Lightweight Concrete—From Basics to Innovations
Total Page:16
File Type:pdf, Size:1020Kb
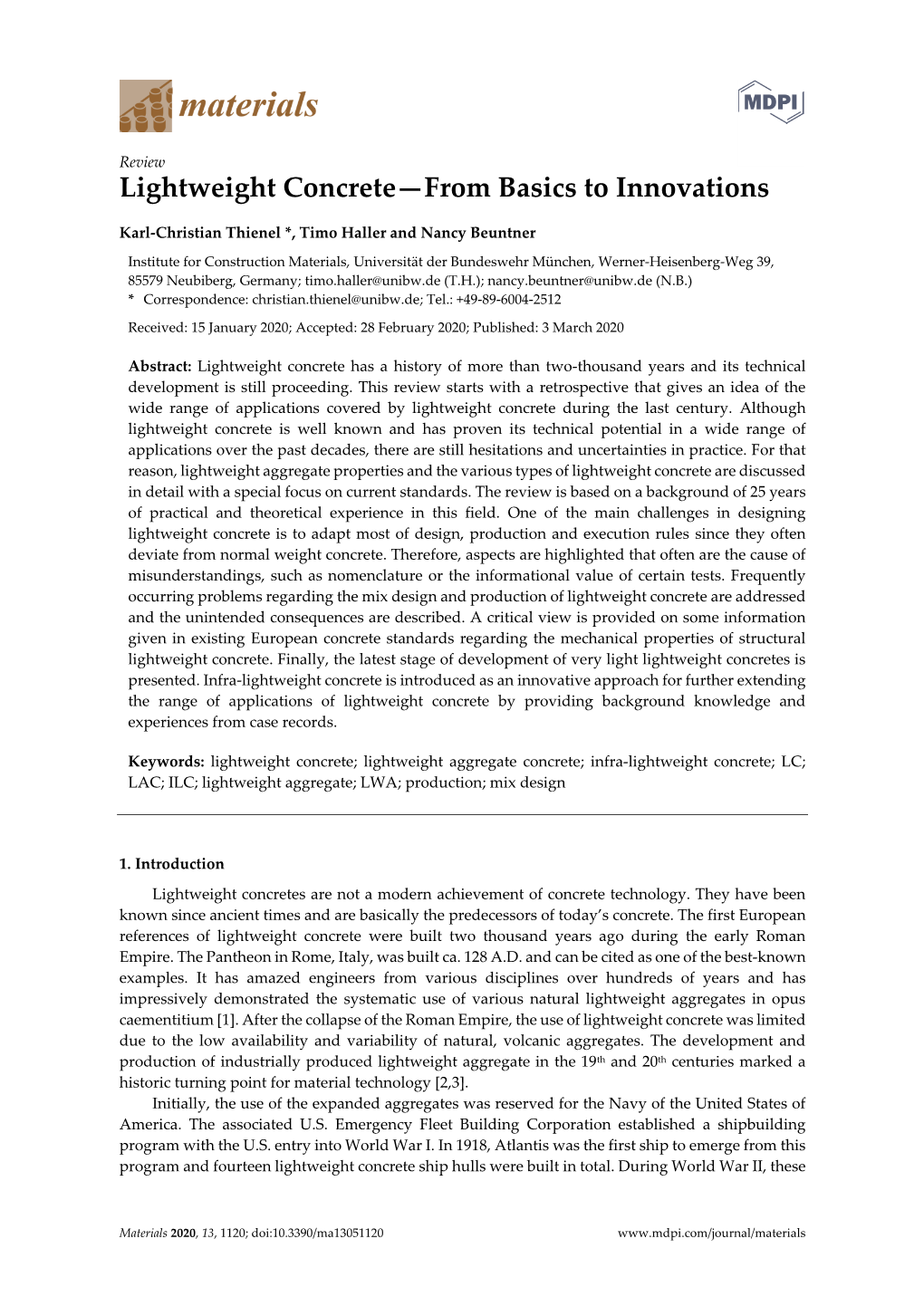
Load more
Recommended publications
-
Application of WST-Method for Fracture Testing of Fibre-Reinforced Cement Based Composites
NORDTEST project No. 1672-04 Application of WST-method for fracture testing of fibre-reinforced cement based composites Swedish National Testing and Research Institute Application of WST-method for fracture testing of fibre-reinforced concrete INGEMAR LÖFGREN, JOHN FORBES OLESEN AND MATHIAS FLANSBJER Department of Structural Engineering and Mechanics Report 04:13 Concrete Structures CHALMERS UNIVERSITY OF TECHNOLOGY Göteborg, Sweden 2004 REPORT 04:13 Application of WST-method for fracture testing of fibre-reinforced concrete INGEMAR LÖFGREN, JOHN FORBES OLESEN AND MATHIAS FLANSBJER Department of Structural Engineering and Mechanics Concrete Structures CHALMERS UNIVERSITY OF TECHNOLOGY Göteborg, Sweden 2004 Application of WST-method for fracture testing of fibre-reinforced concrete INGEMAR LÖFGREN I, JOHN FORBES OLESEN II AND MATHIAS FLANSBJER III IDepartment of Structural Engineering and Mechanics, Chalmers University of Technology. II DTU – Technical University of Denmark, Department of Civil Engineering. III SP – Swedish National Testing and Research Institute. © Ingemar Löfgren, John Forbes Olesen and Mathias Flansbjer, 2004 ISSN 1651-9035 Report 04:13 Archive no. 35 Department of Structural Engineering and Mechanics Concrete Structures Chalmers University of Technology SE-412 96 Göteborg Sweden Telephone: + 46 (0)31-772 1000 Cover: Cover shows the funding agent, the participating labs, and a schematic showing the principle of the wedge-splitting test method.. Department of Structural Engineering and Mechanics Göteborg, Sweden 2004 Application of WST-method for fracture testing of fibre-reinforced concrete Ingemar Löfgren I, John Forbes Olesen II and Mathias Flansbjer III IDepartment of Structural Engineering and Mechanics, Chalmers University of Technology. II DTU – Technical University of Denmark, Department of Civil Engineering, BYG.DTU. -
Tech Brief: Field Control of Concrete Paving Mixtures
Tech Brief NOVEMBER 2019 FHWA-HIF-18-013 FIELD CONTROL OF CONCRETE PAVING MIXTURES INTRODUCTION The variability of a concrete paving mixture can have a significant impact on the performance of the concrete pavement and impact its overall service life. Mixture variability can lead to inconsistent workability, poor consolidation, built-in roughness, and areas of weaker, less durable concrete, all of which can negatively affect pavement performance (Fick et al. 2012). Well-defined and implemented field control of concrete paving mixtures is extremely important to produce, deliver, and place a consistent concrete pavement mixture that meets design criteria and increases the chance of achieving durability goals. This Tech Brief summarizes guidance on the concrete-making process from batching through placement on grade. It draws from key reference documents on field control of concrete mixtures including: • Integrated Materials and Construction Practices for Concrete Pavement: A State-of-the-Practice Manual (Taylor et al. 2006). • Concrete Pavement Field Reference, Pre-Paving (ACPA 2008). • Concrete Pavement Field Reference, Paving (ACPA 2010). • Field Reference Manual for Quality Concrete Pavements (Fick et al. 2012). • Effective Quality Assurance for Concrete Paving Operations (Taylor 2016). • Design and Control of Concrete Mixtures (Kosmatka and Wilson 2016). ACPA (2008) provides a pre-paving checklist covering key items to consider and inspect during pre-paving operations, including some attributes of the concrete mixture and ACPA (2010) provides an additional checklist that focuses on all elements of the concrete paving operation itself. Together, these references serve as a good starting point to establish necessary controls to produce, transport, and place quality paving concrete. -
