Briefing No. 112 September 2014
Total Page:16
File Type:pdf, Size:1020Kb
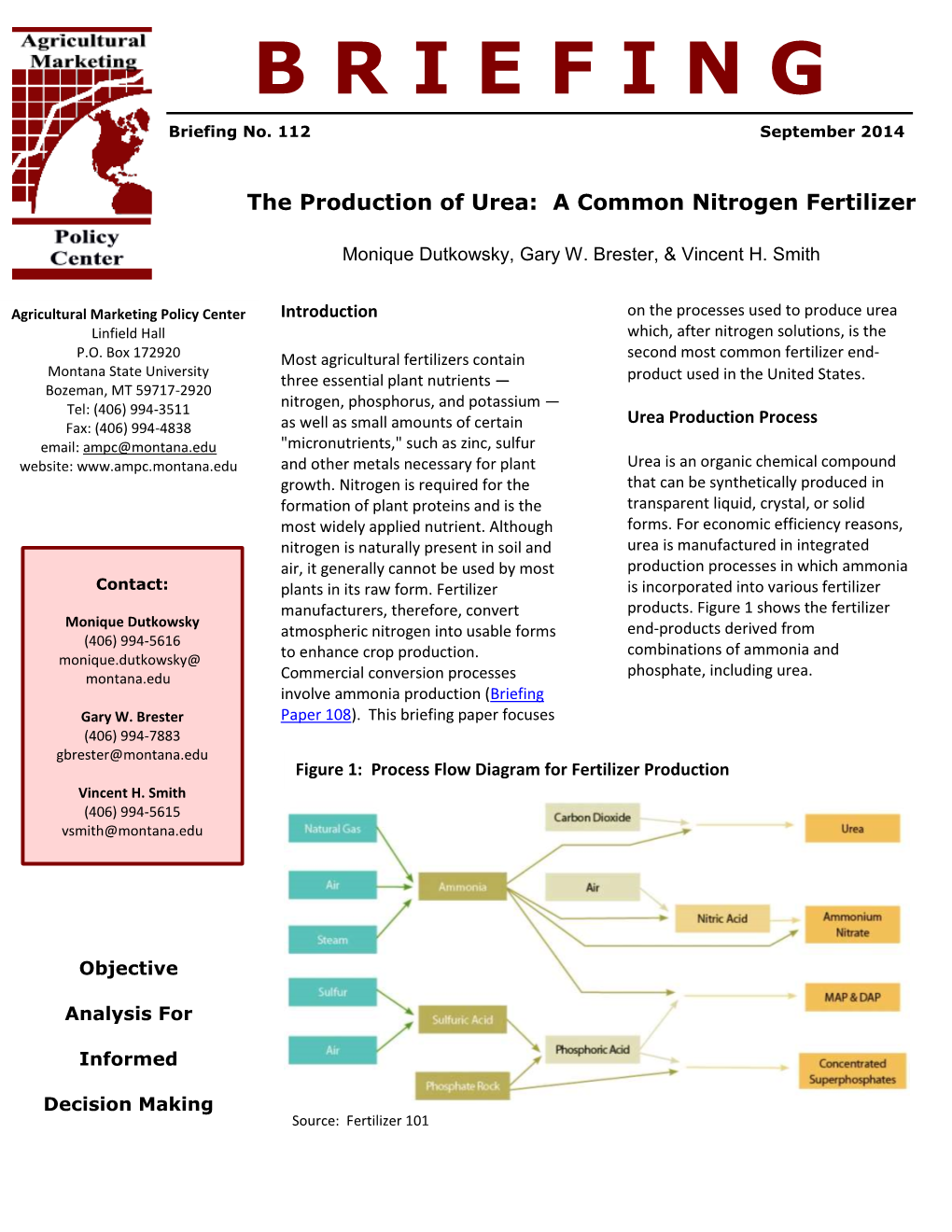
Load more
Recommended publications
-
A Study on Physical Chemistry of Solid a Mmonium Materials for Nox Reduction of Diesel Engine Emissions
A Study on Physical Chemistry of Solid A mmonium Materials for NOx Reduction of Diesel Engine Emissions Cheon Seog (Steve) Yoon and Jong Kook Shin Hannam University, Daejeon, KOREA Hoyeol Lee and Hongsuk Kim Korea Institute of Machinery & Materials, Daejeon, KOREA 2014 DOE CLEERS Workshop University of Michigan, Dearborn, MI, USA 1 Table of Contents • Introduction of Solid SCR System • Ammonium Salts • Chemical Reactions, Decomposition Chemistry • Chemical Kinetic Parameters by TGA, DTA and DSC • Decomposition Rate from Hot Plate Test and Chemical Kinetic Parameters • Simple Reactor with Visible Window • Equilibrium Vapor Pressure Curve for Ammonium Carbonate • Acquisition of Re-solidified Materials from Ammonium Carbonate • Analytical Study of Re-solidified Materials from Ammonium Carbonate by XRD, FT-IR, and EA • Concluding Remarks • Acknowledgement • Reference 2 Solid SCR System • NOx purification technology by using NH3, which is generated from solid ammonium. • Ammonium carbonate, (NH4)2CO3 , is solid at room temperature, and it decomposes into NH3, H2O & CO2 above temperature of 60℃. 3 Material Properties of Ammonium Salts Solid urea Ammonium carbonate Ammonium cabarmate Molecular formula (NH2)2CO (NH4)2CO3 NH2COONH4 Molecular weight 60.07 96.09 78.07 3 Density, g/cm 1.33 1.5 1.6 Mols NH3 per Mol 2 2 2 Mols NH3 per kg 33.3 20.8 25.6 Decomposition temp., ℃ 140 58 60 NH2CONH2↔ NH3+HNCO Reaction mechanism (NH4)2CO3↔2NH3+CO2+H2O NH4COONH2 ↔ 2NH3 + CO2 HNCO +H2O ↔ NH3 + CO2 Cost cheap cheap moderate * HNCO: Isocyanic Acid [ref] G. Fulks, -
1 Abietic Acid R Abrasive Silica for Polishing DR Acenaphthene M (LC
1 abietic acid R abrasive silica for polishing DR acenaphthene M (LC) acenaphthene quinone R acenaphthylene R acetal (see 1,1-diethoxyethane) acetaldehyde M (FC) acetaldehyde-d (CH3CDO) R acetaldehyde dimethyl acetal CH acetaldoxime R acetamide M (LC) acetamidinium chloride R acetamidoacrylic acid 2- NB acetamidobenzaldehyde p- R acetamidobenzenesulfonyl chloride 4- R acetamidodeoxythioglucopyranose triacetate 2- -2- -1- -β-D- 3,4,6- AB acetamidomethylthiazole 2- -4- PB acetanilide M (LC) acetazolamide R acetdimethylamide see dimethylacetamide, N,N- acethydrazide R acetic acid M (solv) acetic anhydride M (FC) acetmethylamide see methylacetamide, N- acetoacetamide R acetoacetanilide R acetoacetic acid, lithium salt R acetobromoglucose -α-D- NB acetohydroxamic acid R acetoin R acetol (hydroxyacetone) R acetonaphthalide (α)R acetone M (solv) acetone ,A.R. M (solv) acetone-d6 RM acetone cyanohydrin R acetonedicarboxylic acid ,dimethyl ester R acetonedicarboxylic acid -1,3- R acetone dimethyl acetal see dimethoxypropane 2,2- acetonitrile M (solv) acetonitrile-d3 RM acetonylacetone see hexanedione 