Synthesis and Applications of Low Silica Zeolites from Bolivian Clay and Diatomaceous Earth
Total Page:16
File Type:pdf, Size:1020Kb
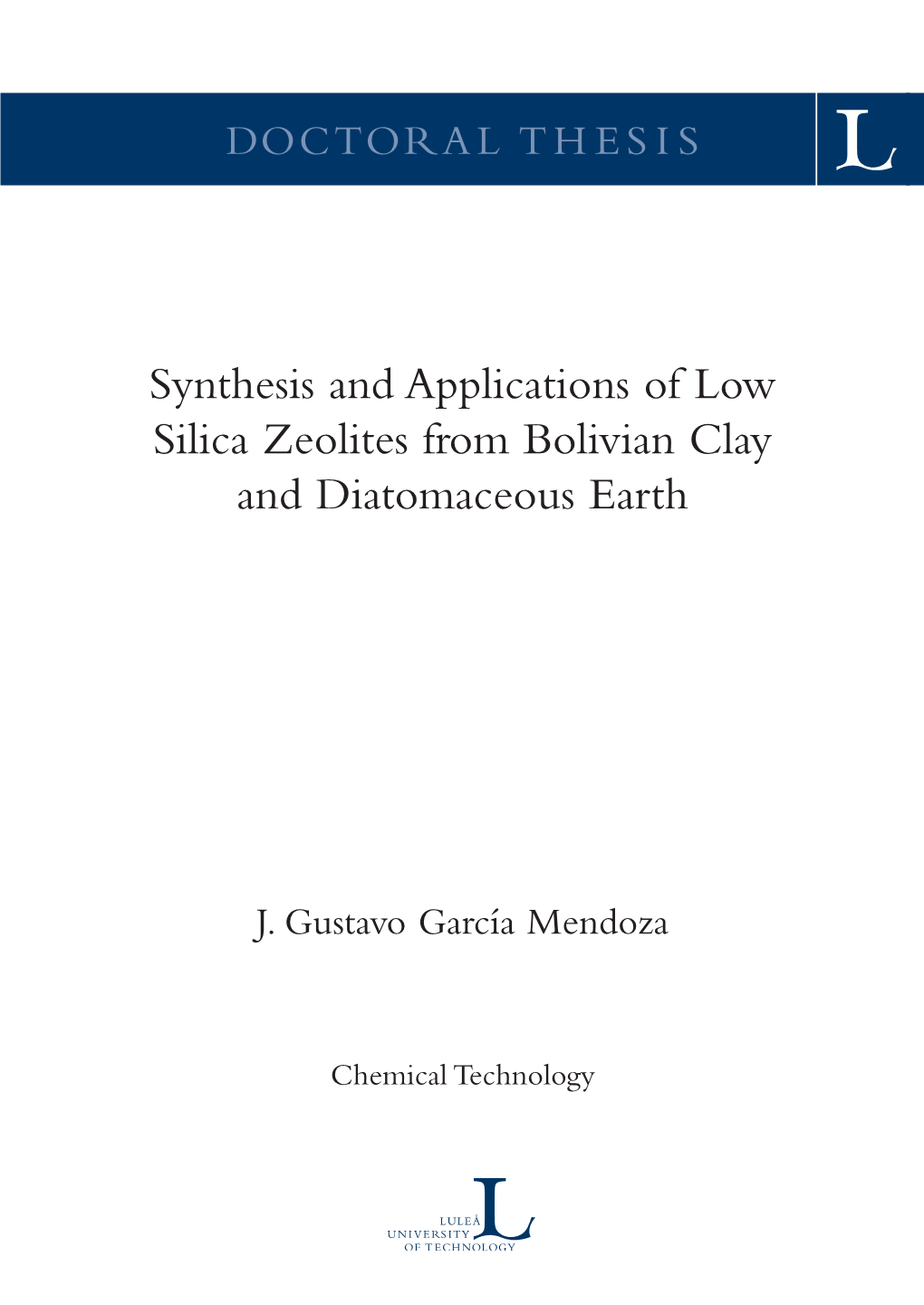
Load more
Recommended publications
-
Marinellite, a New Feldspathoid of the Cancrinite-Sodalite Group
Eur. J. Mineral. 2003, 15, 1019–1027 Marinellite, a new feldspathoid of the cancrinite-sodalite group ELENA BONACCORSI* and PAOLO ORLANDI Dipartimento di Scienze della Terra, Universita` di Pisa, Via S. Maria 53, I-56126 Pisa, Italy * Corresponding author, e-mail: [email protected] Abstract: Marinellite, [(Na,K)42Ca6](Si36Al36O144)(SO4)8Cl2·6H2O, cell parameters a = 12.880(2) Å, c = 31.761(6) Å, is a new feldspathoid belonging to the cancrinite-sodalite group. The crystal structure of a twinned crystal was preliminary refined in space group P31c, but space group P62c could also be possible. It was found near Sacrofano, Latium, Italy, associated with giuseppettite, sanidine, nepheline, haüyne, biotite, and kalsilite. It is anhedral, transparent, colourless with vitreous lustre, white streak and Mohs’ hardness of 5.5. The mineral does not fluoresce, is brittle, has conchoidal fracture, and presents poor cleavage on {001}. Dmeas is 3 3 2.405(5) g/cm , Dcalc is 2.40 g/cm . Optically, marinellite is uniaxial positive, non-pleochroic, = 1.495(1), = 1.497(1). The strongest five reflections in the X-ray powder diffraction pattern are [d in Å (I) (hkl)]: 3.725 (100) (214), 3.513 (80) (215), 4.20 (42) (210), 3.089 (40) (217), 2.150 (40) (330). The electron microprobe analysis gives K2O 7.94, Na2O 14.95, CaO 5.14, Al2O3 27.80, SiO2 32.73, SO3 9.84, Cl 0.87, (H2O 0.93), sum 100.20 wt %, less O = Cl 0.20, (total 100.00 wt %); H2O calculated by difference. The corresponding empirical formula, based on 72 (Si + Al), is (Na31.86K11.13Ca6.06) =49.05(Si35.98Al36.02)S=72O144.60(SO4)8.12Cl1.62·3.41H2O. -
Action of Ammonium Chloride Upon Silicates
Bulletin No. 207 Series E, Chemistry and Physics, 36 DEPARTMENT OF TEiE INTERIOR UNITED STATES GEOLOGICAL SURVEY CHARLES D. WALCOTT, DIRECTOR THE ACTION OF AMMONIUM CHLORIDE UPON SILICATES BY AND GKKOKG-IE Srj::ir, WASHINGTON GOVERNMEN.T PllINTING OFFICE 1902 CONTENTS. Page. Introductory statement......--..-..---.--.------.--.-..--.-.-----------. 7 Analcite-.....-.-.-.--.-.....-.--.'--------....--.-.--..._.-.---.-...---.--. 8 Leucite .....................'.................-....................^-..... 16 The constitution of analcite and leucite.........-..--.-..--...--.---------. 17 Pollucite---. ............................................................ 21 Natrolite--------------------------..-..-----------------.------ --------- 22 Scolecite ................,.:............-.....-.................--.--.... 24 Prehnite .....--.-............--.------------------------------ --------- 25 The trisilicic acids-.--.-.--..---..........-._-----...-.........-...----.- 26 Stilbite.............-..................-....-.-.-----...--.---.......... 29 Henlandite .......... .......................---.-..-.-..-...-----.--..--.. 81 Chabazite............................................................... 32 Thoinsonite...-.-.-..-...._.................---...-.-.-.----..-----..--.. 34 Lanmontite -.-.------.-..-------------.-..-.-..-.-------.-.-----........ 35 Pectolite ......:......... ......................................'.......;.., 36 Wollastonite ....'............................ ................:........... 39 Apophyllite. _.--._..._-....__.....:......___-------------....----..-...._ -
26 May 2021 Aperto
