56 Cracking of Palm
Total Page:16
File Type:pdf, Size:1020Kb
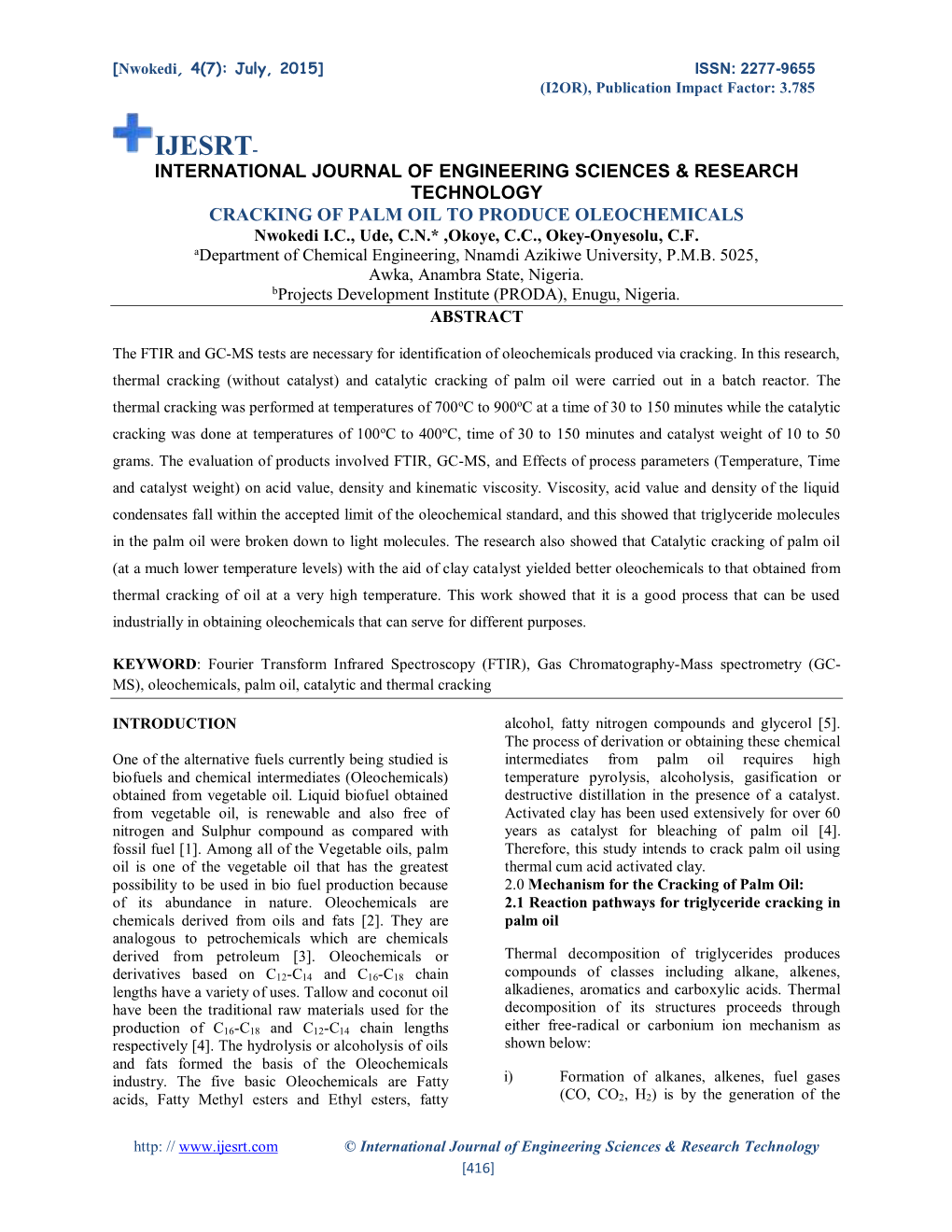
Load more
Recommended publications
-
(12) United States Patent (10) Patent No.: US 9,375.433 B2 Dilly Et Al
US009375433B2 (12) United States Patent (10) Patent No.: US 9,375.433 B2 Dilly et al. (45) Date of Patent: *Jun. 28, 2016 (54) MODULATORS OF ANDROGENSYNTHESIS (52) U.S. Cl. CPC ............. A6 IK3I/519 (2013.01); A61 K3I/201 (71) Applicant: Tangent Reprofiling Limited, London (2013.01); A61 K3I/202 (2013.01); A61 K (GB) 31/454 (2013.01); A61K 45/06 (2013.01) (72) Inventors: Suzanne Dilly, Oxfordshire (GB); (58) Field of Classification Search Gregory Stoloff, London (GB); Paul USPC .................................. 514/258,378,379, 560 Taylor, London (GB) See application file for complete search history. (73) Assignee: Tangent Reprofiling Limited, London (56) References Cited (GB) U.S. PATENT DOCUMENTS (*) Notice: Subject to any disclaimer, the term of this 5,364,866 A * 1 1/1994 Strupczewski.......... CO7C 45/45 patent is extended or adjusted under 35 514,254.04 U.S.C. 154(b) by 0 days. 5,494.908 A * 2/1996 O’Malley ............. CO7D 261/20 514,228.2 This patent is Subject to a terminal dis 5,776,963 A * 7/1998 Strupczewski.......... CO7C 45/45 claimer. 514,217 6,977.271 B1* 12/2005 Ip ........................... A61K 31, 20 (21) Appl. No.: 14/708,052 514,560 OTHER PUBLICATIONS (22) Filed: May 8, 2015 Calabresi and Chabner (Goodman & Gilman's The Pharmacological (65) Prior Publication Data Basis of Therapeutics, 10th ed., 2001).* US 2015/O238491 A1 Aug. 27, 2015 (Cecil's Textbook of Medicine pp. 1060-1074 published 2000).* Stedman's Medical Dictionary (21st Edition, Published 2000).* Okamoto et al (Journal of Pain and Symptom Management vol. -
WO 2017/074902 Al 4 May 20 17 (04.05.2017) W P O P C T
(12) INTERNATIONAL APPLICATION PUBLISHED UNDER THE PATENT COOPERATION TREATY (PCT) (19) World Intellectual Property Organization International Bureau (10) International Publication Number (43) International Publication Date WO 2017/074902 Al 4 May 20 17 (04.05.2017) W P O P C T (51) International Patent Classification: AO, AT, AU, AZ, BA, BB, BG, BH, BN, BR, BW, BY, A61K 8/37 (2006.01) A61Q 19/00 (2006.01) BZ, CA, CH, CL, CN, CO, CR, CU, CZ, DE, DJ, DK, DM, A61K 31/215 (2006.01) DO, DZ, EC, EE, EG, ES, FI, GB, GD, GE, GH, GM, GT, HN, HR, HU, ID, IL, IN, IR, IS, JP, KE, KG, KN, KP, KR, (21) International Application Number: KW, KZ, LA, LC, LK, LR, LS, LU, LY, MA, MD, ME, PCT/US2016/058591 MG, MK, MN, MW, MX, MY, MZ, NA, NG, NI, NO, NZ, (22) International Filing Date: OM, PA, PE, PG, PH, PL, PT, QA, RO, RS, RU, RW, SA, 25 October 2016 (25.10.201 6) SC, SD, SE, SG, SK, SL, SM, ST, SV, SY, TH, TJ, TM, TN, TR, TT, TZ, UA, UG, US, UZ, VC, VN, ZA, ZM, (25) Filing Language: English ZW. (26) Publication Language: English (84) Designated States (unless otherwise indicated, for every (30) Priority Data: kind of regional protection available): ARIPO (BW, GH, 62/247,803 29 October 20 15 (29. 10.20 15) US GM, KE, LR, LS, MW, MZ, NA, RW, SD, SL, ST, SZ, TZ, UG, ZM, ZW), Eurasian (AM, AZ, BY, KG, KZ, RU, (71) Applicant: GLAXOSMITHKLINE CONSUMER TJ, TM), European (AL, AT, BE, BG, CH, CY, CZ, DE, HEALTHCARE HOLDINGS (US) LLC [US/US]; 271 1 DK, EE, ES, FI, FR, GB, GR, HR, HU, IE, IS, IT, LT, LU, Centerville Road, Suite 400, Wilmington, DE 19808 (US). -