2,5- acetonylbenzylhydroxycoumarin (3-(α- -4- R acetophenone M (LC) acetophenone oxime R acetophenone trimethylsilyl enol ether see phenyltrimethylsilyl... acetoxyacetone (oxopropyl acetate 2-) R acetoxybenzoic acid 4- DS acetoxynaphthoic acid 6- -2- R 2 acetylacetaldehyde dimethylacetal R acetylacetone (pentanedione -2,4-) M (C) acetylbenzonitrile p- R acetylbiphenyl 4- see phenylacetophenone, p- acetyl bromide M (FC) acetylbromothiophene 2- -5- -
Environmental Protection Agency § 117.3
Environmental Protection Agency § 117.3 (4) Applicability date. This paragraph TABLE 117.3—REPORTABLE QUANTITIES OF (i) is applicable beginning on February HAZARDOUS SUBSTANCES DESIGNATED PUR- 6, 2020. SUANT TO SECTION 311 OF THE CLEAN (j) Process waste water means any WATER ACT—Continued water which, during manufacturing or Cat- RQ in pounds processing, comes into direct contact Material egory (kilograms) with or results from the production or use of any raw material, intermediate Ammonium benzoate ...................... D ...... 5,000 (2,270) Ammonium bicarbonate .................. D ...... 5,000 (2,270) product, finished product, byproduct, Ammonium bichromate ................... A ....... 10 (4.54) or waste product. Ammonium bifluoride ...................... B ....... 100 (45.4) Ammonium bisulfite ......................... D ...... 5,000 (2,270) [44 FR 50776, Aug. 29, 1979, as amended at 58 Ammonium carbamate .................... D ...... 5,000 (2,270) FR 45039, Aug. 25, 1993; 65 FR 30904, May 15, Ammonium carbonate ..................... D ...... 5,000 (2,270) 2000; 80 FR 37112, June 29, 2015; 83 FR 5208, Ammonium chloride ........................ D ...... 5,000 (2,270) Feb. 6, 2018] Ammonium chromate ...................... A ....... 10 (4.54) Ammonium citrate dibasic ............... D ...... 5,000 (2,270) Ammonium fluoborate ..................... D ...... 5,000 (2,270) § 117.2 Abbreviations. Ammonium fluoride ......................... B ....... 100 (45.4) NPDES equals National Pollutant Ammonium hydroxide ..................... C -
United States Patent (19) 11 Patent Number: 5,788,915 Blount (45) Date of Patent: Aug
IIIUSOO5788915A United States Patent (19) 11 Patent Number: 5,788,915 Blount (45) Date of Patent: Aug. 4, 1998 54 FLAME RETARDANT COMPOSITIONS 57 ABSTRACT UTILIZING PARTIALLY HYDROLYZED AMNO CONDENSATON COMPOUNDS Flame retardant compositions of this invention are produced by incorporating a partially index (LOI) hydrolyzed amino 76 Inventor: David H. Blount, 6728 Del Cerro condensation composition in a more flammable organic Blvd., San Diego, Calif. 92120 material. The partially hydrolyzed amino condensation com pounds are produced by heating urea or heating urea with (21) Appl. No.: 801,776 other nitrogen containing compounds that will condensate with or react with isocyanic acid and/or cyanic acid thereby 22 Filed: Feb. 14, 1997 producing an amino condensation compound which is then Related U.S. Application Data partially hydrolysis is done by reacting it with a limited amount of water. The partially hydrolyzed amino conden 62) Division of Ser. No. 723,779, Sep. 30, 1996. sation compounds may be used alone or may be mixed with or reacted with carbonization auxiliaries, aldehydes and (51) Int. Cl. ........................ C09K 21A00; C08G 12/12 fillers to produce a partially hydrolyzed amino condensation 52 U.S. Cl. ........................... 252/609; 528/259; 252/601 composition which is incorporated in more flammable 58) Field of Search ..................................... 252/609, 601: organic compositions such as polyurethanes, polyester 528/259 resins. epoxy resins, vinyl resins and other resins. The partially hydrolyzed amino condensation salts of 56 References Cited phosphorus, boron or sulfur containing compounds and the U.S. PATENT DOCUMENTS partially hydrolyzed amino condensation-aldehyde resins 3,900,665 8/1975 Weil ....................................... -
Ammonium Carbonate. Drogen in Chlorine Is Dissolved in Water and Then Reacted with Gaseous Ammo- (A) Ammonium Carbonate ((NH4)2CO3, Nia
Food and Drug Administration, HHS § 184.1138 (1) The ingredient is used as a dough (d) Prior sanctions for this ingredient strengthener as defined in § 170.3(o)(6) different from the uses established in of this chapter; a leavening agent as this section do not exist or have been defined in § 170.3(o)(17) of this chapter; waived. a pH control agent as defined in § 170.3(o)(23) of this chapter; and a [48 FR 52439, Nov. 18, 1983] texturizer as defined in § 170.3(o)(32) of § 184.1138 Ammonium chloride. this chapter. (2) The ingredient is used in food at (a) Ammonium chloride (NH4Cl, CAS levels not to exceed current good man- Reg. No. 12125–02–9) is produced by the ufacturing practice. reaction of sodium chloride and an am- (d) Prior sanctions for this ingredient monium salt in solution. The less solu- different from the uses established in ble sodium salt separates out at ele- this section do not exist or have been vated temperatures, and ammonium waived. chloride is recovered from the filtrate on cooling. Alternatively, hydrogen [48 FR 52439, Nov. 18, 1983] chloride formed by the burning of hy- § 184.1137 Ammonium carbonate. drogen in chlorine is dissolved in water and then reacted with gaseous ammo- (a) Ammonium carbonate ((NH4)2CO3, nia. Ammonium chloride is crystallized CAS Reg. No. 8000–73–5) is a mixture of from the solution. ammonium bicarbonate (NH4HCO3) and (b) The ingredient meets the speci- ammonium carbamate (NH2COONH4). fications of the Food Chemicals Codex, It is prepared by the sublimation of a 3d Ed. -
Ammonium Carbamate Acm
