An Agile Approach to Building Risc-V Microprocessors
Total Page:16
File Type:pdf, Size:1020Kb
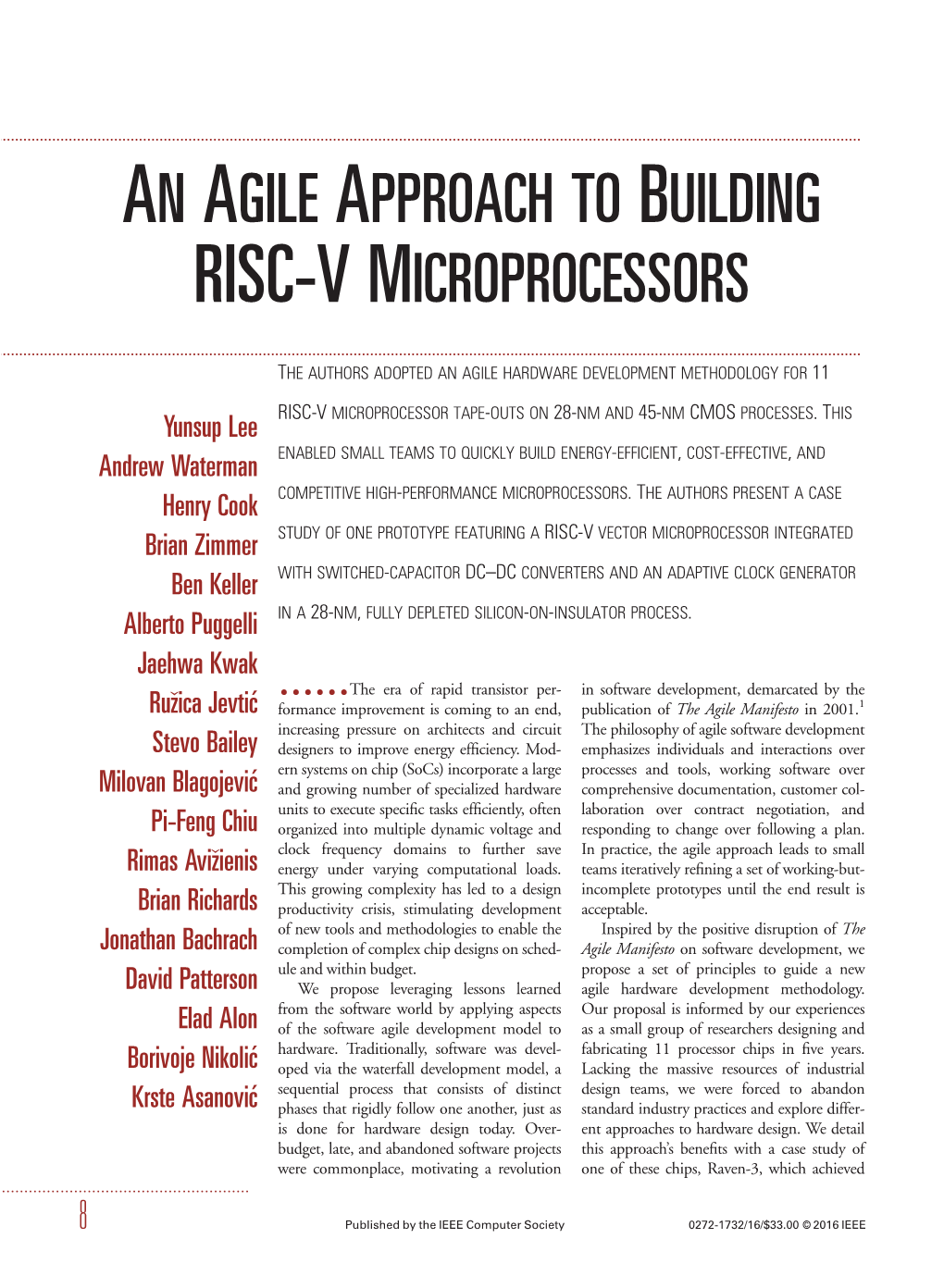
Load more
Recommended publications
-
2018 Enabling Technology Leadership Award
2018 Global In-Vehicle Infotainment Enabling Technology Leadership Award 2018 BEST PRACTICES RESEARCH Contents Background and Company Performance ........................................................................ 3 Industry Challenges .............................................................................................. 3 Technology Leverage and Customer Impact ............................................................. 4 Significance of Enabling Technology Leadership ............................................................. 8 Understanding Enabling Technology Leadership ............................................................. 8 Key Benchmarking Criteria .................................................................................... 9 Best Practices Award Analysis for Automotive Grade Linux .............................................. 9 Decision Support Scorecard ................................................................................... 9 Technology Leverage .......................................................................................... 10 Customer Impact ............................................................................................... 10 Decision Support Matrix ...................................................................................... 11 Best Practices Recognition: 10 Steps to Researching, Identifying, and Recognizing Best Practices ................................................................................................................. 12 The Intersection -
Android Before Ios in The
Vol. 27, No. 1 u hansenreport.com u February 2014 Microsoft Windows Android before iOS in the Car As technology giants Google and Apple baked” and Apple’s approach to the indus- Not Part of Sync 3 focus on extending their reach into the car, try as arrogant. In contrast Google is said Google has made far more progress than its to be more accommodating, indicating it is rival. Both companies have efforts under- willing to adapt Android to make it more Ford Goes with Panasonic and QNX way to make devices based on their respec- useful to carmakers. The software devel- Sync 3, Ford’s third-generation Sync tive operating systems more compatible oped by the OAA is expected to debut in a infotainment system, will be based on with vehicle head units. Google has gone a production vehicle as early as the end of QNX from Blackberry, not Windows Em- step further by showing a willingness to 2014. Nobody is saying if and when iOS in bedded Automotive from Microsoft as adapt its Android operating system to run the Car will find production. with Sync 1 and Sync 2. According to Ford, the vehicle’s head unit, potentially replac- the QNX operating system makes more ing QNX, Linux or Windows. Open Automotive Alliance efficient use of memory and computing At the January 2014 Consumer Elec- Drivers would love to be able to safely power. When an infotainment design goes tronics Show, Google, along with Audi, and easily use smartphones in their cars, to production, carmakers like to have no GM, Honda, Hyundai and Nvidia, and carmakers are keen to offer cars that more than 60% utilization of microproces- announced the founding of the Open let them do that. -
Author Guidelines for 8
Proceedings of the 52nd Hawaii International Conference on System Sciences | 2019 A New Approach to the Evolution of Collaboration Platforms: The Case of South Korea’s Convergence Alliances Heeyoung Jang Minsun Kim Sungmin Cho Korea Institute of Industrial Technology Korea Institute of Industrial Technology Korea Institute of Industrial Technology [email protected] [email protected] [email protected] Jongho Lee Hongbum Kim* Korea Institute of Industrial Technology Korea Institute of Industrial Technology [email protected] [email protected] * Corresponding author Abstract since 2000, there have been no new industries that can generate economy leverage in Korea. While organizations and alliances for