( Vaccinium Myrtillus L . ) And
Food Chemistry 354 (2021) 129517 Contents lists available at ScienceDirect Food Chemistry journal homepage: www.elsevier.com/locate/foodchem Analysis of composition, morphology, and biosynthesis of cuticular wax in wild type bilberry (Vaccinium myrtillus L.) and its glossy mutant Priyanka Trivedi a,1, Nga Nguyen a,1, Linards Klavins b, Jorens Kviesis b, Esa Heinonen c, Janne Remes c, Soile Jokipii-Lukkari a, Maris Klavins b, Katja Karppinen d, Laura Jaakola d,e, Hely Haggman¨ a,* a Department of Ecology and Genetics, University of Oulu, FI-90014 Oulu, Finland b Department of Environmental Science, University of Latvia, LV-1004 Riga, Latvia c Centre for Material Analysis, University of Oulu, FI-90014 Oulu, Finland d Department of Arctic and Marine Biology, UiT The Arctic University of Norway, NO-9037 Tromsø, Norway e NIBIO, Norwegian Institute of Bioeconomy Research, NO-1431 Ås, Norway ARTICLE INFO ABSTRACT Keywords: In this study, cuticular wax load, its chemical composition, and biosynthesis, was studied during development of Cuticular wax wild type (WT) bilberry fruit and its natural glossy type (GT) mutant. GT fruit cuticular wax load was comparable Fruit cuticle with WT fruits. In both, the proportion of triterpenoids decreased during fruit development concomitant with Gene expression increasing proportions of total aliphatic compounds. In GT fruit, a higher proportion of triterpenoids in cuticular Glossy type mutant wax was accompanied by a lower proportion of fatty acids and ketones compared to WT fruit as well as lower Triterpenoids Wax composition density of crystalloid structures on berry surfaces. Our results suggest that the glossy phenotype could be caused Chemical compounds studied in this article: by the absence of rod-like structures in GT fruit associated with reduction in proportions of ketones and fatty β-Amyrin (PubChem CID: 73145) acids in the cuticular wax. -
Biochemistry Prologue to Lipids
Paper : 05 Metabolism of Lipids Module: 01 Prologue to Lipids Principal Investigator Dr. Sunil Kumar Khare, Professor, Department of Chemistry, IIT-Delhi Paper Coordinator and Dr. Suaib Luqman, Scientist (CSIR-CIMAP) Content Writer & Assistant Professor (AcSIR) CSIRDr. Vijaya-CIMAP, Khader Lucknow Dr. MC Varadaraj Content Reviewer Prof. Prashant Mishra, Professor, Department of Biochemical Engineering and Biotechnology, IIT-Delhi 1 METABOLISM OF LIPIDS Biochemistry Prologue to Lipids DESCRIPTION OF MODULE Subject Name Biochemistry Paper Name 05 Metabolism of Lipids Module Name/Title 01 Prologue to Lipids 2 METABOLISM OF LIPIDS Biochemistry