AMMONIUM CARBAMATE ACM CAUTIONARY RESPONSE INFORMATION 4. FIRE HAZARDS 7. SHIPPING INFORMATION 4.1 Flash Point: 7.1 Grades of Purity: Currently not available Common Synonyms Solid crystalline White Ammonia odor Not flammable 7.2 Storage Temperature: Cool Ammonium aminoformate powder 4.2 Flammable Limits in Air: Currently not 7.3 Inert Atmosphere: Currently not available Anhydride of ammonium available carbonate 7.4 Venting: Currently not available Carbamic acid, ammonium salt Mixes with water. 4.3 Fire Extinguishing Agents: Carbon dioxide, dry chemical, or water spray 7.5 IMO Pollution Category: Currently not available 4.4 Fire Extinguishing Agents Not to Be 7.6 Ship Type: Currently not available Wear goggles, self-contained breathing apparatus, and rubber gloves. Keep people away. Used: Currently not available Stop discharge if possible. Call fire department. 7.7 Barge Hull Type: Currently not available Isolate and remove discharged material. 4.5 Special Hazards of Combustion Products: Currently not available Notify local health and pollution control agencies. 8. HAZARD CLASSIFICATIONS Protect water intakes. 4.6 Behavior in Fire: Moderate fire and explosion hazards when exposed to heat 8.1 49 CFR Category: Not listed Fire COMBUSTIBLE. or flame 8.2 49 CFR Class: Not pertinent POISONOUS GAS MAY BE PRODUCED IN FIRE OR WHEN HEATED. 4.7 Auto Ignition Temperature: Not pertinent 8.3 49 CFR Package Group: Not listed. Wear self-contained breathing apparatus, goggles, rubber gloves, and normal 4.8 Electrical Hazards: Not pertinent protective gear. 8.4 Marine Pollutant: No 4.9 Burning Rate: Not pertinent Extinguish with CO2 dry chemical, or water spray. -
PRODUCTION of UREA and UREA AMMONIUM NITRATE
Best Available Techniques for Pollution Prevention and Control in the European Fertilizer Industry Booklet No. 5 of 8: PRODUCTION OF UREA and UREA AMMONIUM NITRATE 2000 EFMA European Fertilizer Manufacturers’ Association Ave. E van Nieuwenhuyse 4 B-1160 Brussels Belgium Best Available Techniques for Pollution Prevention and Control in the European Fertilizer Industry Booklet No. 5 of 8: PRODUCTION OF UREA and UREA AMMONIUM NITRATE Copyright 2000 – EFMA This publication has been prepared by member companies of the European Fertilizer Manufacturers’ Association (EFMA). Neither the Association nor any individual member company can accept liability for accident or loss attributable to the use of the information given in this Booklet. Booklet No. 1 No. 5 Hydrocarbon feed Urea Water Ammonia Air UAN No. 2 No. 6 Water AN Nitric Acid Air Calcium carbonate CAN No. 3 No. 7 Water NPK Sulphuric Acid Phosphate rock (nitrophosphate Sulphur route) K, Mg, S, micronutrients No. 4 No. 8 NPK Water Phosphoric (mixed acid Phosphate Acid route) rock K, Mg, S, micronutrients Phosphate rock 2 CONTENTS PREFACE 5 DEFINITIONS 7 1. INTRODUCTION 8 2. DESCRIPTION OF UREA PRODUCTION PROCESSES 8 2.1 Urea Plant Installations in Europe 12 2.2 Description of BAT Production Processes 12 2.3 Process Water Sources and Quantities 13 2.4 Prilling and Granulation 14 2.5 Feasible and Available Emission Abatement Techniques 16 2.6 Description of Process Water BAT Treatment Systems 16 2.7 Prill Tower Emissions 18 2.8 Granulator Emissions 20 3. DESCRIPTION OF STORAGE AND TRANSFER EQUIPMENT 20 3.1 Ammonia 20 3.2 Carbon Dioxide 21 3.3 Formaldehyde 21 4. -