collaboration Many studies have demonstrated that among the have been promoted by governments for many years, various factors affecting Korea’s rapid economic their performance has not been very meaningful in growth in the twentieth century, government-led terms of activation or outcome, particularly in South industrial policies were the main cause of the economic Korea. Thus, as a tool for creating new industries and development (e.g., [1]). However, in the current growth engines, a new form of collaboration complex economic environment, arguments for platform—convergence alliances—is being promoted maintaining government-led industrial policies are now in South Korea. In order to explore the distinct not appropriate and this is why a new type of economic characteristics and advantages of convergence growth paradigm is necessary. alliances, this research compares this new type of The government, media, scholars, and practitioners platform with existing collaboration platforms. By now emphasize that new strategies for economic using a case analysis framework with in-depth growth must be developed that will help Korea adapt to interviews, this research suggests several implications the era of the Fourth Industrial Revolution. -
Automotive Data Sharing
Automotive Data Sharing 16.10.2020 Executive summary Data sharing in the automotive industry Data initiatives from National Road Authorities The usage of data in the global automotive industry has been increasingly important National Road Authorities (NRAs) are looking to utilize vehicle generated data. They the last couple of years. Even though Original Equipment Manufacturers (OEMs) are, under the ITS Delegated Act 2010/40/EU, required to share data through have been collecting data from their connected vehicles for several years, they have National Access Points. Some have chosen to comply only with the regulations, just recently started to investigate opportunities for sharing the data. OEMs have while others have taken a more proactive approach to improve road operations and traditionally been reluctant to this, because of the uncertain value potential of their traffic safety in their country. Later this year (2020), the EU Member States will data. However, during 2019 and 2020, the OEMs have gradually been accelerating provide a new update on their progress with the National Access Points. We have sharing of vehicle generated data with third parties and penning deals with both data seen a number of data initiatives from the NRAs, and some are even starting to pilot aggregators and data marketplaces. These deals are creating new revenue streams Vehicle to Infrastructure (V2I) use cases. Some notable mentions of V2I applications for the OEMs. are: - Ingolstadt in Germany – also known as Audi City – are working with TTS and Safety Related Traffic Information Audi to enable traffic lights to communicate with Audi vehicles. Throughout our interviews, utilizing Safety Related Traffic Information (SRTI) have - Barcelona in Spain are collaborating with SEAT, DGT, Barcelona City Council been a persistent topic. -
Devices, the Weak Link in Achieving an Open Internet
Smartphones, tablets, voice assistants... DEVICES, THE WEAK LINK IN ACHIEVING AN OPEN INTERNET Report on their limitations and proposals for corrective measures French République February 2018 Devices, the weak link in achieving an open internet Content 1 Introduction ..................................................................................................................................... 5 2 End-user devices’ possible or probable evolution .......................................................................... 7 2.1 Different development models for the main internet access devices .................................... 7 2.1.1 Increasingly mobile internet access in France, and in Europe, controlled by two main players 7 2.1.2 In China, mobile internet access from the onset, with a larger selection of smartphones .................................................................................................................................. 12 2.2 Features that could prove decisive in users’ choice of an internet access device ................ 14 2.2.1 Artificial intelligence, an additional level of intelligence in devices .............................. 14 2.2.2 Voice assistance, a feature designed to simplify commands ........................................ 15 2.2.3 Mobile payment: an indispensable feature for smartphones? ..................................... 15 2.2.4 Virtual reality and augmented reality, mere goodies or future must-haves for devices? 17 2.2.5 Advent of thin client devices: giving the cloud a bigger role? -