Prologue to Lipids 1. Objectives To understand what is lipid Why they are important How they occur in nature 2. Concept Map LIPIDS Fatty Acids Glycerol 3. Description 3.1 Prologue to Lipids In 1943, the term lipid was first used by BLOOR, a German biochemist. Lipids are heterogeneous group of compounds present in plants and animal tissues related either actually or potentially to the fatty acids. They are amphipathic molecules, hydrophobic in nature originated utterly or in part by thioesters (carbanion-based condensations of fatty acids and/or polyketides etc) or by isoprene units (carbocation-based condensations of prenols, sterols, etc). Lipids have the universal property of being: i. Quite insoluble in water (polar solvent) ii. Soluble in benzene, chloroform, ether (non-polar solvent) 3 METABOLISM OF LIPIDS Biochemistry Prologue to Lipids Thus, lipids include oils, fats, waxes, steroids, vitamins (A, D, E and K) and related compounds, such as phospholipids, triglycerides, diglycerides, monoglycerides and others, which are allied more by their physical properties than by their chemical assests. -
WO 2016/105530 Al 30 June 2016 (30.06.2016) W P O P C T
(12) INTERNATIONAL APPLICATION PUBLISHED UNDER THE PATENT COOPERATION TREATY (PCT) (19) World Intellectual Property Organization International Bureau (10) International Publication Number (43) International Publication Date WO 2016/105530 Al 30 June 2016 (30.06.2016) W P O P C T (51) International Patent Classification: AO, AT, AU, AZ, BA, BB, BG, BH, BN, BR, BW, BY, A61K 47/10 (2006.01) A61K 47/22 (2006.01) BZ, CA, CH, CL, CN, CO, CR, CU, CZ, DE, DK, DM, A61K 47/12 (2006.01) DO, DZ, EC, EE, EG, ES, FI, GB, GD, GE, GH, GM, GT, HN, HR, HU, ID, IL, IN, IR, IS, JP, KE, KG, KN, KP, KR, (21) International Application Number: KZ, LA, LC, LK, LR, LS, LU, LY, MA, MD, ME, MG, PCT/US20 15/000302 MK, MN, MW, MX, MY, MZ, NA, NG, NI, NO, NZ, OM, (22) International Filing Date: PA, PE, PG, PH, PL, PT, QA, RO, RS, RU, RW, SA, SC, 23 December 2015 (23. 12.2015) SD, SE, SG, SK, SL, SM, ST, SV, SY, TH, TJ, TM, TN, TR, TT, TZ, UA, UG, US, UZ, VC, VN, ZA, ZM, ZW. (25) Filing Language: English (84) Designated States (unless otherwise indicated, for every (26) Publication Language: English kind of regional protection available): ARIPO (BW, GH, (30) Priority Data: GM, KE, LR, LS, MW, MZ, NA, RW, SD, SL, ST, SZ, 62/096,148 23 December 2014 (23. 12.2014) US TZ, UG, ZM, ZW), Eurasian (AM, AZ, BY, KG, KZ, RU, TJ, TM), European (AL, AT, BE, BG, CH, CY, CZ, DE, (72) Inventor; and DK, EE, ES, FI, FR, GB, GR, HR, HU, IE, IS, IT, LT, LU, (71) Applicant : HOFFMAN, Steven [US/US]; 15 Knichel LV, MC, MK, MT, NL, NO, PL, PT, RO, RS, SE, SI, SK, Road, Mahwah, NJ 07430 (US). -
Molecular Tracers and Untargeted Characterization of Water Soluble Organic Compounds in Polar Ice for Climate Change Studies