AperTO - Archivio Istituzionale Open Access dell'Università di Torino The crystal structure of sacrofanite, the 74 Å phase of the cancrinite–sodalite supergroup This is the author's manuscript Original Citation: Availability: This version is available http://hdl.handle.net/2318/90838 since Published version: DOI:10.1016/j.micromeso.2011.06.033 Terms of use: Open Access Anyone can freely access the full text of works made available as "Open Access". Works made available under a Creative Commons license can be used according to the terms and conditions of said license. Use of all other works requires consent of the right holder (author or publisher) if not exempted from copyright protection by the applicable law. (Article begins on next page) 05 October 2021 This Accepted Author Manuscript (AAM) is copyrighted and published by Elsevier. It is posted here by agreement between Elsevier and the University of Turin. Changes resulting from the publishing process - such as editing, corrections, structural formatting, and other quality control mechanisms - may not be reflected in this version of the text. The definitive version of the text was subsequently published in MICROPOROUS AND MESOPOROUS MATERIALS, 147, 2012, 10.1016/j.micromeso.2011.06.033. You may download, copy and otherwise use the AAM for non-commercial purposes provided that your license is limited by the following restrictions: (1) You may use this AAM for non-commercial purposes only under the terms of the CC-BY-NC-ND license. (2) The integrity of the work and identification of the author, copyright owner, and publisher must be preserved in any copy. -
New Minerals Approved Bythe Ima Commission on New
NEW MINERALS APPROVED BY THE IMA COMMISSION ON NEW MINERALS AND MINERAL NAMES ALLABOGDANITE, (Fe,Ni)l Allabogdanite, a mineral dimorphous with barringerite, was discovered in the Onello iron meteorite (Ni-rich ataxite) found in 1997 in the alluvium of the Bol'shoy Dolguchan River, a tributary of the Onello River, Aldan River basin, South Yakutia (Republic of Sakha- Yakutia), Russia. The mineral occurs as light straw-yellow, with strong metallic luster, lamellar crystals up to 0.0 I x 0.1 x 0.4 rnrn, typically twinned, in plessite. Associated minerals are nickel phosphide, schreibersite, awaruite and graphite (Britvin e.a., 2002b). Name: in honour of Alia Nikolaevna BOG DAN OVA (1947-2004), Russian crys- tallographer, for her contribution to the study of new minerals; Geological Institute of Kola Science Center of Russian Academy of Sciences, Apatity. fMA No.: 2000-038. TS: PU 1/18632. ALLOCHALCOSELITE, Cu+Cu~+PbOZ(Se03)P5 Allochalcoselite was found in the fumarole products of the Second cinder cone, Northern Breakthrought of the Tolbachik Main Fracture Eruption (1975-1976), Tolbachik Volcano, Kamchatka, Russia. It occurs as transparent dark brown pris- matic crystals up to 0.1 mm long. Associated minerals are cotunnite, sofiite, ilin- skite, georgbokiite and burn site (Vergasova e.a., 2005). Name: for the chemical composition: presence of selenium and different oxidation states of copper, from the Greek aA.Ao~(different) and xaAxo~ (copper). fMA No.: 2004-025. TS: no reliable information. ALSAKHAROVITE-Zn, NaSrKZn(Ti,Nb)JSi401ZJz(0,OH)4·7HzO photo 1 Labuntsovite group Alsakharovite-Zn was discovered in the Pegmatite #45, Lepkhe-Nel'm MI. -
Nucleation and Growth Process of Sodalite and Cancrinite from Kaolinite-Rich Clay Under Low-Temperature Hydrothermal Conditions