Ammonium Carbamate Hazard Summary Identification
Common Name: AMMONIUM CARBAMATE CAS Number: 1111-78-0 RTK Substance number: 0091 DOT Number: NA 9083 Date: January 1996 Revision: March 2002 ------------------------------------------------------------------------- ------------------------------------------------------------------------- HAZARD SUMMARY WORKPLACE EXPOSURE LIMITS * Ammonium Carbamate can affect you when breathed in. The following exposure limits are for Ammonia: * Exposure can irritate the skin and eyes causing redness and tearing. OSHA: The legal airborne permissible exposure limit * Breathing Ammonium Carbamate can irritate the nose, (PEL) is 50 ppm averaged over an 8-hour throat and lungs causing coughing and/or shortness of workshift. breath. NIOSH: The recommended airborne exposure limit is IDENTIFICATION 25 ppm averaged over a 10-hour workshift and Ammonium Carbamate is a white crystalline (sand-like) 35 ppm, not to be exceeded during any 15 minute powder. It is used as a fertilizer and ammoniating agent. work period. REASON FOR CITATION ACGIH: The recommended airborne exposure limit is 25 ppm averaged over an 8-hour workshift and * Ammonium Carbamate is on the Hazardous Substance 35 ppm as a STEL (short-term exposure limit). List because it is cited by DOT and EPA. * Definitions are provided on page 5. WAYS OF REDUCING EXPOSURE HOW TO DETERMINE IF YOU ARE BEING * Where possible, enclose operations and use local exhaust ventilation at the site of chemical release. If local exhaust EXPOSED ventilation or enclosure is not used, respirators should be The New Jersey Right to Know Act requires most employers worn. to label chemicals in the workplace and requires public * Wear protective work clothing. employers to provide their employees with information and * Wash thoroughly immediately after exposure to training concerning chemical hazards and controls. -
List of Lists
United States Office of Solid Waste EPA 550-B-10-001 Environmental Protection and Emergency Response May 2010 Agency www.epa.gov/emergencies LIST OF LISTS Consolidated List of Chemicals Subject to the Emergency Planning and Community Right- To-Know Act (EPCRA), Comprehensive Environmental Response, Compensation and Liability Act (CERCLA) and Section 112(r) of the Clean Air Act • EPCRA Section 302 Extremely Hazardous Substances • CERCLA Hazardous Substances • EPCRA Section 313 Toxic Chemicals • CAA 112(r) Regulated Chemicals For Accidental Release Prevention Office of Emergency Management This page intentionally left blank. TABLE OF CONTENTS Page Introduction................................................................................................................................................ i List of Lists – Conslidated List of Chemicals (by CAS #) Subject to the Emergency Planning and Community Right-to-Know Act (EPCRA), Comprehensive Environmental Response, Compensation and Liability Act (CERCLA) and Section 112(r) of the Clean Air Act ................................................. 