Concrete CO2 Fact Sheet
NRMCA Publication Number 2PCO2 Concrete CO2 Fact Sheet June 2008 © Copyright 2008 by the National Ready Mixed Concrete Association All Rights Reserved Concrete CO2 Fact Sheet Forward This publication was written by the National Ready Mixed Concrete Association to help its members understand the complexities of climate change and the greenhouse effect. NRMCA and its members are dedicated to continuous environmental improvement through product and process innovation. This publication provides a brief overview of the concrete industry’s role in minimizing environmental impact related to carbon dioxide emissions. Disclaimer This publication is intended for the use of professional personnel, competent to evaluate the significance and limitations of its content, and who will accept responsibility for the application of the material it contains. The National Ready Mixed Concrete Association and the other organizations cooperating in the preparation of this publication strive for accuracy but disclaim any and all responsibility for application of the stated principles or for the accuracy of the sources. Unless otherwise indicated, all materials on these pages are copyrighted by the National Ready Mixed Concrete Association or cooperating organizations. All rights reserved. Therefore, reproduction, modification or retransmission, in any form is strictly prohibited without prior written permission from the National Ready Mixed Concrete Association. © 2008 National Ready Mixed Concrete Association. JUNE 2008 2 Concrete CO2 Fact Sheet CONCRETE CO2 FACT SHEET Introduction Concrete is the most widely used building material in the world because of its beauty, strength and durability, among other benefits. Concrete is used in nearly every type of construction, including homes, buildings, roads, bridges, airports and subways, just to name a few. -
Isotope Techniques Applied to Ancient Roman Mortars - 1
Isotope Techniques applied to Ancient Roman Mortars - 1 - Interested in European research? RTD info is our quarterly magazine keeping you in touch with main developments (results, programmes, events, etc.). It is available in English, French and German. A free sample copy or free subscription can be obtained from: European Commission Directorate-General for Research Information and Communication Unit B-1049 Brussels Fax (32-2) 29-58220 E-mail: [email protected] Internet: http://europa.eu.int/comm/research/rtdinfo/index_en.html EUROPEAN COMMISSION Directorate-General for Research Directorate I — Environment Unit I.1 — Policy Aspects of Research and Urban Development Contact: Brian Brown European Commission Office CDMA 03/178 B-1049 Brussels Tel. (32-2) 29-63628 Fax (32-2) 29-50656 E-mail: [email protected] EUROPEAN COMMISSION Isotope Technologies Applied to the Analysis of Ancient Roman Mortars Results of the CRAFT Project EVK4 CT-2001-30004 Edited by: Caterina Rehm-Berbenni, Andrei Druta, FUTUREtec GmbH Göran Åberg, IFE – Institute for Energy Technology Jacques Neguer, Israel Antiquities Authorities Christoph Külls, Hydroisotop GmbH Giuseppe Patrizi, Servin Scrl Thomas Pacha, Krusemark GmbH Peter Kienzle, Archäologischer Park Xanten Roberto Bugini, CNR ICVBC “Gino Bozza” Maria Grazia Fiore, Soprintendenza Archeologica del Lazio Directorate-General for Research 2005 City of Tomorrow and Cultural Heritage EUR21624 EN Europe Direct is a service to help you find answers to your questions about the European Union Free phone number: 00 800 6 7 8 9 10 11 LEGAL NOTICE Neither the European Commission nor any person acting on behalf of the Commission is responsible for the use which might be made of the following information. -