Materials Research. 2013; 16(2): 424-438 © 2013 DOI: 10.1590/S1516-14392013005000010 Nucleation and Growth Process of Sodalite and Cancrinite from Kaolinite-rich Clay under Low-temperature Hydrothermal Conditions Carlos Alberto Ríos Reyesa*, Craig Williamsb, Oscar Mauricio Castellanos Alarcónc aEscuela de Geología, Universidad Industrial de Santander, Carrera 27 Calle 9, Ciudad Universitaria, Bucaramanga, Colombia bSchool of Applied Sciences, University of Wolverhampton, Wulfruna Street, Wolverhampton WV1 1SB, England cPrograma de Geología, Universidad de Pamplona, Ciudad Universitaria, Pamplona, Colombia Received: October 28, 2011; Revised: August 24, 2012 The synthesis of low-silica zeotypes by hydrothermal transformation of kaolinite-rich clay and the nucleation and growth processes of sodalite and cancrinite in the system Na2O–Al2O3–SiO2–H2O at 100 °C were investigated. The synthesis products were characterized by X-ray powder diffraction (XRPD), scanning electron microscopy (SEM), Fourier transform infrared spectroscopy (FT-IR), 29Si and 27Al Magic Angle Spinning Nuclear Magnetic Resonance (MAS-NMR) and thermogravimetric analysis (TGA). Our data show that the sequence of the transformation of phases is: Poorly crystalline aluminosilicate → zeolite LTA → sodalite → sodalite + cancrinite → cancrinite. Synthesized materials appeared stable thermodynamically under the experimental conditions, with zeolite LTA (a metastable phase) occurring as a minor phase, compared with the presence of sodalite and cancrinite. Keywords: synthesis, low-silica, hydrothermal, kaolinite, transformation 1. Introduction The Bayer process is the principal industrial means positively charged species to neutralise them3. Cations can of refining bauxite to produce alumina (Al2O3), which enter these porous materials to balance the charge of their must be purified before it can be refined to aluminium structural frameworks6. -
High-Pressure Study of a Natural Cancrinite
American Mineralogist, Volume 97, pages 872–882, 2012 High-pressure study of a natural cancrinite PAOLO LOTTI,1 G. DIEGO GATTA,1,2,* NICOLA ROTIROTI,1,2 AND FERNANDO CÁMARA3 1Dipartimento di Scienze della Terra, Università degli Studi di Milano, Via Botticelli 23, 20133 Milano, Italy 2CNR, Istituto per la Dinamica dei Processi Ambientali, Via M. Bianco 9, 20131 Milano, Italy 3Dipartimento di Scienze della Terra, Università degli Studi di Torino, Via Valperga Caluso 35, 10125 Torino, Italy ABSTRACT The high-pressure elastic behavior and the P-induced structure evolution of a natural cancrinite from Cameroun {Na6.59Ca0.93[Si6Al6O24](CO3)1.04F0.41·2H2O, a = 12.5976(6) Å, c = 5 .1168(2) Å, space group: P63} were investigated by in situ single-crystal X-ray diffraction under hydrostatic conditions up to 6.63(2) GPa with a diamond-anvil cell. The P-V data were fitted with an isothermal Birch-Murnaghan type equation of state (BM EoS) truncated to the third order. Weighted fit (by the 3 uncertainty in P and V) gave the following elastic parameters: V0 = 702.0(7) Å , KV0 = 51(2) GPa, and KV´ = 2.9(4). A linearized BM EoS was used to fit the a-P and c-P data, giving the following refined parameters: a0 = 12.593(5) Å, Ka0 = 64(4) GPa, Ka´ = 4.5(9), for the a-axis, and c0 = 5.112(3) Å, Kc0 = 36(1) GPa, K´c = 1.9(3) for the c-axis (elastic anisotropy: Ka0:Kc0 = 1.78:1). A subtle change of the elastic behavior appears to occur at P > 4.62 GPa, and so the elastic behavior was also described on the basis of BM EOS valid between 0.0001–4.62 and 5.00–6.63 GPa, respectively. -
Crystal Chemistry of Cancrinite-Group Minerals with an Ab-Type Framework: a Review and New Data