ADA+-+Iot+Automotive FINAL.Pdf
The market for automobiles enhanced with IoT "When Henry Ford made cheap, reliable cars is staggering. A 2013 forecast by GSMA, a global people said, 'Nah, what's wrong with a horse?' association of wireless carriers, found every car That was a huge bet he made, and it worked." will have some type of connection by 2025. The ~ Elon Musk, inventor, entrepreneur and CEO market for technology to connect cars and the of Tesla Motors Internet was an estimated $18 billion in 2012 and is expected to increase three times that number in the next four years. EXECUTIVE SUMMARY “Not only that, but this remarkable technology Since Henry Ford helped automate their can seamlessly sync a wireless smartphone or manufacture, cars have become central to our tablet to a vehicle’s audio and display system lives. This makes the automobile a central hub for communication with pedestrians, other for not only transportation, but as a vehicles and even road infrastructure,” communications center: The ideal ecosystem according to Rajiv Kapur of Broadcom India. for the Internet of Things (IoT). In 2014, the Application Developers Alliance The connected vehicle is truly a microcosm of and its Emerging Technology Working Group IoT. Not only can a networked car, truck or bus began identifying five areas influenced by IoT so include internal sensors that determine such that developers have insight into creating a things as speed, location and temperature of robust IoT ecosystem. This whitepaper serves as the vehicle, but it also may interact with an exploration of IoT by looking at its current surrounding roads, buildings and other vehicles state in automotive; best practices for creating to provide up-to-the-minute information to apps; and new opportunities to explore. -
Assessment of the Technical Feasibility of ICT and Charging Solutions
Assessment of the technical feasibility of ICT and charging solutions Deliverable No. D4.2.1 Workpackage No. WP4.2 Workpackage Title Technical feasibility of ICT and charging solutions Authors ENIDE, ICCS, CEA, CIRCE, CRF, TECNO, UNIGE, VEDE Status (Final; Draft) Final Dissemination level (Public; Public Restricted; Confidential) Project start date and duration 01 January 2014, 48 Months Revision date 2014 – 10 – 31 Submission date 2014 – 10 – 31 This project has received funding from the European Union’s Seventh Framework Programme for research, technological development and demonstration under grant agreement no 605405 Copyright FABRIC <D4.2.1> Public Contract N. 605405 TABLE OF CONTENTS EXECUTIVE SUMMARY ............................................................................................................................ 12 1. INTRODUCTION ............................................................................................................................... 17 1.1 GENERAL .................................................................................................................................... 17 1.2 CONTRIBUTION TO FABRIC OBJECTIVES ...................................................................................... 17 1.3 DELIVERABLE STRUCTURE ........................................................................................................... 17 2. METHODOLOGY .............................................................................................................................. 19 2.1 GENERAL -
DIPLOMSKO DELO Varnost in Policijsko Delo Varnost Mobilnih Naprav Z Operacijskim Sistemom Android
