, which followed: 15:15 - Tour of Sidney Sussex College and Q&A with undergraduate students 16:00 - Punting down the ‘Backs’ on the River Cam 18:00 - Dinner in College (Hall Court) 19:00 - Evening social activities (Quiz, etc.) (Knox-Shaw Room) Throughout the course of the day, we were allotted moments of ‘free-time’ where we had the chance to explore the city for ourselves, and learn about Cambridge’s weird and wonderful history. -
Simple Pendulum
The (Not So) Simple Pendulum ©2007-2008 Ron Doerfler Dead Reckonings: Lost Art in the Mathematical Sciences http://www.myreckonings.com/wordpress December 29, 2008 Pendulums are the defining feature of pendulum clocks, of course, but today they don’t elicit much thought. Most modern “pendulum” clocks simply drive the pendulum to provide a historical look, but a great deal of ingenuity originally went into their design in order to produce highly accurate clocks. This essay explores horologic design efforts that were so important at one time—not gearwork, winding mechanisms, crutches or escapements (which may appear as later essays), but the surprising inventiveness found in the “simple” pendulum itself. It is commonly known that Galileo (1564-1642) discovered that a swinging weight exhibits isochronism, purportedly by noticing that chandeliers in the Pisa cathedral had identical periods despite the amplitudes of their swings. The advantage here is that the driving force for the pendulum, which is difficult to regulate, could vary without affecting its period. Galileo was a medical student in Pisa at the time and began using it to check patients’ pulse rates. Galileo later established that the period of a pendulum varies as the square root of its length and is independent of the material of the pendulum bob (the mass at the end). One thing that surprised me when I encountered it is that the escapement preceded the pendulum—the verge escapement was used with hanging weights and possibly water clocks from at least the 14th century and probably much earlier. The pendulum provided a means of regulating such an escapement, and in fact Galileo invented the pin-wheel escapement to use in a pendulum clock he designed but never built. -
DAVA SOBEL Contents
LONGITUDE The True Story of a Lone Genius Who Solved the Greatest Scientific Problem of His Time DAVA SOBEL Contents 1. Imaginary Lines 2. The Sea Before Time 3. Adrift in a Clockwork Universe 4. Time in a Bottle 5. Powder of Sympathy 6. The Prize 7. Cogmaker’s Journal 8. The Grasshopper Goes to Sea 9. Hands on Heaven’s Clock 10. The Diamond Timekeeper 11. Trial by Fire and Water 12. A Tale of Two Portraits 13. The Second Voyage of Captain James Cook 14. The Mass Production of Genius 15. In the Meridian Courtyard Acknowledgments Sources For my mother, Betty Gruber Sobel, a four-star navigator who can sail by the heavens but always drives by way of Canarsie. 1. Imaginary Lines When I’m playful I use the meridians of longitude and parallels of latitude for a seine, drag the Atlantic Ocean for whales. —MARK TWAIN, Life on the Mississippi Once on a Wednesday excursion when I was a little girl, my father bought me a beaded wire ball that I loved. At a touch, I could collapse the toy into a flat coil between my palms, or pop it open to make a hollow sphere. Rounded out, it resembled a tiny Earth, because its hinged wires traced the same pattern of intersecting circles that I had seen on the globe in my schoolroom— the thin black lines of latitude and longitude. The few colored beads slid along the wire paths haphazardly, like ships on the high seas. My father strode up Fifth Avenue to Rockefeller Center with me on his shoulders, and we stopped to stare at the statue of Atlas, carrying Heaven and Earth on his. -
Articles Published in Antiquarian Horology Volumes 1-29 December 1953 - June 2008
Articles published in Antiquarian Horology Volumes 1-29 December 1953 - June 2008 VOLUME 1 1953 Vol.1/1 Roll of Founder members ............................................................................................................................................ 3 No Real Night by H Alan Lloyd ................................................................................................................................. 4 An Unorthodox Watch by C S Jagger........................................................................................................................ 6 The Tower of Babel by John W Castle ...................................................................................................................... 7 Vol.1/2 A neglected Chapter by T P Camerer Cuss .............................................................................................................. 10 A Viennese Flower-Vase Clock by Dr H von Bertele .............................................................................................. 13 Bejamin Lewis Vulliamy by S Benson Beevers ....................................................................................................... 15 15th & 16th Century Clocks by C B Drover................................................................................................................ 17 Early Oxford Clockmakers by Dr C F C Beeson ...................................................................................................... 19 Vol.1/3 The Huygens Collection by F A B Ward ..................................................................................................................