Team Thomas Sustainability Report 2018
Team Thomas Sustainability Report 2018 1 Introduction At Thomas Concrete Group, care for people and the environment is crucial. That’s why sustainability is and has been important to Team Thomas for a long time – a fact that is best illustrated in our Group’s Mission statement “To be the closest to customers and together actively contribute to building a sustainable society”. Our company has highly competent and committed employees who develop and produce ready-mixed and pre-casted concrete. We care and want to make a difference. Every day, members of Team Thomas wake up early in the morning, ready to serve customers at construction sites and driven by a common ambition to improve the environment around us. Together with all other companies in the construction industry, we have a great responsibility to be transparent and honest in our efforts to continuously improve sustainability performance. Every material used in construction has its own merits. Hence, it’s important to always look at the facts and proven data when making a choice. Concrete is an amazing and sustainable construction material. It is natural, beautiful and creative. Unlike most other material being used that might only last for fifty years, it could be said that concrete is a symbol of sustainability. After all, what other buildings stand for more than 2000 years like the ancient buildings in Rome have? I’m proud of what our Group has done in the area of modern sustainability, but every day we have to actively continue working to improve. Hopefully, you’ll find this report inspiring and a good way of seriously sharing what we practically do. -
Making Concrete Change: Innovation in Low-Carbon Cement and Concrete
Chatham House Report Johanna Lehne and Felix Preston Making Concrete Change Innovation in Low-carbon Cement and Concrete #ConcreteChange Chatham House Report Johanna Lehne and Felix Preston Energy, Environment and Resources Department | June 2018 Making Concrete Change Innovation in Low-carbon Cement and Concrete The Royal Institute of International Affairs Chatham House 10 St James’s Square London SW1Y 4LE T: +44 (0) 20 7957 5700 F: + 44 (0) 20 7957 5710 www.chathamhouse.org Charity Registration No. 208223 Copyright © The Royal Institute of International Affairs, 2018 Chatham House, the Royal Institute of International Affairs, does not express opinions of its own. The opinions expressed in this publication are the responsibility of the author(s). All rights reserved. No part of this publication may be reproduced or transmitted in any form or by any means, electronic or mechanical including photocopying, recording or any information storage or retrieval system, without the prior written permission of the copyright holder. Please direct all enquiries to the publishers. ISBN 978 1 78413 272 9 A catalogue record for this title is available from the British Library. Printed and bound in Great Britain by Latimer Trend. The material selected for the printing of this report is manufactured from 100% genuine de-inked post-consumer waste by an ISO 14001 certified mill and is Process Chlorine Free. Typeset by Soapbox, www.soapbox.co.uk Cover image: Staircase, Benesse Museum House, Naoshima, Japan. Copyright © Education Images/UIG via Getty Images -