PhD Thesis in SCIENCE AND MANAGEMENT OF CLIMATE CHANGE Molecular tracers and untargeted characterization of water soluble organic compounds in polar ice for climate change studies. PhD Candidate Ornela Karroca Supervisor Prof. Andrea Gambaro Co-Supervisor Dr. Roberta Zangrando 1 GLOSSARY 1. ABSTRACT ........................................................................................................................................ 4 2. INTRODUCTION ............................................................................................................................... 5 3. THESIS GOALS ................................................................................................................................ 15 4. EXPERIMENTAL SECTION ............................................................................................................... 16 4.1 Reagents and standard solutions ............................................................................................ 16 4.2 Quantitative analyses .............................................................................................................. 17 4.2.1 Instrumentation and working conditions .......................................................................... 17 4.2.2 Amino acids and phenolic compounds: Method validation .............................................. 21 4.2.2.1 Chromatographic separation ..................................................................................... 21 4.2.2.2 Quality control........................................................................................................... -
Obese Mice with Dyslipidemia Exhibit Meibomian Gland Hypertrophy and Alterations in Meibum Composition and Aqueous Tear Production
International Journal of Molecular Sciences Article Obese Mice with Dyslipidemia Exhibit Meibomian Gland Hypertrophy and Alterations in Meibum Composition and Aqueous Tear Production Eugene A. Osae 1,* , Tiffany Bullock 2, Madhavi Chintapalati 2, Susanne Brodesser 3 , Samuel Hanlon 1, Rachel Redfern 1, Philipp Steven 4 , C. Wayne Smith 2, Rolando E. Rumbaut 2,5 and Alan R. Burns 1 1 College of Optometry, University of Houston, Houston, TX 77204, USA; [email protected] (S.H.); [email protected] (R.R.); [email protected] (A.R.B.) 2 Children’s Nutrition Research Center, Baylor College of Medicine, Houston, TX 77030, USA; [email protected] (T.B.); [email protected] (M.C.); [email protected] (C.W.S.); [email protected] (R.E.R.) 3 CECAD Research Center, Lipidomics/Metabolomics Facility, University of Cologne, 50931 Cologne, Germany; [email protected] 4 Department of Ophthalmology, Division for Dry-Eye and Ocular GvHD, Medical Faculty, University of Cologne, 50937 Cologne, Germany; [email protected] 5 Center for Translational Research on Inflammatory Diseases (CTRID), Michael E. DeBakey Veterans Affairs Medical Center, Houston, TX 77030, USA * Correspondence: [email protected]; Tel.: +1-346-317-6273 Received: 14 October 2020; Accepted: 16 November 2020; Published: 20 November 2020 Abstract: Background: Dyslipidemia may be linked to meibomian gland dysfunction (MGD) and altered meibum lipid composition. The purpose was to determine if plasma and meibum cholesteryl esters (CE), triglycerides (TG), ceramides (Cer) and sphingomyelins (SM) change in a mouse model of diet-induced obesity where mice develop dyslipidemia. Methods: Male C57/BL6 mice (8/group, age = 6 wks) were fed a normal (ND; 15% kcal fat) or an obesogenic high-fat diet (HFD; 42% kcal fat) for 10 wks. -