1151 The Canadian Mineralogist Vol. 49, pp. 1151-1164 (2011) DOI : 10.3749/canmin.49.5.1151 CRYSTAL CHEMISTRY OF CANCRINITE-GROUP MINERALS WITH AN AB-TYPE FRAMEWORK: A REVIEW AND NEW DATA. II. IR SPECTROSCOPY AND ITS CRYSTAL-CHEMICAL IMPLICATIONS NIKITA V. CHUKANOV§ Institute of Problems of Chemical Physics, 142432 Chernogolovka, Moscow Oblast, Russia IGOR V. PEKOV, LYUDMILA V. OLYSYCH, NATALIA V. ZUBKOVA AND MARINA F. VIGASINA Faculty of Geology, Moscow State University, Leninskie Gory, 119992 Moscow, Russia ABSTRACT We present a comparative analysis of powder infrared spectra of cancrinite-group minerals with the simplest framework, of AB type, from the viewpoint of crystal-chemical characteristics of extra-framework components. We provide IR spectra for typical samples of cancrinite, cancrisilite, kyanoxalite, hydroxycancrinite, depmeierite, vishnevite, pitiglianoite, balliranoite, davyne and quadridavyne, as well as the most unusual varieties of cancrinite-subgroup minerals (Ca-deficient cancrinite, H2O-free cancrinite, intermediate members of the series cancrinite – hydroxycancrinite, cancrinite–cancrisilite, cancrinite– kyanoxalite, K-rich vishnevite, S2-bearing balliranoite). Samples with solved crystal structures are used as reference patterns. Empirical trends and relationships between some parameters of IR spectra, compositional characteristics and unit-cell dimensions 2– are obtained. The effect of Ca content on stretching vibrations of CO3 is explained in the context of the cluster approach. The existence of a hydrous variety of quadridavyne is demonstrated. Keywords: cancrinite, cancrisilite, kyanoxalite, hydroxycancrinite, depmeierite, vishnevite, pitiglianoite, balliranoite, davyne, quadridavyne, cancrinite group, infrared spectrum, crystal chemistry. SOMMAIRE Nous présentons une analyse comparative des spectres infrarouges obtenus à partir de poudres de minéraux du groupe de la cancrinite ayant la charpente la plus simple, de type AB, du point de vue des caractéristiques cristallochimiques des composantes externes à la charpente. -
Archivio Istituzionale Open Access Dell'università Di Torino
AperTO - Archivio Istituzionale Open Access dell'Università di Torino Thermoelastic behavior and dehydration process of cancrinite This is the author's manuscript Original Citation: Availability: This version is available http://hdl.handle.net/2318/142918 since Published version: DOI:10.1007/s00269-014-0656-2 Terms of use: Open Access Anyone can freely access the full text of works made available as "Open Access". Works made available under a Creative Commons license can be used according to the terms and conditions of said license. Use of all other works requires consent of the right holder (author or publisher) if not exempted from copyright protection by the applicable law. (Article begins on next page) 06 October 2021 This is an author version of the contribution published on: Questa è la versione dell’autore dell’opera: Physics and Chemistry of Minerals, 41, 5, 2014, http://dx.doi.org/10.1007/s00269‐ 0114‐0656‐2 ] The definitive version is available at: La versione definnitiva è disponibile alla URL: linkk.springer.com Revision_1 THERMOELASTIC BEHAVIOR AND DEHYDRATION PROCESS OF CANCRINITE Running title: HT behavior of cancrinite Abstract Introduction Experimental methods - Sample preparation - Calibration of the furnace - Unit-cell parameters and intensity data collections - Thermal Equation of State - Structure refinements Results and discussion - Unit-cell parameters evolution with T - High-temperature structural evolution and the effects of the dehydration process - Comparison with previous studies Acknowledgements References Figures/Tables Corresponding author: G. Diego GATTA Dipartimento di Scienza della Terra Universita' degli Studi di Milano Via Botticelli, 23 I-20133 Milano, Italy Tel. +39 02 503 15607 Fax +39 02 503 15597 E-Mail: [email protected] Operating system: Windows XP THERMOELASTIC BEHAVIOR AND DEHYDRATION PROCESS OF CANCRINITE G.D. -