Green Concrete Based on Quaternary Binders with Significant Reduced Of
energies Article Green Concrete Based on Quaternary Binders with Significant Reduced of CO2 Emissions Grzegorz Ludwik Golewski Department of Structural Engineering, Faculty of Civil Engineering and Architecture, Lublin University of Technology, Nadbystrzycka 40 Str., 20-618 Lublin, Poland; [email protected]; Tel.: +48-81-538-4394 Abstract: The article presents studies of plain concretes prepared based on a quaternary binder containing various percentages of selected supplementary cementitious materials (SCMs). The possibilities of nanotechnology in concrete technology were also used. An additional important environmental goal of the proposed solution was to create the possibility of reducing CO2 emissions and the carbon footprint generated during the production of ordinary Portland cement (OPC). As the main substitute for the OPC, siliceous fly ash (FA) was used. Moreover, silica fume (SF) and nanosilica (nS) were also used. During examinations, the main mechanical properties of composites, i.e., compressive strength (f cm) and splitting tensile strength (f ctm), were assessed. The microstructure of these materials was also analyzed using a scanning electron microscope (SEM). In addition to the experimental research, simulations of the possible reduction of CO2 emissions to the atmosphere, as a result of the proposed solutions, were also carried out. It was found that the quaternary concrete is characterized by a well-developed structure and has high values of mechanical parameters. Further- more, the use of green concrete based on quaternary binders enables a significant reduction in CO2 emissions. Therefore quaternary green concrete containing SCMs could be a useful alternative to plain concretes covering both the technical and environmental aspects. The present study indicates Citation: Golewski, G.L. -
Field Monitoring of Shrinkage Cracking Potential in a High
FIELD MONITORING OF SHRINKAGE CRACKING POTENTIAL IN A HIGH-PERFORMANCE CONCRETE BRIDGE DECK By TIM WALKOWICH A Thesis submitted to the Graduate School – New Brunswick Rutgers, The State University of New Jersey in partial fulfillment of the requirements for the degree of Master of Science Graduate Program in Civil and Environmental Engineering Written under the direction of Dr. Hani Nassif and approved by New Brunswick, New Jersey January 2011 ABSTRACT OF THE THESIS Field Monitoring of Shrinkage Cracking Potential in a High- Performance Concrete Bridge Deck Thesis Director: Dr. Hani H. Nassif Over the past decade many state engineers throughout New Jersey have reported cracking on High Performance Concrete (HPC) bridge decks at early ages. The presence of cracking early in the life of a high performance deck offsets the benefits gained in using the material as the potential for corrosion begins at the onset of cracking. While many factors apply to bridge deck cracking, the shrinkage of the concrete’s mass is a primary concern. Because of shear studs and boundary conditions, among other causes that act in restraining the deck itself, it is important to understand the mechanics of concrete under restraint. The AASHTO Passive Ring Test (PP 34-06) is seeing an increase in use in studies analyzing restrained shrinkage. The test simulates a concrete member of infinite length and allows researchers to study the effects of various parameters on restrained shrinkage. This thesis presents the results of a study that analyzed the ring test’s ability to simulate restrained shrinkage on HPC bridge decks. The investigation incorporated an instrumented, simply supported ii composite bridge deck with laboratory samples taken on the day of the pour as well as a finite element analysis. -