1 Appendix A: Alphabetical Listing of Consolidated List ..................................................................... A-1 Appendix B: Radionuclides Listed Under CERCLA .......................................................................... B-1 Appendix C: RCRA Waste Streams and Unlisted Hazardous Wastes................................................ C-1 This page intentionally left blank. LIST OF LISTS Consolidated List of Chemicals -
Chemical Names and CAS Numbers Final
Chemical Abstract Chemical Formula Chemical Name Service (CAS) Number C3H8O 1‐propanol C4H7BrO2 2‐bromobutyric acid 80‐58‐0 GeH3COOH 2‐germaacetic acid C4H10 2‐methylpropane 75‐28‐5 C3H8O 2‐propanol 67‐63‐0 C6H10O3 4‐acetylbutyric acid 448671 C4H7BrO2 4‐bromobutyric acid 2623‐87‐2 CH3CHO acetaldehyde CH3CONH2 acetamide C8H9NO2 acetaminophen 103‐90‐2 − C2H3O2 acetate ion − CH3COO acetate ion C2H4O2 acetic acid 64‐19‐7 CH3COOH acetic acid (CH3)2CO acetone CH3COCl acetyl chloride C2H2 acetylene 74‐86‐2 HCCH acetylene C9H8O4 acetylsalicylic acid 50‐78‐2 H2C(CH)CN acrylonitrile C3H7NO2 Ala C3H7NO2 alanine 56‐41‐7 NaAlSi3O3 albite AlSb aluminium antimonide 25152‐52‐7 AlAs aluminium arsenide 22831‐42‐1 AlBO2 aluminium borate 61279‐70‐7 AlBO aluminium boron oxide 12041‐48‐4 AlBr3 aluminium bromide 7727‐15‐3 AlBr3•6H2O aluminium bromide hexahydrate 2149397 AlCl4Cs aluminium caesium tetrachloride 17992‐03‐9 AlCl3 aluminium chloride (anhydrous) 7446‐70‐0 AlCl3•6H2O aluminium chloride hexahydrate 7784‐13‐6 AlClO aluminium chloride oxide 13596‐11‐7 AlB2 aluminium diboride 12041‐50‐8 AlF2 aluminium difluoride 13569‐23‐8 AlF2O aluminium difluoride oxide 38344‐66‐0 AlB12 aluminium dodecaboride 12041‐54‐2 Al2F6 aluminium fluoride 17949‐86‐9 AlF3 aluminium fluoride 7784‐18‐1 Al(CHO2)3 aluminium formate 7360‐53‐4 1 of 75 Chemical Abstract Chemical Formula Chemical Name Service (CAS) Number Al(OH)3 aluminium hydroxide 21645‐51‐2 Al2I6 aluminium iodide 18898‐35‐6 AlI3 aluminium iodide 7784‐23‐8 AlBr aluminium monobromide 22359‐97‐3 AlCl aluminium monochloride -
Control and Pollution Prevention Options for Ammonia Emissions
EPA-456/R-95-002 Control and Pollution Prevention Options for Ammonia Emissions CONTROL TECHNOLOGY CENTER Sponsored by Information Transfer and Program Integration Division Office of Air Quality Planning and Standards U.S. Environmental Protection Agency Research Triangle Park, NC 27711 Air and Energy Engineering Laboratory Office of Research and Development U.S. Environmental Protection Agency Research Triangle Park, NC 27711 April 1995 EPA-456/R-95-002 April 1995 Control and Pollution Prevention Options for Ammonia Emissions Prepared by Jennifer Phillips VíGYAN Incorporated 1953 Gallows Road, Suite 320 Vienna, VA 22182-3934 EPA Contract No. 68-D1-0073 Work Assignment No. 3-39 Project Manager Robert J. Blaszczak Information Transfer and Program Integration Division Office of Air Quality Planning and Standards U.S. Environmental