Alphabetical List
LIST L - MINERALS - ALPHABETICAL LIST Specific mineral Group name Specific mineral Group name acanthite sulfides asbolite oxides accessory minerals astrophyllite chain silicates actinolite clinoamphibole atacamite chlorides adamite arsenates augite clinopyroxene adularia alkali feldspar austinite arsenates aegirine clinopyroxene autunite phosphates aegirine-augite clinopyroxene awaruite alloys aenigmatite aenigmatite group axinite group sorosilicates aeschynite niobates azurite carbonates agate silica minerals babingtonite rhodonite group aikinite sulfides baddeleyite oxides akaganeite oxides barbosalite phosphates akermanite melilite group barite sulfates alabandite sulfides barium feldspar feldspar group alabaster barium silicates silicates albite plagioclase barylite sorosilicates alexandrite oxides bassanite sulfates allanite epidote group bastnaesite carbonates and fluorides alloclasite sulfides bavenite chain silicates allophane clay minerals bayerite oxides almandine garnet group beidellite clay minerals alpha quartz silica minerals beraunite phosphates alstonite carbonates berndtite sulfides altaite tellurides berryite sulfosalts alum sulfates berthierine serpentine group aluminum hydroxides oxides bertrandite sorosilicates aluminum oxides oxides beryl ring silicates alumohydrocalcite carbonates betafite niobates and tantalates alunite sulfates betekhtinite sulfides amazonite alkali feldspar beudantite arsenates and sulfates amber organic minerals bideauxite chlorides and fluorides amblygonite phosphates biotite mica group amethyst -
Identification Tables for Common Minerals in Thin Section
Identification Tables for Common Minerals in Thin Section These tables provide a concise summary of the properties of a range of common minerals. Within the tables, minerals are arranged by colour so as to help with identification. If a mineral commonly has a range of colours, it will appear once for each colour. To identify an unknown mineral, start by answering the following questions: (1) What colour is the mineral? (2) What is the relief of the mineral? (3) Do you think you are looking at an igneous, metamorphic or sedimentary rock? Go to the chart, and scan the properties. Within each colour group, minerals are arranged in order of increasing refractive index (which more or less corresponds to relief). This should at once limit you to only a few minerals. By looking at the chart, see which properties might help you distinguish between the possibilities. Then, look at the mineral again, and check these further details. Notes: (i) Name: names listed here may be strict mineral names (e.g., andalusite), or group names (e.g., chlorite), or distinctive variety names (e.g., titanian augite). These tables contain a personal selection of some of the more common minerals. Remember that there are nearly 4000 minerals, although 95% of these are rare or very rare. The minerals in here probably make up 95% of medium and coarse-grained rocks in the crust. (ii) IMS: this gives a simple assessment of whether the mineral is common in igneous (I), metamorphic (M) or sedimentary (S) rocks. These are not infallible guides - in particular many igneous and metamorphic minerals can occur occasionally in sediments. -