DIPLOMSKO DELO Varnost in policijsko delo Varnost mobilnih naprav z operacijskim sistemom Android Februar, 2014 Avtor: Alen Korošec Mentor: doc. dr. Igor Bernik ZAHVALA Zahvaljujem se mentorju doc. dr. Igorju Berniku za organizacijo, strokovno pomoč in nasvete pri izdelavi diplomskega dela. Posebna zahvala gre mojim staršem, ki so mi omogočili študij in me ob tem ves čas nesebično podpirali, me razumeli in me spodbujali k dosegu cilja. Iskrena hvala prijatelju Domnu Zagoršeku za moralno podporo in za vztrajno spodbujanje k pisanju diplomskega dela. Hvala Petri Letonja za slovnični in slogovni pregled diplomskega dela ter za vso ostalo prijazno pomoč. Hvala vsem, ki ste sodelovali v raziskavi in tako pripomogli k dosegu legitimnih rezultatov. Hvala tudi vsem ostalim, ki ste mi kakorkoli pomagali v času študija in pri izdelavi diplomskega dela. Hvala! Kazalo 1 UVOD ........................................................................................ 10 1.1 NAMEN IN CILJI RAZISKOVANJA ........................................................... 11 1.2 OPREDELITEV PREDPOSTAVK .............................................................. 11 1.3 METODE DELA ............................................................................ 11 2 OPIS MOBILNEGA OPERACIJSKEGA SISTEMA ANDROID ................................. 12 2.1 PLATFORMA .............................................................................. 12 2.2 APLIKACIJE ............................................................................... 13 2.3 GOOGLE PLAY .......................................................................... -
D9.3.4 Workshop Report I
WP 9 – Exploitation, Dissemination, Collaboration and Standardisation D 9.3.4: Workshop Report I Deliverable Lead: FGM Contributing Partners: TU Vienna, IBM, TUDA, Ascora Delivery Date: 10/2014 Dissemination Level: Public Version 1.05 The first SIMPLI-CITY workshop “Business meets Science” took place on the 16th of June 2014 at the ITS European Congress in Helsinki. Experts from science and business discussed future trends of Information Systems with a special focus on Road User Information Apps and Services. Furthermore an additional webinar with the same topic was organised on the 18th of September 2014. This document describes both events. This project has received funding from the European Union’s Seventh Framework Programme for research, technological development and demonstration under grant agreement no 318201 SIMPLI-CITY WP9 Public D9.3.4: Workshop Report I Document Status Deliverable Lead Volker Hoffmann, FGM Internal Reviewer 1 Stefan Schulte, TU Vienna Internal Reviewer 2 Jan Reehuis, Ascora Type Deliverable Work Package WP9: Exploitation, Dissemination, Communication and Standardisation ID D9.3.4: Workshop Report I Due Date 30.09.2014 Delivery Date 20.10.2014 Status For Approval Document History V0.1:Volker Hoffmann, FGM, 26.09.2014, Document structure and content V0.2: Volker Hoffmann, FGM, 29.04.2014, Reviewers remarks from TU Vienna included Contributions V0.3: Reviewer remarks from ASCORA and TU Vienna included V1.00: Second version for interal review V1.05: Final Version Final Version October 20th, 2014 Note This deliverable is subject to final acceptance by the European Commission. Disclaimer The views represented in this document only reflect the views of the authors and not the views of the European Union. -
Android Auto Poc Architect October 21 Harman
Maxim Ovchinnikov Android Auto PoC Architect October 21 Harman GENIVI is a registered trademark of the GENIVI Alliance in the USA and other countries 21- Oct-15 This work is licensed under a Creative Commons Attribution-Share Alike 4.0 (CC BY-SA 4.0) Purpose of this PoC The purpose of this project was to integrate the Android Auto Projection (aka AAP or AA) stack into the GENIVI development platform (GDP). GENIVI is a registered trademark of the GENIVI Alliance in the USA and other countries Oct 21, 2015 Copyright © GENIVI Alliance 2015 1 Why Projection? • We live in connected world and people want to stay connected while they are driving • One of the solutions is a projection from a connected device • Projection is secure. • It is ready to be used immediately. No setup, no profiles creations. GENIVI is a registered trademark of the GENIVI Alliance in the USA and other countries Oct 21, 2015 