Alpha Omega Cohort Data Dictionary
Alpha Omega Cohort Data dictionary - Food Frequency Questionnaire - Eveline Waterham Alpha Omega Cohort – Data Dictionary Table of contents 1 Dietary pattern ...................................................................................................................................................... 3 2 Bread and wheat products ................................................................................................................................... 3 3 Butter and margarine ........................................................................................................................................... 4 4 Bread toppings ..................................................................................................................................................... 4 5 Breakfast and milk products ................................................................................................................................. 5 6 Coffee and tea ...................................................................................................................................................... 5 7 Diner ..................................................................................................................................................................... 6 7.1 Starch base ....................................................................................................................................... 6 7.2 Soups ............................................................................................................................................... -
Fatty Acids, Trivial and Systematic Names
FATTY ACIDS, TRIVIAL AND SYSTEMATIC NAMES Trivial Name Systematic Name Abbreviation Formic Acid Methanoic Acid Acetic Acid Ethanoic Acid Propionic Acid Propanoic Acid Butyric Acid Butanoic Acid 4:0 Valerianic Acid Pentanoic Acid 5:0 Caproic Acid Hexanoic Acid 6:0 Enanthic Acid Heptanoic Acid 7:0 Caprylic Acid Octanoic Acid 8:0 Pelargonic Acid Nonanoic Acid 9:0 Capric Acid Decanoic Acid 10:0 Obtusilic Acid 4-Decenoic Acid 10:1(n-6) Caproleic Acid 9-Decenoic Acid 10:1(n-1) Undecylic Acid Undecanoic Acid 11:0 Lauric Acid Dodecanoic Acid 12:0 Linderic Acid 4-Dodecenoic Acid 12:1(n-8) Denticetic Acid 5-Dodecenoic Acid 12:1(n-7) Lauroleic Acid 9-Dodecenoic Acid 12:1(n-3) Tridecylic Acid Tridecanoic Acid 13:0 Myristic Acid Tetradecanoic Acid 14:0 Tsuzuic Acid 4-Tetradecenoic Acid 14:1(n-10) Physeteric Acid 5-Tetradecenoic Acid 14:1(n-9) Myristoleic Acid 9-Tetradecenoic Acid 14:1(n-5) Pentadecylic Acid