Synthesis of Hydroxy-Sodalite/Cancrinite Zeolites from Calcite-Bearing Kaolin for the Removal of Heavy Metal Ions in Aqueous Media
minerals Article Synthesis of Hydroxy-Sodalite/Cancrinite Zeolites from Calcite-Bearing Kaolin for the Removal of Heavy Metal Ions in Aqueous Media Muayad Esaifan 1,2,* , Laurence N. Warr 2 , Georg Grathoff 2, Tammo Meyer 2, Maria-Theresia Schafmeister 2, Angela Kruth 3 and Holger Testrich 3 1 Department of Chemistry, Faculty of Arts and Sciences, University of Petra, Amman 11196, Jordan 2 Institute of Geography and Geology, University of Greifswald, 17487 Greifswald, Germany 3 Leibniz Institute for Plasma Science and Technology (INP), 17487 Greifswald, Germany * Correspondence: [email protected] Received: 5 July 2019; Accepted: 10 August 2019; Published: 13 August 2019 Abstract: A hydroxy-sodalite/cancrinite zeolite composite was synthesized from low-grade calcite-bearing kaolin by hydrothermal alkali-activation method at 160 ◦C for 6 h. The effect of calcite addition on the formation of the hydroxy-sodalite/cancrinite composite was investigated using artificial mixtures. The chemical composition and crystal morphology of the synthesized zeolite composite were characterized by X-ray powder diffraction, infrared spectroscopy, scanning electron microscopy, and N2 adsorption/desorption analyses. The average specific surface area is around 17–20 m2 g 1, whereas the average pore size lies in the mesoporous range (19–21 nm). The · − synthesized zeolite composite was used as an adsorbent for the removal of heavy metals in aqueous solutions. Batch experiments were employed to study the influence of adsorbent dosage on heavy metal removal efficiency. Results demonstrate the effective removal of significant quantities of Cu, Pb, Ni, and Zn from aqueous media. A comparative study of synthesized hydroxy-sodalite and hydroxy-sodalite/cancrinite composites revealed the latter was 16–24% more efficient at removing heavy metals from water. -
Phase Relations of the Hydroxyl Felspathoids in the System Naalsi0 -Naoh-H 0 4 2
THE HYDROXYL FELSPATHOIDS PHASE RELATIONS OF THE HYDROXYL FELSPATHOIDS IN THE SYSTE14 NaAlSiO4-NaOH-H 0 2 By PETER ASCROFT MACKENZIE ANDERSON, B.Se., M.Se. A Thesis Submitted to the Faculty of Graduate Studies in Partial Fulfilment of the Requirements for the Degree Doetor of Philosophy McMaster University May 1968 DOCTOR OF PHILOSOPHY (1968) McMASTER UNIVERSITY (Geology) Hamilton, Ontario TITLE: Phase Relations of the Hydroxyl Felspathoids in the System NaAlSi0 -NaOH-H 0 4 2 AUTHOR: Peter A.M. Anderson, B.Sc. (London University) M.Sc. (McMaster University) SUPERVISOR: Dr. B.J. Burley NUMBER OF PAGES: ix, 78 SCOPE AND CONTENTS: A stUdy was made of the phase relationships in the system NaAlSi0 -NaOH-H 0, at 15,000 p.s.i. and at 450°C, 520°C, 4 2 600°C and 700°C. The following phases were found and characterised: hydroxyl varieties of nosean, sodalite and cancrinite, with formulae approximating to 3NaA1Si04.NaOH.xH20, l6:.xbl.5, sodic nepheline and phase X, apparently a previously unreported phase, with composition approaching Na Al Si 0 • Approximate phase diagrams were deduced 4 2 2 9 for the four temperatures. i1 ACKNOWLEOOEMENTS The writer is very deeply indebted to Dr. B.J. Burley, without whose continued guidance and support, this investigation would have been quite impossible. Drs. C. Calvo and H.P. Schwarcz have also been generous with time and advice, throughout the project. The assist- ance of others, too numerous to mention individually, has been readily given and gratefully accepted; these include most of the members of the Department of Geology.