Sustainable Concrete Plant Guidelines Version
Sustainable Concrete Plant Guidelines Version 1.1 March 2011 Development Development funded by managed by TM This page intentionally left blank. Sustainable Concrete Plant Guidelines Version 1.1 March 2011 © RMC Research & Education Foundation i This page intentionally left blank. ii Acknowledgements Development of the Sustainable Concrete Plant Guidelines was funded by the RMC Research & Educa- tion Foundation. They were prepared for the RMC Research & Education Foundation by Cris Argeles and Miranda Intrator of West Main Consultants with assistance from William Twitty and Mike Armor, indepen- dent consultants. The RMC Research & Education Foundation would also like to thank and acknowledge those organiza- tions and individuals who participated in the development of the Guidelines. The National Ready Mixed Concrete Association (NRMCA) managed the process of developing the Guidelines including interfacing with the consultants and NRMCA members who participated in reviewing the Guidelines. NRMCA also facilitated a sustainable concrete plant survey to help set the baseline for many of the credits within the Guidelines and also facilitated a pilot program to help finalize details of the Guidelines. The following indi- viduals participated in reviewing and finalizing the Guidelines: Johnie Alexander Concrete Supply Company, United States Patrick Bergin Cemstone, United States David Bosarge MMC Materials, United States Rabih Fakih Grey Matters Consultancy, United Arab Emirates Lionel Lemay National Ready Mixed Concrete Association, United -
Section 704—Cement Concrete
P-b07042-B Instructions for Use: These are changes to Section 704 and Section 1001 for bridge deck performance. For use on projects as listed for each district on the spreadsheet entitled “Improved Bridge Deck Performance Pilot Projects 2016” located at P:\penndot shared\Improved Bridge Deck Performance Committee District Surveys\Improved Bridge Deck Performance Pilots. Also include “PTM 528” located in the ECMS File Cabinet as an attachment to the proposal. HEADER: b07041 Section 704 and Section 1001 Provision Body: SECTION 704—CEMENT CONCRETE Section 704.1(b) Material. Revise to read as follows: (b) Material. Cement, Type I/II—Section 701 Fine Aggregate, Type A—Section 703.1 Coarse Aggregate, Type A, Maximum size AASHTO No. 57, unless approved by the District Materials Engineer/District Materials Manager (Stone, Gravel, or Slag)—Section 703.2 Water—Section 720.1 Admixtures—Section 711.3 Pozzolan—Section 724 Table A Cement Concrete Criteria. Revise to read as follows: Page 1 of 12 P-b07042-B TABLE A Cement Concrete Criteria Minimum Proportions Maxim Mix(2,9) Design 28-Day um Coarse(1) Cement Factor(3)(5) Compressive Structural Class of Water Aggregate Design Use (lbs/cu. yd.) Strength Concrete Cement (psi) Solid Compressive Ratio(6) Volume Strength Days (lbs/lbs) (cu. ft./cu. yd.) (psi) Min. Max. 3 7 28 AAAP Bridge Deck 560 640 0.45 — 3,000 4,000 — 4,000 HPC Bridge Deck 560 640 0.45 — 3,000 4,000 — 4,000 AAA(4) Other 634.5 752 0.43 — 3,600 4,500 — 4,000 Slip Form AA 587.5 752 0.47 — 3,000 3,750 11.00-13.10 3,500 Paving(7) AA Paving 587.5 752 0.47 — 3,000 3,750 9.93-13.10 3,500 Accelerated AA 587.5 800 0.47 — — 3,750 9.93-13.10 3,500 Patching(8) AA 587.5 752 0.47 — 3,000 3,750 9.93-13.10 3,500 Structures A 564 752 0.50 — 2,750 3,300 10.18-13.43 3,000 and C 394.8 658 0.66 — 1,500 2,000 11.45-15.10 2,000 Misc. -