Pentadecanoic Acid 15:0 Palmitic Acid Hexadecanoic Acid 16:0 Gaidic acid 2-Hexadecenoic Acid 16:1(n-14) Sapienic Acid 6-Hexadecenoic Acid 16:1(n-10) Hypogeic Acid trans-7-Hexadecenoic Acid t16:1(n-9) cis-Hypogeic Acid 7-Hexadecenoic Acid 16:1(n-9) Palmitoleic Acid 9-Hexadecenoic Acid 16:1(n-7) Palmitelaidic Acid trans-9-Hexadecenoic Acid t16:1(n-7) Palmitvaccenic Acid 11-Hexadecenoic Acid 16:1(n-5) Margaric Acid Heptadecanoic Acid 17:0 Civetic Acid 8-Heptadecenoic Acid 17:1 Stearic Acid Octadecanoic Acid 18:0 Petroselinic Acid 6-Octadecenoic Acid 18:1(n-12) Oleic Acid 9-Octadecenoic Acid 18:1(n-9) Elaidic Acid trans-9-Octadecenoic acid t18:1(n-9) -
1 Musterseite Im C5-Format Für Winword
Comprehensive Analysis of Cocoa Lipidomics – unraveling the unknown chemistry of cocoa butter by Diana Sirbu a Thesis submitted in partial fulfillment of the requirements for the degree of Doctor of Philosophy in Chemistry Approved Dissertation Committee Prof. Dr. Nikolai Kuhnert, Jacobs University Bremen, Germany Prof. Dr. Matthias Ullrich, Jacobs University Bremen, Germany Dr. Frédéric Depypere, Barry Callebaut Lebbeke-Wieze, Belgium Date of Defense: June 1st, 2018 Department of Life Sciences and Chemistry Sirbu Diana 20331305 Ph. D. Thesis 07.09.2018 I dedicated this thesis to my family for their encouragement, lifelong support and inconditional love. Table of contents Preface ............................................................................................................................................................... I Abstract ........................................................................................................................................................... III List of abbreviations........................................................................................................................................ VI List of figures ............................................................................................................................................... VIII List of tables .................................................................................................................................................. XV Chapter 1: ......................................................................................................................................................... -
( 12 ) United States Patent
US010155042B2 (12 ) United States Patent ( 10 ) Patent No. : US 10 , 155 , 042 B2 Bannister et al. (45 ) Date of Patent: * Dec. 18 , 2018 ( 54 ) COMPOSITIONS AND METHODS FOR A61K 31/ 60 (2006 . 01) TREATING CHRONIC INFLAMMATION A61K 47 / 10 ( 2017 .01 ) AND INFLAMMATORY DISEASES A61K 31 / 202 (2006 . 01 ) A61K 31 / 337 (2006 .01 ) ( 71 ) Applicant: Infirst Healthcare Limited , London A61K 31 / 704 ( 2006 . 01 ) (GB ) A61K 31/ 25 (2006 . 01) 2 ) U . S . CI. ( 72 ) Inventors : Robin M . Bannister , Essex (GB ) ; John CPC .. .. .. .. A61K 47 / 14 ( 2013 .01 ) ; A61K 9 / 08 Brew , Hertfordshire (GB ) ; Wilson ( 2013 .01 ) ; A61K 9 /2013 (2013 . 