Protection Agency Research Triangle Park, NC 27711 Prepared for Control Technology Center U.S. Environmental Protection Agency Research Triangle Park, NC 27711 EPA REVIEW NOTICE This report has been reviewed by the Control Technology Center (CTC) established by the Office of Research and Development (ORD) and the Office of Air Quality Planning and Standards (OAQPS) of the U.S. Environmental Protection Agency (EPA), and has been approved for publication. Approval does not signify that the comments necessarily reflect the view and policies of EPA, nor does mention of trade names, organization names, or commercial products constitute endorsement or recommendation for use. This document is available to the public through the National Technical Information Service, Springfield, Virginia, 22161, (800) 553-6847. iv ACKNOWLEDGEMENTS Funding for this project was provided by the Control Technology Center. This report does not necessarily reflect the views of this organization and no official endorsement should be inferred. -
Development of an Analytical Method for Distinguishing
View metadata, citation and similar papers at core.ac.uk brought to you by CORE provided by TopSCHOLAR Western Kentucky University TopSCHOLAR® Masters Theses & Specialist Projects Graduate School 1-1-2004 Development of an Analytical Method for Distinguishing Ammonium Bicarbonate from the Products of an Aqueous Ammonia Co2 Scrubber and the Characterization of Ammonium Bicarbonate Lingyu Meng Western Kentucky University Follow this and additional works at: http://digitalcommons.wku.edu/theses Part of the Environmental Chemistry Commons Recommended Citation Meng, Lingyu, "Development of an Analytical Method for Distinguishing Ammonium Bicarbonate from the Products of an Aqueous Ammonia Co2 Scrubber and the Characterization of Ammonium Bicarbonate" (2004). Masters Theses & Specialist Projects. Paper 243. http://digitalcommons.wku.edu/theses/243 This Thesis is brought to you for free and open access by TopSCHOLAR®. It has been accepted for inclusion in Masters Theses & Specialist Projects by an authorized administrator of TopSCHOLAR®. For more information, please contact [email protected]. DEVELOPMENT OF AN ANALYTICAL METHOD FOR DISTINGUISHING AMMONIUM BICARBONATE FROM THE PRODUCTS OF AN AQUEOUS AMMONIA CO2 SCRUBBER AND THE CHARACTERIZATION OF AMMONIUM BICARBONATE A Thesis Presented to The Faculty of the Department of Chemistry Western Kentucky University Bowling Green, Kentucky In Partial Fulfillment of the Requirements for the Degree Master of Science by Lingyu Meng December, 2004 DEVELOPMENT OF AN ANALYTICAL METHOD FOR DISTINGUISHING AMMONIUM BICARBONATE FROM THE PRODUCTS OF AN AQUEOUS AMMONIA CO2 SCRUBBER AND THE CHARACTERIZATION OF AMMONIUM BICARBONATE Date Recommended 12/15/2004 Dr. Wei-Ping Pan, Director of Thesis Dr. Stuart Burris Dr. M. Thandi Buthelezi Elmer Gray, Dean of the Graduate College, (December 16, 2004) ACKNOWLEDGEMENT I would like to express my deep appreciation to Dr.