Portland Cement Concrete Level II Course Manual
PORTLAND CEMENT CONCRETE LEVEL II TECHNICIAN COURSE “Manual of Instructions for Concrete Proportioning” Effective: November 4, 1994 Revised: January 1, 2016 Portland Cement Concrete Level II Technician Course “Manual of Instructions for Concrete Proportioning” Prepared and Published by Illinois Department of Transportation Bureau of Materials and Physical Research Springfield, Illinois January 1, 2016 PCC Level II Technician Course Manual Revised January 1, 2016 LAKE LAND COLLEGE INSTRUCTOR AND COURSE EVALUATION Course: PCC Level II Technician Course Section: ___________ Date: ___________________ PURPOSE: The main emphasis at Lake Land College is teaching. In this regard, each instructor must be continuously informed of the quality of his/her teaching and the respects in which that teaching can be improved. As a student, you are in a position to judge the quality of teaching from direct experience, and in order to help maintain the quality of instruction at Lake Land, you are asked to complete this evaluation. DIRECTIONS: DO NOT SIGN YOUR NAME. Your frankness and honesty are appreciated. First, please record your general impressions and/or comments on the following: Course __________________________________________________________________________________ ________________________________________________________________________________________ Instructor ________________________________________________________________________________ For each remaining item, circle the number from the scale which seems most appropriate to you for the instructor and course that you are evaluating. You are strongly encouraged to make any comments that will clarify particular rating on the back of this form; please refer to each item you are discussing by its number. WEAK SUPERIOR OBJECTIVES AND APPROPRIATENESS OF THE COURSE: 1. Clarity of The objectives of the course were clearly 1 2 3 4 5 Objectives identified. -
Portland-Limestone Cements: History, Performance, and Specifications
Portland-Limestone Cements: History, Performance, and Specifications Paul D. Tennis, Ph.D. Portland Cement Association Today’s Objectives What is a portland-limestone blended cement History Environmental performance Concrete performance Changes to the specifications Portland-Limestone Cement Why? Provides an option to implement proven technology to obtain desired performance and improve sustainability of concrete What is Portland-Limestone Cement? ASTM C595 and AASHTO M 240 Blended Cement Type IL or Type IT with limestone 5% to 15% limestone HISTORY History of Limestone in Cements 1965 Cement with 20% limestone in Germany for specialty applications 1979 French cement standards allows limestone additions. 1983 CSA A5 allows up to 5% limestone in portland cement 1990 15±5% limestone blended cements routinely used in Germany 1992 UK specs allows up to 20% in limestone cement 2000 EN 197-1 allows 5% MAC (typ. limestone) in all 27 common cements, History of Limestone in Cements 2000 EN 197-1 creates CEM II/A-L (6-20%) and CEM II/B-L (21-35%) 2004 ASTM C150 allows 5% in Types I-V 2006 CSA A3001 allows 5% in other Types than GU 2007 AASHTO M85 allows 5% in Types I-V 2008 CSA A3001 includes PLC containing 5%-15% limestone European Cement Use 100 1.7 2.1 1.8 2.1 2.2 1.5 1.9 6.1 3.4 2.9 1.8 Others 5 3.2 5.0 5.7 9.5 5.4 CEM V - Composite Cement 90 4.0 6.5 5.5 5.1 5.6 CEM IV - Pozzolanic 5.6 4.8 CEM III - Blast furnace slag 80 14.5 12.5 16.8 9.6 14.3 CEM II - Portland-composite 16.8 CEM II - Portland-limestone 70 CEM II - Portland-fly