01 ) ; A61K Caparros - Wanderely , Buckinghamshire 31/ 192 ( 2013 .01 ) ; A61K 31 /60 ( 2013 .01 ) ; (GB ) ; Suzanne J . Dilly , Oxfordshire A61K 47 / 10 ( 2013 .01 ) ; A61K 47 /44 ( 2013 .01 ) ; (GB ) ; Olga Pleguezeulos Mateo , A61K 31 / 19 ( 2013 . 01 ) ; A61K 31 / 202 Bicester (GB ) ; Gregory A . Stoloff , (2013 .01 ) ; A61K 31/ 25 ( 2013 .01 ) ; AIK London (GB ) 31 / 337 ( 2013. 01 ) ; A6IK 31/ 704 ( 2013 .01 ) ( 73 ) Assignee : Infirst Healthcare Limited , London (58 ) Field of Classification Search (GB ) CPC . .. .. A61K 31 /192 ; A61K 31/ 19 USPC .. .. .. 514 / 570 , 571, 557 ( * ) Notice : Subject to any disclaimer, the term of this See application file for complete search history . patent is extended or adjusted under 35 U . S . C . 154 (b ) by 0 days . References Cited This patent is subject to a terminal dis (56 ) claimer . U . S . PATENT DOCUMENTS 3 , 228 ,831 A 1 / 1966 Nicholson et al. (21 ) Appl . No. : 15 / 614 ,592 3 , 800 ,038 A 3 / 1974 Rudel 4 ,571 ,400 A 2 / 1986 Arnold (22 ) Filed : Jun . -
Role of Fatty Acids/Fat Soluble Component from Medicinal Plants Targeting BACE Modulation and Their Role in Onset of AD: an In-Silico Approach
Journal of Graphic Era University Vol. 6, Issue 2, 270-281, 2018 ISSN: 0975-1416 (Print), 2456-4281 (Online) Role of Fatty Acids/Fat Soluble Component from Medicinal Plants Targeting BACE Modulation and Their Role in Onset of AD: An in-silico Approach Prashant Anthwal1, Bipin Kumar Sati1, Madhu Thapliyal2, Devvret Verma1, Navin Kumar1, Ashish Thapliyal*1 1Department of Life Sciences and Biotechnology Graphic Era Deemed to be University, Dehradun, India 2Department of Zoology Government Degree College, Raipur, Dehradun *Corresponding author: [email protected] (Received May 25, 2017; Accepted August 10, 2018) Abstract Fatty acids have been reported in several researches targeting cure and treatment of Alzheimer’s disease (AD). Besides having so many contradictory reports about fatty acids related to the issues of human health, there are many evidences that point towards the beneficial effects of PUFAs and essential fatty acids on human health, even in AD. This study investigated the interaction of fatty acids and phyto-constituents for the inhibition of BACE enzyme (mainly responsible and prominent target for amyloid hypothesis) through in-silico approach. Phyto-compounds from Picrorhiza kurroa, Cinnamomum tamala, Curcuma longa, Datura metel, Rheum emodi and Bacopa monnieri, which are well known, were screened. For screening of drug molecules, Lipinski’s rule is usually used. Because of this rule compounds like Bacoside A, Bacoside A3, Bacopaside II, Bacopasaponin C, Baimantuoluoline C, Daturameteline A, Cucurbitacin B, Cucurbitacin D, Cucurbitacin E, Cucurbitacin I, Cucurbitacin F, Cucurbitacin R, Picroside III, Kutkoside, Picroside II are usually excluded from docking/binding studies because of their higher molecular weight as they do now follow the Lipinski’s rules.