Copyright © GENIVI Alliance 2015 1 Android Auto Android Auto is an app that integrates with your car to make it easier for you to use some of the main features of your Android phone while driving. You can control things like navigation, music, and your phone's dialer from your car's digital display so you can stay focused on the road. Use of Android Auto requires licensing agreement with Google. Please work with your Google Technical Area Manager (TAM) to secure appropriate licensing agreement. GENIVI is a registered trademark of the GENIVI Alliance in the USA and other countries Oct 21, 2015 Copyright © GENIVI Alliance 2015 1 Hardware setup GENIVI -
On Architectures, Methodologies and Frameworks
Rapid SoC Design: On Architectures, Methodologies and Frameworks by Tutu Ajayi A dissertation submitted in partial fulfillment of the requirements for the degree of Doctor of Philosophy (Electrical and Computer Engineering) in the University of Michigan 2021 Doctoral Committee: Assistant Professor Ronald Dreslinski Jr, Chair Professor David Blaauw Professor Chad Jenkins Professor David Wentzloff Tutu Ajayi [email protected] ORCID iD: 0000-0001-7960-9828 © Tutu Ajayi 2021 ACKNOWLEDGMENTS Foremost, I wish to recognize Ronald Dreslinksi Jr., my thesis advisor, who took a chance on me as an incoming graduate student. He ushered me into academic research and made my transition from industry seamless. He taught me to think differently, perform research, and exposed me to a broad array of research topics. His advice, research, and network were important in my development as a student and researcher. I would like to thank the faculty members at the University of Michigan that have provided additional advice and guidance. Several collaborations with David Wentzloff, David Blaauw, and Dennis Sylvester enriched my research experience. I would also like to thank Mark Brehob and Chad Jenkins for their mentorship and guidance as I navigated my way through the program. I am thankful for the opportunity to work with the good people at Arm; Balaji Venu and Liam Dillon provided me with a glimpse into industry research. I am also grateful to my collaborators on the OpenROAD project for exposing me to open-source world. Ad- ditional thanks to my many collaborators at Arizona State University, Cornell University, University of California - San Diego, and the University of Washington. -
HARMAN to Acquire Software Services Company Symphony Teleca
HARMAN to Acquire Software Services Company Symphony Teleca STAMFORD, CT – HARMAN International Industries, Incorporated (NYSE:HAR), the premier audio, visual, infotainment and enterprise automation group, today announced it has signed an agreement with Symphony Technology Group to acquire Symphony Teleca, a privately- held global software services company. Based in Mountain View, CA, Symphony Teleca provides software engineering and integration services that help businesses rapidly design and develop products and technologies at the convergence of device, sensors, cloud and data. With the acquisition of Symphony Teleca, HARMAN will add a fourth division to its three primary businesses: Infotainment, Lifestyle and Professional. The transaction is subject to customary closing conditions and regulatory approvals and is expected to be completed by the end of HARMAN’s 2015 fiscal year. Under the agreement, HARMAN will purchase Symphony Teleca for a base purchase price of $780 million. In addition, the selling stockholders are eligible for a cash earn-out based on a calendar 2015 revenue target. Approximately $548 million will be paid at close - $382 million in cash and $166 million in HARMAN stock. The number of HARMAN shares issued will be based on the volume weighted average trading price 60 days prior to January 21. The remainder of the base purchase price as well as any additional earn-outs will be paid in cash in the first quarter of calendar 2016. The cash and stock transaction is expected to be accretive to HARMAN’s adjusted earnings in fiscal year 2016, excluding purchase accounting charges, transaction costs, integration costs and other special items. The transaction is subject to customer closing adjustments.